机械制造技术基础-实验指导书
实验须知
1. 实验是学习机械制造基础课程不可缺少的组成部分,这对加深理解基本概念,巩固课堂上所学的知识都很重要,每次实验必须认真对待。
2. 做实验前,必须认真预习有关课程内容和阅读实验指导书,熟悉实验内容和步骤。
3. 做实验时要严格按照实验指导书的内容,步骤进行,认真操作,做好实验记录。
4. 做完实验,请指导教师看实验结果,教师确认实验通过后.应将实验台恢复原状,关好电源.经指导教师同意后才能离开实验室。
5. 每次实验后,按实验指导书的要求,填好实验报告,交给指导老师审阅。
实 验 目 录
实验一 热塑性塑料注射成型实验
实验二 冲杯实验
实验三 多弧离子镀膜实验
实验四 快速成型 (LOM)
实验五 车刀几何角度测量
实验五 车刀几何角度测量
实验六 切屑变形测量
实验一 热塑性塑料注射成型实验
一、实验目的
1、了解注射成型的操作过程。
2、了解原料、注射机、模具与试样之间的关系,并注意工艺条件与试样性能变化的关系。
二、实验内容
1、进行注射成型操作,用手动操作方式,依次进行闭模、注射装置前移和注射、保压、予塑和冷却装置后退和开模顶出制品等五个基本过程的操作。
2、用半自动操作方式,在确定的实验条件下,制取试样,然后依次变化下列工艺条件:注射速度、注射压力;保压时间;冷却时间;料简温度。制取其余五组试样。
观察每组试样的外观质量,记录实验条件不同导致外观质量变化的情况。
三、原材料
PS
苯乙烯—甲基丙烯酸甲酯共聚物
四、主要仪器设备
SZ68/40注射成型机(螺杆直径26mm,注射压力158.2MPA,油泵压力13.7Mpa,喷咀球头半径12mm,孔直径4mm)。
注射试样模具(120mm×15mm×10mm大试样Φ100/Φ50圆形模具个一组)。
模温控制装置
测温计(量程0~300ºC,精确度不低于±2ºC)
秒表(精确度±0.1S)
偏光应力仪
五、实验方法
(一)准备工作
1、阅读使用注射机的资料,了解机器的工作原理,安全要求及使用程序。
2、了解原料的规格,成型工艺特点及试样的质量要求,参考有关的试样成型工艺条件介绍,初步拟出实验条件。
原料的干燥条件;
料简温度、喷咀温度;
螺杆转速、背压及加料量;
注射速度、注射压力;
保压压力、保压时间;
模具温度、冷却时间;
制品的后处理条件。
3、按实验设备使用说明书,操作规程要求,做好注射机的检查,维护工作。
4、用手/低压开、合模操作,安装好试样模具。
(二)制备试样
5、用手动操作方式,在注射机温度仪指示值达到实验条件时,在进行恒温10~20分钟,加入塑料施行予塑程序,用慢速进行对空注射。
从喷咀流出的料条,观察离模膨胀和不均匀收缩现象。如料条光滑明亮、无变色、银丝、气泡,说明原料质量及予塑程序的条件基本适用,可以制备试样。
6、用手动操作方式,依次进行闭模—注射装置前移—注射(充模)—保压—予塑/冷却—注射装置后退—开模—顶出制品—顶出复位等操作。
动作中读出注射压力(表值),螺杆前进的距离和时间,保压压力(表值)、缓冲垫厚度、背压(表值)及驱动螺杆的液压力(表值)等数据,记录料简温度、喷咀加热值,注射—保压时间,冷却时间和成型周期。
从取得的缺料制品观察熔体某一瞬间在矩形、圆形流道内的流速分布,由制品试样的外观质量判断实验条件是否恰当,对不当的实验条件进行调整。
7、用半自动操作方式,在确定的实验条件下,连续稳定地制取5模以上作为第一组试样。然后依次变化下列条件:
注射速度;
注射压力;
保压时间;
冷却时间;
料简温度。
制取第二、三、四、五、六组试样。
实验时,每次调节料简温度后有适当的恒温时间。
制备各组试样时,用测温计分别测量熔体温度、动模、定模的型腔面上3个不同位置的温度。
记录四(二)6条所得各项实验数值。
8、按本实验标准观察每组试样的外观质量,记录实验条件不同导致试样外观质量变化的情况。
9、将各组试样放置于应力双折射场内,观察材料的分子取向程度,分析内应力与实验条件,制品结构的关系。
六、实验报告
1. 写出实验所用的原料、模具、注射机以及成型工艺的各项条件。
2. 表列各组试样的外观质量及内应力分布情况,写出外观质量及内应力与成型工艺条件的关系,简述其原因。
七、思考题
1. 在选择料简温度、注射速度、保压力、冷却时间的时候,应考虑哪些问题?
2. 注射成型厚壁的制品,容易出现那些质量缺陷?如何从成型工艺上给予改善?
八、注意事项
1. 电器控制线路的电压维持在220伏。
2. 在闭合动模、定模时,应保证模具方位的整体一致性,避免错合损坏。
3. 安装模具的螺栓、压板、垫铁应适用、牢靠。
4. 禁止料简温度在未达到规定要求时进行予塑或注射动作。
5. 主机运转时,严禁手臂及工具等硬质物品进入料斗内。
6. 喷咀阻塞时,禁用增压的办法清除阻塞物。
7. 不得用硬质金属工具接触模具型腔。
8. 压力表要在指示值为0时及时关闭,不应任意调整泵溢流阀、顺序阀压力。
9. 严防人体触动有关电器,使设备出现意外动作,造成设备人身事故。
实验二 冲杯实验
一、实验目的
确定金属薄板拉深成形的极限拉深比(LDR)。
二、基本原理
把一定直径的圆形金属薄板,通过标准直径的凸模与凹模冲出杯形件。在不破坏的条件下,能冲出杯形的最大毛坯直径与凸模直径
之比作为拉深成型性能指标,称为极限拉深比(LDR):
式中 --不破坏时的最大毛坯直径;
--凸模(冲头)直径。
极限拉深比的倒数即为极限拉深系数
值越大,或
值越小,钣料的拉深成形性能越好,冲杯实验如图6―1所示。
三、实验设备和工具
BHB-80A型钣料试验机、卡尺等。
四、模具与试件
根据JB4409·3--88“薄钢板冲杯和冲杯荷载试验方法”规定,实验模具尺寸与试样厚度的关系如下表:
冲杯实验模具和试件厚度关系表(mm)
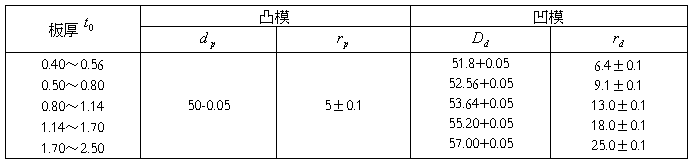
试件外径一般根据材质和拉深系数由计算初步确定,然后,相邻试件直径的级差本实验取3~4mm(一般级差应取1.25mm),试件表面不得有伤痕和划痕,试件边缘不应有毛刺。试件直径测量精度±0.05。
图6―1 冲杯实验装置
1-凸模 2-压边圈 3-试件毛坯 4-凹模 5-试件
五、实验步骤
1、把凸模1装到试验机的中心活塞上,用手把反螺纹拧紧,压边圈2放在压边活塞上面。
2、按照试件毛坯的直径选择定位圈,把定位圈放在压边圈上。
3、在试件毛坯的两面涂上润滑油,把试件放在定位圈中,注意要放正,试件定位圈的外缘与压边圈的外缘对齐。
4、按照试件的厚度选择相应尺寸的凹模,把凹模4装在试验机的凹模座内,再把凹模座放入试验机的模筒中,置于锁紧位置,盖上防尘挡油罩。
5、按下压边开关的按钮,观察压边压力表的指示液压,调整压边调压阀手柄,使压边压力表指示早0.5MPa位置上。
6、打开电液控制器的开关,拧动电流调整旋钮,使小电流表的指针在0.6A以上的位置,保证电液调速阀在开启位置。
7、胀形调压阀手柄在打开位置(拧松),按下中心活塞通油按钮(即胀形开关的按钮),再向拧紧方向调整调压阀手柄,此时在胀形压力表上指示出推动凸模的活塞的液压压力。
8、一面观察被凸模顶出的冲杯试件,一面从胀形压力表指针上观察冲压压力。调整胀形调压阀手柄时,压力表指示不断升高;若压力表指示突然下降时,即表示试件的突缘材料全部进入凹模。冲杯试验完成。或者试件被拉裂。
9、取出试件观察,试件拉裂是否因压力过大引起,若是则要减少压边力。若试件突缘起皱,则应适当增加压边力。上述过程边做,边试。
六、实验数据记录和处理
按照JB4409·3--88的要求,每组同样尺寸的试验要6件以上,逐级进行试验后,选出破裂数少于或等于3件的各组,其中实际毛坯直径最大的那一组,即是极限拉深时最大的毛坯直径D0max。 凸模直径dp为已知,便可计算极限拉深比LDR和极限拉深系数:
和
式中 --凸模直径;
--试件毛坯最大直径。
数据记录和处理结果如表6--2所示:
表6—2
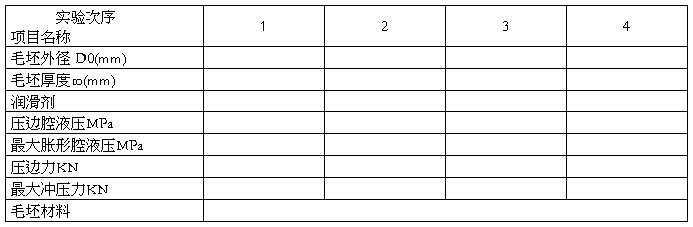
七.实验报告
1、实验报告对本实验的目的、原理、实验装置、操作等作简要叙述。给出试件材料名称、厚度、尺寸规格、润滑剂、压边力、冲压力、、LDR及
等。
2、分析影响冲杯实验结果的因素。
3、简述冲杯实验中金属流动过程。
实验三 多弧离子镀膜实验
一、实验目的
了解表面镀膜的基本原理
二、基本原理
实验在Bulat-6多弧离子镀膜机上进行,其结构主要由弧源、大束流冷阴极离子源、真空系统和供气系统组成。其结构示意图如图4所示。
1、金属等离子体弧源(可以连续弧和脉冲弧方式工作);
2、金属阴极靶;
3、电磁线圈(控制弧斑运动);
4、电磁线圈(控制蒸发粒子运动);
5、二路进气装置;
6、冷阴极离子源;
7、工作台;
8、真空系统;
(1)金属等离子体弧源
这部分包括金属阴极靶及触发电极,控制弧斑运动的电磁线圈,控制蒸发粒子运动的电磁线圈等。金属阴极靶由欲镀金属制成,出发电极是使用脉冲电流作触发形式的阳极,调整脉冲频率可以得到脉冲弧和连续弧两种工作方式。通过调节弧流大小(70~120A),控制Ti靶的蒸发速度;控制弧斑运动的电磁线圈产生的电磁场可对Ti靶表面的弧斑运行进行控制,调节其聚焦电流可使弧斑在靶表面作均匀运行,增加斑的利用率和弧斑的稳定性。通过控制蒸发粒子运动的电磁线圈可对金属等离子体运动轨迹进行控制,增加离化率和减少金属小液滴。
常用弧流为70~90A,聚焦电流中等,沉积偏压为100~800V。
(2)大束流冷阴极离子源
这部分包括阴极、阳极、电磁线圈等。
工作过程:当真空度达到3.0×10-2 Pa后,从离子源通过气孔通入一定量的氩气或氮气,并在阴极和阳极之间加上数千伏的电压。此时产生弱等离子体在阴、阳极之间快速运动,更多的气体分子被电离,产生的等离子体弧流达150~200mA。
(3)真空系统
主要包括:机械泵、扩散泵、多级阀等组成。其作用是建立确保弧源、离子源正常工作,防止样品污染所必需的真空度。
三、实验步骤
1、真空系统的操作步骤:
(1) 开水阀(水压调为3~4Mpa);
(2) 打开总电源,打开机械泵和扩散泵,同时开启预抽阀和抵真空计;
(3) 当扩散泵加热到一定时间后,关上预抽阀,打开前级法。之后前级阀和预抽阀交替工作(目的是使工作室达到一定的真空度的同时,扩散泵的油也不至于因温度过高而氧化);
(4) 当低真空计指示仪表达40格以上时,打开前级阀和主阀,此时低真空计很快达到满量程,再打开高真空计;
(5) 高真空计由低量程到高量程逐渐调至工作所需真空度;
(6) 关机时,先关主阀、高真空计,同时关上扩散泵电源;40至50分钟后,等扩散泵基本冷却后,关上前级阀和机械泵,同时关上电源及冷却水阀。
2、离子源操作
(1) 当真空达到3.0×10-2 Pa时,打开进气针阀,从离子源通气孔通 入Ar气或N2气,直到真空度为1.5~1.7×10-1 Pa时,关上进气针阀。
(2) 打开离子源总电源,电磁线圈电流调为150~170mA。
(3) 打开进气针阀,起动离子源工作(一般情况下,工作电流为150~200mA,工作电压为300~400V)。
(4) 关离子源时,先调小离子源工作电流,电压至零,在关上其启动开关;关上针阀,调小电磁线圈电流至零,关上离子源总电源。
3、多弧离子镀膜(以TiN为例)
(1) 打开进气针阀通入氮气,直至真空度为4.0~4.5×10-1 Pa时,关上进气针阀。
(2) 启动弧源,合上偏压开关,偏压由小直大增加到1.0~1.1 KV,等离子体轰击欲镀工件表面。
(3) 试样表面升温至400~450℃时,打开进气针阀通入N2气,同时降低偏压为200~400 V,开始沉积TiN。
(4) 按沉积TiN膜层厚度确定的时间(单靶1um/h),按顺序关上弧源电源,关上偏压电源,关上针阀。
4、镀膜表面质量观察
观察镀膜表面质量,采用划痕法测量镀膜强度,测量表面显微硬度。
四、实验报告
1、实验报告对本实验的目的、原理、实验装置、操作等作简要叙述。给出镀膜试件材料和靶材料的名称、镀膜结合强度、镀膜厚度,测量表面显微硬度。
2、分析影响实验结果的因素。
实验四 快速成型 (LOM)
一、实验目的
了解快速成型的基本原理
二、基本原理
快速成型制造技术20世纪80年代起源于日本,是近20年来制造技术领域的一次重大突破。快速原型技术是用离散分层的原理制作产品原型的总称,其原理为:产品三维CAD模型→分层离散→按离散后的平面几何信息逐层加工堆积原材料→生成实体模型。
该技术集计算机技术、激光加工技术、新型材料技术于一体,依靠CAD软件,在计算机中建立三维实体模型,并将其切分成一系列平面几何信息,以此控制激光束的扫描方向和速度,采用粘结、熔结、聚合或化学反应等手段逐层有选择地加工原材料,从而快速堆积制作出产品实体模型。快速成形技术系统的工作流程,如图示。[1]
快速成形系统工作流程
快速原型技术突破了“毛坯→切削加工→成品”的传统的零件加工模式,开创了不用刀具制作零件的先河,是一种前所未有的薄层迭加的加工方法。与传统的切削加工方法相比,快速原型加工具有以下优点:
(1)可迅速制造出自由曲面和更为复杂形态的零件,如零件中的凹槽、凸肩和空心部分等,大大降低了新产品的开发成本和开发周期。
(2)属非接触加工,不需要机床切削加工所必需的刀具和夹具,无刀具磨损和切削力影响。
(3)无振动、噪声和切削废料。
(4)可实现夜间完全自动化生产。
(5)加工效率高,能快速制作出产品实体模型及模具。
RPM技术的具体工艺不下30余种,最为成熟的以下四种:
1 立体印刷(SLA-Stereolithgraphy Apparatus)
将激光聚焦到液态固化液态材料(如光固化树脂)表面,令其有规律地固化,由占到线,到面,完成一个层面的建造;而后升降平台,移动一个层片厚度的距离,重新覆盖一层液态材料,再建造一个层,由此层层迭加,成为一个三维实件(如图1所示)。激光立体造型制造精度目前可达±0.1mm,主要用作为产品提供样品和实验模型。此外,日本帝人制机开发的SOLIFORM可直接制作注射成型模具和真空注塑模具。
2 分层实体制造(LOM,Laminated odject Manufacturing)
它采用激光或刀具对箔材进行切割而获得一个层面。具体的说,首先切割出工艺边框和原型的边缘轮廓线,而后将不属于原型的材料切割成网格状。通过升降平台的移动和箔材的送给,可以切割出新的层片,并将其与筠有的层片粘接在一起,这样层层迭加后得到一个块状物;最后将不属于原型的材料小块剥除,就获得所需的三维实体。这里所说的箔材可以是涂覆纸(涂有粘接剂覆层的纸),涂覆陶瓷箔、金属箔或其他材质基的箔材(如图2所示)。LOM可制作一些光造型法难以制作的大型零件和厚壁样件,且制作成本低廉(约为光造型法的1/2)、速度高(约为木模制作时间的1/5以下),并可简便地分析设计构思和功能。
3 选择性激光烧结(SLS,Selective Laser Sintering)
对于由粉末铺成的很好密密实度和平整度的层面,有选择地直或间接粉末熔化或粘接,形成一个层面,铺粉压实,再熔结或接成另一个层面,并与原层面熔结或粘接,哪此层层迭加为一个三维实体(如图3所示)。FDM技术的最大特点是速度快(一般模型仅需几小时即可成型)、无污染,在原型开发和精铸蜡模等方面得到广泛应用。
4 熔融沉积成形(FDM,Fused Deposition Modeling)
将热熔性材料(ABS、尼龙或蜡)通过加热器熔化,挤压喷出并堆积一个层面,然后将第二个层面用同样的方法建造出,并与前一个层面熔结在一起,如此层层堆积面获得一个三维实体(如图4所示)。SLS技术造型速度快(一般制品,仅需1天~2天即可完成)、造型精度高(每层粉末最小厚度约0.07mm,激光动态精度可达±0.09mm,并具有自动激光补偿功能)、原型强度高(聚碳酸脂其弯曲强度可达34.5MPa,尼龙可达55MPa),因此,可用原型进行功能试验和装配模拟,以获取最佳曲面和观察配合状况。
三、系统组成
实验在HRP-IIIA系统上进行,其基本组成如下:
数控系统:由工业控制计算机、控制模块、电机驱动单元、传感器组成,配以HRP2001软件,用于三维图形数据处理、加工过程的实时控制和模拟。
机械单元:由激光扫描单元、可升降工作台、送料装置、通风排尘装置、机身和机壳组成,用于完成系统的加工传动功能。
激光器:由二氧化碳激光管、激光电源、控制器和外光路组成,用于提供加工所需能量。
冷却系统:由可调恒温水冷却器和外管路组成,用于冷却激光器,提高激光能量的稳定性。
系统基本性能参数如下:
1. 电源:220V,50Hz,15A
2. 最大成形空间:450×350×450
3. 成形材料:涂敷有热熔胶的纸、薄膜
4. 激光器:输出功率50Watts 光斑直径0.1-0.2mm
5. 切割速度:500mm/s
四、开机操作
1) 打开电源开关。
2) 打开基础开关,按下调试按钮,启动计算机。
3) 运行HRP2001程序,点击菜单中【制造】,点击下拉菜单中【打开强电】,启动强电,同时制冷器开始制冷。然后点击菜单中【制造】,点击下拉菜单中【打开加热器】,开始加热,根据材料型号设置加热温度,加热30分钟后,操作面板上温度控制器显示温度达到设定值。当温度达到设定值20℃,可进行下一步。
4) 点击菜单中【文件】,将准备加工的STL文件调入计算机,完成开机操作。
五、模型加工
1. 图形预处理
a) 将文件转化维STL格式。
2. 模型制作
a) 点击【设置】菜单,单击【制造设置】,设置系统参数。
b) 选择【模拟制造】开始模拟制造。
c) 选择【制造】菜单,开始制造过程。模型完成,系统自动停止。
3. 关机
a) 单击制造对话框中的“中止”。单击【制造】下拉菜单中的【关闭加热器】和【关闭强电】,关闭HRP2001系统,关闭计算机,关闭机床开关和电源开关。
4. 模型的后处理
模型冷却后,方可从工作台上拿下。用专用工具去掉废料。
每组自行设计一个较简单的三维实体。有关软件的使用参见系统使用说明书。
实验五 车刀几何角度测量
一、实验目的与要求
1、掌握测量车刀几何角度的基本方法与所用仪器的工作原理。
2、弄清车刀各几何角度的定义及其在图纸上的标注方法。
3、巩固和加深对刀具几何角度定义的理解。
二、仪器和用具
1、车刀量角台。
2、直头外圆车刀、弯头外圆车刀、偏刀、切断刀。
三、车刀量角台的结构和工作原理
1、构造
车刀量角台的机构如图1-1所示。它主要由底盘、立柱、刻度板、小刻度盘、大指针、小指针、滑体、定位块、弯板等组成。
在设计、制造和检验车刀时,均以平行于单刀刀杆底面的平面作为基面,因此,在测量车刀的几何角度时,同样应以车刀底面作为基准。
2、工作原理
车刀的几何角度是在车刀的各辅助平面内测量的,而车刀上除了法剖面以外的所有剖面军垂直于车刀的基面。
因此,在设计量角台时,以工作台平面作为车刀的基面(车刀靠工作台平面和定位块定位),以大指针的平面C所在的平面代表个剖面,当工作台转到不同位置时,可能测出车刀各剖面内角度(包括切削平面内角度)。
测量基面内角度时,大指针C面代表走刀方向,将小指针指着测出的刃倾角λs的话:这时大指针(面所在的平面即为车刀的法剖面,因此,能测出车刀法剖面内角)。
测量车刀几何角度时,车刀置于工作台台面上,侧面靠定位块。
四、实验方法及步骤
(一)测主刀刃上的角度;
①主偏角Kr
大小指针为零,转动工作台使主刀刃靠大指针平面C,这时C面为主切削平面,则指针板上刻度线所对底盘上的角度即为Kr。
②刃倾角λs
调整滑体高度,使大指针底边靠刀刃。则大指针所指角度即为λs(右负、左正)。
③前角γ0
使工作台沿逆时针方向转90゜ 这时C面为主剖面。调整滑体、定位块,使大指针底边靠前刀面,则大指针所指的角度为γ0(右负、左正)。
④后角а0
调整滑体和定位块位置,使大指针侧边靠后刀面,则大指针所指的角度为а0。
(二)测副刀刃上的角度;
①副偏角K,r
大小指针对零,转动工作态使副刀刃靠大指针C面,这时C面为副切削平面。指针板上刻度线所对底盘上刻度即为K,r。
②副后角а,0
使工作台顺时针转过90゜ ,调整滑体、定位块,使大指针侧边靠副后刀面,则大指针所指的角度为а,0。
(三)法剖面的角度:
①法剖面的前角γn
在主偏角的前提下,使工作台逆时针方向转90゜ ,这时C面为主剖面,调整小指针,使小指针的角度指着测出的刃倾角λs的角度(这时大指针垂直于刀刃)。调整滑体,定位块,使大指针底边靠前刀面,则大指针所指的角度为γn(右负、左正)。
②法剖面的后角аn
调整滑体和定位块位置,使大指针侧边靠后刀面,则大指针所指的角度为аn。
车刀几何角度测量实验报告
年 月 日
(一)实验目的与要求:
(二)实验数据记录
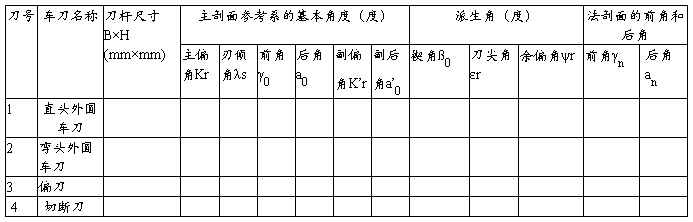
(三)绘制直头外圆车刀标注角度图(标出测量角度)
(四)实验结果分析讨论
实验六 切屑变形测量
一、实验目的与要求
1、了解切屑厚度a0对切屑变形的影响;
2、了解刀具前角γ0对切屑变形的影响;
3、了解切削速度V对切屑变形的影响;
4、仔细观察,研究切屑过程及其变形规律;
二、实验设备、用具及材料
1. 设备:液压牛头刨床(B690);
2. 用具:刨刀、钢尺、卡钳、保险丝;
3. 材料:扁钢(A3尺寸:4×40×100);
三、实验方法步骤
工件的切削层在刀具和工件的相互作用下,与工件层基体分离而成为切屑。在切屑塑性材料过程中,由于加工条件的不同,形成的切屑可为粒状、结状和带状等。
金属切离成切屑的同时,伴随着变形(见图2-1)。因此,切下的切屑长度Ic比被切削层的长度I小,而切屑的厚度a0则比切屑的厚度ac大。假设金属变形后体积不变,则可行切屑的收缩系数:
它近似的表示金属塑性变形的平均值。
测定的方法有两种:长度法和重量法。本实验采用长度法。即把I和Ic的长度或者a0和ac的厚度量出,再代入公式
计算就可以了,实验是按单因素进行,其步骤:
a) 固定切削速度V和刀具前角γ0,后角а0,依次改变切削厚度ac进行切削,测出相应的切屑长度I0,填入报告书中。
b) 固定切削速度V和切削厚度ac,依次改变刀具前角γ0进行切削,测出相应的切屑长度Ic,填入报告书中。
c) 固定切削度а0和刀具前角γ0,后角а0,依次改变切削速度V,测出相应的切屑长度Ic,填入报告书中。
切削层变形的观察与测量实验报告
年 月 日
(一)实验目的与要求:
(二)实验数据记录、仪器与用具
(三)实验记录
1、切削厚度对切屑变形的影响
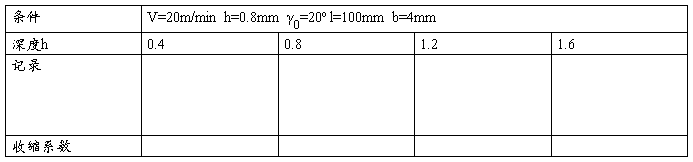
2、刀具前角对切屑变形的影响
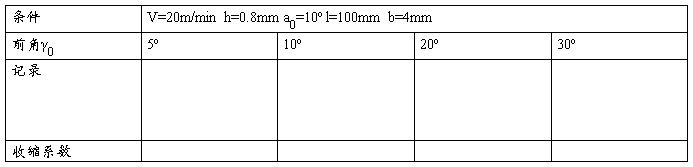