1、目的与要求
1.1 目的
生产实习是理论联系实际的重要课堂。通过生产实习,培养学生理论联系实际的作风,加深理解化工生产的基本原理、生产工艺过程与设备的基础理论、基础知识、生产过程的设计与原理,培养我们化工生产技术经济分析与生产组织管理的能力,提高学习收集和整理生产技术资料的能力和分析与解决问题的能力,进一步培养我们具有材料新产品、新工艺、新设备、新技术的研究与开发的初步能力。
经过大学三年的理论性教育,使我们对生物制药这门学科有了理论上的大体认识,在大三下半年学校安排了我们实习。实习是在校大学生唯一一次接触工厂大规模生产的机会,是学生走上社会的良好过渡,走向工作岗位的入门之课.实习让我们了解到理论和实践之间的差异,找到了工厂大规模生产和实验室小量操作的异同.加深我们对所学知识的理解和消化,同时也学习到各工厂的许多技术细节,掌握了生产的基本工艺原理.这次实习提高了自己培养发现,分析,解决问题的能力,受益非浅,达到了实习的效果。
1.2 要求
通过本次实习,我们应达到以下要求:
(1)了解实习工厂生产的主要产品品种、性能、生产规模和主要原料消耗定额;
(2)详细了解指定实习车间的生产工艺流程、工艺管道布局、控制点、主要工序操作控制方法和操作条件;
(3)了解各主要设备的结构、尺寸、性能;
(4)了解生产流程中采用的耐腐蚀性材料和使用情况;
(5)了解实习车间所用原材料的技术要求和规格;
(6)了解生产过程控制分析和原料产品的分析项目,大致了解主要项目的分析方法;
(7)了解工厂的生产组织和技术管理,安全生产制度;
(8)了解指定实习车间曾出现过的和现在存在的问题,曾采取或打算采取什么改进措施(含生产过程本身以及三废治理及综合利用等方面的问题)。
2、实习指导思想
2.1 指导思想
学生在实习期间应积极贯彻和遵守党和政府的各项方针、政策和法令,严格遵守实习工厂的安全措施和各项规章制度,尊敬师傅、团结同学;对具体的产品工艺要十分熟悉,操作手续,工艺指标清楚,数据齐全,对所涉及的设备构造及工作原理要有一定的了解;绘制出车间布置及工艺流程草图。
对实习工厂组织结构、产品内容、生产过程及生产组织管理体制有比较全面的概括性的了解。
2.2 实习进度安排
(1)厂况介绍,安全教育,生产管理情况介绍,1天;
(2)产品性能与生产原理,工艺流程与指标,设备结构与参数等技术讲座,2天;
(3)生产车间现场跟班实习,3天;
(4)分组讨论及与分厂技术工程师交流讨论,1天;
(5)整理实习报告,考核,1天。
2.3实习地点:巴陵石化分公司己内酰胺事业部。
3、实习内容
3.1 入场教育
3.1.1 安全教育
实习伊始,巴陵石化分公司己内酰胺事业部的工作人员提醒我们无论走到那个车间先找好安全出口,全厂最大的安全隐患是苯泄露及反应釜爆炸,万一遇到这种突发事故,要逆风向高处跑,最好能找到湿毛巾捂住鼻子。在车间参观实习的时候要听指导老师的安排,不可以擅自动仪器设备,遇到紧急事故要听从指导老师,由指导老师处理紧急情况。
3.1.2 己内酰胺事业部简介
巴陵分公司生产己内酰胺是以苯为原料,采用荷兰斯达米卡本公司专利技术HPO法,即磷酸羟胺肟化生产己内酰胺。引进主装置环己酮、羟胺肟化、己内酰胺及废液焚烧的专利技术和专利设备。1992年投料试车,94年5月初第三次开车成功,全线打通流程生产出合格产品并转入正常生产。99年产品部与国内高校联合自主开发新技术,将原年产五万吨己内酰胺扩能至年产七万吨己内酰胺。20##年又和北京石科院共同合作,投产一套氨肟化装置及配套扩改设施,将己内酰胺扩能至14万吨/年。
己内酰胺 分子式:C6H11OH
在液态下为无色,在固态下为白色(片状),具有吸湿性,易溶于水和苯,并具有特殊的气味,凝固点为69℃。己内酰胺应在适中的温度下贮存,要与水、光和空气隔绝,否则易变质。
己内酰胺主要用于生产尼龙-6,由尼龙-6又可加工为:民用纺丝制作内衣、睡衣、衬衫、套服,地毯、毛毯等。工业纺丝用于制作帐篷、汽车轮胎、电缆、绳索、鱼网、绝缘材料等。工程塑料用于制作注射成型和挤压成型的贮器及薄膜。
3.1.3 行为要求《十不准》
进入己内酰胺事业部要求做到以下《十不准》:
(1)不准在生产车间抽烟、喝酒、吃零食;
(2)在厂参观学习时间内不准做与工作无关的事情;
(3)实习期间不准打探、收集事业部商业及生产技术机密;
(4)参观期间不准随便进入生产装置;
(5)下车间参观不准操作任何生产装置设备;
(6)每参观完一个车间必须离开,不准逗留;
(7)入厂期间不准偷盗事业部的财物;
(8)不准损坏公共财物和财产;
(9)不准大声喧哗、吵闹;
(10)不准携带易燃易爆危险品进入事业部。
3.1.4 主要危险化学品危害及相应的安全控制措施
(1)大部分化学产品易燃易爆,因此不要随身携带钥匙,女士不要佩戴耳环、项链等首饰,随身携带的手机需关机;
(2)整个生产流程中涉及到的有毒有害物品主要是苯,遇到苯泄露事故时,应逆风向高处跑。
(3)生产中一些原料和产品是具有强腐蚀性的酸碱液,车间里很多输送管道位于上空,很多管道由于使用已久,可能存在漏液危险,所以在车间内参观时要带安全帽,且不要长时间仰头,尽量保持平视。
3.2 环己酮工艺车间
3.2.1 制氢装置工艺车间
<一> 概述
环己酮车间制氢装置是以石脑油为原料,采用脱砷、脱硫氯除去石脑油中的有害杂质,然后与过热蒸汽混合,经预转化反应生成甲烷等有机物,经转化炉对流段加热至500℃,在总水比4.8以上780℃的温度下转化为大部分的氢气和剩余的甲烷,以及二氧化碳、一氧化碳。转化器中的一氧化碳采用中温变换和低温变换转化为二氧化碳和氢气,变换气中的二氧化碳采用苯菲尔特溶液脱碳法予以脱除,粗氢气中的剩余二氧化碳和一氧化碳经甲烷化反应精制,以生产纯度为92.00%(干基)以上的工业氢直接提供给苯加氢,另一部分工业氢送至变压吸附装置提纯到99.5%以上供羟胺肟化装置使用。
制氢装置原设计生产能力为每小时产工业氢13000标立方米,“五改七”扩能改造后达到每小时产工业氢18500标立方米。正常生产时,每小时供苯加氢装置约8500标立方米的工业氢,变压吸附装置入口10000标立方米的工业氢,另外有少量的氢气供己内酰胺装置使用。苯加氢装置的尾气经过尾气压缩机返回至脱硫入口,一方面可回收尾气中的氢气和甲烷,另一方面可提供钴钼加氢反应的氢气。变压吸附提高羟胺用氢的纯度,减少了羟胺反应的尾气,变压吸附的解吸气经甲烷压缩机送至转化入口,作为制氢的原料。
本装置采用了DCS控制系统,使制氢的生产稳定,安全可靠,操作灵活。本装置各种催化剂都已国产化,催化剂升温还原流程单独进行,大部分的催化剂可在不停车的情况下进行更换和升温还原。
本装置分为脱硫、预转化和转化、脱碳、压缩、司炉以及变压吸附六个部分。
<二> 原料及产品的主要技术规格
制氢装置主要原料为轻油(石脑油),并回收苯加氢尾气、PSA解吸甲烷气。
(1)轻油
轻油原料均为外购。以其中一批油为例分析结果如下:
表3.2.1.21
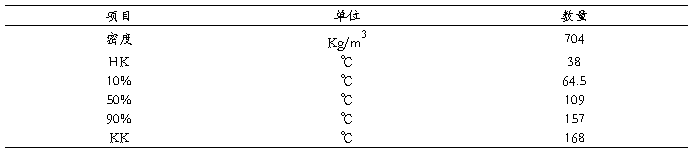
组成表
表3.2.1.22
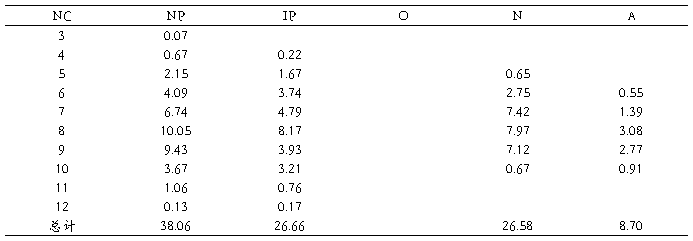
注:NC:碳数;NP:正构烷烃;IP:异构烷烃;O:烯烃;N环烷烃;A:芳烃。
(2)苯加氢尾气
进装置温度 40℃
进装置压力 2.4MPa(G)
流量 800-1500Nm3/h
组成表
表3.2.1.23
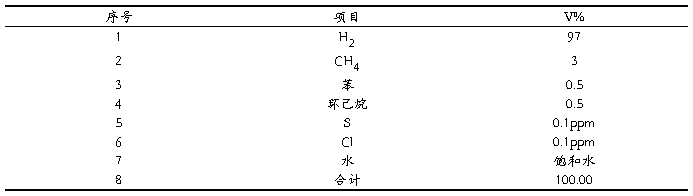
(3)PSA解吸甲烷气
流量 600-1200Nm3/h
组成 CH4 68.6% H2 31.4%
(4)主要原辅材料及公用工程规格
表3.2.1.24
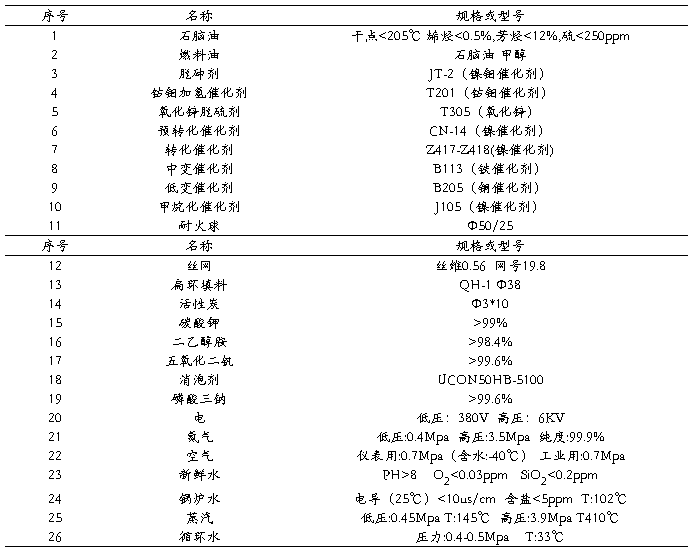
(5)产品规格
装置送苯加氢装置工业氮气、变压吸附出口送羟胺肟化装置纯氢,其性质如下
表3.2.1.25
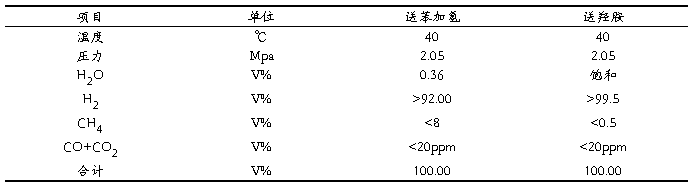
(6)物料平衡
制氢装置扩能后的物料平衡
表3.2.1.26
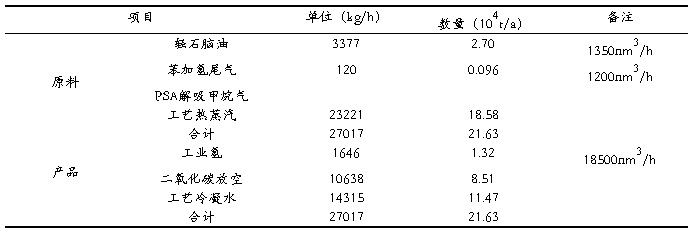
<三> 装置各岗位工艺控制指标
(1)司炉岗位
表3.2.1.31
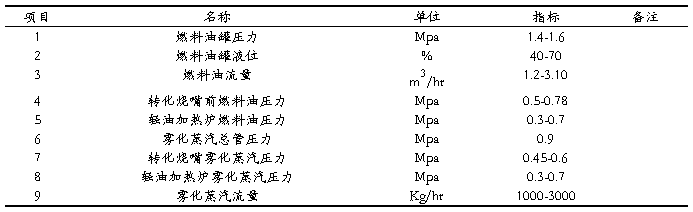
(1)转化岗位
表3.2.1.32
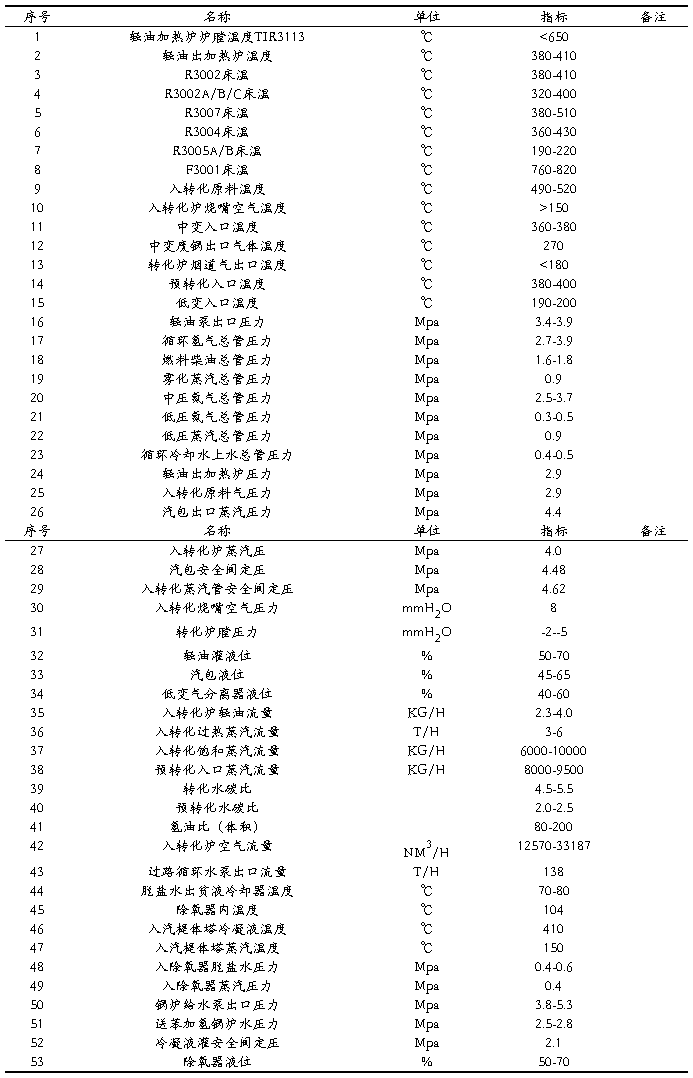
(2)脱碳压缩岗位
表3.2.1.33
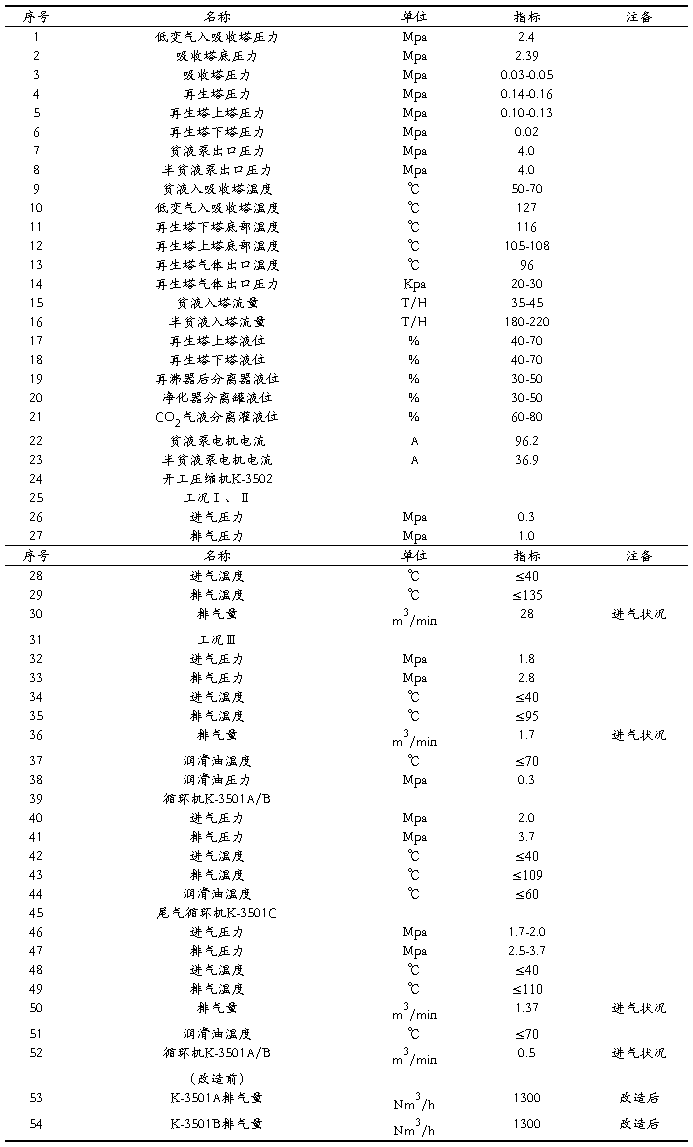
(3)变压吸附岗位
表3.2.1.34

(4)分析指标频率
表3.2.1.35
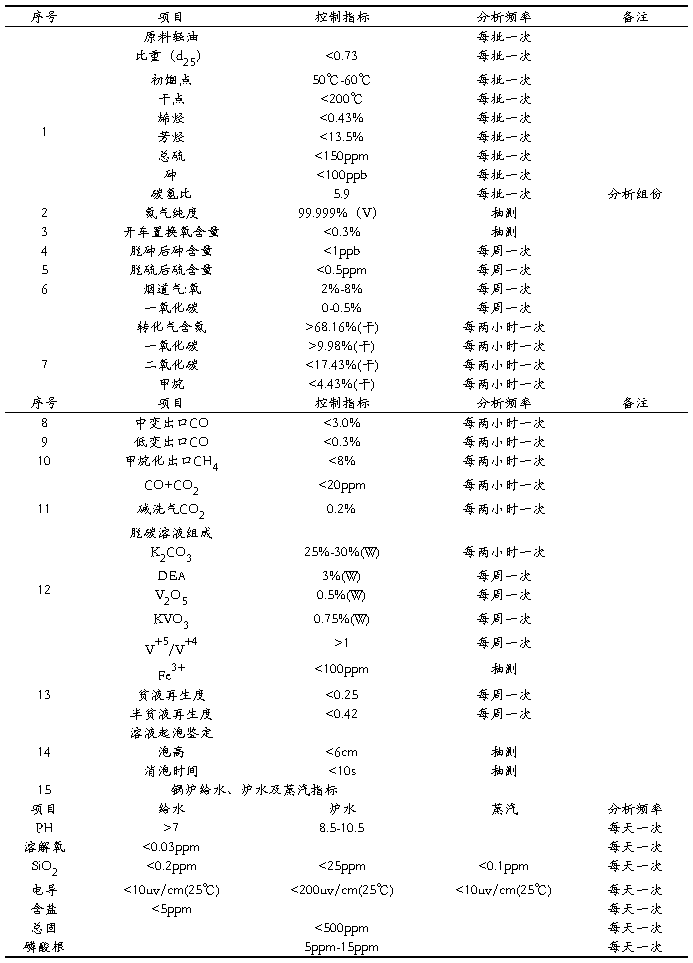
<四>各工序反应原理及影响反映的因素
(1)Ni-Mo、Co-Mo加氢反应(R3002)
R3002炉内触媒分两层装填,上层为Ni-Mo催化剂,下层为Co-Mo催化剂,它们都可以使原料油中的有机硫转变为无机硫,有机氯转变为无机氯,Ni-Mo催化剂还具有脱砷的作用,砷容为5%(W),Co-Mo催化剂的砷容为0.5%。
反应原理:
脱砷反应:
加氢转化反应:
硫醇:
硫醚:
二硫化物:
噻吩:
硫氧化碳:
上式中的R及R'代表烷基。
影响反应的因素:
◆有机硫转化为无机硫的反应是体积缩小,吸热的可逆反应,提高压力,有利于反应的进行,设计压力为3.15Mpa,反应温度主要取决于催化剂的活性温度,适当提高温度可使反应加快,但反应不完全且催化剂容易被破坏,设计温度为380-420℃。
◆同时轻油比也对反应产生影响,轻油比增大,可以降低出口硫含量和减少结焦,设计值为80-120(体积)。
◆此外,催化剂硫化的程度也对反应产生影响。
(2)氧化锌脱硫反应(R3003A/B/C)
氧化锌脱硫反应炉有三个,可以根据需要进行串、并联或单独使用。其反应平衡常数在200-400℃范围内都很大,是目前工业上采用的脱硫效率较好的一中方法。
反应原理:
影响反应的因素:
◆温度:根据催化剂的活性温度范围,设计其进口温度为380-400℃。
◆硫容:硫容是指单位体积或重量的脱硫剂可吸收硫的数量,新催化剂的硫容基本上是固定的,但原料气含有较多的硫化物或不饱和烃时,可提前是催化剂失效。
(3)蒸汽转化反应(R3007/F3001)
原料轻油是由各种烃组份所组成的(包括饱和烃、不饱和烃和芳烃),蒸汽转化反应就是烃类蒸汽转化反应。
反应原理:
同时,还伴有裂解、变换和甲烷化等反应:
影响反应因素:
◆温度:提高反应温度可以提高转化率,但温度过高,催化剂的使用寿命会缩短,且烃类易裂解析碳,所以在控制转化出口甲烷含量的前提下,温度应尽可能低一些。
◆压力:提高压力将使转化出口甲烷含量增加,且易生成游离碳,但加压的影响可通过适当提高反应温度和水碳比的办法来弥补,而且加压可以提高转化反应速率和单位体积设备的生产能力。
◆水碳比:增加水碳比可以降低转化气中甲烷含量,防止催化剂结碳;水碳比过大又增加阻力,降低设备生产能力,导致热能消耗增加。本装置设计值为5.0。
◆催化剂的活性:高活性的催化剂可以加速转化反应,而且氢分迅速提高,有利于避免结碳。
◆催化剂的活性与许多因素有关。除了制造、运输、保管外,装填、升温还原和操作维护等方面也直接影响催化剂的活性。
(4)变换反应(R3004/R3005A/B)
变换反应是将CO与水蒸气反应生成CO2和H2,反应分别在中温和低温变换炉里进行。
反应原来:
影响反应因素:
◆温度:温度的高低对反应的影响很大。温度低反应速度慢,反应平衡常数高,变换率高。温度高反应速度快,反应平衡常数低,变换率低。为了解决这一矛盾,反应分两步走,第一步先进行中温变换,即反应在较高的温度下进行,以较快的反应速度将大部分的CO变换为CO2;第二部则进行低温变换,即反应在较低温度下进行,把残余的CO变换成CO2。
◆水蒸气与CO的比例:同一温度下,H2O/CO比值增加,变换率就增加,反应速度加快;但当真气浓度增加到一定数量时,这种作用就减弱,所以,应控制好适宜H2O/CO比。
◆压力:变换反应是体积不变的反应,压力对平衡无影响,但加压下可加速化学反应速度,有利于变换。
◆气体成分:变换反应是放热反应,如果入口CO含量太高,低变催化剂会应超温而烧坏,因此,低变入口CO含量需严格控制。
(5)甲烷化反应
甲烷化反应就是将碱洗气中少量的CO和CO2通过甲烷化催化转化为甲烷的过程。
反应原理:
影响反应因素:
◆温度:甲烷化反应是一个强放热反应,进气中每1%(V)的CO和CO2的理论温升分别为72℃和60℃,为避免超温,必须严格控制变换和脱碳的工况,使甲烷化入口的CO和CO2含量符合指标。
◆压力:甲烷化反应是体积缩小的反应,适当提高压力对反应有利,设计值为2.30Mpa。
(6)脱碳反应
本装置采用本菲尔特法脱碳,吸收剂为K2CO3,反应方程:
这是一个可逆反应,在吸收塔内发生吸收反应,再在生成塔内发生再生反应。
吸收反应通常按下列步骤进行:
Ⅲ是上述过程中最难的一步,是起控制作用的一步,为加快反应速度,在K2CO3添加活性剂二乙醇胺(DEA)来提高吸收的活性。
为防止脱碳溶液对设备的腐蚀,往脱碳溶液中家务缓蚀剂V2O5.
影响反应因素:
◆溶液的组成:脱碳溶液中含有K2CO3、DEA、V2O5,K2CO3是溶液的主要成分,太低,则影响吸收效率;太高,则家具腐蚀或易结晶而堵塞管道设备。DEA为活性剂,可提高溶液的吸收能力,太低,则活化效果不明显;太高,活化作用的增长也不显著。V2O5为缓蚀剂,它能使系统内设备的碳钢表面生成一层致密的钒化膜,它在溶液中以KVO3的形式存在,随着运行时间的增长,V+5将逐渐还原为V+4应即使补加。为防止塔内溶液气泡,减少杂质的影响,需往系统加入一定量的消泡剂。
◆温度和压力:低温、高压有利于吸收反应,高温低压有利于再生反应的进行,吸收塔通过中部加入半贫液,顶部加入冷却后的贫液保证CO2被充分吸收。再生塔底是利用低变气热源来提供高温,充分脱除CO2。
◆溶液循环量:循环量主要取决于低变气中CO2的含量和溶液的吸收能力。循环量大则吸收的推动力增加,还可以防止气量波动引起C3001出口CO2含量超标,但太大时水、电、汽消耗都要增加,易造成拦液和夹带,反而使净化度下降。
◆溶液再生度:再生度是指再生后的碱溶液中所含CO2和K2O的摩尔数之比。其比值越小,再生就越好,吸收能力就越强,气体的净化度就越好。再生度主要取决于再生塔的压力、温度和循环量。溶液中K2CO3和KHCO3存在着一定的平衡,所以溶液不可能完全再生,但要求再生度必须在一定的范围内。
(7)变压吸附
提纯氢气的原料气中主要组份是H2,其他杂质组份是:CH4、CO2、CO和H2O等,经过变压吸附从原料气中出去杂质提纯氢气。
变压吸附技术是以吸附载体(多孔固体物质)内部表面对气体分子的物理吸附为基础,利用其吸附等温线斜率的变化和弯曲度的大小在系统压力变化后被吸附剂吸附分离,将原料气在较高压力下通过吸附剂床层,相对于氢的杂质CH4、CO2、CO和H2O等组份呗选择性吸附,氢不易被吸附还通过吸附剂床层,达到氢和杂质的分离。然后再减压解吸呗吸附的杂质组份使吸附剂获得再生,以利于下一次进行吸附分离杂质,在这种压力下吸附杂质提纯氢气,减压下解吸杂质使吸附剂再生的循环便是变压吸附过程。
在变压吸附过程中媳妇床内吸附剂解吸是依靠低杂质分呀来实现的,本装置采用的方法是:
●降低吸附床压力(泄压);
●对吸附床层抽真空。
影响变压吸附因素:
◆压力:提高压力可增加吸附剂的吸附量,对提高产品氢气纯度有利;降低压力解吸时,压力越低吸附剂再生效果越好。
◆温度:温度低可增加吸附剂的吸附能力,对提高产品氢气纯度有利;温度低对解吸不利。
◆吸附时间:提高吸附时间产品氢的纯度下降,解吸气量减少,降低吸附时间,产品氢的纯度上升,解吸气量增加。
<五> 工艺流程叙述
(1)脱毒工序
来自原料罐区的轻油进入轻油灌(T3001),经过轻油泵(P3001)加压后,与来自氢气循环压缩机(K3501A/B)的氢气或来自尾气压缩机(K3501C)的苯加氢尾气混合进入轻油加热炉,温度约400℃的轻油、氢混合气一次进入钴钼加氢反应器(R3002)、脱硫反应器(R3003A/B/C)分别将原料轻油中的砷和硫氯脱至小于1ppb和0.5ppm后,送预转化工序。
(2)与转化和转化工序
由脱毒处理工序来的合格轻油气体,按H2O/ΣC等于2.0-2.5的比例添加过热蒸汽进入预转化反应器,在450-490℃生成大量的甲烷、部分氢气、二氧化碳和少量一氧化碳,与甲烷压缩机回收的变压吸附装置解吸气尾气以及汽包来的饱和蒸汽和多热蒸汽混合在总水碳比5.0-5.5经转化炉对流段的原料气加热500-520℃左右,然后进入转化炉(F3001)的辐射段转化管进行转化反应从转化管出来约780℃,甲烷含量为4.4%(V)的转化气进入转化气锅炉(E3001)回收热量,并得到副产物中压饱和蒸汽。该副产蒸汽与转化炉对流段副产蒸汽和中变过路副产抢旗一并由汽包(V3001)进入转化炉对流段的蒸汽过热到420℃,过热蒸汽的一部分经减压后配入原料气中入转化管,其余过热蒸汽一部分去预转化,一部分饱和蒸汽去预转化出口原料气中进入转化管。
(3)变换工序
由转化气锅炉出来的温度约370℃的转化气进入中变炉(R3004)进行变换反应,反应后温度约400℃,一氧化碳含量为3.0%(V)的中变气依次通过中变气-甲烷化换热器(E3002),中变气废锅(E3003)和中变气锅炉水加热器(E3004),使中变气温度降低到200℃后进入低变炉(R3005A/B),进行低温变换但应。中变气的热量分别用于加热脱碳气、副产中压饱和蒸汽和加热锅炉水,由低变炉出来的温度约210℃,一氧化碳含量为0.4%(V)的低变气依次通过低变气锅炉水预热器(E3005)和低变气再沸器(E3008),此时低变气温度将至127℃后再进入脱碳吸收塔(C3001)。低变气的热量分别用于加热锅炉水和苯菲尔溶液。
(4)脱碳工序
由变换来的低变气依次经过低变气锅炉水预热器和低变气再沸器后,温度将至127℃进入吸收塔(C3001)塔底,与来自塔上部和中部的苯菲尔溶液逆流相遇,以出去其中的二氧化碳。脱除了二氧化碳的粗氢从吸收塔顶部出来进入净化气分离器(S3003),分离后去甲烷化。
吸收了二氧化碳的苯菲尔溶液经降压后送至再生塔顶部,再生后的半贫液经半贫液泵(P3003A/B)加压送到吸收塔中部循环使用。再生后的贫液经冷却器(E3010/02)、贫液泵(P3004A/B)和贫液过滤器(FI3002)后进入吸收塔上部循环使用。
再生塔顶部出来的气体经水冷器(E3009)和分离器(S3005)后直接放空和送至普莱克斯公司干冰厂,从分离器排出的冷凝液经冷凝水泵(P3007)大部分送回再生塔顶部,多余的排入化学污水系统。
经脱碳工序脱除二氧化碳后的脱碳气(温度为71℃,二氧化碳含量为:0.1%(V)),依次通过粗氢-工业氢换热器(E3006)和中变气-甲烷化换热器(E3002)后,使气体温度加热到300℃后进入甲烷化炉(R3006)进行甲烷化反应,反应后的工业氢气(温度为343℃,CO+CO2≤20ppm)依次通过粗氢-工业氢换热器(E3006)和工业氢水冷器(E3007),使其温度降到40℃后,送出制氢装置,一部分直接供苯加氢使用,另一部分经变压吸附之后将纯度提高至99.5%以上供羟胺装置使用。
(5)锅炉水工序
脱盐水经(E3010)换热后,进入除氧器(T3020)上部,与下部来的蒸汽逆流相遇,将脱盐水里的氧气除至0.3ppm以下。除氧后的脱盐水经过锅炉给水泵(P3021),一般送低变气-锅炉水预热气(E3005)、中变气-锅炉水换热器(E3004)、转化对流股至汽包(V3001)和另一股中变废锅(E3003)及苯加氢,脱盐水也可经水泵(P3020)直接送苯加氢。
(6)变压吸附工序
经甲烷化出来的>92%的工业一路送至苯加氢装置,另一路送至变压吸附装置。工业氢气在2.05Mpa、<40℃下进入水分离器(V3801)除去原料中夹带水,再进入吸附塔(T3801A-G)提纯,提纯后的氢气(99%)再进入产品氢缓冲罐(V3803)送至羟胺装置。
变压吸附系统的解吸气来自逆放、抽空步骤。解吸气逆放至解吸气缓冲罐(V3804),再通过真空泵(P3801)抽空混合后至混合罐(V3805),送至甲烷压缩机加压后直接送至转化入口。
<六> 制氢装置原材料消耗一览表
表3.2.1.61
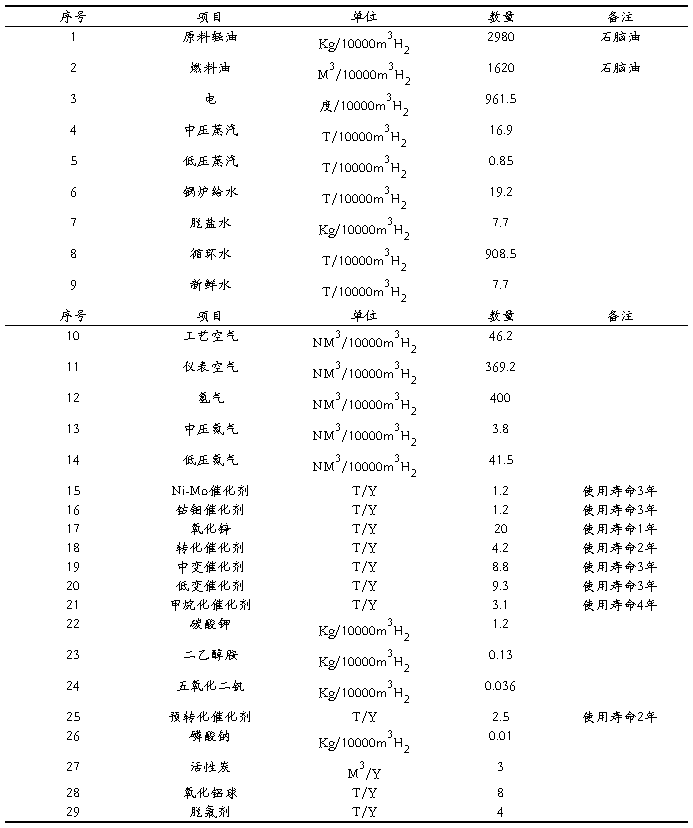
<7> 制氢装置主要设备一览表
表3.2.1.71
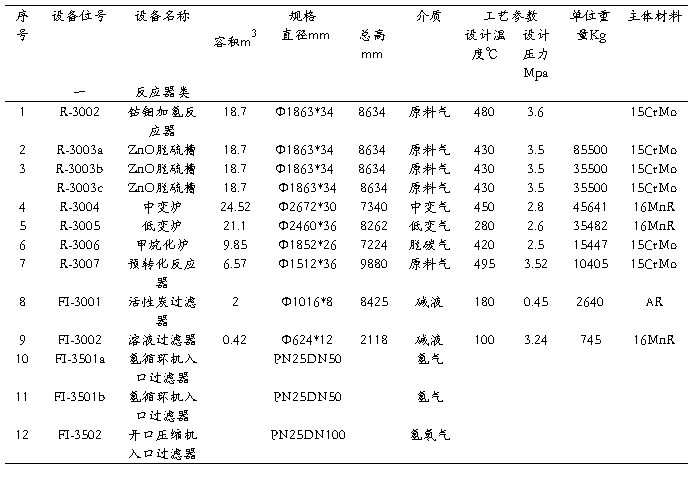
表3.2.1.72
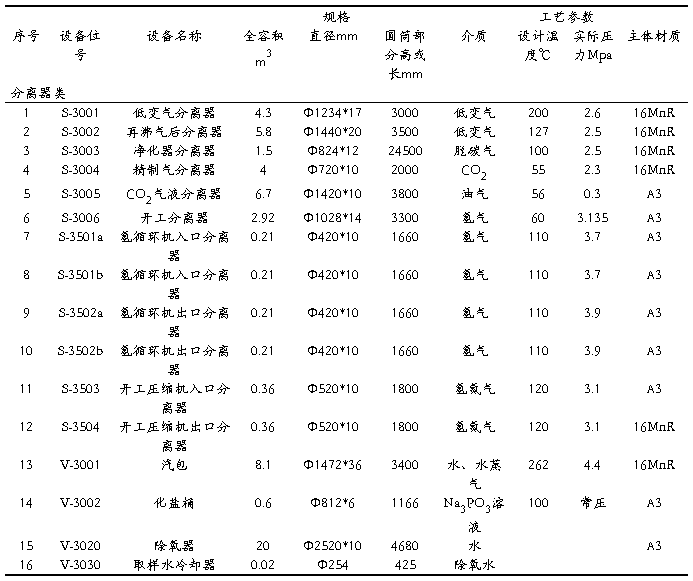
表3.2.1.73
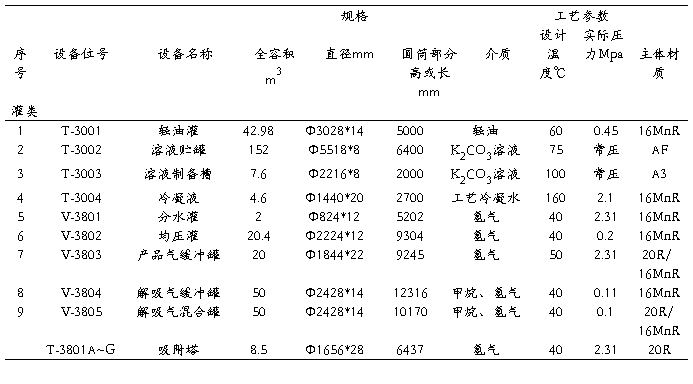
表3.2.1.74
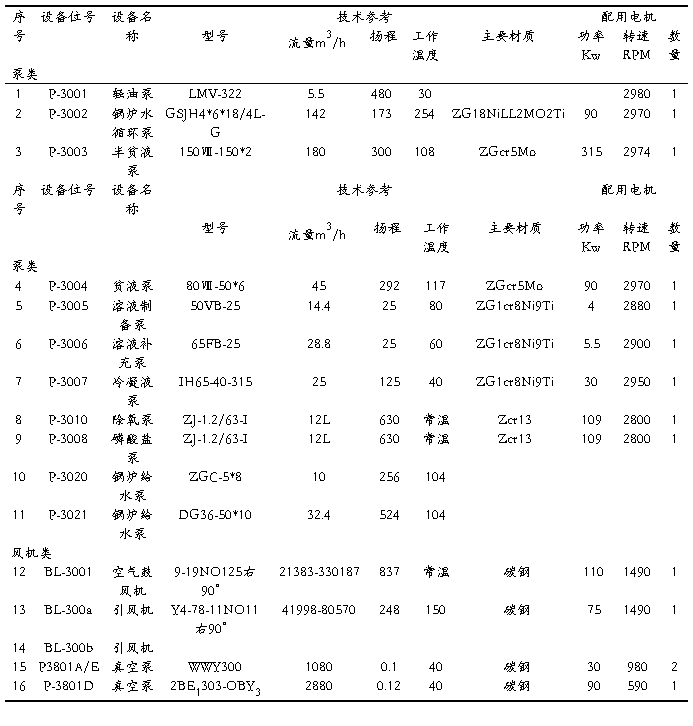
表3.2.1.75
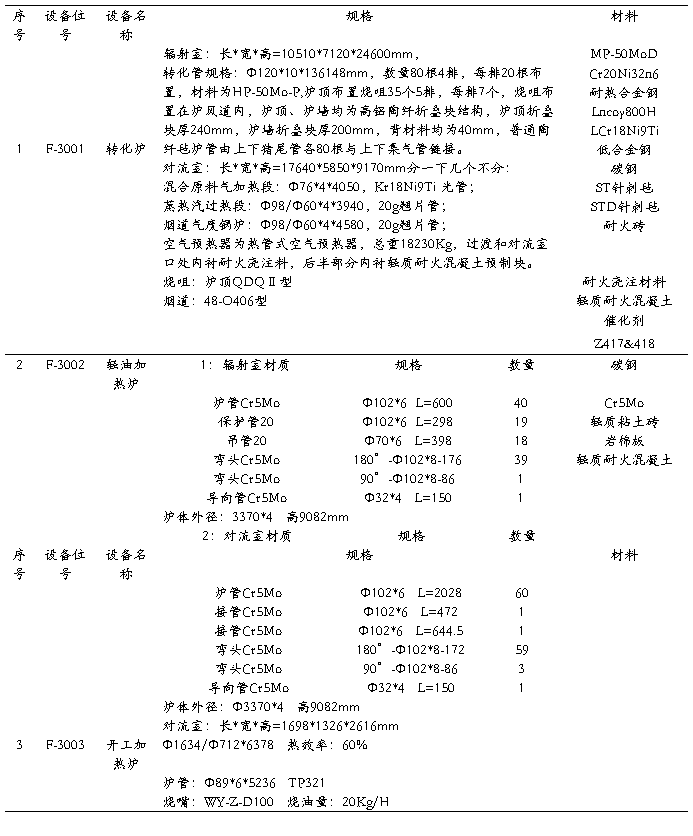
表格3.2.1.76
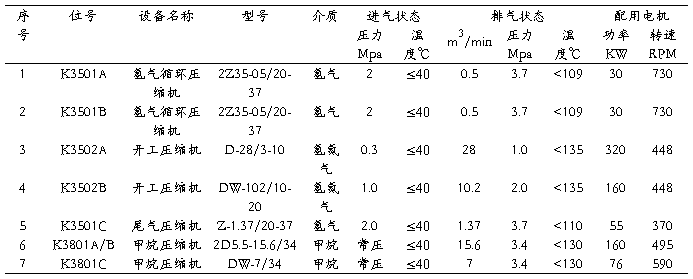
3.2.2 环己烷氧化高压装置车间
<一> 装置状况及特点
(1)装置状况
环己烷氧化装置是己内酰胺事业部的核心装置之一,它的任务是以苯加氢装置来的环己烷作为原料,生产环己酮产品供给肟化装置作原料。
环己烷氧化装置为引进装置,专业商为斯达米卡本公司,负责工艺包装设计,日本千代田化工株式会社负责基础设计,兰州石油化工设计院负责详细设计。本装置土建工程由省建五公司承担,安装由中石油五公司承担。九七年至九九年,氧化高压装置进行了“五改七”的改造,氧化高压装置氧化反应器的扩能由浙江大学提供技术,热回收、吸收系统的扩能改造由天津大学提供技术,烷塔的改造由华东理工大学提供技术,巴陵设计院负责具体设计。二零零六年装置进行扩能改造,中石化工程公司负责氧化高压装置的改造设计。
环己烷氧化按生产特点分为氧化高压和氧化低压两套装置。这一划分,仅仅是针对两套装置中大多数设备的相对操作压力而言的。氧化高压装置(也称5H装置)的生产目的是为了获得粗醇酮;氧化低压装置(也称5L装置)是将粗醇酮经过一系列精制,获得环己酮,并将另一有效组份环己醇通过脱氢转换成环己酮。
本装置采用集散控制系统进行集中监视和控制。为了保证安全生产,根据斯达米卡本规定,界区内的安全联锁系统“SSS”与DCS系统分开设计和安装,但“SSS”的重要阀门的开关则在DCS显示。
本装置的工艺介质主要有:环己烷、环己酮、环己醇、氢氧化钠以及在氧化反应和分解反应中产生的有机酸等。
设备管道采用的材质:凡与有机酸介质接触的设备,氧化系统、分解系统的设备和冷凝、吸收以及废碱液分离系统中的设备均采用316L复合钢板,仅与环己烷、环己酮、环己醇等无腐蚀介质接触的设备和管道均采用碳素钢。
(2)装置规模
环己烷氧化装置经改造后生产能力为年产8万吨环己酮,装置要求达到“两年一修”的生产水平。
(3)环己酮产品的技术规格
a:外观:无色透明油状液体,有丙酮气味。
b:相对密度:相对密度: 0.9644;
0.951;
0.9478;
0.9421。
c:与空气的相对蒸汽密度:3.4。
d:沸点:155.65±0.5℃。
e:熔点:-26℃。
f:折光率:nD20 1.4507。
g:粘点:15 2.45×10-3Pa﹒S,
30 1.803×10-3Pa﹒S ,
659 1.01×10-3Pa﹒S。
h:比热:液体(15-18℃时) 1.803J/g℃。
i:蒸发潜热:4.18×(114-0.141t)KJ/Kg。
j:闪点:43℃。
k:自然点:430℃。
l:爆炸极限:1.1~9.4vo1% 。
m:溶解度:
表3.2.2.11

n:蒸汽压:
表3.2.2.12

◆化学性质:
a:分子式:
b:结构式: =O
c:分子量:98.15
d:化学特性:环己酮的结构式中,具有羰基(C=O),羰基中的碳氧双键由氧的2P轨道和碳的SP2杂化轨道重叠形成一个键,两原子的2P轨道右侧面重叠成一个
键一起组成双键。C=O键能为176~179千卡/摩,比两个C-O键的键能(2×86千卡/摩)还大,而酮分子的羰基,由于氧原子的电负荷性比碳原子大,故其有相当大的极性,对酮的某些化学性质起着决定性作用,其易与氢、氢氰酸、亚硫酸氢钠、格式试剂、羟胺、苯胺等物质起加成反应,能发生醇、醛缩合反应。
◆质量标准
a:中华人民共和国标准(GB/T10669-2001)
表3.2.2.13
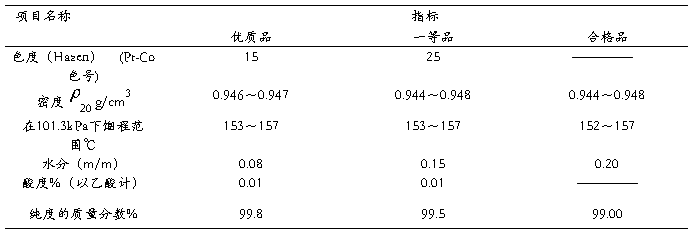
b:产品规格(巴陵分公司规定供6000装置环己酮装格) :环己酮≧99.90wt%
<二>原辅材料规格及动力消耗定额
(1)原辅材料规格
a:环己烷: 表3.2.2.21
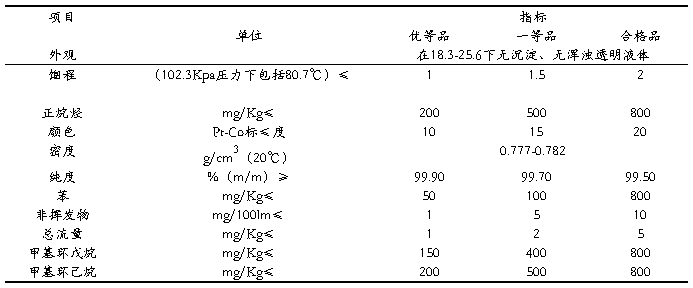
b:氢氧化钠: 表3.2.2.22
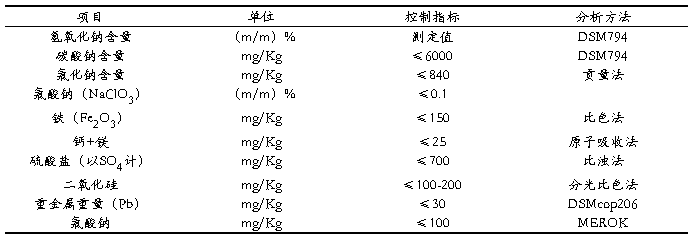
(2)原辅材料及动力定额
表3.2.2.23
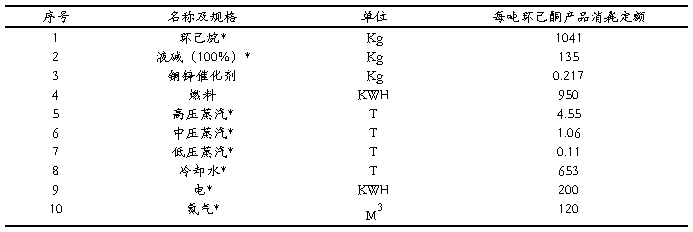
以上带*表示为环己烷氧化高压装置&氧化低压装置合计值。
(3)近五年环己酮产量及原辅材料消耗情况
表3.2.2.24
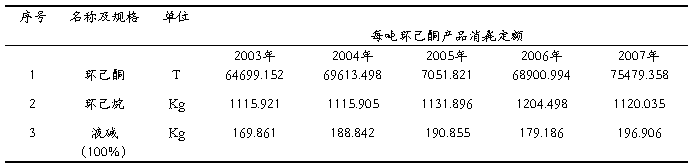
<三> 工艺控制指标
表3.2.2.25
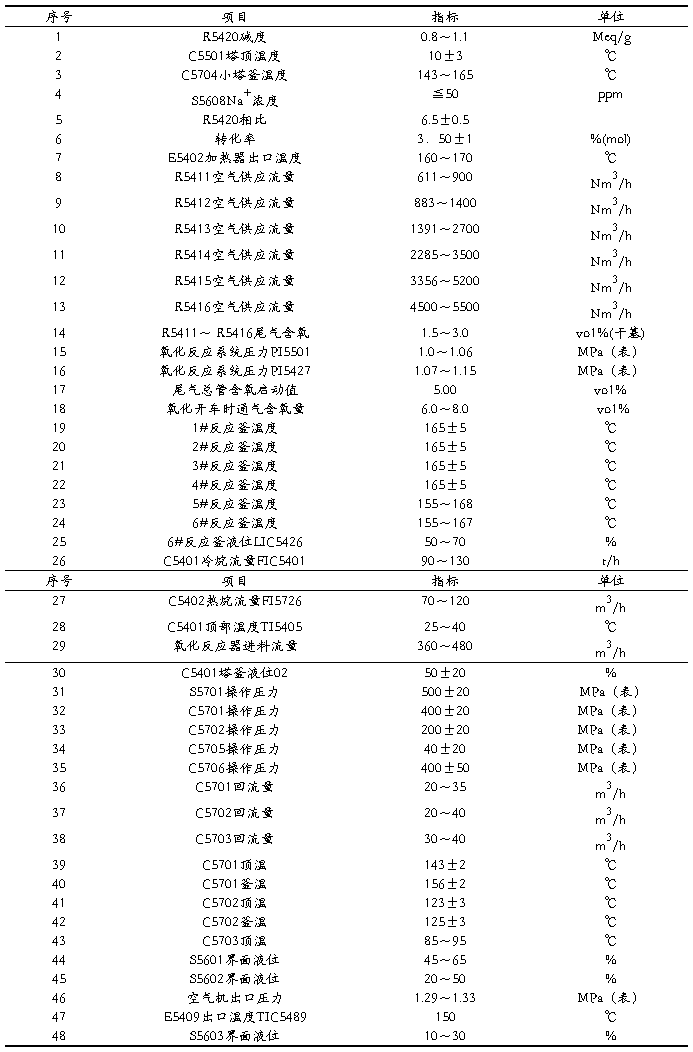
<四> 反应原理和生产方法
(1)以环己烷制备环己酮的生产由两部分组成,即反应部分和精制部分。反应按其化学变化可氛围两个步骤:
Ⅰ环己烷氧化生成环己基过氧化氢:
Ⅱ环己基过氧化氢在碱性条件和钴催化剂条件下,分解成环己酮和环己醇:
在氧化和分解反应进行的同时,同时也产生了酸、酯、醛以及其它高沸点、低沸点的有机杂质。如:
Δ
COOC6H11
Δ
COOC6H11
Ⅲ酸的中和: COONa
COONa
Ⅳ酯的皂化:
COOC6H11 COONa
(CH2)4 +2NaOH (CH2)4 +2H2O
COOC6H11 COONa
(2)影响反应的主要因素
Ⅰ环己烷氧化
环己烷氧化过程是一个极为复杂的反应过程,影响这个反应的因素有温度、压力、转化率、原料纯度等。
◆反应温度和压力的影响:
氧化反应温度与压力是互相有关,不可分割的。因为不同的压力下环己烷有不同的沸点,而反应温度不可能高于该压力的沸点,因此可以说反应温度决定了反应压力。
反应温度和压力的选择通常是:首先反应温度应该保证氧化反应的速度,保证反应器中的耗氧率。在这个前提下,再选择操作压力。
本装置氧化采用无催化空气氧化,因此温度是反应的一个重要条件。提高反应温度会大大加快反应速度,但同时副产物也会增加。
压力越高,尾气中环己烷分压越小,损失的环己烷也会越少,但设备的投资及维修费用也会相应提高。反之压力过低,反应温度就要接近沸点温度,蒸发带出的热量大于反应放出的热量,如要维持反应正常进行,必须外加热量,这对经济运行是不利的。本装置氧化采用氧化反应温度155~170℃,反应压力1.1MPa,尾气含氧2%(V)。
◆反应转化率
环己烷氧化反应的最大特点是低转化率,大循环量。反应开始后,最初产生的分子态产物是过氧化物,然后才是醇、酮及酸和酯类。随着转化率的不断升高,醇、酮上升幅度较大,过氧化物含量几乎不变,而酸酯类上升较慢。当达到一定的转化率时,酸和酯类含量迅速上升,此时有用组分的收率就开始下降。
因此,从提高收率的角度看,应该采用地转化率的方法,因为这时有用物在总产物中的比例高。但是转化率低未反应的物料循环量加大,设备容量就要加大,为输送这些物料所需能量及加热、冷却的能量均要增加。
◆环己烷纯度对反应的影响
环己烷中存在的杂质,将影响反应的正常进行。这些杂质包括苯、醇酮、水及庚烷等。正常的苯加氢反应,苯完全转化为环己烷,如因特殊情况,造成大量的苯进入氧化过程,将导致苯氧化生成焦油,特别在有酮等物质存在下,会加速苯的氧化。其原因是酮的氧化诱导了苯的氧化。此外,苯还有抑制环己烷氧化的作用。因此,严格控制苯加氢产物环己烷中苯的含量是极为重要的。要求烷凝固点≥6.0℃。
反应介质中醇酮进一步氧化,则转变为酸,并且醇酮比环己烷更容易氧化,因此要按规定严格控制烷蒸馏工序馏出液中的醇酮含量。
醇和酮也是环己烷氧化的引发剂,少量醇、酮存在,可以缩短反应的诱导期。这是因为它们被氧化成酸之前也会形成游离基,加快了环己烷氧化反应,故此,本装置氧化初开车时,为缩短反应的诱导期,可采取加醇酮作引发剂。
环己烷中的正庚烷等要严格控制,因为正庚烷能与环己酮形成共沸物而带到己内酰胺产品中,会影响到己内酰胺的挥发性碱。
环己烷中的水份对反应也会有很大影响。在氧化系统中控制水蒸气的分压对减少结渣,延长运转周期有直接的影响,因此对环己烷应预先分出其中所夹带的水份,由尾气带出的环己烷也应分出水后再返回氧化系统。
◆气泡运动对反应的影响
气泡在液体中的运动速度是影响氧化反应的因素之一。一般认为,当气泡过小时,气泡在液体中运动的速度慢,气泡外膜的更新速度也就慢,出于界面上的液体醇、酮的浓度就高,再接触发生深度氧化的可能性增加,酸的产率上升。
如果气泡能迅速在液体中运动,则表面能不断更新,反应生成物迅速转入液相,使气泡的界面上醇酮浓度不致于高出整个液体的浓度。
本装置的氧化釜底部设置有同心环形分布器,空气从不同角度的小孔吹入,能够保证很好的气液接触,同时,为了保证上升的气泡和液体能充分的混合,反应器都装有一台涡轮式搅拌器,强化了气泡在液体中的运动。
Ⅱ分解反应:
◆温度的影响:
温度越高,分解反应速度越快,分解越完全,但同时,环己酮在碱性条件下的缩合也相应增加。温度低,分解反应慢,反应不完全,适宜的分解温度要视工艺要求与特点进行选择。实际操作中,要求其温度控制在85~95℃之间。
◆碱度的影响:
分解反应是在碱性条件下进行的,碱度要使环己基过氧化氢充分分解,得到环己酮和环己醇,碱度过低,分解反应不完全,碱度过高,会使环己酮和环己醇缩合产生黑褐色胶状产物,影响收率。
◆相比的影响:
反应在有机相和无机相间进行,适当的相比,可以获得足够的接触面积,无机相的量太多,就要引入过量的水到过程中,增加了水的循环和消耗,同时也增加了后续过程的负荷,无机相量太少,相间的分散面积不够,碱度增加,同时还影响反应速度。
◆搅拌的影响:
搅拌的目的是保证有机相和无机相之间充分接触面积,使无机相完全分散,以利反应的进行。
(3)生产方法及工艺路线
环己烷氧化装置采用荷兰斯达米卡本的专利技术。以环己烷为原料,采用无催化空气氧化、醋酸钴催化低温分解制得环己酮和环己醇。其工艺路线是:
环己烷氧化成环己基过氧化氢,环己基过氧化氢低温分解成环己醇和环己酮。在氧化反应和分解反应过程中所产生的酸也同时在分解反应器中中和。氧化后产物经分解、分离、环己烷蒸馏、皂化、酮/醇精馏、环己醇转化等工序,最后得到环己酮产品。
与国内许多大学及研究机构合作在环己烷氧化部分采用了多项新技术。
其工艺技术特点是:
◆工艺可靠、已工业化。采用环己烷液相无催化空气氧化醋酸钴催化低温分解的工艺路线,氧化反应温度155~170℃,反应压力1.05MPa(G)。因反应过程不加催化剂,因而避免了结渣的危害,氧化釜和分解器生产周期可达两年。
◆尽管工艺属于有机氧化过程,但仍可得到较高的收率。
◆分解采用新开发的低温分解技术,反应温度88℃,反应压力0.3MPa,在碱液中加入水溶性钴盐催化剂极少(1PPm以下),减少了副反应,增加了收率。
安全方面的特点是:
在装置的布局上,将易燃易爆的5H部分(氧化高压装置)单独布置在厂区的东侧。根据国外专利商的要求,以氧化高压装置为中心的90米半径内不布置有明火的装置或人员较多的车间。对于易燃易爆的石油液化气、环己烷等贮罐,均布置在厂区边缘,并设有消防设施,以确保安全。
为保证安全生产,全厂设置高压氮气(10.0MPa)系统。其任务之一是为环己烷氧化装置的事故处理时使用。紧急事故处理时需1.8MPa的氮气3000Nm³/h,约半小时完成。贮存的高压氮气容量为11300Nm³,可满足两次事故处理的氮气用量。
在环己烷氧化部分为防止生产波动引起生产事故,在氧化高、低压设计了安全联锁,如生产波动范围超过安全要求,安全联锁就会启动保护装置安全。
<五> 工艺流程
(1)工艺流程的叙述
◆热回收、氧化系统
环己烷由环己烷供料泵P5705从回流槽V5702送出,部分环己烷可有P5706A/B供给,流量有FI54012指示,一路经冷却器E5401换热后,由调节阀FPV5401控制进入冷却洗涤塔C5401顶部,一路经调节阀TPV5405送入冷却洗涤塔C5401中部,与直接热交换塔C5402来尾气进行热交换后,底部环己烷由泵P5404送到酸水分离器S5401中,分离的酸水经LLPV5403送到5L的废水提塔(酸水还可送到废水泵P5605入口、废碱蒸发器E5605),环己烷经分离后由C5401的液位调节阀LPV5402送到C5402,同时从烷蒸馏系统送80~100m³/h热烷到C5402顶部一起与氧化尾气换热,经泵P5405送到氧化进料加热器E5402,流量控制在360m³/h到480m³/h,由C5402的液位调节阀LPV5405调节进入氧化反应器R5411,E5402出口温度由中高压蒸汽调节阀TPV5430控制在165℃左右,环己烷在氧化反应器中与压缩空气进行反应生成环己基过氧化氢、环己醇、环己酮和副产物,环己烷物流从R5411依次溢流经过R5412、R5413、R5414、R5415、R5416,空气流量逐次加大,环己烷及反应产物经换热器E5406、E5407A/B后,一路经循环水冷却器E5408,一路经温度调节阀TPV5419由氧化液位调节阀LPV5426控制,进入分解反应器R5420。
为了控制R5412至R5416的反应温度,减少副反应的发生,20##年从P5405出口管线引了一根冷烷管线,经E5403冷却后分别送至R5412至R5416,并增加相应的调节阀。
◆吸收系统
粗醇酮从5L由泵P5905经流量调节阀FPV5502控制流量在2.0m³/h进入E5504与液氨换热后,送到吸收塔C5501顶部吸收氧化尾气中有机物,底部粗醇酮一部分经泵P5501进入氨冷器E5505冷却后,送到C5501中部,一部分经液位调节阀LPV5501和快速切断阀XPV5503送到5L皂化混合器V5602,氧化尾气由压力调节阀PPV5501控制氧化系统压力在1050KPa后排入火炬系统。
◆分解系统
氧化来的环己烷及反应产物经静态混合器进入分解反应器R5420,在控制一定的相比及碱性条件和醋酸钴催化剂的作用下反应生成环己醇、环己酮。NaOH溶液由5L盐萃塔釜液泵P5603经盐萃塔界面液位调节阀LLPV5652送到R5420,醋酸钴催化剂从催化剂槽V5405经泵P5406送入R5420(催化剂可由新碱管线送入,也可经静态混合器送入),循环废碱经循环水冷却器E5420冷却由流量调节阀FPV5492控制进入R5420(循环废碱可经静态混合器进入R5420,也可直接送到R5420)。
◆废碱分离
从分解反应器R5422排出的产物在四个串联的分离器(S5601、S5602、S5603、S5608)中分离成有机相和水相,水相经过调节阀将废碱液送往氧化低压装置V0103,再到废碱蒸发系统处理。由于废碱分离器不能完全有效的分离出废碱液,有机相经过S5608后必须通过新增加的旋流脱盐器S5609和聚结器S5608B/C对废碱液聚结分离,以保障不带碱到烷塔系统。
◆氨系统
液氨由6000装置送入液氨储槽V5004,一路从V5004经快速切断阀XPV5502温度调节阀TPV5505送到氨冷器E5504,一路经快速切断阀XPV5504温度调节阀TPV5509送到氨冷器E5505,液氨在氨冷器E5504、E5505与粗醇酮换热后,气氨由压力调节阀PPV5504、PPV5507控制送到氨压机K5001A/B入口,气氨经K5001压缩后经氨冷器E5001冷却后到液氨槽V5004。
◆烷塔系统
从E5406来的分解产物进入S5701并在S5701中闪蒸,闪蒸的水和环己烷去C5703,底部液体去C5701,环己烷及粗醇酮在E5701中被加热,顶部的环己烷气体进入C5702的再沸器E5702中冷凝,C5701釜液则去C5702做为进料,C5701的再沸器E5701蒸汽由中高压蒸汽提供。进入C5702的液体一部分在再沸器E5702中蒸发,从塔顶出来在E5703中冷凝,C5702釜液去C5703做为进料,C5703中液体大部分在其再沸器E5703中蒸发,从塔顶出来在E5705冷凝,冷凝后的烷流入V5702,E5705中的尾气去E5706,从E5706出来的不凝器由尾气压缩机K5701压缩后,送至C5501,在K5701的中间冷却器冷凝的烷经冷捕集后送回V5702,C5703剩余的混合物流到小塔釜,用泵P5702送至C5704,通过C5704蒸馏后,塔顶产物排入C5703,底部产物经泵P5710排至皂化V5601。
C5701塔顶产物在E5702冷凝后流至V5703并排至V5701,C5702塔顶气相在E5703冷凝后流至V5701,回流泵P5708从V5701送烷入C5701和C5702做为塔顶回流,泵P5701从V5701送烷至C5402顶部作为热烷循环。C5703塔顶产物冷凝后送入V5702,V5702的环己烷经泵P5705送至C5401顶部,V5702底部废水用泵P5704送至低压。由中间罐区T5201的环己烷经环己烷送料泵P5207送环己烷到V5702作为氧化环己烷的补充。
来自S5701的物料经过FPV5701F进入C5706,环己烷及粗醇酮在C5706再沸器E5720中加热,E5720使用的蒸汽是中高压蒸汽(1.1MPa),塔顶气相进入C5705再沸器E5722中冷凝;C5706的塔釜液体经过LPV5701F进入C5705。进入C5705的液体一部分在再沸器E5722中蒸发,从塔顶出来在冷凝器E5721中冷凝,冷凝液进入V5702,不凝气进入E5706;C5705的塔釜液体由泵P5711A/B经过LPV5701C送至C5704,再蒸发后,有泵P5710A/B送至5L装置。(注:C5705的塔釜液体也可由泵P5711A/B经过LPV5701C直接送至5L装置。)
C5706的塔顶气体在E5722中冷凝,冷凝液进入回流罐V5705,回流泵P5712A/B将V5705中的冷凝液一部分经过FPV5703F送至C5706,为C5706提供回流;一部分经过FPV5461,在E5404中冷却后,作为一股冷烷进入C5401;一部分也可通过LPV5702F进入V5701,目的是控制V5705的液位,并提供一股热烷。
C5706的塔顶气体在E5722中冷凝后的不凝气经过PPV5702F控制,送至E5721进行冷凝,冷凝液进入V5702,不凝气进入E5706。PPV5702是用于控制C5706的他定压力。
C5705的回流是由P5706提供,由FPV5703C控制。
3.2.3 环己烷氧化低压车间
<一> 反应原理和生产方法
(1)反应原理:
Ⅰ酯的皂化:
COOC6H11 COONa
(CH2) +2NaOH (CH2) +2H2O + 2C6H11OH
COOC6H11 COONa
Ⅱ环己醇脱氢反应:
(2)反应的主要影响因素
Ⅰ皂化
◆温度的影响:
温度越高,皂化反应速度越快,皂化越完全,但环己酮在碱性条件下的缩合也相应增加。温度低,皂化反应慢,反应不完全。皂化温度既要保证皂化反应完全,有利于己醛转化成重组分,同时也要使醇酮的挥发和循环减至最小。本装置皂化反应温度控制在95-100℃之间。
◆碱度的影响:
皂化碱度要使皂化得到的产物中酯的浓度很低,同时使醇醛缩合出去醛。碱度过低,皂化反应后酯醛含量高,碱度过高,会使环己酮和环己醇缩合产生黑褐色胶状产物,影响收率。碱度控制在1.0meq/g比较有利。
◆相比的影响:
皂化反应在有机相和无机相间进行,适当的相比,可以获得足够的接触面积,无机相的量太多,就要引入过量的水到系统中,增加了水的循环和消耗,同时也增加了后续过程的负荷,无机相量太少,相间的分散面积不够,同时还影响反应速度。相比控制在10VOL%左右。
◆搅拌的影响:
搅拌的目的是保证有机相和无机相之间充分接触,使无机相完全分散,以利于反应的进行。
◆环己烷浓度的影响
环己烷的极性较环己醇、环己酮低,亲水性差,皂化反应中,有机相中环己烷浓度太高,是邮寄相和无机相的混溶性差,减少了皂化反应的接触面积,碱层分层性低,反应受到影响。有机相中不含环己烷,碱液层的分散性就好,皂化反应就完全,环己烷浓度过高还会影响到反应温度的稳定,因环己烷沸点低,蒸发量大,带走了热量,但皂化反应后,加入适量的环己烷,可以促进两相分离。
Ⅱ环己醇脱氢
◆温度的影响:
环己醇脱氢反应为吸热反应,环己醇转化率随温度身高而增加,适当高的温度有利于醇的转化,温度太低,反应不能发生,温度太高,催化剂的使用寿命迅速下降,而且催化剂晶体易烧结而失活,同时高温下,高沸点副产物增多,覆盖催化剂的微孔降低催化剂的比表面和活性。
◆反应压力的影响:
环己醇脱氢反应为体积的增大反应,降低压力有利于平衡向醇转化方向进行,但实际上只能在常压下进行,工业上高温下的减压操作部安全。
◆原料纯度的影响:
原料中高沸点杂质越少越好,可以减少催化剂微孔的堵塞现象,延长催化剂的寿命。
(3)生产方法及工艺
环己烷氧化低压装置工艺路线短:
环己烷氧化高压装置来粗醇酮经皂化、精馏得到环己醇产品,另外环己醇脱氧转化成化基础循环使用。
1997年实现装置60kt/a,1999年实现装置70kt/a改造。
20##年进行装置124kt/a改造。
其工艺技术特点是:
◆精制系统采用先进的填料,既保证了产品质量,又实现了节能。
◆环己醇脱氢采用常压工艺过程,使环己烷氧化物中环己醇转化成为主要产品环己酮。反应温度220℃-250℃,转化率45℅-55℅,出率超过98℅。使用的铜锌催化剂原为国外进口催化剂,97年与辽河催化剂厂合作研制出适合醇脱氢生产的催化剂LY-1,其性能超过进口催化剂T-2492,特别是生产负荷上远高于进口催化剂,实现了催化剂国产化。
<二> 工艺流程叙述
(1)皂化
来自氧化高压装置的粗醇酮送入皂化槽V5601,另外来自中间罐区的50wt℅的氢氧化纳溶液(新鲜碱)和自来水封槽V5804的工艺水分别由泵P8101和泵P5812送入V5601.新鲜碱流量由FIV5652控制,要使皂化反应后的醇浓度较低,而且同时利用醛醇缩合反应将低沸点醛、醇转化为高沸点产物,无机相的纯度必须控制在0.8-1.05meq\g之间。若碱度过高,会有黄褐色胶状醇、酮缩合产物生成,因此加碱亮要根据V5601的碱性变化及时调整。工艺水流量由FIC5651控制,要使AE5652分析样中含有10vol℅的水相,以保证有充足的水相供皂化反应。V5601中的有机相和无机相由搅拌器AGV5601充分混合。有机物和碱水混合物经溢流管流入混合槽V5602.V5601蒸发出的蒸汽经V5601的气相管进入皂化冷凝器E5601.V5601温度必须控制在95℃-100℃之间,这样可以防止游离环己烷存在于无机相中给皂化反应带来不利影响,同时较高的温度有利于己醛转化为较重的产物。在开车初期,为了使皂化反应达到所需的温度,可以通过位于V5601中部的抵押蒸汽喷射器J5601加热。若V5601温度过高,大量醇酮蒸发后进入E5601,醇酮在E5601中冷却后进入S5601的有机相中,使加入V5602的环己烷中醇酮含量过大,容易造成系统乳化。
(2)混合
进入V5602的皂化混合物必须供入环己烷,以便将其中的醇酮萃取到有机相中。环己烷来自皂化分离器S5605由泵P5607加入。氧化高压装置吸收塔C5501底部物料也排入混合槽V5602.V5602产生的蒸汽通过V5602气相馆线流入E5601.为了使V5602的环己烷与环己酮进行充分混合,利用泵P5602回流管线流上的混合喷射器J5602将物料在V5602中循环达到混合要求。V5602底部的混合物由泵P5602排入盐萃取塔C5602,V5602液位由LIC5651控制。
(3)萃取
来自V5602的混合物在盐萃取塔底部成上层有机相和下层水相。C5602的假面液位由LLIC5652控制。上层的有机相上升与自来水封槽V5804的工艺水接触。该工艺谁萃取出分散在有机相中的盐类和氢氧化钠。流量由FIC5654控制在4.0m³\h左右。下降到C5602底部的水相由泵P5603送往氧化高压装置的分解反应器R5420,另外,新鲜碱加入R5420的管线与泵P5603入口相连,加碱流量由FIC5653控制。上升到C5602塔项的有机相流入干燥塔C5801上部。
(4)干燥
C5602项部出来的有机物含有30℅左右的环己烷。由于水在环己酮和环己醇中的溶解度较高,从C5602顶部出来的有机物还含有相当数量的水。环己烷和水必须脱出才能供给精制系统。在干燥塔C5801中,利用烷水共沸将进料中的环己烷和水汽提出。
来自C5602塔顶的有机物进入C5801的顶部塔盘:来自脱氢系统V5905\V59052的粗醇酮通过P5904经E5819换热后加入C5801中的第8层塔盘。C5801进入经塔釜再沸器E5801加热蒸发后,环己烷、水及极少量的醇酮从C5801的塔顶气相口流入冷凝器E5820。C5801的底部物料由塔底产物泵P5820送入初馏塔进料泵P5806的吸入管线。泵P5806入口同时与粗醇酮贮槽T5802相连,前方多余的物料可以进T5802缓冲。
(5)冷凝与分离
来自皂化槽V5601、混合槽V5602、废碱分离罐5606、废水汽提塔C5603的顶部气相管出口的蒸汽在E5601中冷凝,来自干燥塔C5801顶部气相管出口的蒸汽在E5820中冷凝。这些蒸汽冷凝后靠重力作用流入分离器S5605。凝液在S50605中分离成水层和有机层。下层的水层由LLIC5631控制界面液位50%左右,多余的水排入水封槽V5804。上层的有机层中环己烷含量较高,由泵P5607送到V5602和C5703。E5601/E5802尾气排入火炬总管,使与该冷凝器相连的设备的操作压力固定在与大气压接近的压力下。火炬总管尾端与低压氮气管线相连,为避免火炬管形成爆炸混合气,开停车时火炬管线要用少量的氮气吹扫。TI5631在E5601尾气管线上,TI5822在E5820尾气管线上,尾气温度保持在40℃左右,尾气温度过高就会报警,此时大量的环己烷蒸汽就会进入火炬总管,因此要避免尾气温度过高。
(6)废碱液蒸发
从氧化高压装置来的废碱液排往废碱缓冲罐V0103,由于氧化高压装置过来的废碱液压力较高,废碱液在V0103中闪蒸。闪蒸后的水蒸气和烷蒸汽在罐顶换热器E0103作用下冷凝,冷凝液流入V0104,不凝气通过V0103罐顶呼吸阀排空。当V0104液位高于50
%时,由于现场操作人员通过真空罐回收到系统中。V0103底部的废碱液经P5103送往立式单程蒸发器E5605,流量由FIC5638控制。供往E5605壳程的蒸汽流量由FIC5627控制,使废碱液分离罐S5606排出的皂化液浓缩到40wt%左右。烷水蒸汽由S5606顶部气相管进入E5601。S5606上部装有除沫网,以挡住烷水蒸汽中夹带的含有钠盐的液滴。为减少废碱蒸发系统发泡和结垢,需要定期补加废碱消泡剂,由现场操作人员通过氮气将V0105中消泡剂压入V0103。S5606底部的废碱蒸液由泵P5601送往Sec800装置。
(7)废水汽提
送往废水汽提塔C5603的工艺废水来自本装置的水封槽V5804、氧化高压装置回流槽V5702以及尾气制氮装置的废液分离罐。在C5603中,工艺废水由进再沸器E5607的低压蒸汽加热,混合在工艺废水中的环己醇、环己酮和环己烷被汽提出来,汽提后的蒸汽从C5603顶部气相口进皂化冷凝器E5601。汽提后的废水用P5605经冷却器E5606排往Sec600装置。另外,氧化高压装置烷水分器S5401来的酸水经LLPV5403也送入P5606的入口。
(8)精制
Ⅰ初馏塔C5802/022
C5802和C58022并联用于脱出精制系统进料中微量的轻组分和水,其中C5802负担55%的生产负荷,C58022负担45%的生产负荷。
C5802塔径2.2米,为三段波纹规整填料,其中精馏段为一段填料,填料高5.8米提溜段为两段填料,填料高为13.2米。C58022塔径2.0米,利用原新酮塔C58032改造,内装三段板波纹填料,其中精馏段为一段填料,填料高8.5米,提馏段为两段填料,填料高15.5米。
为降低塔釜的操作温度,两塔在减压下操作。由于C5802和C58022的操作压力低于C5801操作压力,部分进料在塔中汽化,汽化率为13.8%。C5802操作如下:粗醇酮液由进料泵P5806从粗醇酮贮槽T5802送入初馏塔C5802,进料流量由FIC5802控制在19.6m³/h,压力由PIC5806控制在-47.7Kpa(G)。粗醇酮在C5802中蒸发所需的热量由进再沸器E5802的中压蒸汽供给,蒸汽流量由FIC5803控制。C5802塔顶产物在冷凝器E5803中冷却,冷凝器回入流槽V5801。被有机蒸汽饱和的惰性气体从E5803中流往气体冷却器E5804,在较低的温度下,更多的有机物冷凝并排入回流槽V5801.气体冷却器E5804中被有机物饱和的不凝气体流往真空装置X5802。回流泵P5805将21.2m³/h回流液从回流槽V5801中送往C5802顶部,由FIC5806控制将极少部分的轻组分排往昌德公司。C5802底部醇酮和重组分由泵P5804排往酮塔C5805。C58022操作如下:粗醇酮液由进料泵P5806从粗醇酮贮槽T5802送入初馏塔C8022,进料流量由FIC58072控制在18.7m³/h,压力由PIC58262控制在-47.7Kpa(G)。粗醇酮在C58022塔顶产物在冷凝器E58072/082中冷却,冷凝液流入回流槽V58022。不凝气体流往真空装置X58022。回流泵P58082A/B将22.2m³/h回流液从回流槽V58022中送往C58022顶部,由FIC58282控制将极少部分的轻组分排往昌德公司。C58022底部醇酮和重组分由泵P58072排往酮塔C5805。回流槽V5801/V58022中累积的水通过其底部的现场排放管由现场操作人员定期排放。
Ⅱ酮塔C5805
C5805用于分离环己酮和环己酮,为提高它们的相对挥发度,塔在真空下操作。由于C5805的操作压力低于初馏塔压力,进料在塔中汽化,气化率为26.7%。为了减少由不凝气带出系统的环己酮,第二冷凝器E5823冷凝温度设定为35℃。C5805塔径4.2米,内装四段板波纹规整填料,其中精馏段为三段填料,填料高24米,提馏段为一段填料,填料高8.6米。
初馏塔塔底产物由泵P5804/P58072送至C5805最下面一层填料的上部,正常负荷下流量为40.2m³/h左右。物料在酮塔蒸发所需的热量由进再沸器E5821的中亚蒸汽供给,蒸汽流量由FIC5870控制。C5805塔顶气相经冷凝器5822、E5823冷却后,冷凝液流入回流槽V5805。被环己酮饱和的不凝气体流往真空装置X5805。真空装置X5805顶部压力在6Kpa(绝压),压力由PIC5807控制。
X5805为三级抽真空装置:第一级由喷射器J5810和真空冷凝器E5824组成;第二级由喷射器J5811A和真空冷凝器J5825A组成;第三级由喷射器J5811B和真空冷凝器E5825B组成。第一级喷射器J5810通入中压蒸汽,混合汽在E5824冷凝,不凝气体进入第二级喷射器J5811A。J5811A通入中压蒸汽,混合汽在E5825A冷凝,不凝汽体进入第三级喷射器J5811B,混合气体E5825B中冷凝。不凝汽体(尾气)经止回阀、阻火器排入大气。E5824、E5825A/B中的冷凝液流入水封槽V58042。
酮塔回流泵P5822将约20m³/h~56.6 m³/h的回流液从回流槽V5805中送至C5805顶部,部分作为环己酮成品(流量16.9 m³/h左右),经环己酮冷却器E5811排入环己酮贮槽T5803(环己酮质量不合格时改送粗醇酮贮槽T5802),流量由PIR5872指示。C5805塔底环己酮,重组分和少量环己酮由底部产物泵P5821分别送往环己酮塔C5803/C5804 ,该流量约为20.5 m³/h。
Ⅲ醇塔C5804/C5803
C5803和C5804并联用于回收环己酮和环己醇,两塔各负担50%的负荷。为降低塔釜温度,两塔在真空下操作。C5804操作如下:由泵P5821将C5805塔釜物料送至环己醇塔C5804,流量由LIC5871控制在10.28 m³/h左右。从环己醇脱氢分离器S5905约1.1 m³/h未蒸发的醇酮和高沸物送至C5804底部。环己醇蒸发所需的热量由通入再沸器E5812中的高压蒸汽供给,蒸发流量由FIC5852控制。C5804顶部产物经冷凝器E5813和气体冷却器E5814冷却,冷凝液流入回流槽V5803。被环己醇饱和的不凝气体从E5814流往三级抽真空装置X5804。回流泵P5811将约19 m³/h的回流液从回流槽V5803送至C5804顶部。一部分作为塔顶产品送入环己醇贮槽T5804(环己醇质量不合格改送粗醇酮贮槽T5802)。含有少量环己醇和残渣的塔釜产物由P5810送往昌德公司,流量由FIC5853控制在0.4 m³/h左右。C5803操作如下:由泵P5821将C5805塔釜物料送至环己醇塔C5803,流量由FIC5831控制在10 m³/h左右。从环己醇脱氢分离器S59052约1.5 m³/h未蒸发的醇酮和高沸物送至C5803底部。环己醇蒸发所需的热量由通入再沸器E5806中的高压蒸汽供给,蒸汽流量由FIC5826控制。C5803顶部产物经冷凝器E5807和气体冷却器E5808冷却,冷凝液流入回流槽V5802。被环己醇饱和的不凝气体从E5808流往抽真空装置X5803。回流泵P5808将约16 m³/h的回流液从回流槽V5802送至C5803顶部。一部分作为塔顶产品送入环己醇贮槽T5804(环己醇质量不合格改送粗醇酮贮槽T5802)。含有少量环己醇和残渣的塔釜产物由P5807A/B送往昌德公司,流量由FIC5829控制在0.4 m³/h左右。
(9)脱氢反应器R5901
R5901脱氢反应所需的环己醇由脱氢进料泵P5813从环己醇贮槽T5804提取,经脱氢进料预热器E5910,与来自脱氢反应器R5901的环己醇/环己酮蒸汽进行热交换,温度从79℃上升到160℃左右,流量由FIC5901控制在7 m³/h ~10 m³/h左右。进入环己醇蒸发器E5901后,大部分环己醇被蒸发,少量(进料的15%左右)未蒸发的醇酮和高沸物在分离器S5905中与环己醇蒸汽分离,由S5905底部排料管线排入醇塔塔底,流量指示为FIT5911。环己醇蒸汽进入脱氢换热器E5902A/B,与脱氢反应器R5901出来的环己醇/环己酮蒸汽进行热交换,然后从顶部进入脱氢反应器,反应温度为220~250℃。部分环己醇在脱氢催化剂作用下发生脱氢反应,生成环己酮与氢气,脱氢反应后的气体混合物从反应器R5901出来经过E5902A/B换热,然后通过进料预热器E5910和冷凝器E5903、E5904冷却至50℃,醇酮混合冷凝液流入V5905。约1.5的醇酮混合液由泵P5905送至吸收塔C5501的进料深冷器E5504,其余的醇酮混合液由泵P5904经E5819送至干燥塔C5801。E5903、E5904气相部分(主要是氢气及微量醇/酮、环己烯蒸汽)进入分离器S5906,经压缩机K5902/K5903压缩至2300Kpa,送至SEC4000装置。
(10)新脱氢反应器R59012
新脱氢系统是装置扩能改造后,新增的一套相对独立的系统,工艺流程与老脱氢一样,新老脱氢共用氢气压缩系统。老脱氢的生产能力为6万吨/年,新脱氢为8万吨/年。
(11)热油系统
热油系统提供脱氢反应所需要的热量,包括热油炉、热油循环泵,膨胀槽和热油贮槽。氧化低压装置有热油炉3台,其中F5901/F5903两台热值功率75万大卡,F5902热值功率为150万大卡。热油炉燃料均为液化气,液化气由外界分别送入缓冲罐V5906、V59062,V5906由PPV5917控制压力后分别供给F5901、F5902。V59062由PPV59152控制压力后供给F5903。
热油循环泵将经过脱氢反应器壳程换热后的热油送至热油炉,热油在热油炉被加热至260℃左右循环回脱氢反应器。膨胀槽安装在装置三楼,底部有管线和热油循环管相连,顶部通过呼吸阀与大气相通,以保证热油循环管充满热油。新老脱氢热油系统相对独立,但是2套进出热油炉的热油管线间有管线相连,必要时可以互串,用来满足非正常情况下至少一套脱氢反应器的热量供给。
3.2.4 苯加氢工艺流程
<一> 氢气干燥
有制氢装置供来的的氢气经氨气冷却冷凝器冷却后,进入水分离器,分离出冷凝水后
与环乙铜精制装置送过来的氨气混合后再经干燥器进一步用分子筛吸附脱水,然后进入氨气缓冲器,混合缓冲后进入氢气压机。干燥器中分子筛吸水饱和后,利用制氢装置开工压缩机,将稳定塔,制氢装置的开工压缩机以及氢气干燥器切换泄压时放出的气体经在生气加热器用高压蒸汽加热后进入氢气干燥带出分子筛中水分,再经再生气冷凝器进行冷却,再生气冷却器用冷却水冷却,经再生气水分离器分离出水后送至制氢装置开工压塑机入管口,如此循环利用。
<二> 笨干燥
有原料送来的笨经过进料预热器进行初步的加热,预热器为低压蒸汽加热,笨物料加热至80℃后进入笨干燥塔的顶部,笨水混合物在干燥塔内会产生闪蒸,笨水混合物由干燥塔顶部进入冷却器,冷却器内为循环水冷却,经过冷却后的物料流入笨水分离器,在此,笨水分离,底部的水分由现场排水排除,笨则由于重力作用回流至笨干燥塔的顶部。笨干燥塔底部出料至笨干燥塔出料冷却,冷却器内位循环水冷却,冷却后的笨物料进入笨槽和笨泵入口,直接供加氢反应系统使用。
<三> 苯加氢反应系统
干燥处理后的氢气经过氢气压缩机的压缩后,通过主反应器。笨从原料罐区供来,经笨干燥塔干燥后进入笨贮槽。经笨加料泵送入主反应器,回流经笨泵出口冷却器冷却水冷却后,返回笨贮槽。主反应器中的液相物料从主反应器的底部经环乙烷循环泵送入锅炉给水换热器的管程与其壳程内锅炉水进行热交换后,返回主反应器,进行强制式循环。均相催化剂HC402-2由专用槽车运来,然后用氮气压入催化剂槽,经催化剂泵打入主反应器的底部出口循环管内,经循环泵锅炉给水换热器管程后进入主反应器。主反应器中的反应产物以气相方式从主反应器的顶部引出,从装有固相催化剂LD-143的后反应器顶部进入,通过进一步的加氢反应后从后反应器的底部出去进入锅炉给水预热器后进入中温冷却器后,45℃左右的环乙烷气液混合物料进入第一分离器内进行分离,在第一分离器中,未凝的少量环乙烷及过剩氢气以及其他情性气体进入尾气转换器,冷却到40℃后再进入低温冷却器,经低温水在冷却后,进入第二分离器,在第二分离器中气液再次分离,液相部分回流至第一分离器中,气象部分作为冷剂进入尾气换热器,换热后排至制氢装置尾气开工压缩机,作为制氢原料使用。
锅炉水由街区外供来,经锅炉水给水预热器预热后进入汽包,然后再进入锅炉给水换热器中,与主反应器的循环物料进行热交换。锅炉给水以热缸虹吸方式进行循环汽化。汽水混合物在汽包中分离,蒸汽送至脱庚烷塔的再沸器中作为热源使用。
有第一分离器分离过来的液相环乙烷,在进预料热器和经过与稳定塔的再沸器底部流出的环乙烷换热后进入稳定塔,在稳定塔中,环乙烷中的轻组份杂质被蒸出,其冷凝液相部分回流入塔内,不凝气与尾气缓冲罐排除的尾气汇合,送入燃料气管网。
正常生产时,主反应器的外循环泵密封油是笨泵直接供给的。非正常生产时,主反应器的外循环泵所用的密封油是由第一步分离器底部管线引出环乙烷,经由密封油泵,少量供到主反应器外循环泵的机械密封装置进入到泵内,进入反应器,大部分循环回到第一分离器。
3.3己内酰胺制备和精制车间
己内酰胺制备和精制车间包括重排岗位、中和岗位、萃取岗位、离子交换岗位、蒸发岗位、蒸馏岗位和产品包装岗位。
◆重排岗位是制备己内酰胺,其原理如下:肟在酸如硫酸、多聚磷酸以及能产生强酸的五氯化磷、三氯化磷、苯磺酰氯、亚硫酰氯等作用下发生重排,生成相应的取代酰胺,如环己酮肟在硫酸作用下重排生成己内酰胺:
反应机理
在酸作用下,肟首先发生质子化,然后脱去一分子水,同时与羟基处于反位的基团迁移到缺电子的氮原子上,所形成的碳正离子与水反应得到酰胺。
迁移基团如果是手性碳原子,则在迁移前后其构型不变,例如:
◆中和岗位是己内酰胺的除杂同时也是硫胺的制备过程,中和得到的硫胺中含有己内酰胺,用脉冲法出去己内酰胺,在蒸馏得到39%的硫胺液,储存后接入蒸发塔,再重复结晶浓缩,最后得到硫胺产品。
◆萃取岗位可萃取得到70%的己内酰胺水溶液。萃取过程是:先用苯萃取出70%浓度的含杂质己内酰胺,在用水反萃取苯中的己内酰胺,得到35%的己内酰胺溶液,再在102℃解热蒸发35%的己内酰胺,出去其中的水和苯。
◆蒸发岗位是产品的浓缩过程,将原浓度为38~39%的产品浓缩到90%左右。最后用闪蒸的方法得到98%左右浓度的产品。
◆蒸馏岗位是将己内酰胺蒸出,得到产品的步骤。
◆离子交换岗位是为了出去SO42-等无机离子。
3.4 锦纶6聚合工艺车间
3.4.1应用:
锦纶6由于具有良好的性能被广泛用于纺织工业、汽车工业、机械工业、电子电气、日用产品及化工建材业等方面。
民用上可以用来制造服装、食品包装材料、地毯丝、渔网丝、鬃丝等。
工业上可大量用来制造帘子线、印刷胶片、容器、管道、工业用布、缆绳、传送带、机械零部件等。
国防上主要用作降落伞及其他军用织物。
3.4.2 原料简介:己内酰胺 C6H11NO
Ⅰ主要理化性质:
白色晶体或结晶粉末或无色液体,熔点69℃,沸点262.5℃、比重1.023(70℃),手触有润滑感,工业品有微弱的叔胺气味。易溶于水、乙醇、乙醚、氯仿和苯等。受热时起聚合反应。
Ⅱ危害:
◆火灾(急性危害):可燃,在火焰中释放出刺激性或有毒烟雾(或气体)。 预防:禁止明火。急救/消防:泡沫、干粉、二氧化碳、大量水。
◆接触预防:防止粉尘扩散!严格卫生条件!避免青少年和儿童接触!
◆吸入(急性危害):腹部痉挛,意识模糊,咳嗽,头晕,头痛 。预防:局部排气或呼吸防护 。急救/消防:新鲜空气,休息,并给予医疗护理。
◆皮肤(急性危害):皮肤干燥,发红。预防:防护手套,防护服 。急救/消防:脱掉污染的衣服,用大量水冲洗皮肤或淋浴。
◆眼睛(急性危害):发红,疼痛。预防:面罩或眼睛防护结合呼吸防护。急救/消防:先用大量水冲洗十几分钟(如可能易行,摘除隐形眼镜),然后就医。
◆摄食(急性危害):腹痛,腹泻,恶心,呕吐。预防:工作时,不得进食、饮水或吸烟。急救/消防:漱口,不要催吐,并给予医疗护理。
◆溢漏处置:如为熔融态,使其固化(常温下凝结较快)。将溢漏物扫入容器中,可首先润湿防止扬尘。用大量水冲净残余物(额外个人防护:适用于有害颗粒物的P2过滤呼吸器)。
3.4.3聚合方式:
锦纶6的聚合根据开环剂的使用不同,可以分为两种,一种是用碱类物质作为开环剂,称之为碱法聚合,又称快速聚合;一种主要是以水作为开环剂,称之为水解聚合。
碱法聚合的优点是反应速度快,所得产物分子量很高,缺点是反应过程不易控制,产品的平均分子量及分子量分布波动大,不利于大规模的纺丝生产。
水解聚合过程容易控制,分子量分布窄,易于以后的纺丝加工。水解聚合是工业上开发最早,目前普遍采用的方法,是今后PA6生产发展的一个趋势。
己内酰胺聚合反应涉及的主要反应是:
Ⅰ水解开环反应:
该反应为吸热可逆反应,反应速度快。
Ⅱ聚合加成反应:
该反应为可逆吸热反应,升高温度有利于反应的进行。
Ⅲ缩聚反应
该反应为可逆放热反应,缩聚反应决定聚合物的平均分子量,降低温度和压力有利于反应的进行。降低反应压力或抽真空,将反应生成的水蒸发,反应将向右进行。
3.4.4影响产品质量的主要因素
(1)聚合温度
聚合温度是影响聚合反应的主要因素,它对聚合反应的速度,聚合产物中低分子物(单体和低聚物)的含量,聚合产物的平均分子量都有直接影响。
Ⅰ、温度对聚合反应速度的影响
温度升高能增强参加反应物质的活动能力,从而使反应速度加快,使反应达到平衡的时间缩短。
Ⅱ、温度对聚合产物平均分子量的影响
温度升高,使达到平衡时的聚合物粘度下降,即平均分子量降低。这是因为分子链的缩聚与水解反应是一个可逆过程,水解反应是吸热过程,而缩聚反应是放热过程。
当温度升高时,不利于放热反应的进行,故反应向水解方向移动,使产物分子量降低。
Ⅲ、温度对聚合物中低分子物含量的影响
不论采用何种聚合方式,在己内酰胺的聚合产物中总存在着一些可溶于热水的低分子物。水溶性低分子物包括单体及低聚物,统称为可萃取物。
聚合温度越高,单体及低聚物的含量就越多。这是因为己内酰胺聚合时,存在一个聚合物与单体及低分子化合物间的化学平衡,随着温度的升高,该平衡向生成单体及低分子化合物方向移动。
所以在聚合反应达到平衡之前,加压聚合管和减压聚合管上段升高温度有利于加快反应速度,缩短反应时间。而减压聚合管中段、下段降低温度有利于提高聚合物平均分子量,降低低分子物含量。在生产过程中要严格工艺控制,不得随意变动工艺控制指标。聚合温度要求控制稳定,波动大时将影响聚合物质量。
Ⅳ、温度的其它影响
聚己内酰胺的熔融体对热、氧等很敏感,主要是聚合体本身存在着可以裂解的薄弱环节。当温度过高时,聚己内酰胺会发生裂解,能分解出气体,温度在300℃左右(分解点)气体发生急剧增加,这主要由于大分子链上-C-C-和-C-N-链断裂所致。氧的存在能促使热分解进行,使分解温度下降,因此温度越高聚合物对氧越敏感,对防氧要求越高。
(2)聚合时间
随着聚合时间延长,单体转化率和聚合物平均分子量都随着增加,直至平衡。在聚合反应后期,随聚合时间延长分子量分布越趋均匀,这是因为较长的分子链上的酰胺键数目比较短的分子链上的酰胺键数目多,所以解聚的机会也多。聚合过程中,反应速度随时间变化。反应达到平衡所需要的时间,视其它反应条件而定,一般地说,聚合初期温度越高,达到平衡的时间越短。
(3)开环剂
纯净的己内酰胺在绝对干燥的条件下,即使以很高的温度长时间加热也不会聚合。但只要加入少量的水或反应时能生成水的物质,就能使己内酰胺在较低温度下开环聚合。这些能促使己内酰胺开环聚合的物质称为开环剂。
Ⅰ、水的用量对反应速度的影响
a:不论水量多少,反应总有诱导期存在,随着水量的增加,诱导期缩短。
b:随着水量的增加,反应速度也随着增加,从而缩短了达到平衡所需的时间。
Ⅱ、水量对产物平均分子量的影响
己内酰胺开环聚合过程中水量的多少不仅影响反应速度,而且直接影响产物的平均分子量:在反应初期,水量越多,反应速度越快;在反应后期,水量越多,越不利于分子链的进一步增长,从而使产物的平均分子量下降。
(4)分子量稳定剂
对于纺织纤维用的聚己内酰胺的平均分子量,根据纤维品种的不同,有不同的要求。在聚合时,必须使聚合的平均分子量在工艺所要求的数值上稳定下来。从理论上讲可以用改变聚合物中残余水量的办法来控制分子量,但实际上很难做到,而且这样得到的聚合物平均分子量很不稳定。在以后的纺丝等过程中,很容易由于聚合物中含水量的变化而引起平均分子量的很大波动。因此在实际生产中,一般都在聚合时加入一些能封闭这些大分子活性端基的物质来控制平均分子量,这些物质称之为分子量稳定剂。
一般常用的分子量稳定剂是己二酸、醋酸等有机酸,它们的端羧基与聚合体大分子的端氨基作用后,使大分子的两端均为羧基,或为羧基和乙酰基,这样就能阻止大分子链的进一步增长,使聚合体的分子量稳定下来。
聚合物的最终平均分子量与加入的分子量稳定剂的用量有直接的关系。一般在其它条件不变时,稳定剂加入量越大,聚合物的平均分子量越小,反应达到平衡所需的时间越短,这是因为分子量稳定剂同时也有促进开环的作用。
(5)氧
己内酰胺对氧很敏感,被氧化后会生成黄褐色的裂解产物。己内酰胺被氧化的程度与温度、时间、原料中的杂质以及各种添加剂的性质和设备的材质有关。实验表明:
◆在相同条件下温度越高,作用时间越长,己内酰胺被氧化程度越严重。
◆己内酰胺中挥发性物质能加速己内酰胺的氧化。
◆加入碱金属氢氧化物可以对己内酰胺的氧化变黄起抑制作用。
◆加入酸类,特别是无机酸,会大大加速己内酰胺的氧化。
◆铁、铜、银等重金属离子对己内酰胺的氧化起加速作用,特别是在银的存在下,微量的氧也能使己内酰胺氧化。铜离子的存在对己内酰胺氧化的加速作用也较大。
所以不仅在生产过程中采用氮气进行保护,而且对在生产过程中能直接接触到高温物料的设备都要求使用不锈钢做内壁。
(6)聚合管液面控制
在聚合过程中,聚合管液面忽高忽低不但影响了聚合时间,造成聚合物分子量分布不均匀,而且液面下降时粘附在管壁上的聚合物凝结成固状物,当液面再次升高时这些固状物再次进入熔体中形成凝胶,对产品质量造成不良影响,严重时造成后聚管壁物料氧化结块影响装置的稳定连续运行。
总之,己内酰胺水解聚合是一个复杂的过程,影响因素很多。为了得到高品质的产品必须严格按工艺要求操作。
3.4.5萃取原理
萃取过程是切片中可萃取物向水相扩散过程。在尼龙6切片和水的萃取过程中均匀分散于切片中的单体和低聚物,在热水的作用下,靠近切片表面的部分的单体和低聚物首先溶解并进入溶液相主体,留下一层多孔质结构,随后的继续溶解,需要溶剂首先进入孔隙之中,然后再与溶质作用。溶质被溶解之后要借助浓度差作为推动力从内部扩散到切片表面,再进入液相主体。
3.4.6干燥原理
干燥指利用热能,使湿物料中的水分汽化而除去的过程。本装置主要利用热氮气与湿聚酰胺6切片逆向接触,通过传热过程将湿聚酰胺6切片表面与内部的水分除去,同时进行部分固相增粘。
固相增粘:
◆预聚体起始分子量越大,粒子尺寸越小,粒子含水量愈低,可达到的最终分子量愈大。
◆温度越高,反应速度越快,反应温度在180℃以上时,产品呈微黄色,只有反应温度在170℃以下时,产品颜色没有变化,而且切片没有出现黏结现象。
◆尼龙6固相增粘至少需20h才能达到平衡。
◆相同温度下,减压抽真空比连续通N2工艺有较快的反应速度,体系真空度越高,增粘速度越快。
3.4.7聚合车间装置简介:
巴陵分公司己内酰胺事业部聚合车间1号聚合装置系1995年从德国ZIMMER公司引进成套设备技术,采用DCS集散控制系统进行工艺控制,以液体己内酰胺为原料,经过续聚合、造粒、萃取、干燥、切片输送等工序生产锦纶6切片。经过多年的生产实践和摸索,在消化和吸收德国ZIMMER公司的技术的基础上我公司自行设计并建成了一套年生产能力为2万吨的聚合装置。目前我车间聚合装置能生产民用、工业用、高、低粘等多种牌号的锦纶6切片。
3.5 精细车间
3.5.1吸附与吸附剂
(1)吸附现象:
当流体与多孔固体接触时,流体中某一组分或多个组分在固体表面处产生积蓄的现象称为吸附。根据吸附力性质,吸附现象可分为物理吸附与化学吸附。
◆物理吸附:
也称为范德华吸附,它是吸附质和吸附剂以分子间作用力为主的吸附。
◆化学吸附:
吸附质和吸附剂以分子间的化学键为主的吸附。
(2)吸附剂:
在固体表面积蓄的组分称为吸附物或吸附质(adsorbate),多孔固体称为吸附剂(adsorbent)。吸附剂分为天然的吸附剂(如硅藻土、白土、天然沸石等)与人工制作的吸附剂。
人工制作的吸附剂主要有活性炭、活性氧化铝、硅胶、合成沸石分子筛、有机树脂吸附剂等,工业上常用吸附剂为人工制作的吸附剂。工业上常用吸附剂要求为:
◆具有较大的内表面:吸附容量大;
◆选择性高:吸附剂对不同的吸附质具有不同的吸附能力,其差异愈显著,分离效果愈好;
◆具有一定的机械强度:抗磨损;
◆有良好的物理及化学稳定性;耐热冲击,耐腐蚀;
◆容易再生;
◆易得,价廉。
吸附剂物理性能参数
①密度:
◆填充密度rB(又称体积密度):是指单位填充体积的吸附剂质量。
◆表观密度rP(又称颗粒密度):单位体积吸附剂颗粒本身的质量。
◆真实密度r:是指扣除颗粒内细孔体积后单位体积吸附剂的质量。
②比表面积
指单位质量的吸附剂所具有的吸附表面积,㎡/g。吸附剂孔隙的孔径大小直接影响吸附剂的比表面积,孔径的大小可分三类:大孔、过渡孔、微孔。吸附剂的比表面积以微孔提供的表面积为主。
③吸附容量
单位质量的吸附剂所吸附吸附质的质量,它反映了吸附剂吸附能力的大小。吸附量可以通过观察吸附前后吸附质体积或质量的变化测得。
3.5.2双氧水提纯工艺
(1)蒽醌法生产双氧水的原理
国内外情况一样生产H2O2几乎全部采用蒽醌法,巴陵公司生产的供氨肟化装置使用的双氧水也是蒽醌法生产的。
蒽醌法的主要反应原理如下:
①烷基蒽醌(RAQ)氢化产生烷基氢蒽醌(HRAQ)
②烷基氢蒽醌氧化产生烷基蒽醌及H2O2。
注:
◆R为C2-O5烷基,通常多-C2H5,即多用乙基蒽醌(EAQ);也有用戊基蒽醌(AAQ)者。
◆催化剂为钯(钯/载体或钯黑),早期曾用镍(兰尼镍)。
◆RAQ预先溶于混合溶剂中,组成工作液,此工作液在H2O2生产过程中循环利用。
◆所用混合溶剂一般由一非极性溶剂(作为RAQ溶剂)和一极性溶剂(作为HRAQ溶剂)按一定配比组成。
具体溶剂如下:
(a)非极性溶剂:C9-C11高沸点芳烃(AR);
(b)极性溶剂:从下列不同溶剂中选用:磷酸三辛酯(TOP)、醋酸甲基环己酯(MCA)、二异丁基甲醇(DIBC)、氢化萜松醇(HT)、四丁基脲(TBU)
3.5.3工艺简介
(1)双氧水提纯工艺:
27.5%的工业双氧水,用泵送进吸附塔(四个树脂床,相互并联,两两成组,一组投用,一组再生备用),双氧水从树脂床底部进入从顶部流出,按一定流速经过树脂床与树脂接触,由于树脂的吸附作用双氧水中的蒽醌、重芳烃等有机物被树脂吸附截留下来,通过树脂吸附后的双氧水大幅下降,纯度提高作为产品外送其他车间使用。为了树脂床不存在短路、串流现象,确保双氧水纯度,树脂床上下端安装有大量水帽,确保双氧水分布均匀,同时起到拦截树脂流失作用。为防止破损树脂进入下道工序,纯净双氧水送入下道工序前经过一个金属烧结式过滤器进行过滤。
(2)树脂再生工艺:
树脂吸附容量有限,当出口TOC≥100PPm(产品质量要求),树脂床按要求退出运行,进行再生。甲醇对蒽醌、重芳烃有很好的溶解效果,甲醇浸泡树脂,树脂吸附的蒽醌等有机物溶于甲醇中。多次甲醇浸泡,吸附中杂质溶于甲醇,恢复树脂吸附能力。
(3)甲醇回收工艺:
再生树脂后的粗甲醇中含有少量蒽琨、重芳烃、水。甲醇沸点远远低于蒽醌、重芳烃、水等杂质。利用沸点差特性,采用填料精馏塔以低压蒸汽为热源,实现甲醇与蒽醌、水、重芳烃的分离,纯度达98%以上甲醇蒸汽从塔顶出来在塔顶冷凝器与循环水换热冷凝为甲醇溶液,其他重组分残留在塔底定期外排。控制顶温与回流液纯度确保甲醇质量。
4、各车间工艺流程图
目录
1、 目的与要求............................................................................................................... 1
1.1 目的................................................................................................................... 1
1.2 要求................................................................................................................... 1
2、实习指导思想.............................................................................................................. 2
2.1 指导思想............................................................................................................ 2
2.2 实习进度安排..................................................................................................... 2
2.3实习地点:巴陵石化分公司己内酰胺事业部。..................................................... 2
3、 实习内容................................................................................................................... 2
3.1 入场教育............................................................................................................ 2
3.1.1 安全教育................................................................................................. 2
3.1.2 己内酰胺事业部简介................................................................................ 2
3.1.3 行为要求《十不准》................................................................................ 3
3.1.4 主要危险化学品危害及相应的安全控制措施............................................. 3
3.2 环己酮工艺车间................................................................................................. 4
3.2.1 制氢装置工艺车间................................................................................... 4
3.2.2 环己烷氧化高压装置车间....................................................................... 29
3.2.3 环己烷氧化低压车间.............................................................................. 42
3.2.4 苯加氢工艺流程..................................................................................... 50
3.3己内酰胺制备和精制车间................................................................................... 52
3.4 锦纶6聚合工艺车间......................................................................................... 53
3.4.1应用:.................................................................................................... 53
3.4.2 原料简介:己内酰胺 C6H11NO................................................................ 53
3.4.3聚合方式:............................................................................................. 54
3.4.4影响产品质量的主要因素........................................................................ 55
3.4.5萃取原理................................................................................................. 58
3.4.6干燥原理................................................................................................. 58
3.4.7聚合车间装置简介:............................................................................... 58
3.5 精细车间.......................................................................................................... 58
3.5.1吸附与吸附剂.......................................................................................... 58
3.5.2双氧水提纯工艺...................................................................................... 60
3.5.3工艺简介................................................................................................. 60
4、各车间工艺流程图..................................................................................................... 61