全国炼钢----连铸生产技术会总结
会议地点:唐山
会议时间:7月9日、7月10日
参会人:炼钢厂:王文辉; 技术中心:付长亮
大会报告内容如下:
由于大会报告内容比较多,且设立分会场,因此重点关注热门领域的报告,将报告总结为部分企业概况、热门技术和几点思考三个部分。部分大会报告的具体内容可参见PDF电子文档。
一部分企业装备及生产概况
1、首钢京唐公司
2台550m2烧结机;4座70孔焦炉;2座5500m3高炉;2座KR脱硫装置;2座铁水脱磷预处理专用转炉;3座脱碳炼钢转炉;4台大型板坯连铸机;2250mm和1580mm热连轧机各一套;2230mm、1700mm和1420mm冷连轧机组各一套;设计年产904万吨钢。
2、宝钢
3、武钢条材总厂
武钢条材总厂是20##年6月由原一炼钢厂、大型轧钢厂、棒材厂,20##年2月加入CSP厂组建而成。
原一炼钢厂成立于1958年,于1998年实施“平改转”改造。现拥有2座铁水脱硫站、2座120吨转炉、3座LF炉、1座双工位RH真空炉、3台奥钢联五流方坯连铸机等工艺装备,生产200mm—480mm各类规格方坯,年产能230万吨,主要为轨梁线、高线和棒材分厂提供优质方坯原料。
高速线材生产线组建于1996年,主要生产钢帘线、弹簧钢、冷镦钢、焊丝钢等品种,年设计产能70万吨。
棒材分厂地处于汉阳,于1996年从汉钢剥离后划归武钢股份,主要产品规格为Φ10—40mm建筑用螺纹钢筋及各类圆钢。开发有工业纯铁、轴承钢、齿轮钢、弹簧钢等,年设计产能80万吨。
CSP分厂成立于20##年,产品最薄规格厚度为0.8mm,最大宽度为1600mm;年产钢材248万吨。2套三工位170t铁水脱硫站、2座150t转炉、2套150t LF钢包精炼炉、1套150t RH真空装置(另预留1套)、2台薄板坯连铸机、2座辊底式隧道炉、1座七机架轧机、1套层流冷却设备、1条运输链及1条精整线等。
4、鞍钢
包括鞍山本部股份公司、朝阳鞍凌公司、鞍钢股份鲅鱼圈分公司、成都钢钒公司、攀枝花钢钒公司、西昌钢钒新钢业公司。
转炉 17座(100-260t);LF 12座(80-260t);RH 9座(100-260t);ANS 2座(180、260t);VD 2座(100t);方圆坯 4台(120-380mm);板坯 12台(135-300mm。
5、马鞍山钢铁
马钢第一钢轧厂圆坯生产线:120t转炉→110tLF精炼→95tVD→3机3流圆坯连铸机,规格Φ380mm、Φ450mm,主要产品为车轮轮箍用钢、高压锅炉管用钢、环件用钢等,年产30万t。
马钢特钢生产线:110t电炉→120tLF炉→120RH炉→5机5流圆坯连铸机,规格有Φ380mm、Φ450mm、Φ600mm,主要产品为轨道交通用钢、石油用钢、汽车用钢、风电环件用钢、高压锅炉管用钢、工模具用钢、高端制造用钢等。
6、淮钢
生产流程:90t转炉→90tLF精炼炉→100tRH真空精炼→6机6流方坯连铸、6机6流圆坯连铸。规格有Φ380mm、Φ450mm、Φ500mm、Φ600mm断面,典型钢种:37Mn5、42CrMo4V、4130X、15CrMoG、12Cr1MoVG、SA210C、36Mn2V、45Mn2、35CrMo、X42、Q345E等。
二热门技术
1、首钢京唐的洁净钢生产工艺技术
首钢京唐选用铁水包多功能化技术、更高脱硫效率的KR铁水处理工艺、国内首次采用铁水脱磷预处理和脱碳转炉少渣冶炼(简称脱磷转炉+脱碳转炉冶炼工艺)、高循环速率RH炉外精炼装置、高拉速板坯连铸。
(1) KR铁水脱硫预处理
Ø 采用铁水包多功能化技术 (高炉铁水称量-运输-脱硫-装炉“一包到底”工艺);
Ø 炼铁厂与炼钢厂之间布局紧凑,加之不对铁水进行转兑,铁水温降得到了有效控制;
Ø KR进站铁水温度平均为1386℃,为提高脱硫预处理效率提供了十分有利条件。
(2)脱磷转炉冶炼
脱磷转炉装入量为320t左右,废钢比8%左右,氧枪供氧强度在1.4Nm3/min/t,炉底设有16个双环缝式喷口吹入N2搅拌,底吹气体流量控制在0.25Nm3/min/t,脱磷转炉吹炼时间在7min左右,冶炼周期平均为22.8min。
京唐公司铁水磷含量在0.080~0.145%之间,经过脱磷转炉冶炼,铁水磷绝大多数降至0.02~0.05%范围内(平均为0.033%),从而可减轻脱碳转炉冶炼负担,为缩短脱碳转炉炼钢周期和生产洁净钢发挥重要作用。
(3)脱碳转炉冶炼
该转炉既可以对脱磷转炉冶炼后的铁水进行脱碳炼钢,也可以对常规铁水进行冶炼。脱碳转炉基本为全铁水冶炼,装入量为310t左右,出钢量294t左右,氧枪供氧强度为3.0 Nm3/min/t,炉底有8个环缝式底吹喷口吹入N2/Ar进行搅拌,底吹强度为0.05 Nm3/min/t左右。
由于之前脱磷转炉脱除了70%左右的磷,在统计2797炉次中,终点钢水磷含量≤0.01%炉次超过60%。通过适当增加脱碳转炉石灰用量,采用合理氧枪枪位和供氧强度等,可稳定将钢水的[P]降低至0.006%以下。此外脱碳转炉冶炼终点的碳氧积[%C][%O]平均为0.00231,显著低于常规冶炼工艺的0.0026。
就生产周期而言,经过脱磷处理的铁水,其碳、硅、磷含量较常规铁水降低,脱碳转炉吹炼时间缩短,加之脱碳转炉不装废钢、溅渣护炉也较短,其冶炼周期相比常规转炉冶炼减少5min左右。
(4)炉外精炼
Ø 两台CAS-OB:用于普通低、中碳热轧品种,应用比例占全品种的20%;
Ø 1台双工位LF:用于超低硫、极低硫含量控制的低合金高强度钢,如管线、工程机械等,占全品种的27%;
Ø 两台双工位RH:用于汽车、家电、镀锡板的低碳、超低碳钢及部分低合金高强度钢,应用比率在53%。
(5)高拉速连铸
4台板坯连铸机,1#和3#配有电磁制动的FC结晶器,用于汽车板、家电板等冷轧钢种,拉速能达到2.0~2.5m/min。2#和4#没有装备FC结晶器,主要用于中碳、低合金高强度钢等热轧钢种。
2、包钢干式VD
包钢于20##年对其1#100tVD抽真空系统进行干式抽真空改造,是国内首家将干式抽真空系统应用于VD真空精炼炉的企业。20##年在新建的VD上也采用干式抽真空系统。
(1)干式真空泵和蒸汽喷射泵的定义、原理和优缺点
定义:干式真空泵很早就出现了,但没有明确的定义,就代替油封式机械泵来说,一般通用的说法是:能在大气压到l0-2Pa的压力范围内工作,在泵的抽气流道(如泵腔)中不能使用任何油类和液体、排气口与大气相通,能连续向大气中排气的泵,即称为干式真空泵(也称为无油机械真空泵)。蒸汽喷射真空泵是利用流体流动时的静压能与动能相互转换的气体动力学原理来形成真空。
原理:干式真空泵系统(VPS)是采用干式机械泵组成的系统,因此,它不需要蒸汽和大量的水,运行成本极低。VPS需要除尘器过滤掉进入机械泵组内的颗粒粉尘以满足泵组对环境的要求。干式真空泵系统主要由一台过滤器和多台(1#13台、4#16台)机械泵组成,过滤器为旋风布袋式除尘器,在干泵组中有两种机械泵:螺杆泵和罗茨泵。
优缺点:
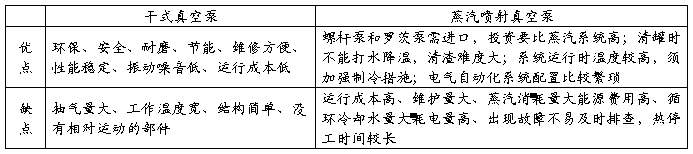
(2)使用效果
炼钢厂1#干式VD从20##年1月至3月期间,共热试了40炉钢,钢种分别为36Mn2VT、34Mn6和36MnVT。1#VD进入深真空时间、深真空时间、真空度分别为:5'03"、13.9'和0.011kpa,达到了保证值要求。VD后氢、氧、氮含量分别为:2.42ppm、14.5ppm和36.3ppm。可见,1#干式VD的脱气效果与原蒸汽喷射VD比较基本相当。
炼钢厂4#干式VD热试从20##年4月3日开始到5月23日止,共计抽真空炉数130炉,其中含钢水抽真空炉数有69炉,空罐抽真空炉数有61炉。进入深真空时间最短6min、最长21min、平均8.4min;真空度最小0.244mbar、最大1.014 mbar、平均0.3mbar,没有达到保证值要求。
干式真空泵在1#VD应用结果表明:经过干式VD系统处理后,预抽时间及VD后钢水中的气体含量基均能达到保证值要求,且脱气效果与原蒸汽喷射VD比较基本相当。4#干式VD由于真空罐干燥的不是太好等方面原因,进入深真空时间还较长,达不到保证值要求,因此需要继续用热罐烘烤或含钢水抽真空,以便进一步考察其效果。
3、福建三钢滑动水口挡渣
福建三明钢铁公司炼钢厂于20##年首先研发,申请专利并用于生产,显示了良好的挡渣效果,可大幅度降低出钢脱氧过程中的合金消耗和降低精炼工序的负荷。很快受到生产板材和高合金比钢种为主的钢厂的关注和采用,取得了良好的效益。目前较先进的钢厂滑板寿命已可达24~26次,一般的寿命也都在10次以上,可以和板坯连铸机的连浇炉数匹配;更换时间最短已可小于10分钟,钢包内渣层厚度可降至25~40mm。
工作原理:在转炉出钢口末端设计闸阀系统,与自动下渣检测系统相结合,通过执行系统,采用液压控制的方式开启或关闭闸板,通过上下闸板之间流钢孔的错位实现挡渣的目的。
(1)滑动水口挡渣的技术内容
Ø 挡渣闸阀设计
采用轮式滑动框的门式机构,主要特点:闸阀机构在线整体更换、离线更换机构闸板砖及检修调试,减轻劳动强度,缩短更换时间。工作原理是通过水冷油缸推动轮式滑动框,开启或关闭下闸板,达到出钢和挡渣目的。由于闸阀机构要能够承受高温烘烤,不严重变形,为此机构本体选择抗氧化,耐热性较好的钢件。
Ø 耐材材质与寿命选用
耐火材料是转炉出钢口闸阀系统中的关键性材料,其材质的合理选定是出钢口闸阀系统安全使用的重要保证。出钢口闸阀机构用的耐火材料由出钢口砖、内水口砖、内闸板砖、外闸板砖和外水口砖五块砖组成,同时砖与砖间采用凹凸连接方式。目前耐材寿命基本按出钢口龄≤130炉、内水口≤60炉、滑板≤13炉组织生产,即能保证安全运行,又能满足三钢的生产节奏需求。
Ø 自动下渣检测
注流含渣百分比曲线采用近红外热像仪、远红外热探测仪对注流热成像,并实时采集转炉生产过程中相关的工艺参数,包括:开氧信号、吹氧时间、转炉倾角等,在出钢时对注流热图像进行图像处理,当图像处理系统检测到注流含渣百分比超过设定值,触发控制系统控制液压机构关闭闸阀,注流含渣量变化曲线如下图所示。
Ø 液压快速驱动
设计时主要考虑油缸的耐热性能
Ø 机构快速更换
机构初定位时间决定了机构整体安装时间,经过不断改进,机构初定位方式经历了从圆柱体定位---圆锥体定位---底部定位桩+半圆椎体定位。
Ø 出钢自动控制
转炉出钢初期下渣量约占流入钢包总渣量的15%,出钢后期下渣量约占总下渣量的65%,出钢完毕转炉复位时的下渣量约占总下渣量的20%。要实现无渣出钢,必须解决各阶段的挡渣任务。
(2)滑动水口挡渣的使用效果
Ø 机构使用情况

机构更换时间

Ø 事故率
1#百吨转炉至20##年使用至今,合计共发生2次由于滑板问题导致的停炉事故。
Ø 挡渣成功率
滑动水口自动+手动挡渣成功率100%(采用滑动水口自动挡渣成功率大于97%),分别比挡渣塞挡渣提高约11.9%,比挡渣球挡渣提高约29.9%。
Ø 下渣量
采用滑动水口挡渣,与使用挡渣塞挡渣和挡渣球挡渣,渣层厚度分别减少了5.8mm和20.3mm,下渣量分别减少了1.5kg/t和3.2kg/t。
Ø 钢水回磷量
普钢(钢种Q235为例)采用滑动水口挡渣钢水回磷量约13.6ppm,分别比挡渣塞挡渣降低3.4ppm,比挡渣球挡渣降低26.4ppm。优钢(以ML08Al为例)采用滑动水口挡渣钢水回磷量约21.1ppm,比挡渣塞挡渣降低10.0ppm。
成分分析
转炉滑动水口挡渣的运行成本合计为2.36元/吨钢。
冶炼HRB400E钢采用滑板挡渣与挡渣塞挡渣对比,硅锰节约1.26元/吨钢,硅铁节约0.23元/吨钢,扣除合金进入钢水中的合金残余铁引起的成本差异0.14元/吨钢,合金节约成本为1.26+0.23-0.14=1.35元/吨钢,则使用滑动水口挡渣综合效益1.35+0.98-2.36=-0.03元/吨钢。(挡渣塞挡渣总承包成本0.98元/吨钢)
冶炼优质钢(ML08Al)采用滑板挡渣与挡渣塞挡渣对比,铝锰节约0.8元/吨钢,铝线节约3.32元/吨钢,扣除合金进入钢水中的合金残余铁引起的成本差异0.11元/吨钢,合金节约成本为0.8+3.32-0.11=4.01元/吨钢,则使用滑动水口挡渣综合效益4.01+0.98-2.36=2.63元/吨钢。
4 唐钢转炉“留渣-双渣”少渣炼钢
(1)“留渣-双渣”少渣工艺的发展
国外:1979年,日本新日铁室兰厂开发了脱硅铁水在转炉内的小渣量冶炼,即SMP法。1983年,神户制钢开发了石灰和苏打粉联合预处理铁水的OLTPS法。由此,开创了转炉少渣冶炼的发展历程。
国内:首钢京唐公司300t转炉:“双联法”操作,脱磷炉与脱碳转炉,生产P≤0.005%钢种。
演变:首钢公司从20##年开始,在首钢首秦和迁钢分别连续试验单转炉“留渣-双渣”操作,取得较好的效果,目前首钢集团首钢长治、首钢水钢均推广应用“留渣-双渣”少渣炼钢操作工艺,工艺相对成熟。
唐钢长材部转炉炉容为50t,炉容比0.75t/m3,供氧强度为4.2 Nm3/min/t,吹氧时间为12min,转炉冶炼周期25min,20##年以来逐步摸索“留渣-双渣”少渣冶炼。
(2)转炉“留渣-双渣”少渣冶炼留渣条件
①大渣量:溅渣后炉内渣量40-60kg/t;②高碱度:前一炉终渣碱度为2.5-3.0;③高FeO,吹炼前期FeO含量在15~25%;④低温:吹炼前期温度在1300~1400℃。
是否要留渣还要根据上一炉的重点情况、本炉生产节奏、冶炼钢种的需要、铁水废钢条件选择性留渣。如上一炉最高温度大于1700℃,终点碳含量小于0.03%,即高温后吹钢水,终渣FeO过高,转炉在炉渣改质和固化后处理不好极有可能引发装铁大喷;铁水Si大于0.7%时,因渣量较大,R偏低,不易留渣。
(3)工艺实践情况
对双渣操作时的20炉钢进行半钢倒渣温度、半钢磷含量、脱磷率及重点一次拉碳情况进行分析。
半钢温度在1350~1470℃之间,当半钢温度在1410左右时的半钢脱磷率最大。主要因为温度低时脱磷的动力学条件变差,而温度高时脱磷反应速率降低。
双渣法倒渣时Lp平均为60.83,双渣法终点Lp平均为226.27,而单渣法终点Lp为177.54。
双渣MgO含量超过10.5%时,渣中P2O5呈下降趋势,可以解释为当MgO含量小于10%时,可以增加C2S在液态渣中饱和溶解度,使渣在较高碱度情况下也可以保持流动性较好的液渣而不析出固相C2S。
(4)存在的问题
初期存在的问题:①前期温度控制,由于铁水物理热、化学热;废钢加入量,供氧强度,枪位等多种因素影响,选择吹氧时间倒渣时机不好掌握,倒渣时温度控制区间大;②各摇炉工双渣操作手法没有规范同一的操作方法,双渣效果差距较大,倒渣量也不充分,半钢脱磷率从28%到65%,需要进一步摸索实验;③倒渣带铁对半钢倒渣的渣样进行破碎,磁选,含铁量(铁单质+铁氧化物)为28%~47%,倒渣带铁量较大,渣铁分离不彻底。
冶炼周期问题:双渣时开氮气吹渣及倒渣要增加时间,冶炼周期相比单渣法要延长5min左右。
吹炼后期脱磷困难:部分“留渣-双渣”炉次操作过程控制失误,导致转炉终点P过高,达0.030~0.040%,且处理比较困难。原因:a)双渣倒渣效果不好。包括双渣前吹炼升温速度过快、倒渣量较少等,前期脱磷效果不好。b)渣量减少。“留渣-双渣”炉次实施双渣倒渣后,至终点炉内渣量为70~80kg/t钢,常规单渣工艺终点炉内渣量为100-110kg/t钢,渣量减少,渣中磷含量增加,实测“留渣-双渣”法终点渣中P2O5为3.68%,单渣法终点渣中P2O5为3.14%,渣中P2O5浓度增加导致4CaO·P2O5也增加,在终点温度较高、渣量较少的条件下,易导致脱磷困难。
双渣时渣铁分离效果不稳定:在前期操作不好情况下双渣倒渣带铁以铁珠为主,带铁最高可达50.28%,终点倒渣以FeO为主,带铁最高为38.0%,折算倒渣带铁最高达32.40kg/t。钢铁料消耗较大。
(5)经济指标
①造渣料单耗降低,由65.29kg/t降低至47.82kg/t;②钢铁料消耗降低,综合对比“留渣-双渣”炉次和常规单渣炉次,钢铁料降低2.51 kg/t;③氮气消耗量增加,与单渣消耗相比,但其量消耗增加了20m3/t。
5 唐钢小方坯火焰切割缩小切口
唐钢第二钢轧厂切割嘴改造前的铸坯割口一般为5~6mm。把切割嘴切割氧通道喉口降低至2.1mm、切割氧压力调整到1.3Mpa,割口降低到4mm;把切割嘴切割氧通道降低至1.9mm、氧压力调整到1.35Mpa时,割口降低到3.5mm。但切割氧压力的提高增加了喉口的磨损,降低了切割嘴的寿命。

(1)技术改造实施过程
在原切割嘴的基础上,用机床把混合气通气孔出气端打通,形成一个一定深度的环形混合仓。改造前预热燃烧气是从七个小孔中喷射出来,气流之间有很宽的气隙,很容易与周围空气形成紊乱的气流,不利于中心切割氧长距离保持束状喷射。
(2)改造后效果
增设混合仓后,均匀的高温燃烧气体,避免了周围空气的卷入,提高了燃烧气体的温度,缩小了燃烧气体的范围,使预热的范围更精准,割口降低到3.1mm以下。高温气流的稳定,减少了钢花的喷溅,有效避免了切割过程中切割嘴被钢瘤堵塞的现象,提高了切割嘴的寿命。
改造后割口平均可降低2mm,割口降低1mm,唐钢第二钢轧厂每年就可从割口这一项降低450多吨铸坯消耗。按此计算每年可为减少铸坯消耗900吨。按照铸坯和废钢渣的差价为600元每吨,每年可增效54万元。
6 唐钢中厚板边裂控制
唐山中厚板公司生产普碳、低合金、船板、高碳、含B钢、压力容器等钢种,生产断面主要为250*2000mm、220*2000mm的铸坯,轧制板材厚度6-120mm,宽度20##-2800mm。边裂是中厚板生产的主要质量缺陷之一,主要原因是连铸坯角部表面的横微裂,经过轧制变形后,出现边部锯齿状裂纹和边部烂边。
通过系统研究了各项工艺参数对铸坯边裂缺陷的影响,形成了减少扇形段漏水、避免高温浇注、提高连铸二冷矫直温度、降低振动台的偏摆量等一系列行之有效的控制连铸坯边裂的工艺技术,明显减轻了板坯角部横裂纹缺陷,提高了铸坯质量,板材边裂由0.59%降低到0.15%。但不能杜绝边裂,为了彻底消除了因连铸坯角部横裂纹缺陷引起的板材边裂缺陷,试验矫直区增加水量的冷却制度,收到了较好的效果。
具体措施:减少扇形段漏水;减少振动偏摆量;合适钢水温度,实行15~25℃的过热度控制,坚持恒拉速,稳定结晶器液位波动;提高保护渣的碱度,保护渣析晶率增加,增大拉坯阻力,传热均匀,减轻铸坯振痕深度和铸坯边裂发生;控制钢中[Al]和[N]的含量,唐钢中厚板实践钢中[Al]含量控制在0.015%左右;提高钢水洁净度;控制矫直温度。
控制矫直温度采取过两种方法:热行法;冷行法。
热行法:中厚板公司前期采用弱冷方式控制边裂,;结晶器水量降低;3-8段两侧边部水嘴堵塞;弯曲段加装导水板;弯曲段两侧水嘴由原来的90°改为65°的小喷嘴和幅切阀门,使得弯曲段铸坯边部30mm处无水等措施,板材边裂不合格品由原来的0.59%降低到0.15%,降低了74.6%,效果比较明显。
冷行法:中厚板公司的边裂缺陷通过“热行”法得到有效控制,但未彻底的解决。为此该厂试验加强角部冷却,降低矫直区铸坯的角部温度,使角部温度降至低于该钢种第Ⅲ脆性温度区间的下限温度,即“冷行”法。把内弧水量由原来的29L/min提高到270L/min,外弧水量由原来的54L/min提高到450L/min,铸坯进入矫直区前温度为670-710℃,通过铸坯酸洗边裂明显减少,板材边裂不合格品由原来的0.15%降低到0.02%,降低了0.13%,边裂基本得到消除。
三几点思考
(1)在改进工艺技术、开发产品的基础上,首先要保证现有工艺及产品质量良好,重点要保证产品质量的稳定和可靠,其关键就是要精细化操作,抓好生产过程中的每一个环节,保证生产过程稳定和规范。
(2)过多的LF精炼控制对保证钢水的洁净度有着不利影响,LF精炼在我厂炼钢过程起着承前启后的作用,但从观念上应该不要去依赖LF,尽量提前完成各项指标,尤其是钢水氧含量应在LF前做到最低。
(3)“双渣-留渣”少渣操作能够降低渣料消耗、降低钢铁料消耗,在许多钢铁厂得到推广,目前我厂已经将其作为转炉冶炼工艺措施,需进一步进行摸索,深入挖潜增效。
(4)转炉滑动水口的应用能够提高挡渣效果,对钢水质量的提高有很大好处,该技术在福建三钢得到较好的应用。就品种而言,普钢生产成本会增加,优质钢采用滑动水口成本会降低;此外,滑动水口在国内的应用尚不完全成熟。但是,改进滑板结构、提高滑板寿命、克服当前滑板不足仍应深入研究。
(5)缩小我厂铸坯火焰切割割口是需要思考的一项工作,该技术可以降低切割铁损、降低成本,同时可提高铸坯断面平整度、减小铸坯切割流。
(6)中厚板边角裂纹的控制、尤其是含B钢角部裂纹控制是板坯生产的一项重要工作,唐钢采用的“冷行法”虽然可以消除边角裂纹,但设备要求比较苛刻,“热行法”依旧是多数钢铁厂公认的有效措施,在此方面应进行深入工作。