生产实习报告
学 院: XX学院
专 业:机械设计制造及其自动化
班 级: XXXXXXXX
学 号: XXXXXXXXXXXX
学生姓名: XXXXX
指导教师: XX XX
20##年 7月
贵州大学明德学院本科生产实习
诚信责任书
本人郑重声明:本人所呈交的生产实习报告,是在导师的指导下独立进行研究所完成。报告中凡引用他人已经发表或未发表的成果、数据、观点等,均已明确注明出处。
特此声明。
作者签名:
日 期:
目 录
一、 生产实习的目的与意义....................................... 1
二、 生产实习单位介绍........................................... 1
三、 安全教育的目的与意义....................................... 2
四、 实习工段介绍............................................... 3
1.轴类车间--连杆............................................. 3
2.轴类车间--曲轴............................................. 4
3.轴类车间--凸轮轴........................................... 5
4.大马力--缸盖............................................... 8
5.箱体车间--4H缸体......................................... 10
6.机修车间--机械磨锋........................................ 12
7.dCi11--车间大马力机加..................................... 14
8.装试车间--大马力装配...................................... 16
9.车身厂--车身............................................. 18
10.再造车间--再造........................................... 18
五、 课程学习................................................. 19
1.数控加工工艺............................................. 19
2.企业6S管理.............................................. 20
3.连杆加工工艺............................................. 23
4.曲轴加工工艺............................................. 24
六、实习总结与心得............................................ 25
生产实习报告
一、 生产实习的目的与意义
1.通过生产实习,可以进一步巩固和深化所学理论知识,并将理论与实践相结合,在实践中提高学生观察问题、分析问题以及解决问题的能力。为后续专业课学习、毕业设计打下良好基础。
2.通过生产实习,使学生进一步接触社会、认识社会,提高社会交往能力,学习工人师傅和工程技术人员的优秀品质和敬业精神,培养学生的良好专业素质,为今后从事工程设计工作打好基础。
3.熟悉主要典型零件(柴油机机座、机体、曲轴、凸轮轴、齿轮等或减速机箱体、传动轴、齿轮等)的机械加工工艺过程,了解拟定机械加工工艺过程的一般原则及进行工艺分析的方法。
4.参观工厂的先进设备及特种加工,以扩大学生的专业知识面以及对新工艺、新技术的了解。
二、 生产实习单位介绍
东风汽车公司始建于1969年,是中国汽车行业骨干企业之一。公司主要业务分布在十堰、襄阳、武汉、广州四大基地,形成了“立足湖北,辐射全国,面向世界”的事业布局。公司总部设在“九省通衢”的武汉。主营业务涵盖全系列商用车、乘用车、发动机及汽车零部件和汽车水平事业。公司现有总资产732.5亿元,员工12.4万人。20##年销售汽车132.1万辆,实现销售收入1969亿元,综合市场占有率达到14.08%。在国内汽车细分市场,中重卡、SUV、中客排名第一位,轻卡、轻客排名第二位,轿车排名第三位。20##年公司位居中国企业500强第20位,中国制造企业500强第5位。“东风”品牌,20##年入围《中国品牌价值研究院》主办的“中国品牌500强”榜单,位列第50位。
经过39年的发展,公司已经构建起行业领先的产品研发能力、生产制造能力与市场营销能力,东风品牌早已家喻户晓。在科学发展观的指引下,公司的经营规模和经营质量快速提升,公司也相应确立了建设“永续发展的百年东风,面向世界的国际化东风,在开放中自主发展的东风”的发展愿景,提出了“打造国内最强、国际一流的汽车制造商,创造国际居前、中国领先的盈利率,实现可持续成长,为股东、客户、员工和社会长期创造价值”的事业梦想。如今,公司12万多员工正在为这一愿景和事业梦想而努力奋斗。展望未来,东风公司一定会在新的发展阶段,为广大用户提供更多的优质产品和服务,为社会、为国家、为中国汽车工业做出更大的贡献。
东风公司构建了完整的研发体系,在研发领域开展广泛的对外合作,搭建起全系列商用车、乘用车、校车研发平台及其支撑系统,进一步完善了商品计划和研发流程。东风将在消化、吸收国内外先进技术的基础上不断强化自身研发能力,提升核心竞争力。
瞻望前程,东风公司已经确立了“建设一个永续发展的百年东风,一个面向世界的国际化东风,一个在开放中自主发展的东风”的发展定位。公司将紧紧抓住中国全面建设小康社会和国内汽车市场持续走强的历史性机遇,力争通过五年的奋斗,实现产销规模、经营效益和员工收入三个翻番,企业综合实力稳居行业领先,东风品牌跻身国际。把东风建设成为自主、开放、可持续发展,并具有国际竞争力的汽车集团。
三、 安全教育的目的与意义
安全教育是安全管理工作的重要环节。安全教育的目的是提高全员的安全意识,安全管理水平和防止事故发生,实现安全生产。
安全教育是提高全员安全素质,实现安全生产的基础。通过安全教育,提高企业各级生产管理人员和广大职工搞好安全工作的责任感和自觉性,增强安全意识,掌握安全生产的科学知识,不断提高安全管理水平和安全操作水平,增强自我防护能力。有些领导在布置全产时往往在布置生产结尾时谈到安全问题,顺使喊一句"最后强调一个问题,就是大家要重视安全生产,不要出事故"。还有的讲,"我是逢会必讲要大家注意安全"。正确的说这些仅仅是提醒,没有深入进行针对性的布置。这些现象的原因,
1.是安全意识不高,对安全在经济效益中的作用和地位认识不足;
2.是缺乏安全知识,难以提出具体意见。要改变这一状况,必须使安全教育经常化、制度化。使广大职工广泛掌握安全技术知识和安全操作技能,端正对安全生产的态度,才能减少或消灭事故,实现安全生产。
安全工作是与生产活动紧密联系的与经济建设、生产发展,企业深化改革,技术改造同步进行,只有加强安全教育工作才能使安全工作适应形势的需要。如企业实行承包经营责任制,促进了经济发展。但是,一些企业在承包中片面追求经济效益的短期行为,以包代管,出现拼设备、拼体力、违章指挥、违章作业。其主要原因是安全教育培训没有跟上,安全意识淡薄、安全素质差。因此,在新的形势下,强化安全教育是十分必要的。
四、 实习工段介绍
1 轴类车间--连杆
连杆是发动机的重要零件。它的作用是连接曲轴和活塞,把作用在活塞顶面的膨胀气体所作的功传给曲轴,推动曲轴旋转,从而将活塞的往复直线运动转变为曲轴的旋转运动,又受曲轴的驱动而带动活塞压缩气缸中的气体。
图片如下:
(1) 连杆材料
连杆采用的材料一般是优质碳素钢或合金钢,如45钢、55钢、40Cr、40MnB等。
(2) 连杆的工艺特点
外形复杂,不易定位;连杆的大、小头是由细长的杆身连接,故刚性差,易弯曲、变形;尺寸精度、形位精度和表面质量要求高。
工艺流程
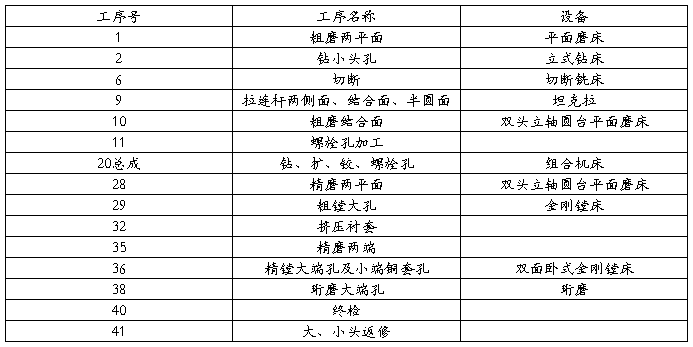
2 轴类车间--曲轴
曲轴:
功用及结构特点:曲轴与连杆配合将作用在活塞上的气体压力变为旋转的动力,传给底盘的传动机构。同时,驱动配气机构和其它辅助装置,如风扇、水泵、发电机、机油泵等。曲轴由主轴颈,连杆轴颈、曲柄、平衡块、前端和后端等组成。曲轴前端装有正时齿轮,驱动风扇和水泵的皮带轮以及起动爪等。东风商用车厂生产的EQ6100、6102曲轴均为整体式结构。6102曲轴为附带整体后油封结构。
材料:曲轴常用材料有:球墨铸铁、调质钢、非调质钢。
对于汽油机曲轴,由于功率较小,曲轴毛坯一般采用球墨铸铁铸造而成,常用材料有:QT600-2、QT700-2、QT800-2、 QT900-6、 QT800-6、等温淬火球铁(ADI球铁)等。
柴油机曲轴毛坯一般采用调质钢或非调质钢,调质钢常用材料有:45、40Cr或42CrMo ;非调质钢常用材料有48MnV 、C38N2、38MnS6。
热处理加工:
第一工序:淬火
1、零件表面清洗(弱碱水)
2、U型感应器加热
3、淬火连杆颈
HRC55以上,淬硬层深3-5mm
第二工序:回火(整体回火)
加热260度,采取零件校直,防止热处理变形,回火后零件喷丸(用钢砂清理零件表面)去除氧化层。中心孔修正。
3 轴类车间--凸轮轴
1、凸轮轴是控制气门开闭时刻和运动规律的主要零件。凸轮轴上各凸轮的相互位置按照发动机规定的点火顺序排列。因此,根据各凸轮轴的相对位置和凸轮轴的旋转方向,可以判断发动机的点火顺序。
2、凸轮轴的加工工序如下所示:
(1)材料:45钢 汽油机用
同时车12个凸轮、1个偏心轮
铣键槽(起定位作用)、装正时齿轮
粗磨12个凸轮、1个偏心轮
表面淬火、中频感应、局部淬火
精磨12个凸轮和1个偏心轮
精磨第5个主轴颈
校正1个齿轮颈、3个主轴颈
精磨小轴颈和第1个轴颈端面
校正1个齿轮、3个主轴颈
抛光5个主轴颈、12个凸轮、1个偏心轮
探伤(荧光磁粉)
综合检查
清洗、防锈
包装
(2)材料:球墨铸铁(QT700-2) 柴油机(重型)用
铣凸轮轴端面。
钻两个工艺孔
打标记号
粗磨中间轴颈
精磨中间轴颈
上数铣机床(所有主轴颈、小轴颈、倒角)
精磨所有主轴颈
精磨小轴颈和第1主轴颈的前端面
铣键槽(定位作用)
上数控磨床(粗、精磨主轴颈、偏心轮)
清除毛刺(气动塑料毛刷)
探伤(荧光磁粉)
抛光
清洗
防锈包装
3、凸轮轴工艺分析
凸轮轴一般由碳钢模锻或球墨铸铁铸造。为了提高耐磨性,各个轴颈和凸轮表面需经渗碳或高频淬火。
(1)、凸轮轴的结构特点:
汽油机的典型凸轮轴,如下图所示,轴的前端装有正时齿轮,轴上除了进、排气凸轮及轴颈外,还有驱动部分电器和机油泵的齿轮及驱动汽油泵的偏心轮。柴油机的凸轮轴没有驱动部分电器的齿轮和驱动汽油泵的偏心轮,除此之外,和汽油机的凸轮轴相似。
(2)、凸轮轴的工艺特点
为减少凸轮轴的弯曲变形,多缸凸轮轴常采用多轴颈支撑;为使凸轮轴安装时能直接从轴承孔里穿进去,凸轮轴上的轴颈直径必须大于凸轮外廓的最大尺寸;为保证柴油发动机准确的配气时间,凸轮轴上装有定时齿轮,通过中间齿轮曲轴上的定时齿轮驱动运转。
4 大马力--缸盖
功能:1、缸盖与缸体及活塞顶部一起形成燃烧室,作为发动机将化学能转化为动能的场所;
2、缸盖水套内腔与缸体水套、水箱、节温器、水泵及风扇等形成发动机冷却循环系统;
3、与凸轮轴、挺杆、气门弹簧、摇臂等形成发动机的配气系统;
4、与油底壳、机油收集器、机油泵、油道等形成发动机的机油润滑系统;
5、与喷油器、燃油导轨、燃油泵、油管、油箱等形成发动机的燃油供给系统。
结构特点:气缸盖安装在气缸体的上面,从上部密封气缸并构成燃烧室。它经常与高温高压燃气相接触,因此承受很大的热负荷和机械负荷。水冷发动机的气缸盖内部制有冷却水套,缸盖下端面的冷却水孔与缸体的冷却水孔相通。利用循环水来冷却燃烧室等高温部分。缸盖上有进、排气门座,气门导管孔,用于安装进、排气门,还有进气通道和排气通道等。汽油机的气缸盖上加工有安装火花塞的孔,而柴油机的气缸盖上加工有安装喷油器的孔。顶置凸轮轴式发动机的气缸盖上还加工有凸轮轴轴承孔,用以安装凸轮轴。
材料:1、常用的缸盖材料有灰铸铁、合金铸铁、铝合金及镁合金等;
2、卡车用发动机的缸盖材料多以灰铸铁、合金铸铁或低铜铬铸铁等为主,其机械性能、铸造性能和耐热性能较好;
3、小型发动机的缸盖多采用铝合金材料,充分发挥其比重小、导热性能好的特点。
工艺流程:
① 毛坯粗铣底面
② 以底面为基准、半粗铣顶面
③ 钻铰定位销孔
④ 铣进、排气管面
⑤ 铣前后端面
⑥ 去毛刺
⑦ 钻进、排气面上螺纹底孔,钻横向水道孔
⑧ 铰横向水道孔
⑨ 扩、铰排气面上堵盖孔
⑩ 压入横向铸铁棒
11 钻通十二个推杆孔和二十六个螺栓孔
12 钻进气面三个M10螺纹底孔,锪螺栓孔平台
13 扩、铰进气面上堵盖孔
14 钻摇臂支座螺纹底孔
15 从顶面扩螺堵孔,攻丝,从顶面钻,攻暖风阀孔
16 攻进、排气管面及顶面螺纹孔,钻斜油孔凹坑
17 钻通十二个导管底孔
18 锪弹簧凹座,导管孔口倒角
19 钻通两个斜油孔
20 钻前后端面螺纹底孔
21 前后端面螺纹孔攻丝
22 锪导管底孔凹坑,锪进、排气阀座底孔
23 振动倒屑
24 精铣缸盖底面
25 喷油嘴孔、水套孔加工
26 进、排气阀座底孔口倒角
27 铰气导管底孔及阀座底孔
28 铣R40圆弧槽
29 喷油嘴孔口倒角
30 清洗
31 从顶面钻六个21/8螺堵孔
32 堵盖装配
33 螺堵装配
34 气压实验
35 烘干处理
36 压进、排气座阀
37 压导管
38 枪铰进、排气导管孔,锪排气阀座锥面
39 最终清洗
40 最终检查
41 发送气缸盖总成
5 箱体车间--4H缸体
缸体是发动机的基础零件,通过它把发动机的曲柄连杆机构(包括活塞、连杆、曲轴、飞轮等零件)和配气机构(包括缸盖、凸轮轴等)以及供油、润滑、冷却等机构连接成一个整体。缸体形状复杂、薄壁、箱体结构。因而要求缸体要有足够的强度和刚度,底面具有良好的密封性,外型为六面体,多孔薄壁零件,冷却可靠,液体流动通畅。且缸体毛坯的技术要求及毛坯质量要求不允许有裂纹、冷隔、疏松、气孔、砂眼、缺肉等铸造缺陷。若缸体毛坯加工余量过大,造成加工节拍长,增加机床的负荷,影响机床和刀具的使用寿命。
4H作业部生产的缸体其材料为HT250,灰口铸铁的优点具有足够的韧性,良好的耐磨性、耐热性、减震性和良好的铸造性能、以及良好可切削性、且价格便宜。
1、缸体工艺工艺安排遵循的原则:
(1)首先从大表面切除多余的加工层,以便保证精加工后变形量很小。
(2)容易发现内部缺陷的工序应按排在前。
(3)把各深孔加工尽量安排在较前面的工序以免因较大的内引力,影响后序的精加工。
2、缸体工艺过程的拟定:
(1)先基准后其它:先加工一面两销。
(2)先面后孔:先加工平面,切去表面的硬质层,可避免因表面凸瘤、毛刺及硬质点的作用而引起的钻偏和打刀现象,提高孔的加工精度。
(3)粗、精分开:有利于消除粗加工时产生的热变形和内应力,提高精加工的精度。有利于及时发现废品,避免工时和生产成本浪费。
(4)工序集中:为了减少工序,减少机加工设备降低成本。应最大限度的集中在一起加工,提高生产效益和加工精度。相关孔集中在一台机床上加工还可以减少重复定位产生的定位误差,尤其是提高位置精度。
3、加工工艺路线:
(01)粗铣底面、前后端面、瓦盖结合面、瓦座侧面,镗曲轴半圆孔
(02)底平面及主副油道孔加工(卧式加工中心DM800IIB)
(03)铣顶面,钻缸盖螺栓孔、推杆孔、挺杆孔、水孔(卧式加工中心DM800IIB)
(04)底面孔系及前后端面部分孔系加工(卧式加工中心DM800IIB)
(05)粗镗缸孔(粗镗床EQZ777)
(06)半精铣前后端面(卧式加工中心DM800IIB)
(07)机冷器面孔系及斜油孔加工
(08)挺杆侧及顶面部分孔系加工
(09)瓦盖拧紧、打瓦盖标记
(10)主凸孔、前后端面及孔加工
(11)打标记(打标机、清洗机)
(12)缸体吸铁屑、刷油道
(13)中间清洗
(14)终清洗
(15)人工吸铁屑
(16)人工压装砂孔堵盖及油孔堵盖
(17)压凸轮轴衬套(衬套压床EP5003-1)
(18)水套试漏(总成试漏机DFCY04)
(19)终检下线
(20)防锈
4、缸孔的技术要求:
1) 配缸间隙公差0.03
2) 缸孔直径公差0.045
3) 缸孔圆柱度公差0.01
4) 干缸套压入过盈量0.045~0.075
5) 缸孔对主轴承孔的垂直度0.05
6 机修车间--机械磨锋
专业刀具的修磨,提高生产效率;防止浪费,从而降低生产成本。
刀具的分类:
1、加工外表面刀具:车刀、刨刀、铣刀、外表面拉刀;
2、孔加工刀具:钻头、扩孔刀、铰刀、锉刀、内表面拉刀;
3、螺纹加工刀具:丝锥、板牙、螺纹车刀;
4、齿轮加工刀具:滚齿刀、插齿刀、剃齿刀、花键拉刀;
5、工件切断刀具:切断车刀、切断铣刀、高碳钢锯条。
另外刀具按照结构形式进行分类,又可以分为整体式,焊接式,镶齿式,可转位式。
制造刀具的材料主要有高速钢,硬质合金,立方氮化硼,陶瓷材料,金刚石,工具钢等。
(1) 高速钢
高速钢是一种加入了较多的钨、钼、铬、钒等合金元素的的高合金工具钢。高速钢具有较高的热稳定性、高的强度和韧性、一定的硬度和耐磨性,在600℃仍然能保持较高的硬度。按用途不同,高速钢可分为通用型高速钢和高性能高速钢。
通用型高速钢,广泛用以制造各种复杂刀具,可以切削硬度在250~280HBS以下的结构钢和铸铁材料。其典型牌号有W18Cr4V(称称W18),W14Cr4VMnXt,W6M05Cr4v2(简称M2),W9Mo3Cr4V(简称W9)。 高性能高速钢包括高碳高速钢、高钒高速钢、钴高速钢和超硬高速钢等。其刀具耐用度约为通有型高速钢刀具的1.5~3倍,适合于加工超高强度等难加工材料。其典型牌号有W2Mo9Cr4Vo8(M42),是应用最广的含钴超硬高速钢,具有良好的综合性能;W6Mo5Cr4V2AI和W10Mo4Cr4V3AI(5F-6)是两种含铝的超硬高速钢,具有良好的切削性能。
(2) 硬质合金
硬质合金是将钨钴类(WC),钨钴钛(WC-TiC),钨钛钽(铌)钴(WC-TiC-TaC)等难熔金属碳化物,用金属粘结剂Co 或Ni等经粉未冶金方法压制烧结而成。
(3) 陶瓷刀具材料
陶瓷刀具材料的品种牌号很多。按其主要成分大致可分为以下三类。
1)氧化铝系陶瓷 此类陶瓷的突出优点是硬度及耐磨性高,缺点是脆性大,抗弯强度低,抗热冲击性能差,目前多数用于铸铁及调质钢的高速精加工。
2)氮化硅系陶瓷 这种陶瓷的抗弯强度和断裂韧性比氧化铝系陶瓷有所提高,抗热冲击性能也较好,在加工淬硬钢、冷硬铸铁、石墨制品及玻璃钢等材料时有很好的效果。
3)复合氮化硅一氧化铝(Si3N4+Al2O3)系陶瓷 该材料具有极好的耐高温性能、抗热冲击和抗机械冲击性能,是加工铸铁材料的理想刀具。其特点之一是能采用大进给量,加之允许采用很高的切削速度,因此可以极大地提高生产率。
(4) 立方氮化硼(CBN)
立方氮化硼是靠超高压、高温技术人工合成的新型材料,其结构与金刚石相似。它的硬度略逊于金刚石,但热硬性远高于金刚石,且与铁族元素亲和力小,加工中不易产在切屑瘤。
(5)聚晶金刚石(PCD)
聚晶金刚石是用人造金刚石颗粒,通过添加CO、硬质含金、NiCr 、Si-SiC以及陶瓷结合剂,在高温(1 200℃)、高压下烧结成形的刀具,在实际中得到了广泛地应用。
7 dCi11车间--车间大马力机加
大马力车间是我在发动机厂所看到的最先进的自动生产车间,生产dcill发动机,6缸,420马力,特点是省油。生产流程为:上线→缸体分装线→活塞分装线→缸盖分装线→半总成试漏机→下线。出厂试验出线90%合格,出厂100%合格,采用先进的高压共轨(保证喷油嘴在最合适的时间喷最合适的油量达到最佳燃烧比)及涡轮增压技术(将排出的气体加压后再利用),配公司生产的天龙车和重卡。车间3/4为装配线,90%机床是加工中心。采用干式试漏(充气式),缸体缸盖是铸造成型,年产大马力发动机3万台。恒温测量对缸体缸盖质检,流水线采用夹具托盘。缸盖装配线有较多检测、助力装备和拧紧装备。服务器检测生产线状况,机械手自动涂装。
(1)dci 11发动机介绍
① dci 11 是一种大马力直列六缸发动机,d—柴油,c—高压共轨,i—电喷;
② 匹配东风天龙、东风大力神、工程机械车;
③ 厂房建于20##年,主要生产dci 11四大件:缸体、缸盖、曲轴、凸轮轴。
(2) 主要零件
① 缸体:箱体类零件,曲轴、凸轮轴装在缸体中,缸盖用螺纹连接在缸体上,凸轮轴安装在缸体侧面
② 曲轴:能量传递:动力-曲轴大端-飞轮-离合器;曲轴小段-皮带轮-部分能量转化为电能,供给汽车其余用电部件,如照明系统、音响等。
③ 凸轮轴:进气凸轮、排气凸轮——直径比主轴颈小;工作过程:空气-空气滤清器-吸气-喷油-压缩-燃烧-废气进入排气口和水道。
④ 缸垫:作用:密封,防止窜气;
⑤ 喷油器:垂直安在缸盖上,有6个微孔,喷出高压雾状燃油;
⑥ 高压油泵:为燃油建立高压,使燃烧更加充分
⑦ 缸孔——6个
⑧ 曲轴——强度要求高
(3)曲轴工艺
1.毛坯 长1050mm,铣完后,打基准中心孔;几何中心:圆规画圆,找圆心;质量中心:由于6缸发动机曲轴有6个连杆件,2个一组,零件旋转时,600~1200r/min的转速,会产生动不平衡,且产生的冲击力非常大,冲击载荷会影响刀具及机床的精度。用V型卡爪支撑曲轴,找出平衡点,即质量中心可使余量分配均匀;
2.加工毛坯面:用铣床、大余量切削;
3.加工主轴进油孔、曲轴油孔;
4.淬火:电磁感应加热;对零件表面进行硬度处理,改变曲轴表面硬度及耐磨性,心部韧性不变;改变金相组织,用回火方式改善组织内部应力(在200~300℃下回火3小时);
5.探伤:磁粉探伤,照射时发光,可探明细微裂纹;
6.加工中心:a.两个基准:质量中心、几何中心;b.工艺孔;零件变形:理想,均匀变形;实际,W,Z,D状,非均匀变形。通过加工中心修正,打三个点找到圆心,沿母线以外的余量磨掉,变形量超出机床可修正范围则会自动报警。c.工艺孔中心线-分度-连杆中心——磨两端轴承位置;
7.修正加工:曲轴姿态,装配标准;
8.平衡:这是曲轴特有的工序。通过离心力掌控,平衡机对离心力进行修正;
9.抛光:这是汽车轴类零件共有的一道工序。属于微量加工,只有几个微米;目的是去除零件表面呈锯齿状的毛刺。毛刺很锋利,如不去除,会拉掉轴瓦,并抱死主轴;
10.终检;
11.清洗;
12.键的安装。
(4)凸轮轴工艺
1、特殊工艺 ——校直,零件较细,易弯曲须校直;
2、一般工艺——车-铣键槽-打中心孔-外铣-淬火-回火-校直。
(5)缸体、缸盖
1、定位——一销两面;
2、面——与定位块平行,由块面组成;
3、铣平面、钻孔。
(6)加工中心与组合机的比较
① 节拍:加工中心主轴由基准快速移动到坐标位置,依次加工,需多次调刀,节拍慢;相对而言,组合机不需要多次调刀,故比加工中心节拍快;
② 精度:
a.生活实例:在墙上钻孔,钻头与墙面接触之后会产生跳动,一般有两种应对方法,一种是用力控制,另一种是先在墙上打一个小孔,在继续钻。
b.组合机:用组合机钻孔也会产生跳动,用让刀的方法来解决,但让刀不可太大,以免损伤刀具。
c.加工中心:闭环系统:主轴-移动-到位,到位后刀具不再运动,精度高;也有可能产生跳动,加工中心进刀量很大,有1000多毫米,高转速、大进给、大切削力,使得加工精度比组合机高。
③ 组合机用于粗加工,加工中心用于精加工,目的:减少调刀次数及空行程。
(7)设备
高精度设备—加工中心,用于成品阶段;刀具上有小孔,是冷却水通道;利用加工中心加工基准面,可保证高精度定位基准。
8、装试车间--大马力装配
(1)大马力发动机
DCRL(高压共轨柴油机),直列6缸,11升排量,适用于天龙等品牌的重型大卡车,载重量达40多吨。
(2)特色
车间恒温在20度左右,这样在恒温状态下装配大马力发动机,零件与零件之间的间隙得到保障,气门间隙变化调节更为准确。采用中央空调系统,调整车间室内温度,使车间内气压高于车间外气压,以达到无尘效果,这样就可以提高发动机寿命。因为曲轴、凸轮轴的轴瓦与轴之间利用油膜来达到润滑效果,否则,当轴高速运转时会严重损耗它们的寿命。车间噪音少,环境好,设备排放整齐。车间里的电动扳手造价将近10万元每把,可以上传信息,从而更好地协调发动机的装配。
(3)车间功用
分为三部分:
1、机械加工:加工缸体、缸盖、曲轴、凸轮轴四大零件
2、装配车间:将缸体、缸盖、曲轴、凸轮轴及它们的相关辅件零件装配在一起
3、实验站:模拟发动机对其各性能进行检测,采用英国式实验架,东风dcill作业部主要使用热式检测,现在国内大多数汽车厂均使用这种方法,热式检测性价比高。国外有些汽车厂使用冷氏检测,就是在无冷却液。无机油的情况下对发动机进行检测,虽然检测更好准确有效,但检测费用高。
装配流程:
1缸体上线
2装主轴瓦
3装曲轴
4拧紧主轴承螺栓
5装后油封
6装飞轮壳
7装飞轮
8装压盘
9装离合器壳
10装活塞连杆总成
11拧紧连杆螺母
12拧紧正时齿轮室座
13装凸轮轴
14装正时齿轮室盖
15装机油泵
16装油底壳
17装减震器
18装缸盖总成
19预拧紧缸盖螺栓
20装摇臂轴
21装机油泵传动轴
22调气门间隙
23装喷油器总成
24装汽缸罩盖
25装空气压缩机
26装排气管
27装增压器
28装增压器进气管接头
29装曲轴箱通风
30装水泵
31装节温器
32装风扇皮带轮
33装冷却器
34装放水阀
9、车身厂--车身
(1)车架总成装配工艺流程:从梁分装--车架装配--装配紧固--铆接--打标记--钻孔--铆接--翻转
(2)连接方式:铆接,焊接,油压,冲压。
(3)焊接:气体保护焊、电弧焊、点焊、缝焊、CO2+Ar混合气体保护焊。
(4)车架特点:材料16Mn,使用双层梁的结构,作用为加强强度。
10 再造车间--再造
再造业简介:产品在设计时有一个使用寿命,再造就是打破原有设计寿命,通过更新设计,重新评估其寿命,以减少资源消耗。
生产流程:
①拆下发动机上的电气部分,进行清洗;
②对发动机作完全解体
③检验零部件
④对精度要求高的零部件,委托dci11进行三坐标检测
⑤肉眼难以观测的零件检验,委托康明斯作业部进行检测
⑥对于所有不达标的零部件,作完全破坏性报废,以免流入市场
⑦ 用化学溶液脱漆、除锈、除积碳
⑧用煤油清洗
⑨台架试验
⑩最终完善
?送品质保证部,对发动机进行系统评审,发放合格证。
五、课程学习
1、数控加工工艺
采用数控机床加工零件时,只需要将零件图形和工艺参数、加工步骤等以数字信息的形式,编成程序代码输入到机床控制系统中,再由其进行运算处理后转成驱动伺服机构的指令信号,从而控制机床各部件协调动作,自动地加工出零件来。当更换加工对象时,只需要重新编写程序代码,输入给机床,即可由数控装置代替人的大脑和双手的大部分功能,控制加工的全过程,制造出任意复杂的零件。
总的来说,数控加工有如下特点:
(1) 自动化程度高,具有很高的生产效率。
(2)加工对象的适应性强。
(3)加工精度高,质量稳定。
(4)易于建立与计算机间的通信联络,容易实现群控。
加工工艺流程:
(1)、机床的合理选用
(2)、数控加工零件的工艺性分析
(3)、加工方法的选择与加工方案的确定
(4)、工艺与工步的划分
(5)、零件的安装与夹具的选择
(6)、刀具的选择与切削用量的确定
(7)、对刀点和换刀点的确定
(8)、工艺加工路线的确定
2、企业6S管理
(1)、6S来源发展
5S最早起源于日本现代工厂管理中,在日语发音中,5个S第一个字母均以S起音,因此称之为5S,5S作为一种企业管理基础工程,实施后成绩显然,而逐步流行到除日本以外的其它国家和地区,并越来越受到广大管理者的重视。随着企业发展变化,在原来5S基础上增加了安全,也即我们今天讲的6S管理。
6S即:
整理(SEIRI)、整顿(SEITON)、清扫(SEISO)、清洁(SEIKETSU)、素养(SHITSUKE)、安全(SECURITY)。
6S+节约(SAVING)为7S,再+服务(SERVICE)为8S,再+满意(SATIFACTION)为9S
(2)、6S方针
以人为本,全员参与,自主管理,舒适温馨。
(3)、推进6S目标
改善和提高企业形象;促进效率的提高;改善零件在库周转率;减少甚至消除故障,保障品质;保障企业安全生产;降低生产成本;改善员工精神面貌,增加组织活力;缩短作业周期确保交货期。
(4)、6S管理的作用
6S是最佳推销员;6S是节约家;6S对安全有保障;6S是标准化的推动者;6S形成令人满意的职场;6S是保证品质的基础。
(3)、6S管理的内容方法
①.整理(SEIRI):
整理的内容

②.整顿(SEITON):
整顿三要素

整顿三原则

③.清扫(SEISO):
清扫的目的及作用

执行的方法:建立责任区域------制定清扫标准------确立责任人
推进步骤:安全教育,保养教育,知识教育。
④.清洁(SEIKETSU):
清洁的作用和要点

⑤.素养(SHITSUKE):
素养推行要领和方法

人品的提升:对父母尽孝,对家庭尽爱,对工作尽职,对上司尽责,对下级尽教。
注意仪装,礼貌用语,态度诚恳。
⑥.安全(SECURITY):
安全管理的目的:保障员工的安全,保证生产正常运转,减少经济损失,紧急对应措施。
执行的方法:安全隐患识别,实行现场巡视。
安全宣传、安全教育、安全检查。
(4)、6S实施细则
①.教育培训,责任区域,责任部门,动员大会。
②.推行计划,制定基准,职能培训,建立看板。
③.工具器材,识别实施,建立责任,行动实事。
④.进行改善,定期检查,定期评比,结果公布。
3、连杆加工工艺
(1) 连杆的结构特点
连杆是汽车发动机中的主要传动部件之一,它在柴油机中,把作用于活塞顶面的膨胀的压力传递给曲轴,又受曲轴的驱动而带动活塞压缩气缸中的气体。连杆在工作中承受着急剧变化的动载荷。连杆由连杆体及连杆盖两部分组成。连杆体及连杆盖上的大头孔用螺栓和螺母与曲轴装在一起。为了减少磨损和便于维修,连杆的大头孔内装有薄壁金属轴瓦。轴瓦有钢质的底,底的内表面浇有一层耐磨巴氏合金轴瓦金属。在连杆体大头和连杆盖之间有一组垫片,可以用来补偿轴瓦的磨损。连杆小头用活塞销与活塞连接。小头孔内压入青铜衬套,以减少小头孔与活塞销的磨损,同时便于在磨损后进行修理和更换。
连杆的作用是把活塞和曲轴联接起来,使活塞的往复直线运动变为曲柄的回转运动,以输出动力。因此,连杆的加工精度将直接影响柴油机的性能,而工艺的选择又是直接影响精度的主要因素。反映连杆精度的参数主要有5个:
① 连杆大端中心面和小端中心面相对连杆杆身中心面的对称度;
② 连杆大、小头孔中心距尺寸精度;
③ 连杆大、小头孔平行度;
④ 连杆大、小头孔尺寸精度、形状精度;
⑤ 连杆大头螺栓孔与接合面的垂直度。
(2) 连杆的主要技术要求
连杆上需进行机械加工的主要表面为:大、小头孔及其两端面,连杆体与连杆盖的结合面及连杆螺栓定位孔等。
(3) 连杆的材料和毛坯
连杆在工作中承受多向交变载荷的作用,要求具有很高的强度。因此,连杆材料一般采用高强度碳钢和合金钢;如45钢、55钢、40Cr、40CrMnB等。近年来也有采用球墨铸铁的,粉末冶金零件的尺寸精度高,材料损耗少,成本低。随着粉末冶金锻造工艺的出现和应用,使粉末冶金件的密度和强度大为提高。因此,采用粉末冶金的办法制造连杆是一个很有发展前途的制造方法。
连杆毛坯制造方法的选择,主要根据生产类型、材料的工艺性(可塑性,可锻性)及零件对材料的组织性能要求,零件的形状及其外形尺寸,毛坯车间现有生产条件及采用先进的毛坯制造方法的可能性来确定毛坯的制造方法。根据生产纲领为大量生产,连杆多用模锻制造毛坯。连杆模锻形式有两种,一种是体和盖分开锻造,另一种是将体和盖锻成—体。整体锻造的毛坯,需要在以后的机械加工过程中将其切开,为保证切开后粗镗孔余量的均匀,最好将整体连杆大头孔锻成椭圆形。相对于分体锻造而言,整体锻造存在所需锻造设备动力大和金属纤维被切断等问题,但由于整体锻造的连杆毛坯具有材料损耗少、锻造工时少、模具少等优点,故用得越来越多,成为连杆毛坯的一种主要形式。总之,毛坯的种类和制造方法的选择应使零件总的生产成本降低,性能提高。
4、曲轴加工工艺
(1)曲轴的作用
曲轴是汽车发动机中的重要零件,它与连杆配合将作用在活塞上的气体压力变为旋转的动力,传给底盘的传动机构,同时,驱动配气机构和其它辅助装置。
曲轴在工作时,受气体压力,惯性力及惯性力矩的作用,受力大而且受力复杂,同时,曲轴又是高速旋转件,因此,要求曲轴具有足够的刚度和强度,具有良好的承受冲击载荷的能力,耐磨损且润滑良好。
(2) 曲轴的结构及其特点
曲轴一般由主轴颈,连杆轴颈、曲柄、平衡块、前端和后端等组成。一个主轴颈、一个连杆轴颈和一个曲柄组成了一个曲拐,曲轴的曲拐数目等于气缸数(直列式发动机);V型发动机曲轴的曲拐数等于气缸数的一半。
(3) 曲轴的主要技术要求分析
①. 主轴颈、连杆轴颈本身的精度,即尺寸公关等级IT6,表面粗糙度Ra值为1.25~0.63μm。轴颈长度公差等级为IT9~IT10。轴颈的形状公差,如圆度、圆柱度控制在尺寸公差之半。
②. 位置精度,包括主轴颈与连杆轴颈的平行度:一般为100mm之内不大于0.02mm;曲轴各主轴颈的同轴度:小型高速曲轴为0.025mm,中大型低速曲轴为0.03~0.08mm。
③. 各连杆轴颈的位置度不大于±20′。
④. 曲轴的材料和毛坯的确定。
曲轴工作时要承受很大的转矩及交变的弯曲应力,容易门生扭振、折断及轴颈磨损,因此要求用材应有较高的强度、冲击韧度、疲劳强度和耐磨性。常用材料有:一般曲轴为35、40、45钢或球墨铸铁QT600-2;对于高速、重载曲轴,可采用40Cr、42Mn2V等材料。本课题采用球墨铸铁QT600-2.
曲轴的毛坯根据批量大小、尺寸、结构及材料品种来决定。批量较大的小型曲轴,采用模锻;单件小批的中大型曲轴,采用自由锻造;而对于球墨铸铁材料则采用铸造毛坯。
5曲轴的机械加工工艺过程
曲轴的尺寸精度、加工表面形状精度以及位置精度的要求都很高,但刚性比较差,容易产生变形,这就给曲轴的机械加工带来了很多困难,必须予以充分的重视。
曲轴需要加工的表面有:主轴颈、连杆轴颈、键槽、φ22的外圆。由于使用了工艺搭子,铣键槽安排在切除工艺搭子后,磨削外圆安排在保留工艺搭子前。
根据曲轴的结构特点及机械加工的要求,加工顺序大致可归纳为:铣两端面;车工艺搭子和钻中心孔;粗、精车三连杆轴颈;粗、精车各处外圆;精磨连杆轴颈、主轴颈和φ20、φ22外圆;切除工艺搭子、车端面、铣键槽等。
六、实习总结与心得
通过这次的实习使我对自己的专业有了更为详尽而深刻的了解,同时这也是对大学里所学知识的巩固与运用。在十堰的实习中我的理论和实践进行了结合。这些都对我的观念起着潜移默化的作用。从这次实习中,我体会到了实际的工作与书本上的知识是有一定距离的,并且需要进一步的再学习。只是作为实习的这一段时间远远不能够对一个企业做深入地了解,只能是肤浅的、粗略的了解一下产品工艺的简单流程,和一些先进的与本专业相关的工业技术。
当前随着科学技术的迅猛发展,各种产品品种类繁多,生产工艺、生产流程也各不相同,但不管何种产品,从原料加工到制成产品都是遵循一定的生产原理 ,通过一些主要设备及工艺流程来完成的。因此,在专业实习过程中,首先要了解其生产原理,弄清生产的工艺流程和主要设备的构造及操作。其次,在专业人员指导下,通过实习过程见习产品的设计、生产及开发等环节,初步培养我们的知识运用能力。经过这次的实习让我亲眼见到了许多平时在学校里只闻其名不见其形的机床,让我对各种各样的机床有了比较清楚的认识。
科技在发展,时代在进步。我们只有不断努力提高自己,才能在飞速发展的社会中前进,不被他人落下。