第一章 施工组织管理与质量控制
第一节 施工组织设计与管理
一、施工组织设计
施工组织设计是从全局出发,按照客观的施工规律和当时、当地的具体条件,统筹考虑施工活动中的人力、资金、材料、机械和施工方法等主要因素后,对整个工程施工进度和资源消耗作出的科学安排。其目的是使工程建设在一定的时空内实现有组织、有计划、有秩序的施工,以期达到施工的相对最优效果。
(一)施工组织设计的种类
施工组织设计一般可分为施工组织规划设计、施工组织总设计、单位工程施工组织设计和特殊用途的施工组织设计四种。
1.施工组织规划设计:在初步设计阶段编制主要根据具体建设条件、资源条件、技术条件和经济条件,作出一个基本轮廓的施工计划,借以肯定拟建公路的经济合理性和技术可行性,它是施工总设计的编制依据。
2.施工组织总设计是根据施工组织规划设计编制的,用以指导施工单位进行全场性的施工准备工作和有计划的运用施工力量。开展施工活动,并结合实际,使组织规划进一步具体化和作某些必要的调整。
3.单位工程施工组织设计是在施工图阶段以单位工程为对象编制的,用以直接组织单位工程的施工。它在施工组织总设计和施工单位施工部署的指导下,具体地安排人力、物力,是施工单位编制作业计划和制定季度施工计划的重要依据。
(二)施工组织设计的内容
1.工程情况简介:如工程规模、数量、工期、特征,主要地质、水文、气候情况,技术要求等。
2.施工技术方案:主要是施工方法,尤其是冬季、夏季和雨季或缺水、风沙、高原等地区及技术复杂的特殊施工方法。
3.施工进度计划:包括以实物工程量和投资额表示的工程总进度计划和分年度计划,以及需用工日数、机械台班数。
4.施工总体及部分工程平面布置,土石方平衡规划,施工现场平面布置。
5.劳力需要量及来源:包括总需要量和分工种、分年度的需要量。
6.施工机械、筑路材料、施工用水、用电的分年度需要量和供应情况,解决方案。
7.道路、防洪、排水和生产、生活用房等设施的建设及完成时间要求。
8.施工准备工作进度表。
(三)编制施工组织设计的依据和步骤
依据:设计文件和施工组织规划设计;会审图纸、现场核对、恢复定线所取得的补充资料;施工队伍的素质及机具装备水平;技术组织措施;有关规范、规程、合同等。
步骤:见教材P3图1—1
二、施工组织设计的实施
(一)施工作业计划
施工作业计划应根据施工组织和现场具体情况,灵活安排,平衡调度。以确保施工进度与质量。施工作业计划可分为月作业计划和旬作业计划。
(二)施工调度
是组织施工中各个环节、各专业、各工种协调动作的中心。它的主要任务是保证施工有条不紊地进行,并为施工中的正确指挥创造有利条件,以促使施工任务按期保质完成。
(三)施工现场的平面管理
为搞好施工现场平面管理,首先要严格执行批准的施工组织设计中的平面布置图。其次,要加强经常性的现场管理,合理分配使用场地,协调个方面关系,保证现场交通和给水排水系统畅通。
(四)施工原始记录
它是各项工程完成情况的文字和数据反映,也是鉴定工程好坏的主要凭证和总结和总结经验教训。
第二节 施工网络计划技术
一、网络计划的基本概念
网络计划是以加注工序作业时间的箭杆和节点组成的网络图来表示施工进度计划。其基本原理是:先用网络图的形式表示某项工程个工序的先后顺序和相互关系。再通过计算找出计划中的关键工序和关键线路。最后通过不断改善得出最优方案付诸实施。在执行中进行有效的控制与监督,以保证合理利用人力、物力和财力,获得最佳的经济效益。
(一)网络图的分类
1.按网络图的标注方式分为 代号
单代号网络 工序名称
持续时间
用节点(圆圈)表示工序,箭线表示工序之间的逻辑关系
双代号网络。 i 工序名称 j
用箭线(杆)表示工序, 持续时间
节点(圆圈)表示工序之间的逻辑关系。
2. 按工序延续时间估计精确度的不同分为
肯定型网络图:各工序的持续作业时间是固定的,它可以用制定定额的方法来确定。
非肯定型网络图:各工序的作业,往往没有先例而无法确定,或者因为影响工作的因素太多不便确定,故作业时间一般是估计值。
第五章 路基施工技术
第三节 路基土方施工
一、路基土的分类与分级
(一) 路基土分类
土的分类方法很多,目的不同,方法各异,有地质分类、工程分类,等等。每一种分类都只能反映土的某些方法特征。如地质分类突出成因,着重反映土的发生、变化过程,为确定其物理和化学性质服务。在工程实践中需要的是能表达土的主要工程特性的分类。例如为了解决渗流问题,则要突出土的渗透性,在考虑粒度成分界限值时,要注意使粒组的划分与其透水性的变化相协调。而路基土的分类则要突出土的压实性和水稳性。
我国公路路基土采用的分类方法是,首先按有机质含量多少,划分成有机土和无机土两大类;其次,将无机土按粒组含量由粗到细划分为巨粒土、粗粒土和细粒土三类;最后,若为巨粒土和粗粒土,则按其细粒土含量和级配情况进一步细分,若为细粒土,则按其塑性指数和液限在塑性图上的位置进一步细分。
路基土可以归纳为如下4类:
1、 巨粒土:包括漂石、块石、卵石、碎石、卵石夹土;
2、 砾石土:包括级配良好砾与级配不良砾、含细粒土砾、粉土质砾与粘土质砾;
3、 砂类土:包括级配良好砂与级配不良砂、细粒土质砂、粉土质砂与粘土质砂;
4、 细粒土:包括高低液限粉土和高低液限粘土。
(二)土石工程分级
对安排施工和确定定额来说,最有实用意义的是将土石按其开挖的难易程度进行分级。表4-1是土石的六级分级,即将土分为松土、普通土和硬土三级;将岩石分为软石、次坚石和坚石三级。表4-2与表4-3为土石的十六级分级,即将土分为Ⅰ~Ⅳ四级,将岩石分为Ⅴ~XⅥ十二级。我国公路土石分级通常采用六级,但有时也要用到十六级,六级与十六级的对应关系如下:
六 级: 松 土 普通土 硬 土 软 石 次坚石 坚 石
十六级: Ⅰ~Ⅱ Ⅲ Ⅳ Ⅴ~Ⅵ Ⅶ~Ⅸ Ⅹ~ⅩⅥ
二、路堤基底处理
填方路段应将路基范围内的树根全部挖出并将坑穴填平夯实。填土范围内原地面表层的种植土、草皮等应予清除,清除深度一般小于15cm。清除出来的含有许多植物根系的表土可以铺在路堤边坡上,以利植物生长,起到边坡保护作用。
路堤基底清理后应予以压实。在深耕地段(大于30cm)地段,必要时应先将土翻松、打碎,再整平、压实。经过水田、池塘、洼地时,应根据具体情况采用排水疏干、换填水稳定性好的土、抛石挤於等处理措施,确保路堤的基底具有足够的稳定性。
地面横坡为1:5~1:2.5时,原地面应挖成台阶,台阶宽度应小于1m;地面横坡陡于1:2.5,应作特殊处理,防止路堤沿基底滑动,常用的处理措施有:
1、经检算下滑力不大时,先清除基底表面的薄层松散土,再挖宽1~2m台阶,但坡脚附近的台阶宜宽一些,通常为2~3m(图4-1)。
2、经检算下滑力很大或边坡下部填筑土层太薄时,先将基底分段挖成不陡于1:2.5的缓坡,再在缓坡上挖宽1~2m的台阶,最后一级台阶宜亦宽一些(图4-2)。
3、若坡脚附近地面横坡比较平缓时,可在坡脚处作土质护堤或干砌片石垛护堤(图4-3)。护堤最好用渗水性土填筑,但用于路堤相同的土填筑宜可。片石垛最好用大块的片石分层干砌,里外咬合紧密,不得只砌表面而内部任意抛填。片石垛的断面尺寸应通过稳定性检算确定。
三、填料的选择
一般的土和石都可以用作路堤的填料。用卵石、碎石、砾石、粗砂等透水性良好的填料,只要分层填筑分层压实,可不控制含水量;用粘性土等透水性不良的填料,应在接近最佳含水量情况下分层填筑与压实。
淤泥、沼泽土,含残余树根和易于腐烂物质的土,不能用作填筑路堤。液限大于50%及塑性指数大于26的土,透水性很差,且干时坚硬难挖,具有较大的可塑性、粘结性和膨胀性,毛细现象也很显著,浸水后能长时间保持水分,因而承载力很低,故一般部作为路堤填料,如非用不可,应在接近最低含水量情况下充分压实,并设置完善的排水设施。
含盐量超过规定的强盐渍土和过盐渍土不能作为高等级公路的填料;膨胀土除非表层用非膨胀土封闭,一般也不宜于作高等级公路的填料。
工业废渣是较好的填料。高炉矿渣或钢渣至少应放置一年以上,必要时应予破碎。粉煤灰属于轻质筑路材料,当路堤修筑在软弱地基或滑坡体上时,采用轻质填料有利于路堤的稳定。有些矿渣使用前应检验有害物质含量,以免污染环境。
应当指出,有多种资源可供选择时,应优先选用那些挖去方便、压实容易、强度高、水稳性好的土料。路堤受水浸淹部分,应尽量选用水稳性好的填料。
四、路堤填筑方式
路堤宜采用水平分层填筑,即按照横断面全宽分成水平层次,逐层向上填筑。如原地面不平,应从最低处分层填起,每填一层经过压实符合规定要求后,再填上一层。原地面纵坡大于12%地段,可采用纵向分层填筑法施工,沿纵坡分层,逐层填压密实。但填至路堤的上部,仍应采用水平分层填筑法。水平分层填筑是填筑路基的基本方法,它最能保证填土质量,一般均应采用。
在同一路段上要用到不同性质填料时,应注意:
1、不同性质的填料要分别分层填筑,不得混填,以免内部形成水囊或薄弱面,影响路堤稳定。
2、路堤上部受车辆荷载的作用影响较大,故一般宜将水稳性冻稳性较好的土填再路堤的上部;但路堤的下部可能受水浸淹时,也宜用水稳性好的土填筑。
3、透水性较大的土填在透水性较小的土之下时,如果两者粒径相差悬殊,应在层间加铺过渡垫层,以免上层的细颗粒散落到下层内;如果透水性较小的土填在透水性较大的土之下时,其顶面应作成4%的双向向外横坡,以免积水。
4、沿纵向同层次要改变填料种类时,应做成斜面衔接,且将透水性好的填料置于斜面的上面为宜。
5、填方相邻作业段交接处若非同时填筑,则先填地段应按1:1坡度分层留好台阶;若同时填筑,则应分层相互交迭衔接,搭头长度不得少于2m。
五、桥涵等构造物处的填筑
桥台台背、涵洞两侧及涵顶、挡土墙墙背的填筑在这些构造物基本完成后进行,由于场地狭窄,又要保证不损坏构造物,填筑压实比较困难,而且容易积水。如果填筑不良,完工后填土与构造物连接部分出现沉降差,就会发生跳车,影响行车的速度、舒适与安全,甚至影响构造物的稳定,养护期间要经常修补路面,也会导致堵塞交通。所以要注意选好填料和认真施工。
1、填料。在下列范围内一般应选用渗水性土填筑:台背顺路线方向,上部距翼墙尾端不少于台高加2m,下部距基础内缘不少于2m;拱桥台背不少于台高的3~4倍;涵洞两侧不少于孔径的2倍;挡土墙墙背回填部分。如果台背采用渗水土有困难时,在冰冻地区自路堤顶面起2.5m以下,可用与路堤相同的填料填筑。特别注意,不要将构造物基础挖出来的劣质土混入填料中。
2、填筑。桥台背后填土应与锥坡填土同时进行,涵洞、管道缺口填土,应在两侧对称均匀回填;涵顶填土的松铺厚度小于50~100cm时,不得通过重型车辆或施工机械;靠近构造物100cm范围内不得有大型机械行驶或作业。
3、排水。桥涵等结构物处填土,在施工中要竭尽防治雨水流入;对已有积水应挖沟或用水泵将其排除。对于地下渗水,可设盲沟引出。当不得不用非渗水土填筑时,应在其上设置横向盲沟或用粘土等不透水材料封顶。当土墙墙背应做好反滤层,使水能顺利地从泻水孔流出去。
4、压实。应在接近最佳含水量状态下分层填筑,分层压实。每层松铺厚度不宜超过20m。密实度应达到设计要求。如设计无专门规定,则按路基压实度标准执行。用非渗水土填筑时,必须加强压实措施,或对填土性能进行改善处理(如掺生石灰),以提高强度和减少雨水的渗入。
六、路堑开挖方式
1、横挖法
从路堑的一端或两端按横断面全宽逐渐向前开挖,称为横挖法。这种开挖方法适用于较短的路堑。
2、纵挖法
没路堑纵向将高度分成不大的层次依次开挖。纵挖发适用于较长的路堑。
七、土方机械作业
1、推土机作业
推土机作业由切土、运土、卸土、倒退(或折返)、回空等过程组成一个循环。影响作业效率的主要因素是切土和运土两个环节。因此,以最短的时间和距离切满土,尽可能减少土在推运中的散失,是衡量推土机作业方式优劣的依据。基本作业方式有:
1)下坡推土——利用下坡时推土机的重力分力,如速切土,增加推土量。但坡度不宜超过20%,否则回空时爬坡困难。
2)并列推土——两台或三台推土机并列同速推进,可以减少土的溜失。两铲刀间距一般约15~20cm。
3)拉槽推土——推土机连续多次在同一处推土,形成一条浅槽,在槽内推运可以减少土的漏失。槽深一般不大于铲刀的高度。
4)接力推土
在取屠场较长而土质较硬时,可自近而远分段将土推送成堆,然后再由远而近将各段土对一次推送至卸土点。这样不但可以提高运土效率,又可以减少运土时间。
5)波浪式推土
2、铲运作业
铲运机能够独立完成土方的铲装、运输、铺填、整平和预压等项作业,而且具有相当的机动灵活性,主要用于运输距离大,土方量集中的铲运工作。
1)一般铲土
铲运机在Ⅰ、Ⅱ级土中施工时,开始应使铲刀以最大深度切入土中(不超过30cm),随着行驶阻力的增加而逐渐减少铲土深度,直到铲斗满为止。
2)波浪式铲土
这种铲运方法适用于较硬的土。开始铲土时,使铲刀以最大深度切入土中,随着拖拉机负荷逐渐增加,发动机转速降低,相应地减小切土深度,这样反复若干次,直到铲斗铲满为止。这种铲推方法的优点时可以充分利用发动机功率,并能改善装土条件,从而可以提高工作效率。
3)跨铲铲土
这种方法适用于较坚硬的土层,铲土时按土4-8所示程序来布置铲土道。作业时,先在取土场第一排(1、2、3区)铲土道上取土,两相邻铲土道之间留出半个铲斗宽的土不铲。然后再在第二排(4、5区)铲土道上取土,其起点应在第一排铲土道的起点处向后移半个铲道宽。第三、四排铲土道依次后移,使各铲土道前、后、左、右重合起来。采用这种方法,由于铲土的后半段减小了切土宽度,能使拖拉机有足够的牵引道将铲斗装满,又可以缩短铲土道长度和铲土时间。
如果取土场狭窄,不能按上述施工程序布置时,也可以采用单排跨铲,如图4-9所示,每条铲土道间留出1.0~1.3m的宽度,在铲除这些土梗时可较少切土阻力。
4)下坡铲土
这种方法主要是利用铲运机的重力分力提高铲土效率。铲土下坡角一般为7~8°,最大不超过15°。如在平地取土坑铲土,应先将一端铲低,然后保持一定的坡度向后延伸铲土道,人为地创造下坡铲土的有利地形。进行下坡铲土时,应特别注意安全。一般下坡时铲运机应低速行驶;当铲运机进入坡道地段时应立即放下铲斗,以便利用铲斗与地面之间的阻力降低铲运机的行驶速度;当铲斗铲满,但后轮未进入缓坡地段前,不应提升铲斗和关闭斗门,以便利用斗前土的阻力而起制动作用。
5)顶推铲土
铲运机在坚硬的土、冻深在20cm以内的土或松散的干砂中作业,由于拖拉机的附着力不足,牵引力不能充分发挥时,可用推土机在铲运机铲土行程中进行顶推助铲。用这种方法施工须具有一定的工程量和工作量,方可避免推土机窝工。一般要求取土场的宽度不小于20m,长度不短于80m,铲运机半周程运距不短于250m。
铲运机施工运行路线的选择,要综合考虑施工效率、地形条件、机械磨损等因素,已达到运距短,地道平稳和修筑通道的工作量小等目的。在填筑路堤和开挖路堑工程中,常用的运行路线有椭圆形、“8”字形、“之”字形、穿梭形和螺旋形等。
1)椭圆形运行路线
这种路线如图4-10所示。它的最大优点是,在不同的地形条件下布置灵活,顺逆运行方向可以随时改变,同时运行中干扰也比较小。缺点是重载上坡的转角大,转弯半径大。
所谓“8”字形实际上是由两个椭圆形的连接,如图4-11所示,不同的是减少了两个180°的急转角。它在一次循环运行中可以完成两次铲土和两次卸土。同时重载和空载行驶的距离都比较短,效率高,在同一个运行路线中可以容纳多台铲运机同时施工。缺点是要求较大的施工场地,而且取土场应在路线的两侧,条件限制较多,因此在小型工地较少采用。
3)“之”字形运行路线
实际是若干“8”字形首尾相接的路线,如图4-12所示。这种路线适用于较场的地段施工,并宜于机群作业,即各机列队(每机间隔20m)依次行进填挖到尽头,作180°转弯后反向运行,只是所填挖的地段应与上次错开。这种运行路线一次循环太大,施工面太长,在多雨季节很难应用。
4)穿梭形与螺旋形运行路线
如图4-13所示,与上述几种相比,铲运机空载行驶距离短,全程也较短,在一个循环中可以两次铲卸土作业,因此施工组织简单。缺点是对一侧取土坑有局限性,运行路线中完成一个循环由四次转弯,增长了运行时间,另外拖拉机单侧磨损较重。
螺旋形实际上是穿梭形的一种变形,铲运机纵向铲土后,转向路堤上横向卸土,随后驶向路堤的另一侧取土坑再行铲装。这种运行路线的主要优点是运距短,功效高。缺点是急转弯多,拖拉机易产生偏磨。
3、挖掘机作业
1)正铲挖掘机的基本作业
(1)侧向开挖:运土车辆的运行路线位于挖掘机开挖路线的侧面(图4-14)。它的特点是,卸土时平均回转角小于90°,而且车辆可以直线进出,不需调头和倒驶,缩短了循环时间,效率高。
(2)正向开挖:装车时车辆停在挖掘机的后方(图4-15)。它的特点是,挖掘机前方挖土,回转至卸土处,其转角大于90°,从而增大了循环时间,但其开挖面较宽。此外,由于车辆不能直接开进挖掘道,而要调头和倒驶,使施工现场拥挤,挖掘机不能连续作业,效率降低。因此这种方式只适用于挖掘进口处。
2)反铲挖掘机的基本作业
(1)沟端开挖:开挖时挖掘机从沟的一端开始,然后沿沟中线倒退开挖(图4-16a),运输车辆停在沟侧,此时动臂只回转40°—45°左右即可卸料。如挖的沟宽为机子最大回转半径的两倍时,车辆只能停在挖掘机的侧面,动臂要回转90°方可卸料。
如挖掘的沟渠较宽时,可分段进行,如图4-16b所示。当开挖到尽头时,再调头开挖相邻的一段。这种分段法每段的挖掘宽度不宜过大,以车辆能在沟侧行驶为原则,达到减少作业循环时间。
(2)沟侧开挖:它与前者不同的是,车辆停在沟端,挖掘机在沟侧,动臂回转小于90°即可卸料(图4-17)。由于每循环所用的时间短,所以效率高。但挖掘机始终沿沟侧行驶,因此开挖边坡较陡。
3)拉铲挖掘机的基本作业
拉铲挖掘机的开挖方法与反铲挖掘机基本相同,只是挖掘的半径大,深度深。
(1)沟侧开挖:挖掘机位于沟侧,挖掘宽度等于或大于甩斗的挖掘半径。此外,在弃土场工作时,可以使土的甩出距离较远。这种开挖方法主要用来取土填筑路堤和开挖基坑,如图4-18a所示。
(2)沟端开挖:挖掘机停在沟的一端(图4-18b),开挖的宽度可达挖掘半径的两倍。此法可挖出陡峭的边坡,又可以两侧卸土。
4、装载机作业
装载机是一种工作效率较高的铲土运输机械,它兼有推土机和挖掘机两者的工作能力,可以进行铲掘、推运、整平、装载和牵引等多种作业。其优点是适应性强,作业效率高,操纵简单,是一种发展较快的循环作业式机械。装载机与运输车辆配合,可采用如下作业方式:
1)“I”字形作业
运输车辆平行于工作面,装载机则垂直于工作面,前进铲土后,直线后退一定距离,并提升铲斗,此时,运输车辆退到装载机铲斗卸土位置,装满后驶离。这种方式装载机不需调头,但要求运输车辆与其配合默契。
2)“V”字形作业
运输车辆与工作面成约60°;装载机则垂直与工作面,前进铲土后,在倒车驶离过程中调头60°,使与运输车辆垂直,然后驶向运输车辆卸料。这种方式循环时间较短。
3)“L”字形作业
运输车辆垂直与工作面,装载机铲土后,倒退并调转90°,然后驶向运输车辆卸土。这种方式需有较宽的工作场地。
5、平地机作业
平地机是一种铲土、运土、卸土同时进行的连续作业机械。主要工作装置是一把刮刀,它可以调整四种作业动作,即刮刀平面回转,刮刀左右端升降、刮刀左右引申和刮刀机外倾斜,来完成刮刀刀角铲土侧移、刮刀刮土侧移、刮刀刮土直线和机身外刮土等作业。
第二节 路基压实
填土经过挖掘、搬运、原状结构已被破坏,土团之间留下了许多孔隙,在荷载作用下,可能出现不均匀或过大的沉降或落甚至失稳滑动,所以路基填土必须进行压实;对于松土层构成的路堑表面,为改善其工作条件也应予以压实。
一、 影响压实效果的主要因素
1、含水量
土中含水量对压实效果的影响比较显著。当含水量较小时,由于粒间引力(可能还包括了毛细管压力)使土保持着比较疏松的状态或凝聚结构,土中孔隙大都互相连通,水少而气多,在一定的外部压实功能作用下,虽然土孔隙中气体易被排出,密度可以增大,但由于水膜润滑作用不明显以及外部功能也不足以克服粒间引力,土粒相对移动不容易,因之压实效果比较差;含水量逐渐增大时,水膜变厚,引力缩小,水膜又起着润滑作用,外部压实功能比较容易使土粒移动,压实效果渐佳;土中含水量过大时,孔隙中出现了自由水,压实功能不可能使气体排出,压实功能的一部分被自由水所抵消,减少了有效压力,压实效果反而降低。由击实试验所得的击实曲线图(图4-19)可以看出,曲线有一峰值,此外的干容重为最大,成为最大干容重γ0。与之对应的含水量则称为最佳含水量w0。这就得出一个结论:只有在最佳含水量的情况下压实效果最好。
2、土类
在同一压实功能作用下,含粗粒越多的土,其最大干容重越大,而最佳含水量越小,即随着粗粒土增多,其击实曲线的峰点越相左上方移动(图4-20)。施工时,应根据不同土类,分别确定其最大干容重和最佳含水量。
3、压实功能
同一类土,其最佳含水量随压实功能的加大而减小,而最大干容重则随压实功能的加大而增大。当土偏干时,增加压实功能对提高干容重影响较大,偏湿时则收效甚微。故对偏湿的土企图用加大压实功能的方法来提高土的密实度是不经济的,若土的含水量过大,此时增大压实功能就会出现“弹簧”现象。另外,当压实功能加大到一定程度后,对最佳含水量的减小和最大干容重的提高都不明显了,这就是说单纯用增大压实功能来提高土的密实度未必合算,压实功能过大还会破坏土体结构,效果适得其反。
二、路基压实标准
衡量路基的压实程度是工地实际达到的干容重与室内标准击实试验所得的最大干容重的比值,即压实度或称压实系数。
所谓重型击实试验法,是与原来的击实试验法(现称轻型击实试验法)相比较而言的。重型击实法增大了击实功能,从而提高了路基的压实标准。其所得最大干容重,对砂性土约提高6%~10%,粘性土约提高10%~18%;而最佳含水量则有所降低,砂性土为1%~3%,粘性土为3%~9%。
重型击实试验法的原理和基本规律与轻型击实试验法相仿,但击实功能提高了4.5倍。重型与轻型击实法差别大致如表4-6。
三、压实方法
压实土层的密实度随深度递减,表面5cm的密实度最高。填土分层的压实厚度和压实遍数与压实机械类型、土的种类和压实度要求有关,应通过试验路来确定。同样质量的振动压路机要比光轮静碾压路机的压实有效深度大1.5~2.5倍。如果压实遍数超过10遍仍达不到压实度要求,则继续增加遍数的效果很小,不如较小压实层厚。
碾压时,横向接头的轮迹应有一部分重叠,对振动压路机一般重叠40~50cm,对三轮压路基一般重叠1/2后轮宽;前后相邻两区段亦宜纵向重叠1~1.5,应做到无漏压、无死角和确保碾压均匀。
四、压实质量控制与检查
土的压实应在接近最佳含水量的情况下进行。天然土通常接近最佳含水量,因此填铺后应随即碾压。含水量过大时,应将土摊开晾晒至要求的含水量时再整平压实。
填土接近最佳含水量的容许范围,与土的种类和压实度要求有关。在一定的压实度要求情况下,砂类土比细粒土的范围大;在同一种土类的情况下,压实度要求底的比要求高的范围大。范围的具体值可从该种土的击实试验曲线上查的,即在该曲线土的纵坐标上按要求高的范围大。范围的具体值可以从该种土的击实试验曲线上查的,即在该曲线图的纵坐标上按要求的干密度处画一横线,此线与曲线相交的两点所对应的含水量值就是它的范围。
天然土过干需要加水时,可在前一天于取土点浇洒,使水均匀渗入土中;也可将土运至路堤再用水浇洒,并搅拌均匀。加水量可按下式估算:
(4-1)
式中:V——所需加水量(t);
——天然水的含水量;
——最佳含水量;
Q——需加水的土的质量(t)。
此外还应增加洒水至碾压时的水分蒸发消耗量。
在压实过程中,施工单位的自检人员应经常检查压实度是否符合要求。压实度试验方法可采用环刀法、腊封法、水袋法、灌砂法或核子密度湿度仪法。环刀法适用于细粒土,灌砂法适用于各类土。核子密度湿度仪应与环刀法、灌砂法等进行对比标定后方才可应用。
每一压实层均应检验压实度,合格后方可填筑其上一层。
第三节 软土地基路基施工
一、概述
软土在我国滨海平原、河口三角洲、湖盆地周围及山涧谷地均有广泛分布。在软土地基上修筑路基,若不加处理,往往会发生路基失稳或过量沉陷,导致公路破坏或不能正常使用。
所谓软土,从广义上说,就是强度低、压缩性高的软弱土层;以孔隙比及有机质含量为主,并结合其他指标,可将软土划分为软粘性土、淤泥质土、淤泥、泥炭质土及泥炭五种类型,其主要物理力学特征如表4-7。
习惯上常把软粘性土、淤泥质土、淤泥总称为软土,而把有机质含量很高的泥炭、泥炭质土总称为泥沼。
我国各地不同成因的软土都具有近于相同的共性,主要表现在:
1天然含水量高、孔隙比大。含水量再34%~72%之间,孔隙比在1.0~1.9之间,饱和度一般大于95%,液限一般为35%~60%,塑性指数为13~30,天然容重约为15~19kN/m3.
2透水性差。大部分软土的渗透系数为10-8~10-7cm/s。
3压缩性高。压缩系数为0.005~0.02,属于高压缩性土。
4抗剪强度低。其快剪粘聚力在10kPa左右,快剪内摩擦角在0~5°之间。
5具有触变性。一旦受到扰动,土的强度明显下降,甚至呈流动状态。
6流变性显著。其长期抗剪强度只有一般抗剪强度的0.4~0.8倍。在天然软土地基上采用快速施工修筑一般断面的路堤,所能填筑的最大高度,称为极限高度。达到极限高度时单位面积的荷重就是天然地基的极限承载力。路堤超过极限高度后,必须发生大量沉陷、坍滑,必须采取加固措施,才能保证路堤稳定与正常施工。
二、软土地基的加固措施与施工
1、 塑料排水板
塑料排水板是带有孔道的板状物体,插入土中形成竖向排水通道。因其施工简单、快捷,目前国内广泛应用,效果亦佳。
1)排水板材料
排水板是在工厂生产的,国内外都有许多产品出售。按其结构形式可分为多孔单一结构型和复合结构型两大类:
(1)多孔单一结构型——这是一种经特殊加工的两块聚氯乙烯树脂透水板,两板之间仅有若干个点以突缘相接处,而其间留有许多孔隙,故透水性好。这种塑料板具有耐酸碱、不膨胀、不变质等特点。在多孔单一结构型中还有用纤维质无纺布和多孔质材料制成,这种排水板在土压力作用下过水面积减少,排水效果较差。
(2)复合结构型——内为用聚氯乙烯或聚丙烯做成的芯板,外面套以用涤纶类或丙烯类合成纤维制成的滤膜,其断面如图4-23。板宽一般为100mm,厚3~4mm。
塑料排水板应符合质量标准,因此,购进的产品要用正式商标或牌号,并有出场检验合格证,在工地每10万m至少抽一个样品进行检验,合格后方可使用。目前我国已有许多厂家生产塑料排水板。表4-9为南京塑料厂生产的SPB-1系列塑料排水板技术性能。
2)设计方法
目前对塑料排水板的机理及设计均沿用砂井的理论。即将塑料排水板换算成当量直径Dp的砂井,然后按砂井理论进行设计。设塑料板宽度为b,厚度为,则换算公式为:
(4-6)
式中:——换算系数
例如:b=100mm,=4mm,取
,求得
=50mm。
3)施工方法
塑料排水板要用插板机插入土中。插板机种类很多,性能不一,从机型讲,有轨道式、轮胎式、链条式、步履式等多种。图4-24为步履式插板机。从插设方法讲,一类是套管式插板机。另一类是无套管式插板机。前者施工步骤如下:
将塑料排水板由后边的卷筒通过井架上方的滑轮,插入套管内——排水板被套管的输送滚轴夹住,一起压入土中——达到预定深度后,输送滚轴反转松开排水板,上拔套管,塑料排水板被便留在土中——在地面以上20cm左右将排水板切断。
无套管式插板机是用钻杆直接将塑料排水板插入土中。这种插板机较轻便,操作简单,速度快,但塑料排水板容易被损伤或随钻杆拔起,地基强度较大时更不宜使用。
2、 砂井
砂井是利用各种打桩机具击入钢管,或用高压射水、爆破等方法在地基中获得按一定规律排列的孔眼并灌入中、粗砂形成砂柱。由于这种砂井在饱和软粘土中起排水通道的作用,又称排水砂井。砂井顶面应铺设砂垫层,已构成完整的地基排水系统。
软土地基设置砂井后,改善了地基的排水条件,缩短了排水途径,因而地基承受附加荷载后,排水固结过程大大加快,近而使地基强度得以提高。上述塑料排水板以及后面介绍的袋装砂井就是在砂井基础上发展而成的。
砂井适用于路堤高度大于极限高度,软土层厚度大于5m时。
砂井的间距、深度要根据软土的地层情况、允许施工期,由计算确定,砂井直径一般为20~30cm,视施工机械而定。
砂井的施工
1) 入空心管法
在履带起重机的吊壁上安装一个供穿心锤用的导向架,以锤击钢管;或用一个振动锤夹住钢管施以振动力,前者是为冲击式,后者是为振动式。钢管应比砂井长0.5~1.0m,以利拔管。管的底部应有木桩尖、混凝土桩尖或活瓣桩尖。施工步骤如下:
装上桩尖,将钢管定位——靠锤打击或振动器振动使钢管下到要求深度——钢管上拔0.5~1.0m消除桩底真空吸力,以便活瓣张开,然后提起重锤和桩帽,在钢管上口搁上漏斗,先灌入少许水,然后砂水交替灌入——以4~6m/min的速度徐徐拔管,并用大锤不断敲击钢管加速砂子下落。
2) 射水法
这种方法对软土地基扰动最少,但需大量水及要有方便的排水条件。施工步骤如下:
将套管安置在砂井位置上——将射水管放进套管内射水,套管徐徐下沉,若遇到较坚实土层,可用锤轻轻敲击顶部,使套管下沉——套管达到要求深度后,上下移动射水管使套管中的土充分流出——灌砂——拔起套管。
3)爆破法
对于6~7m的浅砂井,用直径76m的螺纹钻钻口,在钻口内放置条形药包,爆炸扩空,孔内灌砂。药包制作过程如图4-25。a)传爆线一端弯成环形,放入10cm宽的水泥纸袋上,按量放炸药于纸上;b)卷严,并用麻绳扎牢;c)为防水,外边用宽3~4cm的塑料布裹缠;d)两端用胶布密封,即成条形药包。用药量与砂井直径、土质情况和埋藏深度有关,只能通过试验确定。
施工步骤如下:
用螺纹钻钻垂直孔,孔深比砂井深度大0.5m,以便放置药包——用管子钳卡住铁管用人力连同药包压入孔内,压入深度比砂井深度大0.2~0.3m,以防孔底回淤——将传爆线一端连在雷管和导火索上,点爆——爆成井孔后即灌水使孔壁不坍塌,经检查后,砂水交替灌入,灌满为止。
3、 袋装砂井
井径对固结时间的影响没有井距那样敏感。从理论上讲,井径只要能满足排水要求即可,软粘土渗透系数一般只有砂井渗透系数的1%,砂井的理论直径可以很小。但一般砂井如果井径太小,即无法施工,也无法放置因地基变形而断开失效。因此,国内外曾广泛采用网状织物袋装砂井,其直径仅8cm左右,比一般砂井省料的多,造价比一般砂井低廉,且不会因施工操作中的误差或地基发生水平和垂直变形而丧失其连续性。
袋装砂井的打孔一般采用钢管打入式和射水式,以打入式为例,施工步骤如下:
将内径约12cm的套管打入土中预定深度——将预先准备好的长度比砂井长2m左右、用聚氯乙烯纤维制成的袋,在底部装入大约一满锹重的砂,并将底口扎紧,然后放入孔内——将袋的上端固定在装砂漏斗上,从漏斗口将干砂边振动边灌入沙袋,装实装满为止——徐徐拔出套管。
4、 排水砂垫层
排水砂垫层是在路堤底部地面上铺设一层较薄的砂层。如图4-26,其作用是在软土顶面增加一个排水面。在填土过程中,荷载逐渐增加,促使软土地基排水固结,渗出的水就可从砂垫层中排走。
为确保砂垫层能顺畅排水,要采用透水性良好的材料,如中砂、粗砂;要保证砂垫层在其使用其间的整体连续性;要防止砂垫层被细粒土所污染而造成堵塞,在砂垫层的上下两侧亦设反滤层。
砂垫层的厚度是直接控制用砂量的主要因素,也是保证整体连续的一个主要条件。确定砂垫层厚度需考虑:一是以不致因地基沉降而使砂垫层发生错断,从而影响排水效果;二是以不致因排到砂垫层中的孔隙水由于水头过高而渗入路堤填土,导致低路堤的强度和稳定性降低。一般采用的厚度为0.6~1.0m。
砂垫层适用于施工期限不紧,路堤高度为极限高度的二倍以内、砂源丰富、软土地基表面无隔水层的情况,当软土层较薄,或底层又有透水层时,效果更好。前述塑料排水板、袋装砂井、砂井等加固措施都要配合设置砂垫层。
5、 土工织物铺垫
在软土地基表层铺设一层或多层土工织物,可以减少路堤填筑后的地基不均匀沉降,又可以提高地基的承载能力,同时也不影响排水。对于淤泥之类高含水量的超软弱地基,再采用砂井及其它深层加固法之前,土工织物铺垫可作为前期处理,以提高施工的可能性。若在砂垫层上增铺土工织物,可以防止填土污染砂垫层。
土工织物的铺设很简单,在工厂将几幅拼缝成需要尺寸,一般宽3.6~4.5m,长比路堤低宽多4~6m,顺路堤坡脚回折2~3m。为了保护土工织物,上下都应铺设厚0.2~0.3m左右的砂垫层。
6、 预压
在软土地基上修筑路堤,如果工期不紧,可以先填筑一部分或者全部,使地基经过一段时间固结沉降,然后在填足和铺筑路面;在拟建涵洞和侨台等结构物处,先填土预压,待地基强度提高到一定程度后,挖去填土在建造结构物。在修筑路堤时还可预先把土填的比设计高度高一些,或加宽填土宽度,以加速地基固结下沉,以后在挖除超填部分。这种预压或超载预压的方法,简单易行,但需较长的固结时间。并常需配合采用砂垫层、砂井等排水措施方能满足工期要求。
预压加荷的速率应保证地基只产生沉降而不致丧失稳定。当路堤较高时,可采取分级加荷,第一级加荷要尽量大一些,预压期都要半年至一年。加荷速率由理论计算或用下列方法确定:
1) 地面沉降速率——埋设沉降板,每1~2天观测一次,要求中线表面日沉降量不大于10mm。
2) 边桩水平位移——边桩长1.0~1.5m,打入地面1.0m左右,要求日水平位移不超过5mm。
3) 地基孔隙水压力——在地基不同深度埋设孔隙水压力计进行观测,要求孔隙水压力不超过预压荷载应力的50~60%。
7、 挤实砂(碎石)桩
挤实砂桩是以冲击或振动的方法强力将砂、石等材料挤入软土地基中,形成直径较大密实柱体,提高软土地基的整体抗剪强度,减少沉降。挤实砂装是以增大土体的密实度为主要目的,它与排水砂井的作用不同。砂桩直径约为0.6~0.8m。施工步骤如下:
将套管就位——提起芯管,灌砂——锤击下沉——沉到设计深度——提起芯管,灌砂——锤击套管和芯管——将砂挤出套管——提起套管和芯管——灌砂,锤击芯管,使砂密实,直至形成砂柱。
挤实砂桩另一种施工方法是利用振动来制成砂桩(称为振实砂桩)。其施工步骤如下:
将上面安有垂直振动器的套管就位——振动下沉——将砂灌入套管中——边振动边使套管上下运动——套管逐步上提——最后形成密实的砂柱。
8、 旋喷桩
利用工程钻机,将旋喷注浆管置入预定的地基加固深度,通过钻杆旋转,徐徐上升,将预先配置好的浆液,以一定的压力从喷嘴喷出,冲击土体,使土和浆液搅拌成混合体,形成具有一定强度的人工地基。旋喷法可以根据不同的施工对象、用途,调整灌入材料用量、浓度,使加固土体满足工程需要的强度。目前灌入材料以水泥浆为主,当土的渗透性较大或地下水流速过大时,为了防止浆液流失,可在浆液中掺加三乙醇铵和氯化钙等速凝剂。
钻机就位和检查——钻进,至预定深度——旋喷并提升钻杆。
9、 生石灰桩
用生石灰碎块置入桩孔中形成桩体,成为生石灰桩。其孔径多用20~40cm,桩长多在12m以内。也有采用更小孔径的,用打入或钻进方法成孔在填入2~5cm的生石灰块。生石灰桩可以掺入一定数量的粉煤灰或砂,有时还掺入少量石膏,以利出发反应,提高强度。
10、换土
采用人工或机械挖除路堤下全部软土,换填强度很高的粘性土和砂、砾、卵石、片石等渗水性材料。换土根本改善了地基,不留后患,效果好。适用于软土层较薄且易于排水施工的情况。水塘、河沟和古埋藏河谷,填土层一般较薄且程局部分布,常采用换土方法予以处理。因软土地区地下水位较高,开发困难,所以采用人工或机械开挖换土时,换土深度一般不宜超过2m。
采用机械开挖,一般可使用索铲挖土机、抓斗等。开挖边坡有直立至1:0.2。开挖时若用水泵抽水,容易引起边坡坍塌,如果用不需压实的良好换填材料,并及时换填,以不排水为宜。
抛石挤淤是强迫换土的一种形式,它不必抽水挖淤,施工简便,这种方法用于湖塘或河流等积水洼地,常年积水且不宜抽干,表层无硬壳,软土液性指数大,厚度薄,片石能沉至下卧硬层的情况。一般用于软土厚度为3~4m。石块的大小视软土稠度而定,一般不宜小于0.3m。抛填片石时,应自中部开始逐次向两侧展开,使淤泥向两边挤出,待抛石露出水面后用重型压路机碾压,其上铺设反滤层,在进行填土。在下卧层层面具有明显横向坡度时,片石抛填应从高向低的一测进行,并在低的一侧多填一些,以求稳定。
爆破排淤也是换土的一种形式。利用炸药爆炸时的张力作用,使软土扬弃或压缩,然后填以强度较高的渗水土或一般粘性土,达到换土的目的。采用爆破排淤的施工方法换填深度较大,功效较高,适用于软土层较厚,稠度大,路堤较高及施工期紧迫的情况。爆破排淤又可分先填侯爆和先爆后填两种施工方法。前者适于稠度较大的软土,先填的路堤随爆随沉,避免回淤。后者适于稠度小的软土。
11、反压护道
反压护道是在路堤两侧填筑一定宽度和一定高度的护道。他利用力学平衡以保持路基的稳定。反压护道一般采用单级形式,由于反压护道本身的高度不能超过极限高度,所以反压护道适用于路堤高度不大于极限高度倍的情况,单级反压护道的高度宜采用路堤高度的1/3~1/2。
反压护道虽然容易,但占地多,在填料来源困难的地方也难于应用;而且,反压护道只能解决软土地基路基的稳定问题,对沉降并无补艺,往往还会加大沉降量。
第四节 山区路基施工
一、 深挖路堑的边坡坡度与形状
路签边坡坡度大于20m时称为深挖路堑。深挖路堑边坡的合理坡度与形状是保证边破稳定的关键,而这又与地层情况有密切关系。
(一)粒土地层
细粒土一般都具有粘聚力和内摩阻角,边坡坡度可以通过圆弧法检算确定。这种路基宜在边破上每隔10m左右的高度上设置宽1~2m平台,形成阶梯式边坡,平台应尽量作在地层分隔处。平台的纵向坡度宜与路线纵坡平行。平台应有1%~2%的向外排水横坡,或设置纵向排水沟,其纵坡不得小于0.3%。折线型边坡由于变坡点易被雨水冲刷破坏,除非与以保护,一般不宜采用。
(二)砂类土地层
砂类土地层的路签边坡坡度可用直线法检算确定。其边破形状同细粒土地层,以阶梯式为好,但
对于边坡上的松散夹层要进行保护。在坡脚处最好设置碎落台,以免堵塞边沟。
(三)砾石土和巨粒土底层
砾石土和巨粒土的路堑边坡坡度通常采用工程地质法确定,即参考当地自然山坡和人工边坡,以及地质构造、水文条件等因素,推断适宜的稳定边坡坡度。其边坡形状也宜采用阶梯式,平台最好设在地层分界处,边坡上的松散夹层应予以防护。
(四)岩石地层
岩石路堑边坡坡度要根据岩体结构和岩性,并参考当地自然山坡和人工边坡,以及以往的经验,论证确定,有条件时,也可用岩石力学的方法进行分析核对。
若层状结构面或镶嵌结构的一组主要节理面或几组主要节理面的交线倾角陡于30 °,且走向大致与路线平行时,可按此倾角开挖边坡,否则应做支挡工程。若岩层为散粒结构,颗粒之间完全脱离,或已风化成碎石、砂和土状,或受断裂构造挤压成角砾或泥质时,这种岩层已丧失岩石性质,边坡坡度应按砾石土或细粒土考虑。
关于岩石边坡的形状,对于块状结构、层状结构和镶嵌结构的岩体,可采用一坡到顶的直线形变坡;对于破碎结构和散粒结构的岩体,若上下的破碎程度有显著差别,可采用适应于该层稳定性的折线边坡,或在分界处设置平台,形成阶梯式边坡;对于由软硬岩层交替组成的互层结构,当交互层次多而薄,或软层厚而硬层薄时,可按软岩性质作成直线形边坡,并对边坡进行全面防护;当软层和硬层均比较厚时,宜在分界处设平台,形成阶梯式边坡,并对软层予以防护。
二、岩石的开挖方法
岩石路堑通常采用爆破法开挖,有条件时宜采用松土法开挖,局部情况亦采用破碎法开挖。
(一) 爆破法开挖
1、爆破材料
1)炸药
炸药的种类繁多,工程中常用的有以下几种:
铵梯炸药——它属于混合炸药中硝铵类炸药,呈黄色粉末状,有硝铵、三消基甲苯(TNT)和木份等配合而成。路基工程中常用的二号岩石铵梯炸药,其配比为85:11:4。铵梯炸药受潮和结块后,爆炸性能会降低,而生成的有毒气体明显增加。湿度超过3%则可能拒爆,湿度大于0.5%时不得用于地下爆破,大于1.5%不得用于露天爆破。
铵油炸药——由硝酸铵和柴油(或加木粉)的混合物,通常两者比例为94.5:5.5(称为3号铵油炸药),当加木粉时,其比例为92:4:4(称为1号铵油炸药)。铵油炸药取材方便,成本低廉,使用安全,但具有吸湿结块性,不能久存,最好现拌现用。
胶质炸药——主要由硝化甘油和硝酸钾(或硝酸钠)组成,另外加入二硝化乙二醇、硝化棉、木粉等。常用的硝化甘油及二硝化乙二醇含量各为62%和35%的耐冻胶质炸药。这些炸药较敏感,容易分解、渗油和挥发而提高敏感性,冻结后触动即可爆炸,危险性较大。但它的爆炸威力大,不吸湿,有较高密度和可塑性,适用于下水和坚硬岩石爆破。
黑火药——用硝酸钾、硫磺和木炭按一定比例(最佳为75:10:15)混合而成。好的黑火药为深灰色的颗粒,不粘手。对火星和碰撞极敏感,威力低,适用于开采石料。
2)起爆材料
雷管——有火雷管和电雷管两种。火雷管即普通雷管,一般为10个号码,通常用6~8号;电雷管又分为基法、延法和毫秒三种。
导火索(引火线)——用来传递火焰引爆火雷管或直接引爆黑火药。
导爆索(传爆线)——爆速快,适用于深孔、洞室爆破及水下爆破,可提高爆破效果。
电气点火装置——引发电雷管用。
2、药包量计算
药包量计算就是求一个炮孔所需炸药的质量。爆破一定体积的岩石所需的炸药量与很多因素有关,一般是根据爆炸效果要求,由经验公式求得。
3、爆破方法
1)表面爆破
炸药直接放在岩石表面(或用土和草皮覆盖)进行爆破。效率很低,只用在爆破少量分散的岩石。
2)浅孔爆破
炮孔直径小于75mm,深度不超过5m。通常用手提式凿岩机打孔。适用于工作量不大的岩石路堑,或作为其他炮型的辅助炮型。
3)深孔爆破
是指孔径大于75mm,深度5m以上的爆破。炮孔多采用冲击式钻机和潜孔钻机打成,在配合挖运机械可实现石方施工机械化。深孔爆破每次爆破的石方量大,从而可加快施工进度,应该广泛采用。其炮孔主要参数如下:
抵抗线长: (m)
式中: H——台阶高度(m);
D——硬度系数,取0.64~0.56;
d——炮孔直径(mm);
——高度影响系数,见表4-11。
炮眼深度:L=(1.0~1.5)H(m)
孔距:
排距:b(m),方格布置b=a;三角形布置b=0.87a。
4)光面爆破和预裂爆破
光面爆破是在开挖限界的周边,适当排列一定间隔的炮孔,在有侧向临空面的情况下,用控制炸药的方法,预先炸出一条裂缝,使爆体分开,作为隔震减震带,起保护和减弱开挖界限以外山体或建筑物的地震破坏作用。光面爆破及预裂爆破之后,在边坡壁上通常均留下半个炮孔的痕迹。
进行光面或预裂爆破时,应严格保持炮孔在同一平面内,炮孔间距a和抵抗线W之比应小于0.8。装药量应控制适当,并采用合理的药包结构,通常使炮孔直径大于药卷直径1~2倍,或采用间隔药包、间隔钻孔装药。预裂炮的起爆时间在主炮之前,光面炮在主炮之后,其间隔时间取25~50ms。统一排孔必须同时起爆,最好用传爆线起爆,否则会影响爆破质量。光面爆破和预裂爆破的主要设计参数,归纳如下:
光面炮眼间距
预裂炮眼间距
光面炮眼抵抗线 W0=1.33
装药密度
式中:d——钻孔直径,cm;
——每m钻孔装药量,kg/m;
a、 w的单位与d同。
4、爆破施工作业
1)炮位选择
炮孔的位置、方向和深度都会直接影响爆破的效率,合理的选择炮孔位置十分重要。选择时,应注意岩石的结构,避免在层理和裂缝处凿孔,以免药包爆炸时,气体油裂缝泄出,降低爆破效果或失效。炮孔应选在临空面较多的方位,或者有意识的改造地形使第一次给第二次爆破创造较多的临空面。
2)凿岩(钻孔)
凿岩设备有空压机、凿岩机和钻孔机等。对于浅孔,大多采用风钻,向下钻孔时,使用轻型手动式风钻,向上或倾斜方向钻孔时,采用支架式重型风钻。对于深孔,可使用冲击钻机,回转钻机等。
3)装药与堵塞
装药方式有以下几种:
集中药包——炸药完全装在炮孔的底部,对于工作面较高的岩石,崩落效果好,但不能保证岩石均匀破碎;
分散药包——炸药沿孔深的高度分散装置,可使岩石破碎均匀,适用于高作业面的开挖段;
药壶药包——炮孔底部制成葫芦型储药式,以增大装药量,适用于量大而集中的石方爆破。
装完药后,应对药孔进行堵塞,防止漏气。堵塞材料可用干砂、粘土、碎石和滑石粉等。
4)起爆和清方
起爆就是通过导火索等起爆器材使炮孔内的炸药爆炸,有火花起爆、电力起爆等方法。
爆破后,应组织机械配合运输工具将石方运出现场,以利再次爆破或进行其他作业。
清方机械的选择,正铲挖掘机的适应性强,但进出工点比较缓慢。轮式装载机机动灵活,可铲装较大的石块,但卸载高度不如挖掘机,此外,装载机可以自铲、自装、自运。通常,清方工作的运距在40~100m时宜用装载机,100m以上宜用挖掘机配合自卸卡车,小于40m时宜用推土机。
(二)松土法开挖
开挖岩石除了采用爆破法之外,松土法也越来越被广泛采用。松土法是充分利用岩体自身存在的裂面和结构面,用推土机牵引的松土器将岩体翻碎,在用推土机或装载机与自卸汽车配合,将翻松了的岩块搬运出去。
(三)破碎法开挖
这种方法是用破碎机凿碎岩块。凿子装在推土机或挖掘机上。它利用活塞的冲击作用,使凿子产生冲击力,因此,其破碎岩块的能力决定于活塞的大小。它利用活塞的冲击作用,使凿子产生冲击力,因此,其破碎岩块的能力决定于活塞的大小。破碎法宜用于岩体裂缝较多,岩块体积较小,抗压强度低于100Mpa的岩石。破碎法的工作效率不高,不宜作为开挖岩石的主要方法,仅用于不能使用爆破法或松土法施工的局部场合。
三、高填路堤
凡填方边坡高度超过20m(填粗砂、中砂者为12m)者,称为高填路堤。
高填路堤的边坡形状,填料为细粒土时,一般宜采用折线形边坡。
四、填石路堤
填石路堤一般是指石质挖方路段的开挖石块填筑的路堤。
五、路基排水设施
(一) 路基地面排水措施
路基地面排水设施的作用是将可能停滞在路基范围内的地面水迅速排出,并防止路基范围外的地面水流入路基内。
1、边沟
挖方地段和填土高度小于边沟深度的填方地段均应设置边沟,用以汇集和排除路基范围内或流向路基的少量地面水。边沟的断面形式,一般土质边沟宜用梯形,矮路堤或机械化施工时可用三角形,在场地宽度受到限制时,可用石器矩形。石质路堑边沟可作为矩形,积雪、积砂路段宜做成流线型。梯形边沟的内侧边坡一般为1:1到1:1.5,外侧边坡与路堑边坡相同,有碎落台时外侧边坡与内侧相同,三角形边沟内侧边坡可用1:2~1:3,外侧边坡通常与挖方便坡一致。边沟的深度和底宽一般不应小于0.4m,干旱地区及分水点可采用0.3m。高速公路和一级公路的边沟断面能大一些,其深度和底宽可用0.8~1.0m。
边沟沟底纵坡通常与路线纵坡一致;但路线纵坡小于0.2%时,应采用变化边沟深度的办法以保证其纵坡不小于0.2%;当纵坡大于3%时应考虑加固,以免发生冲刷;边沟长度一般不宜超过300m,三角形边沟不宜超过200m。
一般不允许将截水沟的水排入边沟内,如特殊情况需排入时,宜应加大边沟断面,并予以加固。
2、截水沟
设在路堑坡顶外或山坡路堤上方,用以截拦上方流来的地面水。其断面形式一般为梯形,在地面横坡较陡时可做成石砌矩形。截水沟底宽不小于0.5m,深度按流量确定,但不应小于0.5m。土质截水沟的边坡一般为1:1~1:1.5。沟底纵坡通常不得小于0.5%,特殊困难时,亦不得小于0.2%。沟底纵坡较大或有防渗要求时予以加固。截水沟长度不宜超过500m。
堑顶外截水沟,有弃土堆时,设在弃土堆之外,无弃土堆时,距堑顶边缘至少5m(黄土地区至少10m,并需加固防渗);山坡路堤上方截水沟离开路堤坡脚至少2m。
3、排水沟
其作用是将边沟、截水沟、取土坑或路基附近的积水引入就近桥涵或沟谷中去。排水沟的断面和纵坡要求与截水沟基本相同。紧靠路堤护坡道外侧的取土坑,若条件适宜,可用以排水,这时,取土坑底部宜做成自两侧向中部倾斜2%~4%的横坡。出入口应与所连接的排水沟平顺衔接;当出口部分为天然沟谷时,不要使水形成漫流。
4、跌水和急流槽
在纵坡陡峻地段的截水沟、排水沟、可用单级或多级跌水或急流槽连接。跌水和急流槽的断面一般采用矩形,用浆气片石或混凝土修筑,进口部分始端和出口部分终端的群墙应埋在冻结线以下。
急流槽的主体部分应每隔2~5m设置一个防滑平台,嵌入地基内。急流槽的纵坡不宜陡于1:1.5。
5、拦水带
为避免高路堤边坡被路面汇集的雨水冲坏,可在路肩上做拦水带,将水流拦截至挖方边沟或在适当地点设急流槽引离路基。拦水带高出路肩15~20cm,埋入25~30cm,拦水带顶宽,浆气片面为25cm,混凝土为15cm。设拦水带的内侧路肩应适当加固。
(二) 路基地下排水设施
1. 明沟和槽沟
明沟和槽沟都是用与兼排地面水和浅层地下水的设施(图4-30)。
当设置在路基旁侧时宜顺路线方向布置;当设置在山坡上的低洼地带或天然沟谷时宜顺山坡沟谷走向布置。
沟谷宜埋入不透水地层内。沟壁上最下一派渗水孔(或缝隙)的底部高出沟底不小于0.2m,并宜略高于沟中设计流量的水流表面。沟的深度可按上述条件决定。
为避免开挖断面过大和节省圬工,明沟深度一般不宜超过1.2m,再深时可改用槽沟,槽沟深度不宜超过2.0m,再深时可改用渗沟。
2. 边坡渗沟
边坡渗沟用于疏干潮湿的边破和引排边坡上局部出露的上层滞水和泉水,并起加固边坡的作用。适用于坡度不小于1:1的土质路堑边边坡,也常用于加固潮湿的容易发生表土坍滑的土质路堤边坡。
边坡渗沟应垂直嵌入边坡。对于较小范围的局部湿土,宜用条带形布置,对于较大范围的局部湿土,宜用分岔形布置。当边坡表土普遍潮湿时,宜用拱形于条带型相结合的布置。
边坡渗透基底埋置在边坡潮湿土层以下较干而稳定的土层内。可按潮湿带的厚度做成具有泄水坡(2%~4%)的阶梯形,最下一个台阶的长度宜大一些,基底一般用5号浆砌片石铺砌。
边坡渗沟断面通常采用矩形,其宽度不小于1.2m。深度视边坡潮湿土层的厚度而变。由于边坡渗沟集引的地下水流量较小,故可只在其底部用大粒径石料填充做为排水通道,其外周设置适当的反滤。渗沟内部的其余空间可用筛洗干净的小颗粒渗水材料填充。
分岔形渗沟的分岔部分和拱形渗沟的拱部断面下侧可用粘土填筑,做成防渗层。
边坡渗沟的顶部一般用单层干砌石覆盖,其表面大致与边坡面齐平。必要时可在干砌片石表面用水泥砂浆勾缝。
边坡渗沟下部的出水口一般采用干砌片石垛,其作用是支挡渗沟内部的填充料并将渗沟中集引的水排入边沟内,其位置一般放在边沟的外面。
边坡渗沟应从下游向上游开挖,而且各条边坡渗沟要间隔开挖,还要及时回填。
3. 引水和截水渗沟
引水渗沟用以引出低洼湿地或泉水出露地带或地下凹槽地层处的地下水,或用以降低路基范围内的地下水。截水渗沟用以截断流向路堑的地下水。路堑边沟下过边沟旁的引水渗沟一般顺边沟走向布置,但其排水出口部分则宜偏离路基。其他引水渗沟可布置成条带状或树枝状,其主沟轴线宜循最短通路将所集引的地下水排至路基范围以外。截水渗沟应布置在渗流上游较稳定的地层内,其平面布置宜尽可能与渗流方向垂直。
截水渗沟的基底必须置入不透水地层以内,引水渗沟可以不置入不透水地层内。
引水和截水渗沟断面采用矩形(图4-31),内部用筛洗干净的渗水材料填充,填充料与沟壁之间须设置反滤层。
其底部的排水通道,通常采用盖板矩形沟(边墙及基底用7.5号浆砌片石筑,盖板用15号混凝土预制)或圆管(用15号混凝土预制)。截水渗沟只需在渗流上游一侧沟壁进水,下游侧沟壁可用粘土或浆砌片石作成隔渗层。
截水和引水渗沟应从下游想上游开挖,并应随挖随作支撑,以防坍塌;反滤层填筑时,各层要用薄板隔开,同时填筑,至一定高度后,上抽隔板,继续填筑,至要求高度为止,顶部覆以单层干砌片石,表面用水泥砂浆勾缝,其上再用厚度不小于0.5m的土 填到与地面齐平。
六 、路基坡面防护
易于冲蚀的土质边坡和易于风化的岩石路堑边坡,在风化营力和雨水冲刷的作用下,将会发生冲沟、溜坍、剥落、掉块和坍塌等坡面变形,故必须及早采取相应的防护措施。
(一)植物防护
植物防护是一种施工简单、费用低廉、效果较好的坡面防护措施。植物能覆盖表土,防止雨水冲刷;调节土的湿度,防止产生裂缝;固结土壤,避免坡面风化脱落,同时还能起到保护环境,美化路容的作用。
1. 种草
适用于草类能生长的土质路堑和路堤边坡,其坡度小于1:1.25,且高度不高者。若边坡土层不宜种草,可将边坡挖成台阶,然后铺一层5~10cm厚的种植土。草籽应选用适合当地土质和气候条件的根系发达、茎干低矮、枝叶茂盛、生长能力强的多年生草种。播种草籽一般在春、秋季,按撒播或行播进行,草籽埋入深度应不小于5cm。为使草籽均匀分布,可先将种子与砂、干土或锯末混合后撒播。路堤的路肩和路堑的堑顶边缘应埋入与坡面齐平的宽20~30cm的带状草皮。
2. 平铺草皮
适用于各种土质边坡,极严重风化的岩石和严重风化的软质岩石边坡,坡度不小于1:1。
草皮应选择根系发达、茎矮叶茂的耐旱草类。草皮规格一般为宽20cm,长30cm,厚5~10cm,干燥炎热地区厚度可增加到15cm。草皮应铺过堑顶肩部至少100cm,或铺至截水沟。
铺草皮一般应在春季或初夏进行,气候干燥地区则应在雨季进行。铺设前将边坡表层挖松整平,洒水润湿。草皮应与坡面密贴,四周用木桩或竹桩钉固。
3. 植树
适用于各种土质边坡和极严重风化的岩石边坡,边坡坡度不陡于1:1.5。树种应为根系发达、枝叶茂盛、能迅速生长分 之底矮灌木。乔木不利于边坡的稳定,不宜采用。植树间距40~60cm。植树之坑深一般为25cm,直径20cm。应在当地植树季节栽种。
(二)灌浆及勾缝
灌浆适用于较坚硬的、裂缝较大较深的岩石路堑边坡;勾缝适用于较硬、不易风化、节理裂缝多而细的岩石路堑边坡。灌浆可用1:4或1:5的水泥砂浆,裂缝很宽时,可用混凝土灌注。勾缝用1:2或1:3的水泥砂浆,也可用1:0.5:3或1:2:9的水泥石灰砂浆,灌浆和勾缝前应先冲洗坡面,并清除裂缝内的泥土杂草。
(三)抹面
适用于尚未严重风化的各种易风化岩石边坡,但对由煤系岩层及成岩作用很差的红色粘土岩组成的边坡不适用。边坡坡度不受限制,但坡面应较干燥。抹面使用年限较短,一般为8~10年。
抹面厚度3~7cm,分为2~3层。抹面护坡之周边与未防护坡面衔接处应严格封闭,其措施为:凿槽嵌入岩石内,嵌入深度不小于10cm,并和衔接之坡面平顺;坡脚宜设1~2m高的浆砌片石护坡。
在软硬岩石相间的边坡上,仅对软层抹面时,在分界处,抹面也应嵌入硬岩层内至少10cm,当需增强抹面的抗冲蚀能力和防止开裂时,可在表面涂沥青保护层。
抹面前须将边坡表面的风化岩石清刷干净;边坡上大的凹陷应用浆砌片石嵌补,宽的裂缝应灌浆。采用石灰炉渣浆抹面时,在灰浆抹上后,稍干即进行 拍,直至表面出浆为止,然后抹平涂上速凝剂。抹面不宜在严寒季节、雨天及日照强烈时施工,其适宜的气温为4℃~30℃,并注意盖草洒水养生。如发现裂纹或脱落要及时灌浆修补。
(四)捶面
适用于易受冲刷的土质边坡或易风化剥落的岩石边坡,边坡坡度不大于1:0.5,使用年限为10~15年。
捶面厚度为10~15cm,一般采用等厚截面,当边坡较高时,采用上薄下厚截面,捶面护坡与未防护坡面衔接处应封闭,其措施与抹面相同。坡脚设1~2m高的浆砌片石护坡,捶面材料常用石灰土、二灰土等。
捶面前应清除坡面浮石松土、嵌补坑凹,有裂缝时应勾缝。在土质边坡上,为使护面贴牢可挖小台阶或锯齿。坡面应先洒石灰水润湿,捶面时 拍要均匀,提浆要及时,提浆后2~3h进行洒水养生3~5d。寒冷地区不宜在冬季施工。养护时如发现开裂和脱落应及时修补。
(五)喷浆及喷射混凝土
适用于易风化但尚未严重风化的岩石坡度,坡面较干燥。对高而陡的边坡,上部岩层较破碎而下部岩层完整的边坡和需大面积防护的边坡,采用此种类型更为经济。对成岩作用差的粘土岩边坡不宜采用。
喷浆厚度不宜小于5cm,喷射混凝土厚度以8cm为宜,分2~3次喷射。喷浆及喷射混凝土的护坡的周边与未防护坡面之衔接与抹面护坡相同。坡脚应作1~2m高的浆砌片石护坡。
(六)单层干砌片石护坡
干砌片石厚度一般为0.3m,其下设不小于0.1m厚的碎石或砂砾垫层;基础应选用较大石块砌筑,其埋深至侧沟底,基础与沟相联时,采用5号浆砌片石筑;施工应自上而下进行栽砌,彼此镶紧,接缝要措开,缝隙见用小石块填满塞紧。
(七)浆砌片石护坡
适用于各种易风化的岩石边坡。若用于路堤边坡上,应待路堤沉实后再施工;边坡坡度不易于1:1。
浆砌片石护坡一般采用等截面,其厚度视边坡高度及陡度而定,一般为0.3~0.4m。边坡过高时应分级设平台,每级高度不宜超过20m,平台宽度视上级护坡基础的稳固要求而定,一般不小于1m。当护坡面积大,而边坡较陡时,为增强护坡的稳定性,可采用肋式护坡。
(八)浆砌片石骨架护坡
在土质边坡和极严重风化的岩石边上,可采用浆砌片石骨架,在在骨架内铺草皮、捶面或栽砌卵石。
浆砌片石骨架一般采用方格型,间距3~5m,与边坡水平线成45°角。护坡的顶部0.5m及坡脚1m,用5号浆砌片石镶边;骨架应嵌入坡面一定深度,其表面与草皮或捶面齐平。
(九)浆砌片石护墙
浆砌片石护墙能防治比较严重的坡面变形,适用于各种土质边坡及易风化剥落的岩石边坡。边坡坡度不大于1:0.5。分等截面和变截面两种形式(图4-32)。
等截面护墙高度,当边坡为1:0.5时,不宜超过6m;当边坡缓于1:0.5时,不宜超过10m。
变截面护墙高度,单级不宜超过20m,否则应采用双级或三级护墙,但高度一般叶柄宜超过30m。双级或三级护墙的上墙高不应大于下墙高,下墙的截面应比上墙大,上下墙之间应设错台,其宽度应使上墙修筑在坚固牢靠的基础上,一般不宜小于1m。
等截面护墙厚度一般为0.5m,变截面护墙顶宽b一般为0.4m,底宽B根据墙高H而定:
七、岸坡冲刷防护
沿河路基受到流水冲刷时,应采取冲刷防护措施。冲刷防护工程一般分为岸坡防护(直接防护)、导流构造物防护(间接防护)和改移河道三种类型。山区狭窄河谷地段不宜设置导流构造物,也难于改移河道,宜优先考虑岸坡防护措施。常用的岸坡防护有:
(一) 草皮护坡
草皮可用于流速不大于1.8m/s地段的河岸防护。
草皮护坡多采用叠砌台阶式,如图4-33。草皮尺寸为25×40cm,厚为10~15cm,叠砌前先平整坡面,
将草皮紧贴坡面,并用柳枝尖桩或竹尖桩顶紧,桩长为0.3~0.5m。在坡脚部分,一般铺草皮2~3层,伸出坡脚外的宽度可视具体情况决定,但不应小于1.0m,铺砌层的表面应与地面齐平。
(二)抛石防护
抛石防护的应用很广,对于经常浸水且水深较深地段的路基边坡防护及洪水季节防洪抢险时更为常
用。在缺少较大的石料地区,也可用预制混凝土块作为抛投材料。为了减少坡脚处的局部冲刷及增加抛石的稳定性,抛石堆的水下边坡不宜陡于1:1.5,当水深较深流速较大时,不宜陡于1:2~1:3,抛石防护的顶端不应小于所用最小石块尺寸的2倍,所抛石料应选用质地坚硬、耐冻且不宜风化崩解的石块。为了使抛石有一定的密度,宜用不小于计算尺寸的大小不同的石块掺杂抛投。
抛石防护除防洪抢险外,一般应枯水季节的施工。
新建路基的抛石防护。可采图4-34a的断面形式。在既有路基边坡防护抛石时,一般采用图4-34b的形式。
(三)干砌片石护坡
此种护坡用于周期性浸水的河岸或路基路基边坡防护。适用于洪水时水流较平顺,不受主流冲刷且流速小于3m/s的地段。根据护坡的厚度常分为单层的或双层的两种。
为了防止边坡内细粒土被水流冲淘出来,并为了增加护坡的弹性,以抵抗力的冲击作用,应在护坡面层与边坡土之间设置1~2层的砂、砾垫层,垫层厚10~15cm。
干砌片石护坡砌筑前应先夯实整平边坡,砌筑石块要互相嵌紧。干砌片石护坡基础,当冲刷深度小于1.0m,可才用墁石铺砌基础(图3-35a)。当冲刷深度大于1.0m时,宜才用浆砌片石脚墙基础(图4-35b)。
(四)浆砌片石护坡
用于经常浸水的受主流冲刷或受较强烈的波浪作用的路基边坡防护和河岸及水库边岸防护,亦可用于有流冰及封冻的河岸边坡防护。
护坡砌筑石料宜选用坚硬、抗压强度大于30Mpa、遇水不崩解的石料。水泥沙浆在非严寒地区可使用7.5号,在严寒地区应使用10号。浆砌片石护坡下设置10~15cm的卵、砾石垫层。
(五)石笼防护
石笼防护的优点是具有较好的柔性,而且可利用较小的石料。当水流中含有大量泥砂时,石笼中的空隙能很快淤满,而形成一个整体的防护层。其缺点是铁丝容易锈蚀,使用期限一般为8~12年。当水流中带有较多的滚石时,容易将铁丝网冲破,不宜使用石笼防护。用于防护坡岸时,一般在最下的一层采用扁长方体石笼,其余宜采用长方体石笼的垒砌形式。
第五章 基层(底基层)施工技术
基层(底基层)可分为无机结合料稳定类和粒料类。无机结合料稳定类又称为半刚性型或整体型,常包括水泥稳定类、石灰稳定类和综合稳定类。粒料经常分为嵌锁型和级配型。
半刚性基层材料的显著特点是:整体性强、承载力高、刚度大、水稳性好,而且较为经济。国外高等级公路上越来越多地采用半刚性基层。国外常采用水泥稳定粒料、石灰粉煤
灰稳定粒料、粘压水泥混凝土或贫水泥混凝土作为沥青路面的基层。
第一节 半刚性基层材料的强度形成原理及缩裂特性
一、强度形成原理
(一) 石灰稳定类材料强度形成原理
石灰稳定类包括石灰土、石灰砂砾土、石灰碎石土等。其强度形成主要指石灰与细粒
土的相互作用。
土中掺入石灰,石灰与土发生强烈的相互作用,从而使土的工程性质发生变化。初期表现为土的结团、塑性降低、最佳含水量增大和最大密实度减小等;后期变化主要表现在结晶结构的形成,从而提高土的强度与稳定性。
石灰加入土中发生的物理与化学反应主要有离子交换、Ca(OH)2(氢氧化钙)的结晶、碳酸化和火山灰反应。其结果使粘土胶粒絮凝,生成晶体Ca(OH)2、CaCO3(碳酸钙)和含水硅、铝酸钙等胶结物,这些胶结物逐渐由胶凝状态向晶体状态转化,致使石灰土的刚度不断增大,强度与水稳定性不断提高。
离子交换反应是指石灰加入土中,在水的参与下易离解成Ca2+和(OH)—离子,Ca2+可与粘土胶体颗粒反离子层上的K+、Na+离子发生离子交换,其结果使得胶体吸附层减薄,从而使粘土胶体颗粒发生聚结,土的湿坍性得到改善。离子交换是石灰土初期强度形成的主要原因。Ca(OH)2的结晶反应是石灰吸收水分形成含水晶体,所生成的晶体相互结合,并与土粒结合起来形成共晶体,把土粒结成整体,从而使石灰土的水稳性得到提高。碳酸化反应是指Ca(OH)2与空气中的CO2反应生成CaCO3的过程,当水灰土的表层发生碳酸化反应,形成一层硬壳,从而阻碍CO2的渗入,使碳酸化反应过程较长,所以它是石灰土后期强度增长的主要原因之一。火山灰反应是指土中的活性硅铝矿物在石灰的碱性激发下解离在水的参与下与Ca(OH)2反应生成含水的硅酸钙和铝酸钙的过程,所生成新的化合物与水泥水解后的产物相类同,是一种水稳性良好的结合料。火山灰反应是在不断吸收水分的情况下逐渐发生的,因而具有水硬性性质。碳酸化与火山灰反应对提高石灰土的强度与稳定性起着决定性作用。
影响石灰土强度与稳定性的主要因素有:土质、石灰的质量与剂量、养生条件与龄期等。
各种成因的亚砂土、亚粘土、粉土类土和粘土类土都可以用石灰来稳定。一般来说,粘土颗粒的活性强、比面积大、表面能量也较大,因而掺入石灰等活性材料后,所形成的离子交换、碳酸化作用、结晶作用和火山灰作用都比较活跃,故石灰土强度随土的塑性指数增大而增大。但土质过粘时,不易粉碎和拌和,反而影响稳定效果,且易形成缩缝。石灰土的强度随土的PH值的增大而增大,这是因为土中溶液的碱性较大时,有利于土中硅铝矿物等的解离,从而促进石灰与土之间火山灰反应及其它化学反应的进行。
各种化学组成的石灰均可用于稳定土。但白云石石灰的稳定效果优于方解石石灰。活性CaO+MgO的含量越高,稳定效果越好。石灰细度越大,其比面积愈大,在相同剂量下与土粒的作用愈充分,反应进行的越快,因而效果越好。生石灰在灰土中消解可放出大量热能,加速灰土的硬化,另外,刚消解的石灰成胶状Ca(OH)2,其活性和溶解度均较高,能保证石灰与土中胶粒更好的作用,因而,采用生石灰稳定土的效果优于熟石灰稳定土。
石灰剂量是按消石灰占干土重的百分率计。石灰剂量较低时(小于30~40%),石灰主要起稳定作用,使土的塑性、膨胀性、吸水性降低,具有一定的水稳性。随着石灰剂量的增加,石灰土强度和稳定性提高,但剂量超过一定范围,过多的石灰在空袭中以自由灰存在,将导致石灰土的强度下降。石灰土的最佳剂量随土质不同而异,土的分散度越高则最佳剂量越大。最佳石灰剂量也与养生龄齐有关,在28d内,最佳石灰剂量随着龄期的增长而增大,28d后基本趋于稳定。这是因为,时间短,参与反应的石灰数量就少,多余的石灰以“自由”状态存在,对强度不利。随着龄器的增长,参与反应的石灰逐渐增多,所需的石灰数量也相应增多,而28d后,反应渐趋缓慢,最佳石灰剂量也就趋于稳定。
石灰土的强度形成需要一定的温度和湿度。高温和适当的湿度对石灰强度的的形成是有利的,这是因为,温度高可使反应过程加快,适当的湿度为Ca(OH)2结晶和火山灰反应提供了必要的洁净水。但湿度过大(湿砂养生)会影响新生物的胶凝结晶硬化,从而影响石灰土强度的形成。石灰土的强度随龄期的增长大体符合指数规律。
(二) 水泥稳定类材料强度形成原因
水泥稳定类包括水泥稳定砂砾、砂砾土、碎石土、土等,其强度的形成是水泥与细粒
土的相互作用。
水泥矿物与土中的水分发生强烈的水解和水化反应,同时从溶液中分解出Ca(OH)2并形成其它水化物。水泥的各种水化物生成后,有的自行继续硬化形成水泥石骨架,有的则与土相互作用,其作用形式有:离子交换及团粒化作用、硬凝反应、碳酸化作用。
在水泥水化后的胶体中,Ca(OH)2和Ca2++2(OH)-共存。而构成粘土的矿物是以SiO2为骨架合成的板状或针状的结晶,通常其表面带有Na+和K+离子。析出的Ca2+与土中的Na+和K+离子进行当量吸附交换。其结果使大量的土粒形成较大的土团。由于水泥水化生成物Ca(OH)2具有强烈的吸附活性,而使这些较大的土团粒进一步结合起来,形成水泥土的链条状结构,并封闭土团之间孔隙,形成稳定的联结。
随着水泥水化反应的深入,溶液中析出大量Ca2+,当Ca2+的数量超过上述离子交换需要量后,则在碱性环境中使组成粘土矿物的SiO2和Al2O3的一部分或大部分同Ca2+进行化学反应,生成不溶于水的稳定的结晶矿物(即硬凝反应),增大了土的强度。
水泥水化物中的游离Ca(OH)2不断吸水中的HCO3-和空气中的CO2,生成CaCO3。这种反应能使土固结,提高土的强度,但比硬凝反应的作用差一些。
影响水泥稳定土强度与稳定性的主要因素有土质、水泥成分与剂量、水等。
土的类别和性质是影响水泥稳定土强度的重要因素之一。土的矿物成分对水泥稳定土的性质有重要影响。除有机质或硫酸盐含量高的土外,各种砂砾土、砂土、粉土和粘土均用水泥稳定。有少量蒙脱石类矿物和不含腐殖质的各种碳酸盐土、覆盖粘土和冰渍粘土用水泥稳定后可取得良好效果。由石英颗粒所组成的最佳级配土,由于土体的密实度很大而保证了水泥能充分表现其结合性质,因而适于用水泥稳定。黑土腐殖层,尤其是草皮灰化土的腐殖层,用水泥稳定得到的强度最低。用水泥稳定含有大量蒙脱石和过于亲水的碱土其效果亦较差。
就土的粒度而言,适宜于用水泥稳定的土的范围相当广泛。但要达到规定的强度,水泥剂量随粉粒和粘粒含量的增加而增高。因此,稳定重粘土水泥用量过高而不经济,且重粘土难于粉碎和板和。实践证明用水泥稳定级配良好的土,既节约水泥,又能取得满意的稳定效果。
水泥的成分和剂量对水泥稳定土的强度有重要影响。通常认为,各种类型的水泥都用于稳定土。实践证明,对于统一种土,水泥矿物成分是决定水泥稳定土强度的主导因素。一般情况下,硅酸盐水泥的稳定效果较好,而铝酸盐水泥则较差。当水泥的矿物成分相同时,水泥稳定土的强度随着水泥比表面和活性的增大而提高。在硬化条件相似的情况下,当水泥的矿物成分相同时,随着水泥分散度的增大,其化学活性和硬化能力有所增长。
水泥稳定土的强度随水泥剂量的增加而增加,但考虑到水泥稳定土的抗温缩与抗杆缩以及经济性,应有一个合理的水泥用量范围。
含水量对水泥稳定土的强度有重大影响。当混合料中含水量不足时,水泥就要与土争水,若土对水有较大的亲和力,就不能保证水泥完成水化和水解作用。水泥稳定土需要湿法养生,以满足水泥水化的需要。水泥剂量大、养生温度高时,其增长速率大。水泥稳定土的强度随龄期的增长而增长,二者之间大致成指数关系。
(三) 综合稳定类材料强度形成原理
综合稳定类是指以水泥或石灰为主要结合剂、外掺少量活性物质或其他材料,以提高
和改善土的技术性质。
1、 石灰粉煤灰(以下简称二灰)稳定类
二灰稳定类包括二灰、二灰土、二灰砂、二灰砂砾、二灰碎石等。
单纯用石灰稳定砂性土效果一般较差,而采用二灰综合稳定则效果显著提高。粉煤灰是一种火山灰物质,它含有活性的氧化硅和氧化铝,在石灰的碱性激发及相互作用下生成含水的硅铝酸钙。这些新生的胶凝物质晶体具有较强的胶结能力和稳定性。由于粉煤灰系空心球体,所以掺入粉煤灰后,石灰土的最佳含水量增大、最大干密度减少。
2、 水泥石灰综合稳定类
在水泥稳定土中,由于水泥和水的数量均比其在水泥混凝土中的数量要少得多,再加
上土又是一种分散度极高的材料(与砂石料相比),它能强烈地与水泥水化的产物发生各种反应,从而破坏了水泥正常水化与硬化的条件,致使水泥不能充分发挥自身应有的作用。为了改善水泥在途中的硬化条件,提高水泥稳定效果,常常在掺加水泥的同时掺加少量其它添加剂。
二、半刚性基层材料的缩裂特性
半刚性基层材料的缺点是抗变形能力低,在温度或湿度变化时易产生开裂,当沥青面层较薄时,易形成反射裂缝,进而严重影响路面的使用性能。了解各种半刚性基层材料的缩裂规律,有利于工程技术人员科学地进行高等级公路路面基层的选型、材料配合比设计和施工,从而把裂缝减少到最低程度。
第二节半刚性基层材料的要求及组成设计
一、对原材料的一般要求
(一) 原材料试验项目
1、含水量 用烘干法、含水量快速测定仪或酒精法确定材料的含水量。
2、颗粒分析 用筛分法(含土材料用湿筛分析法)测定级配是否符合要求并确定
材料配合比。
3、液限与塑限 计算塑性指数并审定是否符合规定(100g平衡锥测液限,搓条法测塑限)。
4、对密度与吸水率 用多孔网篮或容积1000cm3以上的比重瓶测定相对密度与吸水率,用以评定粒料质量。
5、压碎值 评定石料的抗压碎能力是否符合要求(压碎值仪测定)。
6、有机质和硫酸盐含量 确定土是否适宜于用石灰或水泥稳定(对土有怀疑时作此项试验)。
7、有效钙镁含量确定石灰质量,通用滴定法或钙电极法测定。
8、水泥标号和终凝时间 确定水泥的质量,是否适宜应用。
9、烧失量 确定粉煤灰是否适用。
(二) 对原材料的一般要求
1、土质
堆土质的一般要求是宜于粉碎,满足一定级配,便于碾压成型。
1) 液限与塑性指数
水泥稳定类使,土的液限不易超过25%。塑性指数不易超过6;用水泥稳定粒径较
均匀的砂时,难于碾压,可在砂中掺入少量塑性指数小于12的粘性土(亚粘土);二灰稳定类时,土的塑性指数为12~20;石灰稳定类时,土的塑性指数为15~20。
2) 颗粒组成
用作基层时,集料最大粒径不应超过30mm(方孔筛,下同);用作底基层时,集
料最大粒径不应超过40mm。最大粒径太大,拌和、摊铺、压实均有困难,表面平整度也难达到要求。最大粒径太小,则动稳性不足且投资增加。水泥稳定类材料用作底基层时,土的均匀系数应大于5,实际中宜选用均匀系数大于10(均匀系数指通过量为60%的筛孔与通过量为10%的筛孔尺寸的比值)。水泥稳定类集料的颗粒组成应满足表5-2的要求。表中2号级配可用于基层,1号可用于底基层。二灰稳定类集料适宜的级配组成见表5-3。
3) 压碎值
半刚性基层材料所用的碎、砾石应具有一定的抗压碎能力。二级和二级以下公路
的集料压碎值不大于35%(底基层可放宽至40%);一级、高级公路的集料压碎值不大于30%。
4) 硫酸盐与腐殖质
水泥稳定时,土的腐殖质含量不应大于2%,硫酸盐含量不应大于0.25%。腐殖质
含量超过2%以及塑性指数偏高的土,不应单用水泥稳定,若需采用这种土,必须先用石灰进行处理之后,方可用水泥稳定。石灰及二灰稳定类所用土的有机质含量不应超过10%,硫酸盐含量不应超过0.8%。
2、无机结合料
无机结合料目前最常用的是水泥、石灰和粉煤灰。
1) 水泥
普通硅酸盐水泥、硅酸盐水泥、矿渣水泥或火山灰水泥都用于稳定土,但应选用终
凝时间较长(宜在6h以上)的水泥。快凝水泥、早强水泥以及受潮变质的水泥不应使用。宜采用标号低的水泥(如325)。
2) 石灰
石灰质量应符合Ⅲ级以上的生石灰或消石灰的技术指标。实际使用时,要尽量缩短
石灰的存放时间,如需存放较长时间,应采取覆盖封存措施妥善保管。
3) 粉煤灰
粉煤灰的主要成份是SiO2、Al2O3、Fe2O3、CaO,前两种成份的总含量应大于70%。
根据CaO含量的大小,粉煤灰可分为硅铝粉煤灰(CaO含量一般在2%~6%)和高钙粉煤灰(CaO含量为10%~40%)。我国的粉煤灰含CaO、MgO量较少,约3%~5%,因此,不具备自行结硬的特性。粉煤灰的烧失量一般小于10%,有的在20%以上,烧失量过大,将明显降低混合料的强度,有的甚至难于成型。粉煤灰的粒径变化范围0.001~0.3mm,但大部分在0.01~0.1mm之间,其比表面积一般在2000~3500cm2/g之间。干粉煤灰和湿粉煤灰都可以应用。干粉煤灰如堆在空地上,要加水,防止飞扬造成污染。湿粉煤灰的含水量不易超过35%。使用时,应将凝固的粉煤灰块打碎或过筛,同时清除有害杂质。
3、 水
一般人、畜引用的水源均可使用。
二、混合料配合比设计的一般原则与实验项目
(一) 一般原则
混合料组成设计所要达到的目标是:所设计的混合料组成在强度上满足设计要求、抗裂性达到最优且便于施工。
混合料组成设计的基本原则是结合料剂量合理、尽可能采用综合稳定以及集料应有一
定级配。
混合料组成中,结合料的剂量太低则不能成为干刚性材料,剂量太高则刚度太大,容易脆裂。实际上,限制低剂量是为了保证整体性材料具有基本的抗拉强度,以满足荷载作用的强度要求。限制高剂量可使模量不致过大,避免结构产生太大的拉应力,同时降低收缩系数,使结构层不会因温度变化而引起拉伸破坏。
采用水泥、石灰综合稳定时,混合料中有一定水泥可提高早期强度,有一定石灰可使刚度不会太大,掺入一定数量的粉煤灰可以降低收缩系数,必要时可根据材料性质和施工季节,加入早强剂和其它掺剂。
集料应有一定的级配。集料数量以达到靠拢而不紧密为原则,其空隙让无机结合料填充,形成各自发挥优势的稳定结构。
(二) 混合料试验项目
1、重型击实试验 确定最佳含水量和最大干密度,以规定工地碾压时的合适含水量和
应达到的最小干密度;确定制备强度试验和耐久性试验的试件所应该用的含水量和干密度;确定制备承载比试件的材料含水量。
2、承载比 求工地预期干密度下的承载比,确定材料是否适宜作基层或底基层。
3、抗压强度 进行材料组成设计,选定最适宜于用水泥或石灰稳定的材料(包括土),规定施工中所用的结合料剂量,为工地提供质量评定标准。
4、耐久性 用于湿循环或冻融循环试验确定适宜于用石灰或水泥稳定的材料,探索石灰水泥稳定材料在潮湿冰冻条件下的使用性能。
三、半刚性基层材料组成设计的现行方法
现行混合料组成设计的主要内容是根据表5-4的强度标准值(七五研究成果),通过试验选取适宜于稳定的材料,确定材料的配比以及最大干密度和最佳含水量。表中所列数值指龄期为7d(温度6d、浸水1d)的无侧限抗压强度。
具体设计步骤如下:
1、制备同一种土样、不同结合料剂量的混合料,水泥和石灰的剂量可参考表5-5、5-6所列数值。
二灰稳定类混合料试件的制备可根据不同情况进行。对硅铝粉煤灰,采用石灰粉煤灰作基层或底基层时,石灰与粉煤灰之比可以是1:2~1:9。采用石灰粉煤灰土做基层或底基层时,石灰与粉煤灰的比常用1:2~1:4(对于粉土,以1:2为宜)。石灰粉煤灰与细粒土的比例可以是30:70~90:10。采用石灰粉煤灰粒料做基层或底基层时,石灰与粉煤灰的配比常用1:2~1:4,石灰粉煤灰与级配粒料(中粒土和细粒土)的配比可以是1:6~1:4,石灰粉煤灰与粒料的配比也可以用1:1左右,但后者可能强度较低,裂缝较多。
2、采用重型击实试验确定各种混合料的最佳含水量和最大干密度,至少做三个不同水泥或石灰剂量混合料的击实试验,即最小剂量、中间剂量和最大剂量。其它剂量混合料的最佳含水量和最大干密度用内插法确定。
3、按工地预定达到的压实度,分别计算不同结合料剂量时试件应有的干密度。
4、按最佳含水量和计算得到的干密实度制备试件,进行强度试验。作为平行试验的试件数量应符合表5-7中规定。如试验结果的偏差系数大于表中规定的值,则应重做试验,并找出原因,加以解决。如不能降低偏差系数,则应增加试验数量。
5、时间在规定温度下保湿养生6d,浸水1d,进行无侧限抗压强度试验,试验温度为:冰冻地区202℃,非冰冻地区25
2℃。计算试验结果的平均值和偏差系数。
6、根据表5-4的强度标准,选定合适的结合料剂量。此剂量试件室内试验结果的平均抗压强度应满足如下公式的要求:
(5-1)
式中:——设计抗压强表(表5-4);
——试验结果的偏差系数(以小数计);
——标准正态分布表中随保证率(或置信度
)而变的系数。高等级公路上应取保证率95%,此时
=1.645。
工地实际采用的石灰或水泥剂量应较室内试验确定的剂量多0.5%~1.0%。
石灰土稳定碎石和石灰土稳定砂砾,仅对其中的石灰土进行组成设计,对碎石和砂砾,只要求它具有较好的级配。石灰土与碎石砂粒的重量比宜为1:4。二灰稳定粒料的组成设计,则应包括全部混合料(或25mm以下的粒料)。条件不具备时,可仅对二灰进行组成设计,确定二灰的配合比后,在二灰中掺入一定比例的粒料。
五、二灰稳定材料的早强问题
二灰稳定类材料后期强度高,隔温性和水稳性好,但其早期强度低,影响交通开放,在重交通道路上也常因早强不足而导致路面早期破坏。在低温条件下,其强度增长率更低,这就限制了基层的施工季节。因此,如何提高二灰稳定类材料的早期强度,是目前公路工程技术人员较为关注的问题之一。
掺加少量水泥或化学添加剂可提高二灰稳定类材料的早期强度。掺入少量水泥可提高早期强度,但不足之处在于工艺上有初、终凝时间限制,且其早期强度的提高主要来源于水泥水化产物的形成,而粉煤中含有的SiO2、Al2O3并未得到充分的发挥和利用。因此,用掺加化学添加剂提高二灰稳定类的早期强度是有效途径之一。
第三节 半刚性基层施工
在我国,高等级公路干刚性基层施工中,混合料的板和方式有路拌法和厂拌法,其摊铺方式有人工和机械两种。从施工程序来看,一般是先通过修筑试验路段,制定标准施工方法后进行大面积施工。
一、修筑试验路段
在进行大面积施工之前,修筑一定长度的试验路段是很必要的。目前在我国高等级公路基层修筑实践中,许多施工单位通过修筑试验路段,进行施工优化组合,把主要问题找出来,并加以解决,由此提出标准施工方法用以指导大面积施工,从而使整个工程施工质量高、进度快,经济效益显著。
修筑试验路段的任务是:检验拌和、运输、摊铺、碾压、养生等计划投入使用设备的可靠性;检验混合料的组成设计是否符合质量要求及各道工序的质量控制措施;提出用于大面积施工的材料配合比及松铺系数;确定每一作业段的合适长度和一次铺筑的合理厚度;提出标准施工方法。
二、半刚性基层的大面积施工
(一) 路拌法施工
拌刚性基层或底基层路拌法施工的主要工序为:准备下承层施工测量
备料
摊铺
拌和
整平与碾压成型
初期养护。
1、下承层准备与施工测量
施工前对下承层(底基层或土基)按质量验收标准进行验收,并精心加工。之后,恢
复中线,直线段每20~25cm设一桩,平曲线段每10~15m设一桩,并在两侧路面边缘外0.3~0.5m处设指示桩,在指示桩上用红漆标出基层(或底基层)边缘设计标高级松铺厚度的位置。
2、备料
所用材料应符合质量要求,并根据各路段基层(底基层)的宽度、厚度、及预定的干密度,计算各路段需要的干燥集料数量。根据混合料的配合比、材料的含水量以及所用车辆的吨位,计算各种材料每车料的堆放距离,对于水泥、石灰等混合料,常以袋(或小翻斗车)为计算单位,故应计算出每袋结合料的堆放距离。也可根据各种集料所占的比例及其松干密度,计算每种集料松铺厚度,以控制集料施工配合比,而对结合料(水泥、石灰等)仍以每袋的摊铺面积来控制剂量。
3、摊铺与拌和
用平板机、推土机或人工按试验路段的松铺系数进行摊铺,摊铺力求均匀。摊铺工作就绪后,就可使用稳定土路拌机进行拌和作业。常用路拌机规格与型号参见第二章。路拌时,首先调整液压分配阀的控制手柄,使路拌记得工作装置渐渐深入混合料之中达到标尺要求的深度,这样拌和机就可以工作速度开始作业,工作速度以1.2~1.5km/h最为适宜。当然,不同的拌合条件,最佳拌和速度是不同的。在拌和开始阶段要反复检查拌和深度,是否留有“夹层”或切入下承层太深。拌和路线应自基层的最外延向中心线靠拢。拌和中适时测定含水量,如含水量大于最佳时,应进行自然蒸发,使含水量达到最佳值。若含水量小于最佳值,应补充洒水进行拌和。一般在摊铺洒水时,用水量应稍大些,这样可避免二次拌和所造成的浪费。
4、 碾压
拌和好的混合料以平地机整平,并刮出路拱,然后进行压实作业。无机结合料稳定类
结构层应用12t以上的压路机碾压。用12~15t三轮压路机碾压时,每层的压实厚度不应超过15cm;用18~20t的三轮压路机碾压时,每层的压实厚度不应超过20cm。对于稳定中粒土和粗粒土,采用能量大的振动压路机时,每层的压实厚度根据试验确定,压实厚度超过上述规定时,应分层铺筑,每层的最小压实厚度为10cm。压实应遵循先轻后重、先慢后快的原则。直线段,由两侧路肩向路中心碾压,即先边后中;平面线段,由内侧路肩向外侧路肩进行碾压。
碾压过程中,如有“弹簧”、松散、起皮等现象,应及时翻开重新拌和,或用其它方法方法处理,使其达到质量要求。在碾压结束之前,用平地机再终平一次,使其纵向顺适,路拱和超高符合设计要求。终平应仔细进行,必须将局部高出部分刮出并扫出路外,对于局部低洼之处,不再进行找平,留待铺筑沥青层时处理。
5、 养生与交通管理
重视保湿养生,养生时间应不少于7d。水泥稳定类混合料碾压完成后,即刻开始养生,
二灰稳定类混合料是在碾压完成后的第二或第三天开始养生。养生期结束,应立即铺筑沥青面层或做下封层。基层上未铺筑封层和面层时,不应开放交通。当施工中断,临时开放交通时,也应采用保护措施。
(二) 厂拌法施工
厂拌法施工前,应先调试拌和设备。调试的目的在于找出各料斗闸门的开启刻度(简
称开度)以确保按设计配合比拌和。先要测定各种原材料的流量——开度曲线。然后按厂拌设备的实际生产率及各种原材料的设计重量比计算各自的要求流量,从流量——开度曲线上可查出各个闸门的刻度。按得出刻度试拌一次,测定其级配、含水量及结合料剂量,如有误差则个别调整后再试拌。一般试拌一、二次即可达到要求。拌和生产中,含水量应略大于最佳值,使混合料运到现场摊铺后碾压时的含水量不小于最佳值,按照合同或规范要求,在拌和厂抽检混合料的配合比。将拌和好的混合料送到现场,如运距远,车上混合料应覆盖,以防水分损失过多。用平地机、摊普机、摊铺箱或人工按松铺厚度摊铺均匀,如有粗细颗粒离析现象,应以机械或人工补充拌和,如果采用摊铺机施工,厂拌设备的生产率、运输车辆及摊铺机的生产率应尽可能配套,以保证施工的连续性。其它工序同路拌法。
目前,我国高等级公路的半刚性基层施工多采用集中厂拌和摊铺机摊铺,修筑的基层平整度、高程、路拱、纵坡和厚度都达到了规范或合同的要求。从而避免了人工或平地机施工中配料不准、拌和不匀、反复找平、厚度难以控制等问题,不仅提高了工程质量,而且加快了工程进度。实践证明:提高高等级公路基层施工质量的根本出路在于机械化。因此,我们建议,基层施工应尽可能采用集中厂拌和摊铺机摊铺的施工方法。当条件不具备时,低基层施工方可采用路拌和人工摊铺。图5-1为二灰砂砾机械化施工工艺流程图。
三、施工中应注意的几个问题
(一) 施工季节
无机结合料稳定类结构层宜在春末或夏季组织施工,施工期的最低气温应在5℃以上,并保证在冻前有一定成型期,即第一次重冰冻(-3~-5℃)到来之前的半月至一个月(水泥类)及一个月至一个半月(石灰与二灰类)完成。若不能完成则应覆盖土层以防冻融破坏。
在雨季施工水泥稳定类结构层时,应特别注意气候变化,勿使水泥混合料雨淋,并采取措施排出表面水,勿使运到路上的集料过分潮湿。
(二) 水泥稳定类材料施工作业长度的确定
确定水泥稳定类混合料的作业长度,应综合考虑水泥的终凝时间、延迟时间对施工质量的影响、施工机械的效率及气候条件等因素,并尽可能减少接缝。水泥稳定类混合料从拌和到碾压之间延迟时间宜控制在3~4h。必须延长延迟时间时,不应超过水泥终凝时间。因此,必须采用流水作业法,各工序必须紧密衔接,尽量缩短从拌和到完成碾压之间的延迟时间。一般情况下,每一流水作业段长以200m为宜。
(三) 路拌法施工中土与粉煤灰用量的控制
再二灰稳定类基层施工中,石灰剂量可以检测,土与粉煤灰的比例只能在施工中加以控制,若控制不好,不仅影响强度,还会使压实度检测失去意义。实际上,土与粉煤灰不同于砂砾和碎石,后者在装卸或摊铺过程中体积变化不大,而土和粉煤灰经装卸、运输和摊铺等,都能使密度变化,室内测量的松干密度总是偏小。如用其松干密度计算虚铺厚度将使工地用量偏多。此外,工地的运土工具较杂,难以用堆土距离控制。因此,可用稳压厚度控制配比的方法,即固定稳压的亚路机型及遍数,实测稳压后土及粉煤灰的干密度。反过来,通过抽检稳压厚度来控制土与粉煤灰的比例。
(四) 接茬处理
石灰、二灰稳定类基层施工中,两工作段的衔接处应搭接拌合。即前一段拌和后,留5~8m,不进行碾压。后一段施工时,将前段留下未压部分,一起再进行拌合,对于水泥稳定类基层,当天两工作段的衔接处理方法同前,但应对前一段未压部分要再加水泥,重现拌和。当天最后一段水泥稳定类基层施工完后,将已压成段末端切成垂直断面,在第二天摊铺下段时,应在前一天余留未碾段内添加部分水泥,并与下段一起拌和。
拌和机及其他机械不宜在已成型的结合料稳定层上“调头”。若必须在其上“调头”时,应采取保护措施(加铺覆盖层等)。
(五) 养生期的探讨
半干刚性基层分层施工时,下层碾压完后,可立即铺筑上层,不需专门的养生期,但在铺筑上层之前,应始终保持下层表面潮润。
基层完工后,养生期一般宜少于7d。养生期结束,方可铺筑沥青面层或做封层。在近年来高等级公路半刚性基层路面修筑实践中,一些施工单位在基层混合料中掺入早强剂,养生不到7d,就已做上面层,但禁止重车通行。还有一些施工单位在干刚性基层施工后2~3d内就铺筑面层,这种做法的理由是基层板体形成前,铺筑面层并压实是对基层的进一步压实,不会引起破坏,而且因沥青面层覆盖,减少了基层水分蒸发,基层的强度形成所需的水分自身能够满足。对二灰稳定类,基层因其强度形成较慢,更适于基层与面层的连续施工。但也有人认为:沥青混合料摊铺温度较高,加速了基层表面水分蒸发,沥青面层未压实前,水分从沥青混合料孔隙中蒸发,影响其层强度的形成。关于这一问题,目前仍无定论,还需进一步研究。缩短养生期以加快工程进度,是无机结合料稳定类基层施工中必须解决的现实问题。
第四节 粒料类基层(低基层)施工技术
粒料类基层按强度构成原理可分为嵌锁型与级配型。嵌锁型包括泥结碎石、泥灰结碎石、添隙碎石;级配型包括级配碎石、级配砾石、复合级配的天然砂砾、部分砾石经扎制掺配而成的级配砾、碎石等。
一、 粒料类基层强度形成原理
(一)嵌锁型
嵌锁型基层,其强度主要依靠碎石颗粒之间的嵌索和摩阻作用所形成的内摩阻力,而颗粒之间的粘结力是次要的,级这种结构层的抗剪强度主要取决于剪切面上的法向应力和材料内摩阻角。它由三项因素构成:粒料表面的相互滑动摩擦;剪切时体积膨胀而需克服的阻力;粒料重新排列而受到的阻力。
(二)级配型
级配型粒料基层的强度和稳定性取决于内摩阻力和粘结力的大小。因此,其强度与稳定性在很大程度上取决于集料的类型(碎石、砾石或碎砾石)、集料的最大粒径和级配以及混合料中0.5mm以下细料的含量及塑性指数。同时,还与其密实度有很大关系。因此,对级配型,主要控制最大粒径、细料含量及其塑性指数和现场压实度。
二、 级配碎石基层的材料要求
(一)碎石
级配碎石用作基层时,碎石的最大粒径不应超过30mm。粒经过大,石料宜离析,也不利于机械摊铺、拌和及整平。碎石中的扁平、长条颗粒的总含量应不超过20%,材料应清洁。用作基层时,级配碎石的颗粒组成见表5-8,其中2号级配可用作联结层。级配曲线应接近圆滑,避免同一种尺寸的颗粒过多或过少。
级配碎石所用石料的压碎值应满足:一级和高速公路的基层小于26%;一级、高速公路的底基层和二级公路的基层小于30%;二级公路底基层和二级以下公路的基层小于35%。
(二)石屑或其他细集料
石屑或其他细集料可以使用一般碎石场的细筛余料,也可用扎制沥青表处和贯入式用石料时的细筛余料,或专门扎制的细碎石。
当级配碎石中细料塑性指数偏大时,塑性指数与0.5mm以下的细料含量的乘积应符合:在年降雨量小于600mm的中干和干旱地区,地下水位对土基没有影响时,应不大于120;在潮湿多雨地区,应小于100。
三、级配碎石基层的施工
(一) 施工中应注意的问题
级配碎石基层施工力求做到:集料级配要满足要求,配料必须准确,特别是细料的塑
性指数必须符合规定,掌握好虚铺厚度,路拱横坡符合规定,拌和均匀,避免粗细颗粒离析。
级配碎石应在最佳含水量时,采用12t以上的压路机压实至要求的密实度,压实度以
重型击实标准计。采用12t以上三轮压路机的每层压实厚度以不超过15~18cm为宜,采用重型振动压路机或轮胎压路机时每层压实厚度可为20~23cm。
基层未洒透层沥青或未铺封层时,不应开放交通,以免表层破坏。
第五节 质量控制与验收
一、施工质量控制
施工过程质量控制的主要项目有:含水量、集料级配、石料压碎值、结合料剂量、无侧限饱水抗压强度、拌和均匀性、压实度、弯沉值等。表5-10中列出了主要试验项目的测定频度和质量标准。
外形管理项目有高程、厚度、宽度、恒坡度、平整度等,其测定频度和质量标准列于5-11中。
二、检查验收
基层(底基层)检查验收的内容包括竣工后的外形和质量,通常以1km长的路段为评定单位,采用大流水作业法施工时,也可以每天完成的段落未评定单位。抽样检查必须是随机的。
竣工外形的检查数量和合格标准值见表5-12
三、质量控制与验收中几个问题的探讨
1、 压实度检测方法
基层(底基层)压实度的检测方法最常用的有环刀法和灌砂法。环刀法主要用无机结合料稳定细粒土类,灌砂法可于各种类型的基层(底基层)。灌砂法测定结果较准确。水袋法与核子密度仪法目前在我国褒贬不一,尚未推广。高等级公路基层施工不仅要求质量高,而且速度快,现有的测试手段难以适应,特别在有些情况下,往往因检测影响了工程进度。因此,必须寻求新的检测手段。在压实度检测中,国外采用光电技术测定粒料基层的压实度,原苏联将光电测试设备安装在一对覆印轮上,将测定轮与覆印轮的位移差输入光电装置显示,从而给出压实度指标。瑞典DYNAPAC、德国BOMAG公司及我国自己研制的YS-1型压实计的应用大大提高了检测速度与精度,具有广阔的应用前景。
2、 厚度检测方法
厚度检测是外形管理的重要内容之一,常用的方法有定点水平测量法、挖坑测厚(与灌砂法一起进行)和取芯样等。当采用厂拌法施工时,定点水平测量能精确反映结构层厚度,但当采用路拌机拌和施工时,定点水平测量法所得结果偏小,这是因为路拌机往往在拌和中或多或少会切入下承层一定深度。当然施工层厚度的增加是以削弱下承层厚度为代价,在一定范围内不会造成强度不足的问题。但应避免路拌机切入下承层过深,而导致施工层强度不足及下承层厚度减少过多的问题,严格控制拌和深度。建议路拌法施工中,以取芯样或挖坑测厚。
3、 无侧限抗压强度的快速测定
无机结合料类基层(底基层)施工质量控制中,无侧限抗压强度(R)测定是按常规方法制备试样,养生6d,浸水1d进行的,用时较长。因此,国内外许多科研施工单位探索快速养生检测无限抗压强度的途径。我国以对石灰土提出了以6h、9h、和18h蒸养测得的R值推算7d的R值的回归公式,即
(5-11)
式中:——标准养生测定的R(MPa);
——某小时蒸养测定的R(MPa)。
实际应用推荐9h蒸养。
在我国,利用短杆贯入击数作为石灰土强度测定的辅助方法,也得到了应用。
4、 弯沉测定结果验收标准
粒料类基层(底基层)碾压完后,可立即测定其表面弯沉值。而对无机结合料稳定类结构层,其强度随龄期增长较多,对水泥稳定类,常采用28d龄期的强度和参数作为设计依据;而对石灰及二灰稳定类,则宜用90h龄期的强度和参数作为设计依据。因此,碾压完成后初期测得的弯沉值,不能直接用来判定基层或底基层的强度或承载力是否达到了要求。已具有经验或资料的地区,可以根据当地的经验进行弯沉值的检测。
从严格意义上讲,对于高等级公路基层(底基层)万沉值的检验标准值得进一步研究。基层(底基层)表面的弯沉值指标是由路面表面容许弯沉值按弹性层状体系理论反算而得,而现行规范的容许弯沉值公式是过去十几年大量调查研究和统计得到的,因而对目前我国高等级公路半刚性基层沥青路面设计的适应性值得探讨。另外,容许弯沉值是指在设计年限末的不利季节,在标准轴载作用下,容许出现的最大回弹弯沉。而结构层表面初期弯沉值与容许弯沉值到底有何定量关系目前尚无定论,若用容许弯沉值作为初期整体强度检查与验收的标准,显然是不合理的。
总之,基层(底基层)质量控制与验收中的检测方法及有关质量标准将会随着高等级公路的建设而逐步得到改进和完善。
第六章 沥青路面施工技术
沥青路面具有表面平整、无接缝、行车舒适、耐磨、噪音低、施工期短、养护维修简便,且适宜于分期修建等优点,因此得到了广泛的应用。国外大部分高等级公路路面采用沥青混凝土面层。在我国,高等级公路路面面层的最常见类型为沥青混凝土和沥青碎石(见表5-1)。
通常,把未经摊铺、碾压的沥青混凝土混合料和沥青碎石混合料统称为沥青混合料,本章主要对沥青混合料的材料要求、组成设计及拌和、摊铺、碾压等问题进行讨论。
第一节 沥青混合料的强度机理及材料要求
根据矿料最大粒料的不同,沥青混凝土混合料分为粗粒式、中粒式和砂砾式;按标准压实后的剩余空隙率还可将其分为Ⅰ型(剩余空隙率为3%~6%,城市道路为2%~6%)和Ⅱ型(剩余空隙率为6%~10%)。沥青碎石混合料分为粗粒式、中粒式和细粒式。
沥青混合料按其强度构成的不同可分为嵌挤型和级配型两大类。嵌纪型沥青混合料的强度是以矿料之间的嵌挤力和内摩阻力为主、沥青的粘结作用为辅而构成。沥青碎石就属此类,这类混合料是以颗粒较粗、尺寸均匀的矿料构成骨架,沥青结合料填充其空隙,并把矿料粘结成一个整体。这类沥青混合料的结构强度受自然因素(温度)的影响较小。
按密实级配原则构成的沥青混合料的结构强度,是以沥青与矿料之间的粘结力为主,矿料的嵌挤力和内摩阻力为辅而成的。
悬浮密实结构:由连续级配矿料组成的密实混合料,即矿料从大到小连续变化,并且各有一定数量。实际上同一档较大颗粒都被较小一档颗粒挤开,大颗粒犹如悬浮于较小颗粒之中。这种结构通常按最佳级配原理进行设计,密实度与强度较高,但受沥青的性质影响较大,故稳定性较差。
骨架空隙结构:粗粒料彼此紧密相接,细粒料的数量较少,不足以充分填充空隙。因此,混合料的空隙较大,矿料能充分形成骨架。这种结构中,粗粒料之间的内摩阻力起着重要的作用,其结构强度受沥青的性质影响较小,因而稳定性较好。
骨架密实结构:是综合以上两种方式组成的结构。混合料中既有一定数量的粗粒料形成骨架,又根据粗粒料空隙的多少加入细料,形成较高的密实度。间断级配即是按此原理构成。
二 强度机理
沥青混合料的强度由两部分组成,一是矿料之间的嵌挤力与内摩擦力;二是沥青与矿料之间的粘结力。
1、 矿料之间的嵌挤力与内摩擦力
沥青混合料中嵌挤力与内摩擦力的大小,主要取决于矿料的尺寸均匀度、颗粒形状与表面粗糙度。矿料尺寸较大、颗粒均匀、有棱角、表面粗糙时,所组成的混合料具有较大的嵌挤力与内摩阻力。沥青含量对摩阻量大小也有影响,摩阻力随沥青含量的减少而增大。沥青的粘度、混合料的温度和受荷载时的变形速度,对沥青混合料的嵌挤力和内摩阻力的影响极小。
2、 沥青混合料的粘聚力
沥青混合料的粘聚力主要取决于:矿料与沥青材料之间相互作用所形成的粘结力和沥青本身的粘聚力。
沥青与矿料互相作用使沥青在矿料表面产生化学组分的重新分布,在矿料表面形成一层扩散结构膜,此膜以内的沥青称为结构沥青,此膜以外的称为自由沥青。结构沥青与矿料之间的相互作用,并使沥青性质发生改变;自由沥青与矿料之间不发生作用,仅将分散的矿料结合起来,使沥青的性质不改变。如果矿料颗粒之间的接触处由扩散结构膜所联结,则会使沥青的粘滞度增高,并使扩散结构膜接触面积增大,从而获得更大的粘结力。如果矿料颗粒之间为自由沥青所联结,则粘结力较小。
矿料表面形成沥青扩散结构膜的主要原因是沥青与矿料两界面之间相互作用过程中产生了物理吸附、化学吸附和选择性扩散吸附等比较复杂的多样性吸附过程。
物理吸附是沥青与矿料之间由于分子力(即范德华力)作用所产生的一种吸附过程。它普遍存在于矿料与沥青(吸附剂与被吸附物)之间,其吸附程度主要取决于作用各相接触界面的的表面性质,而主要是表面自由能的作用。提高物理吸附可通过在沥青中掺加表面活性物质,使沥青更好的裹覆矿料表面,在矿料表面形成吸附层。但在一定条件下,物理吸附过程是可逆的,即矿料表面吸附的沥青膜在水的作用下产生剥离。
化学吸附是沥青中的某些物质(如沥青酸)与矿料表面的金属阳离子发生化学反应,生成沥青酸盐,在矿料表面形成吸附层的过程。化学相互作用力的强度,超过分子作用力许多倍。因此当沥青与矿料形成化学吸附层时,相互间的粘结力远大于物理吸附,也只有产生化学吸附,沥青混合料才具有良好的水稳性。化学吸附的产生与否以及吸附程度,决定于沥青与矿料的化学成分。例如在沥青中含有沥青酸与沥青酸酐能与碱性矿料中的高价金属盐产生化学反应,生成不溶于水的有机酸盐,而与酸性矿料之间只产生物理吸附。煤沥青中既有酸性物质(如酚类)又有碱性物质()因而与酸性和碱性矿料都能起化学吸附作用。
三、材料的基本要求
组成沥青混合料的是沥青和矿料。
(一)沥青材料
沥青材料有道路石油沥青、软煤沥青、液体石油沥青等。根据“七.五”研究成果,我国高等级公路沥青路面的石油沥青技术要求建议值如表6-1所示。表中加热后针入度比是测定加热损失后的样品针入度与原针入度之比乘100,即得出残留物针入度占原针入度的百分比数。
在有条件时,应测定沥青在60摄氏度时动力粘度(Pa.s)和135摄氏度的运动粘度(m2/s),并在检验报告中注册。沥青标号应根据当地气候条件、施工季节及气温、路面类型、矿料性质和施工方法等予以选用。
随着公路交通的发展,交通密度及车辆轴重明显增加,对路用沥青材料也不断提高的新技术要求,为了反映这些新的要求,近年来,许多国家的沥青技术标准都有了相应的修订。其发展趋势有如下特点:
1.采用年度级化分标号。由于25摄氏度不能真实反映沥青的路用性能,因此,多采用60摄氏度的动力年度来划分等级,并采用135摄氏度(考虑施工温度)时的运动粘度指标与之匹配。
2.使用的粘度等级提高、划分等级减少。随着车辆轴载及交通密度的增加,使用的沥青粘度提高,同时在使用中并不需要太多的等级(标号),故等级数也减少(通常为4--5个等级),且大多为间断划分(我国目前为连续划分标号)。
3.评定指标的项目减少。为便于生产实际应用,评定指标的项目明显减少。
4.用加热老化后的沥青性能作为平定的依据。原始性能沥青相同的沥青,加热老化后的性能差别可能很大,故测定原始性能无多大实际意义。目前,多采用薄膜烘箱实验后的性能作为评定依据。
(二)矿料
沥青混合料所用的矿料有碎石、轧制砾石、石屑、砂和矿粉。
1。粗集料
沥青面层所用粗集料的粒径规格宜按表格不符合表6-2规定,但确认与其他材料配合后的级配符合各类沥青面层的材料使用要求时,也可使用。
粗集料不禁应洁净、干燥、无风化、无杂质、而且应具有足够的强度和耐磨性以及良好的颗粒形状,其技术要求见表6-3,安定性实验根据需要进行,石灰岩用于高级公路时,石料压碎值指标可放宽至28%
,但必须得到主管部门批准/对高级公路沥青层面的碎石不宜采用鄂式破碎机加工。抗滑表层使用的粗集料应尽量选用坚硬、耐磨、抗冲击的碎石或扎制砾石,其技术要求见表6-4。石料磨光值是必须进行的指标,道瑞拨耗损失及石料冲击值根据需要进行。不良路段指高速公路的立体交叉口,急弯陡坡路段及集镇附近。
轧制砾石的质量与碎石要求相同。轧制砾石用作高等 等级公路沥青棉层的沥青混合料时,粒径大于5mm
的颗粒中至少有两个破裂面以上的含量应不小于50%。
酸性石料(花岗岩、石英岩)不宜用于高等级公路,不得不使用时,宜使用针入度较底的沥青,并采用抗剥离措施。通常在沥青中参加胺类表面活化抗剥离剂,也可用水泥或消石灰作为填料的一部分,但用量不能超过矿料总重的2%。2。细集料
细集料是指粒径小于5mm的天然砂(河砂、海砂、山砂)、人工砂、石屑。天然砂的细度模数及级配见表6-6。细集料的治质量术要求见表6-7,安定性实验根据需要进行,泥土含量指标仅适用于天然砂,此处指水洗法小于0.075mm部分含量。细集料应与沥青具有良好的粘结力,酸性岩石的人工砂或石屑不宜用于高等级公路沥青面层。
3.填料
填料一般采用石灰岩或岩浆岩中强基性岩石等憎水性石料经磨而得到的矿粉。矿粉应干燥、洁净、无团粒,其质量技术要求应符合表6-8的规定。粉煤灰可作为填料的一部分使用,但应经实验确认其属于碱性,与沥青有良好的粘结力,其质量要求与矿粉同。
第二节 沥青混合料组成设计
一、组成设计目标
高等级公路路面面层,为汽车提高安全、经济、舒适的服务,并直接承受汽车何载的作用和自然因素的影响。因此,铺筑面层所用混合料的组成设计必须考虑稳定性、耐久性、抗滑稳定性、抗疲劳特性及工作度(亦称施工和宜性)等问题。
1。高温稳定性
沥青混合料的强度和抗变形能力降低。因此,高温季节,沥青的粘滞度降低,矿料之间的粘结力削弱,导致强度与抗变形能力降低。因此,高温季节,在行车荷载的重复作用下,路面易出现车辙、波浪、推移等病害。提高高温稳定性,可采用提高粘结力和内摩阻力的方法。在沥青混合料中,增加粗矿了含量,
使粗矿料形成空间骨架结构,从而提高沥青混合料的内摩阻力。适当提高沥青材料的粘稠度,控制沥青与矿料的比例(油石比),严格控制沥青用量,采用具有活性的矿粉以改善沥青与矿料的相互作用,就能提高沥青混合料的粘结力。此外,在沥青中掺入天然橡胶、合成橡胶、聚异丁烯、聚乙烯等聚合物,也能获得良好的高温稳定性。
除了材料本身的性质以外,结构效应对热稳性也有一定影响,如沥青层的厚度及相对厚度的矿料尺寸。由于轮胎的约束效应和基、面层之间的摩阻力,薄层沥青显现出较厚层更高的承载力。如果选用矿料尺寸同层厚相近,也可得到较高的稳定性。
我国过去评定沥青混合料的高温稳定性是采用高温时的抗压强度和温度稳定系数两项指标。由于无侧限抗压强度的试件的受力状态与沥青混合料在路面中的实际受力状态不符,所以高温抗压强度和温度稳定性系数的实验结果,往往不能反映沥青混合料的路用性能。
目前我国采用马歇尔试验的稳定度和流值来评价沥青混合料的高温稳定性。研究表明,马歇尔稳定度和流值指标与沥青混合料的高温稳定性有一定的相关性。同时,试验设备和方法较为简单,便于现场质量控制,因此马歇尔法被广泛采用。但马歇尔稳定度和流值是一项经验性的混合料指标,它不能确切反映永久变形产生的机理,近年来国际上有以蠕变实验取代它的趋势。沥青混合料在一定荷载作用下,变形随时不断增加的特性成为蠕变。蠕变试验即可以判别混合料的稳定性,知道混合料的组成设计,又可以预估车辙量,为路面设计提供依据,因而得到众多研究者的关注。
此外,还有采用维姆稳定度、三轴试验等方法。三轴试验方法是一种比较完善的方法,它可以比较详尽的分析沥青混合料的组成与力学性质之间的关系,同时由于它的受力状态与沥青混合料路面中的受力状态比较相近,所得实验结果与使用情况有较好的相关性。但实验仪器和操作方法较为复杂,所以目前仅用于沥青混合料的研究,很少直接应用于生产。
2.低温抗裂性
随着温度的降低,沥青的粘滞度增高,强度增大,但变形能力降低,并出现脆性破坏。气温下降,特别是在急剧下降时,沥青层受基层的约束而不能收缩,产生很大的温度应力,若累计温度应力超过沥青混合料的极限抗拉强度,路面便开始产生开裂。裂缝往往出现在低温季节,无论是低温荷载裂缝、冻涨裂缝还是反射裂缝都是在外因作用下沥青混合料低温发“脆”所致,而低温缩裂则是温度下降时内部应力所致。
影响低温开裂的因素有很多,主要因素是沥青混合料所用沥青的性质、当地的气温状况、路基的类型和路面的结构及层间结合状况。从低温抗裂性的要求出发,沥青混合料在低温时具有较低的劲度和较高的抗变形能力。因此,混合料组成设计中,应选用稠度较低、温度敏感度低、抗老化能力强的沥青。在沥青中掺入橡胶等聚合物,也能大大提高混合料的低温抗裂性能。目前对沥青混合料低温抗裂性采用开裂温度预估、变形对比和开裂统计法评定。开裂温度预估是通过某温度时沥青路面产生的拉应力与沥青混合料的抗拉强度的对比来预估路面开裂温度,从而判断其低温缩裂的可能性。变形对比分析是根据沥青面层的相对延伸率与沥青混合料的极限相对延伸率对比,以判断沥青混合料的抗裂性。开裂统计法是通过野外调查研究,建立低温开裂指数与各种因素的统计关系,进而进行抗裂性的评定。
3.耐久性
在自然因素的长期作用下,要包正路面具有较长的使用年限,必须具备较好的耐久性。耐久性差的沥青混合料常会引起路面过早出现裂缝、沥青膜剥落、松散等病害。影响沥青混合料耐久性的主要因素有:沥青性质、矿料的矿物成分、沥青混合料的组成结构(残留空隙、沥青空隙率)等。
沥青的性质和矿料的矿物成分,对耐久性的影响已如强度机理中所述。就沥青混合料组成结构而言,首先是沥青混合料的空隙率。空隙率的大小与矿料骨料的级配、沥青材料用量以及压实度等有关。从耐久性角度出发,希望沥青混合料空隙率尽量减小,以防沥青的老等,但考虑到热稳性,一般沥青混合料中均应残留3%--6%空隙(或以饱水率2%--4%计)。当空隙率大,且沥青与矿料粘附性差的混合料,在饱水后矿料与沥青粘附力降低,易发生剥落,引起路面早期破坏。
此外,沥青路面的使用寿命还与混合料的沥青含量有很大关系。当沥青用量较正常的用量减少时,则沥青膜变薄,混合料的抗变形能力降低,脆性增加。如沥青用量偏小,将使混合料的空隙率增大,沥青膜暴露较多,因而作用加速。同时加大渗水性,促使水对沥青的剥落作用。有研究认为,沥青用量较标准沥青用量少0.5%的混合能使路面的使用寿命减少一半以上。在有条件的地方,也可在沥青中掺入抗剥落剂,以提高矿料与沥青之间的粘结力,进而提高混合料的耐久性。
我国过去规范曾采用水稳定系数来反映耐久性。沥青混合料的水稳定性系数是以真空饱水后抗压强度降低的百分比来表示。先行规范改为马歇尔试验法后,采用空隙率(或饱和水率)、饱和度(即沥青填隙率)和残留稳定度等指标来表示耐久性。
4.抗滑性
高等级公路的发展,对沥青混合料的抗滑性提出了更高的要求。沥青混合料路面的抗滑性与矿料的微表面性质、混合料极配组成以及沥青混合料用量等因素有关。为为提高抗滑性,配料时应特别注意粗矿料的耐磨光性(用磨光值检验),应选择硬质有棱角的矿料。硬质矿料往往属于酸性石料,与沥青的粘附性差,为此,在沥青混合料配料时,如果用当地产的软质矿料必须在其中掺入外运的硬质矿料组成附和矿料和掺入抗剥落剂等措施。国外有资料认为,在开极配沥青混合料中采用表面结构粗糙的矿料,最大颗粒为9.5—12.5mm,可获得最佳的抗滑性。沥青的用量对抗滑性的影响非常敏感,沥青用量超过最佳用量的0.5%即可使抗滑系数明显降低。如果用沥青混合料的稳定性不佳,路面易出现车辙和泛油现象,也会使抗滑性下降。
5.抗疲劳性
抗疲劳性是沥青混合料抵抗荷载重复作用的能力。通常把沥青混合料出现疲劳时的重复应力值成为疲劳强度,相应的重复作用次数成为疲劳寿命,而把可以承受无限次重复荷载循环而不发生疲劳破坏的应力值称为疲劳极限。从组成设计方面考虑,影响抗疲劳性能的主要因素有:沥青的质量与含量、混合料的空隙率、矿料的性质及级配。研究表明:最佳的疲劳寿命存在一个最佳的沥青含量。这个含量不仅与矿料的级配有关,而且与矿了的种类有关,通常它与最大混合料劲度所需最家含量相符,而要比马歇尔稳定度所确定的最佳沥青含量稍大。混合料的疲劳寿命随空隙率的降低而显著增加(这个规律对控制应力和控制应变两种加载模式均适用),密级配混合料比开级配混合料有较长的疲劳寿命。
6.工作度(施工和易性)
工作度是指沥青混合料滩铺和碾压工作的难易程度。工作良好的混合料容易进行滩铺和碾压。影响沥青混合料工作度的因素有很多,诸如当地气温、施工条件及混合料性质等。
从混合料组成而言,影响工作度的首先是混合料的级配情况。如粗细矿料的颗粒大小相距过大,缺乏中间尺寸,混合料容易分层层积(粗粒集中表面,细粒集中底部);如细矿料太少,沥青层就不能均匀的分布在细颗粒表面;细矿料过多,则使拌和困难。此外当沥青用量过少,或矿粉用量过多时,混合料容易变的疏松不易压实。反之,如沥青用量过多,或矿粉质量不好,则易使混合料粘节成团,不易滩铺。沥青通常不是工作度问题的主要原因,但其仍有一定影响,这是因为混合料的温度影响着沥青的粘度,温度太低混合料无法施工,而温度太高混合料又太软。此外,沥青的等级,以及混合料中的沥青用量,都可以影响工作度。
生产对沥青混合料的工艺性能,大多凭目力坚定。有的研究者曾以流变学理论为基础提出过一些沥青混合料过工作度的测定方法,但仍处在试验研究阶段。
二、混合料的组成设计
沥青混合料组成设计的主要任务是选择合格的材料、确定各种粒径矿料和沥青的配比。设计的总目标则是确定混合料的最佳组成,使之满足路用性能要求,而且经济。但由于沥青混合料是一种可变的相互矛盾的体系,当高温稳定性满足要求时,可能出现低温稳定性问题;而当采取一定措施满足低温稳定性时,却有可能对抗疲劳不利。因此,混合料组成设计中,应结合当地具体情况,抓主要矛盾,求得相对比较合理的“配方”。高等公路沥青混凝土混合料配合比设计以马歇尔试验为主,并通过车辙试验对抗车辙能力进行辅助性检验,沥青混合料60摄氏度时车辙试验的动稳定度应不小于1000次/mm(较热地带不小于1500次/mm),其它公路不小于600次/mm。沥青碎石混合料的配合比设计应根据以往的试验经验经过试拌试铺论证决定,马歇尔实验的结果参考。
(一) 矿料的最大粒径
各国对沥青混合料的最大粒径(D)同路面结构层最小厚度(h)的关系均有规定,除前苏联规定矿料最大粒径分别为面层厚度的0.6倍与底基层厚度的0.7厚度外一般均规定为0.5倍以下。我国研究表明:随着h/D的增大,疲劳耐久性提高,但车辙量增大。相反,h/D减少,车辙量也减小,但耐久性降低,特别是在h/D<2时,疲劳耐久性急剧下降。为此,建议结构层的厚度h与最大粒径D之比控制在h/D2,尤其是在使用国产沥青时h/D更应接近于2。例如最大粒径30—35mm的粗粒式沥青混凝土,其结构层厚度应大于4—7cm,D为20—25mm的中粒式沥青混凝土,其结构层厚度应大于4—5cm,D为15mm的细粒式沥青混凝土,其最小结构厚度应为3cm。同样,D为35—40mm的沥青碎石,其最小结构厚度应为7—8cm。
只有控制了结构厚度与最大粒径之比,才能拌和均匀,易于摊铺,特别是在压实时,易于达到要求的密实度和平整度,保证施工质量。
(二) 矿料配合比设计
1.确定级配曲线
根据理论曲线和实际使用情况的调查资料,确定即能保证具有一定密实度,又能保证稳定性的矿料级配范围。各种沥青混合料的矿料级配范围列于表6-9、6-10,级配曲线可采用表中所列级配的中值。
2.计算各矿料的配比
实际施工时,往往人工轧制的各种矿料的级配很难完全符合某一级配的范围,必须采用两种或两种以上的矿料配合起来,才能符合级配要求。
选择符合要求的各种矿料,分别进行筛析试验,并测定各种矿料的相对密实度。根据各种矿料的颗粒组成,确定达到级陪曲线要求时的各种矿料的配比。
矿料配比确定方法有试算法、正规方程法、图解法等,其中图解法最为常用。试算法是先假定混合料中某一粒径的颗粒是由一种对这一粒径占优势的矿料所组成,其他各种矿料不含这种粒径,这样根据各种主要粒径去试探各种矿料在混合料中的大致比例,如比例不合适,在稍加调整,逐步逼近,最终达到符合混合料级配要求的个矿料配合比例,但这种方法只适合于2—3中矿料的组成。下面介绍两种常用方法。
1) 图解法
图解法是根据“平衡面积法”确定出矿料组成的方法,如果矿料种类较多,计算也较
麻烦,且精度底。
(1)绘制标准级配和各种组成矿料的级配曲线
在普通的方格纸上画成矩形图(如图6—1a),纵轴表示矿料通过百分率,横轴表示筛孔直径。连接对角线,即表示为标准级配曲线。根据选定的标准级配各筛通过率(一般可取级配范围的中值)在纵轴上取坐标引水平线与对角线相交,从交点引垂线与横轴相交的坐标即表示相应各个筛空的孔径。
按上述方法所得的筛孔径与各筛孔通过百分率的坐标位置,绘制组成矿料的级配曲线,如图6—1b。
(2)确定各组成矿料的配合比
根据各种矿料的相邻级配曲线之间的关系,按不同情况确定其配合比。
① 相邻两条级配曲线重叠(即图中矿料A的下部和矿料B的上部搭接),找出级配曲线A与B分别和下、横轴距离相等(a=a`)的位置,从这从这位置画垂线与矩形对角线(标准级陪曲线)交于一点。
② 相邻两条级配曲线的前一条曲线的下点与后一条曲线的上点正好在同一个垂线上(即图中矿料B的下点和矿料C的上点),把两级配曲线上、下端连接起来与矩形对角线交于一点。
③ 相邻两条级配曲线彼此离开一端距离(即图中矿料C和矿料D的情况),则分别从两级配曲线的上端、下端向矩形中央做垂线,再做该两条垂线平分线(b=b`),并与对角线交于一点。
用以上方法所得对角线的交点,分别做水平线,就可求的个组成矿料的配合比,如图所示。
根据上述图解法确定的矿料配比,计算混合料的级配组成。必要时,适当予以修正,使设计的级配组成合乎要求。
2) 正规方程法
正规方程法用于多种矿料组成设计,所得结果准确,手算比较麻烦,但若采用微机或袖珍计算机很容易实现。正规方程计算法的基本思想是:设有k种矿料,各种矿料在n级筛析的通过百分率为P(j),欲配制某级配范围中值的矿质混合料,若矿质混合料任何一级筛孔的通过量P
(j),它是由各种组成矿料在该级的通过百分率P
(j)乘各种矿料在混合料中的用量X
之和。即
P
(j)=P(j) (6—1)
式中:i----料种类,i=1,2,…,k;
j----筛孔数,j=1,2,…n。
解这个方程即可求得矿料配合比。
(三)
确定沥青最佳用量
沥青最佳用量可以采用各种理论或半理论半经验公式计算,但是由于实际材料性质的差异,计算公式也有很大的局限性,只能做粗略估计沥青用量。而且由于沥青用量对沥青混合料,特别是密实性沥青混合料的技术性质影响很大,因此,沥青混合料的沥青用量一般均需要通过实验确定。我国现行施工规范规定,沥青混合料的沥青用量,采用马歇尔实验法确定。该方法是首先从表6—9、6—10所列的沥青用量范围或已有初步估计沥青用量。以估计值为中值,以0.5%间隔上下变化沥青用量制备马歇尔试件不少于5组。然后在规定的试验温度及试验时间内用马歇尔试验仪测定其稳定度、流值、密度,并计算其空隙率和饱和度及矿料间隙率。根据实验和计算所得的结果分别绘制沥青用量同密度、稳定度、流值、空隙率与饱和度的关系曲线(图6—2)。
从图6—2中求取相应于稳定度最大值的沥青用量为a相应于密度最大的沥青用量a
及相应与规定空隙率范围中值的沥青用a
,求取三者的平均值作为最佳沥青用量的初始值OAC
。
OAC=(a
+ a
+ a
)/3 (6--2)
求出各项指标均符合沥青混合料技术标准(表6—11、6—12)的沥青用量范围
OAC=OAC
,其中值为OAC
。
按最佳沥青用量初始值OAC在图6—2中求取相应的各项指标值,检验其是否符合表6—11的技术标准,同时检验VMA是否符合要求,如均能符合时,由OAC
及OAC
综合决定最佳沥青用量OAC,如不能符合,应调整级配,重新进行配合比设计马歇尔试验,直到各项指标均能符合要求为止。
按上诉方法决定最佳沥青用量OAC时,还应根据实验经验和公路等级及气候条件考虑下诉情况进行调整:
对较热地区的高等级公路,预计有可能产生较大车辙的情况时,可以在中限值OAC与下限OAC
范围内决定,但一般不宜小于中限值OAC
的0.5%。
对寒冷地区公路,最佳沥青用量可以在中限值OAC与上限值OAC
范围内决定,但一般不大于中限值OAC
的0.3%。
(三) 水稳性和抗车辙能力的检验
按最佳沥青用量OAC制作马歇尔试件进行浸水马歇尔试验或真空饱水马歇尔试验,检验其残留稳定度是否合格。如不符和,应重新进行配合比设计。
当最佳沥青用量OAC与两个初始值OAC和OAC
相差较大时,宜将OAC与OAC
或OAC
同时制作试件,进行残留稳定度实验。如不符合,应重新进行配合比设计。
按最佳沥青用量OAC制作车辙试件,在60C条件下用车辙试验检验动稳定度是否符合技术要求,如不符合,应对矿料级配或沥青用量进行调整,重新进行配合比设计。
当最佳沥青用量OAC与两个初始值OAC、OAC
相差甚大时,宜将OAC与OAC
或OAC
同时制作试件,进行车辙试验。
确定矿料级配及沥青用量,须反复调整及综合以上试验结果,并参考以往工程实践经验。
三、抗滑表层的材料组成设计
路面的抗滑性能是确保行车安全高速运行的基本条件。近年来,随着我国高等级公路的修建,路面表层抗滑问题已引起工程技术人员和管理人员的广泛关注。“七.五”期间,有关科研和生产部门已对次进行了研究,取得了重要成果。
防滑耐磨层的主要功能除与面层一样应有抗车辙能力外,更应满足路表摩阻系数和纹理深度指标的要求,因此要采用磨光值符合要求的矿料和合格沥青。在矿料组成方面,国外学者一致认为应采用开级配沥青混凝土,而且75%的粒料应介于12.7mm和4.76mm之间,4.76mm以下的矿料应尽量减少,使其内部具有大量空隙,表面水可以在内部流动,并能使极少量的表面水在空隙内部暂时储存,这样就叫减少了高速行驶的车辆发生飘滑和滑溜的可能性。更重要的是防滑层内部的空隙可以为轮胎和路面之间的的水分提供一个压力消减槽,这可以大大路面在潮湿状态时的抗滑性。英美等国建议的矿料组成如表6—13
根据我国当前沥青和矿料的供应情况及施工技术水平,建议防滑耐磨层的矿料组成为:粗骨料以D~D/4为主,占2/3左右的重量比,以提供良好的抗滑性和抗车辙能力;D/4以下的细料部分采用理想级配组成以提高结构的稳定性和抗裂性,这样的组成仍有一定空隙,但渗水量大大降低,兼顾了各方面要求。具体计算采用变k法的折断性级配组成,0~2级的k值取0.6,以保证主骨料占2/3,其范围以k=0.60.05控制,计算公式为:
P=P
(1-
)
式中:P----任意级粒径通过百分率;
x----级数,x=3.32lg;
n----总级数n=3.32lg;
其中:dn----最小粒径,以0.005mm为控制点;
D----最大粒径。
当计算范围值时,P=97.5,计算范围值时,P
分别取95和100。
所谓范围值,是指工地拌好的混合料抽样检查时,允许的变动范围,而试验配料时仍应以中值的级配曲线为准。在实际应用中,根据最大粒径的标称尺寸容许有5%以内的含量大于最大粒径的规定,故最大粒径处矿料通过百分比P应以95%~100%计。
根据公式计算得第2级的P中值和范围后,2级以后的k值为0.7,以保证其稳定性与耐久性,如下式:P
=P
(1-
)
这样的矿料组成,拌和、摊铺、压实都较易,为提高沥青与矿料的粘附性,矿粉含量中1%~1.5%可用消石灰代替,或采用增粘剂。
从理论和实践两方面考虑,推荐抗滑表层的矿粉级配范围见表6—9、6—10。抗滑表层沥青混合料的马歇尔应符合表6---11的设计技术标准。
第三节 施工前的准备工作
施工前的准备工作主要有确定料源及进场材料的质量检验、机械选型与配套、拌和厂选址、修筑试验路段等项工作。
一、确定科源及进场材料的质量检验
1.沥青材料
目前,我国高等级公路路面所用的沥青大部分从国外进口,如京津塘高速公路、广佛高速公路、西三一级公路、济青一级公路等,主要采用新加坡的壳牌(shell)、埃索(Esso)、 BP等公司的沥青或阿尔巴尼亚沥青。有一些工程,如沪嘉高速公路、沈大高速公路则采用国产的基本满足重交通道路沥青技术要求的稠油沥青。近几年来,对国产稠油沥青在高等级公路工程中的应用研究及工程实践表明,用满足重交通道路石油沥青技术要求的单家寺、欢喜岭、克拉玛依稠油沥青铺筑的高级沥青路面平整、坚实、无明显车撤,早期的裂缝基本消除或大大减少,路用性能达到或超过进口沥青,因而可以取代进口沥青。国产稠油沥青与国外进口沥青性质比较。
当然,国产沥青目前也还有不少问题需要解决,如包装及运输等,有的品种质量不稳定。 在全面了解各种沥青料源、质量及价格的基础上,无论是进口沥青还是国产沥青,均应从质 量和经济两个方面综合考虑选用。对进场沥青,每批到货均应检验生产厂家所附的试验报告, 检查装运数量、装运日期、定货数量、试验结果等。对每批沥青进行抽样检测,试验中如有 一项达不到规定要求时,应加倍抽样试验,如仍不合格,则退货并索赔。沥青材料的试验项 目有:针入度、延度、软化点、薄膜加热、蜡含量、比重等。有时根据合同要求,可增加其 它非常规测试项目。
2.石料
确定石料料场,主要是检查石料的技术标准能否满足要求,如石料等级、饱水抗压强度、 磨耗率、压碎值、磨光值及石料与沥青的粘结力,这些都是料场取舍的关键条件。实际中, 些石料虽然达到了技术标准要求,但不具备开采条件,在确定料场时也应慎重考虑。对各个料场采取样品,制备试件,进行试验,并考虑经济性等问题后确定。
碎石受石料本身的结构与加工设备(鄂式或锤式轧石机)的影响较大,应先试轧,检验 针片状含量及级配情况。对进场石料也要进行上述项目的检验,以防其它不合格料场的材料 入场。
3·砂、石屑及矿粉
砂的质量是确定砂料场的主要条件。’进场的砂、石屑、矿粉应满足规定的质量要求。
二、拌和设备的选型及场地布置
(一)拌和设备选型
通常,根据工程量和工期选择拌和设备的生产能力和移动方式(固定式、半固定式和移动式)。而且,其生产能力应和摊铺能力相匹配,不应低于摊铺能力,最好高于摊铺能力5%左右。高等级公路沥青路面施工,应选用拌和能力较大的设备。生产能力大的设备,其单位产品所消耗的人工、燃料和易损配件等费用较低。当然,生产能力大的设备,价格(一次性投资)也较高,但它们之间并不成比例关系。一般来说,生产能力增大一倍,设备的价格不会超过其原价的1/3。如果一台生产能力大的设备使用寿命按10年计算(10年折旧完),在这10年使用期中,仅燃料节约一项就可补偿购买大型设备所增加的投资及因此所付的利息。但是如果生产能力超过原材料的供应能力和摊铺机的摊铺能力,搅拌设备不能满负荷工作,也会造成浪费。目前,沥青混合料设备种类很多,小的每小时产量只有几吨、十几吨,大的每小时可生产400t以上。近年来,国外研制的大型拌和设备可达800~1000t/h。目前应用较多的是生产率在300t/h从以下的拌和设备(常见拌和设备型号与规格见第二章所述)。
(二)拌和厂的选址与布置
沥青混合料拌和设备是一种由若干个能独立工作的装置所组成的综合性设备。因此,不论哪一类型拌和设备,其各个组成部分的总体布置,都应满足紧凑、相互密切配合又互不干扰各自工作的原则。
1.固定式沥青混合料拌和厂
沥青混合料拌和厂一般包括原材料存放场地,沥青贮存、熔化及加热设备,搅拌设备,试验室及办公用房(有的还有宿舍)等。在设计时首先要选择厂址和确定场地面积。
沥青混合料拌和厂工作时会产生较大的粉尘与噪音等污染,因此,厂址不宜选在目前和将来的居民区,但是又要满足拌和对供电和给排水的要求。厂址离施工工地以在2h运距之内为佳。此外,厂址还应处于主交通干线或至少有7m宽路面道路的旁边。
在选择好厂址后,就要估算场地面积。该面积应能容纳工厂的所有设施,并根据其生产能力来估算,表6-15所列数据可供参考。
沥青混合料拌和厂场地面积参考表
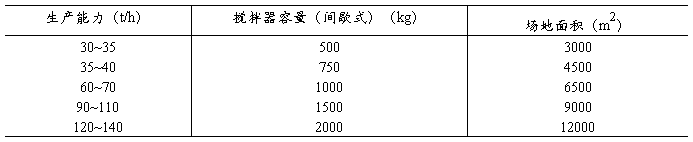
场地形状以矩形为佳,场地内的各项设施和布置应协调。一般说来,设备的主体应布置在中央位置,办公楼、宿舍和试验室等房舍应位于厂进口处,并沿路边建造。砂石料堆场或贮仓设在后边(相对于厂进口方向),既要便于向搅拌设备供料,又要便于车辆从外面运进卸下砂石料。砂石料的贮量以能供应3~5d的工作需要为宜,因此其场地应有足够的面积,且最好用水泥混凝土墙隔成几个区域,每个区域宽5~7m,长20~30m,墙高2.5~3m。矿粉仓、沥青库和燃料罐等生产供应设施可设置于砂石料场的同侧或另侧,并应以便于向主设备供送所需材料为准。配电间应安置在较偏辟而又安全的地方。秤量矿料及成品的地磅要设置在车辆的进出口处。此外,在厂的四周和场地内还要留有绿化带和设置花坛的地方。
2.半固定式沥青混合料拌和设备
半固定式沥青混合料拌和设备总体布置的原则是,将各个组成部分分别安装在多辆平板挂车上,能够以最短的时间和最少的劳力迅速拆卸、转运和重新安装,并投入生产。所用平板挂车都是为适应不同组成部分的安装和运输而特别设计制造的。
半固定式沥青混合料拌和设备一般分成干燥机组、搅拌机组和辅助机组三大部分,即由冷骨料给料装置及输送机、干燥筒组成的干燥机组;从热骨料提升机直到搅拌器之间各部分组成的搅拌机组;由矿粉供给系统、沥青供给系统和除尘装置等共同组成的辅助机组。并且,按照这样的分组,将搅拌设备安置在相应的车辆上,使其便于拆装、转移和投入使用。
半固定式沥青混合料拌和设备的各平板挂车都带有支腿,在工作时由支腿支撑着全重,以避免轮胎受压,同时增加工作时设备的稳定性。
3.移动式沥青混合料拌和设备
移动式沥青混合料拌和设备一般都是小型的,且大多是用来拌制沥青碎石混合料。因此,其各组成部分较为简单,可以全部安装在一辆特制的平板挂车上。
三、施工机械检查.
施工前对各种施工机具应作全面检查。
1.拌和与运输设备的检查
沥青混合料拌和设备在开始运转前要进行一次全面检查,注意联接的紧固情况,检查搅
拌器内有无积存余料、冷料运输机是否运转正常和有无跑偏现象,仔细检查沥青管道各个接头,严禁吸沥青管有漏气现象,注意检查电气系统,对于机械传动部分,还要检查传动湖
张紧度。检查运输车辆是否符合要求,保温设施是否齐全。
2.洒油车应检查油泵系统、洒油管道、量油表、保温设备等有无故障,并将一定数量沥青装入油罐,在路上先试洒,校核其洒油量。每次喷洒前应保持喷油嘴干净,管道畅通,喷油嘴的角度应一致,并与洒油管呈15~25”的夹角。
3.矿料撒铺车应检查其传动和液压调整系统,并应事先进行试撒,以确定撒铺每一种规格矿料时应控制的间隙和行驶速度。
4.摊铺机应检查其规格和主要机械性能,如振捣板、振动器、熨平板、螺旋摊铺器、刮板送料器、料斗闸门、厚度调节器、自动找平装置等是否正常。
5.压路机应检查其规格和主要机械性能(如转向、启动、振动、倒退、停驶等方面的能力)及滚筒表面的磨损情况。
四、修筑试验段
沥青路面大面积施工前,采用计划使用的机械设备和混合料配合比铺筑试验段。通过试验段的修筑,主要研究合适的拌和时间与温度(拌和前进行流量测定,建立料仓开度与流量的关系);摊铺温度与速度;压实机械的合理组合,压实温度及压实方法;松铺系数;合适的作业段长度。在试验段中,抽样检测每种沥青混合料的沥青含量、矿料级配、稳定度、流值、空隙率、饱和度、密实度等。沥青混合料压实12h后,按标准方法进行密实度、厚度的抽检(一般每种混合料取6处)。
通过试验段修筑,优化拌和、运输、摊铺、碾压等施工机械设备的组合和工序卸接;提出混合料生产配合比;明确人员的岗位职责。最后提出标准施工方法。现就其中两个主要问题讨论如下。
(一)生产配合比的确定
按试验室所作的配合比经试拌后混合料的各种指标有时不满足要求,因此结合试拌与试铺,进行必要的调整,方可作为生产配合比。调整混合料配比时应以前次试验为基础,针对出现的问题采取相应的措施进行局部调整。下面是对试拌混合料时一般性调整的指导原则。
1.空隙率与稳定度均较低
系沥青含量过多或细料偏多或两者兼有所致。提高空隙率的方法有多种。其中之一是在混合料中添加粗矿料以提高 VMA(矿料间隙率)值。提高空隙率的另一种方法是降低沥青含量。但应注意,只有当混合料中的沥青含量超出一般规定,而减少沥青含量又不会使沥青膜低于要求厚度,且不影响路面耐久性时,方可使用此种方法。在混合料中增加表面粗糙且有棱角的矿料可提高VMA值和摩阻力。但有些石料的破裂面非常光滑(如石英类岩石),如果使用此类矿料来提高稳定性是比较困难的。
2.空隙率低、稳定度满足要求
系沥青含量偏多或主骨料够但级配中间料断档太长所致。空隙率低易出现泛油现象,尤其当主骨料被压碎时,将会引起失稳和泛油。因此,空隙率低的混合科,即便是稳定度暂时可以满足要求,也应该用上面所述的方法进行调整。
3.空隙率满足要求、稳定度低
对此,可能是因为混合料级配不佳、矿料本身强度不足、沥青与矿料粘结性差等造成,可根据具体情况进行调整。
4.空隙率高、稳定度满足要求
空隙率高常会使透水性提高。所以,既使混合料的稳定度满足要求,也要将空隙率调低些。通常采用的方法是适当增加细料。
5.空隙率高、稳定度低
对于空隙率高而稳定度低的混合料,需要按前面阐述的方法调低空隙率。如果经调整后,仍然不能同时改善空隙率和稳定度两项指标时。则要按照开始所述的方法,重新选择矿料。
(二)机械组合
高等级公路路面的施工机械应优先选择自动化程度较高和生产能力较强的机械,以摊铺、拌和为主导机械并与自卸汽车、碾压设备配套作业,进行优化组合,使沥青路面施工全部实现机械化。目前常见的问题是摊铺与拌和生产能力不配套,不能保证连续作业,从而影响施工进度和质量。特别是摊铺能力远大于拌和能力,使摊铺机频繁停机影响了摊铺质量。运输车辆数的确定可根据第~章所述的排队论法或下节所述的方法确定。压实机械的配套,根据碾压温度及摊铺进度确定合理的碾压长度,然后配备庆实机具。表6-16为交通部第一公路工程总公司承担京津塘高速公路某段沥青路面施工机械的配套情况。
配套示例 表6-16
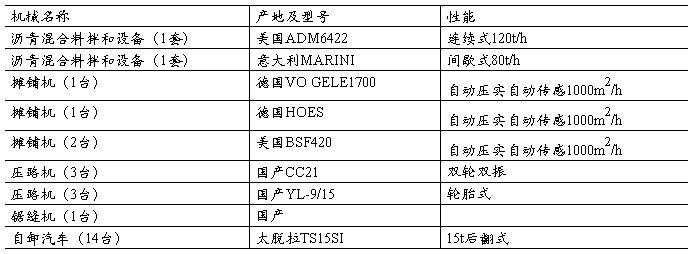
本节中有关机械的检查及运行中的具体问题,将在以下各节中详细讲述,以保证各节内容的系统性。
第四节 沥青混合料的拌和与运输
一、拌和与运输的一般要求
(一)试拌
沥青混合料宜在拌和厂制备(传统式与滚筒式拌和设备的工艺流程见第二章)。在拌制一种新配合比的混合料之前,或生产中断了一段时间后,应根据室内配合比进行试拌。通过试拌及抽样试验确定施工质量控制指标。
1.对间歇式拌和设备,应确定每盘热料仓的配合比。对连续式拌和设备,应确定各种矿料送料口的大小及沥青、矿料的进料速度。
2.沥青混合料应按设计沥青用量进行试拌,试拌后取样进行马歇尔试验,并将其试验值与室内配合比试验结果进行比较,验证设计沥青用量的合理性,必要时可作适当调整。
3.确定适宜的拌和时间。间歇式拌和设备每盘拌和时间直为30~60s,以沥青混合料拌和均匀为准。
4.确定适宜的拌和与出厂温度。沥青(均指石油沥青,以下同)的加热温度宜为130~160℃,加热不宜超过6h,且当天加热宜当天用完,不宜多次加热,以免老化。砂石加热温度为140~170℃,矿粉不加热。沥青混合料(指石油沥青混合料,下同)出厂温度宜控制在130~160℃。
(二)沥青混合料的拌制
根据配料单进料,严格控制各种材料用量及其加热温度。拌和后的沥青混合料均匀一致, 无花白、无离析和结团成块等现象。每班抽样做沥青混合料性能、矿料级配组成和沥青用量 检验。每班拌和结束时,清洁拌和设备,放空管道中的沥青。做好各项检查记录,不符合技 术要求的沥青混合料禁止出厂。
(三)沥青混合料的运输
沥青混合料用自卸汽车运至工地,车箱底板及周壁应涂一薄层油水(柴油:水为1:3)混合液。运输车辆上应覆盖,运至摊铺地点的沥青混合料温度不宜低于130℃。运输中尽量避免急刹车,以减少混合料离析。
二、拌和与运输的生产组织
沥青混合料的生产组织包括矿料、沥青供应和混合料运输两方面,任何一方面组织不好都会引起停工。
(一)拌和
1.材料供给
所用矿料符合质量要求,贮存量应为平均日用量的5倍,堆场应加遮盖,以防雨水。研究表明:矿料含水量的多少对设备生产能力的影响很大,矿料的含水量大则意味着烘干与加热费时,生产能力降低,燃料消耗率增加。例如干燥滚筒生产能力为 50~80t/h时,含水量为5%~8%的矿料,含水量每增加1%,干燥能力下降约10%,每吨产品的燃油消耗率将增加10%。矿粉和沥青贮量应为平均日用量的2倍。
2.拌和设备的运行
起动前要拉动信号,使各岗位人员相互联系,确认准备就绪时才能合上电闸。对各组成部分的起动,应按料流方向顺序进行。待各部分空运转片刻,确认工作良好时,才可开始上料,进行负荷运转。
通常用装载机将不同规格的矿料投入相应的料仓,在拌和设备运行中要经常检查砂石料仓贮料情况。如果发现各斗内的贮料不平衡时,应及时停机,以防满仓或贮料单仓。检查振一动筛的橡皮减振块,发现有裂纹时,要及时更换,贮料仓中的存料要过半后才可开始秤量。矿粉要根据用料情况上料,防止上料过多或卡住机器。防止沥青从保温箱中溢出,必要时可用工具在箱内搅动,以免沥青溢出。
拌和设备在停机之前应先停止供给砂石料并少上矿粉,使滚筒空转3~5min,待简内出完余料再停止简的转动。在简空转时还应加大喷撒器的风门,尽快驱除简内的废气,并使筒冷却,然后关闭喷燃器的油门和燃油泵的总油门。停机后矿粉仓和矿粉升运机内不得有余料,在停止搅拌前应先停止喷沥青,将进入搅拌器内的余料子拌几分钟后放净,以便刷净搅拌器内的残余沥青。
拌和设备在每次作业完毕后都必须立即用柴油清洗沥青系统,以防止沥青堵塞管路。
(二)运输
沥青混合料成品应及时运往工地。工前应查明具体位置、施工条件、摊铺能力、运输路线、运距和运输时间,以及所需混合料的种类和数量等。拌和设备时开时停会造成燃料的浪费,并影响混合料的质量。车辆数量必须满足拌和设备连续生产的要求,不因车辆少而临时停工。在生产中所用运输车辆数量n视拌和设备生产能力G(t/h)、车辆的载重能力G0(t)及运输时间等因素而定。
要组织好车辆在拌和设备处装料和工地卸料的顺序,尤其要计划好车辆在工地卸料时的停置地点。装料时必须按其载重量装足,安全检查后再启运。
为了精确控制材料,载料车出厂时应进行称量,常用磅秤或使用拌和厂的自动称星系统(全自动拌和厂)。有些拌和厂还随机称量每辆料车的空车自重,且要求磅房保存这种空重的永久性记录。电子自动打印重量卡已在许多地方采用,卡片一般记有毛重、空重和净重。
为了不因特殊事故或其它原因而使设备停工,拌和设备应有足够的混合料成品贮仓。
三、拌和质量检测
(一)拌和质量的直观检查
质检人员必须在料车装料过程中和开离拌和厂前往摊铺工地途中经常进行目测。仔细的目测有可能发现混合料中存在的某些严重问题。
沥青混合料生产的每个环节都应特别强调温度控制。这是质量控制的首要因素。目测经常可以发现沥青混合料的温度是否符合规定。料车装载的混合料中冒黄烟往往表明混合料过热。若混合料温度过低,沥青裹覆不匀,装车将比较困难。此外,如运料车上的沥青混合料能够堆积很高,则说明混合料欠火,或混合料中沥青含量过低。反之,如果热拌混合料在料车中容易坍平(不易堆积),则可能是因为沥青过量或矿料湿度过大所致。
(二)拌和质量测试
1.温度测试
直观检验固然很重要,但检验人员必须进行测定。沥青混合料的温度通常在料车上测出。较理想的方法是使用有度盘和铝装枢轴的温度计,将枢轴从车箱一侧的预留孔中插入混合料中,使之达到足够的深度(至少15cm),混合料直接与枢轴接触,可测出料温。也可用手枪式红外测温计。这是一种测量表面反射温度的仪器。由于红外测温计仅能测出材料表面温度,故其温度读数对于料车中间的材料便不可能准确。为了解决这一问题,检验人员应在混合料从拌和机或聚料斗出料口卸出时,就应用这种仪器进行测定。红外测温计能迅速获得全面的数据,但使用时应经常校准。
2.沥青混合料的取样和测试
沥青混合料的取样与测试是拌和厂进行质量控制最重要的两项工作。取样和测试所得的数据,可以证明成品是否合格。因此,必须严格遵循取样和测试程序,确保试验结果能够 真实反映混合料的质量和特性。作为称职的检验人员,必须能采集有代表性的样品,进行现 场试验室试验,并解释试验数据。
取样和测试程序及要求一般由合同规范规定。主要包括抽样频率、规格和位置,以及要做的试验等方面的内容。取样时,首先应确保所取样品能够反映整批混合料的特性。测试的主要内容是马歇尔稳定度、流值、空隙率、饱和度、沥青抽提试验、抽提后的矿料级配组成必要时进行残留稳定度测定(饱水72h、60C的稳定度与60℃的稳定度之比乘100%)。测试频率在我国目前做法不一,有些地方的施工合同规范规定每天从沥青混合料拌和机中抽样制备4个试件(与工地桩号联系),或者每250t混合料不少于1次,进行上述内容的测定,并于6h内将测定结果报告试验监理工程师。我们认为,按生产量确定抽样频率是比较合理的。
3.检测记录
检验人员必须保留详细的检验记录。这些记录是确定沥青混合料是否符合规范要求,能否付款的依据。因此,记录必须清楚、完整和准确。这些记录还将成为施工和工程用料的历史记录。所以,检验记录也就成为日后研究和评价该项工程的依据。
为了能够反映实际情况,这些记录和报告必须在进行所规定的试验或测量的当时抓紧时间填写。每项工程都必须记日志。应记录:工程编号、拌和厂位置、拌和设备的类型和型号、原材料来源、主要工作人员姓名以及其它数据。还应记录日期和当天的气象情况及拌和厂的主要活动和日常工作。对异常情况,特别是对沥青混合料可能产生不利影响的情况必须进行说明。
(三)拌和质量缺陷及原因分析
造成沥青混合料拌和质量缺陷的原因十分复杂,表6-17列出了出现问题的现象及可能原因。它能帮助拌和厂技术人员有效地控制生产质量。
四、沥青混合科生产实例
现以沈大高速公路沥青路面施工中所采用日本新泻铁工所NDP-150型滚筒式拌和设备 的生产为例,介绍沥青混合料生产的全过程。
对NDP-150型拌和设备,当矿料密度l.6t/m3,含水量5%,出料温度140~160℃时,设备的额定生产能力是150t/h,贮存仓可贮存成品80t,贮存72h,降温不大于5℃。
1.工艺流程
装载机将各种规格矿料投入料斗内,矿粉单设贮料仓,上述两部分冷料按配合比要求分别通过两条悬挂计量皮带连续输送给传送带,由此进入干燥式拌和滚筒,冷料供料机里的流量由变速电机转速控制,矿料在简内连续旋转前进,根据中心控制室电子计算机发出矿料重量指令沥青自动供给,并在滚筒内与矿料拌和,从而获得满足要求的沥青混合料。控制室装有各种仪表和信号装置,可监视整套设备运转情况,反映出矿料、矿粉、沥青用量的变化,实现生产过程的全自动控制。
2.计量控制
1)生产前中心试验室先确定混合料配合比(表6-18)
2)测定不同转速时各冷料斗对应的流量(t/h)。
在生产前,用拌和设备外部排料装置,测定各冷料斗供料器在一定开度下变速电机不同转速时的流量,每个转速测定次数不少于三次,求出平均值,绘制图表备用,要求供料误差不超过0.5t/h。
3)确定各配合比相对应的要求转速。
以中粒式LH-20-Ⅱ为例,列于表6-20。
4)测定冷料含水量
工地试验室每晨测定一次各规格冷料的含水量,如果超过限值,控制室可通过调速旋钮对供料机流量进行调整。
5)计算机调控计量
将有关数据输入计算机,按所需转数控制供料器,根据设定的供料器查看计量显示器数值(t/h),不断调整旋钮,直到相符为止。
按要求转速控制的各冷料斗流量,通过水平传送皮带汇集到计量皮带上,传感器将瞬时的重量讯号发送控制室,沥青重量则根据有关讯号,自动跟踪。
工地要测定冷骨料从汇集计量皮带到达拌和滚筒沥青喷洒部位的迟延时间(测定时间数约为6s)
沥青体积用升计算,通过温度与密度的关系,由升转换为千克,AH-120沥青温度与密度的关系见表6-21,控制室按表列数据控制喷油量。
4.质量检测
试验室每天上下午做两次沥青混合料马歇尔试验,监视各项质量指标的波动。并要求检测每批进场沥青的针入度、延度、软化点,抽检进场矿料规格,每晨测含水量并通知控制室。
第五节 沥青混合料摊铺技术
摊铺作业是沥青路面施工的关键工序之一,常包括下承层准备、施工放样、摊铺机各种参数的调整与选择、摊铺机作业等主要内容。下面,在介绍摊铺沥青混合料一般要求的基础上,对上述主要内容进行详细讨论。
一、摊铺沥青混合料的要求
摊铺时应先检查摊铺机的熨平板宽度和高度是否适当,并调整好自动找平装置。有条件时,尽可能采用全路幅摊铺,如采用分路幅摊铺,接茬应紧密、拉直,并宜设置样桩控制厚度。双层式沥青混凝土面层的上下层铺筑宜在当天内完成,如间隔时间较长,下层受到污染的路段铺筑上层前应对下层进行清扫,并浇洒粘层沥青,摊铺时,沥青混合料温度不应低于100℃摊铺厚度应该为设计厚度乘以松铺系数,沥青混合料的松铺系数通过试铺碾压确定,也可按沥青混凝土混合料的1.15~1.35,沥青碎石混合料1.15~1.35取值。细粒式取上限,粗粒式取下限,摊铺后应检查平整度及路拱,发现问题及时修整。
施工气温应在10℃以下或冬季气温虽在10℃以上,但有时大风时,摊铺时间应在上午9时至下午4时进行,做到快卸料、快摊铺、快整平、快碾压,摊铺机的熨平板及其它接触热沥青混合料的机具要经常加热。在摊铺沥青混合料前,应对接茬处已被压实的沥青层进行预热,沥青混合料摊铺后,在接茬处用热夯夯实、热烙铁熨平,并使压路机沿接茬加强碾压。
雨季施工时,应注意气象预报,加强工地现场与拌和厂联系,现场应缩短施工路段,各工序要紧密衔接。运料汽车和工地应备有防雨设施,并做好基层及路肩的排水工作。下承层潮湿时,不得摊铺沥青混合料,对未经压实即遭雨淋的沥青混合料,要全部清楚,更换新料。
二、准备工作
1、下承层准备
在铺筑沥青混合料时,它的下承层(即前一层)无非是基层、联结层和面层下层。虽然下承层完成之后,已进行过检验验收,但在两层施工的间隔,很可能因某种原因,如雨天、施工车辆通行或其他施工干扰等,会使其发生程度不同的损坏,如基层可能出现弹软和松散或表面浮尘等,因此,需进行维修。沥青类联结层下层表面可能泥泞污染,必须清洗干净。下承层表面出现的任何质量缺陷,都会影响到路面结构的层间结合强度,以至于路面整体强度。特别对桥头及通道两端基层发生沉陷,则应在两端全宽范围内进行挖填处理(一定深度与长度范围内重新分层填筑与压实)。并在两端适当长度内,线形略向上抬起0~3cm,实线形“饱满”。对下承层缺陷处理后,即可撒透层油或粘层油。
2、施工放样
施工放样包括标高测定与平面控制两项内容。标高测定的目的是确定下承层表面高程与原设计高程相差的确切数值,以便在挂线时纠正到设计值或保证施工层厚度。根据标高值设置挂线标准桩,借以控制摊铺厚度和标高。对无自控装置的摊铺机,不存在挂线问题,但应根据所测标高值和本层应铺厚度综合考虑确定实铺厚度,用适当垫块或定位螺旋调整就位,为便于掌握铺筑宽度和方向,还应放出摊铺的平面轮廓线或设置导向线。
标高放样应考虑下承层标高差值(设计值与实际标高值之差)、厚度和本层应铺厚度。综合考虑后定出挂线桩顶的标高,在打桩挂线。当下承层厚度不够时应在本层内加入厚度差并兼顾设计标高。如果下承层厚度够而标高低时,应根据设计标高放样。如果下承层厚度与标高都超过设计值时,应按本层厚度放样。若厚度和标高都不够时,应按差值大的为标准放样。总之,不但要保证沥青路面总厚度,而且要考虑标高布超出容许范围。当两者矛盾时,应以满足厚度为主考虑放样,放养时计入实测的松铺系数。挂线的技术及有关事项将在自动找平装置运用中详述。
3、摊铺机工前检查
摊铺机在每日施工前,必须对工作装置及其调整机构进行专门检查,即检查刮板输送器、闸门和螺旋摊铺器(即供料系统)的状况是否良好,有无粘附沥青混合料(包括受料斗);振捣梁的底面及其前下部是否磨损过大,行程及运动速度是否恰当,它与熨平板之间的间隙以及离熨平板底面的高度是否合适;熨平板底面有无磨损、变形和粘附混合料,其加热装置是否良好;厚度调节器和拱度调节是否良好;各部位有无异常振动;采用自动调平装置时要检查装置是否良好。
上述各项都必须进行试运转检查,遇有故障应及时消除与调整,确认工作装置及其调节机构均处于良好状态之后,方允许正式投入施工。
三、摊铺机参数的调整与选择
摊铺机参数包括结构参数和运行参数两大部分。在摊铺前,根据施工要求需调整和选择摊铺机的结构参数有:熨平板宽度和拱度;摊铺厚度与熨平板的初始工作迎角。运行参数主要指摊铺速度。
1、熨平板宽度与拱度的调整
为了减少摊铺次数,每一条摊铺带的宽度应该按该型号摊铺机的最大摊铺宽度来考虑。宽度为B的路面所需横向摊铺的次数n按下式计算:
(6-4)
式中:B——路面宽度(m);
b——摊铺机熨平板的总宽度(m);
x——相邻摊铺带的重叠量(m),一般x=0.025~0.08m。
公式6-4的意义是,路面的宽度应为摊铺机总摊铺宽度减去重叠量后的整倍数。如果n值不能满足整数时,则尽可能在减少摊铺次数的前提下,使所剩的最后一条摊铺带的宽度不小于该摊铺机的标准摊铺宽度。实在不足时只好采用切割装置(截断滑靴)来切窄摊铺带。
每一条摊铺带尽可能宽,这样不仅可减少机械通过次数,还可减少路面的纵向接茬,有利于质量的提高。在确定摊铺带宽度时应注意:上下铺层的纵向接茬应错开30cm以上;摊铺下层时,为了便于机械的转向,熨平板的侧边与路缘石或边沟之间应留有10cm以上的间距;在纵向接茬处应有一定的重叠量(平均为2.5~5cm);接宽熨平板时必须同时相应地接长螺旋摊铺器和振捣梁,同时检查接长后熨板底板的平直度和整体刚度。
熨平板宽度调整之后,要调整其拱度。各种型号摊铺机的调拱机构大致相同,调整后可在标尺上直接读出拱度的绝对数(mm)值或横破百分数。调整好拱度后要进行试铺校验,必要时再次调整。一些大型摊铺机,常设计有前后两副调拱机构。这种双调拱机构,其前拱的调节量略大于后拱。这样有利于改善摊铺成的表面质量和结构致密的均匀性。如果调整不当,将出现表面致密度不均等缺陷。经验表明,前拱过大,混合料易向中间带集中,于是出现两侧疏松,中部紧密并被刮出亮痕和纵向撕裂状条文;反之,前拱过小,甚至小于后拱,混合料被分向两侧,于是将出现中间疏松,两侧紧密并挂出亮痕和纵向撕裂状条文。只有前后拱符合规定时,才能获得满意的摊铺效果。一般人工接长调整宽度的熨平板,其前后拱之差为3~5mm,液压伸缩调宽的熨平板,差值为2~3mm。
2、摊铺厚度的确定和熨平板初始工作迎角的调整
摊铺工作开始前要准备两块长方垫木,以此作为摊铺厚度的基准。垫木宽5~10cm,长与熨平板纵向尺寸相同或稍长,厚度为松铺厚度。将摊铺机停置于摊铺带起点的平整处后,抬起熨平板,把两块垫木分别置于熨平板两端的下面,如图6-3所示。如果熨平板加宽,垫木则放在加宽部分的近侧边处。
垫木放好后,放下熨平板,让其提升油缸处于浮动状态。然后转动左右两只厚度调节螺杆,使它们处于微量间隙的中立位置。此时,熨平板以其自重落在垫木上。
熨平板放置妥当后,接着调整其初始工作迎角。此迎角视机型、铺层厚度、混合料种类和温度等因素的不同而异,各机型在实用说明中都有规定。
多数摊铺机上装右手动调整机构,用以调整初始工作迎角。调节的正确与否,只能通过实际摊铺的厚度去检验。每调整一次,必须在5m范围内作多点厚度检验,取其均值,与设计值比较。一次调整之后,在测定均值之前,不得作任何调整。对于凹凸不平较大的下承层,几处测量仍难求得正确的厚度值时,可从摊铺的面积和所使用的混合料数量求出每m2所用混合料的重量,以此与规定的密度作比较,就可确定摊铺厚度要不要再次调整。所铺的实际平均厚度h可按下式计算:
(cm) (6-5)
式中:G——已用混合料的重量(t);
A——铺筑面积(m2);
——未最终压实的混合料密度(一般取2t/m3)。
摊铺厚度还直接与刮板输送器的生产能力有关。在实际施工过程中,如果知道刮板输送器的生产能力,又知道最大摊铺宽度,就可方便地调整摊铺厚度。
具有自动调平装置的摊铺机,在机械结构上可以靠改变熨平板侧臂安装位置来获得有限级(如三级)的初始工作迎角,每一级初始工作迎角适应一定范围的摊铺厚度。同时,依靠电子液压调平装置来控制工作迎角的瞬时变化,以保证摊铺平整度。
对液压伸缩熨平板,由于基本熨平板与左右伸长熨平板不在同一纵向位置上,当初使工作迎角改变时,两者的后缘距地面高度会变得不一致。所以在调整工作迎角之后,要使用同步调整机构,调整左右伸长熨平板的高度,使其后缘与基本熨平板后缘处于相同高度。
3、布料螺旋与熨平板前缘距离的调整
现代摊铺机的熨平板前缘与布料螺旋之间的距离是可变得。它主要根据摊铺厚度、混合料级配及油石比、下承层强度与刚度、矿料粒径等条件,对这一距离进行适当调整。当摊铺厚度较大、矿料粒径也大、沥青混合料温度偏低、或发现摊铺层表面出现波纹则宜将距离调大;在石灰稳定土、水泥稳定土、二灰及二灰土基层上摊铺厚度较小的沥青层时,宜将距离调小;一般摊铺条件下(厚度10cm以下的中、粗粒式沥青混合料,矿料粒径约3cm,正常摊铺温度),宜将距离调至中间位置。
熨平板前缘与布料螺旋之间的距离变化,会引起熨平板前沿堆料高度的变化,影响摊铺质量。因此,这一调整是在其他项目调整全部完成后进行。
4、振捣梁行程调整
绝大多数摊铺机在熨平板之前设有机械往复式振捣梁,由一偏心轴传动。偏心轴一般由一台液压电机驱动,往复运动的行程可进行有级或无级调整,视摊铺厚度、温度和密实度而定,通常在4~12mm之间。一般情况下,薄层、矿料粒径小宜短行程,反之,摊铺厚度大、温度低、矿料粒径大时,宜长行程,摊铺面层只能运用短行程。
5、熨平板前刮料护板高度的调整
有些摊铺机熨平板前装有刮料护板。起作用在于保持熨平板前部混合料的堆积高度为定值。因此,刮料护板的高度调整得当,有助于提高摊铺质量。国外研究表明,当摊铺厚度小于10cm时,刮料护板底刃应高出熨平板底板前缘13~15mm,对于液压伸缩调幅的熨平板,此值要稍减小,如果摊铺厚度增加,或混合料粒径增大,刮料护板要适当提高。反之,摊铺层减薄、混合料中细料多或油石比较大时,应适当降低刮料护板高度。为确定在熨平板全宽范围内料堆高度一致,刮料护板底刃必须平直,且与熨平板底边缘保持平行。
6、摊铺机作业速度的选择
摊铺机的作业速度对摊铺机的作业效率和摊铺质量影响很大。正确选择作业速度,是加快施工进度、提高摊铺质量的重要手段。现代摊铺机都具有较宽的速度变化范围,从零值倒每分钟十米之间,可进行无级调节。如果摊铺机时快时慢、时开时停将导致熨平板受力系统平衡变化频繁,会对铺层平整度和密实度产生很大影响;过快使铺层疏松、供料困难,停机会使铺层表面形成台阶状,且料温下降,不易压实。
选择摊铺速度的原则是保证摊铺机连续作业。首先要考虑供料能力,包括沥青混合料拌和设备的生产能力和运输车辆的运输能力。供料能力应使摊铺机在某种速度下连续作业。因此,合理的摊铺速度可根据混合料供给能力、摊铺宽度和厚度按下式求得:
(m/min) (6-6)
式中:Q——混合料供给能力 (t/h);
h——压实后的摊铺厚度 (cm);
b——摊铺宽度(m);
——沥青混合料压实后的密度(一般取2.35t/m3).
如以代入公式可写成:
(m/min) (6-7)
根据摊铺机的标准宽度或加宽后的高度b和沥青混合料搅拌设备的生产能力Q,以不同的摊铺厚度h值代入公式6-7,就可列出一张相应摊铺速度的关系表,以供摊铺作业时查阅。
实际上,摊铺速度还因所用混合料种类、温度及铺筑的层次不同而有所区别。一般面层下层的摊铺速度较快,约为10m/min,面层上层的摊铺速度较慢,为6m/min以下。这是为了使面层能获得足够的密实度和平整度。对于薄层罩面,更要慢些。因为机械前进速度慢,铺沥青混合料摊铺机中,不论是机械式的有级变速,或液压式的无级变速,摊铺工作速度以及振捣梁的频率都能满足工作要求。
四、摊铺及作业
1、 熨平板加热
每天开始施工前或停工后再工作时,应对熨平板进行加热,即使夏季热天也必须如此。
因为100℃以上的混合料碰到30℃以下的熨平板底面时,将会冷粘在板底上,这些粘附的粒料随板向前移动时,会拉裂铺层表面,便之形成沟槽和裂纹。如果先对熨平板进行加热,则加热后的熨平板可对铺层起到熨烫的作用,从而使路表面平整无痕。但加热熨平板不可火力过猛,以防过热。过热除了易使板本身变形和加速磨损外,还会使铺层表面烫出沥青胶浆和拉沟。因此一旦发现此种现象应立即停止加热。
在连续摊铺过程中,当熨平板已充分受热时,可暂停对其加热。但对于摊铺低温混合料和沥青砂,熨平板则应连续加热,以使板底对材料起熨烫的作用。
2、 摊铺机供料机构操作
摊铺机供料机构包括刮板输送器和向两侧布料的螺旋摊铺器两部分。两者的工作应相
互密切配合,工作速度匹配。工作速度确定后,还要力求保持其均匀性,这是决定路面平整度的一项重要因素。
刮板输送器的运转速度及闸门的开启度共同影响向摊铺室的供料量。通常刮板输送器的运转速度确定后就不大变动了,因此,向摊铺室的供料量基本上依靠闸门的开启高度来调节。在摊铺速度恒定时,闸门开度过大,使得螺旋摊铺室中部积料过多,形成高堆,造成螺旋摊铺器的过载并加速其叶片的磨损。同时也增加熨平板的前进阻力,破坏熨平板的受力平衡,使熨平板自动向上浮起,铺层厚度增加。如果关小闸门或暂停刮板输送器的运转,掌握不好,又会使摊铺室内的混合料突然减少,同时会破坏熨平板的受力平衡,使熨平板下沉,铺层厚度减小。
摊铺室内最恰当的混合料是料堆的高度平齐于或略高于螺旋摊铺器的轴心线,即稍微看见螺旋叶片或刚盖住叶片为度。料堆的这种高度应沿螺旋全长一致,因此要求螺旋的转速配合恰当。
闸门的最佳开度,应在保证摊浦室内混合料处于上述的正确料堆高度状态下,使刮板输送器和螺旋摊铺器在全部工作时间内都能不停歇地持续工作,但由于基层不平以及其它复杂的原因,为保证摊铺室内混合料维持标准高度,刮板输送器与螺旋摊铺器不可避免地要有暂停运转和再起动的情况发生。不过这种情况越少越好,因为过多的频繁停转与再起动会造成其传动机构过快磨损。最好使它的运转时间占其全部工作时间的80~90%。为了保持摊铺室内混合料高度经常处于标准状态,最好的办法就是采用闸门自控系统。
无论是手操纵还是自控供料系统供料,都要求运输车辆对摊铺机有足够的持续供料量。如果出现摊铺机停机待料,此时为了避免受料斗里的混合料温度降低而凝结在斗内,必须把它送空。而经常这样做,除了造成铺层出现波浪外,还会加速刮板输送器的磨损。因此,从这个角度上考虑,也要求汽车能不断地及时供料,使摊铺机能顺利地连续顶推车辆卸料及摊铺作业。
3、 摊铺方式
摊铺宽度的确定方法已如前述。摊铺时,先从横破较低处开铺。各条摊铺带的宽度最
好相同,以节省重新接宽熨平板的时间(液压伸缩式调宽较省时)。使用单机进行不同宽度的多次摊铺时,应尽可能先摊铺较窄的那一条,以减少拆接宽次数。
如果为多机摊铺,则应在尽量减少摊铺次数的前提下,各条摊铺带的宽度可以有所不同(即插队作业方式),梯队间距不宜太大,宜5~10m之间(国内也有10~75m,美国15.2~30.5m),以便形成热接茬。如为单机非全副作业,每幅不宜铺筑太长,应在铺筑100~150m后调头完成另一幅,此时一定要注意接好茬。也有人认为,为减少横向施工接茬,每条摊铺带在一天施工中应尽可长些,最好一个施工班一条接茬,具体可结合实际定。在铺筑面层时最好是单机或双机全副铺筑,如为单机时,中间纵向茬要切割涂油,使两次摊铺混合料紧密、平整相接。
4、 接茬处理
(1)纵向接茬
两条摊铺带相接处,必须有一部分搭接,才能保证该处与其它部分具有相同的厚度。
搭接的宽度应前后一致,搭接施工有冷接茬与热接茬两种。
冷接茬施工是指新铺层与经过压实后的已铺层进行搭接。搭接(重叠)宽度约为3~5cm,过宽了会使接茬处压实不足,产生热裂。过窄会在接茬处形成斜坡。新摊铺带必须与前一条摊铺带的松铺厚度相同。在摊铺新铺层时,对已铺的摊铺带接茬处边缘应铲修垂直。碾压新摊铺带时,也要先将其接茬边缘铲齐。
热接茬施工一般是在使用两台以上摊铺机梯队作业时采用的,此时两条毗邻摊铺带的混合料都处于压实前的热状态,所以纵向接茬易于处理,且连接强度较好。毗邻摊铺带的搭接宽度约2~5cm。不管采用冷接法或热接法,摊铺带的边缘都必须齐整,这就要求机械在直线上和弯道上行驶始终保持正确的位置。为此,可沿摊铺带一侧敷设一根导向线,并在机械上安置一根带链条的悬杆,驾驶员只要注视所悬链条对准导向线行驶即可。
(2)横向接茬
前后两条摊铺带横向接茬质量的好坏对路面的平整度影响很大,它比纵向接茬对汽车行驶速度和舒适性的影响更大。
处理好横接茬的一个基本原则是,要将第一条摊铺带的尽头边缘锯成垂直面,并与纵向边缘成直角。
五、自动找平装置的运用
所有摊铺机都装有浮动式熨平板。具有自动找平功能,不会机械地复现下承层表面的波形。这种具有“滤波”的作用随摊铺机的结构、类型不同而不同。一般轮式优于履带式。轮式摊铺机带有台车式的双前轮,较之单前轮结构的自调功能好;履带式摊铺机,支重轮架为弹性摆动式悬挂,优于刚性悬挂。熨平板侧臂愈长,自调平功能愈佳。实际工作中,工作环境对浮动式熨平板的干扰因素错综复杂,很少有规律。因此,单纯依靠自动调平功能来“滤波”,不可能安全消除各种干扰因素的影响,必须辅之外加调整。用人工转动调整手轮,通过螺旋传动来改变熨平板的工作迎角,用以改变平整度,其效果在很大程度上取决于工人的经验和熟练程度,实际上这种方式无法满足高等级公路施工摊铺质量的要求。而自动找平装置的诞生解决了这个问题。
运用自动找平装置,需要有一个准确的基准面(线),常用的基准面(线)控制有基准线钢丝法、滑撬法、厚度和平整度,但采用此法要求操作中各环节都必须从严要求。
(一) 纵坡基准的选择
使用自动调平装置必须事先选好纵坡基准。基准有专设的悬线或现成参考物,如已铺好的路面结构层、路缘石等。
1、弦线基准及敷设
当下承层高低不平,边侧又无平坦的基准面参考时,可在边侧专门设置符合设计纵坡
的参考弦线(细钢丝或尼龙线),让传感器的触件沿着弦线移动。参考弦线要在施工前设好,它由弦线、铁立杆、弹簧秤和张紧器等组成,如图6-4所示。
钢丝可使用直径为2~2.5mm的弹簧钢丝,每段长度以200m为宜。总长度应满足二三天的施工用量。钢丝的优点是不受外界因素变化的影响,缺点是张紧度显示得不明显,易于现松弛现象。为此,要作脚踩试验。200m长钢丝的张紧力一般需800~1000N。
尼龙线的缺点是遇水会伸长,所以在遭受露水、雨水或受潮后都要在此张紧。每天早晨上班前要复查其张紧度,必要时再行张紧。但是尼龙线柔软,使用起来十分方便,所以使用者较多。每根尼龙线长约150~200m,立杆间距10m时,其张紧力需300~400N。
基准线的敷设情况如图6-4所示。两根立杆的间距一般为5~10cm,在弯道处的间距要短些。标桩3是用来测定拉线的标高,所以它应设在立杆附近,以便于检查,其数量视坡度变化程度而定。敷设基准线时将其一段固定,另一端通过弹簧秤4连接于张紧器5上,有时基准线的两头都装有弹簧秤和张紧器,便于张力的调整。
敷设基准线时,除了应按规定的纵坡保证各支点都处于正确的标高位置外,还要注意其纵向走向的正确性,最好使每根立杆与路中线的距离相等。这样,就兼做导向线。对敷设好的基准线必须复核其标高的正确性,如果标高不正确,非但失去使用自动调平装置的意义,反而会出现不平整或纵坡不合要求的铺层。另外,为了避免施工过程中可能发生碰撞,最好在各立杆上做出醒目的标志。
2、利用现成表面作基准
现成的基准面有较平整的下承层或路缘石,甚至坚实的边沟等。作为传感器的接触件有滑撬、平均梁(如图6-5和6-6所示)等,应视所参考的基准面种类而定。对于底层的铺筑,视原基层平整情况,可采用长短不一的平均直梁(参看图6-5之10、11)或带小脚或小滚轮的平均梁。以辅好的路面作基准大多用于摊铺纵向邻接的摊铺带,此时由于已筑路面较平整,可采用滑撬作接触件(图6-6)。纵坡如属冷接茬施工,小滑撬应置放在离路面较平整,较为可靠,因为接茬的紧准是碾压后的路面,而路边缘可能会因碾压有所变形。如果是热接茬施工,小滑撬可放置在未碾压路面的边缘处。
(二) 纵向传感器的安置、检查与调整
纵向传感器的安装位置一般在牵引点上或熨平板上或在牵引点与熨平板之间(图6-7)。
在安装妥善后要将它调整在其“死区”的中立位置(“死区”的范围一般在工厂内已调整好,不必再调整)。调整之前要先检查左右牵引臂较点的高度是否一致,其适当的高度应是油缸行程处于中心位置。调整时要将牵引臂的铰销锁住。传感器处于中立位置时其信号灯不亮,如果信号灯亮,则表明它还未处在中立位置,要再次调整。调好后,拔出牵引臂锁销,将传感器的工作选择开关拨到“工作”位置。此后接上电线,打开电源开关进行约10min的预热。等到摊铺机摊铺到10~15m后,铺层厚度达到规定值时,就可让自动调平装置投入工作。
(三) 横坡的控制
一般情况下,铺层的横坡由横坡控制系统配合一侧的纵坡传感器来控制。但是如果一
次摊铺的宽度较大(6m以上),由于熨平板的横向刚度降低,容易出现变形,使摆锤式横坡传感器的检测精度降低,因此常改用左右两侧的横坡控制系统。当路面的横坡变化过多过大时,也常如此。横坡控制系统包括横坡传感器、选择器和控制器等。
直线段摊铺时,只要给定设计的横坡值,就能实现自动控制。在弯道上摊铺时,因横坡在变化,难以实现自动控制。为了正确的操作,可事先在弯道路段每5m打一标桩,将各桩处的坡度值记入表格内,并画一曲线图;如果转弯半径很小,两桩的间距可适当缩小(最小为1m),进和出弯道处都要有标桩,不过其间距可较大些。操作人员根据图表在进入某标桩之前约2m处提前调整横坡选择器(因为横坡的实际变化滞后于调整动作)。
六、摊铺过程的质量检验及缺陷分析
(一) 质量检验
1、沥青含量的直观检查
如果混合料又黑又亮、料车上的混合料成圆锥状或混合料在摊铺机受料斗中“蠕动”,
则表明沥青含量正常;如果混合料特别黑亮,料车上的混合料呈平坦状或沥青结合料从骨料中分离出来则表明沥青含量过大(或骨料没有充分烘干,表面上看起来沥青太多);如果混合料呈褐色、暗而脆、粗骨料没有被安全裹覆、受料斗中的混合料不“蠕动”,则表明含量太少(或过热、拌和不充分)。
2、混合料温度
沥青混合料在正常摊铺和碾压温度范围内,往往冒出淡蓝色蒸汽。沥青混合料产生黄色蒸汽或缺少蒸汽说明温度过高或过低。
通常在料车到达工地时,测定混合料的温度。有时在摊铺机后测定。每天早晨要注意做这项工作,因此时下承层表面温度和气温都比较低。平时只要混合料似有温度较低现象或初次碾压,而压路机跟不上时,则应测定温度。
测量铺层的温度时,应将温度计的触头插进未压实的面层中部,然后把触头周围轻轻用足踏实。目前也有许多地方采用电子点温计测定。
3、厚度检测
摊铺机在摊铺过程中,应经常检测虚铺厚度。
4、表观检查
未压实混合料的表面结构无论是纵向或横向都应均匀、密实、平整、无撕裂、小波浪、局纹、拉沟等。产生这些质量缺陷的原因有:机械本身的调整、摊铺机的操作和混合料的质量等方面,如表6-23所示。
为了防止和消除在施工中可能发生的各种质量缺陷,应注意以下几点:
1、波浪形基层的摊铺,不必考虑摊铺厚度的均一性,实际的混凝土用量应比理论计算的要多。在波浪地段,即使摊铺得很平整,在碾压后仍会出现与基层相似的波形。因此对有大波浪的基层应在其凹陷处预先铺上一层混合料,并予以压实。在平整度较差的地段摊铺联结层和面层时,应预先测好各点铺层的标高,把厚度调节器调整到与各点标高相适应的位置。但要求达到更高平整度时,最好采用自动调平装置。
2、摊铺机的操作及本身的调整对摊铺质量影响很大。摊铺机速度的改变会导致摊铺厚度的变化。为了保持恒定的摊铺厚度,当速度变快时,厚度调节器应稍微向右(增加厚度方向)转动。当速度减慢时,则稍微向左(减少厚度的方向)转动。其调整量还应根据混合料种类的不同而不同。转动厚度调节器时,每次不应超过1/4圈,一般尽量避免转动它(除非发现了严重的凹凸与波浪),因此利用熨平装置的自动调节能力可能比转动厚度调节器去调整更好些。
振捣梁起捣实混合料,同时混合料对熨平板有一定支承的作用,如果工作不正常,会改变混合料的支承能力,从而使摊铺厚度发生变化,铺层出现不平。振捣梁的底面比熨平板底面低得太多时,熨平板的边缘容易粘附混合料,这样熨平板底面就不能全部用来压实混合料,而是铺层易形成裂纹和拉沟。如果振捣梁的底面过高时,熨平板底板容易磨损。振捣梁的底面应调整到比熨平板底面低0.4~0.5mm为宜。
熨平板底面磨损或严重变形时,铺层容易产生裂纹和拉沟,故应及时更换。有时熨平板的工作迎角太小,也会使铺层的两边形成裂缝或拉沟。在这种情况下,可调整熨平板的前缘拱度,并在试铺过程中应多次调整,直到能铺出具有良好的铺层为止。如果多次调整仍不能消除上述缺陷,就应该更换熨平板的底板。
3、沥青混合料的性质也是影响摊铺质量的主要原因之一。混合料的性质不稳定,易使摊铺厚度发生变化。如温度过高,沥青量过多,矿粉掺量过多等都会使铺层变薄。
混合料中的沥青与矿粉过量会减小其承载能力,所以熨平板的工作迎角应增大,使铺层增厚一些。这种混合料还容易受温度的影响。一般温度应控制在140~160℃的范围内,当高于此范围时,混合料变软而承载力大大降低。温度过低时,混合料又会变硬。此外,在混合料搅拌以及运输过程中,如管理不当都会使其性质发生变化,从而影响铺层厚度。所以,此时应根据混合料性质的变化而及时改变熨平板的工作迎角。此种变化可从铺层厚度突然变化中察觉到。含沥青、矿粉及小于0.074mm的石屑较多的混合料都是很难铺的,在摊铺过程中,铺层厚度变化也较频繁,亦应给以足够的重视。
当矿料中的大颗粒尺寸大于摊铺厚度时,在摊铺过程中该大颗粒将被熨平板拖着滚动,使铺层产生裂纹、拉沟等。所以应严格控制矿料粒径,使其最大粒径小于摊铺厚度的一半。
混合料的配比不当,会产生全铺层的裂缝。因为振捣梁在摊铺过程中对混合料进行捣实的同时,还要将它向前推移,如果混合料的大颗粒过多,就会出现全铺层的大裂缝。为了消除这种裂缝,有时可将熨平板加热进行热熨,但大多数情况需要改变混合料的配比。
4、其它因素。轮胎摊铺机气压超限(一般为0.5~0.55MPa),摊铺机易打滑,气压过低,机体会随受料重量变化而上下变动,使铺层出现波浪。履带式摊普机履带松紧超限将导致摊铺速度发生脉冲,进而使铺面形成搓板。履带或轮胎的行驶线上因卸料而撒落的粒料未消除,该部分摊铺厚度易突变。被顶摊的料车刹车太紧,使摊铺机负荷增大,或料车倒退撞击摊铺机或单侧轮接触、另侧脱空等会引起速度变化或偏载,使铺面出现凸楞。施工中往往第一、二车料质量常较差,注意取舍或调剂使用。自动熨平装置运用中,挂线不紧,中间出现挠度,会引起铺层波浪。采用冷接茬法摊铺时,其纵向接茬由于密实度不够,行车不久往往会产生坑洼和裂缝。因此必须注意接茬的重叠量,并在前一条摊铺带未被弄脏或变形之前就摊铺后一条。以上这些因素,在施工中加以注意,缺陷是能够避免的。
第六节 沥青混合料的压实技术
压实是沥青路面施工的最后一道工序,若采用了优质的筑路材料,精良的拌和与摊铺设备及良好的施工技术,摊铺出了较理想的混合料层,而良好的路面质量最终要通过碾压来体现。如果碾压中出现任何质量缺陷,必将前功尽弃。应此,必须重视压实工作。
压实的目的是提高沥青混合料的强度、稳定性以及疲劳特性。研究表明,在渠化交通条件下,若压实不足,会出现车辙。10.2cm厚的沥青混凝土路面,其压实度为95%,当其渠化交通进一步压实至100%时,将产生5mm的车辙深度;标准压实度相应的孔隙率增加1%,疲劳寿命将要降低约35%,压实度每降低1%,沥青混合料的渗透性提高两倍,压实不足,导致空隙率增大,从而加速沥青混合料的老化;过压将会使矿料破碎而使压实度反而降低或空袭率过小,易出现泛油和失稳,影响路面的强度与稳定性。因此,必须合理地进行碾压,
压实工作的主要内容包括碾压机械的选型与组合、压实温度、速度、遍数、压实方式的确定及特殊路段的压实(弯道与陡坡等)。
一、碾压机械的选型与组合
(一) 常用沥青路面压实机械
目前,最常用压路机有静作用光轮压路机、轮胎压路机和振动压路机。
1、静作用光路压路机
静作用光轮压路机可分为双轴三轮式(三轮式)和双轴双轮式(双轮式)。三轮式后面有两个较大的驱动轮,前面是一个较小的从动轮,常用于沥青混合料的初压,其重量为2.5~16t,国外也有三轮三轴串联式光轮压路机。
双轮式压路机,前后各一个轮子。根据结构要求,转向轮可为分开式,也可为整体式,其重量大约1.0~12t。这种压路机通常较少,仅作为辅助设备。双轮式压路机的结构与三轮压路机的结构比较,具有更好的压实适应性,能在摊铺层上横向碾压,产生更均匀的密实度。
三轮三轴式压路机有三个等宽的碾压滚轮,分装在刚性机架的前中后三根轴上,后轮为驱动轮,直径较大,中、前轮均为从动轮,直径较小,也有制成三个均为驱动轮的型式。该种压路机大多为重型,适用于压实沥青混凝土路面,且在作业时可以随被压层表面的不平度自动地重新分配各滚轮上的荷载(见图6-8),压平料层的凸起部分,主要用于要求平整度高的高等级公路路面的压实作业。
2、轮胎压路机
轮胎压路机根据其大小,可装5~11个光面橡胶轮,这些橡胶轮通常具有改变轮胎压力的性能,其工作重量一般为5~25t。轮胎压路机可用来进行接缝处的预压、坡道预压、消除裂纹、薄摊铺层的压实等作业。
3、振动压路机
振动压路机分为自行式单轮振动压路机、串联振动压路机和组合式振动压路机。
自行式单轮振动压路机,前面有一个振动轮,后面是两个橡胶驱动轮。有些机型前轮也是驱动轮。为了压实沥青混合料,振动轮有不同振幅和频率可供选用。这种压路机的工作重量大致为4~12t。自行式单轮振动压路机,常常用于平整度要求不高的路面作业。
沥青混合料的压实度要求较高时,常适用串联振动压路机。串联振动压路机分为单轮振动和双轮振动,并且大型串联振动压路机有较多的频率和振幅。驱动轮是一个或两个,工作重量为1~8t。串联振动压路机的转向系统有:铰接转向、前轮转向及前后轮偏移的铰接转向。
铰接转向的铰接点设置在前后轮间的中央位置(图6~9a),转向时,前半部分和后半部分绕垂直地面的中心轴旋转。铰接转向能更机动灵活地压实弯道处的路面。压路机转弯时,可偏移行驶,同时前后轮能保持在同一碾压带上。铰接转向,几乎可均匀分配前后轴上的荷载。但要求司机熟练掌握交接转向技术。
前轮转向结构中,旋转轴位于前轮中间(图6-9b )。当压路机转向时,转弯与转向角直接相关。由于转向角越大,产生的剪切力也越大,因此,转向轮从中间分为两部分(即分开式),以减少剪切力。使用分开式前轮转向的优点是,能减少前轮转向时的位移量,减少剪切力。但前轮转向的振动压路机,不可能前后轮都振动,因而不利于平均分配轴荷载。
前后轮偏移(中心线不在同一直线上)铰接转向,是标准铰接转向装置的进一步发展,其代表机型为BW160AD和141AD型压路机(BOMAG公司生产),这种压路机上装有一个特殊铰接结构,它能使压路机后半部分中心线偏移10cm(图6-10)。
使用这种压路机的优点是,当靠路缘碾压时,能较少转弯中损坏路缘的危险(图6-11)。使用传统的铰接式压路机碾压,在转弯时因结构限制,机械后半部分易损坏路缘。因此,铰接转向和前后轮偏移铰接转向的串联振动压路机,在当今沥青混合料压始中,使用得最广泛。
组合式压路机是轮胎压路机和振动压路机的一种组合形式。这种压路机由一个振动轮和3~4个充气橡胶轮,这些橡胶轮可安装在压路机前面或后面。这一设想,原是为了把轮胎压路机的优点同振动压路机的优点结合在一起。然而,实践证明,这种结合是令人失望的,只有经过适当的选择和运用,才是有效的。
(二) 选型与组合
结合工程实际,选择压路机种类、大小和数量,应考虑摊铺机的生产率、混合料特性、摊铺厚度、施工现场的具体条件等因素。
摊铺机的生产率决定了需要压实的能力,从而影响了压路机大小和数量的选用,而混合料的特性则为选择压路机的大小、最佳频率与振幅提供了依据。如混合料矿料含量的增加或最大尺寸的增大,都会使其工作度下降,要达到要求的密实度就需要较大压实能力的压路机。沥青稠度高时,也是如此。选择压路机重量和振幅,应与摊铺层厚度相适应,摊铺层厚度小于6cm,最好使用振幅为0.35~0.6mm的中小型振动压路机(2~6t),这样,就可避免材料出现推料、波浪、压坏骨料等现象。在压实较厚的摊铺层(厚度大于10cm)时,使用高振幅(可高达1.00mm)的大、中型振动压路机(6~10t)。压路机的选择必须考虑施工现场的具体情况,若有陡坡、转弯的路段应考虑压路机操作的机动灵活性。BOMAG公司制定了根据材料级配、摊铺厚度及环境因素,最有效地选择压路机型号的图表。
压路机的需要量是根据合同范围确定。但在工程开始时,难以得知压实遍数。因为混合料的冷却速率及其他因素难以确定。因此,只有在摊铺初期通过仔细观察、测量和试验才能得出,一般要求压路机尽可能尾随摊铺机。在混合料温度、厚度、下承层温度变化的条件下,研究混合料冷却速率表明:利用温度参数可以相当准确地估算有效压实时间。所谓有效压实时间是指混合料从摊铺后的温度冷却至最低压实温度所需的时间,这种有效时间的估计可帮助工地工程技术人员确定需要多少台压路机。
例如沈大高速公路某施工队碾压机械组合见表6-24。考虑了压实温度的要求和摊铺机生产率后提出与气温相应的碾压长度为:常温时(15℃左右)40~50m;偏低时(<10℃)20~40m;偏高时(>20℃)50~80m;高温时(>30℃)100m左右。
二、压时作业的程序及一般要求
压实程序分为初压、复压和终压三道工序。初压的目的是整平和稳定混合料,同时,为复压创造有利条件,是压实的基础,因此要注意压实的平整性;复压的目的是使复合料密实、稳定、成型,混合料的密实程度取决于这一道工序,因此必须与初压紧密衔接,且一般采用重型压路机;终压的目的是消除轮迹,最后形成平整的压实面,因此,这道工序不宜采用重型压路机高温下完成,否则,会影响平整度。当然,为保证压实表面的平整、密实及外形规则,碾压作业亦应按一定的要求进行,并对未压实的边角应辅以小型机具压实。
1、 压实程序
初压时用6~8t双轮压路机或6~10t振动压路机(关闭振动装置)压两遍,初压温度为110~130℃,初压后检查平整度、路拱,必要时予以修整。如在碾压时出现推移,可待温度稍低后再压;如出现横向裂纹,应检查原因及时采取措施纠正。
复压时用10~12t三轮压路机、10t振动压路机或相应的轮胎压路机进行,宜碾压
4~6遍至稳定和无明显轮迹,复压温度为90~110℃。
终压时用6~8t振动压路机(关闭振动装置)碾压2~4遍,终压温度为70~90℃。
2、压实方式
碾压时压路机应由路边压向路中,这样就能始终保持压路机以压实后的材料作为支撑边。三轮式压路机每次重叠宜为后轮宽1/2,这种碾压方式,可减少压路机前推料、起波纹等。双轮压路机每次重叠宜为30cm。压路机压是速度可参考表6-25。
3、应注意的其他问题
在碾压过程中,为了保证正常的碾压温度范围,每完成一遍重叠碾压,压路机就要向摊铺机靠近一些。这样作,也可避免在整个摊铺层宽度上,在相同横断面换向所造成的压痕。变更碾压道时,要在碾压区内较冷的一端,并在停止压路机振动的情况下进行。
压路机作业中,在平缓路段,驱动轮靠近摊铺机,以减少波纹或热裂缝(单轮驱动压路机)。碾压中,要确保压路机滚轮湿润,以免粘附沥青混合料。有时可采用间歇喷水,但应防止用水量过大,以免使混合料表面冷却。
压路机每碾压一遍的末尾,若能稍微转向,就可将摊铺机后面的压痕减至最小。压路机不得在新铺混合料上转向、调头、左右移动位置或突然刹车和从碾压完毕的路段进出。碾压后的路面在冷却前,任何机械不得在路面上停放,并防止矿料、杂物、油料等落在新铺路面上。路面冷却后才能开放交通。
三、接茬处的碾压
接茬压实的程序是先压横向接茬后压纵向接茬。
1、 横向接茬碾压
在条件许可的地方,可使用较小型压路机对横向接茬采用横向碾压(条件受限制的地方也可采用纵向碾压)。横向碾压开始时,使压路机轮宽的10~20cm置于新铺的沥青混合料上碾压,这时压路机重量的绝大部分处在压过的铺层上。然后逐渐横移到整个滚轮进入新铺层上。需要的话,开始时先用压路机静压,然后振动碾压。
2、 纵向接茬碾压
(1)热料层与冷料层相接
对这种接茬可采用两种方法碾压。第一种方法是压路机位于热沥青混合料上,然后进行振动碾压,这种碾压方法,是把混合料从热边压入相对的冷结合边,从而产生较高的结合密实度;第二种方法是在碾压开始时,只允许轮宽的10~20cm在热料层上,压路机的其余部分位于冷料层上,碾压时,过量混合料从未压实的料中挤出,这样就减少了结合边缘的料量,这种方法产生的结合密度较低。在这两种碾压过程中,压路机的碾压速度都应很底。
(2)热料层相接(梯队作业时)
这种接茬的压实方法是:先压实离中心热接茬两边大约为20cm以外的地方,最后压实中间剩下来的一窄条混合料。这样,材料就不能从旁边挤出,并形成良好的结合。
四、特殊路段的碾压
特殊路段的碾压指弯道、交叉口、路边、陡坡等处的压实作业。
1、 弯道或交叉口的碾压
应选用铰接转向式压路机作业,先从弯道内侧或弯道较低一边开始碾压(以利于形成支撑边)。对急弯应尽可能采取直线式碾压(即缺角式碾压),并逐一转换压道,对缺角处用小型机具压实。压实中注意,转向同速度向吻合,尽可能用振动碾压,以减少剪切力。
2、 路边碾压
压路机在没有支撑边的厚层上碾压时,可在离边缘30~40cm(较薄层时,预留20cm)处开始碾压作业。这样,就能在路边压实前,形成一条支撑侧面,以减少沥青混合料碾压时铺层塌边。在以后碾压留下的未压部分时,压路机每次只能向自由边缘方向推进10cm。
3、陡坡碾压
在陡坡碾压时,压路机的很大部分作用力将向下坡方向,因而增加了混合料顺坡下移的趋势。为抵消这种趋势,除了下承层表面必须清洁、干燥、喷洒粘层沥青处,压实时应注意,先采用轻型压路机预压(轮胎压路机不宜用作预压)。无论是上坡还是下坡,压路机的从动轮始终朝向摊铺方向,即从动轮在前,驱动轮在后(与一般路段碾压时相反)。这样做,从动轮起到了预压作用,从而使沥青混合料能够承受驱动轮所产生的剪切力。如果采用振动压路机,则应先静碾,待混合料达到稳定后,方可采用低振幅的振动碾压。
陡坡碾压中,压路机的起动、停止、变速要平稳,避免速度过高或过低,混合料温度不宜过高。
五、提高压实质量的关键技术
碾压温度的高低,直接影响沥青混合料的压实质量。混合料温度较高时,可用较少的碾压遍数,获得较高的密实度和较好的压实效果;而温度较低时,碾压工作变得较为困难,且易产生很难消除的轮迹,造成路面不平整。因此,在实际施工中,要求在摊铺完毕后及时进行碾压。一般来说,沥青混合料的最佳压实温度为110~120℃之间(国外也有人认为最佳碾压温度为120~150℃,这与沥青材料性能及压实设备有关),最高不超过160℃。所谓碾压最佳温度是指在材料允许的温度范围内,沥青混合料能够支撑压路机而不产生水平推移、且压实阻力较小的温度。
摊铺机后面的碾压作业段长度,由混合料的种类和压实温度来确定。一般来说,压路机尽可能靠近摊铺机进行碾压。达到了密实度后,再以最少的碾压遍数进行表面修整时,压路机可离摊铺机远一点。
若碾压时混合料温度过高,会引起压路机两旁混合料隆起,碾轮后的摊铺层裂纹,碾轮上粘起沥青混合料(尽管用水喷洒),及前轮推料等问题。而碾压温度过低时(50~70℃),由于混合料的粘性增大,导致压实无效,或起副作用。研究表明:当沥青混合料的摊铺初始温度每提高10℃,碾压时间需延长近30%。可见沥青混合料温度较高时,有利于缩短碾压时间,加快施工速度。
压实质量与压实温度有直接关系,而摊铺后混合料温度是在不断变化的,特别是摊铺后4~15min内,温度损失最大(1~5℃/min),因此必须掌握好有效压实时间,适时碾压。有效压实时间的长短与混合料的冷却速度、压实厚度等因素密切相关。影响冷却速度的因素有气温、湿度、风力和混合料下承层的温度等。凡遇气温低、湿度大、风力大,以及下承层温度低等,都会使有效压实时间缩短,并增加碾压困难。当沥青层厚增大25%时,其有效压实时间增大近50%。对较薄层沥青层碾压时,反而要比较厚的沥青层压实困难些,这主要是因为较薄层的沥青混合料温度降低速度要比后层快的多,从而使其有效压实时间大大缩短。
2、选择合理的压实速度与遍数
合理的压实速度,对减少碾压时间,提高作业效率有十分重要的意义。在施工中,保持适当的恒定碾压速度是非常必要的。一般速度控制在2~4km/h,轮胎压路机可适当提高,但不超过5km/h。速度过低,会使摊铺与压实工序间断,影响压实质量,从而可能需要增加压实遍数来提高压实度。碾压速度过快,会产生推移、横向裂纹等。
国外有关资料指出:振动压路机压实沥青混合料的速度为8~10km/h(但美国沥青学会建议不超过4.8km/h),可获得较高的压实质量和经济效益。表6-26所列三组对比试验表明,在不同碾压温度条件下,当碾压遍数相同,而碾压速度不同时(5km/h和10km/h两种速度),沥青混合料的压实度平均值相差很小,仅为1%。
选择碾压速度的基本原则是:在保证沥青混合料碾压质量的前提下,最大限度地提高碾压速度,从而减少碾压遍数,提高工作效率。
3、选择合理的振频和振幅
目前,越来越多的振动压路机被用来碾压沥青混合料,为了获得最佳的碾压效果,合理地选择振频和振幅是非常重要的。
振频主要影响沥青面层的表面压实质量。振动压路机的振频比沥青混合料的固有频率高一些,则可获得较好的压实效果。试验表明,对于沥青混合料的碾压,其振频多在42~50Hz的范围内选择。
振福主要影响沥青面层的压实深度。当碾压层较薄时,宜选用高振频、低振福;而碾压层较厚时,则可在较低振频下,选取较大的振幅,以达到压实的目的。
对于沥青路面,通常振福可在0.4~0.8mm内进行选择。
4、混合料特性
沥青混合料的特性对压实质量亦有较大影响,表6-27中列出了影响的原因、后果及对策,在碾压作业中可供参考。
六、压实质量的检测
压实质量的检测应根据合同有关文件(技术规范)的规定及要求进行。主要检测项目有压实度、厚度、平整度、粗糙度。而且要求表观密实均匀。当沥青混合料碾压成型后,其缺陷一般很难修整。对一些较大缺陷,如厚度不足,平整度太差、松散、泛油等应急时返工,即使已成型变硬也要返工。对松散、泛油往往是局部返工。而对厚度不足或平整度太差则往往要求某一段落全面返工,当然,经济损失是较大的。因此,现场压实过程中质量的检查与问题及时纠正是十分重要的,要努力把缺陷降低到最低程度,最好不出现返工现象。
厚度和压实度一般可通过钻取芯样的办法来检测。核子密度仪目前作为辅助检测手段,国内许多施工单位使用后认为,该仪器的测量准确性还值得进一步探讨。有时也在工地通过钻芯样检测沥青混合料的级配及沥青用量等。
第七节 沥青面层施工质量控制与验收
一、国内外沥青路面质量检测方法简介
国内外对高等级公路路面面层施工质量的控制指标不少,相应地检测手段也较多,包括面层厚度、平整度、强度、抗滑、渗水。以及车辙、裂缝等测试设备。目前国外最先进的路面平整度测试仪是英国运输与道路研究所(TRRL)制作的激光平整度仪。
目前,我国使用最多的是XLPY型系列连续式平整度仪。也有一些地区使用了颠簸累计仪。西安公路学院根据车桥振动加速度谱分析法研制的测震仪用于路面舒适性的评价与分析,取得了令人满意的结果。
国外测定路面抗滑的先进仪器采用机电一体的纵横综合测定挂车机构,该仪器测定的车速可达20~60km/h,摩阻系数测定值精度较高,可达0~0.05%。在测定表面纹理结构方面:英国采用激光纹理仪;美国采用透水法,即在渗水器与路面接触处加一橡胶垫,根据橡胶垫与公路接触处渗出的水来推算路面的粗糙度;法国用合成树脂将路面纹理翻制取形,然后切断面放大观察,以求表面粗糙度。
在我国抗滑性能测定的仪器和方法有:摆式仪(BM法)、五轮仪、制动仪、减速仪及滑溜拖车法、试验车法等。表面纹理深度采用铺砂法测定。
在路面强度测定方面,法国采用了拉克鲁瓦自动弯沉仪。目前,我国仍使用杠杆式弯沉仪测定路面弯沉(壁长3.6m与5.4m两种型式),国内有关科研单位已研制了自动弯沉仪。
国外较先进的沥青路面裂缝测定仪器采用了遥感摄影技术,它使用红外遥感摄影得到沥青路面裂缝图像,利用光电效应将图像转变成电量,输入计算机进行数据处理,直接得到裂缝率或车辙面积率,这一技术已在英、法等国采用。西安公路学院利用光电技术研制的PERA型路面车辙仪不久将投放市场。
路面厚度测定常采用射线或超声检测技术,而以超声技术使用较多。通常用反射法测定面层厚度,但仅在水泥混凝土路面厚度检测中使用较成功,对于沥青路面则难保证测量精度,尚在研究阶段,沥青路面碾压的厚度我国多采用钻取芯样或挖坑测定的方法。在我国,路面自动测厚仪也在研制开发。
高等级公路路面工程的评价往往依据于多项指标。法、英、日等发达国家都普遍装备了“综合测试专用车”,车上配有各种检测仪器及数据处理器等。只要到测试现场一次,就能测取各种所需的数据,方便且效率高。一台路面“综合测试专用车”约需人民币上百万元,如此高昂的价格限制了它在我国的推广应用。但由于它有许多优点,在一些检测中心配置还是可能的,用来测定多指标值建立数据库,评价路面使用性能。
二、我国沥青路面施工质量控制及验收的基本内容
下面一些表给出了沥青混凝土与沥青碎石层的检测项目级标准。
1、 质量控制的基本内容
沥青路面施工质量控制包括所用材料的质量检验、修筑试验段、施工过程的质量控制和
工序间的检查验收。
施工前沥青材料应按规定的技术要求进行各项指标的试验。在施工中,逐班抽样检查时,
根据情况可只做针入度、软化点、延度三项试验。
施工前对石料、砂及石屑、矿粉也应进行质检。对石料测定的项目有:炕压强度、磨损率、磨光值、压碎值、级配组成、相对密实度(比重)、含水量、吸水率、土及杂质含量、扁平细长颗粒含量、与沥青粘结力、松方单位重等;对砂和石屑测定其相对密度(比重)、级配组成、含水量、含土量等;对矿粉测定其相对密度和含水量并进行筛析试验。
施工过程中应对沥青混合料性能做抽样检查,其项目有:马歇尔稳定度、流值、空隙率、饱和度、沥青抽提试验、抽提后的矿料级配组成。
2、 质量控制标准
施工中沥青土、沥青碎石路面施工质量控制标准见表6-28和表6-29。
3、 竣工验收
竣工后的沥青混凝土和沥青碎石路面检查验收的标准见表6-30。对非破损检验的宽度、中线高程、横坡度,每1检查段的长度宜以1km长为评定单位,求取平均值。监理抽查时的检查段的选择按随机取样的原则确定,总长度不少于施工历程的30%,且不少于3个检查段。平整度及摩擦系数采用全线测定时为全程连续测定,并以每100m为1个计算长度,求取平均值。钻孔取样检查的厚度、压实度、沥青用量、矿料级配以全线随机取样的方法选点,以全线平均值评定。检查指标平均值的评定标准对一般公路可考虑的保证率,对高等级公路可考虑
的保证率。当评定指标为单边检验时,
,t=2.282;
,t=1.645。平整度、弯沉应符合
表中规定值的要求,厚度、宽度、粗糙度、摩擦系数等,应符合
表中规定值的要求。当评定指标为双边检验时,
,t=1.645;
,t=1.96。中线高程、横坡、沥青用量、矿料级配等,应符合(设计值—允许值)<
(设计值+允许值)的要求。
弯沉的测定应在基层的设计龄期或第二年的不利季节时进行。贝克曼梁及自动弯沉仪可选择其中一种测定。表中全线是指一个施工单位施工的全长。
第七章 水泥混凝土路面施工技术
水泥混凝土路面具有刚度大、强度高、稳定性好、养护维修费用低等优点。国内外对水泥混凝土路面的修筑技术一直进行不懈地研究和总结,使水泥混凝土路面在技术上日益完善,得到了广泛应用。特别是在高等级、重交通的道路上有了较大的发展。一些国家的高等级公路,根据交通量的大小,常用水泥混凝土面板的厚度为22~28cm,在交通量很大的重交通下,采用的板厚度为30~32cm,基层常采用水泥稳定力料或碾压式水泥混凝土(RCC)等。
第一节 材料要求与混合料组成设计
水泥混凝土面层直接承受行车荷载的重复作用及环境因素(温度和湿度)的影响。因而要求混凝土板必须具有足够的强度和耐久性,同时具有抗滑、耐磨、平整的表面,以确保行车的安全和舒适。而这些要求能否达到则与材料品质、混合料组成有很大关系,因此,必须研究水泥混凝土的路用要求,分析其影响因素,从而选择合适的材料,科学地进行配合比组成设计,为修筑出符合标准的水泥混凝土路面提供基本保证。
一、对水泥混凝土的基本要求
(一) 工作性(施工和易性)
水泥混凝土在凝结硬化之前,称为新拌混凝土。新拌混凝土是不同粒径粒子的分散相在水介质中的一种复杂分散系,它具有弹—粘—塑性性质。目前在生产实践中,对其性质主要用工作性来表征。混凝土的工作性常包括:“流动性”、“可塑性”、“稳定性”、“易密性”四个方面。优质的新拌混凝土应具有:满足输送和浇捣要求的流动性;不以外力作用产生脆断的可塑性;不产生分层、沁水的稳定性和易于浇捣致密的密实性。
目前还没有一种能够全面表征新拌混凝土工作性的测定方法,最常用的方法有:坍落度试验、维勃稠度试验和捣实因素试验等。
二、混凝土组成材料的要求
组成混凝土的材料有:水泥、细集料(砂)、粗集料(碎石)、水及外加剂。
(一) 水泥
水泥是混凝土的胶结材料,混凝土的性能很大程度上取决于水泥的质量。高等级公路水泥混凝土路面应采用强度高、干缩性小、抗磨性与耐久性好的水泥。水泥品种及标号的选用,必须根据公路等级、工期、铺筑时间和方法及经济性等因素综合考虑决定。从国内外路用水泥的使用情况看,主要采用硅酸盐水泥和普通硅酸盐水泥,也可采用其他品种水泥,但必须符合路用性能及经济上合理的要求。根据我国路用水泥的使用情况调查,并参照国外对路用水泥的规定,建议水泥标号:特重、重交通不小于425。
根据路用性能要求及试验路的测定和调查,对路用水泥的主要技术品质建议;熟料中铝酸三钙含量不得超过5%,铁铝酸四钙含量不得低于18%;熟料中游离氧化钙含量不得超过1.0%;碱含量应符合中热硅酸盐水泥(GB200-89)的规定;三氧化硫、氧化镁含量和安定性应符合(GB175-85)的规定;0.08mm(方孔筛)筛余不得超过10%;初凝不得早于1.5h ,终凝不得迟于10h。各龄期强度值不得低于表7-2的数值;水泥胶砂试件28d龄期的干缩率不得大于0.09%;砂浆磨耗率不得超过1.0%。
据调查,目前国内大中型水泥厂中约有55%的厂家,其熟料矿物组成符合或基本接近现有水泥指标。因此,路面宜选用硅酸盐水泥(普通硅酸盐水泥)。
(二)细集料
混凝土中粒径在0.16~5mm范围的集料称为细集料。细集料可采用天然砂(如河砂、海砂和山砂等),也可用扎制石料得到的人工砂(如石屑等)。作为细集料的砂应满足一定的级配及细度模数、有害杂质含量少等技术要求。
1、级配
优质的混凝土用砂希望具有高的密度和小的比表面,这样才能既保证新拌混凝土有适宜的工作性和硬化后混凝土有一定的强度、耐久性,同时又达到节约水泥的目的。混凝土用细集料的级配要求,应与相应的粗集料级配所组成的矿质混合料一并考虑。但是,如果细料的级配不良则很难配制成良好的矿质混合料。因此,细级料不仅应质地坚硬、耐久、洁净,且应符合表7-3的级配要求。
表中Ⅰ区砂属于粗砂范畴,当应用Ⅰ区砂配制混凝土时,应铰Ⅱ区砂采用较大的砂率,否则,新拌混凝土的内磨阻力较大、保水差、不易捣实成型。Ⅱ区砂是中砂和一部分偏粗的细砂组成,系一般常用的砂。Ⅲ区砂为细砂和一部分偏细的中砂组成,应用Ⅲ区砂配制时,宜采用铰Ⅱ区砂为小的砂率。这是因为Ⅲ区砂所配制的新混凝土粘性略大,比较细软,易于插捣成型,而且由于Ⅲ区砂的比表面大,故对新拌混凝土工作行的影响比较敏感。为提高混凝土的耐磨性,小于0.08mm的颗粒不应超过3%。
2、细度模数
细度模数是各号筛的累计筛余百分率之和除以100,按下式计算:
式中:——分别是5、2.5、……、0.16号筛的累计筛余(%)。
表7-3以细度模数的砂,按0.63mm筛孔的累计筛余划分为3个级配分区。
为粗砂;
为中砂;
为细砂;
为特细砂。细度模树只反应全部颗粒粗细程度,而不能反映颗粒的级配情况。因为细度模数相同而级配不同的砂,可配制出性质不同的混凝土。所以考虑砂的颗粒分布情况时,应同时应用细度模数和级配两项指标,才能真正反映其全部性质。路用砂细度模数宜在2.5以上。
3、杂志含量
细集料中含有泥土(包括尘屑和粘土等)、有机质、硫化物和硫酸盐等杂质时,会在级料表面形成包裹层而妨碍级料同水泥石的粘附,妨碍水泥水化,而且还会同水泥水化产物产生不良的化学反应等。为此,细级料中有害杂质的含量不应超过限量。含泥量不大于3%,采用冲洗法测定;硫化物及硫酸盐含量(折算成SO3)不大于1%;采用比色法测定有机质含量,颜色不深于标准溶液的颜色。同时砂中不得混有石灰、煤渣、草根等其他杂物。
(三)粗级料
为保证混凝土具有足够的强度、良好的抗滑、耐磨及耐久性,粗集料(碎石与砾石)应质地坚硬、耐久、洁净、符合一定级配。
1、粗级料技术要求
卵石和砾石的技术要求应符合表7-4的规定。
表中针状指矿料长度不大于平均粒径的2.4倍,片状指厚度小于平均粒径的0.4倍。表面粗糙且多棱角的碎石集料,同水泥石的粘附性好,配合混凝土具有较高的强度,在相同水泥浆用量条件下,砾石配制的混凝土具有较好的工作性。
对于寒冷地区的混凝土,集料的坚固性要求在硫酸钠溶液中浸湿和烘干5次循环后的重量损失小于5%(寒冷地区)或3%(严寒地区)。
混凝土集料中如含有非晶质活性二氧化硅,同时水泥中碱性氧化物含量较高(>0.6%),并且混凝土长期处于潮湿环境,则水泥中的碱性氧化物水解后生成的氢氧化钠和氢氧化钾会同级料中的活性二氧化硅发生化学反应,在级料表面生成一种复杂的碱—硅酸凝胶体。这种凝胶体吸水后体积膨胀,能引起混凝土结构破坏,这种损坏现象称为“碱—级料反应”。目前已确定含非晶质二氧化硅的岩石有:蛋白质、玉髓、鳞石英、方石英、硬绿泥岩、硅镁石灰岩、玻璃质或隐晶流纹岩、安山岩和凝灰岩等。
2、级配
粗集料的最大粒径应不大于40mm,其级配可采用连续级配或间断级配,连续级配的优点是所配制的混凝土较密实,具有优良的工作性,不易产生离析现象。间断级配同它相比,配制相同强度混凝土所需的水泥用量可少些,但容易产生离析现象,并需采用强力振捣。根据今年我国使用经验,粗集料集配范围可参考表7-5。
(四)水
清洗集料、拌和混凝土及养生所用的水,不含有影响混凝土质量的油、酸、碱、盐类、有机物等。饮用水一般均适用,非饮用水经化验;硫酸盐含量(SO4计),不超过2.7mg/cm3、含盐量不得超过5mg/cm3、PH值不得小于4时,也可使用。
(五)外加剂
为了改善混凝土的技术性质,有时在混凝土的制备过程中加入一定量的外加剂。常用的外加剂有流变剂、调凝剂和改变混凝土含气量的外加剂三大类。
1、流变剂
流变剂是改善新拌混凝土流变性能的外加剂,如塑化剂、减水剂和流化剂,而减水剂是这类外加剂的最典型代表。
减水剂又称分散剂。由于使用时单位体积混凝土混合料中的用水量减少,故名减水剂。混凝土加入适量的减水剂,可在保持新拌混凝土工作性相同的情况下,显著地降低水灰比,或在水灰比不变的条件下,可大大改善新拌混凝土的工作性,从而提高混凝土的强度和改善混凝土的抗冻、抗磨、收缩等一系列物理—力学性能。
新拌混凝土掺加减水剂后,通常减水率为10%到20%;而摻加高效减水剂后,其减水率可达25%到30%。为区别于普通减水剂,故将高效能减水剂称为“流化剂”(或超塑化剂SP)。
减水剂又按其对水泥凝结时间、以及是否引气而分为标准型、引气型、缓凝型和减水早强型等减水剂。目前常用的有木质素系减水剂(简称M剂),萘氏减水剂(NF、MF等),水溶性树脂(密胺树脂)类减水剂(SM)等。
2、调凝剂
调凝剂是调节水泥凝结时间的外加剂,是促凝剂、速凝剂和缓凝剂的总称。
水泥凝结时间与水泥矿物的水化速度、水泥—水胶体体系的凝聚过程、加水量有关。因此,凡能改变水泥矿物水化速度,“水泥—水”胶体体系凝聚过程及拌和水量的外加剂,均可作为调凝剂使用。
1)促凝剂
促凝剂是缩短混凝土中水泥浆从塑性状态转化到固体状态所需时间的外加剂。促凝剂与水泥矿物作用能生成稳定和难溶化合物,加速水泥浆凝聚结构的生成。常用的促凝剂有水玻璃、铝酸钠、碳酸钠、氟化钠、氯化钙和三乙醇胺等。其中氯化钙、三乙醇胺等也间有早强剂的作用。
2)缓凝剂
换凝剂是延缓水泥凝结时间的外加剂。根据前述的调剂原理,因其在水泥及其水化无表面上的的吸附作用,或与水泥反应生成不溶层而达到缓凝的效果。
为调节水泥凝结时间的缓凝剂(天然时拌制混凝土),如羟基酸盐类(洒石酸等)、所墙基碳水化合物类(糖蜜等)和无机化合物类等。
3)早强剂
早强剂是加速水泥混凝土早期强度发展的外加剂。早强剂对水泥中的硅酸三钙和硅酸二钙等矿物的水花有催化作用,能加速水泥的水化和硬化,具有早强的作用。通常采用的有氯化钙早强剂,三乙醇符合早强剂等。
4)速凝剂
速凝剂是使水泥混凝土迅速凝结和硬化的外加剂,可用于冬季施工。速凝剂与水泥在加水拌和时立即反应,使水泥中的石膏失去缓凝作用,促成铝酸三钙迅速水化。并在溶液中析出其水化物,导致水泥迅速凝结。
我国目前生产的“红星1型”,“711型”和“782型”等速凝剂,是由剂中促凝剂复合而成的。例如红星1型系由矾土、纯碱和石灰石煅烧而成的铝氧熟料,再与生石灰和纯碱按一定比例混合磨细而成。通常速凝剂加量为水泥用量的2.5%到4.0%时,水泥初凝时间可在5min之内,终凝在10min之内,并能提高早期强度,28d强度常低于不加者,但以后并不下降。
3、改变混凝土含气量的外加剂
引气剂能在混凝土中形成细小的、均匀分布的,并在硬化后仍能保持的空气微泡。
引气剂为憎水性表面活性物质,由于它能降低水泥—水—空气的界面能,同时由于它的定向排列,形成单分子吸附膜,提高泡膜的强度,并使气泡排开水分而吸着于固相粒子表面,因而能使搅拌过程混进的空气形成微小(孔径0.01到2mm)而稳定的气泡,均匀分布于混凝土中。
目前常用的引气剂有松香热聚物、烷集磺酸钠和烷基苯碳酸钠等阴离了表面活性剂。适宜的掺加量为水泥用量的0.005%到0.01%,混凝土中含气量为3%到6%。对新拌混凝土,由于这些气泡的存在,可改善工作性,减少沁水和离析。对硬化后的混凝土,由于气泡彼此隔离,切断毛细孔通道,使水分不易渗入,又可缓冲其水分结冰膨胀的作用,因而可提高混凝土的抗冻性、抗渗性、和抗蚀性。但是由于气泡的存在,混凝土强度有所降低。
所选用的外加剂的质量应符合国家标准(GB8076—87)的规定(见表7-6)并应在充分调查试验和实地使用后,再决定所选用的外加剂是否适用。
由于引用外加剂后会改变混凝土对制备工艺的要求,使用时应特别小心,同时,要注意配量正确和在混合料中拌和均匀。
三、接缝材料要求
接缝材料按使用性能分为接缝板和填缝料两类。接缝板应选用适应混凝土板的膨胀与收缩、施工时不变形、耐久性良好的材料。填缝料应选用与混凝土板壁粘结力强、回弹性好、能适应混凝土的收缩、不溶于水和不渗水、高温不溢、低温不脆的耐久性材料。
1、接缝板的技术要求
胀缝材料一般下部为接缝板、上部为填缝料。可作为接缝板的材料有杉木板、软木板、橡胶、海绵泡沫树脂类等。接缝板应具有一定的压缩性和弹性,当混凝土膨胀时不挤出,收缩时能与混凝土板缝联接不产生间隙;在混凝土路面施工时不变性且耐腐蚀。接缝板的技术要求见表7-7。
2、填缝料的技术要求
填缝料按施工温度分为加热施工式和常温施工式两种。
加热施工式填缝料目前主要有沥青橡胶类、聚氯乙烯胶泥类和沥青玛蹄脂类等。其技术要求见表7-8。表7-8中的弹性填缝料适用于公路等级较低的混凝土路面的缩缝,高弹性填缝料适用于公路等级较高的混凝土路面的涨缝和高速公路、机场道面的接缝。
常温施工式填料目前有聚氨脂焦类、氯丁橡胶类、乳化沥青橡胶类等。其技术要求见表7-9。
研究表明,接缝板中的软木板、加热式施工填料中的聚氯乙烯胶泥和常温式施工中的M880建筑密封膏以及聚脂改性沥青性能较优,可供混凝土路面工程使用。
四、钢筋
水泥混凝土路面所用的钢筋有传力杆、拉杆及补强钢筋等。钢筋的品种、规格应符合设计要求,钢筋应顺直,不得有裂缝、断伤、刻痕。表面油污和颗粒状或片状锈蚀应清除。所用的钢筋强度及弹性模量应符合表7-10的要求。
五、混凝土配比设计
水泥混凝土路面板厚度的计算以抗弯拉强度为依据,因此,混凝土的配合比设计应根据设计弯拉强度、耐久性、耐磨性、工作性等要求和经济合理的原则选用原材料,通过实验和必要的调整,确定混凝土单位体积中各种组成材料的用量。配合比设计的主要任务是选好水灰比、用水量和砂率这几个参数。其一般步骤为:根据已有的配合比试验参数或以往的经验,初拟设计配合比,并按其进行试验,在作必要的调整,得到设计配合比;根据混凝土的现场实际浇筑条件,如集料供应情况(级配、含水量等)、摊铺机具和气候条件等,进行适当调整,提出施工配合比。
(一)设计方法
配合比设计可采用经验公式法,其设计步骤为:
1、确定混凝土的配合比强度
式中:——设计弯拉强度(见表7-1)(MPa);
——提高系数,其值为1.10~1.15,可根据施工技术水平和工程的重要性选用。
2、计算灰水比C/W
碎石混凝土: (7-2)
(7-3)
式中:——水泥胶砂标准时间弯拉强度(MPa)。
路面混凝土的最大水灰比(C/W),应符合规定:公路、城市道路和厂矿道路,不应大于0.50;机场道面和高速公路,不应大于0.46;冰冻地区冬季施工,不应大于0.45。
3、计算用水量W
在水灰比一定的条件下,确定用水量也就是确定混凝土中的水泥浆用量。而后者取决于混凝土的工作性要求(以坍落度表征)和组成材料性质(集料表面性质和最大粒径、细级料的粗度和含量等)。每一立方米混凝土的用水量W(kg/m3)可按下述经验关系确定:
碎石混凝土:W=104.97+3.09hs+11.27(C/W )+0.61Sr (7-4)
W=86.89+3.70hs+11.24(C/W )+1.00Sr (7-5)
式中:Sr——砂率(%),参考表7-11选用;
hs——坍落度(cm),一般取1~3cm。
4、计算水泥用量
C=W(C/W) (kg/m3) (7-6)
路面混凝土的水泥用量应不小于300 kg/m3。一般情况下,采用425号水泥时,水泥用量约为310~340 kg/m3;采用525号水泥时,水泥用量约为300~320 kg/m3。
5、计算集料用量
(kg/m3) (7-7)
粗集料用量 (7-8)
式中:——水的密度(kg/m3)(可取为1);
——水泥密度(kg/m3)(可取为2.9~3.1);
——细集料的饱和面干密度(kg/m3);
——粗集料的饱和面干密度(kg/m3)。
6、外加剂用量
通过试拌与试验确定。
7、配合比的调节
通过上述计算得到的配合比,是根据以往经验公式和参数确定的材料初步用量,它同材料的实际情况存在一定的差异。为此,必须通过试验进行配合比调整。
1)试拌调整 按上述初步定出的配合比,取样试拌,测定其工作性(坍落度或维勃稠度试验)。如果测得的工作性低于设计要求,则可保持水灰比不变,适当增加水泥浆用量;如果测得的工作性超过设计要求,则可以减少水泥浆用量,或者保持砂率不变,增加砂石用量。当砂浆过多时,可酌量增加石子;砂浆少时,则可酌情增加砂浆。每次调整加入少量材料,重复试验(时间不得超过20min),知道符合要求为止。
2)强度试验 按符合工作要求的配合比,适当增减水泥用量,配置3组配合比的新拌混凝土梁式试件,并测定其实际密度。经养生到规定龄期后测定其强度。如果实测强度未能达到要求的配制强度时,可采用提高水泥标号、减小水灰比或改善集料级配等措施。
3)实验室配合比计算 通过调整得到符合工作性和强度要求的配合比后,还应按混凝土的实测密度校正其计算密度。混凝土的计算]密度为经试拌调整后每立方米混凝土各种材料单位用量之和(也即,)。校正系数k为实测密度同计算密度之比值。各种材料用量均乘以校正系数k,即为定出的实验室的配合比。
4)施工配合比换算试验室配合比是在集料处于标准含水状态(饱和面干状态)下计算出来的。施工现场的集料含水量经常变化,因而需根据拌制时集料的实际含水量对试验室的配合比进行调整。级料中的水分应在用水量中扣除,因水分所减少的集料数量则在集料用量中补足,由此得到施工配合比。
除经验公式以外,国内也提出了正交试验法。正交试验法是用一种规格化表格来安排试验,这种表格为正交表。在正交表中,任两列的各水平搭配次数都一样,成为正交性,保证了试验点在因子空间中的均衡分散性,具有很强的代表性。另外,每列因素在各水平上出现的次数都一样,可最大限度地排除各种干扰,保证有效地因子比较,称为整齐可比性。这是正交设计效率高的原因。因此,对于规模较大的水泥混凝土路面工程采用正交试验法,以较少的试验次数优选出满足要求的水灰比、用水量和砂用量。这种方法既缩短了试验时间,又减少了试验工作量。
第二节 轨道式摊铺机施工
一、施工准备工作
施工前的准备工作包括材料准备及质量检验,混合料配合比检验与调整,基层的检验与整修等项工作。
(一)材料准备及其性能检验
根据施工进度计划,在施工前分批备好所需要的各种材料(包括水泥、砂、石料及必要的外加剂),并在实际使用时核对整理。对已选备的砂和石料抽样检测含泥量、级配、有害物含量、坚固性;对碎石还应抽检其强度、软弱及针片状颗粒含量和磨耗等。如含泥量超过允许值,应提前一二天冲洗或过筛至符合规定为止,若其他项目不符合规定时,应另选料或采取有效的补救措施。
已备水泥除应查验其出厂质量报告单外,还应逐批抽验其细度、凝结时间、安全性及3、7和28d的抗压强度等是否符合要求。为节省时间,可采用2h压蒸快速测定方法。受潮结块的水泥禁止使用,另外,新出厂的水泥至少要存放一周后才可使用。外加剂按其性能指标检验,并需通过试验判定是否适用。
(二)混合料配合比检验与调整
混凝土施工前必须检验其设计配合比是否合适.否则,应及时调整。
1、工作性的检验与调整 按设计配合比取样试拌,测定其工作度,比要时还应通过试铺检验。检验与调整的方法如前所述。
2、强度的检验 按工作性符合要求的配合比,成型混凝土抗弯拉及抗压试件,养生28d后测定强度,或压蒸4h快速测定强度后推算到28d强度。强度较低时,可采用提高水泥标号、降低水灰比或改善集料级配等措施。
除进行上述检验外,还可以选择不同用水量、不同水灰比、不同砂率或不同集料级配等配制混合料,通过比较,从中选出经济合理的方案。施工现场砂和石子的含水量经常变化,必须逐班测定,并调整其实际用量。
(三)基层检验与整修
1、 基层质量检验
基层强度应以基层顶面的当量回弹模量值或以黄河标准汽车测定的计算回弹弯沉值作为检查指标。基层质量检查项目与标准为:当量回弹模量值或计算回弹弯沉值,现场每50m实测2点,不得小于设计要求;压实度以每100m2测一点,以不得小于规定要求;厚度每50m测1点,允许误差10%;平整度每50m测一处,用三米直尺量,最大不超过10mm;宽度每50m测一处,不得小于设计规定;纵坡高程要求用水准仪测量,每20m测1点,允许误差
10%mm;横坡亦要求用水准仪测量,当路面宽度为9~15m时检测5点、大于15m时检测7点,允许误差应
。
基层完成后,应加强养护,控制行车,不使出现车槽。如有损坏应在浇筑混凝土板前
采用相同材料修补压实,严禁用松散粒料填补。对加宽部分,新旧部分的强度应一致。
2、 测量放样
测量放样是水泥混凝土路面施工的一项重要工作。首先应根据设计图纸放出路中心线
及路边线,在路中心线上一般每20m设一中心桩,同时应设膨胀缩缝、曲线起迄点和纵坡转折点等中心桩,并相应在路边各设一对边桩。放样时,基层的宽度应比混凝土板每测宽出25~35cm。膨胀土路基上的基层,其宽度应横贯整个路基。主要中心桩应分别固定在路旁稳固位置。测设临时水准点于路线两旁固定建筑物上或另设临时水准桩,每隔100m左右设置一个,不易过长,以便于施工时就近对路面进行标高复核。根据放好的中心线及边线,在现场核对施工图纸的混凝土分块线。要求分块线距井盖及其他公用事业检验井盖的边线至少1m的距离,否则应移动分块线的位置。放样时为了保证曲线地段中线内外侧车道混凝土块有较合理的划分,必须保持横向分块线与路中心线垂直。对测量放样必须经常进行复核,包括在浇捣混凝土过程中,要做到勤测、勤核、勤纠偏。
二、机械选型和配套
轨道式推摊机施工,是机械化施工中最普通的一种方法。轨道式推铺机施工方法各工序可选用的机械烈于表7-12。
各施工工序可以采用不同类型的机械,而不同类型的机械具有不同的工艺要求和生产率。因此,整个机械化施工要求考虑机械的选型和配套。
(一) 主导机械选型
决定水泥混凝土路面质量和使用性能的施工工序,主要是混凝土的摊铺成型和拌和。因此,通常把混凝土摊铺成型机械作为第一主导机械,把混凝土拌和机械作为第二主导机械。在机械选型时,应首先选定主导机械,然后根据主导机械的技术性能和生产率,选配配套机械。
主导机械的选择,应考虑满足施工质量和进度的要求,同时还要考虑我国现阶段工程
单位的技术人员素质、管理水平和购买能力等实际情况。配套机械的选型和配套数量,须保证主导机械发挥其最大效率,且使用配套机械的类型和数量尽可能少.用机械铺筑的路面质量(密实度和平整度)以及操作进度取决于水泥混凝土的拌制质量.工作度主要与混凝土配合比有关,也与拌和方式有关.在选择拌和机型时,主要考虑:拌和品质和拌和能力、机械可靠度、工作效率和经济性。
(二) 配合机械及配套机械
1、 配合机械
配合机械主要是指运输混凝土的车辆。选择的主要依据是混凝土的运量和运输距离。研究表明:运距在1km以内,以2t以下的小型自卸车比较经济;运距在5km左右时,以5~8t中型自卸车最为经济。考虑到混凝土在运输过程中水份的散失和离析等问题,更远的运输距离以采用容量为6m3以上的混凝土拌和运输车较为理想。
2、配套机械
1) 前方系统(最大辅助宽度4.5m)
(1)以机型为主导机械的配套机械
纵向修光机 1台 插入式振捣器 2台
养生剂喷洒器 2台 纹理制动机 1台
调速调厚切缝机 2台 灌缝机 2台
养生用洒水库 1辆 移动电站 1台
(2)以C-450X机型为主导机械的配套机械
刮板式匀料机 1台 养生剂喷洒器 2台
纹理制动机 1台 调速调厚切缝机 2台
灌缝机 2台 养护用洒水库 1辆
移动电站(20kw) 1台
2) 后方系统
(1)一般双卧轴强制拌合机配套机械
装载机(ZL30、ZL40) 2台 翻斗车(1t) 6~8台
集料箱 1~2套 地磅 1~2台
供水泵 1台 计量水泵(外加剂用)1台
移动电站 1台
(2)配有自动控制配料系统的混凝土拌和楼(站)配套机具
装载机 1~2台 散装水泥泵车 2辆
供水泵(3.5KW) 1台 计量水泵(外加剂用) 1台
移动电站(120KW) 1台
(三)机械合理配套
合理配套主要指拌和机与摊铺机、运输车辆之间的配套情况。当摊铺机选定后,可根据机械的有关参数和施工中的具体情况计算出摊铺机械的生产率(参见第二章)。拌和机械与之配套就是在保证摊铺机械生产率充分发挥的前提下,使拌和机械的生产率得到正常发挥,并在施工中保持均衡、协调一致。
当摊铺机和拌和机得生产率确定后,车辆在整个系统内的配套实质上是车辆与拌和机的配套。车辆的配套问题可以应用排队论,找出合理的配套方案。考虑到装载点与车辆的配套是一个动态系统,即随着摊铺作业的推进,车辆的运输路程随时间的增加而增加。在运输与装载过程中,随机影响因素又较多,如道路状况、操作水平、设备运行状况等都在不断变化,因此对排队论中单通道模型进行改进,增加时间变化等因素便于在配套方案中适时优化控制,通过输入不同的采集数据得到不同的结果,然后进行分析比较,找出合理的优化方案。
三、拌和与运输
(一)混凝土拌和
在拌和机的技术性能满足混凝土拌和要求的条件下,混凝土各组成材料的技术指标和配比计量的准确性是混凝土拌制质量的关键。在机械化施工中,混凝土拌和的供料系统应尽量采用配有电子秤等自动计量设备,有困难时,最低限度也要采用集料箱加地磅的计量方法,而体积计量法难于达到计量准确的要求,应停止使用。采用自动计量设备,在施工前,应按混凝土配合比要求,对水泥、水和各种集料的用量准确调试后,输入到自动计量的控制存储器中,经试拌检验无误,在正式拌和生产。一般国产强制式拌和机,拌制坍落度为1~5cm的混凝土,其最佳拌和时间的控制:立轴强制拌和机为90~180s,双卧轴强制拌和机为60~90s。最短拌和时间不低于底限,最长拌和时间不超过最短拌和时间的三倍。拌和中,如需加入外加及时,应对外加剂单独计量。混凝土各组材料的计量精度不应超过:水和水泥1%;粗细骨料
3%;外加剂
2%。
(二)运输
为保证混凝土的工作性,在运输中,应考虑蒸发失水和水化失水(指水泥在拌和之后,开始水化反应,其流动度下降),以及因运输的颠簸和振动使混凝土发生离析等。要减少这些因素的影响程度,其关键是缩短运输时间,并采取适当措施防止水分损失(如用帷布或其他适当方法将其表面覆盖)和离析。
机械化施工时,可以采用自卸汽车或搅拌车运输混凝土。一般情况下,坦落度大于5.0cm时用搅拌车运输。从开始搅拌到浇筑的时间,用自卸汽车运输时必须不超1h,用搅拌车时不得超过1.5h,若运输时间超过限值,或者在夏天铺筑路面时,以使用缓凝剂。
(三)卸料
卸料机械有侧向和纵向两种,侧向卸料机在路面铺筑范围外操作,自卸汽车不进入路面铺筑范围,需有可供卸料机和汽车行驶的通道。纵向卸料机在铺筑范围内操作,由自卸汽车后退供料,在基层上不能预先安设传力杆及其支架。
四、混凝土的摊铺与振捣
(一)轨道模板安装
轨道试摊铺机施工的整套机械,在轨道上移动推进,也以轨道为基准控制路面表面的高程。由于轨道和模板同步安装,统一调整定位,将轨道固定在模板上,既做水泥混凝土路面的侧模板也是每节轨道的固定基座(图7-1)。
轨道高程控制是否精确,轨道是否平直,接头是否平顺,将直接影响路面表面的质量和行驶性能,轨道模板本身的精度标准和安装的精度要求分别见表7-13和7-14。模板要能承受从轨道传下来的机组重量,横向要保证模板的刚度。轨道数量根据进度配备,并要有拆模周期内的周转数量。施工时日平均气温在20℃以上时,按日进度配置;日平均气温低于19℃时,按日铺筑进度2倍配置。设置纵缝时,应按要求间距,在模板上预先作拉杆置放孔。对各种钢筋的安装位置偏差不得超过1cm;传力杆必须与板面平行并垂直接缝,其偏差不得超过5mm;传力杆间距偏差不超过1cm。
(二)摊铺
摊铺是将倾卸在基层上或摊铺机箱内的混凝土按摊铺厚度均匀地充满模板范围之内。摊铺机械可以选用刮板式、箱式和螺旋式。
1、 刮板式摊铺机
摊铺机本身能在模板上自由地前后移动,在前面的导管上左右移动。并且由于刮板本
身也旋转,所以可以将卸在基层上的混凝土堆,向任意方向摊铺。这种摊铺机比其他类型摊铺机的重量轻,容易操作,易于掌握,故使用较普遍,使其摊铺能力较小。德国弗格勒()J型、美国格马可(GOMACO)和我国南京建筑机械厂仿制的C-450X等摊铺机都采用这种形式。
2、箱式摊铺机
混凝土通过卸料机(纵向或横向)卸在钢制的箱子内。箱子在机械前进行驶时横向移动,同时箱子的下端按松铺厚度刮平混凝土。
混凝土混合料一次全部放在箱内,重量大,但摊铺均匀而准确。其摊铺能力大,故障较少。
3、螺旋式摊铺机
由可以正反方向旋转的螺旋杆(直径约50cm)将混凝土摊开。螺旋后面有刮板,可以准确调整高度。这种摊铺机的摊铺能力大,其松铺系数一般在1.15~1.30之间。它于混凝土的配合比、集料粒径和坍落度等因素有关。但施工阶段主要取决于坍落度。大致的参考数值见表7-15。合适的松铺系数按各工程的配合比情况由试验确定。
(三)振捣
混凝土振捣,可采用振捣机或内部振动式振捣机进行。
混凝土振道机是跟在摊铺机后面,对混凝土进行再一次整平和导实的机械。振捣机的一般构造如图7-2所示(德国公司采用)。在振捣梁前方设置一道与铺筑宽度同宽的复平刮梁。其作用一方面是补充摊铺机初平的缺陷,更重要的是使松铺混凝土在全宽度范围内达到正确高度,它与振捣密度和路面平整度直接相关。其后是一道全宽的弧面振捣梁,以表面平板式振动把振动力传至全厚度。振动频率在50Hz~100Hz之间,属于低频振捣。按混凝土工艺学的振动机理,低频是以集料接触传递振动能量。振捣梁的弹性支承使施振时同时具有弹压力。布料的均匀和松铺厚度掌握是关键。复平梁前沿堆有确保充满模板的少量余料,余料堆积高度不应超过15cm,过多会加大复平梁推进阻力。弹性振捣梁通过后混凝土已全部振实,其后部混凝土应控制有2~5mm回弹高度,提出的砂浆,使整平工序能正常进行。靠近模板处的混凝土,用插入式振捣器补充振捣。
内部振动式振捣机主要用并排安装的振捣棒插入混凝土中,由内部进行振实。振捣器一般安装在有轮子的架子上,可在轨道上自行或用其他机械牵引。振捣棒有斜插入式和垂直插入式两种。
五、表面修整
振实后混凝土还应进行整平、精光、纹理制作等工序。
采用机械修整时的表面修整机有斜向移动和纵向移动两种。斜向表面修整机通过一对与机械行走轴线成10~13°的整平梁作相对运动来完成修整,其中一根整平梁为振动整平梁。纵向表面修整机为整平梁在混凝土表面沿纵向往返移动,由于机体前进而将混凝土板表面整平。机械修整的速度需考虑混凝土的易修整性和机械的特性。轨道或模板的顶面应经常清扫,以便机械能顺畅通过。
整平操作时,应使整平机械前的拥料涌向路面横颇高的一侧。采用机整平时,要注意随时清除因修光梁往复运行推到路面边沿的粗集料,确保整平效果和机械正常行驶。在施工中途有停歇时,整平梁停驻处混凝土表面常有微小的棱条出现,可辅以人工抹面。
精光工序是对混凝土表面进行最后的精细修整,使混凝土表面更加致密、平整、美观,这是混凝土路面外观质量的关键工序。国产C-450X机由于整机采用三点式整平原理和较为完善的修光配套机械,整平质量较高。由于机国内未引进、开发纵向修光机组,所以精光工作由人工辅助完成。施工中应加强质量检查、校核,保证精光质量。
纹理制作是提高水泥混凝土路面行车安全性的重要措施之一。施工时用纹理制作机,对混凝土路面进行拉槽或压槽,使混凝土表面在不影响平整度的前提下,具有一定的粗糙度。纹理制作的平均深度控制在1~2mm以内,制作时应控制纹理的走向与路前进方向垂直,相邻板的纹理要相互衔接,横相邻板的纹理要沟通以利排水。适宜的纹理制作时间以混凝土表面无波纹水迹比较合适,过早和过晚都会影响纹理制作质量。近年来,国外还采用一种更有效的方法,即在完全凝固的面层上用切槽机切出深5~6mm、宽3mm、间距20mm的横向防滑槽。
六、养生
混凝土表面修整完毕后,应进行养生,使混凝土拌在开放交通前具有足够的强度。在养生初期,为减少水分蒸发,避免阳光照射,防止风吹和雨淋等,可以用活动的三角形罩棚将混凝土板全部遮盖起来。
混凝土板表面的沁水消失后,可在其表面喷洒薄膜养生剂进行养生,养生剂应在纵横方向各洒一次以上,洒布要均匀,用量要足够。也可采取洒水湿养,用湿草帘或麻袋等覆盖在混凝土板表面,每天洒水喷湿至少2~3次。
养生时间按混凝土炕弯拉强度达到3.5Mpa以上的要求由试验确定。通常,适用普通硅酸盐水泥时约为14d,使用早强水泥时约为7d,使用中热硅酸盐水泥约为21d。
模板在浇筑混凝土60h以后拆除。但当交通车辆不直接在混凝土板上行驶,气温不低于10℃时,可缩短到20h后拆除;温度低于10℃时,可缩短到36h后拆除。拆模板时不应损坏混凝土板和模板。
七、接缝施工
1、纵缝
纵缝的构造一般采用如图7-3a所示的平缝加拉杆型。若采取全幅施工时,则用如图7-3b所示的假缝加拉杆型。
平缝施工应根据设计要求的间距,预先在模板制作拉杆置放孔,并在缝壁一侧涂刷隔离剂,拉杆应采用螺纹钢筋,顶面的缝槽以切缝机切成,深度为3~4cm,并用填料填满。顶面不切缝时,施工时应及时清除已打好面板上的粘浆或用塑料纸遮盖,保持纵缝的顺直和美观。
假缝施工应预先将拉杆采用门型式固定在基层上,或用拉杆置放机在施工时置入。假缝顶面的缝槽应采用切缝机切成,深为6~7cm,使混凝土在收缩时能从此缝向下规则开裂,防止因切缝深度不足引起不规则裂缝。
2、 横向缩缝
混凝土结硬后,应适时切缝。切得过早,因混凝土的强度不足,会引起集料从砂浆中
脱落,而不能切出整齐的缝。切的过迟,混凝土板会在非预定位置出现早期裂缝。合适的切缝时间控制在混凝土获得足够的强度,而收缩应力并未超出其强度范围时。它随混凝土的组成和性质(集料类型、水泥类型和含量、水灰比等)、施工时的气候条件(温度及其变化、风等)等因素而变化。研究表明,适宜的切缝时间是施工温度与施工后时间的乘积为200~300个温度小时或混凝土的抗压强度为8.0-10.0Mpa时比较合适。切缝方法以调深调速的切缝机锯切效果较好。为减少早期裂缝,切缝可采用“跳仓法”,即每隔几块板切一缝,然后再逐块锯。切缝深度为板厚1/3~1/4,切缝太浅会引起不规则断板。
3、胀缝
胀缝分浇筑混凝土终了时设置和施工中间设置两种。
施工终了时设置胀缝,可采用图7-4a所示的形式。传力杆长度的一半传过端部挡板,固定于外侧定位模板中。混凝土浇筑前应先检查传力杆位置。浇筑时,应先摊铺下层混凝土。浇筑邻板时应拆除顶头木模,并设置下部胀缝板、木制嵌条和传力杆套管。
施工过程设置胀缝,则可采用图7-4b所示的形式。胀缝施工应预先设置好胀缝板和传力杆支架,并预溜好滑动空间,为保证胀缝施工的平整度以及机械化施工的连续性,胀缝板以上的混凝土硬化后用切缝机按胀缝板的宽度切二条线,待填缝时,将胀缝板以上的混凝土凿去,这种方法,对保证胀缝施工质量特别有效。
4、施工缝
施工缝为施工间断时设置的横缝,常设于胀缝或所缝处,多车道施工缝应避免设在同一横断面上。施工缝如设于缩缝处,板中应增设传力杆,其一半锚固与混凝土中,另一半应先涂沥青,允许滑动。传力杆必须与缝壁垂直。
5、接缝填封
混凝土板养生期满后应及时填封接缝。填缝前缝内必须清扫干净并保持干燥。填缝料应与混凝土缝壁粘结紧密。目前用的强制式灌缝机和灌缝枪,能把改性聚氯乙烯胶泥和橡胶沥青等加热施工式填缝料和常温施工时填缝料灌入缝宽不小于3mm的缝内,也能把分子链较长、稠度较大的聚氨脂焦油灌入7mm宽的缝内。
八、特殊季节施工中应注意的问题
水泥混凝土路面施工质量受环境因素影响较大,对高、低温季节及雨季施工应考虑其特殊性,确保工程质量。
(一) 高温季节施工
施工现场(拌和和铺筑场地)的气温℃时,即属于高温施工。高温会促进水化作
用,增加水分的蒸发量,容易使混凝土板表面出现裂缝。因而,在高温季节施工应尽可能降低混凝土的浇筑温度,缩短从开始浇筑到表面修筑完毕的操作时间,并保证混凝土进行充分的养生,施工单位应提出高温施工的工艺设计,包括降温措施、保持混凝土工作性和基本性质的措施等。
当整个施工环境气温大于35℃,且没有专门的工艺措施时,不应进行水泥混凝土路面
施工。无论什么情况和条件,混凝土拌和物的温度不能超过35℃。在高温季节施工时,应定期专门测定混凝土拌和物的温度。
在我国的地理纬度和气候条件下,绝大部分地区夏天是可以铺筑水泥混凝土路面的,但应根据工程的条件采取降温和其他措施。如材料方面可采取降低砂石料和水的温度或掺加缓凝剂等措施。铺筑方面,可通过洒水降低模板与基层温度、缩短运输时间以及摊铺后尽快覆盖表面等。
(二)低温季节施工
水泥混凝土路面施工操作和养生的环境温度等于或小于5℃,或昼夜最低气温有可能低到—2℃时,应视为低温施工。
低温操作和养生时,混凝土会因水化速度降低而使强度增长缓慢,同时也会因结冰而遭受冻害。因此,在低温季节施工时,施工单位必须提出低温施工的工艺设计,包括低温操作和养生的各项措施。
1、 提高混凝土拌和温度
气温在0℃以下时,水及集料必须加温。一般规定水加热温度不能超过60℃。砂石料
应采用间接加热法,如保暖储仓、热空气加热、在矿料堆内埋设蒸气管等。不允许用炒烧等方法直接加热,也不允许直接用蒸气喷洒砂石料,砂石料加热不能超过40℃。不允许对水泥加热。根据对原材料的加热程度,可以计算出水泥混凝土拌和物的温度,其公式如下:
(7-9)
式中:——表面干燥保水状态的集料质量(kg)及温度(℃);
——水泥质量(kg)及温度(℃)
——集料所含水的质量(kg)及温度(℃)
——搅拌用水的质量(kg)及温度(℃)。
2、路面保温措施
混凝土铺筑后,通常采用蓄热法保温养生。即选用合适的保温材料覆盖路面,使已知热材料拌成的混凝土的热量和水泥水化的水花热量蓄保起来,以减少路面热量的失散,使之在适宜温度下硬化而达到要求的强度。这种方法只需对原材料加热而路面混凝土本身不加热,施工简便,易于控制,附加费用低,是简单而经济的冬季施工养护手段。
保温层的设计应就地取材,在能满足保温要求的同时要注意经济性。常用麦秸、谷草、油毡纸、锯末、石灰等作保温材料,覆盖于路面混凝土上。保温层至少10cm厚,具体视气温而定。
3、其他应注意的问题
设计混凝土配合比时,注意不宜用过大的水灰比,一般不宜超过0.6。应延长搅拌时间,较常温施工增加50%左右。出料温度不能低于10℃。混凝土摊铺时,不宜把工作面铺大、拉长,应集中力量全幅尽快推进,加速完成摊铺工艺。建立定期测定温度制度。在拌和站应测检砂石料、水和水泥入拌前温度、混凝土拌和物出料时温度,每台班不少于4次。测定混凝土摊铺时温度,即测定经运输工具运达工地卸料后的混凝土温度很摊铺振实后的温度,每台班不少于6次。测定混凝土养生阶段温度。浇筑完后头两天每隔6h测1次,其后每昼夜至少3次,其中1次应在凌晨四点测定。测温孔位置应设在路面板边缘,深度10~15cm,温度计在测孔内应留3min以上。路面纵向每50cm设一对测孔。全部测孔应按路面桩号编号,绘制测孔布置图,并绘出每一测孔的温度时间曲线。
铺筑后的路面混凝土,要求在72h内养生温度应保持在10℃以上,接下来7d养生温度保持在5℃以上。
(三)雨季施工
雨季来临之前,应掌握年、月、旬的降雨趋势的中期预报,尤其是近期预报的降雨时间和雨量,以便安排施工。拟定雨季施工方案和建立雨季施工组织,了解和掌握施工路段的汇水面积和历年水情,调查施工区段内,路线的桥涵和人工排水构造物系统是否畅通,防止雨水和洪水影响铺筑场地和拌和场地。
在拌和场地,对拌和设备搭雨棚遮雨。砂石料厂因含水量变化较大,需要经常测定,以调整拌和时的加水量。雨季空气潮湿,水泥储放要防止漏雨和受潮。混凝土在运输途中应加以遮盖,严禁淋雨并要防止雨水流入运输车箱中。在铺筑现场,禁止在下雨时施工。如铺筑前现场有雨水,应及时排出基层积水。在混凝土达到终凝之前,覆盖塑料膜不允许雨水直接淋浇在已抹平的路面上。需在雨下操作时,现场应制备工作雨棚,雨棚应轻便易于移动,大小高矮应按操作方便设计。
九、提高表面功能的技术措施
水泥混凝土路面表面功能包括抗滑、耐磨、平整等方面的内容。
室内试验和试验路研究结果表明,提高抗滑能力的技术途径主要有:确保粗、细集料的抗磨光和抗磨耗性能;采用不同的表面处理工艺形成粗糙耐久的表面构造,常用的拉槽、压槽、裸槽、嵌屑等处理都是可行的。
提高耐磨性的主要措施是:采用抗压强度较高的混凝土;采用优质材料,如耐磨耗的水泥和砂、石料,严格控制砂、石含砂量。
提高表面平整度,在设计方面的主要措施有,减少各种构造缝,采取优质填缝料;施工方面的主要措施有,严格控制模板安装质量,防止模板变形;混凝土拌和及摊铺要均匀;混凝土振捣适当,提浆均匀,加强抹平并随时用样板校验;表面拉漕和压纹时采用平直的导梁;减少工作缝,缩缝尽量不用压缝。
第三节 滑模式摊铺机施工
滑模式摊铺机的特点是不需轨模,整个摊铺机的机架支撑在四个液压缸上,它可以通过控制机械上下移动,以调整摊铺机铺层厚度。在摊铺机的两侧设置有随机移动的固定滑模板,因此不需另设规模。这种摊铺机一次通过就可以完成摊铺、捣振、整平等多道工序。
一、施工工艺
滑模式摊铺机的摊铺过程如图7-5所示。首先由螺旋摊铺器1把堆积在基层上的水泥混凝土向右横向铺开,刮平器2进行初步刮平,然后振捣器3进行捣实,刮平器4进行振捣后整平,形成密度而平整的表面,在利用搓动式振捣板5对混凝土层进行振实和整平,最后用光面带6光面。
滑模式摊铺机的整面工作与轨道式基本相同,只是工作时各工作装备均由电子液压操纵机构来控制。
第四节 质量控制与验收
工程质量应以设计文件要求为标准。为了保证混凝土路面的施工质量,要求在施工过程中对每一道工序进行严格的检查和控制。对已完成的路面要求进行外观检查,并量测其几何尺寸,根据设计文件要求进行核对。此外还要查阅施工记录,其中包括原材料试验和试件强度资料、配合比、隐蔽构造(各种钢筋的位置等)等,作为工程质量鉴定的依据。
(一)原材料质量检验
混凝土用的水泥、砂、碎(砾)石、水、外加剂、填缝材料和钢筋等原材料按规定进行检查和试验(参见原材料要求),并做好记录。对水泥胶砂抗弯拉和抗压强度可采用2h压蒸法快速测定。根据压蒸2h测得的抗弯拉和抗压强度,分别按下式推算出28d的相应强度(MPa):
(7-10)
(7-11)
式中:——分别为水泥胶砂试件标准养生28d的抗弯拉和抗压强度;
——相应为水泥胶砂试件压蒸2h的抗弯拉和抗压强度。
(二)工作性测试
摊落度试验是1918年美国D.Abrams提出的,目前世界各国普遍采用。坍落度是新拌混凝土自重引起的变形,它只对富水泥浆的新拌混凝土比较敏感(适合于流动性混凝土)。对于相同性质的新拌混凝土,不同试样的坍落度可能相差很大;相反,不同组成的新拌混凝土,它们工作性质有很大差别,但却可能得到相同的坍落度。因此坍落度不是满意的工作性指标。
维勃稠度试验是瑞典V.Bahrner于1940年首先提出的。凡坍落度小于10mm的新拌混凝土,可采用维勃稠度仪测定其工作性(适合于稠硬性混凝土)。近年来世界各国均采用国际标准协会建议的《混凝土拌和物——稠度测定方法(维勃试验)》(ISO-4110)。维勃稠度仪是由美国T.C.Powers建议的重塑仪发展而来的。实验方法是将坍落度筒放在直径为240mm、高度为200mm的圆筒中,垂直提起坍落度筒,在新拌混凝土顶上置一透明圆盘。开动振动台并记录时间,从开始振动至透明圆盘被水泥浆布满的瞬间止,所经历的时间,以s计(精确至1s),即为新拌混凝土的维勃稠度值。
捣实因素试验由英国Glanbille等人于1964年提出,该法是对新拌混凝土作标准数量的功后测定密实度改变的程度。这一试验特性是对低工作性的新拌混凝土反应较为敏感,
(三)混凝土强度检测
1、一般规定
混凝土的强度检验应以28d龄期的抗弯拉强度为标准。一般采用梁式试件测定抗弯拉强度,也可用圆柱劈裂强度测定结果由经验公式推算小梁抗弯拉强度。当同时采用钻芯劈裂试验的推算强度和小梁抗弯拉强度时,应同时符合规定的强度要求。混凝土抗弯拉强度检验,应付和下列规定:
1)应使用正在摊铺的混凝土拌和物制作试件,时间的养生条件与现场混凝土板养生相同。
2)每天或每铺筑200m3混凝土,应同时制作二组试件,龄期应分别为7d和28d;每铺筑1000至2000m3混凝土应增作一组试件,用于检查后期强度,期龄不应小于90d。
3)当水泥混凝土的7d强度普遍达不到28d强度的60%(矿渣水泥混凝土为50%)时,应检查分析原因,并对混凝土的配合比作适当修正。
4)浇筑完成的混凝土板,应检查实际强度,可在现场钻取圆柱试件,进行圆柱劈裂强度试验,以圆柱劈裂强度推算小梁抗弯拉强度。
2、强度快速测定方法
1)压蒸法
抗弯拉强度是水泥混凝土路面最重要的指标。但用28d强度试验来控制混凝土的质量是很难满足现代施工要求的。近年来,提出了水泥混凝土压蒸4h的强度快速测定技术。根据压蒸4h测得的抗弯拉强度()和抗压强度(
)可根据下式推算得标准养生28d的抗弯拉强度(
)和抗压强度(
):
=2.918+1.728
(7-12)
=14.591+1.826
(7-13)
式中强度的单位为Mpa。
2)现场快速检测方法
现场快速测定法常见有超声回弹法和射钉法
超声-回弹法是用超声仪测定在混凝土中的超声声速和利用回弹仪测定混凝土的回弹值,根据下列回归公式,求得混凝土的强度:
(7-14)
(7-15)
式中:f、R——分别为混凝土试件的抗弯拉与抗压强度(MPa);
V——超声声速(km/s);
N——回弹值。
射钉法是由国产紧固技术的射钉枪、把钉射入混凝土中,根据射钉外露长度L(mm)来估算混凝土强度。
(四)表面功能测定方法
1、抗滑法与舒适法
参照国外有关标准同时兼顾我国目前施工工艺水平和实际交通状况,采用表面构造深度来衡量其抗滑性,抗滑标准的建议值如表7-17。
表7-17中为竣工验收值,环境不良路段,对高度、一级公路指立交、平交、变速车道等处;对其他公路指急弯、陡坡交叉路口或集镇附近;对年降雨量在500mm以下的地区,表列数值可适当降低。混凝土路面的平整度以3m直尺量测为准。其与路面之间的间隙,高速、一级公路3mm;其他各级公路
5mm。当用平整度仪量测时,高等级公路
2.5mm。
2、耐磨性
为检测混凝土的耐磨性,国内有关单位已研究了MS-250混凝土钻孔磨耗机和HM-A型混凝土磨耗机。用磨耗机圆盘旋转1600转后,混凝土表面环形轨道上均匀6点的平均磨耗深度作为磨耗指标。
二、外观检查与竣工验收标准
外观检查包括混凝土是否有蜂窝、麻面、裂缝、脱皮、石子外露和缺边掉角等现象,以及是否残留有麻袋、草帘等印痕。路面应平整不积水,纵横接缝应顺直不变,填缝料应饱满整齐,不得污染路面。
混凝土面层质量验收的允许误差应符合表7-18的规定。填缝料和接缝板的施工质量,应不低于表7-19、7-20的规定。
第五节 碾压混凝土(RRC)与沥青混凝土(AC)复合式路面修筑技术
把有垫层、基层、碾压水泥混凝土板及板上沥青混凝土层所组成的路面称为碾压水泥混凝土与沥青混凝土(RRC+AC)复合式路面。
一、RCC+AC复合式路面概述
随着水泥混凝土路面施工工艺的不断发展,80年代中后期兴起的碾压混凝土路面(RCCP),目前在我国开始推广。RCCP平整度差,且表面难以形成粗糙面,在高速行驶时抗滑性能下降快,平整、抗滑、耐磨三方面的不足,使其难以在高等级公路上以展风采。
三、RCC+AC施工技术
(一) RCC材料要求及配合比设计
RCC在材料组成和强度形成机理方面接近于普通混凝土,而作为路面结构材料成型时又与沥青混凝土和水泥稳定粒料类似,所以在混合料配合比设计时有其自身的特点。
1、材料组成
由于施工工艺不同,RCC对集料的级配要求、水泥和水的用量等与普通混凝土均有所
不同。从组成结构看,碾压混凝土为骨架密实结构,需要有一定数量粒径连续的粗集料(>5mm),以形成骨架空间网络;又必须有相当数量的细集料()填充空隙,使其达到较高密实度。
1) 集料
RCC所用粗集料为强度不低于Ⅲ级的机扎碎石,并采用连续级配。集料最大粒径40mm
和20mm的级配范围建议值如表7-21和7-22。
试验表明,从强度、工作度及施工工艺要求看,RCC集料最大粒径20mm比40mm更为合适。
砂率的大小对RCC的品质影响很大,集料最大粒径不等,所选用的水灰比及所需的砂率也不同。适宜的选择范围见表7-23。
另外,RCC集料压碎值、含泥量、扁平针状颗粒含量对RCC技术性能的影响比普通混凝土大,因此,必须严格控制。
2) 水泥
水泥的技术条件与普通混凝土相同。但其凝结硬化要慢、吸水性小、抗裂性要好。对
集配良好的碎石,水泥用量通常为8%~13%(以混凝土密度计),对级配差且含软质骨料多(约5%)的材料,可取高限。
在RCC+AC结构中,RCC作为下层,因此在保证RCC强度要求的前提下,可掺入适量粉煤灰(以细度、含量和烧失量为控制指标),如20%(等量取代)或40%(超量取代)。
3) 砂
RCC结构密实,胶凝作用强,为减少水泥用量,应尽量减少砂浆中的灰浆损失。因此,
选用中砂和粗砂为宜。
4) 外加剂
由于RCC早期强度发展较快,初凝和终凝时间较短,加之和易性较差,因此,为延长碾压时间已达到要求的密实度,可加入缓凝减水剂,如木质素磺酸钙0.25%~0.3%(以水泥加粉煤灰的干重量计)。
2、室内试件成型方法及工作度控制
室内试件成型采用平面振动加压成型,即在常用试板上加一均匀分布的荷载(压重块),通过机械振动台进行振密成型。该法与测定混凝料工作度的改进维勃仪工作原理基本一致。压重的重量通过测定RCC密实度(即压实率)确定,压时率用振实混凝土的平均密度除以理论最大密度表示。试验表明,一般应达到96%以上,才能满足路用性能的要求。
室内工作度的测定是采用改进后的维勃仪进行的,即在圆盘上加一压重块并予以固定,测定指标为改良VC值(简称)。VC值表示在规定的重量、振频、振幅条件下,混合料振动出浆所需的时间,以S计。压块单位面积重量为28.3g/cm2, VC值对全碾式取7010s;对复合式取45
15s。
3、RCC配合比设计
配合比设计应遵循密实填充和混合料离析系数最小的原则,其设计步骤为:
1)计算试配强度
(7-16)
式中:——保证率系数,根据路面等级、结构类型和结构保证率确定,RCC+AC复合式路面结构中,建议
=1.645,即保证率为95%;
s——标准差,如本单位有足够的统计资料,按经验选用,否则,可参考表7-24选用;
——RCC设计抗弯拉强度(MPa)。
2)计算灰水比
(7-17)
式中:为水泥胶砂标准试件抗弯拉强度(MPa),应采用实际试验值。如无法取得时,可采用水泥标号的标准弯拉强度乘以水泥标号富余系数确定。富余系数值应按各地实际统计资料选用。如无统计资料时,可取1.13。
3)计算用水量
(7-18)
式中:——初估用水量(kg/m3);
——砂率(%),参考表7-23选用;
——改良维勃值(S),其值按现行试验规定测定。测定时,需在维勃仪圆盘上增加荷重9kg。
当RCC的各种材料确定后,需对用水量按下式修正;
(7-19)
式中:W——用水量(kg/m3);
C——水泥用量
——水泥标准稠度用水量
F——粉煤灰用量
——与小于0.15mm粉料通过量有关的经验用水量,从表7-25查取。若加入粉煤灰,此项不考虑。
4)水泥及砂石用量的计算表达式与(7-6~7-8)相同。
5)测定混合料工作度(Vc值)。如不符合要求,则需适当调整,重新进行试验。同时制备相应的梁式试件,测定28d弯拉强度,直至达到要求为止。
(二)RCC施工工艺
RCC的拌和易采用双卧轴强制拌和机,装载和运输过程中,需采取措施防止混合料的离析。模板应具有斜向支撑的型钢,以承受振动压路机作业时产生的侧向力,并保证自身不变性。
施工时应做到连续供料、匀速摊铺、专人检查、及时调整厚度等。人工摊铺时,压实系数约为1.35~1.37;机械摊铺时,压实系数约为1.46。压路机的选型和组合(钢轮和胶轮)以及碾压过程中振频、振幅的选择至关重要。振动压路机仪选用自重6~10t、低频29~32Hz、高频42~50 Hz、振幅0.3~0.7mm、静线压力大于20kg/cm、动线压力大于60kg/cm。碾压程序一般为静压-低频-高频-静压。当采用全厚式路面时,最后一次静压必须采用轮胎压路机,以消除轮迹。每道工序一般碾压1~2遍,视表面平整、出浆和压实度而定。面板厚度超过22cm时,可分层施工。
RCC路面施工中的接茬处,可根据实际情况采用“导木法”、“斜坡法”等工艺。
RCC路面的养生不应少于7d,并严禁车辆通行。切缝可在碾压完成后24~48h进行。缩缝间距可较普通混凝土路面适当延长,一般为10~15m。
(三)沥青(AC)层按现行沥青路面施工技术规范的有关规定施工。
AC层材料要求与组成设计可参考沥青混凝土路面。为了加强层间结合,RCC板与沥青面层之间应喷洒粘层油。粘层油可采用AH-100沥青,其用量视RCC表面粗糙程度而定,一般为0.3~0.6kg/m3。喷洒粘层油后须均匀撒少量矿粉(约为沥青用量的30%~40%)。沥青面层厚度以3~5cm为宜。
(四)防止反射裂缝的技术措施
RCC+AC复合式路面结构中,当温度下降时,RCC板产生水平位移,从而引起沥青层开裂。另外,当汽车轮载通过接缝时,相邻板的挠度差引起沥青层剪切变形,以至使面层出现裂缝。为了解决反射裂缝问题,可采用的措施有:提高基层强度与刚度或横缝设转力杆以减小相邻板挠度差;提高沥青混凝料的强度;从结构设计上着手解决,如在RCC与沥青层之间设置沥青橡胶层、沥青砂层、沥青混合料联结层(过渡层)、土木织物、钢丝网、油毡等,有些国家则采用锯口封缝的方法。
1、铺设沥青-橡胶层(应力吸收层)
沥青橡胶应力吸引层(SAMI)起着一种软介层的作用,它能把接缝位移引起应力完全消散在夹缝内。其施工方法为:把一种橡胶沥青加热到180℃时,以(1.22~1.63)kg/m2的用量洒铺,再趁热撒布预拌好的等粒径粗砂14kg/m2,竣工厚度为9~13mm。这种橡胶沥青具有下列特性:在117℃时,绝对粘度为1000~8000Pa.s;在60℃时绝对粘度为7000~60000Pa.s;软化点54~71℃;劲度模量。
厂拌的SAMI在137℃~149℃时铺筑,可以使铺筑厚度均匀。注意混合料不要与刮板粘结,用轮胎压路机粘压,配合比最大取沥青:骨料=10:90。
2、设置过渡层
过渡层是设置在沥青混凝土与RCC板之间的一种碎石混合料层。碎石的级配采用76~10、64~2.5及50~0.15mm三种。随着板的位移增大,采用碎石较大粒径的颗粒。选用针入度60-80的沥青1.5%~3%,空隙率为25%~35%。混合料搅拌时间最长为30s,拌和温度为93~121℃,并在65~80℃温度下,用40~100kN串列轮压路机碾压2~3次,施工后一昼夜铺设整平层,随即开放交通。
3、土木织物法
织物对沥青混凝土起着加强的作用,而且也是一种防水层。所用粘层沥青必须能填充织物孔隙。当接缝较宽,又没有填缝,便不会有足够的沥青渗入纤维织物,织物也就起不到防水的作用。当然,土木织物的物理力学性质,如抗腐蚀、耐热、抗拉强度、顶破与撕裂强度与变形特性等也要满足路用性能的要求。施工时,清扫水泥混凝土路面,洒乳化沥青,铺土工布,并立即铺筑沥青混凝土。施工时,土工布粘在混凝土板上,变成了上层沥青层的粘结层,但应防止泛油。
4、锯口封闭法
目前的各种技术均不能根本解决反射裂缝问题。在沥青层上锯缝并封闭,即可防止水或不良异物进入,还可为释放沥青层内的应力提供一个平面。这种处理方法可以减少反射裂缝处的剥落。
德国沿水泥混凝土路面板的伸缩缝位置,切断铺设的沥青混凝土面层,填如填缝料,取得了良好的效果。日本对4cm厚度的沥青混凝土层采用了同样的方法,但未填缝,取得了防止产生不规则反射裂缝的效果。最新出版的《RCCP技术纲要(草案)》中规定,RCC作为基层时,应设置横缝,沥青混凝土层设缝应和RCC板缝位置相一致。
锯缝可以干锯或湿锯,锯口必须弄干,清除干净以使填缝料粘结得好。美国某些州,在封缝前已将粘连间断带置于接缝底部。
美国用一种热橡胶沥青填缝料,作为新封缝的材料。填缝料应填满整个接缝以使冷却后填缝料的水平面低于路表面1.6-3.2mm。封缝应干净,不要有稀散的填缝料溢出。
锯缝的时间应当在任何低于冰点的温度出现前将AC层锯开,要尽早或至少在开放交通前封缝。
综上所述,RCC路面在我国的研究取得了一些成果,但要作为干等级公路路面,还有许多技术问题,如拉杆、传力杆的设置、表面功能等,以及对RCC板厚设计计算,目前国内外尚未解决。对RCC+AC复合式路面结构仍处在研究阶段,需从理论与实践两方面对这一新型结构的合理厚度,作为下层的RCC表面合理平整度、材料配合比、施工技术、质量控制及设计方法进行深入研究,以指导设计与施工。