广东工业大学华立学院
课 程 设 计(论文)
课程名称 机 械 设 计 基 础
题目名称 遥控器外壳注射模具
学生学部(系)机 电 工 程
专业班级 XXXXXXXXXXX
学 号 XXXXXXXXXXXX
学生姓名 XX
指导教师 XXX
年 月 日
目录
序言……………………………………………………………………………………3
一、模具工业的概况…………………………………………………………………3
二、我国模具工业技术概况及其主要发展方向……………………………………3
三、塑件的工艺分析…………………………………………………………………4
1.零件图………………………………………………………………………4
2.ABS材料分析………………………………………………………………5
3.塑料成型工艺性能分析……………………………………………………5
4.塑件的工艺性分析…………………………………………………………6
a. 塑件的表面质量分析…………………………………………………6
b. 塑件的结构工艺性能分析……………………………………………6
四、模具设计…………………………………………………………………………6
1. 模具加工精度的确定………………………………………………………6
2. 浇注系统设计………………………………………………………………6
a.浇注系统的设计原则…………………………………………………6
b.主流道的设计…………………………………………………………7
c.分流道的设计…………………………………………………………8
d.浇口形成………………………………………………………………8
3. 模具结构分析………………………………………………………………9
a. 标准模架的选择………………………………………………………9
b. 开模行程的校核………………………………………………………9
c. 模具闭合高度校核……………………………………………………9
d. 模板尺寸的校核………………………………………………………9
e. 喷嘴尺寸校核…………………………………………………………9
4. 成型零部件设计……………………………………………………………9
a. 型腔分型面设计………………………………………………………10
b. 排气槽的设计…………………………………………………………11
c. 成型零件设计计算……………………………………………………11
5. 脱模机构设计和脱模力的计算……………………………………………12
6. 复位机构与导向机构设计…………………………………………………12
7. 塑模温控系统设计…………………………………………………………13
五、注射机的选择…………………………………………………………………14
1. 注射量确定…………………………………………………………………14
2. 锁模力确定…………………………………………………………………14
3. 成型压力……………………………………………………………………15
六、总结………………………………………………………………………………16
参考文献……………………………………………………………………………16
序 言
本设计主要是对遥控器外壳注射模各方面设计,是根据本人所学知识和经查找各方资料所全力完成好的,它对本套塑料注射模进行了多方面的分析,包括塑件材料和结构工艺性分析、塑件成型工艺方案的拟订,以及相关的设计计算等等。本设计主要分为三部分:
一、模具工业的概况
在讨论注塑模设计之前,先要对国内外的塑料模具工业的状况、塑料模具工业的发展方向有一个较清晰的了解,这也就使我们对本课题的意义有所了解。首先要对模具有一个整体的认识。模具是机械、汽车、电子、通讯、家电等工业产品的基础工艺装备之一。作为工业基础,模具的质量、精度、寿命对其他工业的发展起着十分重要的作用,在国际上被称为“工业之母”,对国民经济发展起着不容质疑的作用。
模具工业是制造业中的一项基础产业,是技术成果转化的基础,同时本身又是高新技术产业的重要领域,在欧美等工业发达国家被称为“点铁成金”的“磁力工业” ;美国工业界认为“模具工业是美国工业的基石”;德国则认为是所有工业中的“关键工业” ;日本模具协会也认为“模具是促进社会繁荣富裕的动力” ,同时也是“整个工业发展的秘密”,是“进入富裕社会的原动力” 。在模具工业的总产值中,冲压模具约占50%,塑料模具约占33%,压铸模具约占6%,其它各类模具约占11%。
塑料模具工业是随塑料工业的发展而发展的。塑料工业是一门新兴工业。自塑料问世后的几十年以来,由于其原料丰富、制作方便和成本低廉,塑料工业发展很快,它在某些方面己取代了多种有色金属、黑色金属、水泥、橡胶、皮革、陶瓷、木材和玻璃等,成为各个工业部门不可缺少的材料。
目前在国民经济的各个部门中都广泛地使用着各式各样的塑料制品。特别是在办公设备、照相机、汽车、仪器仪表、机械制造、交通、电信、轻工、建筑业产品、日用品以及家用电器行业中的电视机、收录机、洗衣机、电冰箱和手表的壳体等零件,都已经向塑料化方向发展。目前,世界的塑料产量已超过有色金属产量的总和。
塑料模具就是利用特定形状去成型具有一定形状和尺寸的塑料制品的工艺基础装备。用塑料模具生产的主要优点是制造简便、材料利用高、生产率高、产品的尺寸规格一致,特别是对大批量生产的机电产品,更能获得价廉物美的经济效果。塑料模具的现代设计与制造和现代塑料工业的发展有极密切的关系。随着塑料工业的飞速发展,塑料模具工业也随之迅速发展。
二、我国模具工业技术概况及其主要发展方向
在中国,人们已经越来越认识到模具在制造中的重要基础地位,已成为衡量一个国家制造业水平高低的重要标志,并在很大程度上决定着产品质量、效益和新产品的开发能力。我国塑料模工业从起步到现在,历经半个多世纪,有了很大发展,模具水平有了较大提高。
我国模具工业起步晚,底子薄,与工业发达国家相比有很大的差距,但在国家产业政策和与之配套的一系列国家经济政策的支持和引导下,我国模具工业发展迅速。目前我国模具年生产总量虽然已位居世界第三,但设计制造水平在总体上要比工业发达国家落后许多。
纵观发达国家对模具工业的认识与重视,我们感受到制造理念陈旧则是我国模具工业发展滞后的直接原因。模具技术水平的高低,决定着产品的质量、效益和新产品开发能力,它已成为衡量一个国家制造业水平高低的重要标志。因此,模具是国家重点鼓励与支持发展的技术和产品,现代模具是多学科知识集聚的高新技术产业的一部分,是国民经济的装备产业,其技术、资金与劳动相对密集。提高模具标准化水平和模具标准件的使用率。模具标准件是模具基础,其大量应用可缩短模具设计制造周期,同时也显著提高模具的制造精度和使用性能,大大地提高模具质量。
在科技发展中,人是第一因素,因此我们要特别注重对知识的更新与学习,实现产、学、研相结合,培养更多的模具人才,搞好技术创新,提高模具设计制造水平。在教学中积极采用多媒体与虚拟现实技术,逐步走向网络化、智能化环境,实现模具企业的敏捷制造、动态联盟与系统集成。我国模具工业是一个完全信息化的、充满着朝气和希望而又实实在在的新时代即将到来。
在信息社会和经济全球化不断发展的进程中,模具行业发展趋势主要是模具产品向着更大型、更精密、更复杂及更经济快速方面发展,技术含量不断提高,模具生产向着信息化、数字化、无图化、精细化、自动化方面发展;模具企业向着技术集成化、设备精良化、产品品牌化、管理信息化、经营国际化方向发展。
三、塑件的工艺分析
1.零件图
图1零件图
2.ABS材料分析
ABS材料是丙烯腈—丁二烯—苯乙烯共聚物。这三种组分各自的特性,使ABS具有良好综合力学性能。丙烯晴使ABS有良好的耐化学腐蚀及表面 硬 度,丁二烯使ABS坚韧,苯乙烯使它有良好的加工性和染色性。
ABS属于热塑性塑料,外观为粒状或粉状,呈微黄色,不透明但成型的塑件具有较好的光泽。ABS无毒,无味。密度1.02~1.05g/cm3成型温度范围(180℃--240℃),成型时有较好的流动性。ABS材料具有较高的抗冲击强度,且在低温下也不迅速下降(抗寒性);有良好的的机械强度和一定的耐磨性,耐油性,化学稳定性和电气性能。ABS有一定的硬度和尺寸稳定性,易于成型加工,且易着色。ABS几乎不受酸、碱、盐、及水和无机化盐的影响,溶于
酮、醛、酯、氯代烃中,不溶于大部份醇类及烃类溶剂,但与烃长期接触会软化溶胀。ABS塑料表面不可接触受冰醋酸,植物油等化学药品,否则会引起应力开裂。此外,ABS的缺点是耐热性不高,低介电强度,低拉伸率,热变形温度为93℃,脆化温度为-27℃,使用的温度范围为-40℃~100℃,而且ABS的耐气候性也差,紫外线作用下容易氧化降解,从而会导致制件变硬发脆。
3.塑料成型工艺性能分析
塑料成型工艺特性是塑料在成型加工过程中所表现出来的特有性质,下面,对注塑材料ABS工艺特性进行分析:
a.收缩性 塑料从温度较高的模具中取出冷却到室温后,其尺寸或体积会发生收缩变化,这种性质称为收缩性。收缩性的的大小以单位长度塑件收缩量的百分数来表示,称为收缩率。一般对于大型模具的收缩率计算,我们采用实际收缩率进行计算:SS=a-b/b×100% (SS:实际收缩率;a:模具或塑件在成型温度时的尺寸;b:塑件在室温时的尺寸;c:模具在室温时的尺寸) 对我所设计的零件属于小型的模具,所以采用SJ=c-b/b×%(Sj:为计算收缩率) 由于本次毕业设条件的原因,没有办法自己去测量出:c b 值。于是我们通过查找资料《塑料成型工艺与模具设计》附录B 常用塑料的收缩率,可得:ABS塑料成型收缩率为:0.003-0.008,由于塑件的结构,模具的结构,成型工艺条件等都会影响塑料的收缩率变化。我们取一个相对平均值:0.005。
b.流动性 塑料在一定的温度、压力作用充填模具开腔的能力,称为塑料的流动性。塑料的流动性差,就不容易充满开腔,易产生缺料或熔接痕等缺陷。但流动性太好,又会在成型时主生严重的飞边。ABS材料属于热塑性塑料,分子成线型,具有良好的流动性。其次:料温,压力,模具结构都会影响塑料的流动及充模能力。
c.吸湿性 吸湿性是指塑料对水分的亲疏程度。按吸湿或粘附水分能力的大小分类,ABS塑料属于吸湿性塑料,吸水率为:0.05%-0.5%。在注塑成型过程中比较容易发生水降解,成型后塑件上出现气泡,银丝与斑纹等缺陷。因此,在成型前必须进行干燥处理。一般干燥温度取80-90℃,干燥时间为两小时。
d.热敏感性 塑料的化学性质对热量的敏感程度称为热敏性。热敏性塑料在成型过程中很容易在不太高的温度下发生热分解、热降解,从而影响到塑件的性能,色泽和表面质量等,另处,塑料熔体发生热分解或热降解时,会释放出一些挥发性气体,这些气体一般具有腐蚀性,或有毒,不管是对人,还是模具都会造成一定的影响。ABS塑料成型温度为210℃-250℃,经查中国人力资源专家网提供的材料编经验值得,到达260℃变色,于料温达到280℃时,塑料出现分解。于是注塑成型是,一般取210℃-250℃。
综上所述:ABS收缩比较大,成型收缩后,对型芯具有比较大的包裹力,为方便塑件顺利脱模,应将脱模斜度设计为较大值:型腔40′~1°40′型芯30′~1°ABS溶融时具有良好的流动性;较低的热敏性;属于吸湿性塑料。于是在成型是需要控制好,成型温度,压力,注射前的干燥处理等。
4.塑件的工艺性分析
a.塑件的表面质量分析
该塑件要求外行美观,外表面要求非常光滑,没有斑点及熔接痕现象,内表面相对光滑点,内、外表面粗糙度分别可取Ra0.4μm、Ra0.2μm。塑件制品内、外表面成型后方不可见边缘有缺陷,边缘面要求平整。
b.塑件的结构工艺性能分析
1.塑件的形状较为复杂,中间有个很小深度的沉积面,在最外面使用了小圆弧过渡,四条棱也分别使用了圆弧过渡,后面进行了抽孔,另外在上表面打了很多有规率一样大小的圆孔。
2.塑件整体结构较为小,平均壁厚为1.0mm,超过ABS塑料的最小成型壁厚。可注塑成型。
四、模具设计
1.模具加工精度的确定
本次设计的遥控器是日常用品,其外壳要能承受磨损。对于制件的外观要求合表面精度等级要求比较高。现初定制品精度等级为4级。
经分析,现确认模具的制造加工精度为IT7级,而型芯和型腔的加工精度均为IT6,型腔采用机械粗加工后电火花精加工,其它采用机械加工。
2. 浇注系统设计
浇注系统是指模具中从注射机喷嘴开始到型腔为止的塑料流动通道。浇注系统设计好坏对制品性能、外观和成型难易程度影响颇大。
a.浇注系统的设计原则:
1) 结合型腔的布置考虑,尽可能采用平衡式分流道布置。
2) 尽量缩短熔体的流程,以便降低压力损失,缩短充模时间。
3) 浇口尺寸位置和数量的选择十分关键,应有利于熔体的流动、避免产生湍流、涡流、喷射和蛇形流动,并有利于排气。
4) 避免高压熔体对模具型芯和嵌件产生冲击,防止变形和位移的产生。
5) 浇注系统凝料脱出应方便可靠,凝料应易于和制品分离或易于切除和修整。
6) 熔接痕部位与浇口尺寸、数量及位置有直接关系,设计浇注系统时要预先考虑到熔接痕的部位、形态以及以制品质量的影响。
7) 尽量减小因开设浇注系统而造成的塑料用量。
8) 浇注系统的模具工作表面应达到所需的硬度、精度和表面粗糙度,其中浇注口应有IT7以上的精度要求。
9) 设计浇注系统时应考虑储存冷料的措施。
10) 尽可能使主流道中心与模板中心重合。若无法重合也应使两者的距离尽量缩小。
主流道衬套选择标准件:
图2 上壳主流道套
b.流道的设计:
为了使凝料顺利拔出,主流道的小端直径D应大于注射机的喷嘴直径d,通常为:
D=d+(0.3—1)mm
D=4+0.5=4.5mm
主流道入口的凹坑球面半径R2也应该大于注射机喷嘴球面头半径R1,通常为:
R2=R1+(1—2)mm
R2=16+2=18mm
主流道半锥角通常为2°~6°,过大会产生湍流或涡流产生空气,过小使凝料脱模困难,还会使充模时熔体的流动阻力过大。
主流道内壁表面粗糙度应在Ra0.8um以下,抛光时沿轴而进行。主流道的长度L一般按模板厚度确定。为了减少熔体充模时的压力损失,应尽可能缩短主流道的长度,L一般控制在60mm以内。
c.分流道的设计:
分流道是指主流道与浇口之间的通道。其作用是使熔融塑料过渡和转向。由于圆截面加工困难。本次设计上壳采用半圆形断面分流道。根据以上原则和零件的实际情况,决定选用双点浇口形式,这种浇口适用于成型壳、盒、罩和容器等制品,是应用广泛的浇口形式。它的优点为:由于浇口小,熔体通过点浇口时流速增大,前后压差大,提高了充模的速度,从而可获得外表清晰,有光泽的制品;熔体流过点浇口时由于摩擦阻力使部分能量转变为热量,使熔体温度略升高,粘度下降,改善了流动性,这对薄壁制品是有利的;其缺点:浇口尺寸小,充模阻力大,对熔体粘度较高的塑料会产生充填不满的缺陷;为了取出点浇口式浇注系统凝料,要增加一个分型面,模具具有两个分型面的三板式结构,结构比较复杂。
d.浇口的形成
选择浇口形式应该遵循以下原则:
1) 尽可能采用平衡式设置;
2) 型腔排列进料均衡;
3) 型腔布置和浇口开设部位力求对称,防止模具承受偏载而产生溢料现象;
4) 确保耗料量小;
5) 不影响塑件外观。
根据以上原则和零件的实际情况,为了使从主流道来的熔融塑料能均衡地以最短的流程到达各浇口并同时充满各型腔,本设计上壳采用非平衡式的分流道布置形式,下壳决定选用针点浇口进胶,这种浇口适用于成型壳、盒、罩和容器等制品,是应用广泛的手机成型的浇口形式。它的优点为:由于浇口小,熔体通过点浇口时流速增大,前后压差大,提高了充模的速度,从而可获得外表清晰,有光泽的制品;熔体流过点浇口时由于摩擦阻力使部分能量转变为热量,使熔体温度略升高,粘度下降,改善了流动性,这对薄壁制品是有利的;其缺点:浇口尺寸小,充模阻力大,对熔体粘度较高的塑料会产生充填不满的缺陷;为了取出点浇口式浇注系统凝料,要增加一个分型面,模具具有两个分型面的三板式结构,结构比较复杂。
图3上壳主流道,分流道,及浇口的设计
3. 模具结构分析
a.标准模架的选择
上壳选用的模架尺寸:
表1上壳模架尺寸
单位: mm

b.开模行程的校核
开模行程=H1+H2+5~10
其中:H1――脱模距离(顶出距离);
H2――制作高度包括浇注系统在内。
XS-ZY-125注射机的模板行程300mm,合格。
c.模具闭合高度校核
根据注射机的参数,Hmax≤450mm Hmin≥200mm
而根据所选标准模架组合尺寸所得,对于遥控器上壳而言:
H=35+80+80+60+15=270mm <H<
因此,满足要求。
d.模板尺寸的校核
所选注射机的模板尺寸为428mm*458mm,而本次两个注射模采用的是300mm*250mm。
e.喷嘴尺寸校核
本模具主流道始端的球面半径为R16,略大于XS-ZY-125注射机的喷嘴球半径R12。故符合标准。
4.成型零部件设计
成型零件是与塑料接触的决定制品几何开关的模具零件。它包括凹模、凸模、型芯、成型镶块及壁厚等,是塑料模具的主要组成部分。
a.型腔分型面设计
合理选择分型面,有利于制品的质量提高,工艺操作和模具的制造。因此,在模具设计过程中是一个不容忽视的问题,选择分型面一般根据以下的原则:
(1) 分型面应该选择在制品最大截面处,这是首要原则。
(2) 尽可能使制品留在动模的一侧。
(3) 尽可能满足制品的使用要求。
(4) 尽可能减小制品在合模方向上的投影面积,以减小所需的锁模力。
(5) 不应影响制品尺寸的精度和外观。
(6) 尽量简单,避免采用复杂形状,使模具制造容易。
(7) 不妨碍制品脱模和抽芯。
(8) 有利于浇注系统的合理设置。
(9) 尽可能与料流的末端重合,有利于排气
由于上壳采用侧浇口,因此遥控器上壳以内表面及其延伸界面为分型面。下壳采用针点式浇口,因此以遥控器外表面投影面积最大处为分型面。
图4(a)遥控器上壳分型面设计
图4(b)遥控器型芯下模分型面分析设计
b.排气槽的设计
排气槽的作用是将型腔和型芯中周围空间内的气体及熔料所产生的气体排到模具之外。该注射模属于小型模具,在推杆的间隙和分型面上都有排气效果,无需另外开排气槽。
c.成型零件设计计算
该塑模的成型零件表面的工作尺寸用平均收缩率方法计算。
(1)型腔的径向尺寸计算
型腔的径向尺寸:DM = [ DS + DS·SCP - 3/4△]+δZ
其中:DS — 塑件名义尺寸,型芯和型腔各自对应。
SCP — 塑件的平均收缩率
△—塑件允许的公差值
δZ—模具制造公差,本设计是按塑件公差的 1/3— 1/6来取的。
(2) 型腔的高度尺寸计算
型腔深度尺寸:HM = [ HS + HS·SCP – 2/3△ ] +δZ
其中:HS — 塑件高度名义尺寸
SCP、△ 和δZ均与上述意义相同。
(3)成型孔之间中心距尺寸计算
LM = [LS + LS·SCP]±1/2δZ
其中:LM — 模具中心孔或型芯中心距尺寸
LS — 塑件中心距名义尺寸
此外,凸台高度、起伏凸边高度、起伏凸边位置、非配合圆弧等,一切距离位置尺寸都属于双向公差的计算。(注:ABS的收缩率为0.3%~0.8%。)
5.脱模机构设计和脱模力的计算
由于该塑件的脱模阻力不大,而推杆又加工简单、更换方便、脱模效果好,因此采用圆形推杆脱模机构。推杆的设置位置采取以下原则:
(1)推杆设在脱模阻力大的地方。
(2)推杆位置均匀分布。
(3)推杆设在塑料制品强度刚度较大的地方。
(4)推杆直径应满足相应的强度、刚度条件。
脱模力计算
当开始脱模时,模具所受的阻力最大,推杆刚度及强度应按此时计算,亦即无视脱模斜度(a=0)
由于制品是薄壁矩形件
Q=8t·E·S·l·f/(1-m)(1+f) (kN)
式中Q—脱模最大阻力(kN)
t—塑件的平均壁厚(cm)
E—塑料的弹性模量E—塑料的弹性模量(N/cm2)
S—塑料毛坯成型收缩率(mm/mm)
l—包容凸模长度(cm)
f—塑料与钢之间的摩擦系数
m—泊松比,一般取0.38~0.49
取 S=0.005,E=1.8×10N/cm
已知,t=0.1cm,l=10cm, f=0.28
Q=8×0.1×1.8×10×0.005×10×0.28/(1-0.43)(1+0.28)=3.31kN
6. 复位机构与导向机构设计
在顶杆的脱模机构中,顶出塑件后再次合模时(或闭模前),必须要求顶杆等元件回复或预先回复到原来的位置。通常采用弹簧推动板复位,但当推顶装置发生卡滞现象时,仅靠弹簧难以保证,须复位杆与弹簧并用。设计中具有活动型芯的脱模机构时,必须考虑到合模时互相干扰的情况,应在塑模闭合前使顶杆提前复位,以免活动型芯撞击顶杆,应设置先复位装置。复位杆由标准可查得。
本设计中的模具使用弹簧先复位装置,在顶杆固定板上装有弹簧,借弹簧力合复位杆作用,在合模时,使顶出杆先复位,这种方法的特点是结构简单,容易制造,但弹簧容易失效,故要经常更换弹簧。
导向机构的主要作用是为保证在模具闭合后,动、定模板相对位置准确;在模具装配过程中也起到了定位的作用,合模时,引导动、定模板准确闭合,能够承受一定的铡向压力,以保证模具的正常工作。
本设计中导向机构采用导柱导向,导柱采用带头导柱,其结构简单,加工方便,在导柱的末端以导向套给以配合,导柱倒装。结构形式如下图所示:
一般导柱应有以下几个重要的技术要求:
1. 导柱的长度应根据具体的情况而定,一般比凸模端面高出8~12mm。
2. 导柱的前端做成半球形状,以使导柱顺利进入导孔。
3. 数量为6,均匀分布在模具周围侧壁厚度、底板厚度的计算。
注射模的工作状态时长时间的承受交变负荷,同时也伴有冷热的交替。现代的注射模使用寿命至少几十万次,因此模具必须有足够的强度和刚度。
7. 塑模温控系统设计
在注射过程中,模具的温度直接影响着制品质量和注射周期,各种塑料的性能不同,成型工艺要求的不同相应的模具对温度要求也不同, ABS在注射成型时所需的模具对温度为40—60度之间。对任何塑料制品,模温波动较大都是不利的。过高的模温会使制品在脱模后发生变形,延长冷却时间,使生产率下降。过低的模温会使降低塑料的流动性,难于充满型腔,增加制品的内应力和明显的溶接痕等缺陷。由于模温不断地被注入熔融塑料加热,模温升高,单靠模具自身散热不能使其保持较低的温度,因此必须加冷却机构。
冷却装置系统的设计要点:
(1) 实验表明冷却水孔的数量愈多,对制品的冷却也愈均匀。
(2) 水孔与型腔表面各处最好有相同的距离,即孔的排列与型腔形状相吻合,水孔边距型腔的距离常用12—15mm。
(3) 对热量聚积大温度上升高的部位应加强冷却。
(4) 进水管直径的选择应使水流速度不超过冷却水道的水流速度,避免产生过大的压力降。冷却水道直径选用6mm。
(5) 凸凹模与成型型芯应分别冷却,并保证其冷却平衡。
(6) 冷却水道不应穿过没有镶块或其接缝部位,水道连接必须密封以免漏水。
(7) 复式冷却循环并联而不应串联。
(8) 进、出口冷却水温差不应过大,以免造成模具表面冷却不均。
由于塑件材料为ABS,其注射成型模具并无加热要求。故只用冷却水道在动、定模板之中各取一个达到冷却效果即可。
五、注射机的选择
1.注射量确定
遥控器塑体总体计算
a.运用PRO/E中的分析命令,可得出体积。
b.运用PRO/E中的分析命令,可以分析出整个手机上壳在分型面上的投影面积。
该塑件的注射容积较小,在此采用一模一腔,即
=80%
2.锁模力确定
由式
式中 F-注射机的额定锁模力
n-型腔数,n=2;
k-安全系数,取k=1.2;
-融料在型腔中平均压力,ABS为30mpa;
A-塑件投影面积;
图五 开模方式以及整体建模
3.成型压力
ABS的成型压力为=30mpa,
取70-150,
>
根据节根据V、S及塑件的尺寸选择卧式注射机,其型号为XS-Z-500,主要参数如下:
表2 XS-ZY-125注射机参数
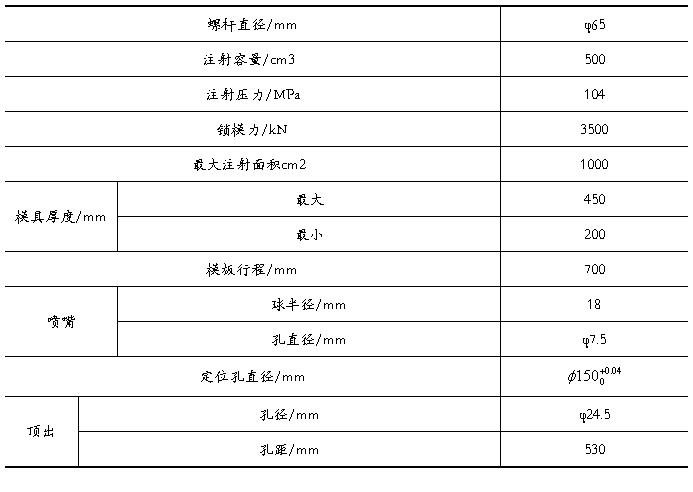
六、总结
模具设计是一门综合性很强的技术,设计的好坏,关系到制造好模具质量的成功与否,所以要搞好一套模具必须要尽心尽力的完成好它。经过一个学期的学习,我学到了很多知识,未完成本次设计打下了坚实基础,不过还有好多不尽人意的地方还需要学习和改善。
本遥控器外壳注射模具设计采用了反浇口浇注系统,保证了遥控器外壳的光洁度。它通过上模型芯和下模型芯成型,成型后留在下模型芯,再通过顶料杆顶出,从而完成好本零件的制作。分型面的选择是模具制造更加简便,同时也保证了外观的美观。本设计是一模一腔设计,相对较简单,适合于中小批量生产在模具结构比较复杂容易磨损的地方,利用高性能的模具材料采用镶嵌式的结构,提高模具寿命的同时,降低模具加工难度。设计当中,运用了PRO/E,塑料顾问专家等模具辅助设计软件对塑件进行三维造型、交口位置的选择、注模分析、接痕缩痕分析、气泡分析、冷却系统设计的分析。提前解决了许多生产方面出现的问题,提高了模具一次试模成功率。
参考文献
1. 林清安.《PRO/Engineer Wildfire 模具设计》. 清华大学出版社.2004
2. 朱光力 万金宝.《塑料模具设计》.清华大学出版社.2003
3. 魏万壁 丁闻.《实用注塑成型设计手册》.化学工业出版社.2000
4. 张孝明.《塑料模具设计》.机械工业出版社.1998
5. 成大先.《机械设计手册》第三版.化学工业出版社.2002