1.1 摩擦磨损实验机的原理及使用说明
1.1.1 实验机机械部分的原理
图3-64为HIT-1型球盘式摩擦磨损实验机原理图。电动机2经带传动1驱动托盘3回转,下试件4安装在托盘3上并随托盘3一起回转,上试件5装在夹头6中。载荷P由砝码7的重量W产生,摆杆8在摩擦力F作用下摆动,摆杆的另一端压在压力传感器9上,压在压力传感器上的力Q可经数据采集测量系统获得。工作时,托盘3中可加入润滑油或在下试件4表面上滴润滑油(边界润滑),也可不加润滑油(干摩擦)。
图3-64 HIT-1型球盘式摩擦磨损实验机原理图
试验机主要技术指标:
转速:100~500r/m
最大载荷:W=10N
1.1.2 摩擦系数测试原理
如图3-64所示,本实验机作用在试件上的载荷P由砝码重量W产生,P与W的关系为:
P=W (N) (3-4)
图3-65 试件结构及尺寸
作用在上试件5上的摩擦力F与作用在压力传感器9上的力Q的关系为:
QL1=FL2 (3-5)
本试验机 L1=L2=100mm
则:
Q=F (3-6)
摩擦系数:
(3-7)
所以,只要预先确定加载砝码W的重量再测出传感器受力Q的大小,即可计算出摩擦系数f。
1.1.3 数据采集处理系统
本试验机配有自动数据采集处理系统,图3-66为数据处理系统框图,系统的硬件有:传感器、数据采集卡、计算机等。
图3-66 数据处理系统框图
数据的结果有两种形式:
一是由计算机直接做出摩擦系数随时间的变化曲线。在屏幕上显示,并在打印机上打印出曲线。
二是计算机只记录实验数据,并通过计算机打印出数据,由学生手工绘图。
1.1.4 本试验机的应用范围
(1) 改变上下试件材料,研究不同材料配副的摩擦、磨损情况。
(2) 改变速度快慢,研究不同速度下的摩擦,磨损情况。
(3) 改变载荷大小,研究不同载荷下的摩擦、磨损情况。
(4) 改变试件的表面加工质量,研究表面质量不同时的摩擦、磨损情况。
(5) 改变润滑状态,研究不同润滑条件下的摩擦、磨损情况。
第二篇:摩擦与磨损原理
摩擦与磨损原理
(复习资料)
摩擦学定义:摩擦学是研究作相对运动的相互作用表面及其有关的理论和实践的一门科学技术。
摩擦学又是一门涉及多学科的边缘学科,其涉及的主要学科为物理学、化学、机械工程、断裂力学、材料力学、流体力学等等。摩擦学涉及领域广泛,主要的研究内容可以归纳为以下几个方面:1、摩擦;2、磨损;3、流体润滑理论;4、边界润滑;5、润滑剂与润滑技术;6、摩擦学测试技术。
摩擦学设计的任务就是利用摩擦学的现有知识,对一个特定对象通过合理的设计方法使其获得良好的摩擦学性能。
摩擦学设计过程中需要注意摩擦学的几个主要特性:(1)、摩擦学的系统性;(2)、摩擦学的时空性;(3)、摩擦学的多学科性。
固体表面的微观几何形状统称为表面形貌。真实表面形貌,它由表面形状误差、波纹度和表面粗糙度组成。
1、 表面形状误差:在制造机器零件的过程中,机床-工件-刀具系统的误差及弹性变形,导致表面形状误差,数值由最大偏差表示,一般用平面度、圆度和圆柱度等误差来表示。
2、 波纹度是制造机器零件过程中,机床—工件-刀具系统的振动和机床传动件的缺陷周期性重复在机器零件已加工表面上的结果。
3、 波纹度是制造机器零件过程中,机床—工件-刀具系统的振动和机床传动件的缺陷周期性重复在机器零件已加工表面上的结果。
表面形貌参数:微观不平度也称为微观不平度十点平均高度,是在取样长度L内,5个最大的轮廓峰高的平均值与5个最大的轮廓谷深的平均值之和称为Rz。
在取样长度内,被测轮廓线上各点到中线距离的绝对值总和的算术平均值,称为轮廓算术平均偏差Ra。
表面的物理吸附和化学吸附:物理吸附是非常快的可逆过程,吸附分子保持自己的特性,并可脱吸。化学吸附比物理吸附具有更大的活化能,吸附过程是不可逆的,化学吸附膜比物理吸附稳定。
金属表面层是由若干层次组成的表面层:外表面层有物理吸附和化学吸附作用生长的吸附层及因氧化形成的氧化膜层。塑性变形层称内层。
真实物体的表面不是理想光滑的表面,当两个表面相接触时,只是在表面的个别地方接触,这些离散的接触面积的总和构成实际接触面积。
名义接触面积:又称表面接触面积或几何接触面积,它是两接触物体的宏观界面的边界所确定的面积。真实接触面积:两接触物体通过各微凸体直接传递界面相互作用力,发生变形而产生的微接触面积之和,不到名义接触面积的0.01~0.1%。
赫兹接触理论:赫兹早在1881年就提出了著名的弹性接触理论,其假设条件为:认为材料是均匀的,各向同性的、完全弹性的;接触表面的摩擦力可忽略不计,表面是理想的光滑表面,在上述假设下,基本公式才能成立。
摩擦理论:当两个互相接触的固体,在外力作用下作相对的切向运动、或具有相对切向运动趋势时,在两固体接触表面之间就会产生一种运动阻力,这种阻力称为摩擦力。这种现象称为摩擦现象。
a,按摩擦副的运动状态分类:
(1)静摩擦:两个物体在作宏观运动前的微观滑移,其接触表面之间的摩擦称为静摩擦。(2)动摩擦:两个物体作相对运动时,其接触表面之间的摩擦称为动摩擦。一般情况下,动摩擦系数小于最大静摩擦系数。
b,按摩擦副的运动形式分类:
(1)滑动摩擦:两个相互接触的表面作相对滑动时摩擦,称为滑动摩擦。
(2)滚动摩擦:物体在力矩的作用下,沿接触表面滚动时的摩擦,称为滚动摩擦。例如各种车辆的车轮在地面的滚动等。
c,按摩擦副表面的润滑状况分类:
(1)干摩擦:常指名义上无润滑的摩擦。
(2)流体摩擦:被具有体积特性的流体层隔开的两固体相对运动的摩擦。摩擦发生在流体内部分子之间,摩擦力的大小与摩擦副表面状态无关,而只与流体内部的分子运动阻力有关,即与流体粘性有关。
(3)边界摩擦:两固体接触表面间被存在一层极薄的润滑膜隔开,其摩擦和磨损不取决于润滑剂的粘度,而是取决于两固体表面的特征和润滑剂的特性。
经典摩擦定律:
第一定律:滑动摩擦力的大小与接触面之间的法向载荷成正比。
第二定律:滑动摩擦力的大小与各义接触面积无关。
第三定律:滑动摩擦力的大小与滑动速度无关。
粘着摩擦理论:当两表面相接触时,在载荷作用下,主要在微凸体的顶端接触,接触点的单位压力很大,使其产生塑性变形,表面变形点将牢固的粘着,使两表面形成一体,即称为粘着或冷焊。当一表面相对另一表面滑动时,则剪断这些连接粘着点的力就是摩擦力。
一般来说,对于理想的弹-塑性材料,摩擦力主要就是剪断金属粘结点所需的剪切力。设粘结点部分的剪切强度为τb,则摩擦力为:
因而 (6-30)
式中Ar——实际接触面积; ——压缩屈服极限。
滚动摩擦可以分为三种基本形式:(1)自由滚动:滚动元件沿着平面无约束地作直线滚动,这是最简单的滚动形式,或称纯滚动。(2)受制滚动:滚动元件受制动或驱动力矩的作用,因而在接触区同时有法向压力和表面切向力的作用。(3)槽内滚动:两个相互滚动的表面,由于几何形状造成接触区内各点的切向速度不等因而伴随滑动的滚动。
滚动摩擦阻力的起因主要有以下几个方面:1、微观滑移;2、弹性滞后:滚动元件滚过滚道时,滚道要产生弹性变形,这需要消耗一定能量,当接触消除时,大部分变形能又得到释放。由于松驰效应,释放的能要比原先的变形能小,这个能量差即被认为是滚动摩擦的损耗;3、塑性变形;4、粘附效应。
磨损理论:磨损是伴随摩擦而产生的必然结果,它是相互接触的物体在相对运动时,表层材料不断发生损耗的过程。磨损过程大致可分为三个阶段:(1)、“跑合阶段”;(2)、“稳定”磨损阶段;(3)、“急剧”磨损阶段。
一般磨损的分类要考虑三方面的作用影响:
(1)表面的作用。如机械运动的形式、是滑动还是滚动、表面分子作用形式等。
(2)表层的变化。物理性能的变化,如硬度等;化学性能的变化,如化学膜的作用变化;表层的结构变化,是变形还是无变形等,以及组织成份的变化,如钢的表层含碳量等。
(3)破坏的形式。主要是磨屑形式和表面磨损形状。
1、粘着磨损: 当摩擦副接触时,由于表面不平,发生的是点接触。在相对滑动和一定载荷作用下,在接触点发生塑性变形或剪切,使其表面膜破裂,摩擦表面温度升高,严重时表层金属会软化或熔化,此时,接触点产生粘着。然后出现粘着——剪断——再粘着——再剪断的循环过程,这就形成粘着破坏(或粘着磨损)。
2、磨粒磨损: 对于粗糙硬表面把软的工作表面划伤,或者两接触面受外界硬粒划伤工作表面,都属于磨粒磨损。磨粒磨损主要是磨粒对金属表面进行切削的过程。
3、表面疲劳磨损: 表面疲劳磨损是指摩擦时表面有周期性的载荷作用,使接触区产生很大的变形和应力,并形成裂纹而破坏的现象。疲劳磨损最普遍形式是出现在滚动接触的表面上。
4、腐蚀磨损:腐蚀磨损是材料在摩擦时与周围介质发生化学或电化学相互作用的磨损,它是一种需要考虑环境介质影响的磨损过程。腐蚀磨损时材料的摩擦表面破坏是同时发生了两个过程,即腐蚀和机械磨损。
5、微动磨损:微动是发生于接触表面上极小振幅的运动。微动磨损是微动状态下材料接触表面的破坏过程。1992年,Zhou通过了大量试验证明每对摩擦副同时存在的材料的二类微动图:a, 运行工况微动图;b, 材料响应微动图。
影响磨损的因素:1、摩擦副材质的影响;2、环境介质的影响;3、外界机械作用的影响;4、温度的影响;5、接触表面状态的影响。
材料的耐磨性:材料的耐磨性是指在一定摩擦条件下某种材料抵抗磨损的能力。由于材料的磨损性能不是材料的固有特性,而是与磨损过程相关因素(如载荷、温度、速度等)、材料特性等因素有关的系统特性。
表面处理技术的主要目的是利用各种物理、化学或机械工艺过程改变基材表面状态、化学成份、组织结构或形成表面覆层,优化材料表面,达到提高表面耐磨性。表面工艺方法主要有下列几类:
a,电化学方法:利用电极反应,在基体上形成镀覆层,如电镀、化学转化等。
b,化学方法:利用化学物质的相互作用,在基体表面形成镀覆层,如化学镀、化学转化等。
c,热加工法:利用高温条件下材料熔融或热扩散,在基体表面形成镀、渗层,如热浸,表面合金化等。
d,高真空法:利用材料在高真空下气化或受激离子化而形成表面镀覆层,如真空蒸发镀、溅射镀、离子镀等。
e,其他物理方法:如机械镀、涂装、激光表面加工等。
润滑材料:润滑油是用石油经减压蒸馏所得的馏份油或残渣油,根据需要经过脱腊、脱沥青,加氢,酸碱处理等精制过程,得到半成品,再经过调和,加入适量的添加剂而成。润滑油在机械中的作用主要是降低摩擦和减缓磨损,其次还具有冷却、防护、密封和清洗作用。
润滑油降低摩擦和减缓磨损的能力称为润滑性能。在液体摩擦状态下,油的润滑性仅与粘度有关,在其他条件相同时,油的粘度大,则润滑性能好。粘度就是液体流动时在液体分子之间的内摩擦,即流体膜的剪切阻力。
在矿物油中加入某些物质,尽管量很少,但对润滑油的使用性能的改进却十分显著,这些加入的少量物质统称为添加剂。添加剂大致可分为二大类。一类是影响润滑油物理性质的添加剂,如各种降凝剂、增粘剂、消泡剂等;另一类是在化学方面起作用的添加剂,如各种抗氧剂、防锈剂、极压抗磨剂等。
润滑脂是由稠化剂(分散相)和稠化液体润滑剂(基础油、分散介质)以及少量的稳定剂和添加剂所构成。润滑脂是一种介于液体和固体之间的膏状润滑材料。用于机械的润滑脂能起到润滑、密封和保护作用,但不具备清洗和冷却作用。
与润滑油相比较,润滑脂有以下特点:主要优点为具有较高的承载能力,抗极压性能好;能用于比较苛刻的环境,适应性好,减震性强,保护密封性好;有良好的充填和保持能力;使用寿命较长,成本低。而缺点是粘滞性强,内摩擦系数大;流动性差,无冷却作用;高温下会发生相变,胶体结构破坏而析油,丧失正常的润滑能力。
固体润滑材料是指那些介于摩擦副表面间,以减少摩擦或磨损的粉末状或薄膜状的固体材料。在某些特殊工况条件下(高温、低温、高真空、强辐射、易燃等),使用油、脂润滑会显得不适用或者根本无效,此时,使用固体润滑材料就能较好地满足对润滑的要求。固体润滑材料多数具有层状结构。
雷诺方程:
雷诺方程是从粘性流体力学的基本方程出发,作了一定的假设而导出的微分方程,这些假设条件是:
(1)体积力忽略不计,即不考虑任何外力场对润滑过程的影响,如电力、磁力和重力等;(2)沿油膜厚度方向油压为常数,这是因为油膜厚度很薄,一般为百分之几毫米,油压不可能有很大变化;(3)摩擦表面的曲率半径远大于油膜厚度,为此可展成平面,推导公式时便于采用笛卡尔直角坐标;(4)流体和摩擦表面接触处没有滑动,即与摩擦表面接触的油层其流动速度与摩擦表面速度一致;(5)润滑剂是牛顿粘性流体,剪切应力与速度梯度成正比,符合牛顿粘性公式;(6)润滑油膜中流体作层流运动;(7)流体的惯性力忽略不计。
图6.22(a)所示的两滑动表面间流体作层流运动,并形成动压油膜。取空间坐标系X、Y和Z,而U、V和W分别代表流体沿X、Y和Z方向的流动速度,上表面沿X和Z方向的运动速度为U1与W1,下表面沿X和Z方向的运动速度为U2与W2。在油膜中取出一个柱体(图6.22(b)),其底面为dxdy,其高度为h。用qx表示沿y方向单位宽度的流量,而分别沿x和y方向上流量的变化率。则单位时间内沿X方向自左面流入柱体的容积流量为qxdy,而自右流出柱体的流量为
,与此相同,在Y方向流入柱体的流量为qydx,流出柱体的流量为
。
由此可知,沿X和Y方向流出和流入柱体流量的差值为:
(6-40)
如果柱体上底面的运动速度为W1,下底面的运动速度为W2,则柱体容积以速度(W1-W2)dxdy增长。由于流体流动的连续性和不可压缩性,流体流入与流出柱体流量差值必等于柱体体积的增量,即:
(6-41)
上式右边前两项表示流体沿X和Y方向上流量的变化,而后一项表示柱体上下底面垂直速度引起的流量变化。
图6.22 流体流动的连续性
在动压油膜中取一微元体,其边长分别为dx、dy和dz(图6.23)。如果沿X方向上,左面的压强为p,其正压力则为pdydz;右面的压强为,则相应的正压力为
。如微元体下表面的剪应力为τ,则其剪切力为τdxdy;在上表面的剪应力为
,则相应的剪切力为
。
由微元体力的平衡得:
去括弧并简化得:
为了避免混淆,准确地表示出剪应力τ的作用面及方向,将上式改写为:
(6-42)
τ下标x表示剪应力沿X方向,下标z表示作用在垂直于z轴的平面内。
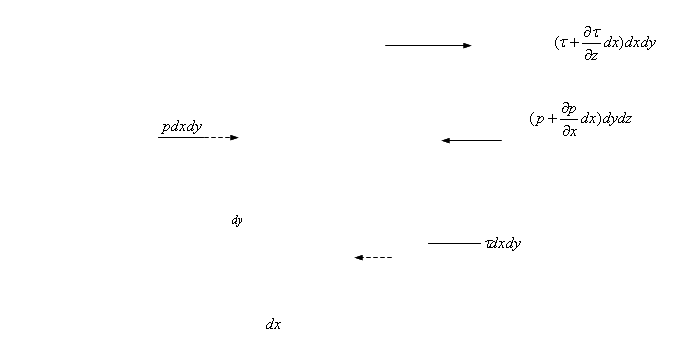

同样可以证明:
根据假设条件(2)可知,沿Z方向上油膜压力梯度为零,即,亦即
为零。
由牛顿粘性公式:
(6-43)
u为X方向的流动速度,v为Y方向的流动速度,代入压力梯度的公式后,得:
(6-44)
此处假定粘度η沿油膜厚度方向(Z方向)上为常量。这个假定与实际情况不符,在中等速度的滑动轴承中沿油膜厚度上的温差在22~25℃的范围内,由此引起的粘度变化达5~10倍。假定粘度η为常数,目的在于简化计算。则得:
因压强p沿坐标Z方向为常量,p不是z的函数,因此对进行两次积分,求得油膜中任意点的流速公式为:
(6-45)
式中C1、C2为积分常数,由边界条件确定,根据假设条件(4),油膜上下表层的流动速度与摩擦表面的速度相等,即:
z = k, u = U1; z = 0, u = U2
代入(6-45)式,得:
将C1、C2代入(6-45)式,得到油膜中任意点的流速为:
(6-46)
则沿X方向单位宽度上的流量为:
代入上下限并简化,得:
(6-47)
同理可得:
(6-48)
式中: U1、U2——为上、下摩擦表面沿X方向的运动速度;
V1、V2——为上、下摩擦表面沿Y方向的运动速度;
将qx、qy值代入流量连续方程(6-41)式:
得
令,经整理后则得雷诺方程的完整表达式为:
(6-49)
上式称全雷诺方程,也即三维雷诺方程。表达了流体动压润滑时,油膜压力沿X和Y两方向发生变化以及流速沿X、Y和Z三方向发生变化时,压力梯度、流速、油膜厚度、润滑油粘度等参数之间的关系。式中等号左边部分的两项表征沿X和Y方向油压的变化,等号右部方括号内前两项考虑沿X和Y方向上速度和油膜厚度变化的影响,而最后一项表征摩擦面作平行移动对油膜的挤压作用,W1-W2亦可写成。
流体动压轴承分为径向轴承和推力轴承两大类。承受径向载荷的轴承称为径向轴承,承受轴向载荷的轴承称为推力轴承。
流体润滑中两摩擦表面间完全被润滑油膜隔开,避免了粗糙表面上微凸体间的直接接触,减小了金属表面磨损,摩擦力的大小取决于流体的粘性。
取决于润滑剂和基体金属表面的相互作用的特性,处于液体摩擦和干摩擦之间的一种润滑状态称为边界润滑。
由吸附或化学反应生成的起润滑作用的润滑膜称为边界膜。边界膜可分为三种:1、物理吸附作用;2、化学吸附作用;3、化学反应作用。含有硫、磷或氯等活性原子的添加剂(极压添加剂)在摩擦所产生的高温(通常在150~200℃)下与金属起化学反应,形成硫、氯、磷等化合物(如硫化铁)的边界膜,即为化学反应膜。
摩擦学试验研究方法:
根据试验的目的和条件,摩擦磨损试验可分为:1,使用试验;2,台架试验;3,试样试验。
使用试验:这是在实际使用条件下,用真实零件进行的摩擦磨损试验。作为对零件材料的性能和结构的直接鉴定,试验所得数据资料具有真实性和可靠性。但是这种试验也存在一些困难和缺点,主要有:1)试验过程中的测量很困难,甚至需要研制专门的测量装置。有时为了减少偶然因素的影响,提高数据的精确度,需要在不同地点进行摩擦磨损试验,测量有关数据。因此,试验周期都相当长,一般需要几个月甚至几年时间才能获得试验结果,耗费的人力和物力较多。2)由于运营运转条件变化不定,易受偶然因素影响测量数据的精确性和重复性,因而可比性差,不利于研究摩擦磨损的规律性,而且无法对影响摩擦磨损的因素逐个进行研究。随着摩擦学技术的发展,目前这种试验已不用于机理研究,这是作为产品的鉴定而进行使用试验检验。
台架试验:台架试验是将实际使用的零部件,甚至整台机器装在专用的试验机上进行试验。这种试验条件比较接近实际,对影响摩擦磨损的各种因素,可以进行人为控调,从而减少偶然因素的影响,提高了试验数据的可靠性。此外,还能强化试验条件,缩短试验周期,对比于现场的使用试验可以减少试验费用。台架试验可以校验试样结果的正确性,也可检验产品质量是否合格,是否达到规定的要求。
试样试验:试样试验是根据相应的试验机的规定,把摩擦副材料制成结构形状比较简单、尺寸较小的试样。这种试验在摩擦磨损研究中比较常用。它的主要优点是:1)有利于研究摩擦磨损本身的过程和机理;能有效地控制各种影响摩擦磨损的因素。减少一些偶然因素对试验结果的影响,很适宜于逐个研究各因素对摩擦磨损的影响。2)试验所得数据重复性好,对比性强,而且试验费用少,同期短,可以在短时间内进行多参数和重复的试验验证。
磨损量是磨损研究中评定材料耐磨性的一个重要指标。磨损量的测定方法一般有:1 称重法:利用精密天平(精度为1/10000g或更高)等仪器测量试样在试验前后质量的变化,此法较简单且有一定精度,比较常用,适宜于小尺寸试样。2 测面积法:利用形貌仪、万能显微镜或读数显微镜等,测量试样在试验前后摩擦面法向尺寸面积的变化,以此来确定磨损量的多少。为了便于测量,在磨损试验前,可在摩擦表面上人为地作出标记。
谈谈摩擦学的认识,结合自己的研究方向,提出关键摩擦学问题,并提出研究方案。