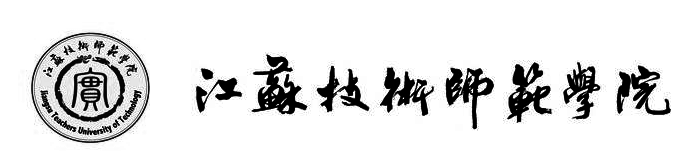


塑料模具课程设计说明书
学院名称: 材料工程学院
专 业:机械设计制造及其自动化
班 级: 08模具Z
学 号: 08321409
姓 名: 马凯华
指导教师: 卢雅琳
二〇一一 年 六 月
前 言
模具课程设计是在完成冷冲模具设计、塑料模具设计、CAD软件等相关专业课程学习之后,一个重要的综合性的环节。在设计之前,要具备机械制图、公差与技术测量、机械原理及零件、模具材料及热处理、模具制造工艺、塑件成型工艺及模具设计等方面必要的基础知识和专业知识。初步了解塑件的成型工艺和生产过程,熟悉各种塑料模具的典型结构。
课程设计的基本目的是:
(1)综合运用塑料模具设计、机械制图、公差与技术测量、机械原理及零件、模具材料及热处理、模具制造工艺、塑件成型工艺及模具设计等方面必要的基础知识和专业知识,分析和解决塑料模具设计问题,进一步巩固加深和拓宽所学的知识。
(2)通过设计实践,逐步树立正确的设计思想,增强创新意识和竞争意识,基本掌握塑料模具设计的一般规律,培养分析问题和解决问题的能力。
(3)通过计算、绘图和运用技术标准、规范、设计手册等有关设计资料,进行塑料模具设计全面的基本技能训练,为毕业设计打下一个良好的实践基础。
目 录
第1章 塑件工艺性分析... 2
1.1 塑件工艺性分析... 2
1.2 初步拟定总体设计方案... 4
第2章 注射模的结构设计... 6
2.1 分型面的选择... 6
2.2 型腔数目的确定与排列方式... 6
2.3 浇注系统的设计... 6
2.4 排气系统的设计... 10
2.5 成型零件的结构设计... 11
2.6 脱模机构的设计... 13
2.7 合模导向机构的设计... 14
2.8 冷却系统的设计... 16
第3章 模架的选择及模具的工作原理... 17
3.1 模架的选择... 17
3.2 模具总装图及工作原理... 17
第4章 注射机的选择及校核... 19
4.1 注射机的选择... 19
4.2 注射机的校核... 20
参考文献... 22
附录………………………………………………………………………………………… 23
第1章 塑件工艺性分析
1.1 塑件工艺性分析
1.1.1塑件的原材料分析
图1-1所示塑件为小油壶盖,材料为低密度聚乙烯(LDPE),LDPE为无毒、无味、表面无光泽的乳白色圆柱形颗粒。具有良好的延伸性、电绝缘性、密度低、透明性好等优点,在室温下可以抵抗多种溶剂。制品采用LDPE主要考虑到他具有强的化学惰性,不易被腐蚀,还具有较高的弹性。分子量较低,分子链有支链,结晶度较低(),质地柔软,透明性较PE好。耐冲击,耐低温性极好,但耐热性及硬度都低。结晶性原料,吸湿性小,可不必干燥。流动性好,流动性对压力敏感。
查文献[1]得:LDPE的收缩率为:,平均收缩率为:
;比重:
;熔融温度:
;成型模温:
;成型压力:
;流长比:275。收缩率大易变形,翘曲,必须控制模温,保持冷却均匀。
塑件的原材料分析结果如表1-1所示:
表1-1 塑件的原材料分析
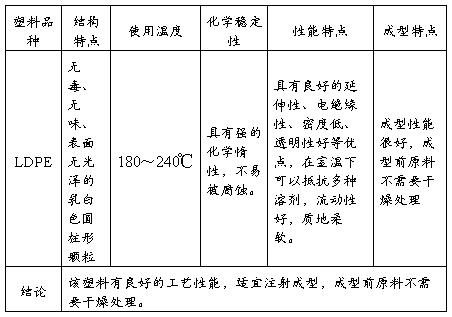
1.1.2塑件的结构工艺性分析
如图1-2所示,此塑件外形为圆柱形壳类零件,腔体深为16mm,壁厚均匀为2mm,总体尺寸不大不小,塑件成型性能良好,可强制脱模。
1.1.3塑件的尺寸精度分析
此塑件尺寸按MT5级塑料件精度查询取公差值(参见“模塑件尺寸公差表” )。分析后的塑件尺寸精度图如图1-3所示:
1.1.4塑件的表面质量分析
该塑件是壶盖,要求外表美观、无斑点、无熔接痕,表面粗糙度可取Ra1.6,粗糙度可取Ra0.8。
1.1.5塑件注射成型的工艺参数
塑件注射成型工艺参数见表1-2,试模时,可根据实际情况作适当调整。
表1-2 LDPE塑料的注射成型工艺参数
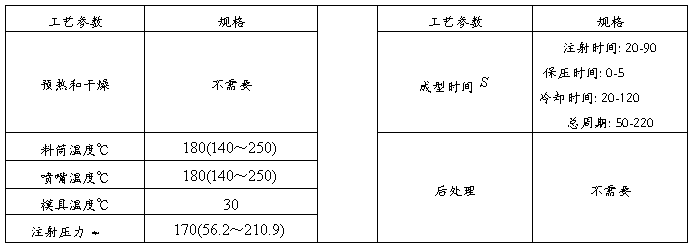
1.2 初步拟定总体设计方案
方案一:采用一模两腔,分型面设在壶盖底部,型腔布置采用直线型。用脱模板强制脱模,模具设计为三板式。
方案二:采用一模四腔,分型面设在壶盖底部,型腔布置在中心线上,关于中心点对称。用脱模板强制脱模,模具设计为三板式。
方案三:采用一模四腔,分型面设在壶盖底部,型腔布置为双排,每排2腔,排列方式为矩形,型腔关于中心线对称。用脱模板强制脱模,模具设计为三板式。
方案一生产效率低;方案二型腔排列不合理,型腔布置不够紧凑;方案三模具生产效率高,型腔布置合理,塑件精度也能满足要求。为了使模具与注射机的生产能力相匹配,提高生产效率和经济性,并保证塑件精度,经综合考虑,采用方案三为佳。
根据前面所选方案及塑件结构特点,模具设计时考虑如下:
(1)壶盖为小制件,可采用一模多腔。由于壶盖用量大,在注射条件许可的情况下,希望型腔数尽可能多,该模具用于4A注射机,故确定为1模4腔。型腔布置为双排,每排2腔。模具的闭合高度、安装定位等均应符合注射机的技术参数。
(2) 强脱时要克服塑件内阻力,用脱模板实现脱模;分型面设在壶盖底部。
第2章 注射模的结构设计
根据塑件形状、精度、大小、工艺要求和生产批量,模具设计时按下面的步骤进行。
2.1 分型面的选择
结合塑件结构特点,塑件成型后必然留在型芯上,故模具分型面应设在塑件截面最大处,尽量取在料流末端,利于排气,保证塑件表面质量。
2.2 型腔数目的确定与排列方式
2.1.1型腔数目的确定
壶盖作为包装容器大批量生产,是小型制件,精度要求不高,考虑到现有注塑机的锁模力、注射量及壶盖的精度和经济性因素(模具制造费用、设备运转费用低一些),可以采用一模四腔的模具形式。
2.1.2型腔排列形式的确定
该塑件所用材料是低密度聚乙烯(LDPE),可利用LDPE材料弹性较高的优点,靠推板将较浅的制件强行从型腔中脱出,因此本设计采用脱模板推出的强制脱模方法,型腔的排列方式采用两行两列的矩形排列。
2.3 浇注系统的设计
首先考虑到产品的使用要求,成型塑件表面不能留有浇口痕迹;其次根据产品材料LDPE的性能和成型特点、塑件结构形式,粘度、以及粘度对剪切力的敏感程度等因素,模具设计成三板式采用点浇口,浇口设置在塑件底部位置。点浇口可显著提高熔体的剪切速率,使熔体粘度大为降低有利于充模,对于LDPE这样对剪切速率敏感的熔体尤为有效。并且塑件作为包装容器,外观质量要求高,点浇口的残留痕迹小,可确保塑件的表面质量,脱模时浇口处自动拉断,便于实现制品生产过程的自动化,提高了生产效率,增加了经济效益。采用平衡浇注系统,型腔排列紧凑,减小了模具尺寸,为了能使各个型腔能同时均衡地充满,采用BGV(Balanced Gat Value)法通过人工修改各个型腔浇口尺寸达到平衡。利用冷料穴储存前锋冷料。
浇道与注塑机的喷嘴同轴,断面为圆形,锥度为3;分流道采用平衡式布置,圆形断面结构,流道设计的原则是尽可能短一些,以减少流道中的凝料及压力损失,使塑料不会因降温过多而影响其注射成型。
2.3.1主流道设计
模具浇口套主流道球面半径与注射机喷嘴球面半径
的关系为:
;模具浇口套主流道小端面直径
与喷嘴出口直径
的关系为:
。
1) 主流道尺寸
根据所选注射机,则主流道小端尺寸为:
D=d+(0.5-1)mm=4+0.75=4.75mm ;
主流道球面半径为:
R=r+(0.5-1)mm=12+0.75=12.75mm;
2) 主流道衬套形式
本设计虽然是小型模具,但为了便于加工和缩短主流道长度,衬套和定位圈还是设计成分体式,主流道长度取93mm,衬套如图2-1所示,材料采用T10A钢,热处理淬火后表面硬度为。
3) 主流道凝料体积
。
4) 主流道剪切速率校核
由经验公式,校核合格。 式中
;
。
2.3.2分流道设计
1) 分流道应能满足良好的压力传递和保持理想的填充状态,使塑料熔体尽快地经分流道均衡的分配到时各个型腔,因此,采用平衡式分流道,如图2-2所示。
2) 分流道长度
第一级分流道长度L=40mm。
第二级分流道长度L=23mm。
3) 分流道的形状、截面尺寸以及凝料体积
(1) 形状及截面尺寸
为了便于机械加工及凝料脱落,本设计的分流道设置在分型面上定模一侧,截面形状采用加工工艺性比较好的梯形截面。梯形截面对塑料熔体及流动阻力均不大,一般采用下面经验公式来确定截面尺寸,即:
,
据参考文献[2]取;
H=
(2) 凝料体积
分流道长度:;
分流道截面积:A=;
凝料体积:q=172×5=860mm
=0.86cm
4) 分流道剪切速率校核
采用经验公式γ=3.3q/πR=6.7×10
,(3-9)在
之间,剪切速率校核合格。
式中 q=,
。
t——注射时间,取1s;
——截面面积(
);
——截面周长(0.9cm)。
5) 分流道的表面粗糙度
分流道的表面粗糙度并不要求很低,一般取0.8μm~1.6μm即可,在此取1.6μm。
2.3.3浇口设计
1) 浇口类型及位置的确定
该模具是中小型塑件的多型腔模具,同时从所提供塑件图样中可看出,在中部的圆周上设置侧浇口比较合适。侧浇口是典型的矩形浇口,能很方便地调整充模时的剪切速率和浇口封闭时间,因而又称为标准浇口。这类浇口加工容易,修整方便,并且可以根据塑件的形状特征灵活地选择进料位置,因此它是方泛使用的一各浇口形式,普遍使用于中小型塑件的多型腔模具。
2) 浇口结构尺寸的经验计算
(1) 侧浇口深度和宽度经验计算
经验公式为:
h=nt=1.5mm,。
式中: h——侧浇口深度(mm);
w——浇口宽度(mm);
A——塑件外表面积(约为);
t——塑件厚度(平均厚度约为2mm);
n——塑料系数,查表得n=0.6。
(2) 侧浇口的经验计算
同于侧浇口的种类很多,现查常用经验数据表可得侧浇口尺寸:
深度:h=1.5mm;宽度:w=1.0mm;长度:l=1.0mm。
其尺寸实际应用效果如何,应在试模中检验与改进。
2.3.4冷料穴的设计
1) 主流道冷料穴
如图2-3所示,采用Z形头拉料杆,该拉料杆固定在动模固定板上,开模时利用凝料对球头的包紧力使主流道凝料从主流道衬套中脱出。
2) 分流道冷料穴
在分流道端部加长5mm作为分流道冷料穴。
2.4 排气系统的设计
经综合考虑,采用开设排气槽的排气方式。排气槽的作用主要有两点。一是在注射熔融物料时,排除模腔内的空气;二是排除物料在加热过程中产生的各种气体。越是薄壁制品,越是远离浇口的部位,排气槽的开设就显得尤为重要。另外对于小型件或精密零件也要重视排气槽的开设,因为它除了能避免制品表面灼伤和注射量不足外,还可以消除制品的各种缺陷,减少模具污染等。那么,模腔的排气怎样才算充分呢?一般来说,若以最高的注射速率注射熔料,在制品上却未留下焦斑,就可以认为模腔内的排气是充分的。适当地开设排气槽;可以大大降低注射压力、注射时间。保压时间以及锁模压力,使塑件成型由困难变为容易,从而提高生产效率,降低生产成本,降低机器的能量消耗。
模腔排气的方法很多,但每一种方法均须保证排气槽在排气的同时,其尺寸设计应能防止物料溢进槽内;其次还要防止堵塞。因此从模腔内表面向模腔体外缘方向测量,长6~12mm以上的排气槽部分,槽高度要放大约0.25~0.4mm。另外,排气槽数量太多是有害的。因为如果作用在模腔分型面未开排气槽部分的锁模压力很大,容易引起模腔材料冷流或裂开,这是很危险的。除了在分型面上对模腔排气外,还可以通过在浇注系统的料流末端位置设排气槽,以及沿顶出杆四周留出间隙的方式达到排气的目的。因为排气槽开的深度、宽度以及位置的选择;如果不适当,产生的飞边毛刺,将影响制品的美观和精度。因此上述间隙的大小以防止顶出杆四周出现飞边为限。该制件最好采用以下方式排气:1、彻底清除流道内气体;2、用粒度为200#的碳化硅磨料对分型面配合表面进行喷丸处理。另外,在浇注系统料流末端开设排气槽主要是指分流道末端位置的排气槽,模腔的四周都应排气,各排气槽应相隔25mm,其宽度应等于分流道的宽度6.5mm,高度为0.12mm。
2.5 成型零件的结构设计
模具中确定塑料几何形状和尺寸精度的零件称为成型零件。在本设计中成型零件就是成型壶盖外表面的凹模以及成型内表面的型芯。
2.5.1凹模的结构设计
采用整体式凹模,凹模由整块材料制成,成型的塑件尺寸精度高,没有拼合缝,外形美观,适合于成型外形简单的中小型塑件。
2.5.2凸模的结构设计
采用凸台式型芯,结构简单,而且易于成型,如图2-4所示。
2.5.3成型零件工作尺寸的计算
制品尺寸公差按照GB/T 14486-93中未注公差尺寸选取。制品尺寸标注如图2-5所示。
型腔径向尺寸: l=[L
﹙1+S﹚ -0.75Δ]
=[(1+0.0325)×32-0.75×Δ]
=(1.0325×32-0.75×0.8)
=32.44
l=[L
﹙1+S﹚ -0.75Δ]
=[(1+0.0325)×24-0.75×Δ]
=(1.0325×24-0.75×0.62)
=24.315
型芯径向尺寸: l= [L
﹙1+S﹚ +0.75Δ]
=[﹙1+0.0325﹚×28+0.75×0.70]
=29.435
l= [L
﹙1+S﹚ +0.75Δ]
=[﹙1+0.0325﹚×20+0.75×0.62]
=21.115
型腔深度尺寸: H=[(1+S)×h-2Δ/3]
=[(1+0.0325)×9-0.38×0.5]
=9.4825
H=[(1+S)×h-2Δ/3]
=[(1+0.0325)×18-0.58×0.5]
=18.585
型芯深度尺寸: H=[(1+S)×h+2Δ/3]
=[(1+0.0325)×9+0.38×0.5]
=9.4825
H=[(1+S)×h+2Δ/3]
=[(1+0.0325)×18+0.58×0.5]
=18.92
式中: S——塑件平均收缩率;Δ——塑件公差值;δ——制造公差,(取Δ/3)。
取
2.6推出机构设计原则:
① 推出机构应设置在动模一侧
② 保证推出时塑件不变形或损坏
③ 机构简单动作可靠
④ 良好的塑件外观
⑤ 模时正确复位
本模具采用推杆推出机构。
(1) 推杆的形式 采用等圆截面推杆,其尾部采用轴肩形式,推杆材料为T8A,头部要淬火,硬度应达到40HRC以上,滑动配合部分表面粗糙度达到Ra0.63~1.25,顶杆的位置高在阻力大的地方。
图2—6推杆
(2) 推杆的固定及配合 推杆与推杆孔部为滑动配合,一般选H7/f6,其配合间隙兼有排气作用,但不应大于所用塑料的排气间隙,以防漏料。配合长度一般与顶杆直径的2~3倍,推杆端面构成型腔的一部分,应精细抛光。采用推杆比较容易使单边间隙达到0.01—0.02mm的要求。推杆选用d=8mm推杆推出距离d=14mm。
推杆的固定方式如图:
图2—7推杆固定方式
此模具的型芯在动模,开模后,塑件包紧型芯留在动模一侧,根据塑件是壳类零件的特点,采用脱模板推出形式,这样推出平稳,有效保证了推出后塑件的质量,模具结构也比较简单,脱模板的厚度为20mm。
(3)拉料杆的设计
采用半球形头拉料杆,该拉料杆固定在动模固定板上,开模时利用凝料对球头的包紧力使主流道凝料从主流道衬套中脱出。如图2-8所示:
2.7 合模导向机构的设计
2.7.1导向机构的总体设计
该模具采用4根导柱,其布置为等直径对称布置;导柱安装在支承板上,导套安装在定模固定板上;为了保证分型面很好的接触,要在导套的孔口倒角。
2.7.2导柱的设计
(1) 该模具用带头导柱,不加油槽,为使导柱能顺利地进入导向孔,导柱的端部做成圆锥形。
(2) 导柱的直径应根据模具尺寸来确定,应保证具有足够的抗弯强度,该导柱直径由标准模架可知。
(3) 导柱的安装形式,导柱固定部分与模板按H7/r6配合,导柱滑动部分按H7/k6的配合。导柱工作部分的表面粗糙度为Ra=0.4μm
(4) 导柱应具有坚硬而耐磨的表面,坚韧而不易折断的内芯。该模具中采用碳素工具钢T8A经淬火处理,硬度为50HRC以上。
2.7.3导套的设计
(1) 结构形式。采用带头导套(I)型,如图2-10所示,导套的端面应倒圆角。
(2) 导套孔的滑动部分按的间隙配合,表面粗糙度为0.8μm。导套外径与模板一端采用
配合;另一端采用
配合。
(3) 导套材料可用淬火钢或铜(青铜合金)等耐磨材料制造,该模具中采用T8A。
2.8 冷却系统的设计
由于PE塑料粉属于热塑性塑料,前面塑料分析已近提到,在 冷却时应保证冷却均匀、稳定、速度慢且充分冷却。针对该塑件采用加平行水道,以达到塑件的稳定充分冷却。
第3章 模架的选择及模具的工作原理
3.1 模架的选择
根据
《塑料注射模模架》确定选用三板式模架模架,模架结构如图3-1所示。
3.1.1定模型腔板
定模型腔板,塑件高度18mm,在模板上还要开设冷却水道,冷却水道型腔应有一定的距离,因此厚度取32mm。
3.1.2凸模固定板
凸模固定板,凸模的成型部分直径为32,因此厚度取20mm。
3.1.3垫块尺寸
垫块=推出行程+推板厚度+推杆固定板厚度+
,根据计算,垫块厚度C取63mm。
3.2 模具总装图及工作原理
上述尺寸确定之后,就可以选用A
型标准模架制造,板面为
,模具结构如图3-2所示。
模具工作原理:
成型制件时,先合模,对模具预热一段时间后再开始注射。一次注射完成后,冷却一段时间,然后开模。开模时,模具沿I-I面打开,制件与型腔分离,包裹在型芯上,随动模一起向下运动,移动一段距离后,浇注系统凝料在点浇口处被拉断;当注射机的推杆顶到推板16时,动模座板继续运动而推出机构停止运动,此时,在推杆12和脱模板9的作用下,塑件被顶出,使塑件脱离型芯,完成脱模动作,然后合模,进行下一次循环。
第4章 注射机的选择及校核
4.1 注射机的选择
4.1.1注射量的计算
根据零件的三维模型,利用三维软件直接可查询到塑件的体积为:;查文献[1]可知LDPE的密度为:0.96;所以塑件的质量为:
塑件与浇注系统的总质量按塑件的0.6倍来估算为:
所以注射量为。
4.1.2初选注射机
根据塑件的形状、每一生产周期实际需要的注射量,取一模四件的模具结构,结合现有的成型设备,初步选取SZ-100/60立式注射机(常熟塑料机械总厂),注射机主要技术参数见表4-1所示。
表4-1 注射机主要技术参数
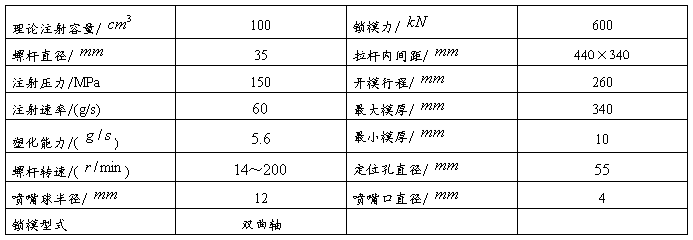
4.2 注射机的校核
4.2.1由注射机料筒塑化速率校核模具的型腔数n
型腔数校核合格。
式中 ——注射机最大注射量的利用系数,一般取0.8;
——注射机的额定塑化量(
);
——成型周期,取
。
4.2.2注射压力的校核
而,注射压力校核合格。
式中 ——塑料所需的注射压力,取
。
4.2.3锁模力校核
在确定了型腔压力和分型面面积之后,可以按下式校核注塑机的额定锁模力:
式中,----注射机的额定锁模力;
----模具型腔内塑料熔体平均压力
,一般为注射机压力的
倍,通常为
,此塑件可取
,可参看《塑料制品成型及模具设计》表
;
----塑件和浇注系统在分型面上的投影面积之和
。
通过实体的模拟,测得其分型面上的投影面积为
,为了更好校核锁模力,引入一个安全系数
:
:安全系数,通常取
,取
;
锁模力为大于胀型力
所需要的满足要求,锁模力校核合格。
4.2.4安装尺寸的校核
从选定模架可知,模架外形尺寸:。
模具高度,
合格;
4.2.5开模行程的校核
开模时,推板随动模部分向开模方向移动当达到开模行程时就停止。
开合模的过程中,模具总的开模行程=(脱模距离)+
(包括浇注系统凝料在内的塑件高度)
(注射机最大开模行程),合格。
各参数校核均合格,所以本模具所选注射机完全满足使用要求。在此注塑机上可以完成制品的制作。
参考文献
[1] 屈华昌.塑料成型工艺与模具设计[M] . 北京: 机械工业出版社
[2] 冯炳尧, 韩泰荣等. 模具设计与制造简明手册[M] . 上海: 上海科学技术出版社, 1985
[3] 蒋继宏, 王效岳.注塑摸具典型结构100例[M] . 北京: 中国轻工业出版社, 2000
[4] 李志刚, 夏巨谌. 中国模具设计大典[M]. 2003
[5] 王树勋. 注塑模具设计与实用技术[M] .广州: 华南理工大学出版社, 1996
[6] 丁闻. 实用塑料成型模具设计手册[M]. 西安交通大学出版社.
[7] 伍先明,王群,庞佑霞,张厚安.塑料模具设计指导书[M]. 北京:国防工业出版社
[8] 陈万林等编著. 实用塑料注射模具设计与制造[M]. 北京: 机械工业出版社, 2000.
[9] 丁华编著. 注射模具设计技术及实例[M]. 北京: 机械工业出版社, 1998-4.
[10] 中国机械工业教育协会组编. 塑料模具设计及制造[M]. 北京: 机械工业出版社, 2001.
[11] 贾润礼,程志远 .实用注塑模设计手册[M].北京: 中国轻工业出版社.
[12] 塑料模具设计手册编写组编. 塑料模具设计手册[M]. 北京: 机械工业出版社, 1984.
[13] 王树勋, 朱亚林, 梅了伶, 龙国梁编. 注射模具设计[M]. 广州: 华南理工大学出版社, 2005.
[14] 王孝培主编. 塑料成型工艺及模具简明手册[M]. 北京: 机械工业出版社, 2000.6.
[15] 邹继强主编. 塑料模具设计参考资料汇编[M]. 北京: 清华大学出版社, 2005.9.
[16] 田宝善 田雁晨 塑料注射模具设计技巧与实例[M]. 北京:化工工业出版社
附 录
1. CAD图纸:包括一张装配图和数张零件图。