塑料模具课程(毕业)设计说明书
设计题目_______________________
__________院(系)_________专业
班级____________学号 ___________
设计人_________________________
指导教师_______________________
完成日期______年_____月______日
1.1支承座注射模设计
本课程设计为一支承座,如图1-1所示。塑件结构比较简单,塑件质量要求是不允许有裂纹、变形缺陷,脱模斜度30′-1°;材料要求为ABS,生产批量为大批量,塑件公差按模具设计要求进行转换。
1.1.1塑件成型工艺性分析
1. 塑件的分析
(1) 外形尺寸 该塑件壁厚为2mm,塑件外形尺寸不大,塑料熔体流程不太长,塑件材料为热塑性塑料,流动性较好,适合于注射成型。
(2) 精度等级 塑件每个尺寸的公差不一样,任务书已给定尺寸公差,未注公差的尺寸取公差为MT3级。
(3) 脱模斜度 ABS的成型性能良好,成型收缩率较小,参考文献(1)表选择塑件上型芯和凹模的统一脱模斜度为1°。
2. ABS工程材料的性能分析
ABS是由丙烯腈、丁二烯和苯乙烯三种化学单体合成。每种单体都具有不同特性:丙烯腈有高强度、热稳定性及化学稳定性;丁二烯具有坚韧性、抗冲击特性;苯乙烯具有易加工、高光洁度及高强度。从形态上看,ABS是非结晶性材料。三中单体的聚合产生了具有两相的三元共聚物,一个是苯乙烯-丙烯腈的连续相,另一个是聚丁二烯橡胶分散相。ABS的特性主要取决于三种单体的比率以及两相中的分子结构。这就可以在产品设计上具有很大的灵活性,并且由此产生了市场上百种不同品质的ABS材料。这些不同品质的材料提供了不同的特性,例如从中等到高等的抗冲击性,从低到高的光洁度和高温扭曲特性等。ABS材料具有超强的易加工性,外观特性,低蠕变性和优异的尺寸稳定性以及很高
的抗冲击强度。
ABS是一种综合性能十分良好的树脂,无毒,微黄色,在比较宽广的温度范围内具有较高的冲击强度,热变形温度比PA、PVC高,尺寸稳定性好,收缩率在0.4%-0.8%范围内,若经玻纤增强后可以减少到0.2%-0.4%,而且绝少出现塑后收缩。ABS具有良好的成型加工性,制品表面光洁度高,且具有良好的涂装性和染色性,可电镀成多种色泽。干燥处理:ABS材料具有吸湿性,要求在加工之前进行干燥处理。建议干燥条件为80~90℃下最少干燥2小时。材料温度应保证小于0.1%。 熔化温度:210~280℃;建议温度:245℃。 模具温度:25~70℃。(模具温度将影响塑件光洁度,温度较低则导致光洁度较低)。 注射压力:500~1000bar。 注射速度:中高速度。
3. ABS的注射成型过程及工艺参数
1) 注射成型过程
(1) 成型前的准备。干燥处理:ABS材料具有吸湿性,要求在加工之前进行干燥处理。建议干燥条件为80~90℃下最少干燥2小时。材料温度应保证小于0.1%。 熔化温度:210~280℃;建议温度:245℃。 模具温度:25~70℃。(模具温度将影响塑件光洁度,温度较低则导致光洁度较低)。 注射压力:500~1000bar。 注射速度:中高速度。
表1-1 ABS的性能参数
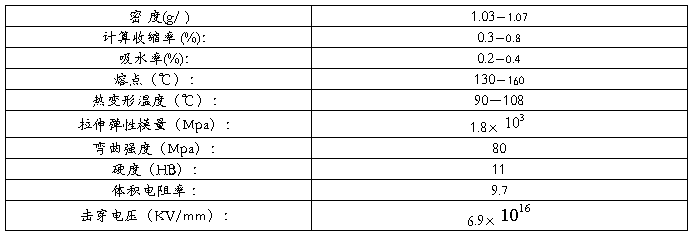
(2)注射过程。塑料在注射机料筒内经过加热、塑化达到流动状态后,由模具的浇注系统进入模具的型腔成型,其过程可分为充模、压实、保压、倒流和冷却五个阶段。
2)注射工艺参数
注射机:螺杆式,螺杆转速为48r/min
预热温度(℃): 80-85
时间(h): 2-3
料筒温度(℃): 前段 180-200
中段 165-180
后段 150-170
喷嘴温度(℃): 170-180
模具温度(℃): 50-80
注射压力(MPa): 60-100
成型时间(s): 注射时间 20-90
高压时间 0-5
冷却时间 20-120
总周期 50-220
1.1.2制定模具的结构形式和初选注射机
1.分型面位置的确定
通过对塑件的结构形式的分析,分型面应选在支承座的截面积最大且利于开模取出塑件的底面上,其位置如图1-2所示。
2. 型腔的数量和排位方式的确定
(1)型腔数量的确定 由于该塑件的精度要求不搞,尺寸也较小,并且为大批量生产,可采用一模多腔的结构形式。同时,考虑到塑件尺寸、模具结构尺寸的关系,以及制造费用和各种成本费用等因素,初步制定为一模四腔形式。
(2)型腔排列形式的确定 由于该模具选择的是一模四腔,其型腔中心距地确定见图1-3及其说明,故流道采用H形对称排列,使型腔进料平衡。如图1-3所示。
图1-2 分型面的选择 图1-3 型腔数量的排列布置
(3)模具的结构形式的初步确定 由上分析,该模具的设计为一模四腔,对称H型直线排列,根据塑件结构形状,推出机构初选推板推出或推杆推出。浇注系统设计时,流道采用对称平衡式,浇口采用侧浇口,且开设在分型面上,这样,动模部分需要添加型芯固定板、支撑板或推件板。综上分析可确定采用大水口的单分型面注射模。
3.注射机型号的确定
1)注射量的计算
通过PRO/E建模分析得塑件质量属性如图1-4所示。
图1-4
塑件体积为:V塑=26.338
塑件质量:M塑=ρV塑=1.05x26.338=27.655g 公式中,ρ可根据参考文献
[2]表9-6取1.05g/
2) 浇注系统凝料体积的初步估算
由于浇注系统的凝料在设计之前不能去定准确的数值,但是可根据经验按照塑件体积的0.2倍到1倍来估算。由于本次设计采用的流道简单并且较短,因此浇注系统的凝料按塑件体积的0.3倍来估算,故一次注入模具型腔塑料熔体的总体积(即浇注系统的凝料和4个塑件体积之和)为
V总=1.3n V塑=1.3x4x26.338= 136.9576≈137.00
3) 选择注射机
根据以上的计算得出在一次注射过程中注入模具型腔的塑料的总体积为137.00,由参考文献[1]式(4-18)V公= V总/0.8=137/0.8=171.25
。根据以上的计算,初步选择公称注射量为200
,注射机型号为SZ-200/120卧室注射机,其图片见图1-5以及主要技术参数见表1-2。
图1-5 SZ-200/120卧室注射机
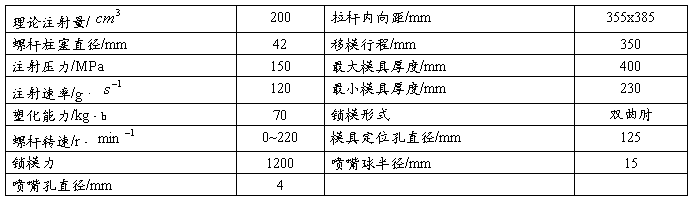
表1-2 注射机主要技术参数
4)注射机的相关参数的校核
(1)注射压力校核。 查参考文献[3] 表2-1可知,该制件属于厚壁件,ABS所需注射压力为80-110Mpa,所以即使选用P0=110MPa,该注射机的公称注射压力P公=150MPa,注射压力的安全系数K1=1.25~1.4,这里我们取K1=1.3,则:
K1p0=1.3X110=143。所以,注射机注射压力合格。
(2)锁模力的校核
①塑件在分型面上的投影面积
A塑=(-4X
)X π/4-
=337.455=338
②浇注系统再分型面上的投影面积A浇,A浇是每个塑件再分型面上的投影面积A塑的0.2~0.5倍,本例中的流道较简单。分流道也较短,所以选择分流道凝料投影面积可适当取小些,这里选取A浇=0.2A塑 。
③塑件和浇注系统在分型面上的总投影面积为
A总=N(A塑+A浇)=N(A塑+0.2A塑)=4X1.2A塑=4X1.2X338=1862.4
④模具型腔内的胀型力F胀,则
F胀=A总P模=1862.4X50=93.12KN
上式中,P模是型腔的平均计算压力值,P模通常取注射压力的20%~40%,所以大致范围在30Mpa~60Mpa,因为材质是ABS,根据其黏度和制品的精度要求,我们选择P模为50MPA。
由表1-2可知该注射机的公称锁模力为F锁=1200KN,锁模力安全系数为K2=1.1~1.2,这里选择K2XF胀=1.2XF胀=1.2X93.12=111.744<F锁 。
1.1.3 浇注系统的设计
1.主流道的设计
主流道通常位于模具中心塑料熔体的入口处,形状一般为圆锥形,便于熔体的流动和开模时主流道凝料的顺利拔出。由于主流道和高温塑料熔体以及注射机喷嘴反复接触,故再设计时常设计为可拆卸更换的浇口套。
1)主流道尺寸
(1) 主流道的长度 一般由模具结构确定,对于小型模具L应尽量小于60mm,本次设计初取50mm进行计算。
(2) 主流道小端直径 d=注射机喷嘴尺寸+(0.5-1)mm=4.5mm
(3) 主流道大端直径 D=d+L主tan(a/2)=8,其中式中a选取4°。
(4) 主流道球面半径SR=注射机喷嘴球头半径+(1-2)mm=15+2=17mm。
(5) 球面的配合高度 h=3mm。
2)主流道的凝料体积
V主=L主(主+
主+R主r主)π/3=50x(
+
+4x2.25)x3.14/3=1573.3
3) 主流道当量半径
Rn==3.125mm
3)主流道浇口套的形式
主流道衬套是标准件可选购,主流道小端口入口与注射机喷嘴反复接触,易磨损,故对材料要求比较高,故一般将主流道衬套与定位圈分开设计,便于拆卸更换。材料选用优质钢材单独加工并进行热处理。故浇口套选用碳素钢T10A,并热处理淬火表面硬度为50HRC-55HRC。形式如下图1-6所示。
图1-6
2.分流道设计
1)分流道的布置形式
为了减少再流道内的压力损失和尽可能避免熔体温度降低以及减少分流道的容积和压力平衡,采用平衡式分流道。如图1-7所示。
2)分流道的长度
根据四个型腔的结构设计,分流道长度适中。
3)分流道的当量直径
流过一级分流道塑料的质量
m=ρV塑=1.05x26.338x2=55.3<200g
但该塑件的壁厚在2-3.5mm之间,查参考文选[3]图2-3的经验曲线差得=4.3,再根据单向分流道长度60,由图2-5查得修正系数Fl=1.05,则分流道直径经修正后为
D=fL=4.3x1.05=4.515≈4.6mm
4)分流道的截面形状
本设计采用梯形截面,其加工工艺性好,熔体的热量散失和流动阻力均不大。
5)分流道界面尺寸
设梯形的上底宽度为B=6mm,地面的倒角为半径R=1mm,梯形高度取H=2B/3=4,设下底宽度为b,梯形面积应满足如下关系式。
H=
代值计算的b=3.813mm,考虑到梯形底部圆弧对面积的减小以及脱模斜度等因素,取b=4.5mm。通过计算等梯形的斜度为a=10.6°,基本符合要求。如图1-8所示。
6)凝料体积
(1)分流道的长度为L分=(23+3.5+6)x2=65mm
(2)分流道截面积 A分=x4=21
(3)凝料体积 V分=L分A分=65x21=1365=1.365
考虑圆弧影响取V分=1.5
7)校核剪切速率
(1)确定注射时间为t=2S。
(2)计算单边流道体积流量:q分==
=27.338
·
(3)由公式γ=可得到
γ分=
=
=2.361x
该分流道的剪切速率处于浇口主流道和分流道的最佳剪切塑料5x~
5x。故分流道的熔体剪切速率合格。
8)分流道的表面粗糙度和脱模斜度
分流道的表面粗糙度要求不是很低,一般去Ra1.25 ~2.5μm。这里我们根据加工实际选取Ra1.6μm,另外脱模斜度一般为5°~10°。而之前计算脱模斜度为10.6°,脱模斜度足够。
3.浇口的设计
根据塑件的要求,不允许出现裂纹和变形,表面质量要求也较高,并采用一模四腔,为便于调整冲模时的剪切塑料和封闭时间,采用侧浇口,其界面形状简单,易加工,也便于试模后修正,且开设再分型面上,从型腔的边缘进料。
1)侧浇口尺寸的确定
(1)计算侧加工的深度。根据表2-6,可得侧浇口的深度h计算公式为
h=nt=3x0.7=2.1mm
其中,n是塑料成型系数,ABS系数为0.7,t为塑件壁厚,这里取t=3mm。
为了便于试模时发现问题并进行修模处理,参照文选查找ABS的侧浇口厚度为1.8~3mm,这里我们选择浇口深度为2mm。
(2)计算侧浇口的宽度,根据侧浇口宽度公式B=可得。
B==
=0.64mm≈0.7mm
式中,n为塑料成型系数,ABS取0.7,A为凹模的内表面积。
(3)计算侧浇口的长度,根据表2-7可取侧浇口的长度L浇=1.00mm
2)侧浇口的剪切速率的校核
(1)确定注射时间为t=2S。
(2)计算单边流道体积流量:q浇==
=13.169
·
(3)由公式γ=≤4x
,可得到
γ===
=32806≈3.2x
<4x
符合剪切速率。
式中, 为矩形浇口的当量半径,即
=
=
=0.75。
4.校核主流道的剪切速率
1)计算主流道的体积流量
Q主==
=55.77
·
2)计算主流道的剪切速率
γ=
=
1.920x
可得到,主流道的剪切速率处于浇口和分流道最佳剪切速率5x~5x
之间。则主流道剪切速率合格。
5.冷料穴的设计及计算
冷料穴位于主流道正对面的动模板上,其作用主要是储存熔体前锋的冷料,防止冷料进入模具型腔影响制品的表面质量。本设计既有主流道冷料穴又有分流道冷料穴,由于该制件要求没有印痕,采用脱模板推出塑件,采用球头拉料杆匹配的冷料穴。开模时,利用凝料对球头的抱紧力使凝料从主流道衬套中脱出。
1.1.4成型零件的结构设计及计算
1.成型零件的机构设计
(1)凹模的结构设计。凹模是成型制品外表面的成型零件。其结构可分整体式、整体嵌入式、组合式和镶拼式四种。这里采用整体嵌入式。
(2)凸模的结构设计。凸模是成型塑件内表面的成型零件。通常是整体式和组合式两种类型。这里采用整体式型芯。
2.成型零件钢材选用
对成型塑件的综合分析,该塑件的成型零件要有足够的强度、刚度、耐磨性及良好的抗疲劳性,还考虑它的机械加工性能和抛光性能。该塑件是大批量生产,所以构成型腔的嵌入式凹模钢材选用P20。成型塑件型芯,由于脱模时与塑件的磨损严重,因此钢材也选用P20。
3.成型零件工作尺寸的计算
采用相应公式的平均尺寸法计算成型零件尺寸,塑件尺寸公差安塑件零件图给定的公差计算。
(1) 凹模径向尺寸计算 塑件外部径向尺寸的转换
L=27
L
=17
L
=10.5
根据公式:L=[(1+S
)L
-X
△
]
计算可得:
L=[(1+0.0055)X27-0.6X0.46]
=26.8725
=26.8
L=16.9045
=16.9
L=10.5578
=10.5
(2)凹模深度尺寸计算
根据公式:H=[(1+S
)H
-X
△
]
计算可得;
H=2
H
=14
H
=18
H=[(1+0.0055)x2-0.75x0.14]
=1.906
=1.9
H=13.888
=13.8
H=17.91
=17.9
(3)型芯径向尺寸计算
根据公式:l=[(1+S
)l
-X
△
]
计算可得;
l=[(1+S
)l
+X
△
]
=[(1+0.0055)x13.5+0.7x0.27]
=13.763
=13.7
(4) 型芯高度尺寸计算
根据公式:h=[(1+S
)h
-X
△
]
计算可得;
h=2
h
=12.25
h=[(1+S
)h
+X
△
]
=[(1+0.0055)x2+0.75x0.14]
=2.116
=2.1
h=12.506
=12.5
(5)Ø2 、Ø6型芯径向尺寸计算
Ø2 、Ø6自由公差按MT3查得:Ø2、Ø6
,不需要转换,则根据公式:l
=[(1+S
)l
-X
△
]
计算可得;
l=[(1+S
)l
-X
△
]
=[(1+0.0055)x2+0.75x0.14]
=2.116
=2.1
l=6.168
=6.1
(6) 成型孔的高度。 4x Ø2以及 Ø6的成型芯是与凹模碰穿,所以高度应取正公差,便于修模。
(7)成型孔间距的计算
C=[(1+S)C
]±
=(1.0055X17)±0.003=17.0935±0.003=17.0
塑件凹模嵌件及型芯的成型尺寸的标准如下图
4. 成型零件尺寸及动模垫板厚度的计算
(1)凹模侧壁厚度的计算。 凹模侧壁厚度与型芯内压强及凹模的深度有关。其厚度根据公式计算。可得
S=()
=(
)
=57.51mm
其中, =25
=25x(0.45x18
+0.001x18)=25x0.820um=20.50um=0.020mm
凹模嵌件初定单边厚度选30mm,而壁厚不满足57.51mm要求,故凹模嵌件采用预应力的形式压入模板中,由模板和型腔共同承受型腔压力。由于型腔采用H型直线对称结构布置,型腔之间的壁厚为S1=80-27=53mm,由于是钱小型腔,间隔符合要求。初步估算模板平面尺寸选用200x200,比型腔布置尺寸大很多。完全符合强度和刚度要求。
(2) 动模垫板的厚度计算。动模垫板厚度与模架的两个垫块有跨度关系,根据前面型腔的布置。模架在200x200的范围内。查表7-4垫块之间跨度约为L=W-2W=(200-2X38)=124MM,根据型腔布置及型芯对动模垫板的压力可计算动模垫板厚度为
T=0.54L()
=0.54x124x(
)
=20.97mm
其中, =25
=25x(0.45x124
+0.001x124)=25x1.304um=32.60um=0.033mm
L是两个垫块之间的距离,约124mm;L1是动模垫板的长度,取200mm,A是4个型芯投影到动模垫板上的面积。
单个型芯所受压力的面积为 A1=axb=13.5x13.5=182.25mm
四个型芯的面积为 A=4XA1=730mm。
动模垫板按照标准厚度取25mm。
1.1.5脱模推出机构设计
本塑件结构简单,可采用推件板推出、推杆推出或两者综合推出方式,要根据脱模力计算来决定。
1.脱模力的计算
(1)Ø6型芯脱模力 因为λ==3/3=1<10,所以视为厚壁圆筒塑件,其脱模力为
F=
其中:K==
=
=0.9536
为脱模斜度,为1°
=d=2r
=2πrh
可以得出 444.5278218
F=
=299.68N
(2)Ø2型芯脱模力 参照(1)Ø6型芯脱模力的计算方法得到
F=
=34.745N
四个Ø2型芯的脱模力为 4 F=138.98N
(3)13.5*13.5矩形型芯脱模力 /t=27/3=9<10所以视为厚壁圆筒塑件,其脱模力为
F=
其中:K==
=
=0.9536
为脱模斜度,为1°
=(L+b)/2
=2(L+b)h
可以得出
F=
=60.15N
(4) 总脱模力 F= F+ F
+ F
=299.68+138.98+60.15=498.41N
2.推出方式的确定
1)采用推杆推出
(1)推出面积 设4MM的圆推杆设置8根,那么推出面积为
=
=2πX4x4=100.48MM
(2)推杆推出应力 查表取许可应力[σ]=12MPa
σ ==
=4.96<[σ]=12 故为合格
所以推出方式采用推杆推出。
1.1.6模架的确定
根据模具型腔的布局的中心距和凹模嵌件尺寸可算出凹模嵌件所占平面尺寸为110x80mm,型腔占平面尺寸为80x70,利用经验公式(7-1)进行计算,即W3=W+10=80+10=90,查表7-4得W=150,因此取150X150mm的模架。
1、各模板尺寸的确定
(1)A板尺寸 A板是定模型腔板,塑件高度为18mm,考虑到模板上要开冷却水道留有距离,故A板厚度为35mm。
(2)B板尺寸,B板是型芯固定板,按模架标准板件取30
(3)C板尺寸 垫块=推出行程+推板厚度+推杆固定板厚度+(5~10)mm=25+20+15+5~10=65~75,初选C为70mm
经上述尺寸计算,模架尺寸可以选择标记为:B3030-35X30X70/T12555-2006.
2、模架各尺寸的校核
根据所选注射机来校核模具设计的尺寸
经过校核模具平面尺寸、模具高度尺寸和开模行程都符合要求。
1.1.7排气槽的设计
塑件由于采用侧浇口进料熔体经塑件下方的台阶向上充满型腔,每个型芯上有两根或四根推杆,配合间隙可作为气体排出,不会出现顶部憋气现象。而且底面的气体沿着分型面、型芯之间的间隙排出间隙外。
1.1.8冷却系统的设计
这里只进行冷却系统的计算,忽略模具因空气对流、辐射以及注射机散发热量,按单位时间内塑料熔体凝固时所放出的热量等于冷却水所带走的热量。
1、冷却介质
ABS熔融温度和成型温度分别是195~240°C与38~93°C。设模具温度为40°C.可以用常温水进行冷却。
2、冷却系统的简单计算
1)单位时间内注入模具中的塑料熔体的总质量W
(1)塑料制品的体积
V=V主+V分+n V塑=1.573+1.365+4x26.338=111.228cm
(2)塑料制品的质量
M=Vρ=1.05x111.228=116.789g=0.1168kg
(3)塑件的壁厚为3mm,查得T冷=12.5s。取注射时间T注=2S,脱模时间为5.5S。则注射周期:T=T冷+T注+T脱=12.5+2+5.5=20s。
故每小时注射次数为N180次
(3) 单位时间内注入模具中的塑料熔体的总质量:
W=Nm=180x0.1168=21.03kg
2)确定单位质量的塑件在凝固时所放出的热量Q
查找ABS单位热流量Q的值得范围在(250~320)kj/kg,故取Q=300kj/kg。
3)计算冷却水道体积流量q
设冷却水道入水口的水温为22°c,出水的水温为25°c,取水的密度为ρ=1000kg/m,水道比热容C=4.187kj/kg·°c。Q=300kj/kg根据公式得:
q==5.61x10
m
/min
4)确定冷却水路的直径d
当q=.89x10 m
/min时,为了是冷去水处于川流状态时,取模具冷却水孔的直径d=8mm。
5)冷却水在管内的流速v,其中,q=5.61 x10 m
/min
V==1.86m/s>1.66 m/s.
6)求冷却管壁与水交界面的膜转热系数h
因为平均水温为23.5,查书的f=0.782,则
h==35489.68kj/(m
·h·°c)
7)计算冷却水通道的导热总面积A
A==
=0.0073 m
8)计算模具冷却水管的总长度L
L==0.0073/3.14x0.008=0.288mm
9)冷却水路的根数,设每条水路长度为200mm,则冷却水路的根数为
X==288/300=0.96根
有上述可知,一条冷却水道足够满足冷却。
1.1.9导向和定位结构的设计
注射模的导向机构用于动、定模之间的开合导向和脱模机构的运动想到。按作用分为外定位和模内定位。模外定位通过定位圈和注射机相配合,使模具的浇口套与注射机喷嘴精确定位。而模内定位机构通过导柱导套进行合模定位。本模具造型简单,故采用标准模架本身的定位机构。
参考文献
[1] 叶永新.王群.塑料成型工艺及模具设计[M].北京:机械工业出版社.2007