三、冶炼工艺
3.1 原料、燃料及辅助材料
3.1.1 原料
电锌系统所需硫化锌精矿主要依托于公司所属采选厂提供,不足部分外购解决,设计按照自产部分占全部锌精矿的60%,兰坪矿占30%,其它小矿点占10% 的方案组织。各种精矿的化学成分和混合矿的化学成分列于表3-1。电锌厂沸腾焙烧炉只能加工公司自产的硫化锌精矿,外购精矿委托加工成焙烧矿后运入电锌系统处理。年需混合精矿20369.51 t,其中自产部分为12221.71 t,品位48.50%;兰坪矿6110.85 t,品位52.07%;其它小矿点2036.95 t,品位50.00%。电锌系统年需焙烧矿17570.58 t,品位57.06%;其中自产精矿10556.11 t,品位55.59%;外购精矿委托加工后的焙烧矿量为7014.4 t,品位59.28%;混合的焙尘、焙砂及焙烧矿的物相组成分别列于表3-4至表3-6。
混合锌精矿化学成分(%) 表3-1
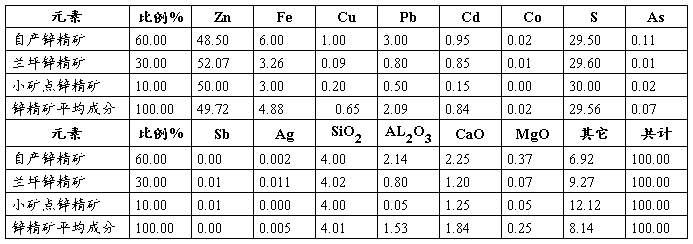
3.1.2 辅料和材料
除硫酸为自产外,其余的辅料和辅料全部外购。每年的需要量列于表3-2。
辅料和材料用量 表3-2
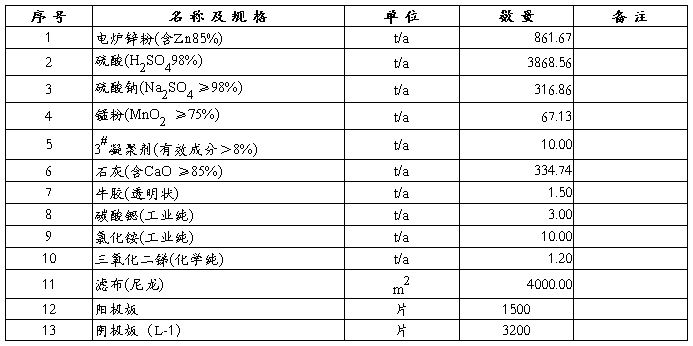
3.2 工艺流程
3.2.1 概述
电锌系统原设计采用常压酸浸,渣处理采用喷淋沉铁工艺,净液为先高温后低温,锌熔铸为反射炉。现生产实际工艺流程浸出为常压酸浸;渣处理采用高温高酸浸出沉矾工艺(沉矾前中和系在同一设备内进行);净化工艺不变;锌熔铸采用工频电炉;铜镉渣处理成海绵镉。经几年的生产调试,上述湿法炼锌工艺已为工人熟练掌握,流程畅通,指标较好。本次改造设计,按照公司提出的要求,依照原冶炼工艺流程进行,不作改动。
沸腾焙烧和硫酸生产不能满足改造后的电锌生产要求,为节省投资,本次设计不对其进行改造,生产所缺焙砂,由外购硫化锌精矿委托加工解决。
3.2.2 改造方案评述
⑴ 球磨上矿
现调浆磨矿系统采用人工上矿,即用人工将焙烧矿装卸在皮带机上,输送到调浆槽调浆的操作方式,存在劳动强度大、灰尘多、环境恶劣。本次改造拟采用气力输送,人工将焙烧矿送入真空吸送受料斗内,在抽风机造成的负压下,将焙烧矿吸入高位贮仓,含尘空气经袋式除尘器收尘后外排,高位贮仓中的焙烧矿经由贮仓下部的排料螺旋加到调浆槽内。采用真空吸送加螺旋给料的上矿方式,可减轻工人劳动强度,改善作业环境,有利于职工身体健康。
⑵ 浸出和渣处理
仍保持原有配置不变,仅适当增加浸出槽和浓密机,以达到改造后的电锌生产能力。
⑶ 净液和铜镉渣处理
仍采用先高温后低温的溶液净化流程。现铜镉渣处理与溶液净化配置于同一厂房内,高温和低温净液各有二台50 m3净化槽,经核算,其能力达不到10000t/a电锌的生产要求,设计拟将铜镉渣处理工序搬迁,空出场地新增二台50m3净化槽。在净液厂房和电解厂房之间的空地上新建一铜镉渣处理车间,铜镉渣调浆球磨设施仍在原地不动,调浆后的铜镉渣矿浆由泵扬送至铜镉渣浸出槽浸出处理,产出的铜渣和海绵镉堆存或外销,贫镉液则泵送到浸出工段。
⑷ 电解和电解熔铸
现电解和电解熔铸配置在同一厂房内。分二列的36个电解槽置于2.50m 平台上,熔锌电炉则设置于与电解槽相对的车间另一端。改造后电解槽总数增到62个,仍分二列设置,现有厂房只能布置电解槽和剥锌场地。设计拟将电锌熔铸设备搬迁至空置的防腐车间内,形成单独的锌熔铸车间和电锌锭库房。电锌片的运输使用平板轨道车。
采用上述改造方案,既充分利用了现有空置厂房和设施,节省改造投资,又为今后的发展留有余地。
3.3 主要技术操作条件
3.3.1 球磨调浆
液固比 3 ~ 4:1
3.3.2 中性浸出
液固比 10 ~ 11:1
浸出温度 60 ~ 65℃
浸出时间 1.0 ~ 2.0 h
浸出始酸 50 ~ 70 g/l
浸出终酸 PH 5.2 ~ 5.4
焙烧矿加入量 80 %
3.3.3 低酸浸出
浸出温度 70 ~ 75℃
浸出时间 1.0 ~ 2.0 h
浸出始酸 50 ~ 70 g/l
浸出终酸 15 g/l
3.3.4 高酸浸出
浸出温度 90 ~ 95℃
浸出时间 4.0 h
浸出始酸 90 ~ 100 g/l
浸出终酸 50 ~ 70 g/l
3.3.5 沉矾
沉矾温度 90 ~ 95℃
沉矾时间 5.0 h
终酸 PH 1.0 ~ 1.5
焙烧矿加入量 20 %
硫酸钠加入量 2 ~ 3 g/l
3.3.6 溶液净化
⑴ 一段高温净化
作业温度 85 ~ 90℃
作业时间 5.0 h
锌粉加入量 1.8 ~ 2.5 g/l
酸度 PH 5.2 ~ 5.4
⑵ 二段低温净化
作业温度 45 ~ 55℃
作业时间 5.0 h
锌粉加入量 1.0 ~ 1.5 g/l
酸度 PH 5.2 ~ 5.4
3.3.7 铜镉渣处理
⑴ 浆化及球磨
液固比 3:1,要求矿浆中大于60目的颗粒小于5 %。
⑵ 浸出
液固比 7 ~ 8:1
操作温度 80 ~ 85℃
始酸 70 ~ 80 g/l
终酸 PH 5.2 ~ 5.4
作业周期 10 ~ 12 h
⑶ 锌粉置换
作业温度 <50℃
酸度 0.3 ~ 0.5 g/l
锌粉量 12 ~ 15 g/l
作业周期 4 ~ 5 h
3.3.8 锌电解
新液含锌 130 g/l
废液含锌 51.64 g/l
废液含硫酸 146.2 g/l
电解温度 38 ~ 40℃
阴极电流密度 450 ~ 480 A/m2
电流效率 88 %
槽电压 3.2~3.4 v
同极距 62 mm
新液废液比例 1:12 ~ 15
清槽周期 30 ~ 40 d
3.3.9 锌熔铸
工频电炉熔池温度 480 ~ 540℃
锌液浇铸温度 470 ~ 480℃
氯化铵用量 0.85 ~ 1.0 kg/t.Zn
3.4 冶金计算
3.4.1 沸腾焙烧冶金计算
⑴ 计算过程主要选取的数据
金属回收率:99 %
主要金属、元素分配率:锌入烟尘为45%,入焙砂为55%:镉入烟尘为60%,入焙砂为40%。
烟尘中以硫化物形态存在的硫为0.5%,以硫酸盐形态存在的硫为2.14%。
焙砂中以硫化物形态存在的硫为0.30 %,以硫酸盐存在的硫为1.10 %。
⑵ 年处理硫化锌精矿(包括自己加工和外委加工)总量为20369.51 t,精矿物相组成列于表3-3。焙烧产出的烟尘和焙砂物相组成列于表3-4和表3-5。焙烧矿物相组成列于表3-6。
⑶ 年产焙烧矿17570.58 t,平均烧成率为87.13%;焙尘产出率为45.87%,焙砂产出率为54.13 %。沸腾焙烧年度物料平衡列于表3-7。
3.4.2 浸出及渣处理冶金计算
⑴ 焙烧矿分配率
中性浸出: 80 %
沉矾中和用:20 %
⑵ 主要有价金属浸出率
锌: 98 %
镉: 93 %
铜: 85 %
锌回收率: 97.12 %
⑶ 浸出过程中,金属损失率是以进入湿法系统的原料含金属为基准的。
⑷ 浸出和渣处理年度物料平衡计算列于表3-8。
浸出和渣处理酸平衡计算列于表3-9。
3.4.3熔液净化冶金计算
⑴ 主要计算指标
锌回收率: 99.5 %
锌粉消耗:电炉锌粉72.56 kg/t.Zn,电炉锌粉含Zn 85 %。
⑵ 净液年度物料平衡列于表3-10。
3.4.4 锌电解冶金计算
⑴ 主要计算指标
锌回收率: 99.8 %
阴极锌化学成分:Zn 99.99 %,Pb 0.005 %。
⑵ 锌电解年度金属平衡列于表3-11。
锌电解热平衡列于表3-12。
3.4.5 锌熔铸冶金计算
⑴主要计算指标
锌回收率: 99.6 %
锌直收率: 98.5 %
⑵ 锌熔铸年度金属平衡列于表3-13。
3.4.6 铜镉渣处理冶金计算
⑴ 主要计算指标
镉回收率: 99.70 %(指本车间)
镉总回收率: 91.50 %(从精矿到海绵镉)
铜渣产率 20.1 % (对铜镉渣)
铜回收率: 95 %(指本车间)
铜总回收率: 80 %(从精矿到铜渣)
⑵ 海绵镉含镉: 50 %
铜渣含铜: 20 %
第二篇:工艺设计报告格式
工艺设计报告