试模申请报告表
日期:20##年__月__日
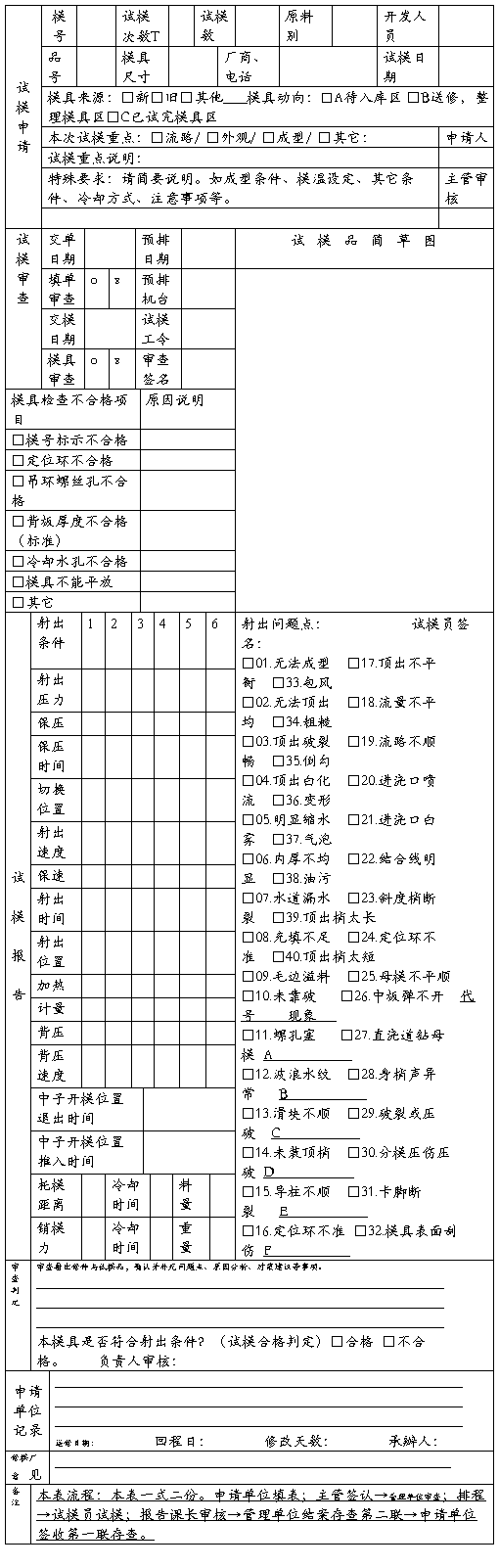
第二篇:试模
试模
当钳工完成模具装配后,即进行 当钳工完成模具装配后,即进行PSI PSI出厂检验,初步 出厂检验,初步检验模具是否有明显不符合设计要求的现象;例如某公 检验模具是否有明显不符合设计要求的现象;例如某公司的注塑模具出厂检查分为六大部分,即注塑成型系统、 司的注塑模具出厂检查分为六大部分,即注塑成型系统、滑块系统、顶出系统、热冷介质通路系统、定位系统和 滑块系统、顶出系统、热冷介质通路系统、定位系统和其它方面,这六个部分又可以分解为若干子项,每一个 其它方面,这六个部分又可以分解为若干子项,每一个子项都必须通过自检和复核等 子项都必须通过自检和复核等 PSI PSI之后即进行试模,完成后由试模人员填写 之后即进行试模,完成后由试模人员填写TIR TIR 试模问题报告,同时将问题纳入到 试模问题报告,同时将问题纳入到TIR TIR标准问题库范围 标准问题库范围分析,分析包括问题点、问题点描述、问题来源、修改 分析,分析包括问题点、问题点描述、问题来源、修改对策等。如果超出了问题库范围,就需要考虑是否对当 对策等。如果超出了问题库范围,就需要考虑是否对当前的问题库进行扩充 前的问题库进行扩充。。 1. 1. 塑料熔体未能顺利充填到远离浇口或截面较薄的型腔部位便 塑料熔体未能顺利充填到远离浇口或截面较薄的型腔部位便已冷凝固化,模腔欠充满。主要原因: 已冷凝固化,模腔欠充满。主要原因: ①①塑料熔体本身的流动黏度高,流动充填性不佳; 塑料熔体本身的流动黏度高,流动充填性不佳; ②②塑料熔体塑化质量差,塑化温度偏低,熔体温度不均,导致流动 塑料熔体塑化质量差,塑化温度偏低,熔体温度不均,导致流动性不良; 性不良; ③③模具温度过低或模温不均而局部温度过低; 模具温度过低或模温不均而局部温度过低; ④④熔体在模内的流程过长或流程过于复杂,充型阻力大,出现滞流; 熔体在模内的流程过长或流程过于复杂,充型阻力大,出现滞流; ⑤⑤喷嘴温度偏低且浇注系统冷料穴设置不当,前峰冷料进入模腔而 喷嘴温度偏低且浇注系统冷料穴设置不当,前峰冷料进入模腔而产生堵塞; 产生堵塞; ⑥⑥熔体充型时,模具排气不畅,导致熔体充型阻力增大; 熔体充型时,模具排气不畅,导致熔体充型阻力增大; ⑦⑦注射机实际注塑量太小,充型所需熔体不足,直接导致模腔缺料; 注射机实际注塑量太小,充型所需熔体不足,直接导致模腔缺料; ⑧⑧螺杆注射行程终了,塑化室内积存塑料过少,导致注射压力传递 螺杆注射行程终了,塑化室内积存塑料过少,导致注射压力传递不良,型腔熔体充型的后阶段动力不足; 不良,型腔熔体充型的后阶段动力不足; ⑨⑨注射机螺杆注射速率过低、注塑压力过小,熔体充型动力不足; 注射机螺杆注射速率过低、注塑压力过小,熔体充型动力不足; ⑩⑩制品壁厚不均或太薄,熔体充型阻力大,熔体温降过快。 制品壁厚不均或太薄,熔体充型阻力大,熔体温降过快。 22 在模腔内两股或多股熔体流的流动前沿汇合处所形成线状痕 在模腔内两股或多股熔体流的流动前沿汇合处所形成线状痕迹,称为熔接痕或熔接线。对熔接强度影响最大的是熔体汇合时 迹,称为熔接痕或熔接线。对熔接强度影响最大的是熔体汇合时的温度。在工程实际中,针对熔接缺陷常采用的方法: 的温度。在工程实际中,针对熔接缺陷常采用的方法:首先,尽可能提高熔接温度。适当提高熔体塑化温度、喷嘴 首先,尽可能提高熔接温度。适当提高熔体塑化温度、喷嘴温度、模具温度及嵌件预热温度;尽量缩短熔体汇合前的流动行 温度、模具温度及嵌件预热温度;尽量缩短熔体汇合前的流动行程或流动时间(有时不惜增加浇口数量);提高螺杆速率实现快 程或流动时间(有时不惜增加浇口数量);提高螺杆速率实现快速充模,以降低熔体在模内充填过程中的热量损失,同时快速充 速充模,以降低熔体在模内充填过程中的热量损失,同时快速充模也可增大熔体流动的剪切摩擦热弥补熔体的热量损失;优化浇 模也可增大熔体流动的剪切摩擦热弥补熔体的热量损失;优化浇注系统设计并配合以适当高的注射压力,增大熔体流动的剪切摩 注系统设计并配合以适当高的注射压力,增大熔体流动的剪切摩擦发热,改善熔体流动状态,增强熔体的汇合能力。 擦发热,改善熔体流动状态,增强熔体的汇合能力。其次,改变熔接痕位置,使其位于塑件上对制品力学性能与 其次,改变熔接痕位置,使其位于塑件上对制品力学性能与表观质量较不敏感的区域。优化浇口尺寸与位置;在不影响塑件 表观质量较不敏感的区域。优化浇口尺寸与位置;在不影响塑件使用要求的前提下改变塑件壁厚。 使用要求的前提下改变塑件壁厚。在模具设计时,尽量减少浇口数量;合理设计冷料穴;在熔 在模具设计时,尽量减少浇口数量;合理设计冷料穴;在熔接痕出现位置合理设计模具的排气措施;尽量少用脱模剂;对原 接痕出现位置合理设计模具的排气措施;尽量少用脱模剂;对原料进行良好干燥。 料进行良好干燥。 3. 3. 缩痕与缩孔均是由于注塑制品的厚壁部位因成型收缩且得不 缩痕与缩孔均是由于注塑制品的厚壁部位因成型收缩且得不到后续熔料的足够补偿而表现出的制品收缩缺陷。注射成型过程 到后续熔料的足够补偿而表现出的制品收缩缺陷。注射成型过程中,总是制品的表层先凝固而中心层后凝固。将导致制品厚壁部 中,总是制品的表层先凝固而中心层后凝固。将导致制品厚壁部位表层塌陷,从而在制品表面产生明显的内凹,内凹较小时称为 位表层塌陷,从而在制品表面产生明显的内凹,内凹较小时称为缩痕,内凹较大时称为凹陷;反之,当制品壁厚处已凝固,表层 缩痕,内凹较大时称为凹陷;反之,当制品壁厚处已凝固,表层的强度、刚度足以抵抗其心部后续收缩而产生的收缩应力的时候, 的强度、刚度足以抵抗其心部后续收缩而产生的收缩应力的时候,将在厚壁部位的材料内部产生一个大的缩孔或形成一系列的微小 将在厚壁部位的材料内部产生一个大的缩孔或形成一系列的微小缩孔。通常当制品出现缩孔的时候,多少都会伴随有表面凹陷痕 缩孔。通常当制品出现缩孔的时候,多少都会伴随有表面凹陷痕迹。 迹。具体解决方案如下: 具体解决方案如下: ①①优化注塑制品结构设计。注塑制品壁厚设计不能太厚,必要时可 优化注塑制品结构设计。注塑制品壁厚设计不能太厚,必要时可通过增设加强筋等方法以减少制品壁厚;尽量保证制品壁厚的均 通过增设加强筋等方法以减少制品壁厚;尽量保证制品壁厚的均匀性,可利用增设加强肋等方法增大流动截面,以利补缩。 匀性,可利用增设加强肋等方法增大流动截面,以利补缩。 ②②优化塑料配方尽量选用收缩率低的树脂;减少再生料的用量;加 优化塑料配方尽量选用收缩率低的树脂;减少再生料的用量;加强物料的干燥;适量添加润滑助剂以改善熔体流动性。 强物料的干燥;适量添加润滑助剂以改善熔体流动性。 ③③优化注塑工艺条件。适当提高注射及保压压力与注射速率以增加 优化注塑工艺条件。适当提高注射及保压压力与注射速率以增加熔体的压缩紧密度;延长注射与保压时间以充分实现补缩;适当 熔体的压缩紧密度;延长注射与保压时间以充分实现补缩;适当降低熔体温度,适当调高模具温度;可采用气辅注射成型。 降低熔体温度,适当调高模具温度;可采用气辅注射成型。 ④④优化模具设计。适当增大浇口及流道截面尺寸;浇口位置设置在 优化模具设计。适当增大浇口及流道截面尺寸;浇口位置设置在塑件厚壁处;改善模具排气条件;设置足够容量的冷料穴,以免 塑件厚壁处;改善模具排气条件;设置足够容量的冷料穴,以免冷料进入模腔影响充模补缩;合理布置冷却水道,在保持模腔各 冷料进入模腔影响充模补缩;合理布置冷却水道,在保持模腔各部位均匀冷却的基础上,对凹陷的厚壁部位适当强化冷却以实现 部位均匀冷却的基础上,对凹陷的厚壁部位适当强化冷却以实现有效补缩;应认真分析熔体在模腔内的流动通道上有无“瓶颈” 有效补缩;应认真分析熔体在模腔内的流动通道上有无“瓶颈” 部位,否则应更换浇口位置或增设浇口数量,必要时增大模腔瓶 部位,否则应更换浇口位置或增设浇口数量,必要时增大模腔瓶颈部位的流道截面;对厚壁制品,可考虑采用扇形浇口或平缝浇 颈部位的流道截面;对厚壁制品,可考虑采用扇形浇口或平缝浇口,从而将注塑制品可能出现的凹陷及缩孔转移到浇口上。 口,从而将注塑制品可能出现的凹陷及缩孔转移到浇口上。 4. 4. 流痕是塑件上在浇口附近出现的明显熔体流动状痕迹,有时 流痕是塑件上在浇口附近出现的明显熔体流动状痕迹,有时也称为流纹。流痕既影响塑件的表面质量,也影响塑件的机械力 也称为流纹。流痕既影响塑件的表面质量,也影响塑件的机械力学性能等。 学性能等。 ①①喷射状流痕。当熔体以过高的注射速率进入截面较大的厚壁模腔 喷射状流痕。当熔体以过高的注射速率进入截面较大的厚壁模腔时形成的蛇形喷射流。处理措施包括优化浇口位置和浇口的形式 时形成的蛇形喷射流。处理措施包括优化浇口位置和浇口的形式与尺寸,以增大浇口处熔体与模具型腔表壁的接触、降低熔体剪 与尺寸,以增大浇口处熔体与模具型腔表壁的接触、降低熔体剪切速率和剪切应力;降低螺杆注塑速率,避免熔体注射入模腔的 切速率和剪切应力;降低螺杆注塑速率,避免熔体注射入模腔的速率过高。如采用搭接式浇口、护耳式浇口、扇形浇口等。 速率过高。如采用搭接式浇口、护耳式浇口、扇形浇口等。 ②②轮状波流痕。当流动状态不良的熔体经流道及浇口以半固化状态 轮状波流痕。当流动状态不良的熔体经流道及浇口以半固化状态注射入模具型腔后,在沿模腔流动时被不断注入的后续熔体挤压 注射入模具型腔后,在沿模腔流动时被不断注入的后续熔体挤压推动形成回流及滞流,从而在塑件表面产生以浇口为中心的轮状 推动形成回流及滞流,从而在塑件表面产生以浇口为中心的轮状波流痕。处理措施包括提高模具温度及喷嘴温度,提高注射速率, 波流痕。处理措施包括提高模具温度及喷嘴温度,提高注射速率,增大注射压力及保压时间,合理设计冷料穴大小及位置,优化浇 增大注射压力及保压时间,合理设计冷料穴大小及位置,优化浇注系统设计以利用熔体流动充填时的剪切热来改善熔体流动不良 注系统设计以利用熔体流动充填时的剪切热来改善熔体流动不良的状态。 的状态。 ③③湍流状流痕。当熔体从截面狭小的流道流入较大截面的型腔或者 湍流状流痕。当熔体从截面狭小的流道流入较大截面的型腔或者流道狭窄、表面粗糙度很差时,熔体在流道(含模腔)内形成湍 流道狭窄、表面粗糙度很差时,熔体在流道(含模腔)内形成湍流,从而导致在塑件表面形成湍流状流痕。处理措施包括适当降 流,从而导致在塑件表面形成湍流状流痕。处理措施包括适当降低螺杆注射速率或采用分级注射加以控制;在塑件的厚壁部位及 低螺杆注射速率或采用分级注射加以控制;在塑件的厚壁部位及塑件侧壁开设浇口,浇口的类型应有利于熔体平缓地进入模腔, 塑件侧壁开设浇口,浇口的类型应有利于熔体平缓地进入模腔,如采用护耳浇口、扇形浇口、薄片式浇口等;有时可适当增大流 如采用护耳浇口、扇形浇口、薄片式浇口等;有时可适当增大流道及浇口截面尺寸以减小熔体流动阻力;必要时可优化塑件结构, 道及浇口截面尺寸以减小熔体流动阻力;必要时可优化塑件结构,避免壁厚不均以防止熔体在模腔内从狭小截面流入厚大截面处; 避免壁厚不均以防止熔体在模腔内从狭小截面流入厚大截面处;另外,可采用增大模具温度、提高料筒及喷嘴温度以改善熔体的 另外,可采用增大模具温度、提高料筒及喷嘴温度以改善熔体的流动特性。 流动特性。 ④④云雾状流痕。当熔体中的树脂及润滑剂等在加工温度下产生的挥 云雾状流痕。当熔体中的树脂及润滑剂等在加工温度下产生的挥发性气体时,其积存于熔体流与模腔表壁之间,干扰熔体的流动 发性气体时,其积存于熔体流与模腔表壁之间,干扰熔体的流动而形成云雾状流痕。对此应采取的措施是:改善模具的排气条件; 而形成云雾状流痕。对此应采取的措施是:改善模具的排气条件;适当增大浇口尺寸、降低熔体充模速率;适当降低模具及熔体塑 适当增大浇口尺寸、降低熔体充模速率;适当降低模具及熔体塑化温度;考虑更换润滑剂等易产生挥发性气体的助剂。 化温度;考虑更换润滑剂等易产生挥发性气体的助剂。 5. 5. 银纹是注塑制品表面或近表面,沿熔体流动方向出现的银白 银纹是注塑制品表面或近表面,沿熔体流动方向出现的银白色丝状斑纹。银纹是由于树脂中的气体移动积存到熔体与模腔表 色丝状斑纹。银纹是由于树脂中的气体移动积存到熔体与模腔表壁之间并被压碎而产生的现象,有时也称云母痕、银丝、银斑等。 壁之间并被压碎而产生的现象,有时也称云母痕、银丝、银斑等。产生银纹的最主要原因是熔体中含有易挥发的气体。对此可采取 产生银纹的最主要原因是熔体中含有易挥发的气体。对此可采取以下措施。 以下措施。 ①①在原料方面。针对降解气银纹,要求尽量选用粒度均匀的树脂, 在原料方面。针对降解气银纹,要求尽量选用粒度均匀的树脂,减少再生料的用量,及时清除料筒内残存的异料,必要时更换塑 减少再生料的用量,及时清除料筒内残存的异料,必要时更换塑料中易产生分解的助剂如润滑剂等;针对水气银纹,应严格干燥 料中易产生分解的助剂如润滑剂等;针对水气银纹,应严格干燥塑料原料,提高螺杆的塑化背压。 塑料原料,提高螺杆的塑化背压。 ②②在成型工艺方面。针对降解银纹,应降低料筒与喷嘴温度,缩短 在成型工艺方面。针对降解银纹,应降低料筒与喷嘴温度,缩短熔体在料筒中的滞留时间,防止熔体局部过热温升,适当降低塑 熔体在料筒中的滞留时间,防止熔体局部过热温升,适当降低塑化与注塑的压力以避免高压下的物料高温现象;对于水气银纹, 化与注塑的压力以避免高压下的物料高温现象;对于水气银纹,可适当调高塑化压力,加大螺杆压缩比,降低螺杆转速,采用排 可适当调高塑化压力,加大螺杆压缩比,降低螺杆转速,采用排气型料筒与螺杆。 气型料筒与螺杆。 ③③在模具设计与注塑操作方面。针对降解银纹,应适当加大主流道、 在模具设计与注塑操作方面。针对降解银纹,应适当加大主流道、分流道及浇口截面尺寸,降低熔体剪切速率,增大冷料穴空间, 分流道及浇口截面尺寸,降低熔体剪切速率,增大冷料穴空间,改善模具的排气条件;对于水气银纹,应增设模具排气通道,检 改善模具的排气条件;对于水气银纹,应增设模具排气通道,检查模具冷却水道是否渗漏及模具型腔表壁是否附有水分。 查模具冷却水道是否渗漏及模具型腔表壁是否附有水分。 6. 6. ①①在注塑原料方面。原料含水过重,原料中易产生分解气的助剂、再生料等,均 在注塑原料方面。原料含水过重,原料中易产生分解气的助剂、再生料等,均会形成气源。因此,应对塑料原料严格干燥,注射机选用排气型料筒;尽量 会形成气源。因此,应对塑料原料严格干燥,注射机选用排气型料筒;尽量减少或更换塑料原料中易分解的助剂,以及减少残留料或再生料的应用。 减少或更换塑料原料中易分解的助剂,以及减少残留料或再生料的应用。 ②②在成型工艺方面。料温与模温控制不当,注射速度过快,注射压力太低,注射 在成型工艺方面。料温与模温控制不当,注射速度过快,注射压力太低,注射量过多或过少,保压不足,冷却不均或不足等均会导致在塑件上产生气泡或 量过多或过少,保压不足,冷却不均或不足等均会导致在塑件上产生气泡或气穴。因此,应适当降低熔体的注射速率,保证模腔内的气体能有充分的时 气穴。因此,应适当降低熔体的注射速率,保证模腔内的气体能有充分的时间排除;适当提高注射压力与模具温度,保持模腔内合理的成型压力,适当 间排除;适当提高注射压力与模具温度,保持模腔内合理的成型压力,适当延长保压时间;注射用量适当;加强均匀冷却的效果;提高注射机料筒预热 延长保压时间;注射用量适当;加强均匀冷却的效果;提高注射机料筒预热段的温度;适当降低塑料熔体温度及在高温段积存的时间,避免引发降解而 §§段的温度;适当降低塑料熔体温度及在高温段积存的时间,避免引发降解而产生分解气。 产生分解气。 ③③在制品结构与模具设计方面。优化模具排气方案,尤其是在模腔内塑料熔 在制品结构与模具设计方面。优化模具排气方案,尤其是在模腔内塑料熔体前峰料汇合处应设置排气通道;通过制品结构与模具浇注系统(特别是浇 体前峰料汇合处应设置排气通道;通过制品结构与模具浇注系统(特别是浇口位置及浇口截面大小)的优化设计,浇口开设在塑件的厚壁处,浇口的截 口位置及浇口截面大小)的优化设计,浇口开设在塑件的厚壁处,浇口的截面形状与尺寸应与塑件的质量成适应,实现塑料熔体在模内合理化流动,使 面形状与尺寸应与塑件的质量成适应,实现塑料熔体在模内合理化流动,使受熔体填充挤压的气体,在其受挤压过程中特别是在熔体最后汇合处,能通 受熔体填充挤压的气体,在其受挤压过程中特别是在熔体最后汇合处,能通过良好的排气措施顺利排除。 过良好的排气措施顺利排除。 7. 7. 塑料熔体在注射充填过程中,进入与模具型腔结构相关的分型面间隙、 塑料熔体在注射充填过程中,进入与模具型腔结构相关的分型面间隙、滑块滑配面间隙、镶件配合缝隙、推杆孔隙等部位,发生溢料。主要原因: 滑块滑配面间隙、镶件配合缝隙、推杆孔隙等部位,发生溢料。主要原因: ①①锁模力不足。 锁模力不足。 ②②锁模不平衡及锁模力波动。 锁模不平衡及锁模力波动。 ③③塑料原料黏度过低或过高。熔体黏度过低,即使模具配合缝隙设计精度高,也 塑料原料黏度过低或过高。熔体黏度过低,即使模具配合缝隙设计精度高,也会增加飞边形成的可能性;而熔体黏度过高,熔体流动充填阻力增大,会导 会增加飞边形成的可能性;而熔体黏度过高,熔体流动充填阻力增大,会导致模腔内成型压力升高,从而会因锁模力不足而形成飞边。 致模腔内成型压力升高,从而会因锁模力不足而形成飞边。 ④④注射压力过高、注射速率过快、模具浇口截面尺寸过小,料筒温度、喷嘴温度 注射压力过高、注射速率过快、模具浇口截面尺寸过小,料筒温度、喷嘴温度及模具温度过高,导致熔体的实际流动黏度偏低。 及模具温度过高,导致熔体的实际流动黏度偏低。 ⑤⑤模具型腔的开设位置过偏,从而使注塑时模具发生单边张力,而形成飞边。 模具型腔的开设位置过偏,从而使注塑时模具发生单边张力,而形成飞边。 ⑥⑥与模具型腔相关的零件因变形、磨损、分型面上存在异物,或者模具活动或固 与模具型腔相关的零件因变形、磨损、分型面上存在异物,或者模具活动或固定部位缝隙的设计精度偏低、加工装配不良,出现配合部位间隙过大。 定部位缝隙的设计精度偏低、加工装配不良,出现配合部位间隙过大。 ⑦⑦模具排气间隙过大、过深。 模具排气间隙过大、过深。 8. 8. 制品表面光泽度不均,甚至阴影等现象。形成原因包括: 制品表面光泽度不均,甚至阴影等现象。形成原因包括: ①①塑料原料干燥处理不充分,原料挥发性太强,原料中有异物,树 塑料原料干燥处理不充分,原料挥发性太强,原料中有异物,树脂本身光泽性不够很好,助剂对光泽度有不良影响; 脂本身光泽性不够很好,助剂对光泽度有不良影响; ②②熔体塑化质量不佳,熔料温度太低,注射量不足,模温偏低,脱 熔体塑化质量不佳,熔料温度太低,注射量不足,模温偏低,脱模剂使用过量; 模剂使用过量; ③③浇口及流道截面过小,浇口位置不合理,熔体在模内的流动状态 浇口及流道截面过小,浇口位置不合理,熔体在模内的流动状态不佳; 不佳; ④④模具未设冷料穴,排气不良,模腔表壁依附有水分,模腔表面不 模具未设冷料穴,排气不良,模腔表壁依附有水分,模腔表面不光滑。 光滑。 9. 9. 色差是制品颜色不均,出现色彩差异。形成原因包括: 色差是制品颜色不均,出现色彩差异。形成原因包括: ①①原料被污染; 原料被污染; ②②色料分布不均; 色料分布不均; ③③色料不稳定; 色料不稳定; ④④材料降解; 材料降解; ⑤⑤脱模剂用量过大。 脱模剂用量过大。解决方案包括: 解决方案包括: ①①提高原料的纯净性,减少原料中挥发性助剂的用量,严格干燥。 提高原料的纯净性,减少原料中挥发性助剂的用量,严格干燥。 ②②提高材料与色料的热稳定性,增强色料的分散性。 提高材料与色料的热稳定性,增强色料的分散性。 ③③检查热电偶、温控仪及加热系统等温控部分是否失调、失灵;降 检查热电偶、温控仪及加热系统等温控部分是否失调、失灵;降低熔体塑化温度。 低熔体塑化温度。 ④④优化塑化螺杆结构,适当降低螺杆转速及塑化压力,提高熔体的 优化塑化螺杆结构,适当降低螺杆转速及塑化压力,提高熔体的塑化质量。 塑化质量。 ⑤⑤减少料筒前端塑化室内的熔体积存量。 减少料筒前端塑化室内的熔体积存量。 ⑥⑥适当降低注射压力与螺杆注射速率。 适当降低注射压力与螺杆注射速率。 ⑦⑦优化浇注系统设计,适当增大喷嘴、流道及浇口尺寸,降低熔体 优化浇注系统设计,适当增大喷嘴、流道及浇口尺寸,降低熔体剪切流动速率。 剪切流动速率。 ⑧⑧适当减少脱模剂使用量。 适当减少脱模剂使用量。 10. 10. 制品表面的色调正常,但偶尔出现黑色的斑点与条纹。 制品表面的色调正常,但偶尔出现黑色的斑点与条纹。根本 根本原因是由于各种因素引发的材料热降解或杂质碳化等。原料中混 原因是由于各种因素引发的材料热降解或杂质碳化等。原料中混有杂质,料筒内有材料分解的残留物;塑料塑化不良致使熔体在 有杂质,料筒内有材料分解的残留物;塑料塑化不良致使熔体在料筒内出现过热或局部过热;注射速率太快、浇口截面过小等引 料筒内出现过热或局部过热;注射速率太快、浇口截面过小等引起塑料过度剪切;模具成型零件表面不光滑,熔体流经此处被拉 起塑料过度剪切;模具成型零件表面不光滑,熔体流经此处被拉伤;排气不良导致气体积存于模内并受到压缩而温度升高,使气 伤;排气不良导致气体积存于模内并受到压缩而温度升高,使气团周围的塑料发生碳化等。解决方案: 团周围的塑料发生碳化等。解决方案: ①①减少塑料再生料的添加量,加强料筒内及模具型腔内残留物的清 减少塑料再生料的添加量,加强料筒内及模具型腔内残留物的清除,避免杂质混入原料中。 除,避免杂质混入原料中。 ②②物料严格干燥,减少原料中易挥发成分的含量,改善热稳定性。 物料严格干燥,减少原料中易挥发成分的含量,改善热稳定性。 ③③优化螺杆结构,降低塑化压力与螺杆的剪切速率,缩短熔体在料 优化螺杆结构,降低塑化压力与螺杆的剪切速率,缩短熔体在料筒塑化室内的积存时间,适当降低熔体塑化温度。 筒塑化室内的积存时间,适当降低熔体塑化温度。 ④④降低螺杆注射速率、增大喷嘴及浇口截面尺寸,以避免因熔体剪 降低螺杆注射速率、增大喷嘴及浇口截面尺寸,以避免因熔体剪切流动太快而引发降解。 切流动太快而引发降解。 ⑤⑤改善模具排气条件,优化排气方案。 改善模具排气条件,优化排气方案。 ⑥⑥降低成型零件表面的粗糙程度,增大脱模斜度。 降低成型零件表面的粗糙程度,增大脱模斜度。 11. 11. 主流道凝料粘在模具主流道内,脱模困难。形成原因是由于 主流道凝料粘在模具主流道内,脱模困难。形成原因是由于注射压力太高,主流道冷却不足,主流道脱模斜度太小,主流道 注射压力太高,主流道冷却不足,主流道脱模斜度太小,主流道衬套与喷嘴的配合设计不正确,模具安装不良,脱流道凝料的装 衬套与喷嘴的配合设计不正确,模具安装不良,脱流道凝料的装置(拉料杆或冷料穴等)设计不正确,脱模剂用量不足等。 置(拉料杆或冷料穴等)设计不正确,脱模剂用量不足等。解决方案: 解决方案: ①①适当降低注射压力和注塑用量; 适当降低注射压力和注塑用量; ②②加强对模具主流道的冷却; 加强对模具主流道的冷却; ③③根据注射机喷嘴球半径合理设计主流道衬套外端球面凹穴的尺寸; 根据注射机喷嘴球半径合理设计主流道衬套外端球面凹穴的尺寸; ④④正确设计模具定位圈尺寸,并确保装模时注射机喷嘴中心线与注 正确设计模具定位圈尺寸,并确保装模时注射机喷嘴中心线与注塑模主流道中心线一致; 塑模主流道中心线一致; ⑤⑤增大主流道的脱模斜度; 增大主流道的脱模斜度; ⑥⑥正确设计脱流道凝料的拉料杆或冷料穴; 正确设计脱流道凝料的拉料杆或冷料穴; ⑦⑦保证主流道内表面光洁,其内表面的加工迹线应顺着主流道凝料 保证主流道内表面光洁,其内表面的加工迹线应顺着主流道凝料的脱模方向; 的脱模方向; ⑧⑧适当增加脱模剂的使用量。 适当增加脱模剂的使用量。 12. 12. 注塑件粘在模内,难以顺利脱模。形成原因包括: 注塑件粘在模内,难以顺利脱模。形成原因包括: ①①注射料过多。 注射料过多。 ②②注射压力太高,保压压力过大与保压时间太长。 注射压力太高,保压压力过大与保压时间太长。 ③③熔体温度太高。 熔体温度太高。 ④④模具温度过低或过高。 模具温度过低或过高。 ⑤⑤塑件脱模斜度设计不当。 塑件脱模斜度设计不当。 ⑥⑥脱模机构设计不合理,推出位置不当,推杆数量偏少,推出力过 脱模机构设计不合理,推出位置不当,推杆数量偏少,推出力过小;模芯无进气装置,造成制品脱模时形成真空。 小;模芯无进气装置,造成制品脱模时形成真空。 ⑦⑦模具型腔成型表面粗糙。 模具型腔成型表面粗糙。 ⑧⑧脱模剂用量不足或喷涂不当。 脱模剂用量不足或喷涂不当。 13. 13. 制品在脱模过程中,塑件上与推杆接触部位被顶发白的现象。 制品在脱模过程中,塑件上与推杆接触部位被顶发白的现象。制品在使用过程中,顶白处极易产生裂纹。形成原因包括: 制品在使用过程中,顶白处极易产生裂纹。形成原因包括: ①①注射压力太高,注射速度太快,保压时间太长,模温太低,制品 注射压力太高,注射速度太快,保压时间太长,模温太低,制品在模内的冷却速度太快及制品冷却不均,致使制品内应力增大; 在模内的冷却速度太快及制品冷却不均,致使制品内应力增大; ②②制品脱模斜度太小,脱模剂喷涂不当或不足,制品脱模阻力太大; 制品脱模斜度太小,脱模剂喷涂不当或不足,制品脱模阻力太大; ③③模具推出机构设计不合理,推出速度太快,致使塑件与推出零件 模具推出机构设计不合理,推出速度太快,致使塑件与推出零件(主要针对推杆或推管)接触处形成较大的推出应力; (主要针对推杆或推管)接触处形成较大的推出应力; ④④制品结构设计不合理。 制品结构设计不合理。 14. 14. ①①避免熔体注射过量。 避免熔体注射过量。 ②②降低注射速率,优化浇注系统设计,实现熔体良好的充模状态。 降低注射速率,优化浇注系统设计,实现熔体良好的充模状态。 ③③降低注射压力及保压压力,缩短保压时间。 降低注射压力及保压压力,缩短保压时间。 ④④适当提高模具温度,降低冷却速度,延长模内冷却时间,优化模 适当提高模具温度,降低冷却速度,延长模内冷却时间,优化模温控制系统与制品结构关系,力求实现制品在模内均匀冷却。 温控制系统与制品结构关系,力求实现制品在模内均匀冷却。 ⑤⑤保证塑件合理留模方式的同时,增大脱模斜度,减小脱模阻力。 保证塑件合理留模方式的同时,增大脱模斜度,减小脱模阻力。 ⑥⑥根据塑件结构特征,选用恰当的推出方式,合理设置推杆位置, 根据塑件结构特征,选用恰当的推出方式,合理设置推杆位置,力求推出平衡;这样可避免制品在脱模时产生变形。 力求推出平衡;这样可避免制品在脱模时产生变形。 ⑦⑦增大模腔表面的光洁度,成型零件在打磨抛光的最后阶段,应顺 增大模腔表面的光洁度,成型零件在打磨抛光的最后阶段,应顺着塑件脱模的方向进行打磨抛光,降低塑件的脱模阻力。 着塑件脱模的方向进行打磨抛光,降低塑件的脱模阻力。 ⑧⑧在制品结构上尽量避免或减少壁厚不均的情况。 在制品结构上尽量避免或减少壁厚不均的情况。 ⑨⑨对重要塑件,为了减少残余内应力对制品形状尺寸精度的影响, 对重要塑件,为了减少残余内应力对制品形状尺寸精度的影响,可在塑件脱模后及时进行后处理。 可在塑件脱模后及时进行后处理。 ⑩⑩当制品出现较大变形时,通常保压压力的过程优化,即通过分段 当制品出现较大变形时,通常保压压力的过程优化,即通过分段分级保压,可以极大地减轻制品翘曲等变形。 分级保压,可以极大地减轻制品翘曲等变形。 5.4 TVR 5.4 TVR 模具检验报告 模具检验报告TVR TVR基于试模获得的成品,通过对它的测量来 基于试模获得的成品,通过对它的测量来判别对应的模具是否达到要求 判别对应的模具是否达到要求TVR TVR的内容包括很多项,最基本是 的内容包括很多项,最基本是塑件关键尺寸及公差检验,不同的企业可制定相应的评判标准。 塑件关键尺寸及公差检验,不同的企业可制定相应的评判标准。典型的 典型的TVR TVR工作步骤如下: 工作步骤如下: ①①确定被检验项目的图纸位置、公称尺寸及其上偏差和下偏差; 确定被检验项目的图纸位置、公称尺寸及其上偏差和下偏差; ②②确定检验方法。企业可根据自身条件确定若干种检验方法; 确定检验方法。企业可根据自身条件确定若干种检验方法; ③③确定检验的样件数量及其尺寸; 确定检验的样件数量及其尺寸; ④④分别计算中间尺寸及其上偏差和下偏差,计算尺寸公式如下: 分别计算中间尺寸及其上偏差和下偏差,计算尺寸公式如下: 2 0 0 0 式中: D= -- 2 0 0 dTol uTol dTol m =- 2 0 0 dTol uTol uTol m = ++dTol uTol D D m m :中间尺寸。 uTol m ,dTol m :基于中间尺寸的上偏差和下偏差。 D 0 :公称尺寸。 uTol 0 ,dTol 0 :基于公称尺寸的上偏差和下偏差。 ⑤⑤计算样件尺寸对应于中间尺寸的上、下偏差率,计算公式如下: 计算样件尺寸对应于中间尺寸的上、下偏差率,计算公式如下: m m min 式中: 式中: uF uF:样件的上偏差率。 :样件的上偏差率。 dF=- max m m dTol D D dF =-uTol D D uF dF:样件的下偏差率。 :样件的下偏差率。 DD max max :最大样件尺寸。 :最大样件尺寸。 DD min min :最小样件尺寸。 :最小样件尺寸。 ⑥⑥检测结论。企业依实际情况设置检测的评判标准,并且据此得出 检测结论。企业依实际情况设置检测的评判标准,并且据此得出检测结论为合格还是不合格。 检测结论为合格还是不合格。根据试模人员完成的 根据试模人员完成的TIR TIR和质量检验部门完成的 和质量检验部门完成的TVR TVR报告, 报告,可以制订 可以制订MPI MPI模具修改指导书, 模具修改指导书,MPI MPI应包括以下几个方面: 应包括以下几个方面: ①①模号和试模序号。 模号和试模序号。 ②②问题点描述。 问题点描述。 ③③零件编号 零件编号((含模穴号 含模穴号))。。 ④④修模对策。 修模对策。 ⑤⑤修模部门。 修模部门。 ⑥⑥TVR TVR对应尺寸及当前状况。 对应尺寸及当前状况。工厂根据 工厂根据MPI MPI的问题点描述和相应的解决方案组织修模,过 的问题点描述和相应的解决方案组织修模,过程中可能涉及到安排新的机加工工序和打光等钳工工序,甚至如 程中可能涉及到安排新的机加工工序和打光等钳工工序,甚至如果某个模具零件报废,需要准备新的物料替代报废件,重新加工, 果某个模具零件报废,需要准备新的物料替代报废件,重新加工,称为重工操作。零部件加工操作完成后,由钳工重新进行装配, 称为重工操作。零部件加工操作完成后,由钳工重新进行装配,然后再次准备试模过程。 然后再次准备试模过程。