中国化工集团油气公司
昌邑石化分公司
500万吨/年常减压蒸馏装置
标定报告
中国化工油气昌邑分公司生产技术部
中国化工油气昌邑分公司运行一部
20##年10月
目录
1. 概述. 1
1.1 装置概况. 1
1.2主要改造工作说明. 1
1.2.1初馏塔系统. 1
1.2.2常压塔系统. 2
1.2.3加热炉系统. 2
1.3本次改造核算. 2
1.4本装置主要组成. 2
2.工艺流程简述. 2
3 .装置开工运转与标定. 8
3.1 标定期间数据与分析. 8
3.2标定结果. 13
3.2.1 原油加工量. 13
3.2.2 轻收及总拔. 13
3.2.3 产品质量. 14
3.2.4 装置能耗. 15
3.2.5 塔系统. 15
3.2.6 换热网络. 16
3.2.7 机泵. 16
3.2.8 加热炉. 16
3.2.9装置防腐. 17
3.2.10 环境保护. 17
4.存在的问题及建议. 17
5.结论. 18
1. 概述
1.1 装置概况
山东昌邑石化有限公司500×104t/a 常减压蒸馏装置,系公司重交沥青装置能量系统优化改造项目核心装置,总投资7.6亿元,装置投资5.4亿元,占地15000m2。由西安长庆科技工程有限责任公司设计,山东环海石化工程建设公司和山东宏扬石化工程公司等公司承建,于20##年5月开工建设,于20##年5月建成投产运行。
装置原设计加工混合重质含硫原料油,处理量为500万吨/年,设计年开工时间为8000小时,为燃料型装置。但随着企业的持续性发展, 加工规模的继续扩大, 以及原油品种的日益多样化, 装置难以适应加工轻质原油的变化情况。
装置于20##年08月,在原装置的基础上,进行了第一次挖潜改造,充分利用已有设备和成熟的工艺,最大限度地减少改造工程量及投资,使其轻油加工能力提升至450万吨/年,尽可能降低生产成本,确保装置安全运行。改造后的装置增加了初馏塔系统,旧闪蒸塔T1001改造成初馏塔,装填8.8m高的规整填料及气液分布器等塔内件;增加一台初馏塔回流罐V1026;新增初顶回流泵P1032AB二台,初侧泵P1033AB二台; 新增初顶油气后冷却器E1033一台。通过初馏系统对混合油进行拔头,对初馏塔提压(约0.1Mpa),将轻烃送至催化装置压缩机入口进行回收。改造后主要问题在于:(1)加热炉炉膛负荷过大 (2)常顶压力高,分馏效果差(3)减顶温度高,真空度低(4)换热效果较差。
于20##年7月装置检修期间针对存在的问题对现有装置进行第二次扩能技术改造。
1.2主要改造工作说明
1.2.1初馏塔系统
由于本次改造调整了换热流程,初馏塔气液负荷增加较大,因此本次改造更换初馏塔(规格为Ø3600/Ø4000×42055),由填料塔更换为板式塔。增加空冷8台,初顶后冷器1台,增加初侧线作为产品外送出装置。
1.2.2常压塔系统
常压塔设顶循、一中、二中三个中段回流油馏分,常三线作为蜡油。
本次改造常压塔利旧,增设二中侧线,常顶空冷由原有6台增加至12台。对常二线、常一中线进行扩径。
1.2.3加热炉系统
常压炉入口增设两排16根钉头管,更换辐射室高强燃烧器16台,更换铸铁板式预热回收系统,常压炉热负荷由32500KW提高至44245KW,加热炉热效率由90%提高至92%。
1.3本次改造核算
1)增加4台换热器, E1035A,,B((初底油-常二中换热器)2台、E1036(原油-初测油换热器)1台、E1008B(原油-常一中换热器);
2)增加2台冷却器,分别为E1033B(初顶后冷器)1台、E1034(初侧油气冷却器) 1台;
3)现有初顶空冷6台供常压塔用,初馏塔顶空冷器需要增加8台。
4)减一中线泵P1011A,B可利旧,电机需更换YB315M1-2(132KW)
常一中泵P1005A,B更换为250AYS80。
常二线泵P1007A,B更换为200AY150×2B。
初顶回流泵P1032A,B,更换为150AY150×2A
初侧泵P1033A,B,更换为80AY100×2A
常压塔增设常二中,由泵P1034A,B抽出,流量为244m³/h,可利旧原常一中泵P1005A,B。
1.4本装置主要组成
电脱盐系统、初馏和换热系统、常压系统、减压分馏系统、蒸汽发生系统、加热炉烟气余热回收系统、三注系统。
2.工艺流程简述
原油自罐区经泵升压后送入装置分为两路。第一路原油依次经E1001A,B(原油-减一中线换热器)、E1002A,B(原油-常二线III换热器)、E1003A,B(原油-常顶循油I换热器)和E1004(原油-减二中线II换热器)、E1008B(原油-常一中换热器)与热源换热;另一路原油依次经E1005(原油-常一线油换热器)/E1036(原油-初测油气换热器)、E1006A,B (原油-常顶循油II换热器)、E1007(原油-常二线油II换热器)、E1008A(原油-常一中换热器)与热源换热后两路合并后约143℃进入V1001A-C(原油电脱盐罐)。
经三级脱盐脱水后原油分为两路。第一路脱后原油依次经E1009(原油—减三线油换热器)、E1010A,B(原油—减压渣油III换热器)、E1011A,B(原油—减三中线油II换热器)、E1016C,D(原油-减压渣油Ⅱ换热器)与热源换热;另一路脱后原油依次经E1012(原油—常三线油换热器)、E1013(原油—减二中线油I换热器)、E1014A-D(原油—减三中线油III换热器)、E1015(原油—常二线油I换热器)和E1016A,B(原油-减压渣油Ⅱ换热器)与热源换热。换热后的两路原油合并后约220℃进入T1001(初馏塔)。
T1001塔顶油气经A1005A-H(初顶油气空冷器)和E1033A,B(初顶后冷器)冷却至40℃后进入V1026(初顶回流罐)进行气液分离。分离出的气体至轻烃回收;分离出的初顶油由P1032A,B(初顶回流及产品泵)升压后分为两路,一路作为塔顶回流返回初馏塔顶;另一路作为石脑油产品送出装置或作为吸收剂进入轻烃回收装置。
初底油由P1002A,B(初底油泵)抽出分为两路。第一路经E1035B (初底油—常二中换热器)、E1017A-C(初底油—减三中线油I换热器)和E1018A-C (初底油—减压渣油I换热器)与热源换热;另一路经E1035A (初底油—常二中换热器)、 E1017D-F(初底油—减三中线油I换热器)和E1018D-F(初底油—减压渣油I换热器)与热源换热。两路初底油合并后约268℃进F1001(常压炉),经加热至365℃后进入T1002(常压塔)。
初测油由泵P1033A,B抽出,经E1036(原油-初测油换热器)和E1034(初测油冷却器)后分两路一路直接出装置,一路和常二线混合后出装置。
T1002塔顶油气经A1001A-L(常顶油气空冷器)和E1022A,B(常顶后冷器)冷却至40℃后进入V1002(常顶回流罐)进行气液分离。分离出的气体一路至V1007(低压燃料气罐)作为加热炉燃料,一路去轻烃回收装置;分离出的常顶油由P1003A,B(常顶回流泵)升压后分为两路,一路作为塔顶回流返回常压塔顶;另一路作为石脑油产品送出装置。
常一线油自T1002第15层塔板自流进入T1003(常压汽提塔)上段,经0.3MPa过热蒸汽汽提后的常一线油由P1006A,B(常一线油泵)抽出,经E1005A,B、A1002(常一线空冷器)和E1023A,B(常一线冷却器)换热冷却后分两路,一路作为航煤馏分出装置,另一路作为柴油馏分与常二线、减一线油合并出装置。
常二线油从T1002第29层塔板自流进入T1003下段,经0.3MPa过热蒸汽汽提后的常二线油由P1007A,B(常二线油泵)抽出,经E1015、E1007、E1002 A,B和A1003(常二线空冷器)换热冷却后与常一线油混合。
常三线油从T1002第41层塔板由P1008A,B(常三线油泵)抽出,经E1012换热后与蜡油混合出装置。
常顶循油由P1004A,B(常顶循油泵)自T1002第5层塔盘抽出,经E1003A,B和E1006A,B与冷源换热后返回第2层塔盘上。
常一中油由P1005A,B(常一中油泵)自T1002第21层塔盘抽出,经E1008A,B与冷源换热后返回第18层塔盘上。
常二中油由泵P1034A,B自35层塔盘抽出,作为轻烃回收稳定塔重沸器热源,之后经E1035A,B(初底油-常二中换热器)与初底油换热,然后返回第32层塔盘。
常压塔底油经过热蒸汽汽提后由P1009A,B(常底油泵)抽出,送到F1002(减压炉)加热后,送入T1004(减压塔)。
T1004塔顶气体经EJ1001A-C(减顶增压器)、E1028A,B(减顶增压冷凝器)、EJ1002A,B(减顶一级抽空器)、E1029(减顶一级抽空冷凝器)后经液环泵P1029升压后,污水进入V1003(减顶分水罐)进行油水分离。V1003分出的污水由P1019A,B(减顶水泵)送出装置;V1003分出的凝缩油由P1010A,,B(减顶油泵)送出装置。不凝气作为燃料送减压炉。当液环泵故障时,油气可由备用的EJ1003(减顶二级抽空器)、E1030(减顶二级抽空冷凝器)抽空和冷凝。
减一线及减一中油由P1011A,B(减一线及一中泵)抽出后分为两路,一路返回减压塔,另一路经E1001A,B、A1004A,B(减一中线空冷器)和E1024A,B(减一中线冷却器)换热冷却后分两路:一路作为减一中返回T1004顶部;另一路作为柴油出装置。
减二线及二中油由P1012A,B(减二线及二中泵)抽出,经E1021 减二中线蒸汽发生器)、E1013和E1004A,B换热后分为两路:一路作为减二中返回T1004;另一路与常三线混合后作为蜡油出装置。
减三线及三中油由P1013A,B(减三线及三中泵)抽出分为两路:一路作为洗涤油返塔;另一路经E1017A-F、E1011A,B和E1014A-D换热后再分为两路:一路作为减三中返回T1004;一路经E1009换热后作为减压蜡油出装置。
减压过汽化油由泵P1014A,B(过汽化油泵)抽出与常压渣油混合后进减压炉。当蜡油冷出料时,蜡油经E1025A-D(蜡油-低温水换热器)冷却后出装置。
减压渣油由P1015A,B(减压渣油泵)抽出,经E1018A-F、E1016A-D和E1010A,B换热后分为两路:一路作为急冷油返回减压塔,另一路作为焦化原料直接出装置。当需要冷出料时经E1026A-D(减渣-低温水换热器)冷却后出装置。
大循环流程图:
3 .装置开工运转与标定
昌邑石化重交沥青装置在现有装置的基础上,充分利用已有设备和成熟的工艺,最大限度地减少改造工程量及投资,进行第二次技术改造,使其轻油加工能力提升至500万吨/年,装置技术改造由洛阳维达设计院进行详细设计,由山东高阳建设集团公司负责建设。20##年7月4改造开始,于20##年8月17日改造完成,于当月22开工正常,出合格产品,进入正常生产阶段。目前已平稳生产近两个月。
装置20##年10月15、16、17日进行性能标定。由于原料的原油配置变化,因此标定原油与设计原油不同,标定原油采用惠州50%:比利牛斯35%:马瑞15%。装置标定按正常负荷500万吨/年工况进行标定。正常负荷数据于20##年10月15日8点全面采样采集。10月17日8点之后,装置标定结束。
本次装置标定,生产平稳,操作正常。
3.1 标定期间数据与分析
表1标定期间原油组成分析数据对比

表2 标定主要操作条件
主要操作条件汇总表
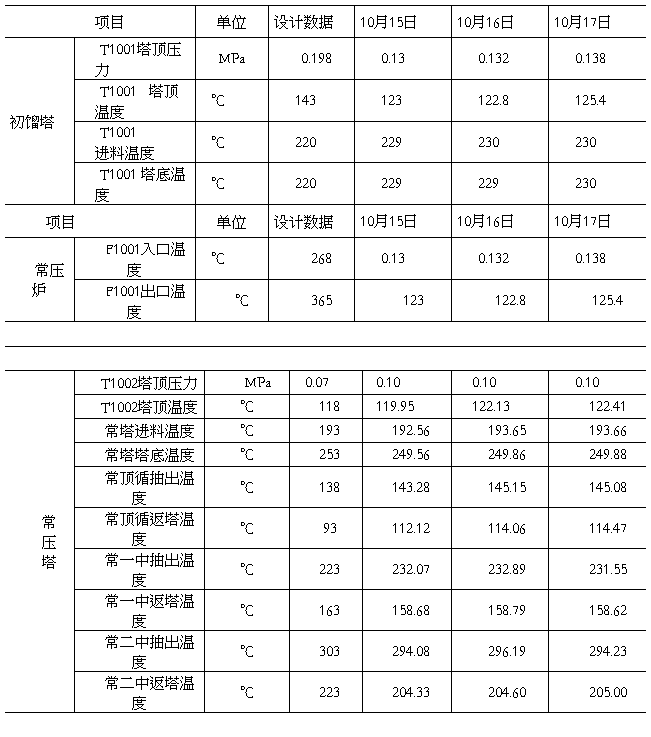
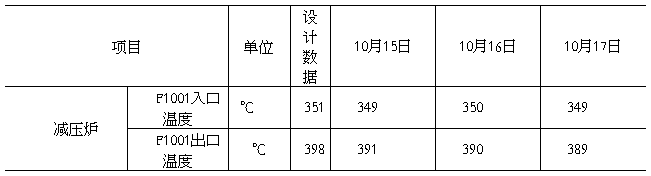

表3 标定期间物料平衡表

表4装置能耗
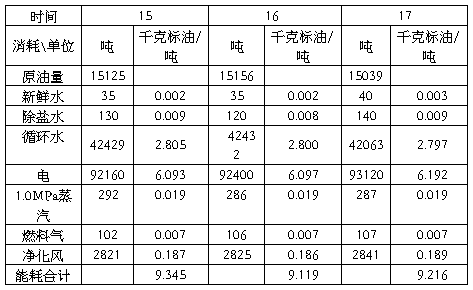
3.2标定结果
3.2.1 原油加工量
常减压装置标定期间日处理量平均为15106T/D, 期间生产操作平稳产品质量合格, 按年开工8400 小时计算, 装置可以达到551 万吨/年的处理能力,为设计能力的110%, 达到装置检修改造的目的。
标定时,装置加工的原油为惠州、比利牛斯、马瑞的混合原油,混合比例为50:35:15。由于没有完整的混合设施,从表1分析数据看,原油性质在不同的时间有所变化。为了对比,列出了从原油评价中的各原油性质和实际分析的混合原油的性质。从实际原油分析数据看,数据中硫含量约在0.74%(wt)左右,酸值约为0.81mgKOH/g左右,与设计中原油为高硫低酸的性质不太一致。
3.2.2 轻收及总拔
标定期间装置轻油收率为41.17%, 总拔为76.37%。
标定期间原油配比稳定,故三天标定的产品收率都基本相同。标定装置拔出率与设计拔出率对比见表5。
表5 装置拔出率对比表
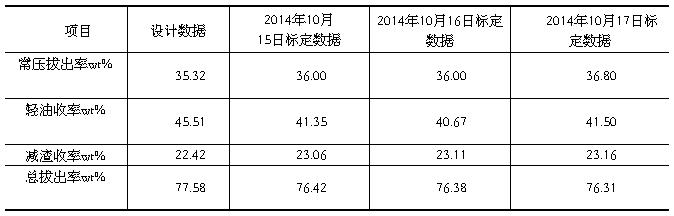
装置设计是依据吉拉索、安哥拉、阿曼、ESPO各占25%的比例设计,设计原油性质相对较轻,拔出率及轻油收率相对较高。与实际原油化验数据对比基本保持一致。
3.2.3 产品质量
标定期间产品质量合格, 初常顶能生产稳定合格的重整原料油;
常一、常二线能生产稳定的柴油组分指标合格;减压蜡油及渣油性质稳定, 保证下游装置的平稳生产。
标定期间常压渣油365℃馏出量为10%。分析原因常压塔针对燃料油型常压塔设计,塔径细、塔盘开孔率低,导致常压塔365℃含量较高。
减压塔操作平稳, 通过控制减压真空度及减压炉温的手段, 控制减压拔出率, 减压渣油510℃前馏出量指标在4%左右, 满足下游装置的需要。
常压渣油365℃含量及减压渣油510℃含量分析数据见表
表6 标定渣油性质表

3.2.4 装置能耗
标定期间装置能耗平均为9.23, 设计值为10.60, 均低于设计值, 分析原因在于:
(1) 加热炉瓦斯消耗量大大降低。加热炉经过改造后, 燃烧器燃烧效果提高,加热炉热效率提高。
(2)优化换热流程提高原油换热终温,减少公用工程消耗,可以有效降低能耗水平,实际生产时应该尽量保持各个中段取热的流量,即高流量、低温差。这样有利于换热,进而提高换热终温。
(3)循环水水量通过监测冷却器冷后温度进行前手阀调节控制大大节省了循环水的利用率。
(4)装置采取节电措施,对于高功率泵采用变频控制,通过及时监测外送油品的冷后温度及时开停风机,节省了电耗。
3.2.5 塔系统
初馏塔标定期间初顶石脑油产出量25t/h,与设计值41.16 t/h略有偏差。初侧油平均产出8.6t/h,与设计值8t/h达到设计要求。为提高初馏塔的拔出率,在下次改造中建议增加塔底注汽,以提高初顶油、初侧油的产品收率,减轻常炉负荷。
常压塔标定期间常压塔气相负荷比设计小,塔顶压力0.04Mpa,设计压力0.17Mpa,油气分压降低,提高了轻质油收率。 常压塔的液相负荷较大,柴油外送负荷接近最大值。
顶循塔板的液相负荷超设计(205t/h)50%以上,标定期间负荷超最大值(400t/h),建议继续对顶循侧线进行改造。
常一中侧线新增换热器E1008B一台,导致原油脱前换热在标定期间偶超150℃以上,超越工艺指标,建议在E1008换热器增加一组三通阀或继续优化换热流程。
3.2.6 换热网络
原油换热终温为286.7℃, 远高于设计值268℃。原因在于由于减压塔拔出效果非常明显, 因此使减压渣油温度升高, 造成原油取热量增加, 使得原油换热终温提高;由于原油换热终温的升高, 使得常压炉负荷降低,由于加热炉炉膛温度升至771℃,加工量负荷至110%至最大负荷,已无提量空间。从下表数据可以看出,换热终温平均在286.7℃左右,达到设计换热网络计算数值,达到了设计指标。
表7 换热网络标定结果

3.2.7 机泵
顶回流泵P1003AB电机功率过小(90KW),电流超出额定电流, 出现超负荷现象, 因此,更换该泵电机至110KW,现已正常。
标定期间,常顶循环泵P1004AB电机负荷较大一直处于满负荷状态,流量超400t/h。需要对改线进行扩径。
3.2.8 加热炉
常压炉设计最大处理量为529640kg/h。装置标定时处理量629444 kg/h远超设计值。余热回收系统排烟温度设计值为138℃,标定期间值为143.9℃,已降低至最小值,余热回收系统有待进一步优化。
标定期间加热炉氧含量分别为1.15%、2.66%, 排烟温度为143.9℃。监测加热炉热效率,常压炉热效率为92.09%,减压炉热效率为91.72%。基本达到设计要求(92.5%)。但在标定期间, 实际标定的常压炉烟气出辐射段温度为771℃,原设计计算值为750℃,不利于进一步提高处理量。
标定期间常炉氧含量设定值2%,常炉热风挡板处于全开状态,减炉热风挡板关至最低限值15%,鼓风机转速调至最大值。常压炉在较大负荷状态下,预热空气供入量不足,无操作弹性 ,建议对常炉烟道进行扩径,达到优化控制的要求。
3.2.9装置防腐
低部位防腐情况
常压低温部位防腐情况对比

从上表可以看出初顶水铁离子含量较高,超设计值3.0 mg/L,原因在于加工原料油性质较差,氯离子、酸值含量较高,造成初顶低温腐蚀较重,对初顶PH值做重点监控,加大缓蚀剂注入量,有效保护缓蚀膜不被破坏。
3.2.10 环境保护
装置生产过程中排出的废水主要有含油污水、含硫污水和含盐污水,其中含油污水、含盐污水送往污水处理场:含硫污水密闭送至污水汽提装置。装置废气主要有燃烧废气和非正常工况下排放的烃类气体两类,其中燃烧废气来自加热炉排放的烟气,其主要污染物是SO2、NOX、和TSP(总悬浮污染物),非正常工况下安全阀起跳排放的主要污染物是烃类,密闭送往火炬系统,不直接排放。正常生产情况下装置无废渣产生。
4.存在的问题及建议
从前面的标定数据分析看,本装置的处理量、产品质量、中段回流取热比例、换热终温、加热炉热效率、装置能耗及设备的运行均达到或优于设计的预期值,说明装置的运行状况良好。但为了进一步优化装置操作,还可做下面的工作:
(1)继续优化换热流程,目前国内同类先进装置换热终温可提高至300℃以上,大大节省了燃料消耗,降低了吨油费用。
(2)脱前温度控制,将换热量较大的常压塔中段回流增加三通控制调节器,可以有效调节入电脱温度达控制指标之内。
(3)初顶油拔出率偏低,适时增加塔底汽提提高其石脑油收率,降低常炉负荷。
(4)常压塔顶循环泵、常一泵负荷较大,常顶循泵出口流量至最大流量,常一泵功率小变频开度一直处于满负荷状态,成为制约装置安全生产的重要因素。建议将常顶循侧线扩径,常一泵更换大功率电机,具体方案需要设计院核定。
(5)加热炉排烟温度无操作弹性,热管换热面积不足,需要增加一组板式换热系统。
(6)常压塔塔径细,加工轻质原油拨出率相对较低,常底油365℃组分含量较高,需要在原有塔的基础上改换高效塔盘,增加塔盘开孔率以达到提高轻质油收率的目的,减轻减压炉及减压塔的负荷。
5.结论
此次标定, 常减压装置操作平稳, 产品质量合格, 原油加工量达到500 万吨/年, 实现了检修改造的目的, 改造基本成功。由产品数据分析看出, 装置在500万吨/年处理量下, 初、常顶油能生产稳定合格的重整原料油, 满足干点≯170℃, 常一线、常二线油能生产稳定合格的柴油, 各项指标符合公司的要求。为下游装置提供的二次加工原料也可满足质量要求。本装置的改造成功,为装置的安全运行奠定了基础,也为后续部门的发展积累了经验,其经济效益和社会效益是显而易见的。