滑动轴承实验指导

一、实验目的及要求
1、 液体动力润滑滑动轴承油膜压力周向分布的测试分析;
2、 液体动力润滑滑动轴承油膜压力周向分布的仿真分析;
3、 液体动力润滑滑动轴承摩擦特征曲线的测定;
4、 液体动力润滑滑动轴承实验的其他重要参数测定:如轴承平均压力值、轴承PV值、偏心率、最小油膜厚度等。
二、实验基本原理
实验台的构造如图3-1所示。
1、实验台的传动装置
由直流电动机通过V带传动驱动轴沿顺时针(面对实验台面板)方向转动,由无级调速器实现轴的无级调速,由软件界面内的读数窗口读出。
图3-1 滑动轴承实验台
2、轴与轴瓦间的油膜压力测量装置
轴的材料为45号钢,经表面游淬火、磨光,由滚动轴承支承在箱体上,轴的下半部浸泡在润滑油中,本实验台采用的润滑油的牌号为0.34PaS。轴瓦的材料为铸锡铅青铜,牌号为ZCuSn5Pb5Zn5(即旧牌号和ZQSn6-6-3)。在轴瓦的一个径向平面内沿圆周钻有7个小孔,每个小孔沿圆周相隔20º,每个小孔连接一个压力表,用来测量该径向平面内相应点的油膜压力,由此可绘制出径向油膜压力分布曲线。沿轴瓦的一个轴向剖面装有两个压力表,用来观察有限长滑动轴承沿轴向的油膜压力情况。
3、加载装置
油膜的径向压力分布曲线是在一定的载荷和一定的转速下绘制的。当载荷改变或轴的转速改变时抽测出的压力值是不同的,所绘出的压力分布曲线的形状也是不同的。转速的改变方法于前所述。本实验台采用螺旋加载,转动螺旋即可改变载荷的大小,所加载荷之值通过传感器数字显示,直接在测控箱面板右显示窗口上读出(取中间值)。这种加载方式的主要优点是结构简单、可靠,使用方便,载荷的大小可任意调节。
4、摩擦系数f测量装置
径向滑动轴承的摩擦系数f随轴承的特性系数值λ =ηn /p的改变而改变(―油的动力粘度,n―轴的转速,p―压力,p= W/Bd ,W―轴上的载荷,B―轴瓦的宽度,d―轴的直径)。
在边界摩擦时,f随λ的增大而变化很小(由于n值很小,建议用手慢慢转动轴),进入混合摩擦后,λ的改变引起f的急剧变化,在刚形成液体摩擦时f达到最小值,此后,随λ的增大油膜厚度亦随之增大,因而f亦有所增大。
摩擦系数f之值可通过测量轴承的摩擦力矩而得到。轴转动时,轴对轴瓦产生周向摩擦力F,其摩擦力矩为Fd/2,它供轴瓦翻转,轴瓦上测力压头将力传递至压力传感器,测力传感器的检测值乘以力臂长L,就可以得到摩擦力矩值,经计算就可得到摩擦系数f之值。
根据力矩平衡条件得:Fd/2=LQ。L―测力杆的长度(本实验台L=120mm),Q―作用在A处的反力。
设作用在轴上的外载荷W,则:f = F/W =2LQ/ Wd
Mf = LQ的值可直接读到,f = 2Mf / Wd
其中:面板上为油膜压力,
为加载力,
为摩擦力矩,
为油温,
为转速。
5、实验系统主要技术参数
实验轴瓦:内径:d=70mm,长度L=125mm
加载范围:0-1000N(100kg)
摩擦力传感器量程:50N
压力传感器量程:0-1.0MPa
加载传感器量程:0-2000N
直流电动机功率:355W
主轴调速范围:2-500rpm
三、主要仪器设备及实验耗材
实验仪器设备:杭州星辰科教设备有限公司的ZCS-Ⅱ型液体动压轴承实验台。
四、实验内容或步骤
实验步骤:
1、准备工作
1) 将光电传感器接至测控箱背板的数字通道1上,从左到右依次将管路压力传感器接至控制箱上的模拟通道1-7上,将轴上的管路压力传感器接至模拟通道8上,摩擦力矩检测传感器接至模拟通道9,负载荷重压力传感器接至模拟通道10上。
2) 将控制箱的电机电源线与电机相联,同时连接控制箱电源。
3) 如果使用计算机测,将计算机与控制箱用串口线相联。
2、实验机构操作
1)在开电机转速之前请确认载荷为空,即要求先开转速在加载,转速慢慢加到200rpm待稳定后,旋动加载螺纹加载约400N,(转速和加载值在测控箱面板的右显示窗口显示);
2)在一次实验结束后马上又要重新开式实验时,请用轴瓦上端的螺栓旋入顶起轴瓦将油膜先放干净,同时在软件中要重新“复位”,这样确保下次实验的数据准确;
3)由于油膜形成需要一小段时间,所以在开机实验或在变化载荷或在变化转速后请待其稳定后(一般等待5-10S即可)再采集数据;
4)长期使用过程中请确保实验油的足量、清洁;油量不够和不干净都会影响实验数据的准确;
5)进入实验主窗体1,选择通讯口COM1或者COM2,在开始加载和电机转速之前先点即“复位”以让软件进入试验台的初始状态,保证实验数据的准确。在确定机构工作稳定后点击“数据采集”,将数据采集进来(共12个数据,它们是7个油膜压力值、1个外加载荷值、1个转速值、1个计算摩擦力矩的压力值)。当数据采集完成后就可进行油膜压力分析了,点击“实测曲线”作出测得的7个压力值曲线,点击“理论曲线”作出理论压力曲线,可对两者进行比较。同时也可手动改变7个点的压力值的大小或载荷、转速值再观察曲线的变化。点击“结果显示”会将相应的结果显示在结果显示框中。
3、摩擦性能仿真与测试
1) 进入主窗体,同样首先选择通讯串口COM1或COM2,选择摩擦特性实验,在实验模式(“理论模拟”和“实测实验”)中选择相应的状态,“实测实验”将从试验台采集的数据发送到软件数据显示列表中,点击“实测曲线”作出摩擦系数实测曲线;
2) 在曲线显示窗口中,纵坐标显示的为摩擦系数,横坐标由操作模式决定(操作模式有“载荷固定”和“速度固定”),相应的横坐标为转速和载荷;
3) 待各压力表的压力值稳定后,由左至右依次记录各压力表的压力值(转速不变);
4) 调节转速并逐次记录有关数据;(保持加载力不变)
5) 卸载、关机。
实验报告内容:
1、实验目的
2、实验数据记录图表
(1)油膜压力实验
工作参数:转速n=200r/min;载荷F=800N
表3-1 实测油膜7点压力值

油膜平均压力: 许用压力:
pv值: 许用pv值:
最小油膜厚度:
(2)摩擦性能实验
表3-2 速度固定下的实测摩擦力矩(速度为200rpm)
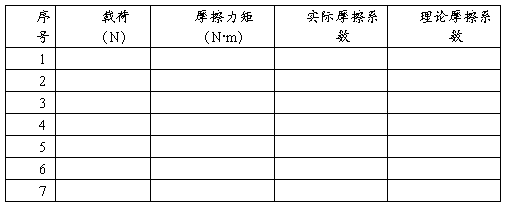
表3-3 载荷固定下的实测摩擦力矩(载荷为500N)
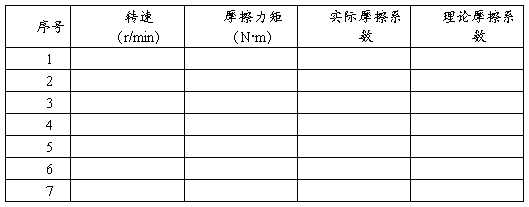
3、实验结果分析
(1)绘制n= 200r/min时油膜压力分布曲线(径向、轴向两种);
(2)绘制n= 200r/min时径向油膜承载能力的计算;
(3)绘制速度一定时,摩擦系数的实测和理论曲线;
(4)绘制载荷一定时,摩擦系数的实测和理论曲线。
五、思考题
1、径向滑动轴承形成液体动压润滑的条件?
2、滑动轴承与滚动轴承比较有哪些独特优点?为什么?
3、径向滑动轴承的轴颈与轴承孔间的摩擦状态?
4、影响轴承承载量的因素是什么?
5、常用的轴瓦材料有哪些?轴瓦材料除应满足摩擦系数小和磨损少以外,还应满足什么要求?
六、主要参考书
1、濮良贵,纪名刚主编.机械设计(第八版).北京:高等教育出版社,2006
南昌大学实验报告
学生姓名: 学 号: 专业班级:
实验类型:综合性实验 实验日期: 实验成绩:
一、实验项目名称 滑动轴承实验
二、实验目的
三、实验基本原理
四、主要仪器设备及耗材
五、实验步骤
六、实验数据及处理结果
(1)油膜压力实验
工作参数:转速n=178r/min;载荷F=1823N
表3-1 实测油膜7点压力值

油膜平均压力: 许用压力:
pv值: 许用pv值:
最小油膜厚度:
(2)摩擦性能实验
表3-2 速度固定下的实测摩擦力矩(速度为 )
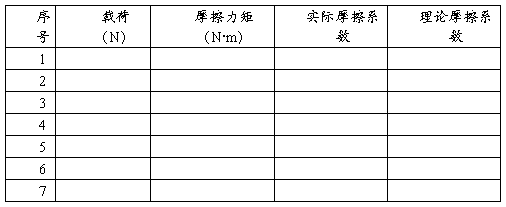
表3-3 载荷固定下的实测摩擦力矩(载荷为 )
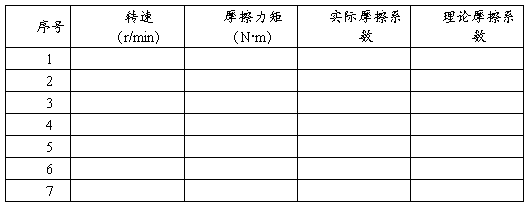
七、实测曲线
(1)绘制n= 500r/min时油膜压力分布曲线(径向、轴向两种);
(2)绘制n= 500r/min时径向油膜承载能力的计算;
(3)绘制速度一定时,摩擦系数的实测和理论曲线;
(4)绘制载荷一定时,摩擦系数的实测和理论曲线。
八、思考讨论题或体会或对改进实验的建议
九、参考资料
第二篇:滑动轴承实验指导书(更新并附实验报告)
滑动轴承实验
一、概述
滑动轴承用于支承转动零件,是一种在机械中被广泛应用的重要零部件。根据轴承的工作原理,滑动轴承属于滑动摩擦类型。滑动轴承中的润滑油若能形成一定的油膜厚度而将作相对转动的轴承与轴颈表面分开,则运动副表面就不发生接触,从而降低摩擦、减少磨损,延长轴承的使用寿命。
根据流体润滑形成原理的不同,润滑油膜分为流体静压润滑(外部供压式)及流体动压润滑(内部自生式),本章讨论流体动压轴承实验。
流体动压润滑轴承其工作原理是通过韧颈旋转,借助流体粘性将润滑油带人轴颈与轴瓦配合表面的收敛楔形间隙内,由于润滑油由大端人口至小端出口的流动过程中必须满足流体流动连续性条件,从而润滑油在间隙内就自然形成周向油膜压力(见图1),在油膜压力作用下,轴颈由图l(a)所示的位置被推向图1(b)所示的位置。
图1 动压油膜的形成
当动压油膜的压力p在载荷F方向分力的合力与载荷F平衡时,轴颈中心处于某一相应稳定的平衡位置O1,O1位置的坐标为O1(e,Φ)。其中e =OO1,称为偏心距;Φ为偏位角(轴承中心O与轴颈中心O1连线与外载荷F作用线间的夹角)。
随着轴承载荷、转速、润滑油种类等参数的变化以及轴承几何参数(如宽径比、相对间隙)的不同.轴颈中心的位置也随之发生变化。对处于工况参数随时间变化下工作的非稳态滑动轴承,轴心的轨迹将形成一条轴心轨迹图。
为了保证形成完全的液体摩擦状态,对于实际的工程表面,最小油膜厚度必须满足下列条件:
(1)
式中,S为安全系数,通常取S≥2;Rz1,RZ2分别为轴颈和铀瓦孔表面粗糙度的十点高度。
滑动轴承实验是分析滑动轴承承载机理的基本实验,它是分析与研究轴承的润滑特性以及进行滑动轴承创新性设计的重要实践基础。
根据要求不同,滑动轴承实验分为基本型、综合设计型和研究创新型三种类型。
二、实验目的
(1)掌握实验装置的结构原理,了解滑动轴承的润滑方式、轴承实验台的加载方法以及轴承实验台主轴的驱动方式及调速的原理。
(2)掌握实验台所采用的测试用传感器的工作原理。
(3)通过实验测试的周向油膜压力分布及轴向油膜压力分布,掌握滑动轴承中流体动压油膜形成的机理及滑动轴承承载机理。
(4)通过实验掌握工况参数和轴承参数的变化对滑动轴承润滑性能及承载能力的影响。
三、实验内容
对于基本型实验,实验内容如下:
(1)轴承中间平面上周向油膜压力分布曲线图[见图2(a)]和轴向油膜压力分布曲线图[见图2(c)]。
(2)周向油膜压力分布曲线图的承载分量的曲线图[见图2(b)],求轴承的端泄影响系数K。
考虑有限宽轴承在宽度B方向的端泄对油膜承载量的影响,其影响系数K可由下式求出:
(2)
式中,F为轴承外载荷,N;B为轴承有效工作宽度,mm;d为轴颈直径,mm;pm为根据油膜压力承载分量的曲线图求出的动压油膜的平均压力,如图2(b)所示。
图2(a)为实测上轴瓦上均布测点l~7位置处的油膜压力形成的周向油膜压力分布曲线;图(b)为过这7个分点分别引垂线段l—1”、2—2”、…、7—7”,使之分别等于图(a)中的油膜压力值的垂直分量后连成的光滑曲线,该曲线被称为动压油膜的承载分量曲线;图(c)为轴向油膜压力分布曲线。
根据承载分量曲线和直径所园成的图形面积等于平均压力pm与直径围成的矩形面积相等的条件,通过数方格数的方法即可求出pm大小。再将求出的pm值代人式2即可求出K。
图2 滑动轴承油膜压力分布曲线图
四、实验装置
实验装置采用西南交通大学研制的ZHS20系列滑动轴承综合实验台。该实验台主要由主轴驱动系统、静压加载系统、轴承润滑系统、油膜压力测试系统、油温测试系统、摩擦观察测试系统以及数据采集与处理系统等组成。
1、主轴驱动系统及电机选择
实验台的主轴支承在实验台箱体上的一对滚动轴承上。该主轴的驱动电动机需满足无极调速、低速大转矩及实验过程中能快速启停等要求。
驱动电机主要有交流异步电动机、直流电动机、步进电机、交流(直流)伺服电动机等类型。
交流伺服电动机的工作原理与普通交流异步电动机相似,但交流伺服电动机的转子电阻比异步电机的大得多,其转矩特性(转矩T与转差率S的关系)也因此较普通电机有很大区别(见图3)。它可使临界转差率大于1,这样不仅使转矩特性更接近于线性.而且具有较大的起动转矩,因此,伺服电机具有起动快、灵敏度高的特点。
图3 伺服电动机的转矩特性
目前,基于稀土木磁体的交流水磁伺服驱动系统,能提供最高水平的动态响应和扭矩密度。所以用交流伺服驱动取替传 统交流调速、直流和步进调速驱动,以便使系统性能达到一个全新的控制水平,从而获得更宽的调速范围和更大的低速扭矩。因此,本实验台选用了交流伺服电动机,其优点归纳如下:
(1)控制精度高。
交流伺服电机的控制精度由电机轴后端的旋转编码器保证,因此交流伺服具有极高的控制精度。
(2)低频特性好。
步进电机在低速时易出现低频振动现象;普通交流电机由变频器进行调速,在低频时的力矩小;直流电机在低速的控制极不稳定。而交流伺服电机运转非常平稳.即使在低速时也不会出现振动现象。交流伺服系统具有共振抑制功能,可以克服机械的刚性不足缺点,并且系统内部具有频率解析功能(FFT),可检测出机械的共振点,使于调整系统。
(3)矩频特性好。
交流伺服电机为恒力矩输出,即在其额定转速(一般为1000r/min)以内,都能输出额定转矩,在额定转速以上为恒功率输出。
(4)过载能力强。
交流伺服电机具有较强的过载能力。它具有速度过载和转矩过载能力。其最大转矩为额定转矩的3倍,可用于克服惯性负载在启动瞬间的惯性力矩。
(5)运行稳定。
交流伺服驱动系统为闭环控制,驱动器可直接对电机编码器反馈信号进行采样,内部构造成位置环和速度环,一般不会出现步进电机的丢步或过冲现象,控制性能更为可靠。
(6)响应速度快。
交流伺服系统的加速性能较好,从静止加速到其额定转速1000 r/min仅需几毫秒,可用于要求快速启停的控制场合。
2、液压系统
实验台的液压系统功能,—是为实验轴承提供循环润滑系统提供压力供油。液压系统框图如图4所示。
为了保证液压加载系统的稳定性,该系统采用变频恒压的接制方式。变频恒压供油系统主要由油泵、变频器、压力传感器组成,如图5所示。通过压力传感器对加载系统的压力监测,实时调节油泵电机的转速使电机—油泵—液压油路系统组成一个闭环控制系统。由于在各种转速下形成的油膜压力和端泄情况有—定的差别,通过变频恒压系统能真正地实现在各种转速下加载压力保持不变。
若液压加载系统向固定于箱座上的加载盖板内的油腔输送的供油压力为p0时,载荷即施加在轴瓦上,则轴承载荷为:
N (3)
式中,p0为油腔供油压力,kgf/cm2;A为油腔在水平面上投影面积,A=60 cm2;Go为初始载荷(包括轴瓦自重、压力变送器重量等),Go=7.5kgf。
图4 液压系统框图
图5 变频恒压控制原理框图
3、油膜压力变送系统
在轴瓦的上半部承载区轴承宽度的中间剖面上,沿周向均布钻有1~7共7个小孔,分别在小孔处安装压力变送器。当轴旋转到一定转速后,在轴承内形成动压油膜,通过压力变送器测出油膜压力值,并在计算机上显示周向油膜压力分布曲线(见图2)。在轴瓦的有效宽度月的l/4处,安装轴向油膜压力变送器8,测出位置8处的油膜压力p8,根据轴向油膜压力分布对称原理,可以测得袖向油膜压力分布曲线[见图2(c)]。
本实验台采用压阻式压力变送器,它由压力敏感部件与压力变送器部件组成。
(1)压力敏感部件。
扩散硅压阻式压力传感器的工作原理:以扩散硅材料制成的膜片作为弹性敏感元件,其硅晶片上通过微机加工工艺构成一个惠斯通电桥、如图2—6所示,图中I表示恒流源,R表示电桥阻值,Vs表示激励电压,Vo表示电桥输出电压。当有外部压力作用时,膜片发生弹性变形,膜片的一部分受压缩,另一部分则受拉伸。两个电阻位于膜片的压缩区,另两个位于拉伸区,并联成惠斯通全桥形式,以使输出信号最大。
图6 惠斯通电桥
(2)压力变送器部件(性能参数见表1)。
因压力传感器是一个在硅晶片上通过加工工艺构成的一个惠斯通电桥,该电桥桥阻的变化与作用在其上的外部作用力大小成正比例关系。为了将电阻变化量转换为电压信号,给电桥提供最大2mADC的恒流源,用于激励压力传感器工作。信号放大和转换处理电路将惠斯通电桥产生的电压信号线性放大处理后,将其转换为4~20mADC工业标准信号变送输出构成压力变送器。其主要性能特点如下。
①稳定性高。每年漂移优于0.2%满量程。
②温度系数小。由于在生产过程中对产品精密地校准及补偿,使其温度误差极小。
③适应性强。产品量程宽,过程连接形式、制造材料、结构具有多样化特征,因而可适应工业测量中的各种场合及不同的介质。
④安装维护方便。产品可任意安装在各测量点而不影响其性能。
表1 压力变送器的性能参数表
4、油温测试系统
在轴承的人口处和出口处分别安装温度传感器各一只,分别采集轴承入口处的润滑油油温t1和出口处的油温t2,则可得到润滑油的平均温度tm[tm=(t1+t2)/2],一般情况下tm不大于75℃。
5、滑动轴承控制系统
实验台的8个油膜压力传感器、液压加载传感器、测摩擦因数用的拉压负荷传感器以及油温传感器采集的测试数据通过A/D转换器,以RS485总线方式传送到计算机的实验数据采集及处理软件系统,交接在屏幕上显示出来,或由打印机订印输出实验结果。
主轴电机的转速大小通过计算机进行设置,设置值通过E5485总线送到伺服电机驱动器,由伺服电机驱动器控制电机的转速。
油压加载系统的压力是内实验人员在电脑上设置加载压力po与液压加载压力传感器的反馈值进行比较,再通过PID调节运算,将动态地改变变频器的输出频率,使其液压加载压力保持恒定。
实验台的控制原理框图如图7所示。
五、实验装置的操作步骤及方法
(1)网上预习“滑动轴承实验”课件。
(2)观察实验台的各部分结构、检查油路及电路是否可靠连接。
(3)用手转动轴瓦,使其摆功灵活、无阻滞现象。
(4)根据实验六操纵面板(见图8),按图示按钮功能使总电源,油压系统及主轴系统处于接通位置,这时系统进入工作状态。
说明:无论做何种实验,均应先启动液压系统电机,后启动主轴驱动电机(伺服电机)。在实验过程中,如遇电机转速突然下降或者出现不正常的噪音和振动时,必须卸载或紧急停车,以防电机突然转速过高,烧坏电机、电器及其它意外事故的发生。
(5)进入滑动轴承实验计算机软件系统。
①启动界面。
运行“开始菜单\程序\组态王6.51\组态王6.51”,弹出“组态王工程管理器”窗口,点击“运行”工具按钮,弹出“提示”对话框,选择“忽略”按钮,进入滑动轴承实验软件界面,如图9所示。
图7 控制原理框图
②点击[实验管理]菜单的“实验管理”进入实验管理系统。
实验人员自行输入“实验时间”,“实验记录号”,“实验分组号”,“实验人员”,“实验指导老师”等,点击【返回】。
③点击[实验分类]菜单,将会显示出可供选择的“径向滑动轴承油膜压力分布曲线”菜单,开始实验(见图11)。
该界面显示有:主轴的转速,油压以及周向的7个油膜压力等。
④点击“静压加载”数字框,弹出键盘,设置加载压力(建议用p0=0.1-0.15MPa)
⑤点击【油泵控制】菜单,选择“启动”,启动油压系统。
⑥油压升起后,点击“当前转速”数字框,设置主轴转速(建议用n=200-500r/min)。设置主轴转速时请先设置为50 r/min,运转稳定后,再逐步按照100 r/min、150 r/min、200 r/min逐步增加到需要设置的主轴转速。
⑦观察油膜周向和轴向的分布曲线,如果曲线模糊,点击“稳定取值”按钮,同时观察右边的油膜压力数值显示窗口的8个点的油膜压力值。
⑧曲线稳定后,点击[暂停采样],在点击打印当前窗口。
⑨实验完成后,根据周向油膜压力曲线图,求出油膜平均压力Pm值,并计算K值。
图8 实验台操纵面板布置图
图9 系统首界面
图10 进入实验管理系统
图11 轴承油膜压力分布曲线
停止运行系统时,务必先关闭主轴驱动电机(按“轴停止”键),等主轴驱动电机停止转动后再卸载轴承静压载荷(调“静压载荷”键),最后关闭液压系统电机,以减轻轴瓦磨损。
停止主轴:点击“轴停止”。
停止油压系统:选择[油泵控制]菜单下的“停止”即可。
六、思考题
1、哪些因素影响液体动压轴承的承载能力及其动压油膜的形成?
2、当载荷增加或转速升高时,油膜压力分布曲线有什么变化?
3、轴向压力分布曲线与轴承宽径比B/d之间有什么关系?当B/d≥4及B/d≤1/4两种情况下,它们的轴向油膜压力分布有何明显差异?求解流体动力润滑雷诺方程的简化方程时又有何不同?
深 圳 大 学 实 验 报 告
课程名称: 机械设计
实验名称: 滑动轴承实验
学 院: 机电与控制工程学院
专 业: 机械设计制造及其自动化
指导教师:
报告人: 学号: 第 组
班 级: 实验时间:
实验报告提交时间:
教务处制
一、实验目的
二、实验原理
三、实验装置结构简图
四、实验步骤
五、实验装置原始数据
轴颈直径 d= mm
轴承有效宽度 B= mm
驱动电机类型 ;功率 kW;额定转速nd= r/min
压力传感器类型 ;量程 MPa
实验油品
六、测定油膜压力分布时选择的工况参数
轴颈转速n= r/min
静压加载油腔油压p0= MPa
轴承循环润滑系统油压pL= MPa
七、实验数据记录
1、测得轴瓦圆周上均布的1~7点的周向油膜压力数值。
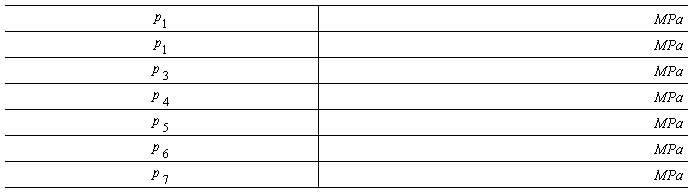
2、测得第8点轴瓦上轴向油膜压力p 8= MPa。
八、根据测得的p1、p2、…、p8,绘制油膜压力分布曲线,完成下列要求
1、绘制周向油膜压力分布曲线。
2、绘制轴向油膜压力分布曲线。
九、求动压滑动轴承端泄影响系数K
1、根据实测的油膜承载量分布曲线,求出油膜平均压力pm。
2、按端泄影响系数,计算K值。
式中,B=60mm;d=60mm; N,其中Go=7.5kgf,A=6000mm2,p0为油腔供油压力,kgf/cm2。
十、思考题
1、哪些因素影响液体动压轴承的承载能力及其动压油膜的形成?
2、当载荷增加或转速升高时,油膜压力分布曲线有什么变化?
3、轴向压力分布曲线与轴承宽径比B/d之间有什么关系?当B/d≥4及B/d≤1/4两种情况下,它们的轴向油膜压力分布有何明显差异?求解流体动力润滑雷诺方程的简化方程时又有何不同?
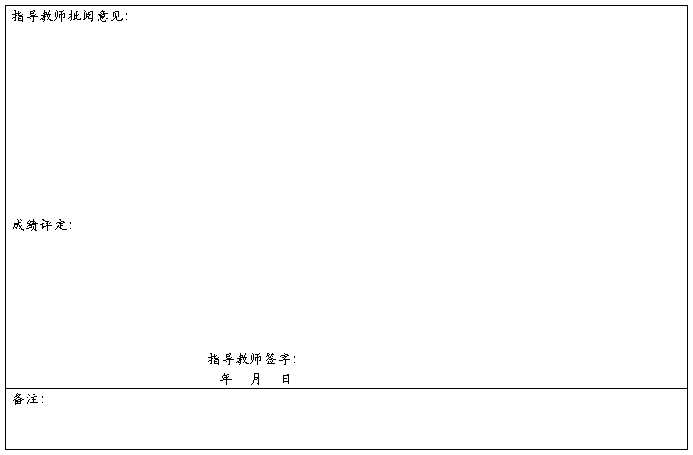