面料检验标准
4.内容
4.1、面料疵点简述
面料的生产需要经过很多工序,任何工序的操作不当都会以疵点的形式出现在面料上,原料的品质不良也同样如此。由于疵点的外观形态并给出准确的名称不是很容易。但是,即使不能根据疵点的外观形态给出疵点名称也不要紧,因为疵点就是疵点,只要根据四分制,量度它的尺寸即可。同时,把该批面料中的主要疵点剪下作为标样,附在检验报告后。
如果能够了解各种疵点的名称及其外观形态,那么会给工作带来很大便利,可以简化检验或者报告的语言,也方便与各方面的沟通。现将主要疵点简述如下。
4.1.1.由纱疵形成的面料疵点
由于原料的品质不良形成的面料疵点。
(1)粗节纱:在织物表面出现某一根纱线的某一段较粗,其直径数倍于正常纱线。连续的粗节纱称为竹节纱。
(2)偏细纱:在织物上有一根或数根纱线的细度明显细于其他正常纱线。
(3)扭结纱:织物上的纱线有扭结或卷曲的外观。
(4)毛丝:织物上某些部位纤维突出端点或呈茸毛状外观。
(5)亮丝:织物上某一根纱线的光泽明显亮于其他纱线的正常光泽。
(6)结头;织物的表面呈现明显的纱线结头。
(7)污渍纱:织物上的纱线带有油污等其他污渍。
(8)杂物织入:有回丝、异色纤维等杂物织入面料。
(9)条干不匀:由于采用了条干不匀的纱线,布面呈现分散性的纱线不匀外观。
4.1.2.经向疵点
加工经纱形成的疵点或在织造中产生的经向疵点。
(1)直条痕:织物的经向有一根或几根纱线异于临近的正常纱线,在布面明显的直条状外观。
(2)粗经:织物上的某根经纱粗于其他经纱。
(3)松经:布面上的某根经纱呈松弛或起皱的外观。
(4)紧经:某根经纱的捻度过大,使经纱的屈曲程度不正常。
(5)吊经:织物上一根或几根经纱的张力过大,致使这些经纱不正常被拉紧。
(6)缺经:由于织造时断经而未及时处理,布面上通匹或一段长度内缺少一根经纱。
(7)断疵:经纱的断头纱尾在布内。
(8)经缩:由于经纱张力不匀,布面呈现块状或条状的起伏不平或起皱外的形态。
(9)双经:两根经纱并列或重叠,织物的组织被破坏。
(10)扣痕:在织物的幅宽方向呈现局部或全部经纱排列不匀的纹路。
(11)扣路:织物的相邻两根经纱之间有空隙。
(12)穿错:由于穿经错误而导致织物的组织发生错误。
(13)错经:组织错误或其他错误,使织物部分经纱与相邻的其他经纱明显不
同。
(14)针路:由于卷布刺毛辊不良使织物的经向有密集的针痕。
(15)布辊皱:由于布辊不良形成的经向折皱。
4.1.3.纬向疵点
加工纬纱形成的或在织造加工中形成的纬向疵点。
(1)纬档:织物纬向呈现的横档.明显不同于正常织物的外观。
(2)稀密路:横档的一种。某一段密度过大,或某一段密度过小。
(3)粗纬:织物上的某根纬纱明显粗于其他正常纬纱。
(4)松纬:某根纬纱的张力低于相邻纬纱,呈松弛或起皱的外观。
(5)紧纬:某根纬纱的张力高于相邻纬纱,使其不正常被拉紧,屈曲小。
(6)断纬:纬纱断裂或断纱。
(7)纬缩:纬纱在布面扭转或起圈。
(8)双纬:两根纬纱并列或重叠,改变了织物的外观。
(9)缺纬:由于断纬未及时处理,致使纬向全幅缺少一根纬纱。
(10)亮纬:某根纬纱的光泽明显亮于其他正常纬纱。
(11)错纬:一根或部分纬纱明显不同于相邻纬纱,可能是组织错误或其他错误。
(12)拆痕:在织造时拆去织物上的原来纬纱重织时留下的痕迹。
(13)云织:织物上呈现短片段纬纱稀密不匀,似云雾状。
(14)百脚:由于织物组织错乱而在布面上产生锯齿状或线条状的纹路。
4.1.4边部疵点
在布边或者距布边一定距离内的疵点。
(1)松边:布边在长度方向上比布身松弛,边部呈现波浪形。
(2)紧边:布边在长度方向上比布身紧缩,布边内凹。
(3)破边:布边上相邻两根或两根以上的经纱断裂。
(4)烂边:布边上多根纬纱断裂,布边凹凸不平整。
(5)荷叶边:布边边缘呈波浪状。
(6)卷边:织物的边部卷起呈绳状。
(7)边撑疵:边部纱线被擦伤起毛或断裂,有小洞,织物变形。
(8)毛圈边:织物的纬纱呈圈状并在布边外。
4.1.5.整修疵点
面料上的疵点经过整修后留下的痕迹。
(1)整修不良:整修时操作不当,织物的局部起毛、起皱或其他不良的外观。
(2)织补痕:疵点经过织补后留下明显的痕迹。
(3)洗迹:清洗织物上的斑疵留下的痕迹。
4.1.6.染色疵点
在染色过程中产生的疵点。
(1)渗色:染色时的染料渗至周围部分。
(2)折皱色条:染整时织物有折叠,结果在折叠处产生了颜色不匀的经向条痕。
(3)染料迹:由于过浓染料或助剂的作用,使匹染织物的局部颜色呈现与临近部位有差异的分散色块痕迹。
(4)晕疵:染色织物上某些部位呈现较浅的颜色。
(5)水渍:织物有水印痕迹。
(6)斑点:纤维之间的吸色有差异,使染色织物的局部有颜色的斑点。
(7)经向条花:染色织物经向呈现不规则的条状轻微色差。
(8)夹花:由于纤维的吸色差异,织物上形成色泽差异。
(9)前后色差:一匹织物的前后两端颜色有差异。
(10)布边色差:布身和布边的颜色有差异。
(11)左右色差:沿织物的幅宽方向一边与另一边的颜色有差异。
(12)经向条痕:由于织人了一根或多根其他性质的纤维或纱线,吸色不同,染色织物表面出现单根或多根经纱异色、错色。
(13)雨状条影:由于经纱的条干不匀.在染色后,经向呈现雨丝状条痕。
4.1.7.印花疵点
在印花过程中产生的疵点。
脱浆:印花织物上部分花纹缺色。
(2)拖浆:色桨沾在印花织物的花型以外部分。
(3)刮刀条花:印花织物表面有多余色浆或形成经向条痕。
(4)色档:织物上有深浅不一的色档。
(5)对花不准:印花织物上的花纹相对位置彼此不准确。
(6)渗化:前后套色浆不准确的相接,或相邻两种颜色在分界处渗化,致使印花织物部分图案模糊,或呈现第三种颜色。
(7)未上色折皱:印花织物呈现未上色的狭长条。
(8)衬布印:有颜色深浅的印痕。
4.1.8.整理疵点
在整理过程中产生的疵点。
(1)毛毯痕:织物上呈现毛毯组织的纹路或其他压痕。
(2)失光:面料失去了应有的光泽。
(3)擦伤痕:在染整加工中,织物受挤压擦伤而留下的痕迹。
(4)起毛:在整理过程中织物受到摩擦,表面起毛。
(5)压痕:由于整理过程中的压力不匀,织物的某一部位比其他正常部位较亮或较薄。
(6)绳状擦伤痕:由于绳状处理不当,织物上呈现纵向长条痕迹。
(7)分条痕:织物呈现规律性间隔的经向条痕。
(8)针孔:靠近布边处有针孔。
(9)深针痕;针痕的位置进入布身,减少了有效门幅。
(10)布铗痕:在靠近布边处有擦伤发亮、异色的痕迹。
(11)鸡爪印:织物表面有不同程度似鸡爪状的皱纹。
(12)纬斜:纬纱倾斜或弯曲。
4.2面料的品质管理规划
在面料的品质管理规划中有很多要素,这里只分成A、B两类。其中A类针对面料本身;B类则是相关要素。
4.2.1规划中的A类要素
(1)立即检查
面料进厂应立即进行检验。“立即”很重要,如较早发现问题,可以及早采取补救措施。要知道重新生产面料是需要时间的。那些特殊规格的面料,例如经纬纱支或经纬密度不同于市售的常用规格,就需要定织定染,从而需要时间。对那些生产流程长的面料,例如色织面料,会需要较长的生产周期。
(2)抽样检验的数量
进料时根据生产需要进行抽检或全检,抽检时先检验面料总数量的10%进行判定,但如果面料的价值较高,或者客户有需要时,在抽检合格后进行100%检验。如果在检验面料总量的10%以后,发现面料品质不合格。应通知供货方采取相应的措施,在改善面料的品质以后再重新检验。
(3)测试
面料检验项目包括物理和化学性能的测试及外观检验。即外观检验仅仅是面料检验的一部分,目测所不能及的内在质量必须通过实验室测试。大多数客户通常会要求指定测试机构测试并确认面料测试报告。即使客户不要求,收货时也应该对面料取样并测试。
这里特别指出的是:测试样由收货方从大货中随机抽取,因为有些供应商会对测试的样品做一些特定的加工。(供应商为了达到所要求面料品质的调试指标,从技术上来说,已经无很大问题,但会使供应商的成本相应提高。例如缩水率要求小于3%,在技术上可以达到,但是整理成本高,还会造成面料数量的损失,供应商或者制造商就会尽可能地把缩水率定在3%左右。这样在测试时,就有可能达不到既定的缩水率。)
如果测试已经合格,公司可以有选择地测试一些与服装加工密切相关的项目,如测定较多数量面料的缩水率、烫缩率等,以获得准确的工艺数据。
(4)检查数量
在检验外观的同时,也要检查各颜色的数量。
4.2.2规划中的B类要素
(1)面料检验员
配备经验丰富的面料检验员,并要求检验员做好检验记录和检验报告。
(2)检验光线
检验应该在标准的光线下进行,一般为750lx,最好有验布机。
(3)客供面料
即使面料是客供的,仍然需要按公司品质管理规划进行管理和检验.并把检验结果通知客户。
(4)不合格的面料
不合格的面料不开裁,是面料品质管理的基本原则。
4.3面料品质检验的主要项目
4.3.1面料的组织结构
(1)面料的组织
面料的组织是指纱线交织的规律。对机织物而言,是指经纬纱的交织规律,如平纹、斜纹、缎纹以及提花等。对针织物,如平针、罗纹、双反面、经缎等。对收货方的检验员来说,并不需要很精确的去分析纱线的交织规律,只需要检验花纹的外观和大小是否符合确认样。所以可目测或借助放大镜、照布镜观察面料的纱线交织规律和花纹外观。任何组织或者花纹的错误,应该判断为重大疵点。
(2)纱线的支数
纱线的支数表示纱线的粗细,一般很难依靠目测来判断,故不要求检验员去检查。但如果发现面料的厚度、紧密度或重量不符确认样时,可送样品至专业的测试机
构要求测试纱线的纱支。
(3)面料的密度
机织物纬向及经向单位长度内的纱线根数,有经密和纬密之分。如果发现面料的厚度、紧密度以及重量不符确认样时,应该检查此项目。面料密度的测定较为简单,常用的有以下几种方法。
a.分解拆纱法:剪取一定尺寸,一般大于2.54cm×2.54cm(1英寸×1英寸)的矩形试样,从边缘起逐根拆除,然后计数,就得到一定长度内的经纬向纱线根数。如果矩形试样的被拆除尺寸等于2.54cm×2.54cm(1英寸×1英寸),计数结果就得到2.54cm(1英寸)内的经纬纱根数。
b.照布镜分析法:在照布镜窗口,点数经纬纱根数。照布镜的窗口尺寸正好是2.54cm ×2.54cm,点数的结果即为1英寸内的经纬纱根数。
c.斜线光栅密度分析法:一种简易方便的测定方法,但是精确度较差。
在测定经纬密度时,取样位置至少离面料头尾1m以上。
(4)面料的重量
针织物经常需要用单位面积重量(如g/m2)或者单位长度重量(如g/m)来表示其规格,但以前者居多。通过称量每匹重量,可以很方便的用下列公式计算出单位面积重量;每匹重量(g)
单位面积重量(g/m)= 匹长(m)×平均宽度(m)
但是以上的计算未将面料的含水率考虑在内,如果要得到较为精确的单位面积重量,实验室测试需要将面料置于标准状态下(65%RH,20℃)24h。
若有烘箱设备,可取20cm×20cm试样三块放置于烘箱中烘干,得到干燥重量加上公定回潮率可得到公定重量;加上标准回潮率,即可得到标准重量。实践中,常常需要进行公英制单位面积重量的换算,可用公式:
单位面积重量=盎司(安士)/码2 ÷0.02956
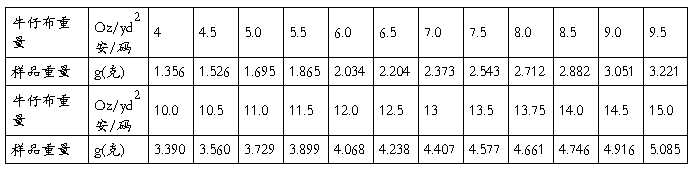
4.3.2面料的幅宽
织造厂最常用的幅宽测量方法是量度布边之间的距离,即面料最外边的两根经纱之间的距离,此为实际幅宽。但在服装生产中,含有边撑针眼的布边是不能用来制衣的,这就需要测量有效幅宽,或称有用幅宽。在测量时,可以测量两侧边撑针眼间的距离。在订购面料时,可以要求织造厂按有效幅宽供货。由于幅宽直接影响制衣排料,因此测量幅宽是重要的检验项目。
在检验面料幅宽时,每匹布应测量三次,即布头、中间和布尾。所谓的布头、布尾也应离布匹的端头1m 。如果在检验时,发现匹与匹之间的幅宽有较大差异,
就要逐匹测量每匹布的幅宽并分档,避免在裁剪时产生“窄幅布” 。 纬向弹力面料由于其布幅的不稳定性,三次测量更为重要。公司在订购面料时,会给出一个幅宽的上下限,例如144/148cm(57/58英寸)、I09/112cm(43/44英寸)等,大货的实际幅宽该在公司订购合同规定的范围内。
4.3.3面料的匹长
从服装生产的角度看,面料的匹长越长越好。从面料生产的角度看,面料的匹长越短,面料供应商越方便。因为面料总会有疵点,有些疵点必须开剪,而开剪必然会缩短面料的匹长。面料裁剪时根据铺料长度进行断长,面料的匹长最好是铺料长度的整数倍,但是在实践中是不可能的。通常的匹长标准不低于27.4m(30码)。
对生产难度大、疵点产生可能性大的面料,由面料工厂可以向公司了解其铺料长度,在得到公司同意后,可以采用相当于铺料长度的匹长。
面料厂为了满足最小匹长,对一些疵点不开剪.仅在布边挂一色线作为疵点标记,即所谓的“假开剪”。应该指出的是,假开剪是一个标记,不等于有了这个标记,疵点就可以接受。为了防止面料厂滥用假开剪,对面料厂一般的要求是:27.4m(30码)以内不允许假开剪,27.4~54.8m(30~60码)不超过一个假开剪,54.8m(60码)以上不超过三个假开剪布头、布尾4.6m(5码)以内不允许假开剪。检验员的责任是检查匹长和疵点数量是否符合要求。
卷装面料匹长的检验在验布机上进行,验布机上的码表可以反映出长度数量。如果是折叠包装的面料,也可以量度折叠层的长度,至少在不同的折叠层量度三次,计算其平均值,则:折叠包装的面料长度=折叠层长度(三次平均值)×层数×2; 面料的匹长不能小于标示长度。
4.3.4面料的花型颜色
(1)花型
面料的花型与确认样核对必须准确无误。
(2)颜色
严格地说,面料的颜色与确认样核对也应准确无误。但从面料的实际生产来说,要求完全一样似乎并不可能。一般的,如果与确认样色差在四级以上(评定变色用灰色样卡)也可接受。如果客户对颜色的要求较高,即使在四级以上,也要将大货面料送客户确认。
在检查大货面料的颜色时,检验员要特别注意同一匹布的前后色差和左右色差,以及匹与匹之间的色差(俗称缸差)。 同一匹布的前后色差和左右色差是不能接受的。而缸差如果在四级以上,一般可接受。如果勉强达到四级(目测有差异)时,生产中必须分色。
进行颜色检验的方法如下所述。
a.在待检面料上剪下全幅宽五英寸长的布条,并标记左右边和匹号、缸号。用该布条在匹布的中间、尾部各核对一次,确保面料无前后色差。
b.在待检面料的布头、中间和布尾,将左右合拢,检查有无左右色差。
c.在其他的待检面料上都剪下这样的布条,同样检验前后、左右的色差。
d.最后把这些布条集中起来,检验匹与匹之间的缸差情况。
e.如果缸差勉强达到四级,并且目测有色差,则需对所有的面料分色。首先根据这些布条的缸差情况,制作缸差卡,作好记号,例如A色、B色等等。用缸差卡去核对所有面料,在面料上也作好A色、B色等记号。将此缸差卡以及各个缸差颜色的数量作为生产技术文件提供给有关部门。
颜色评估的结果与下列三个因素有关:
1.被评估的样品; 2.光源; 3.观察者。
在上述三者中,光源和观察者是可变的因素。尽管人与人对颜色的感觉和认识会有差异,但不足以使评估结果出现很大的偏差。而由于气候、地点和时间等光源条件的变化,有可能使评估结果产生较大偏差。为此,在颜色评估中,标准的人造光源被广泛的采用。灯箱就是一种人造光源,是一种在特定光源条件下进行对色、评定色泽的工具。在灯箱中模拟的标准人造光源有:北向天然光(DAY)、白炽光(A)、紫外光(UV)、冷白荧光(CWF)。可按需要选择,操作简单,能反映色泽的真实情况。其中,北向天然光(DAY)采用的最多。
如果有条件,颜色检验(如原样色差和缸差)可在灯箱中进行。如果没有条件,则可以在自然的北向光下进行对色评级。
4.3.5色牢度
染色牢度是面料的重要品质指标。合格与否的结论必须通过实验室测试。为此可以委托专业的或客户指定的测试机构进行测试。如果测试仅仅是作为内部参考之用,如何选择测试项目并进行判定详见《常用纺织品检测规程》。
(1)水洗色牢度。按照洗标要求选择以下洗涤方法:
a.洗涤的温度:冷、温、热;
b.干衣的方法:滚筒烘干、挂干、平放干燥等;
c.烘干的温度:中温、低温等;
d.整烫:低温、中温、高温;
e.漂白:漂白剂种类;
f.其他洗涤要求。
洗涤后用褪色及沾色样卡进行评级,一般的商业要求为:
变褪色牢度高于4级,沾色牢度在3~4以上。
(2)摩擦色牢度。摩擦牢度的测试较为简单。摩擦牢度分干、湿两种。干摩擦牢度是用于漂白布摩擦染色织物后,观察白布沾色情况。湿摩擦牢度是用含水100%的湿漂白布摩擦染色织物后,观察白布沾色情况。
试验方法是取8cm ×25cm试样两块。一块作干摩擦牢度用,一块作湿摩擦牢度用。试验时将被测试样铺平在摩擦牢度试验仪的试样台上,压牢后另取5cm× 5cm漂白平布固定于摩擦头上。漂白平布经纬方向与被测试样的经纬方向相交成45°角。然后把摩擦头放在试验布上来回摩擦10次,每次来回约1s。一块试样应在经向正面分别磨3次。然后按“染色牢度沾色样卡”评定等级。测定湿摩擦牢度时,摩擦头上的白布应含水100%,评级待干燥后进行。其结果作为内部参考。
一般的商业要求为:干摩擦牢度四级以上,湿摩擦牢度三级以上。
(3)染色牢度褪色样卡和染色牢度沾色样卡
染色牢度褪色样卡和染色牢度沾色样卡是评定染色牢度的工具。以上我们在评定染色牢度时,总是以“级”来描述。“级”是样卡上的读数,也就是试验后样品和原祥色差的读数。
褪色样卡由九对灰色片组成,每对代表不同程度的色差,旁边有级数来表示色差的程度.共分为5、4—5、4、3—4、3、2—3、2、1—2、1九级。五级最好,表示原样和试祥完全没有色差。一级最差。
沾色样卡也是由九对灰色片组成,分别表示不同程度的沾色。五级最好,一级最差。
色样卡是用目测来进行的,为了保证评定的正确性,尽可能在标准的人造光下进行。
4.3.6纬斜与纬弧
纬斜与纬弧是由面料内所产生应力的一种常见疵点,由于其严重影响着服装加工的品质,所以是最重要的检验项目。
一般规定,纬斜与纬弧必须小于2%-3%。从服装加工的要求来说,纬斜与纬弧小于2%更为合适。因为如果纬斜与纬弧大于2%,铺料时就要手工整纬。而大于3%的纬斜和纬弧,应该将面料退回面料厂重新整纬定型。
纬斜与纬弧的量度见图3-2。
4.3.7缩水率
对于服装成品,缩水率是一个重要指标。缩水率过大,会影响服装洗涤后的尺寸,甚至不能穿着。
在服装加工,缩水率是服装样板放大或加长的重要依据。通过确切掌握面料的缩水率,可使裁片在加工后的尺寸规格符合标淮。
对于常规结构的面料结构而言,要求机织服装的缩水率小于或等于3%,针织服装的缩水率小于或等于5%—6%。应该注意的是,该指标的测试条件不是简单的水浸,而是模拟了实际的洗涤状况。
作为客户品质管理体系的重要部分,客户会委托专业的测试机构对面料进行测试,以保证服装的服用性能,即在服用洗涤的过程中不会产生收缩,服装厂的生产也必须在测试通过以后才能进行。
尽管这样,测试仅仅是对样品而言,问题是整批面料的缩水率是否与样品一致呢?作为内部的参考标准,可以依《常用纺织品检测规程》将水洗烘干后的样品,至少放置4h,在松弛的情况下,自然铺平,按照洗标要求的整烫方法,整烫后测量洗后的尺寸,并按以下方式计算缩水率:
水洗前面料的长度(宽度)- 水洗后面料的长度(宽度)
缩水率= ×100%
水洗前面料的长度(宽度)
对水洗的服装来说,面料的缩水率是影响服装尺寸的重要因素,也是确定服装样板尺寸的重要依据。因此需要在服装生产前对面料的缩水率进行测试。测试的具体步骤如下:
(1)抽取10%的布卷,在每个布卷上剪下60cm×60cm的试样。在每块试样上标上50cm×50cm正方形(划线或车线)注明匹号、缸号。
(2)所有的试样按常规成衣水洗工艺洗涤,客人有要求按所要求的洗涤方法进行。
(3)测定每一块面料水洗后的尺寸,并计算其缩水率。
(4)同时观察面料水洗颜色的变化,水洗后的颜色必须满足客户的要求。一般颜色的差异也应该在四级以上。如果差异在四级以下,就要制成色卡让客户确认。客户确认后,测试每一匹或每—卷布的水洗颜色,并分档归类。
(5)如果测得的缩水率相等或非常接近,可按所测得的缩水率制作或适当修改服装样板。通过缩水率的测试,可以预先估计成衣水洗过程中的最大尺寸变化,使服装的尺寸稳定并能够满足规格要求。
(6)如果测得的缩水率过大,可将面料退回面料厂重新整理。
(7)如果测得的缩水率各不相同,就需要用以上方法测试每一卷或每一匹的缩水率,并分档归类,重新制作适合各种缩水率的服装样板。当然也可以把那些缩水率大的面料退回面料厂重新整理。
4.3.8烫缩
大多数服装要经过整烫,面料(特别是合成纤维纯纺及其混纺织物)在受热以后会产生收缩,这样给服装尺寸的掌握带来了一定的困难。有时也会形成皱痕(例如当面料和衬料的受热收缩率不一致时)等不良的外观。为了保证服装在整烫以后的尺寸和外观要求,有必要掌握其烫缩率。
烫缩率的测试应该按该产品的最终整烫条件来选择。如果最终的整烫条件是一般的干烫,则可以测试干烫收缩率。如果最终的整烫条件是蒸汽熨烫,则可以测试汽蒸收缩率。不管测试哪一种烫缩率,都要注意以下几点:
(1)采样:采样时,都要在布匹的头部或尾部除去2m以上。取50cm长的布料,并记录好长度和宽度数据。
(2)熨烫:按大货的工艺执行。
(3)测试:待凉透后,测量试样的长度和宽度,然后计算该面料的收缩率。
熨烫后长度(宽度)收缩量
熨烫收缩率= ×100%
熨烫前试样长度(宽度)
4.3.9熨烫折缝性
服装经过熨烫以后,不仅仅是尺寸的变化,还包括了色泽变化和形状变化等等。为了得到最好的外观,对这些变化在生产前加以试验,在生产中加以控制。当然,这也许不是检验部门的工作,但是技术或工艺部门必须做这一工作。
折缝效果是熨烫性能中一项比较重要的测试。用以评价服装面料在缝制过程中的压烫或缝制后的压烫整体效果。其测试方法如下:
(1)从距布端1m以上、距布边10cm以上的部位裁取试样。
(2)将试祥折叠,放置在有吸气能力的烫台上,可以用全蒸汽工业烫斗,也可以用家用熨斗。采用全蒸汽工业熨斗时,蒸汽压力196.4—392.8kPa(2~4kgf/cm2),施以适当的压力,压烫和汽蒸时间为10s左右,以适当的速度往复三次。温度一般控制如下:
棉、麻 180℃
羊毛、粘胶、铜氨纤维 160℃
涤纶、维纶 140℃
真丝、腈纶、锦纶 120℃
丙纶、氯纶 l00℃
(3)待试样静置24h.进行测评。测评一般采用视觉评价,即观察熨烫后折缝的整体效果(图3—3),图中A为一种理想的效果,B和c则为不良的效果。
图中A良好 图B 不好 图C 不好
4.3.10熨烫色牢度
面料熨烫以后有可能会产生变色、沾色等疵点。通过熨烫试验,可以了解面料
的熨烫性能。熨烫试验可以在加热装置中进行,也可以使用熨斗。大多数服装厂,是采用熨斗来进行熨烫试验。
熨斗的温度用表面温度计或感温纸测定,试样大小一般为40mm×100mm。熨烫条件可以按照洗标的要求进行,观察熨烫后有无发生变色、沾色和烫黄等现象。
应指出的是该试验仅仅是作为熨烫工艺的参考,而不能代表烫色牢度的实验室测试。
4.3.11可缝性
面料是通过缝合状态来满足款式和人体的要求,在一定的缝合工艺条件下,可缝性就与面料的特点、缝线的特点有关。在面料一定的情况下,可以调整缝合工艺条件来满足缝合要求。通过可缝性的测试,可以事先了解缝合的强度和缝合的效果。可缝性的测试也是一种工艺试验。
很多可缝性指标的测试需要在实验室中进行,缝缩率的测试稍简单,并且缝缩率对保证成衣尺寸和线缝美观有着一定的意义。缝缩率是指面料在缝合后,在线迹周围产生的缝皱程度。
从面料上距布端lm、距布边10cm以上的部位裁取经纬纱向各不少于6块的试样。试样应平整,无疵点。每个试样不含有相同的经纬纱,试样尺寸为500mm x50mm。长度方向与接缝方向平行,在长度方向的两端分别做上记号,其尺寸为70mm、30mm,如图3—4中的A、B两点。
将两块相同方向的试样重叠,使试样在一定的缝制条件下,不用手送料,在试样中间缝一直线。然后计算缝缩率S:
缝制前两记号间的长度 -- 缝制后两记号间的长度
S= × 100%
缝制前两记号间的长度
以6块组合试样的平均值表示经纬向的缝缩率。
4.4面料的疵点检验
面料总是有疵点的。面料厂的责任是把疵点数量和程度降低到最少,以满足服装加工的要求。接收方通过检验,确认疵点的程度和数量是否在可接受的范围内。
长期以来,关于疵点的程度和数量可按受的范围常常是面料厂和服装厂矛盾的焦点。面料厂按国家标准中的疵点评分规定进行捡验评等,但也有一些面料厂没有按照国家标准去做。服装厂由于不熟悉这方面的国家标准,常常处于被动状态。但面料疵点确实影响着服装的可加工性和品质。
执行目前的国家标准需要检验者有丰富的经验或经过专门的培训。由于检验者目光不同,检验的结果也不同,这对客户或接收方不够公平。所以,在客检中已经很少采用国家标准进行检验。
在国际贸易中,美国“四分制”检验方法被广泛采用,它是纺织、成衣、贸易都能接受的标淮,是一种实用性和可操作性强的检验方法。
4.4.1四分制检验的内容
1.四分制扣分标准
四分制是将目测到的疵点进行量度。并按表3—2所示的规定进行扣分。
在应用四分制进行检验时,需注意以下四点:
(1)疵点扣分以看得见为原则,轻微的,不易觉察的疵点不予扣分。
(2)一码内的疵点扣分不超过4分,超过的必须开剪。
(3)对挂有假开剪的,也同样按以下标准扣分。
(3)任何形式的破洞、严重影响外观的疵点一律扣4分。
表3—2 四分制扣分标准

2.100平方码疵点评分
有些公司以每100码扣分作为评定该批面料是否可以接受的标准,作为—个公司的标准未尝不可。但是每100码扣分是一个绝对值,对于不同幅宽、不同匹长的面料缺乏比较意义。为了能直观的说明某批面料的品质状况,可用100码的疵点评分予以表示。
首先将被检布匹的疵点扣分予以记录在《面料检验记录表》上,然后按下列公式计算一匹(卷)布的每100码2的疵点评分(K):
(1)机织物
疵点扣分累计×36
K= × 100
抽检码数×幅宽(英寸)
(2)针织物
疵点扣分累计×面料克重(g/码2)
K= ×100
被检布匹的重量(g)
3.K值的确定
100码2的疵点评分直观的反映了该匹布的疵点情况,例如计算的结果为20分/100码2 ,这就表示每平方码有0.2分的疵点,应该说这是可以接受的。
问题是如何来确定合理的K值?
考虑到疵点常常与该品种的生产难度有关,即生产难度越大的品种,疵点产生的可能性越大,盲目的追求高品质并不现实。故在确定K值时,要考虑到品种的特点。如牛津纺、青年布的K值可稍高于普通织物。
K值也与客户的要求有关,如果客户对面料的品质要求高,K值就应稍低。
K值与面料的价值有关,高价值的面料,其K值理应稍低。
K值应该是供需双方对品质的共识。
在一般的情况下对于常规面料,K值可取不大于25。对生产难度大的品种,K值可取25~30。
4.K值的意义
K值在贸易中有着品质的意义。在服装生产中,还有着指导生产的意义。
(1)当K值小于10,说明该面料的品质情况良好,在服装加工中可以使用。
(2)当K值大于10,小于20,说明该面料品质情况较好,在裁剪铺料时稍注意一下疵点即可。
(3)K值大于20,小于25,说明面料的品质可以接受。在裁剪铺料时,要注意发现疵点,对疵点做必要的记号或剔除。
(4)当K值大于25,小于35,根据品种及客户要求,该面料也许可接受。但在服装加工时要特别注意对成衣品质的影响。例如除了在裁剪铺料时对疵点做记号并剔除外,也许还需要100%检验裁片。
(5)当K值大于35,该面料不予接受。
4.5检验面料的方法和步骤
4.5.1面料的基本品质要求
合格的面料应满足以下要求。检验时应该对每一个细节予以注意。如果有必要,可以将一些经常性项目做一个目录,以防止遗漏。
(1)面料的匹长大于27.4m(30码)或符合定单要求。
(2)面料的实际匹长不应少于码单1%。
(3)假开剪的数量不能超过订单要求并且布头、布尾4.6m(5码)以内不能有假开剪。
(4)面料的幅宽应该符合订单要求。
(5)面料不能有前后色差、左右色差及色花。
(6)面料的颜色与确认样比较,其颜色差异必须在4级以上。
(7)匹与匹的颜色差异必须在4级以上。
(8)面料的纬斜或纬弧必须小于2%~3%。
(9)100码2疵点评分应小于30或40。
(10)染色牢度、缩水率及其他测试要求应符合标准。
(11)面料的组织规格符合订单要求。
(12)面料的外观和手感符合客户要求或确认样。
4.5.2面料检验的步骤和方法
1.确定受检数量
a.少于或等于1000码的, 100%检验,;b.1000码至10000码以内的,抽验1000码;(a.b.项在生产紧急时,抽取不少于总数的10%进行检验)c.超过10000码的,抽10%,或按客户要求确定检验数量。
2.选择受检包号或卷号
一般面料厂都有细码单,以说明面料每一卷或每一匹的数量。检验者可以根据需要挑出需要检验的布卷或布匹。如果一批受检布料含有多种颜色,那么每种颜色都要检验到。最好按照每种颜色所占该批面料的比例来确定各种颜色的检验数量。例如,某订单各种颜色的数量及抽样方案如表3—4:
按颜色确定检验数

另外必须注意,抽验是随机的,这可以保证检验结果的正确可靠。
3.检查基本项目
按本指导书“面料品质管理的主要项目”以及 “面料的基本品质要求”,检验面料的外观、重量、密度、手感、花型、颜色、幅宽、匹长、纬斜或纬弧等。如果基本项目不合格,就没有必要再检验疵点,可立即把其归入不合格的布卷。在基本项目合格的前提下,可以做疵点检验。
4.检查数量
核对实际数量与供应商细码单、包内码单以及布卷标记码数是允差不超过1%,超过视为不合格。
5. 检验疵点
不管是手工还是在验布机上检验,拉布的速度应该合适,一般以足够看清为原则。不合适的速度会影响验布的准确性。
在做疵点检验时,要注意只对影响服装加工的、会影响外观的可见疵点扣分。
在检验同时作好记录(表3—3),并计算每匹(卷)布的100码2评分。
6. 发现了疵点,应在布面上加返工标志如返工箭头纸、牛仔布用白色粉笔划记,以便铺料时随时发现如果该批面料不合格需退回面料厂,也方便向面料供应商说明疵点的状况和退货理由。
7. 统计不合格的布卷数
此时,已经可以知道受检面料中的每卷(匹)布是否合格,依据《面料检验记录表》中的检查数据结果进行统计、汇总。
8. 确定该批布是否合格
作为服装厂或客户,当然希望每一卷(匹)均为合格品。但是对于面料厂是不公平的。对于面料厂,面料总会有疵点的观念也是不能接受的。因此需要有一个双方接受的标准。
一般的采用AQL抽样标准检验。常规的面料采用AQL 4.0,LEVELⅡ,SINGLE标准进行检验。特殊情况下面料的检查需与客户沟通,这与面料的价值有关。如果是采用普通检验,可参考表3—5。通过统计不合格的布卷,就可确定该批布是否合格。即当实际不合格的布卷数(匹)小于或等于表中可接受的不合格布卷数(匹),该批面料可以接受。
表3-5 普通抽样检验标准
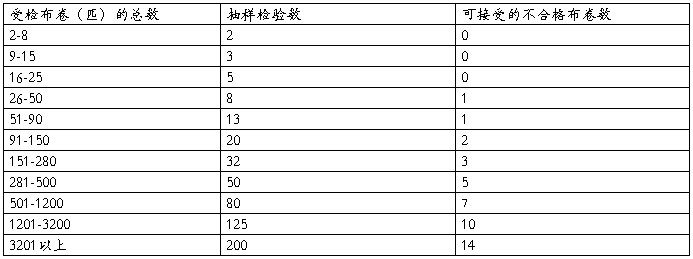