冷作工操作试题
单位: 编制人: 审核人:
命题依据:《大型立式圆柱形储液罐制造与安装》(出版社:中国石化出版社 主编:徐至钧 燕一鸣 出版日期:20##年3月6日)
一、试题名称
大型立式圆柱形储罐底板的排版、预制加工及底板铺设
二、试题内容
大型立式圆柱形储罐底板的排版、预制加工及底板铺设的内容,请回答下列问题:
1. 底板的排版方式大致分为哪三种。5分
2. 底板预制加工施工准备包括的内容。5分
3. 预制的一般规定:
3.1 样板的一般规定;5分
3.2 切割下料及坡口加工的一般规定;5分
3.3 焊接接头坡口的型式;5分
3.4 其它要求。5分
4.底板的预制:
4.1 底板编排下料的基本要求;15分
4.2 罐底边缘板的安装质量要求;15分
4.3 中幅板和边缘板的结构;10分
4.4 罐壁和和罐底间角焊的结构;5分
5.底板的铺设。25分
试题答案:
1. 底板的排版方式大致分为:
条形排版方式、丁字形排版方式、人字形排版方式。
2. 底板预制加工施工准备包括的内容:
道路的平整、基础的验收、图纸及技术资料、施工技术力量、材料、设备、工夹具以及可能出现的异常气候(大风、雨、雪、酷暑、严寒等)的应急措施,与其它工程施工的交叉配合等。
3.1样板的一般规定:
(1)当构件的曲率半径≤12.5m时,弧形样板的弧长不得小于是1.5m;当构件的曲率半径>12.5m时,弧形样板的弧长不得小于是2m。
(2)直线样板的长度不得小于1m。
(3)测量焊缝角变形的弧度样板,其弦长不得小于1m。
3.2 切割下料及坡口加工的一般规定:
(1)钢板切割及焊缝破口加工,宜采用机械加工或自动、半自动火焰切割加工;罐顶板和罐底板的圆弧边缘,可采用手工火焰切割加工。
(2)对于对接接头、厚度>10㎜的钢板和用于搭接接头、厚度>16㎜的钢板,板边不宜采用剪切加工。
(3)当工作环境低于下列温度时,钢板不得采用剪切加工:普通碳素钢—16℃;低合金钢—12℃。
(4)钢板边缘加工面应平滑,不得有夹渣、分层、裂纹及熔渣缺陷。火焰切割坡口产后的硬化层,应磨除。
(5)屈服点>390MPa的钢板,当用于底圈和第二圈罐壁板时,应对坡口表面进行磁粉或渗透擦伤。
3.3 焊接接头坡口的型式:
焊接接头的坡口形式和尺寸,当无图纸无要求时应按现行国家标准《手工电弧焊焊接接头的基本型式与尺寸》或《埋弧焊焊接接头的基本型式与尺寸》的规定的选用。纵缝气电焊及环缝埋弧焊的接头型式,宜符合下列要求:
(1)纵缝气电焊的对接接头的间隙,应为4~6㎜,纯边不应大于1㎜,坡口宽度应为16~18㎜,坡口型式可为X型或V型。
(2)环缝埋弧焊的对接接头的坡口角度为45°±2.5°,纯边不应大于2㎜,间隙应为0~1㎜,坡口型式可为K型或单边V型。
3.4 其它要求:
(1)普通碳素钢在环境温度低于—16℃、低合金钢在环境温度低于—12℃时,均不得进行冷矫正和冷弯曲加工。
(2)所有预制构件在保管、运转及现场堆放时,应采取有效措施防止变形、损伤和锈蚀。
4.1 底板编排下料的基本要求:
根据设计图的技术要求,施工中按材料到货情况绘制出底板排版图,符合下列规定:
(1)排板图直径宜按设计放大0.1~0.2﹪。若焊缝密集(板窄、板短)及基础表面锥度大(即基础中心高出的多)应放大比率加大,反之适当减小些。
(2)其他如边缘板的宽度、中幅板的最短板长和最窄板宽等要符合所执行的标准的规定。
(3)当中幅板采用对接接头时,中幅板尺寸允许偏差应符合规范中对壁板预制允许偏差的规定。
(4)弓形边缘板的尺寸允许偏差应符合规范的规定。
(5)厚度≥12㎜的弓形边缘板,应在两侧100㎜范围内,按《压力容器用钢板超声探伤》的规定进行检查,检查结果达到Ⅲ级标准为合格,并应在坡口表面按规范规定进行磁粉或渗透探伤。
4.2 罐底边缘板的安装质量要求:
(1)底板边板与壁板第一圈板材质应相同厚度亦相对应。
(2)边板组对、焊接、检验必须严格按规范进行。
(3)大角字缝点焊前要对焊口进行“净化”处理,清除污物和水、油、锈等。
(4)避免强制组对点焊,以减少组对附加应力。
(5)内外交替施焊,分段退步,多道焊接,并保证圆滑过渡。
4.3 中幅板和边缘板的结构:
(1)中幅板一般采用搭接焊缝,也有采用带垫板的对接焊缝。搭接宽度最小为5倍底板厚度。为了保证边缘板比较平坦,因而中幅板搭在边缘板上面较好,搭接宽度不小于60mm。底板为单面搭接焊,为了保证其严密不漏,全部搭接焊缝至少焊两遍成形。在罐底上三块钢板重迭部位的相互间距以及重迭处与壁板之间的距离均不小于300mm。在三块钢板重迭处,为了减少焊缝高度和应力集中,可采用如图所示结构:
(2)边缘板在与壁板相焊接的部位做成平滑支承面,边缘板对接焊缝下面一般采用厚度不小于4mm、宽度为50mm的垫板,当边缘板厚度不大于6mm时,可不开坡口,焊缝间隙为1.5倍板厚,当边缘板厚度大于6mm时,应采用V型坡口,对口间隙≥3mm,宜采用内大外小式不等间隙。
4.4 罐壁与罐底间角焊的结构:
罐壁与底板之间的角焊缝,非常重要。角焊缝是采用双面连续角焊的T型接头,角缝尺寸过大过小都不好,尺寸过小焊缝接头强度不够,尺寸过大会造成接头刚度过大,使接头处应力加大,其焊角尺寸接罐壁与底板(或边缘板)两者中较薄者来确定。此焊缝应采用多遍成型以提高焊接接头的冲击韧性。
5.底板的铺设:
(1)在基础上划出两条互相垂直的中心线,并划出弓形边缘板外圆周线。弓形边缘板的外圆周线应以铺设半径为准。铺设半径按下式计算:
Rc=(Ro+na/2π)/cosθ)式中
Rc:弓形边缘板铺设外半径(mm);Ro:弓形边缘板设计外半径(mm);n:弓形边缘板的数量;a:每条焊缝收缩量,手工焊取3;θ:基础坡度夹角(°)。
(2)将底板向下的一面涂刷防腐涂料。
(3)按排版图铺设底板,铺设的顺序是:
A.先铺中间一块中幅板,校对其位置后,再向两端逐块铺设中间一整条底板。
B.从中间一条开始,向两侧逐条铺设中幅板。每条中幅板都是自中间向两端依次铺设。
C.铺设边板:先铺好一块,再向两侧逐块铺设。
D.注意底板的搭接宽度误差不得超过±5mm。
E.整个罐底板铺设后,用盘尺或地规进行划圆检查,尺寸应符合设计规定。
(4)壁板下部200~250mm范围内的边板,由原来的搭接改为对接,对口间隙为8~10mm。依次割出间隙后,下面衬以垫板,用火焰将钢板过渡处烤红,再将对口打平。
(5)铺设底板时,边铺边少量点焊,防止底板移动,焊接前将这些点焊点铲平,再进行焊接。
(6)底板铺设后,局部凹凸度应不大于15mm。
(7)边板的对口焊缝应沿圆周至少留出四条收缩缝,等其他对接缝焊完后进行焊接。
(8)底板焊接时,留出边板及边板与中幅板间的联结焊缝暂不焊接。
考核内容及评分标准:
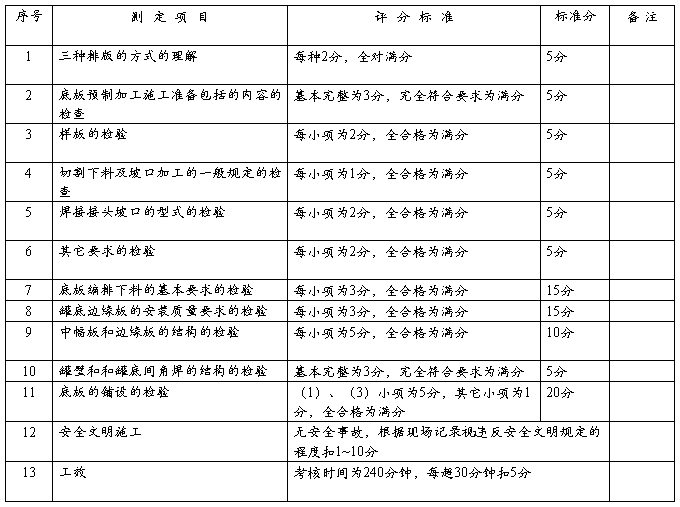
第二篇:高级技师实操题
用102J对101B氮气升温操作程序
一.174D相关阀门和盲板的确认
1.确认NG1000-16″到174D的16″阀和1″旁路关。
2.确认NG1000-16″到174D的16″阀和1″旁路加盲板。
3.确认174D到173J入口截止阀关。
4.确认174D到173J入口加盲板。
5.确认174D到102J截止阀开。
6.确认174D到102J盲板在通位。
7.确认174D顶上FG1004—4″的双截止阀关,中间导淋开。
8.确认174D顶上FG1004—4″上加装临时盲板。
二. 102J相关阀门和盲板的确认
1.确认102J出口到101B的两道截止大阀开。
2.确认102J出口到101B的盲板在通位。
3.确认NG1080-6"到102J出口截止阀关。
4.确认NG1080-6"到102J出口盲板在盲位。
5.确认102J出口到175C的截止阀关。
6.确认102J出口到175C的盲板在盲位。
三.108D、101B及103D相关阀门和盲板的确认
1. 打通108DA/DB/DC流程,108DB/DC串联操作。
2. 确认108DA/DB/DC流程中盲板在通位。
3. 确认HV1108阀及前截止阀关。
4. 复位I-101联锁。
5. 复位I-102J联锁。
6. 开FV1001。
7.开MOV1010。
8. 确认TV1004开。
9. 确认TV1010开。
10. 确认HCV1043开。
四. 低变炉及其后设备相关阀门和盲板的确认
1. 确认104D2进口阀MOV1008及1″旁路阀关。
2. 确认104D2出口阀MOV1007及1″旁路阀关。
3. 确认MOV1009阀开。
4. 确认到121D的MOV1005及2″旁路关。
5. 确认HCV1045及前截止阀关。
6. 确认PG1063-10″到104D2出口的截止大阀开。
7. 确认PG1063-10″到104D2出口的盲板在通位。
8. 确认104D2出口PG1064--12″上的两截止阀关。
9.确认104D2出口PG1064--12″上的盲板在盲位。
10. 确认PG1064-12″到143C的截止阀开。
11. 确认PG1064-12″到143C的盲板在通位。
12. 确认系统所有导淋排放关。
13. 确认FV1022及切断阀关。
14. 确认FV1023及切断阀关。
AAA003 小冰机开车程序
AAA004 表冷器104JTC开车程序
AAA005 冷氨泵2101J开车程序
废热锅炉101C爆管的现象与处理
一.事故判断
1. 发现高压蒸汽压力下降,蒸汽产量下降。
2. 发现142D1工艺冷凝液量增加。
3. 发现101C后温度下降,高变入口温度及床层温度下降。
二. 事故处理
(一). 系统停车
1.主控按HS1251。
2.按HS1206切空气。
3.将103J停车。
4.将102J打循环。
5.将105J/J1停车。
6.通知尿素停车并控制PV1099。
7.将快锅加至满负荷。
8.按HS1004切低变。
9.按HS1253切甲烷化。
10.切130D。
11.关闭MOV1005。
12.停脱碳循环。
13.将氨回收单元停车。
(二). 确认联锁结果正确
1.确认HV1101及HV1103关闭,FV1024及PV1109A关闭。
2.确认XS1128动作,HV1028打开。
3.将FV1020手动减小开度直至全关。
4.确认FV1003及FV1103已关闭;XV1207已关闭,XV1206打开;FV1044保持2T/HR左右流量;PIC1050在自动状态。
5.确认XV1220A/B已关闭,XV1220C已打开,PV1001及PV1002已关闭。
6.确认XV1222A/B已关闭,XV1222C已打开,PV1029已打开。
7.确认膨胀机已联锁。
8.确认FV1001及MOV1010已关闭。
(三). 对系统进行后处理
1.切除加氢气。
2.关闭HV1102,关闭LV1013及其前截止阀。
3.控制一段炉降温速率,控制进入一段炉的乏气量及炉膛压力,防止转化管温度骤然变化。
4.关闭冷箱进出口截止阀,确认MOV1017,MOV1018已关闭。
废热锅炉131C爆管的现象与处理
一.事故判断
1.发现PIC1040及低压蒸汽压力明显升高。
2.发现系统压力PIC1005下降。
3.发现103JTC及104JTC真空度明显上升。
4.发现各个蒸汽及冷凝液电导上升。
二.事故处理
(一). 对系统的停车
1.系统在PIC1004放空。
2.关闭LIC1020及前后截止阀。
3.关闭PIC1040及前截止阀。
4.打开PIC1016将中压蒸汽减压至低压,稳定低压管网压力。
5.将103J停车。
6.将105J/J1停车。
7.通知尿素停车并控制PV1099。
8.将快锅加至满负荷。
9.按HS1004切低变。
10.按HS1253切甲烷化。
11.切130D。
12.关闭MOV1005。
13.停脱碳循环。
14.将氨回收单元停车。
(二). 确认联锁结果正确
1.确认HV1101及HV1103关闭,FV1024及PV1109A关闭。
2.确认XS1128动作,HV1028打开。
3.将FV1020手动减小开度直至全关。
4.确认膨胀机已联锁。
(三).对系统进行后处理
1.将脱硫加氢由外界供给。
2.关闭HV1102,关闭LV1013及其前截止阀。
3.控制一段炉降温速率,控制进入一段炉的乏气量及炉膛压力,防止转化管温度骤然变化。
4.关闭冷箱进出口截止阀,确认MOV1017,MOV1018已关闭。
高压锅炉给水泵104J倒104JA运行
一. 倒泵前准备工作
1.确定104-JA启动开关在手动位置。
2.确认高压汽包液位稳定。
3.强制汽包液位低联锁。
4.增加快锅负荷,中压蒸汽保持1-2吨放空量。
5.确认各仪表正常投用。
6.确认104-JA油系统运行正常。
7.给104-JA盘车一周以上,确认灵活无卡涩。
8.确认104-JA暖泵合格后关闭1"暖泵双截止阀。
9.给104-JA泵体排气。
10.确认104-JAM送电。
11.确认104-JA泵体循环冷却水进出口总阀开。
12.确认104-JA泵体机械密封冷却水上水阀开。
13.确认循环冷却水回路打通。
14.确认104-JA入口阀开。
15.确认 104-JA出口MOV-1033电动阀已送电。
16.确认 104-JA出口MOV-1033保持2-3%开度。
17.确认最小回流线截止阀开。
18.确认泵体平衡回流阀开。
二.倒泵操作
1.通知主控联系电气启动104-JA。
2.调整104-JA平衡管压力,控制平衡管压力与入口压力之间的压差在150KPa。
3.主油泵出口压力大于440 Kpa后停运104-JA润滑油辅油泵。
4.将润滑油辅油泵开关投自动。
5.根据FI-1006和FI-1106变化,调整HIC-1110输出,降低104-JT转速,减少104-J输送流量,现场调整增加MOV-1032开度,增加104-JA输送流量,保持FI-1106流量稳定扣5分。上述调整交替进行,应避免高压锅炉给水流量大范围波动。
6.当HIC-1110输出降至0%,主控通知现场停104-J。
7.关闭104-J出口电动阀MOV-1032。
8.确认辅油泵104-JLJ启动运行。
9.通过主控HS-1114停车或现场打闸停下104-J/JT。
10.关闭104-JT主蒸汽截止阀。
11.确认104-JT主蒸汽截止阀旁路阀关闭。
12.在104-JT转速低于300 rpm以下时关闭密封蒸汽供给阀。
13.在104-JT完全停止后关闭排汽阀。
14.确认排汽阀旁路阀关闭 。
15.关冷凝液抽吸器喷射蒸汽截止阀。
16.关冷凝液抽吸器出口排放阀。
17.开冷凝液收集罐底导淋阀。
18.打开蒸汽放空阀。
19.打开中压蒸汽入口管道导淋。
20.打开联锁切断阀前后导淋。
21.在停车后每15分钟盘车90°直至透平缸体温度降至80℃,轴承温度降至60℃,停盘车。
22.在汽包液位稳定后投用汽包液位低联锁。
二. 104J/104JT交出检修
1.确认104-J出口MOV-1032全关。
2.确认暖泵阀全关。
3.关最小回流线截止阀。
4.关泵体平衡回流阀。
5.关104-J入口阀。
6.开泵体排放阀排尽泵体锅炉给水。
7.泵体温度降至80℃关闭泵体循环冷却水进出口总阀。
8.轴承温度降至60℃,停下104-JLJA,停止油循环。
9.油循环停止后关闭油冷器冷却循环水进出口阀。
10.联系电器办理断电票,断掉104-JLJA动力电源。104-J/JT交出检修。
贫液泵108J倒108JA运行操作
一. 倒泵前准备工作
1.未将108JA起动开关置于手动位置扣2分
2.未确认脱碳系统运行稳定扣1分
3.未确认脱碳系统各塔液位稳定扣1分
4.未强制联锁FSLL1214扣1分
5.未确认各仪表正常投用扣1分
6.未确认进出口电动阀已送电扣1分
7.未确认108JAM已送电扣2分
8.未确认各油杯油位正常,油质好扣1分
9.未确认油质清亮扣1分
10.未给108JA盘车一周以上,确认灵活无卡涩扣2分
11.未确认108JA入口电动阀全开扣1分;
12.未确认108JA已暖泵合格后关闭暖泵线截止阀扣1分
13.未确认108JA密封水已正常投用扣2分
14.未给108JA泵体排气扣2分
15.未确认轴承箱循环冷却水投用扣1分
二. 倒泵操作
1.未将108JA出口电动阀开3~5%扣3分
2.未联系电气启动108JA扣2分,
3.未注意调节FIC1014,维持贫液量的稳定,避免流量大幅波动扣2分。
未边开大108JA出口电动阀,边降108JT转速,两边交替进行扣3分
4.未密切关注贫液流量、各塔液位及吸收塔出口微量扣3分
5.当108JT降至最低转速,108JA出口电动阀全开,未全面检查108JA运行情况扣4分(包括电机温度、轴承温度、有无杂音、有无滴漏,每漏一项扣1分)
6.若一切正常,控制入口蒸汽阀,继续降转,当转速在500RPM未关闭密封蒸汽扣2分 未通知主控手击脱扣阀复位杆顶部,脱扣阀关闭,透平停车扣2分
7.在降转速过程中未及时确认辅助油泵自启动,否则手动启动辅油泵扣3分
8.未全关蒸汽切断阀扣2分
9.当透平完全停止后未关闭排汽阀扣2分
10.未确认排汽阀旁路阀关闭扣2分
11.未关冷凝液抽吸器喷射蒸汽截止阀扣2分
12.未关冷凝液抽吸器出口排放阀扣2分
13.未关闭到表冷器管线上的截止阀扣2分
14.未开冷凝液收集罐底导淋阀扣2分
15.未打开蒸汽放空阀扣3分
16.未打开中压蒸汽入口管道导淋扣3分
17.未在停车后应每15分钟盘车90°直至透平缸体温度降至80℃,轴承温度降至60℃,停盘车扣3分
主控调整脱碳系统运行稳定、贫液流量稳定后,未投用联锁FSLL1214扣3分
三. 108J/108JT交出维护与检修
1.关闭108J进出口电动阀
2.关密封水供给阀
3.停108J辅油泵
4.联系电气辅油泵108JLJAM断电
5.打开108J泵体导淋,泵体排液
6.打开进口过滤器导淋排液
7.说明溶液排至地下槽回收,溶液排尽后交出检修。
甲烷化超温联锁事故处理程序
一. 停车范围判断
未判断甲烷化后工序全面停车
二. 联锁确认
未确认甲烷化炉联锁报警扣1分
未确认联锁结果正确,否则应按联锁逻辑结果将阀门打开或关闭扣2分
未确认103J因入口压力低联锁跳车扣2分
未确认HV1101关闭扣2分
未确认XV1103关闭扣2分
未确认FV1024关闭扣2分
未确认PV1109A关闭扣2分
未确认XS1128动作,HV1028打开扣2分
四. 甲烷化联锁事故处理
系统未在PV1005放空扣5分
系统负荷未减至50%左右运行扣5分
未立即通知尿素停车扣3分。
未通知尿素立即退蒸汽或用PV1099控制给尿素蒸汽量扣2分。
快锅未加至接近满负荷运行扣2分
FV1020未手动减小开度直至全关扣2分
高压蒸汽未经PIC1018及HIC1028减压并平衡管网压力扣3分。
未增加101B主燃料气扣2分。
未调整炉膛压力,防止废气退出一段炉,炉膛压力过低触发PI1059超量程,PAHH1059联锁动作,扩大停车范围扣2分。
未关闭LV1013及其前截止阀扣3分。
105J/J1未视蒸汽平衡和停车范围确定是否停车扣2分。
未关闭冷箱进出口截止阀扣2分
未确认MOV1017,MOV1018已关闭扣2分
当131JX密封气压力低于润滑油总管压力时,未停其油泵扣2分
未将脱硫加氢改由142D2供给扣3分
在合成回路压力低于10MpaG时,未全关HV1019扣2分
在合成回路压力低于10MpaG时,未全关HV1102扣2分。
未停氨回收单元扣3分
PV1107未投自动压力控制扣2分
PV1109B未投自动压力控制扣2分
PV1033B未投自动压力控制扣2分
未关闭PV1108扣2分
未关闭PV1033A扣2分
未切去115C驰放气扣2分。
未停113J/JA扣2分
未停2101J/JA扣2分
未切327C扣2分。
五. 恢复开车
稳定前系统,查找联锁原因,及时排除故障,尽快恢复开车扣3分
增压机105J1跳车事故处理
一. 停车范围判断
(一). 系统送热氨产品工况
105J1跳车,停冷氨泵,系统调整。未判断正确扣5分
(二). 系统送冷氨产品工况:
105J1跳车,系统调整,及时恢复105J1开车,若不能及时恢复,系统PV1004放空,合成单元、氨回收单元停车。
二. 事故处理
(一). 尿素运行正常,系统送热氨产品工况下的事故处理
未关闭LV1015A扣3分
未停124J/JA扣3分
未注意调节各闪蒸槽的液位扣3分
由于105J的负荷降低,105JT高压蒸汽用量减少,未注意调整好高压蒸汽系统避免压力大幅度波动扣3分
未给快锅加负荷保证蒸汽有一定富裕量扣3分。
未根据尿素的用氨量调整前系统负荷,保证尿素用氨量高于合成产氨量扣4分
未确认152D出口到120CF1的平衡管线阀门打开,防止152D超压扣3分
未查明原因,及时恢复105J1开车扣3分
(二). 尿素停车或113J/JA故障,系统全部送冷氨产品工况下的事故处理
未注意调整小冰机高压氨受槽压力,防止小冰机跳车扣3分
未根据氨罐压力将152D液氨少量多次送入氨罐扣3分
未注意严禁氨罐超压、呼吸阀起跳扣2分
未提高各氨贮槽液位,将部分产氨暂时装在氨贮槽内扣3分
未减前系统负荷到80%扣3分
未打开103J防喘振阀,减少合成回路循环量,尽量少产氨扣3分
由于合成回路产汽量减少,尿素未迅速停车退回蒸汽(113J故障,尿素运行正常时)扣2分
未注意蒸汽管网压力,防止安全阀启跳和一段炉水碳比低联锁扣2分
未关PV2001扣2分
未停2101J/JA扣2分
未及时启动105J1扣2分
如果105J1短时间开不起来,未给103J降到调速器最低转速打全循环扣2分
未关闭HV1101扣2分
未关闭HV1102扣2分
系统放空未在PV1004扣3分
未注意各闪蒸槽液位,防止液位高联锁引起105J跳车扣3分
未停氨回收单元扣3分
由于高压蒸汽产汽量的减少,未调整好高压蒸汽系统压力扣2分
如果高压蒸汽压力急剧下降,未按停车程序103J停车扣3分
未及时查找原因,排除故障,恢复开车扣3分
热氨泵113J跳车事故处理程序
一. 停车范围判断
氨回收系统未停车扣3分
未将驰放气倒到PV1033B放空扣2分
未关闭PV1033A切断阀扣2分
未分以下两种不同工况进行描述扣3分:
若105J1运行,合成部分氨送氨罐,则全部倒冷氨操作。判断不正确扣5分
若105J1停运,全部氨以热氨形式送尿素,这种情况下:迅速启动105J1倒冷氨操作,回答不正确扣2分
若105J1不能及时启动,停合成单元,系统PV1004放空。判断不正确扣3分
二.105J1运行,合成部分氨送氨罐
未将所有热氨制成冷氨送氨罐扣4分
由于系统送出热氨的突然中断,可能引起尿素高压氨泵入口压力低联锁,未注意蒸汽管网的压力,防止尿素蒸汽量的波动引起一段炉水碳比低联锁扣3分
未注意调整149D的液位,部分液氨可直接通过147D送到152D扣4分
未阐述所有液氨均经152D后由124J/JA送氨罐扣3分
未注意调整各闪蒸槽液位,避免出现闪蒸槽液位高联锁,引起105J、105J1联锁跳车扣3分
未注意调整LV1015A避免大幅度调节,以免引起124J/JA气化扣3分
全部改为送冷氨产品后,152D的闪蒸量增大,未注意调整105J1的返回阀FV1012扣3分 同时,105J负荷增大,105J提速,未注意高压蒸汽系统的调整,防止引起高压蒸汽系统波动扣4分
未阐述尿素用氨全部由2101J/JA供给扣3分
由于切除了送去115C的驰放气,未及时调节冷箱出口氢氮比以及冷箱液位扣4分 未给快锅加满负荷扣4分。
若蒸汽不够用,未通知尿素减负荷扣4分。
113J/JA未按规程交出检修扣3分
三. 105J1停运,全部氨以热氨形式送尿素
未提高各氨贮槽液位,将部分产氨暂时装在氨贮槽内扣3分。
未迅速通知压缩人员启动105J1扣3分
现场未及时启动124J/JA,倒冷氨操作扣3分
若105J1或124J/JA不能及时启动,或者在检修状态,未将103J降到调速器最低转速打全循环扣3分
未关闭HV1101扣2分
未关闭HV1102扣2分
系统放空未在PV1004扣3分
由于高压蒸汽产汽量的减少,未调整好高压蒸汽系统压力扣2分
如果高压蒸汽压力急剧下降,未按停车程序停103J扣2分
未及时查找原因,排除故障,恢复开车扣2分
空压机101J防喘振阀故障打开事故处理程序
一. 事故判断
未发现FIC1003流量下降或消失扣10分
未发现高压及中压蒸汽产量下降,蒸汽不足扣10分
未通过压缩主控确认101J防喘振阀打开,无法恢复扣10分
二. 事故处理
(一). 对系统的停车
主控未按切空气按纽HS1206扣2分
未将系统在PIC1032放空扣2分
未确认确认仪表空气压缩机已启动扣2分
未将103J停车扣2分
未将105J/J1停车扣2分
未通知尿素停车并控制PV1099扣2分
未将快锅加至满负荷扣2分
未按HS1004切低变扣3分
未按HS1253切甲烷化扣4分
未切130D扣4分
未关闭MOV1005扣3分
未停脱碳循环扣4分
未将氨回收单元停车扣3分
(二). 确认联锁结果正确
未确认HV1101及HV1103关闭,FV1024及PV1109A关闭扣2分
未确认XS1128动作,HV1028打开扣3分
未将FV1020手动减小开度直至全关扣3分
未确认FV1003及FV1103已关闭;XV1207已关闭,XV1206打开;FV1044保持2T/HR左右流量;PIC1050在自动状态扣3分
未确认XV1220A/B已关闭,XV1220C已打开,PV1001及PV1002已关闭扣2分 未确认XV1222A/B已关闭,XV1222C已打开,PV1029已打开扣2分
未确认膨胀机已联锁扣2分
未确认FV1001及MOV1010已关闭扣3分
三. 对系统进行后处理
未关闭HV1102,关闭LV1013及其前截止阀2分
未控制一段炉降温速率,控制进入一段炉的乏气量及炉膛压力,防止转化管温度骤然变化扣2分
未关闭冷箱进出口截止阀,确认MOV1017,MOV1018已关闭1分
膨胀机跳车事故处理程序
一. 事故现象
未确认PDI1022压降突然下降
未发现合成新鲜气比迅速下降,合成反应热量减少扣10分
未发现137L失去液位扣5分
三. 事故处理
未通知尿素立即停车,退回蒸汽60吨以上扣5分
未注意稳定中压蒸汽管网压力扣5分
合成未停2101J/JA扣5分
未调整冷冻回路,所有产氨都经124J/JA送氨罐扣5分
未现场点燃102B,打开HCV1047,关闭HV1025,合成塔增加外部热量扣5分
未注意控制催化剂床层热点温度低于490度扣5分
关小HV1044,HV1046,控制床层温度扣5分
未提高一段炉水碳比扣5分
未将废气热值升高,适当关小PV1002,减少主烧嘴燃烧量扣5分
未开大PV1029,减少一段炉废气燃烧量扣5分
未提一段炉温度扣5分
未降低二段炉空碳比扣5分
未将106D出口工艺气氢氮比提高扣5分
位开大HV1019,保持AIC1029在1.4以上扣2分
未控制合成塔入口惰气含量小于10%扣3分
装置正常运行快锅跳车事故处理程序
一. 事故处理前提
二. 事故处理过程
未通知尿素装置迅速退回50T/HR或更多蒸汽扣20分
当尿素因为退汽不及时危及到合成水碳比联锁时,未适当关小PV1099控制尿素蒸汽供应量扣10分
未采取措施防止由此造成蒸汽机管网的波动扣20分
未将尿素即回的液氨量按产冷氨流程送至氨罐扣10分
未及时组织快锅开车扣10分
快锅恢复正常后,未恢复尿素蒸汽供应量,恢复液氨供应量扣10分
动力电源中断事故停车处理
一. 事故处理原则及条件
(一). 事故处理原则
未说明设备不超温、不超压、不窜气、不超流速少一项扣0.5分,共2分
未说明催化剂床层不超温、不结碳、不中毒、不泡水、不跑 MDEA、不氧化、不粉化、不冲翻,不跑液、跑油、不污染少一项扣0.2分共2分
未说明保证锅炉不干烧扣1分
未说明保证汽包不带水扣1分
未说明各保证泵不抽空扣1分
未说明各保证泵不憋压扣1分
未说明根据停车情况,确认工艺气放空按以下顺序依次打开:PV1004/HCV1042/PV1005/HCV1045/PV1032/HV1108扣2分
(二). 所需要的外部条件
未说明运行经理联系调度合成氨装置及尿素装置作紧急停车处理扣5分
未检查事故柴油发电机已自启动扣5分
二. 处理步骤
主控操作人员在接到运行经理或作业监督的指令后未按 HS1252B 合成氨工艺系统作紧急停车处理,扣5分
主控未确认各阀门是否按联锁因果关系动作,扣5分
主控未按HS-1253切除甲烷化炉,扣5分
主控未按HS-1254切除低变炉,扣5分
压控未及时停105J1和105J1,扣5分
未向101-B 通入 30~35T/H 中压蒸汽 3~5 分钟对一段炉进行蒸汽置换,扣5分 未确认开PIC1032 系统降压至0.5~0.8MPa,扣2分
未确保中压蒸气驱动的高压锅炉给水泵向141D 上水,扣2分
在中压蒸汽满足 104-JT 运行的情况下,未保持 104-JT 运行,扣2分
当中压蒸汽不能满足104-JT运行时,未将141D上至高液位后停104JT,扣2分 停104JT后,未关闭减压站调节阀保持高压管网压力,扣2分
未指出快锅将因风机电机跳车,扣3分
未指出当事故柴油发电机启动后,应尽快使快锅点火,保证中压管网稳定,扣3分 未指出如果快锅已经恢复可继续保持101J 运行扣3分
未指出如快锅不能恢复停运空气压缩机 101JGT ,扣3分
未指出如蒸汽不能满足引风机101-BJT运行时,停运燃气透平101-GJT, 101-B进行自然降温扣3分
未指出由于101-J 联锁仪表空气供应将中断,仪表空气储罐仅能满足系统 25 分钟运行需要,如动力电源又不能及时恢复,整个公用工程、合成氨装置、尿素装置、成品装置、甲醛装置将必续在25 分钟内将各自装置安全停下扣3分
未指出工用工程在动力电源中断后,脱氧槽上水时应避免上水流量大于脱盐水泵额定工作能
力,引起脱盐水泵过流跳车,扣2分
未指出当 101-BJT 和 104-JT 停车后,夹套水的供应将由脱盐水提供直至二段炉TI1052/TI1053温度低于 150°C,扣2分
未指出工用工程在动力电源中断后,如快锅不能及时恢复,合成氨装置将无循环冷却水供应,扣2分
未指出无循环冷却水供应时,对无盘车装置的刚停运的大机泵加强盘车频率,扣2分 未指出如果中压蒸汽可以维持并且 141D 液位可满足的情况下,尽量保持小股工艺蒸汽来缓慢冷却转化管,扣2分
未将下列机泵在停车状态下的开关位置从自动切至手动:108-JA、107-JC、104-JA、121-J/JA 少一项扣0.5分,共2分
天然气完全中断事故停车处理
一. 事故处理原则
未说明设备不超温、不超压、不窜气、不超流速少一项扣1分,共4分
未说明催化剂床层不超温、不结碳、不中毒、不泡水、不跑 MDEA、不氧化、不粉化、不冲翻,不跑液、跑油、不污染少一项扣0.4分共4分
未说明保证锅炉不干烧扣2分
未说明保证汽包不带水扣2分
未说明各保证泵不抽空扣2分
未说明各保证泵不憋压扣2分
未说明根据停车情况,确认工艺气放空按以下顺序依次打开:PV1004/HCV1042/PV1005/HCV1045/PV1032/HV1108扣4分
三. 处理步骤
主控操作人员在接到运行经理或作业监督的指令后未按 HS1252B 合成氨工艺系统作紧急停车处理,扣5分
主控未确认各阀门是否按联锁因果关系动作,扣5分
主控未按HS-1253切除甲烷化炉,扣5分
主控未按HS-1254切除低变炉,扣5分
压控未及时停105J1和105J1,扣5分
未向101-B 通入 30~35T/H 中压蒸汽 3~5 分钟对一段炉进行蒸汽置换,扣5分
未指出如果中压蒸汽管网可以维持的情况下,尽量保持小股工艺蒸汽来缓慢冷却转化管,防止转化管骤冷,扣5分
未指出当转化管温度降至 350~400°C,关FV1002A/B,关FV1044,系统卸压充氮排导淋置换,扣5分
未打开PIC1032 系统降压至0.5~0.8MPa,扣5分
未指出高压蒸汽管网降压,141D 上水至高液位湿法保护,扣5分
未开HV1108用输气管线中残余天然气对原料气预热盘管进行保护,扣4分
未指出停102J,扣4分
未指出由于燃料天然气中断101JGT 将联锁停车,扣4分
未指出燃气透平停车后,停下101BJT,开乏气放空挡板,通过冷空气对流一段炉自然降温,扣4分
燃气透平101JGT 停车后未确认仪表空压机已启动,扣4分
合成气压缩机103JJT开车方案
一.适用范围
本方案适用于103J/JT开车
二.油系统启动操作
启动前未对油箱液位进行检查,扣0.5分
启动前未对油品进行检查,扣0.5分
启动前未对油系统阀位进行检查,扣2分
启动前未对油泵进行检查、盘车,扣1分
启动时未关出口阀,扣1分
启动时未进行点动,扣1分
启动后未对油过滤器排气,扣1分
启动后未对油冷器排气,扣1分
启动后未对油路各点压力进行检查,扣1分
启动后未对油路各回油情况进行检查,扣1分
三. 压缩机缸体置换
(一). 氮气置换空气
置换前未对系统阀门位置进行检查,扣1分
置换前未强制XV1103联锁打开XV1103,扣1分
置换中未采用充压置换法,扣1分
未给出置换合格指标,扣1分
置换合格后未进行氮保压,扣1分
(二). 合成气置换氮气
置换前未强制XV1103联锁打开XV1103,扣1分
置换中未采用充压置换法,扣1分
置换中未利用放空系统排放,扣1分
未给出置换合格指标,扣1分
四. 机组联锁试验
未给出泵出口压力低辅助油泵启动值,扣1分
未写出润滑油压力低辅助油泵启动试验方法,扣1分
未写出润滑油压力低机组停车试验方法,扣1分
未写出润滑油压力低辅助油泵启动值,扣1分
未写出润滑油压力低机组停车值,扣分
未写出配合仪表人员进行试验,扣1分
未写出对各项试验值进行确认,扣1分
未写出各项试验设计指标值,扣1分
未写出配合仪表人员进行试验,扣1分
未写出对各项试验值进行确认,扣1分
未写出各项试验设计指标值,扣1分
未进行ITCC画面确认,扣1分
五. 启动103JTC
未对103JTC系统阀位进行检查,扣1分
未联系主控在DCS上对液位、流量进行设定,扣2分
未对112J油位、泵体进行检查,扣1分。
启动112J前未盘车,扣1分
启动112J未点动,扣1分
未建立PRV103JTC水封,扣1分
未进行暖管就开抽气器,扣1分
抽气器启动顺序错误,扣1分
主抽开启后,未停辅助抽气器,扣1分
六. 盘车启动
未对汽封冷凝器冷却水进、出口阀检查、并排气,扣1分 未进行暖管,扣1分
未调整PI-2570真空在300mm水柱,扣1分
未确认转子被盘动,扣1分
未将控制压力给定在0.015MPa,扣1分
当透平冲转,轴封漏汽增加,未关小低压蒸汽切断阀,扣1分
在开103-JT排汽蝶阀、轴封漏汽6″切断阀时,顺序错误,扣1分 不对蒸汽系统各阀门、导淋进行检查,扣1分
不给出低压暖管压力值,扣1分
不给出升压暖管升压速率,扣1分
不给出暖管合格指标,扣1分
开MOV1035、MOV1034前,不平衡阀前后压力,扣2分
七. 暖管
未对汽封冷凝器冷却水进、出口阀检查、并排气,扣1分 未进行暖管,扣1分
未调整PI-2570真空在300mm水柱,扣1分
未确认转子被盘动,扣1分
未将控制压力给定在0.015MPa,扣1分
当透平冲转,轴封漏汽增加,未关小低压蒸汽切断阀,扣1分
在开103-JT排汽蝶阀、轴封漏汽6″切断阀时,顺序错误,扣1分
不对蒸汽系统各阀门、导淋进行检查,扣1分
不给出低压暖管压力值,扣1分
不给出升压暖管升压速率,扣1分
不给出暖管合格指标,扣1分
开MOV1035、MOV1034前,不平衡阀前后压力,扣2分
八. 机组复位
未对FIC-2540、FIC-2541、FIC-1059做开、关行程试验,扣3分
未进行DCS I-103J复位,扣1分
未进行HMI上“启动旁路”按扭和“脱扣复位”按扭复位,扣1分
未进行现场跳车电磁阀手柄复位,扣1分
九. 启动升压装置
未确认103J高、低压缸出口到密封系统1″切断阀开,扣1分
未按103J HMI上“SYN GAS OPERATION”按扭,扣1分
未到现场确认电磁阀位置,扣1分
十. 升速暖机
未确认FIC-2540、FIC-2541、FIC-1059在自动或半自动状态,扣1分
未确认HMI上“READY TO START”灯亮,扣1分
未将抽汽阀手动开到100%,扣1分
现场未确认GV、ECV阀全开,扣1分
停盘车未关润滑油供油切断阀,扣1分
未给出低速暖机转速及暖机时间,扣1分
未给出机组冲转后检查注意项目,扣1分
低速暖机期间未做手动停车试验,扣1分
提升机组转速达到机组第二暖机速度1500 r/min时,不观察GV阀控制情况,扣1分 不给出1500 r/min运行时间,扣1分
过临界转速不给出检查注意项目,扣1分
过临界转速后未停密封升压器,扣1分
过临阵转速后未关暖管放空阀、MOV1035后导淋的所有导淋阀,扣2分
未将排汽阀位设定到0%,扣1分
未按HMI上“INLET STEAM PRESS REF▲”按钮使入口蒸汽压力参考达到所需值,扣1分 投抽汽前未检查抽汽管线及各阀阀位,扣2分
未给出投抽汽调节的条件,扣1分
投抽汽时未与主控联系,扣1分
未给出投抽汽方法,扣2分
投抽汽后未对机组进行检查,扣1分
画图不准确,扣1分
未标明各升速段转速,扣1分
未标明各升速速率,扣1分
未标出临界转速带,扣1分
低变催化剂还原方案(用102J还原)
一. 还原目的
未写使低变催化剂中氧化铜还原为有活性组份单质铜扣1分
未写除去工艺气中一氧化碳,保证后工序安全运行扣1分
未写达到提高氨产量,节能降耗目的扣1分
二. 升温还原应具备的条件
未写低变催化剂装填完毕,且现场清理干净扣1分
未写H2源稳定扣1分
未写102J具备开车条件2分
未写空分运行正常,有充足氮气扣2分
未写143C冷却水投用,175C中压蒸汽具备投用条件扣1分
未写热电偶TI1306/46/47/48/49/50调校完毕扣1分
未写FI1101/02/04流量计调试完毕扣1分
未写低变还原记录表格齐全,现场配氢操作专人负责扣1分
三.升温还原过程
未写SG1023-12″到175-C换通板扣1分
未写SG1030-12″到104-D2入口换通板1分
未写MS1099-12″到175-C换通板,FG1004-4″加临时盲板扣1分 未写富岛到配氢管线PG1019-1.5″上的换通板扣1分
未写PG1064-12″前换通板,到143C冷却器的换通板扣1分
未写NG1000-16″进口管线加盲板,且1″旁路加盲板扣1分
未写SG1019-12″到173J加盲板,SG1020-12″到175C加盲板扣2分 未写NG1004-12″102-J出口第二截止阀加盲板扣1分
未写MOV-1008阀后加盲板,且旁路阀关,中间导淋开扣1分
未写MOV-1007阀前加盲板,MOV-1007阀旁路加盲板扣1分
未写142D1来的管线PG1063-10″加盲板扣1分
未写FV1023到NG1015-10″的PG1019-1.5″盲板前导淋打开扣1分
未确认102J出口→175C→104D2→143C→174D→→102J入口流程畅通扣2分 未写确认所有排放阀、导淋阀、排污阀全关扣1分
未写循环回路进行N2置换扣1分
未写分析循环回路氧含量≤0.5%扣1分
未写界内加氢管线N2置换合格扣1分
未写FV-1023前后阀及旁路阀关扣0.5分
未写PG1019-3″管线盲板前导淋开扣0.5分
未写富岛来氢管线HY1005-3″截止阀开扣0.5分
未写确认FI1101和FI1102关扣0.5分
未写开阀FI1101和FI1102的阀前导淋用氢气置换氮气合格后关闭扣1分
未确认AE-1031、FI1104投用扣1分
未写调试还原样气至中化时间扣1分
未写全开N1103-1.5″管线双道切断阀系统充氮扣1分
未写当PI1601达到400 kPa时,保持102-J入口压力400 kPa,启动102J,低变升温回路建循环扣1分
未写调整FI1104流量至26000㎏/Hd扣1分
未写循环期间102-J入口压力保持在400 kPa-530 kPa,出口压力不大于0.75Mpag,保持FI1104流量恒定扣1分
未写稍开MS1099-2″上切断阀,投用175C扣2分
未写以TI1306为准,按10℃/h升温速度升至120℃扣1分
未写TI1306 120℃时做1~2次配氢试验、测滞后时间扣1分
未写检查加氢流量调节是否好用,分析加氢浓度等扣1分
未写配氢试验结束后应控制(通过排放)回路氢浓度<0.1~0.3%扣1分
未写TI1306达到175~180℃后,恒温扣1分
未写当TI1347/48/49/50温度都达到180℃时,升温结束,准备配氢扣1分
未写开PG1019-1.5″切断阀和FI1101前针形阀,开导淋排放1分钟后关扣1分
未写稍开FI1101后蝶阀使FI1101流量10.21Kg/h,保持1分50秒左右,切配氢,此时入口氢浓度约为0.1%。若分析氢浓度不足时,反复上述操作使其达到0.1~0.3%扣1分 未写分析氢耗,观察△H2与床层温升,15分钟记录一次扣1分
未写当还原开始时密切注意温升,如超温降入口温度到180~185℃或更低扣1分
未写当出现明显氢耗,且床层有稳定的温升时,逐渐延长配氢时间,最终连续配氢,保持入口氢浓度0.2%~1%扣1分
未写在配氢同时,立即分析低变进出口氢浓度扣1分
未写连续配氢最初入口氢浓度保持在1%,TI1306在180~190℃,热点在TI1347扣1.5分 未写当TI1347层还原后热点下移至TI1348扣0.5分
未写当TI1348层还原后热点下移至TI1349扣0.5分
未写当TI1349层还原后热点下移至TI1350扣0.5分
未写此阶段,在床温不超过205℃的前提下,缓慢提高入口氢浓度1.0%~1.5%扣1分 未写随氢耗增加,用FI1102配氢线,关FI1101前后阀扣1分
未写在此阶段入口氢浓度不允许超过2%,出口氢浓度不允许超过0.5%。扣1分
未写TI1350层催化剂还原后,以每次3~5℃的升温速率提高TI1306,保持入口氢浓度≤2%扣2分
未写TI1306提至200~210℃,床层热点<210℃,维持T1346不变,逐步提高入口氢浓度,按1%速度提至4%,每提一次保持30min以上。注意温升、氢耗,若有异常温升,立即降低氢浓度甚至切除,查明原因并处理后重新提高氢的浓度扣3分
未写氢浓度提至4%、6%、8%、10%、15%,TI1306在210℃,恒温4小时,无温升,△H2为零,床层各点温度基本一致时,催化剂还原基本完成扣3分
未写将TI1306逐渐升至210℃,入口氢浓度提至15%,运行2小时,催化剂床层无温升且分析进出口H2浓度一致,还原结束扣3分
未写切除氢源,PG1019-1.5″管线上盲板复位扣2分
未写关104D2氮升温进出口阀,停102J扣1分
未写切除氢源,PG1019-1.5″管线上盲板复位扣2分
未写关104D2氮升温进出口阀,停102J扣1分
未写切除氢源,PG1019-1.5″管线上盲板复位扣2分
未写关104D2氮升温进出口阀,停102J扣1分
四. 注意事项
未写升温过程中,应按各阶段升温速度进行,当床层各点温度拉平后,才允许配氢试验扣2分
未写还原过程中,严禁床层温度超过230℃。床层入口温度任何时候不得高于210℃扣1分 未写催化剂还原过程中,按提温不提氢,提氢不提温的原则进行操作扣3分
未写还原时若床层温度异常飞升,立即切氢源,分析氮纯度。必要时停循环,封炉,卸压,用合格氮气置换降温扣2分
未写还原期间,严格监测氮气纯度,保证氮气中O2<0.1%,补氮气时要分析总管氮气纯度扣1分
五. 进出口氢浓度的分析频率
合成氨装置停车工艺系统置换保护方案
一. 适用范围
注明本方案适用合成氨装置停车工艺系统的置换保护扣10分
二. 需要外部条件
未指明合成氨装置已实现安全停车扣2分
未指明危机人身安全的因素已消除扣1分
未指明危机设备安全的因素已消除扣1分
未确认氮气正常扣0.5分
未确认仪表空气正常扣0.5分
未确认循环水正常扣0.5分
未确认蒸汽管网正常扣0.5分
未确认操作人员已配备必要的防护用品和通讯器材扣1分 未确认操作人员已配备必要的通讯器材扣1分
未确认相应的工艺方案已下发并且操作人员已熟知扣2分
四. 准备工作
五. 具备条件
101B催化剂钝化结束后,未作一段炉气体分析扣1分 101B催化剂钝化结束后,未作二段炉气体分析扣1分 未指明一段炉出口降温速率25~30℃/h扣1分
未指明一段炉出口温度降到400℃扣1分
工艺系统切除工艺蒸汽后,未开101B低点排导淋扣2分
六. 工作步骤
(一). 108D、101B、103D系统的置换保护
101B催化剂钝化结束后,未作一段炉气体分析扣2分 101B催化剂钝化结束后,未作二段炉气体分析扣2分 未指明一段炉出口降温速率25~30℃/h扣2分
未指明一段炉出口温度降到400℃扣2分
工艺系统切除工艺蒸汽后,未开101B低点排导淋扣2分 未确认102J出口截止大阀关闭扣2分
未确认108DC出口截止大阀关闭扣2分
未指明前系统分段置换扣2分
未指明在MOV-1010单向阀后导淋接N2管,对前系统进行N2置换扣2分 未指明置换合格全关PV-1032充N2保压扣2分
(二). 低变炉的置换保护
未指明低变切除后保温保压扣4分
未指明低变炉包压过程中每小时排放一次冷凝液扣3分
未指明低变炉低于120℃开始泄压充氮置换扣3分
(三). 甲烷化炉的置换保护
未指明停车后甲烷化炉保温保压操作扣4分
未指明甲烷化炉温度降低至低于200°C时甲烷化炉压力泄至0.1MPa,扣3分 未指明充氮气置换合格保持0.5MPa左右的压力扣3分
(四). 分子筛的置换保护