数控车工技师论文
数控车床加工与高效刀具
江西新余职教中心
孙宇翔
摘 要:本文就经济型数控车床批量加工中存在的刀架由于需要频繁换刀从而带来各种问题,就自己在实际加工中从刀具的材料、刀具的设计、加工方法、程序的处理等方面去解决问题方法作一叙述。
关键词:数控车床 刀架 刀具,程序
前 言:数控车床是数字程序控制车床的简称,它集通用性好的万能型车床、加工精度高的精密型车床和加工效率高的专用型普通车床的特点于一身,主要用来加工轴类、盘套类等回转体零件,能够通过程序控制自动完成内外圆柱面、锥面、圆弧、螺纹等工序的切削加工。能够很好地满足企业提高产品质量、降低生产成本、提高经济效益的要求。所以数控车床是国内使用量最大、覆盖面最广的一种机床,特别是职业学校也在广泛使用。数控车专业已被列入了我校的专业工种之一,并被列入国家紧缺人才专业和江西省技工院校精品专业之一,学校数控专业的开设为企业提供了很好的人才资源。在数控车床加工中,产品质量和劳动生产率在很大的程度上受刀具的制约,虽然其车刀的切削原理与普通车床基本相同。但由于数控加工的特性,根据加工零件的实际,正确选择和使用与数控车床匹配的刀具是充分发挥数控车床功能和优势、保证加工精度、提高劳动效率以及控制加工成本的关键。
论文内容:
数控车工专业是一门专业理论和实践并重的新技术专业,涉及的知识面广,专业技能高,实践经验要求丰富。多年来本人一直从事数控车床的实习教学工作。为更好提高教学质量,培养符合企业要求的技术工人。我校和江西长林机械厂江西赛维光伏集团等五家企业进行长期校企合作,为学校培养人才和企业用人取得双赢,效果明显。如在一次的校企合作中,企业来料加工产品是端盖(如图1),盘类零件,外形A、B两面已经加工成形,内孔已经粗加工至∮90㎜,内孔成品∮98㎜上偏差为0.025㎜下偏差为0。∮112㎜上偏差为0.04㎜下偏差为0.01㎜。产品的精度要求不是很高,形状也不大复杂,但批量较大(每月3000件),数控车床是用广州机床厂的GSK980T(经济型),共3台。
图1
一、 原加工所使用的刀具
当时厂家提供两把焊接式(YG8)合金车刀,分别进行粗车、精车外圆、端面、内孔的加工。
二、分析原来刀具存在的问题:
⑴刀具材料:焊接式(YG8)合金刀易磨损。端盖零件用的材料是铸铁,表皮较硬,刀具易磨损。刃磨精度得不到保证,且占用时间,还会使被加工端盖零件的表面精度大大下降,同时加剧刀具磨损,形成恶性循环。
⑵刀具磨损磨刀换刀频繁。焊接式(YG8)合金刀磨损快,换刀需要整刀换,增加刀具成本;GSK98T刀架不能按加工要求自动装、卸刀,需要换刀时人工进行,因定位销钉受力不均匀等原因,螺纹也容易损坏,而且是用两把刀,精度得不到保证,费时较多。
⑶刀架易坏。加工过程中需要频繁旋转刀架换刀,导致刀架磨损,定位精度出现偏差,还出现故障(平均4天一台)。机床厂的维修人员多次上门维修(维修费400元/次)也不能解决问题,造成停产及维修费用增加。
⑷占机时间长。由于换刀后需重新对刀、试车、调试的辅助时间增加;且两把刀加工、刀架自动换刀和空运行行程时间也较长,大大降低加工效率降低。
三、改进刀具的依据
从上述问题可以看出,加工端盖零件涉及刀片材料、刀具结构、工艺设计、程序编写等方面问题,原来所使用的刀具很需要改进,具体考虑如下:
(1) 刀片材料方面:优先选用涂层刀片。涂层硬质合金刀片的耐用度至少比硬质合金(YG8)可提高1~3倍,涂层高速钢刀具的耐用度则可提高2~10倍。选用涂层刀片磨损可以缓慢许多。
(2)刀具结构:
A、选用标准化刀具。因为端盖是批量生产,数控车刀应选用机夹可转位车刀,原因:
a.精度高 保证刀片重复定位精度高,方便定位,保证刀尖位置精度。这样刀尖磨损不需要换整刀而只需换刀片,很好解决了因刀具磨损造成磨刀换刀频繁的问题。
b.可靠性高 结构可靠的车刀,采用复合式夹紧结构以适应刀架快速移动和换位以及整个自动切削过程中不会松动;迅速更换不同形式的切削部件,完成多种切削加工,提高生产效率。这也是解决问题(2)的好方法。
c.刀具成本低。由于是批量生产,虽然机夹刀可转位刀片贵一些,但刀具的成本不会增加,反而降低,而且更耐用。
B、优化刀具结构(合二为一)。尽可能用少的刀具加工出工件上部分或大部分待加工表面,以减少装夹误差,提高加工表面的相互位置精度。在刀的结构上如果能把加工端盖的两把刀合并成装在“一把刀”把上进行加工,则:
a.不旋转刀架。只有“一把刀”在加工,那就不需要旋转刀架,刀架就不会由于磨损而影响精度,更不会引发停产、维修等麻烦, 那刀架易使坏问题就迎刃而解了。
b.保护定位销钉。“一把刀”定位只需要一组定位销钉,而且如果用了数控标准化刀具,换刀只在刀尖的松、紧定位螺丝,不用松紧刀架的定位销钉装、拆刀杆,刀架的定位销钉不会被损坏,也是解决频繁换刀问题的一个方法。
(3)若采用A、选用标准化刀具和B、优化刀具结构(合二为一)方案,不会存在占机时间长的问题(4)。因为:
①采用A、选用标准化刀具,当刀片上的一个切削刃磨钝后,其刀片的装拆和转位都很方便、快捷,不需刃磨即可用新的切削刃继续加工,还大大提高刀杆的利用率。只需快速做简单的对刀,编制程序时作适当的处理就可以了。
②用了B、优化刀具结构(合二为一)方案,两个刀尖相隔一定比原来两把刀刀尖的距离近,换刀和空运行的时间大大缩短,再结合加工工艺、程序编写,设计最短的空行、切削进给路线,可有效提高生产效率,降低刀具损耗。
四、改进后的刀具
本人通过以上分析、研究,根据现有的认识和加工条件,从刀片材料的选择、刀具结构的设计、工艺处理、程序的处理等方面去解决了端盖零件加工中存在的问题,具体方法如下:
(1) 机夹刀片材料:根据被加工零件的铸铁材质,刀片型号可选择为CNMA120408,刀片材质为ISO—K20(日本东芝)CVD复合涂层可转位刀片,这种刀片的特点是:耐磨性高、抗冲击性能好,每个刀刃大约可加工零件120件。比原来效率提高1~3倍。
(2)将两把机加刀合为一把机夹刀(如图2)。刀杆经调质热处理,用螺丝固定刀尖A、B,这样“一把刀”同样可以完成原来两把刀同样的工作,而且装、卸“一把刀”比原来两把刀省时一半。
图2
(3) 用改进后的刀具加工时无须转换刀架,很好地解决了由于要频繁旋转刀架换刀所带来的故障和维修问题。
(4) 刀具磨损后只需要松开螺丝将不重磨刀片转过适当角度或更换,做简单的刀补行程修改即可继续加工,大大在提高效率。
五、注意事项:
(1) 将不重磨刀片A、B放用螺丝固定在左、右两边,要保证两刀片尖在同一平面上。
(2)机加刀车刀安装好后不可以随意取下。
(3)编写程序时必须要以A、B两个刀尖为两个独立刀位点设两组刀补(01、02),在转换刀尖执行刀补时刀具要离开工件一定距离,防止刀具和工件发生碰撞。
(4)刀架每班要转动一次,以保证刀架的锁紧力。
(5)程序编制及说明:
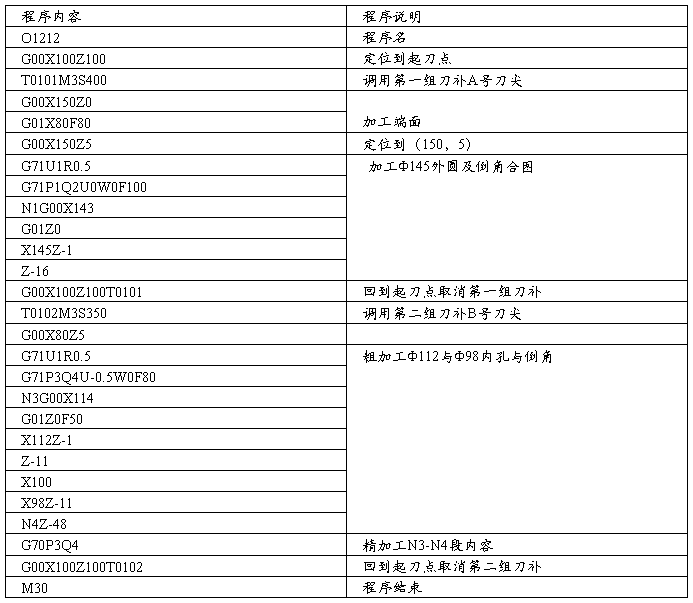
五、结论
通过改进刀具和加工方法,经过生产实践,证明改进后的刀具在保证工件的加工精度的前提下,大大的提高了劳动生产率,降低了生产成本,取得了良好的经济效益,充分挥出数控车床方便、快捷、精准、减轻劳动强度等效能。改进后的刀具完全达到了设计目的。
致 谢: 本人在编写论文的过程中,得到江西长林机械厂高级工程师阮小阳和我校实习实验中心高级教师李勇主任的大力支持与帮助,特此表示感谢。
参考文献:
1. 谢晓红主编. 数控车削编程与加工技术. 电子工业出版社. 2005.
2. 张超英主编. 数控车床. 化学工业出版社. 2003.
3. 陈吉红.杨克冲主编. 数控机床实验指南. 华中科技出版社. 2004.
4. 薛源顺主编 机床夹具设计 机械工业出版社 2005.
5. 杨黎明、黄凯等编 机械零件设计手册 国防工业出版社 1987.
第二篇:数控技师论文
车工技师论文 浅谈数控车床加工程序的编制(共18页,12622字) 在数控车削中,程序贯穿整个零件的加工过程。由于每个人的加工方法不同,编制加工程序也各不相同,但最终的目的是为了提高数控车床的生产效率,因此对于选择最合理的加工路线显得尤为重要。本文将从确定走刀路线、选择合适的G命令等细节出发,分析在数控车削中程序的编制方法。
一、分析零件图样
分析零件图样是工艺准备中的首要工作,直接影响零件的编制及加工结果。主要包括以下几项内容:
分析加工轮廓的几何条件:主要目的是针对图样上不清楚尺寸及封闭的尺寸链进行处理。
分析零件图样上的尺寸公差要求,以确定控制其尺寸精度的加工工艺,如刀具的选择及切削用量的确定等。
分析形状和位置公差要求:对于数控切削加工中,零件的形状和位置误差主要受机床机械运动副精度的影响。在车削中,如沿Z坐标轴运动的方向与其主轴轴线不平形时,则无法保证圆柱度这一形状公差要求;又如沿X坐标轴运动的方向与其主轴轴线不垂直时,则无法保证垂直度这一位置公差要求。因此,进行编程前要考虑进行技术处理的有关方案。
分析零件的表面粗糙度要求,材料与热处理要求,毛坯的要求,件数的要求也是对工序安排及走刀路线的确定等都是不可忽视的参数
1
浅谈梯形螺纹在数控车床上的加工
摘要:在数控车床上加工梯形螺纹有一定的技术难度,特别是在高速切削时难度更大,加工时不容易观察和控制,安全可靠性也较差.这就要求我们对梯形螺纹的加工方法进行不断的探索。
关键词:梯形螺纹 数控车削 加工方法 变速车削
2
梯形螺纹较之三角螺纹,其螺距和牙型都大,而且精度高,牙型两侧面表面粗糙度值较小,致使梯形螺纹车削时,吃刀深,走刀快,切削余量大,切削抗力大。这就导致了梯形螺纹的车削加工难度较大,在多年的数控车床实习教学中,通过不断的摸索、总结、完善,对于梯形螺纹的车削也有了一定的认知,下面就来探究一下梯形螺纹的车削方法。
一、梯形螺纹加工的工艺分析与加工的基本方法
1.梯形螺纹的尺寸计算
梯形螺纹的代号 梯形螺纹的代号用字母“Tr”及公称直径×螺距表示,单位均为mm。左旋螺纹需在尺寸规格之后加注“LH”,右旋则不用标注。例如Tr36×6,Tr44×8LH等。
国标规定,公制梯形螺纹的牙型角为30°。梯形螺纹的牙型如图1,各基本尺寸计算公式如表1-1。
图1 梯形螺纹的牙型
表1-1 梯形螺纹各部分名称、代号及计算公式
名称
代号
3
计算公式
牙项间隙
ac
P
1.5~5
6~12
14~44
ac
0.25
0.5
1
大径
d、D4
d=公称直径,D4=d+ac 中径
d2、D2
d2=d-0.5P, D2=d2 小径
d3、D1
d3=d-2h3, D1=d-p
4
牙高
h3、H4
h3=0.5p+ac,H4=h3
牙顶宽
f、f′
f=f′=0.366p
牙槽底宽
W、W′
W=W′=0.366p-0.536ac
2.梯形螺纹在数控车床上基本的加工方法
1)直进法 螺纹车刀X向间歇进给至牙深处(如图2a)。采用此种方法加工梯形螺纹时,螺纹车刀的三面都参加切削,导致加工排屑困难,切削力和切削热增加,刀尖磨损严重。当进刀量过大时,还可能产生“扎刀”和“爆刀”现象。这种方法数控车床可采用指令G92来实现,但是很显然,这种方法是不可取的。
2)斜进法 螺纹车刀沿牙型角方向斜向间歇进给至牙深处(如图2b)。采用此种方法加工梯形螺纹时,螺纹车刀始终只有一个侧刃参加切削,从而使排屑比较顺利,刀尖的受力和受热情况有所改善,在车削中不易引起“扎刀”现象。该方法在数控车床上可采用G76指令来实现。
3)交错切削法 螺纹车刀沿牙型角方向交错间隙进给至牙深(如
5
图2c)。该方法类同于斜进法,也可在数控车床上采用G76指令来实现。
4)切槽刀粗切槽法 该方法先用切槽刀粗切出螺纹槽((如图2d),再用梯形螺纹车刀加工螺纹两侧面。这种方法的编程与加工在数控车床上较难实现。
(a)直进法 (b)斜进法 (c)交错切削法 (d)切槽刀粗切槽法 图2梯形螺纹几种加工方法
3.梯形螺纹编程实例
例 如图3所示梯形螺纹,试用G76指令编写加工程序。 图3梯形螺纹丝杠
1)计算梯形螺纹尺寸并查表确定其公差
大径d=36 0 –0.375;
中径d2=d-0.5P=36-3=33,查表确定其公差,故d2=33–0.118 –0.453;
牙高h3=0.5P+ ac=3.5;
小径d3=d-2 h3=29,查表确定其公差,故d3=29 0 –0.537; 牙顶宽f=0.366P=2.196
牙底宽W=0.366P-0.536ac =2.196-0.268=1.928
用3.1mm的测量棒测量中径,则其测量尺寸M=d2+4.864dD-1.866P=32.88,根据中径公差确定其公差,则M=32.88–0.118 –0.453;
6
2)编写数控程序
O0008;
T0202;
M03 S400;
G00 X37.0 Z-28;
G76 P020530 Q50 R-0.08; (设定精加工两次,精加工余量为0.16mm,倒角量等于0.5倍螺距,牙型角为30°,最小切深为0.05mm。) G76 X28.75 Z-85.0 P3500 Q600 F6.0;(设定螺纹高为3.5mm,第一刀切深为0.6mm。)
G00 X150.0;
M05;
M30;
以上程序在螺纹切削过程中采用沿牙型角方向斜向进刀的方式,如图2b所示。在FANUC-0i系统中,有时还可采用如图2c所示交错螺纹切削方式,G76编程如下所示:
G76 X28.75 Z-85.0 K3500 D600 F6.0 A30.0 P2;
K:螺纹牙型高度。
D:第一次进给的背吃刀量。
A:牙型角度。
P2:采用交错螺纹切削。
二、变速车削梯形螺纹
在数控车床上车削梯形螺纹工件,低速车削时生产效率很低,高
7
速车削时又不能很好地保证螺纹的表面粗糙度,达不到加工的要求,而直接从高速变为低速车削时则会导致螺纹乱牙。变速车削时的乱牙问题可以用一种简单实用的方法加以解决,车削螺纹时可以先用较高转速车削,再用低速来精车及修光,从而提高了生产效率,并很好地保证了螺纹的尺寸精度和表面粗糙度。
下面还以梯形螺纹工件如图3所示为例,介绍如何在FANUC系统的数控车床上变速车削梯形螺纹。
由于此梯形螺纹的螺距较小,可采用斜进搭配刀法加工,因FANUC系统的G76螺纹切削复合循环指令就是以斜进方式进刀的,故可采用G76指令,粗车梯形螺纹时编程如下,留出精车余量。 G00 X40 Z-20;
G76 P010030 Q80 R0.05;
G76 X29 Z-85 P3500 Q100 F6;
G00 X200 Z50;
粗车完成后,如果此时将转速直接调到低速调用原程序精车,则一定会乱牙,发生崩刃或撞车事故,故我们在低速车削之前要解决车刀乱牙问题。考虑到低速车削时车刀进给速度很慢,我们可以用肉眼来观察车削时螺纹车刀与螺纹牙形槽是否对准,具体操作方法如下:
(1)改变工件坐标系,使车刀车螺纹时不接触工件表面,粗车后将粗车刀停在位置X200 Z50处,此时在录入方式下输入G50 X192后执行,即改变了坐标系,相当于将坐标系原点沿X轴正方向移动了4mm,也就是稍大于一个牙高的距离。此时将车床主轴转速调低,如调到
8
25r/min,重新运行程序,粗车刀将车不到工件表面,在接近工件表面的位置移动。如图4所示。
图4调整前车刀与螺纹槽的相对位置
(2)使车刀与车出的梯形螺纹槽重新对正,由于车刀进给速度很慢,此时我们可以看出车刀与原先车出的梯形螺纹槽是不重合的,车刀偏移了一小段距离,如图5所示,目的就是要使车刀重新对准车出的梯形螺纹槽。操作的原理跟在数控车床上车削多头螺纹是一样的,就是通过改变螺纹车刀车削前的轴向起点位置来达到目的,即修改上述程序段G00 X40 Z-20中的Z-20。我们可以通过肉眼判断需调整的大慨距离,如可先将Z-20改为-21,运行程序后,发现车刀与车出的梯形螺纹槽还没有完全对正。则再修改Z值,重新运行程序,直到车刀与梯形螺纹槽完全对正。如图5所示。
图5调整后车刀与螺纹槽的相对位置
(3)恢复原来的工件坐标系,开始精加工 为了便于理解和不易出错,仍将车刀移到X200 Z50位置,在录入方式下,执行G50 X208,修复原来的工件坐标系,重新运行程序,就可以低速精车梯形螺纹了。精车时也是通过上述改变螺纹车刀车削前的轴向起点位置的方法来修光梯形螺纹的两侧面,同时通过测量,控制切削的次数使螺纹达到尺寸精度的要求。
经过实验,在高速与低速车削的转数都固定时,车刀需要偏移的
9
位移是固定的,有了这个数据,以后在车刀崩刃,或磨损后需换刀时就可以不用再重复调整步骤,直接在低速精车时将车螺纹的起点偏移相应位置就可以了。本文所举加工例子在南京第二数控机床厂的FANUC系统数控车床上完成,当车床主轴转速从560r/min变速到25r/min时梯形螺车刀在Z轴上需向左偏移1.8mm。图示6 所加工的梯形螺纹。
图6 梯形螺纹的加工
当然如果在批量生产加工时还是要一次一次地改变螺纹车刀车削前的轴向起点位置来修光梯形螺纹的两侧面,生产效率将大大降低,为了解决这个问题,我们可以将梯形螺纹左右两侧面的加工过程分别编成两个子程序,每次调用时使车刀轴向偏移0.1mm,在工件的首件试切中确定需调用子程序的次数,从而将整个加工过程编入程序当中,即从加工第二件工件时车床就可以一直自动运行下去,直到工件被加工合格。
像GSK980T、FANUC-OTE等一些功能较全的数控系统由于有复合指令的存在使得编程变得比较简单,但在一些国产经济型数控车床上却不具备这样的功能。这时我们可以将刚斜进法的粗车过程编成子程序,每调用一次车刀都在X轴和Z轴上进给一小段距离,并在首件试切中确定子程序需被主程序调用的次数。粗车完成后,仍用文中所述方法调试出从高速粗车变为低速精车后螺纹车刀需轴向移动的位移,再把精车螺纹左右侧面的加工过程分别编成子程序,在主程序调用即
10
可。
三、加工梯形螺纹的几点注意事项
(1)切削时加切削液,根据情况看是否要加顶尖。
(2)车刀从高速变为低速后要严格对准梯形螺纹槽,操作时要仔细认真,不能马虎。可采用逐步恢复坐标系的方法,即分几次校正车刀,使车刀逐步车削到牙槽底部。
(3)梯形螺纹精粗车刀的刀头宽度不能相差太大,不然换刀后会使切削余量过大,发生崩列等问题。
(4)对于一些大螺距的螺纹,车削时主轴转速不能过高,需参考机床的最高进给速度,否则会发生失步等问题。
四.结论
实际的加工证明,以上在数控车床上变速车削梯形螺纹的方法是切实可行的,且取得了很好的加工效果。对于另外一些大螺距三角形螺纹、蜗杆等只需把粗车进刀的方法如斜进法、分层进刀法等编成子程序,调试出从高速粗车变为低速精车后车刀需轴向移动的位移后,也把精车螺纹左右侧面分别编成子程序,在主程序中将其调用就能完成加工。
参考文献:
1. 顾雪艳等编著. 机械工业出版社. 数控机床编程与操作
2. 陈亚岗,范为军. 江苏盐城技师学院数控系.数控机床结构编程与
11
操作
3. 李清新主编. 机械工业出版社. 伺服系统与机床电气控制
4. 雷学东主编. 南京工程学院. 数控编程与CAM
第1页 共10页
12