贵贵 州 师 范 大 学
学实习报告
二○ ——二○ 学年度 第 学期
材料与建筑工程 学院 年级
专 业
班 级
姓 名
学 号
指导教师
实习单位
实习时间
年 月 日
目录
前 言. 1
第一章 我国氧化铝工业发展概况. 2
我国钢铁工业发展概况..........................................3
我国铁合金工业发展概况.........................................5
第二章 实习目的... 6
第三章 实习内容. 3
3.1实习简介. 3
3.2实习单位介绍. 3
3.3氧化铝生产工艺.. 9
3.3.1拜耳法生产氧化铝的基本原理.. 9
3.3.2原矿浆制备.. 9
3.3.3铝土矿中氧化铝的溶出.. 11
3.3.4溶出矿浆的稀释及赤泥的分离洗涤.. 11
3.3.5铝酸钠溶液晶种分解.. 12
3.3.6氢氧化铝的分离与洗涤.. 14
3.3.7氢氧化铝的焙烧.. 114
3.3.8分解母液的蒸发与苛化.. 16
3.4钢铁生产工艺................................................21
3.4.1炼铁..................................................21
3.4.2炼钢..................................................22
3.5铁合金生产工艺..............................................25
3.5.1铁合金的用途............................................26
3.5.2铁合金的分类............................................26
3.5.3铁合金的生产方法........................................27
3.5.4铁合金冶炼的本质........................................28
3.5.5还原剂的选择............................................29
第四章 实习总结.. 31
前 言
实践是检验真理的唯一标准。在课堂上,我们学习了很多理论知识,但是如果我们在实际当中不能灵活运用,那就等于没有学。毕业实习就是将我们在课堂上学的理论知识运用到实战中。
毕业实习是冶金工程专业教学的重要组成部分,通过毕业实习能够巩固所学的专业知识,提高自身的应用能力和创新能力.我们怎样才能把课本上的知识灵活恰当的运用到生活、工作当中去,成为对别人对社会有用的人才?我们怎样才能适应当今飞速发展的社会,怎样才能确定自己的人生坐标,实现自己的人生价值呢?只有通过实践。
通过本次的专业毕业学习,我们学到了课本上学不到的知识,使我们开阔了视眼,对一些专业性的问题得到了解决和了解 。我想这种专业实习有必要再开展,更能增加学生的实践性,对自己的专业认识也会有很大的提高。我想通过此次的毕业实习我会改变自己的一些不正确的人生观和价值观,这次成功的实习也会带领我朝着辉煌的人生迈进。也必将有助于增强我的职业意识,并激发我在今后的学习中根据实习的经验识时务的调整自己的学习方向和知识结构,以更好的适应社会当今在技术革新迅速、操作接于全自动化的强大生产力推动下的冶金领域,尤其是计算机全程操作发展方向的人才需求。
第一章 1.1我国氧化铝工业发展概况
我国铝土矿与国外相比,经济可利用的基础储备量少,推断的资源量多,探明的资源量少;贫矿多,富矿少,尤为突出的是矿石质量的差别。国外90%以上的铝土矿为高铝、低硅、高铁、易溶出的三水软铝石。我国除占矿石储量的1.54%为三水软铝石之外,其余全部都是高铝、高硅、低铁、难溶的一水硬铝石。除广西铝土矿铝硅比在10以上,其他地区矿石铝硅比都比较低,铝硅比大于10的仅占3.9%,铝硅比在7-10之间的在26.1%,铝硅比在4-7之间的占59.5%,铝硅比在4以下的占7.5%,平均铝硅比为5.56,属于中低品位矿。
我国氧化铝工业的发展自1954年开始,起步较晚但发展迅猛,基本每十年翻一翻。多年来我国分别在郑州、贵州、山西相继投产,现在又相继建成中州铝厂、平果铝厂、重庆铝厂。形成了一个以我国中部地区为氧化铝基地,西北、西南地区为电解铝基地的比较合理的的分局。氧化铝的生产和品种不断增加。根据我国铝土矿的特点,我国必须要有自己独特的技术。经过多年的努力,我国采用并发展了烧结法,首创了混联联合法,使得氧化铝的总收得率和碱度的消耗达到了国外同类工厂的先进水平。并且用经济的方法回收循环母液中的金属镓;利用氧化铝生产中产生的废渣—赤泥来生产水泥,大大提高了氧化铝工业生产的综合效益。当前我国铝工业的主要技术发展方向是:继续发展有我国特色的烧结法和联合法生产工艺,采用间接加热强化溶出,流态化焙烧等新技术和新设备。 20##年以后我国氧化铝工业发展迅速,至20##年产量为20##年的5.5倍,占世界氧化铝产量的44%。在氧化铝工业快速发展的同时,也面临了巨大的挑战。资源、能源、环境、成本、市场等多方面的问题使得我国氧化铝工业的发展进入新的时期。
相比于20##年,20##年我国铝土矿供矿品位急剧下降,带来了氧化铝生产技术经济指标的严重恶化,碱耗上升了81.54%,矿耗增加了20.79%。但值得高兴的是,氧化铝生产节能降耗上却取得了显著成就。
1.2我国钢铁工业发展概况
前些年,有关专家根据欧美发达国家的经验,提出钢产量1亿吨对一个国家发
展钢铁行业是一个警戒线的说法。这个数字不仅是作为衡量一个产钢大国的标准,而且,当达到这个产量时,又可能出现供大于求、市场疲软的现象。真是让人“喜忧参半”。
我国在1993年钢产量达到1亿吨后,到20##年以前,出现钢铁市场供大于求、企业益下滑的不利局面。这期间国家对冶金行业提出了“总量控制、结构调整、淘汰落后”的行策。几年中,宏观调控对稳定钢铁生产发挥了积极作用。但到
了20##年以后,宏观调控已无法对钢铁生产总量进行控制。20##年和20##年全国钢产量分别达到1.67亿吨和1.82亿吨,呈现产销两旺的态势,整个行业效益大幅增长。这到底是怎么了?让人感到一片茫然。
究其原因,客观地讲,是我国宏观的经济形势发挥了作用。我国作为一个发展
中国家,基础设施和工业建设任务十分繁重。一大批具有国民经济发展战略意义的
重点工程相继启动,并随着全球制造业向我国的转移,将在一个时期内对我国的钢铁消费起到较大的拉动作用。但另一方面,笔者认为,有一个出现在钢铁行业内部的问题不容忽视,就是民营钢铁企业的崛起,对钢铁材料的消费起到了推波助澜的作用。
众所周知,经过长期发展,钢铁行业已经从技术密集型行业退出,而成为传统
产业当中的资金密集型产业。改革开放初期,民营企业由于资金匮乏,进入钢铁业也只是“小打小闹”,对钢铁工业发展的大局难以造成影响。但随着民营企业原始资本积累的完成,大规模进入钢铁行业,20##年,民营企业产钢达到1500万吨、铁2000万吨、材3000万吨,分别占全国产量的10%、14%和19%。在已经形成的生产能力基础上,更大的问题是正在建设的生产规模非常大。据一些冶金设备企业人士根据冶金设备订货情况估计,国内在建的炼铁规模是8000万吨。据此推断,未来我国产钢规模将在9000万吨左右,而且绝大多数属于民营企业。这些工程的建设带动了设备制造业、建筑安装业的市场,从而拉动了钢材的消费。建设9000万吨钢铁生产规模到底需要多少钢材?难以准确计算,但肯定不是个小数字。尤其是为了加快工程进度及其他原因,厂房建设已很少采用钢混结构,而全部采用钢框架结构,期中厚板材的过分紧俏就是例证。有人说:“目前,钢铁市场有1/3的消费来源于钢铁业自身”这个推断难说是否准确,但的确有一定的道理,应该引起高度重视试想一下,在建的9000万吨钢铁规模达产后,国内钢铁业将会是怎样一个局面?
长期以来,我国钢铁工业进行结构调整,以完成钢铁工业的合理布局,提高工艺装备水平,淘汰落后的工艺装备和产能,增强企业的整体竞争能力,而不是以盲
目的规模扩张为主旨。增强企业的市场竞争能力的核心,围绕着优化物流、优工
艺、减少消耗、降低成本、生产高质量产品来进行。党的十六大提出,把大力展
民营经济放在重要战略高度来认识。民营钢铁企业的发展不仅带动了钢铁市场的繁荣,而且给国有钢铁企业的生存发展带来了空间。这应该是个好事,而且是个良性循环,笔者也非常赞同。问题是如何利用这个“繁荣”和“空间”,用好了事半功倍,使我们的结构调整顺利实施;反之,则会事倍功半,造成大量人力、物力浪
费,使行业内部竞争环境进一步恶化。
民营企业积极介入钢铁业的动力,源自于其和国有企业的比较优势。民营企业
有机制灵活、劳动力便宜、没有国企的养人负担等优势,使生产成本平均比国企每吨钢减少300~400元,这就促使很多民营企业在建设中,并不是以提高产业水平为前提,而是以快速规模扩张为主,是许多国有中小型钢铁企业的模仿再建。他们星罗棋布地分布在老国企的周围,用国企的人才和成熟的技术进行低水平重复建设。如:高炉以300m3左右为主,转炉以20吨左右为主,轧材以线棒材为主。盲目扩大规模,导致了钢铁行业布局不合理程度加剧、产业集中度降低,有些地区钢铁产能过剩加重,造成运输紧张、资源浪费、环境恶化,原有国有企业因人才外流严重,难以在提高生产水平、实现产业升级上有所作为。当然,我们应当肯定,有许多企
业能够自觉自律,建设了一批好项目,完成了一些“大手笔”,取得了有目共睹的业绩,值得我们引以自豪。
同时,我们也应该看到,目前的“繁荣”和“空间”带来的低水平重复建设和
盲目的规模扩张,不仅发生在民营企业,也同时存在于某些国有企业当中。个中原因不外乎只顾眼前利益的短期行为、只管局部利益的本位主义、无政府主义的越权审批等。钢铁项目涉及各种资源、各种原燃料的平衡发展及合理配置和交通运输、港口建设等多方面的重大问题,如果我们以“市场说了算”、“企业有自主权”为由,来削弱宏观控制的作用,都是有意回避问题的“不作为”行为。我们的各级政府、业内人士、企业决策者必须直面市场形势,抓住机遇,认真吸取国外钢铁业发展的教训,通力合作,克服本位主义,实现优势互补;统筹规划,减少浪费,少走弯路,尽快实现我国钢铁工业的合理布局和产业结构调整,使我国早日由钢铁大国
1.3我国铁合金发展概况
近年来,中国铁合金工业无论从产品品质还是品种、数量都取得了飞跃性的进步,在国际铁合金工业领域中的地位也日益提高。中国已成为名副其实的世界第一大铁合金生产、消费和出口大国。
20##年1-12月,中国铁合金冶炼行业实现累计工业总产值100,853,953千元,比20##年同期增长了26.00%;实现累计产品销售收入95,323,955千元,比20##年同期增长了22.03%;实现累计利润总额1,017,906千元,比20##年同期下降了73.01%。
20##年1-12月,中国铁合金冶炼行业实现累计工业总产值124,284,813千元,比20##年同期增长了25.28%;实现累计产品销售收入119,534,000千元,比20##年同期增长了26.57%;实现累计利润总额1,838,668千元,比20##年同期增长了92.56%。
20##年1-8月,中国铁合金冶炼行业实现累计工业总产值110,678,981千元,比20##年同期增长了51.96%;实现累计产品销售收入104,695,008千元,比20##年同期增长了50.14%;实现累计利润总额3,821,454千元,比20##年同期增长了1,292.53%。
中国铁合金工业在发展的同时,一些问题也日益显露出来。特别是工艺装备水平低下,资源消耗偏高,环保治理落后,严重受制于矿产资源的制约,而且原材料涨价等因素也严重制约了行业的进一步发展和品质的提高。
因此,中国铁合金企业必须抓住新的发展形势,加大整合铁合金行业生产企业力度,坚持走科学发展观的道路,严格把好铁合金生产企业关,行业自身加强自律,规范有秩序竞争,加强人员培训,全面提高素质,只有这样才能在新形势下立于不败之地。
第二章 实习目的
(1)让学生全面充分了解本专业所涉及的有关氧化铝,铁合金和钢铁领域的基本情况,充分认识氧化铝,铁合金和钢铁行业在整个国民经济中的重要地位和作用;
(2)比较全面地了解氧化铝,铁合金和钢铁材料的生产的原料特点、冶炼过程、生产方法、主要工艺流程及产品的应用范围;
(3)了解国内外氧化铝,铁合金和钢铁行业的现状及发展前景;
(4)巩固所学基本知识、基本理论,为后续课程的学习打下良好的基础;
(5)学会查阅文献、收集资料的基本方法。通过实习将所学理论知识与生产实际联系起来,对冶金企业的布局及所用设备有所了解。通过深入一线,加强对冶金工艺流程的了解。
第三章 实习内容
3.1实习简介
时间:2014.2.24—2014.3.10
地点:贵阳市白云区、贵州省清镇市
实习单位:中国铝业贵州分公司、贵阳长乐钢铁有限公司、贵州西电龙腾铁合金有限公司
3.2实习单位介绍
中国铝业股份有限公司(简称“中国铝业” )贵州分公司是遵循国家关于股份制改造的重大决策,按照中国铝业公司总部重组改制部署,集中原贵州铝厂的优良资产,于20##年2月成立的大型铝联合企业,是在纽约、香港和上海上市的中国铝业股份有限公司在贵州的分支机构。
贵州分公司位于贵州省贵阳市白云区境内,现有员工14000余人,资产总额107亿元,具备年产电解铝40万吨、氧化铝120万吨、碳素制品27万吨和多种高附加值产品的设计产能,现有氧化铝、铝及铝制品、碳素制品为主的五大产品系列40多个品种。其中,砂状氧化铝为国内首创,高纯铝为国内独家生产,“洁云”商标和“华光”商标经评审认定为贵州省著名商标。企业质量管理体系、职业健康安全管理体系、环境管理体系和测量检测管理体系通过国家认证,是国家一级计量企业、无泄漏工厂和中国铝业的铝电解、阴极碳素制品试验基地。
作为中国铝业公司拥有独立法人资格的下属企业,贵铝现主要生产经营产品有工业建筑和民用铝型材,电解铝用阳极碳块、阴极碳块和电极糊、铝基(锌基)合金和铝电解用精炼剂、铝合金门窗的安装制做、建筑施工工程、压力容器、电控设备、普通和彩色印刷,以及医疗保健、餐饮住宿、交通、文体娱乐等服务行业。 其中,铝型材设计产能10000吨/年,彩色喷涂铝材设计产能6000吨/年,电泳涂漆铝材设计产能6000吨/年;碳素糊类产品设计产能1.5万吨/年,阳极碳块产品设计产能2.2万吨/年;合金新材料设计产能3000吨。
创新是企业增强核心竞争力的主要途径。中国铝业贵州分公司采用“规划一批、研发一批、转化一批、保护一批”的科技创新管理模式,从分公司到各个厂,从领导到科技人员、广大职工,把科技创新、科技攻关作为企业兴旺发展、立于不败之地的战略工程来抓,形成了科技创新的良好氛围和良性循环。分公司每年都有30项以上的科技研发创新项目申报立项,企业内科技研发立项每年近100项。平均每个月有两项以上的科技创新和近10项攻关完成并运用于生产,这在我国铝工业企业中是没有的。自主研发的“DJYE―I型铝电解工艺过程控系统开发应用”项目,在电解铝厂208台电解槽上推广应用后,不仅产量、质量提高,电解效率、直流电耗及原材料消耗指标都得到优化,取得明显的经济效益; “氧化铝粉尘治理技术开发与应用”项目,开发了适合氧化铝生产的技术设备,成功应用于粉尘污染治理,粉尘排放达到国家标准,年创经济效益900万元以上;“熟料窑增产、提质、节能技术的研究及应用”项目,实现了高效自动控制,提高台时产能3吨,延长运转周期34天,年创经济效益2100多万元;“高粘度重油燃烧技术开发应用”项目,提高了热效率,每年降低成本3600万元以上;“铝电解物料储运及烟气净化管控一体化综合系统”项目,在国内首次应用了无人值守的控制技术,实现了调度、物流及工艺控制一体化,达到国际先进水平,年创经济效益600万元以上。
贵阳长乐钢铁有限公司地处贵州省贵阳市白云区沙文镇,占地面积13万m2,前期投资1.8亿元;公司距贵遵高等级公路及210国道不到1公里,距都拉营和贵州铝厂铁路专线不到5公里,交通十分便利。
为了优化企业结构,提高工艺技术装备水平,加强环境保护,改善劳动条件,提高企业竞争能力,同时也为
了满足社会需求,对西部大开发作出应有的贡献,我公司前期投资1.8亿元,新建成了一条具有九十年代先进水平的集电炉、精炼炉、连铸、连轧四位一体的短流程生产线,总装机容量达3万千伏安;我公司主要工艺设备和公辅设施在国内设计、制造,关键控制元件和计算机PLC系统均采用进口产品。我们以全新的设备和先进的炼钢、轧钢工艺,科学的管理,严格按照国家有关标准和要求,严把质量关,争创名牌产品。目前我公司具备年产35万吨钢,32.5万吨材的综合生产能力。
我公司主要产品为:热轧螺纹钢,并具备优质炭结钢、合结钢的生产能力。为了立足市场,增强企业竞争能力,创名牌优质产品,我公司注册了“长筑”牌钢筋产品商标。我公司生产的合格螺纹钢筋经“贵州省冶金有色金属产品质量监督检验站”多次抽检,产品质量均合格,达到国家标准。20##年,我公司获得了国家质量监督检验检疫总局颁发的“钢筋混凝土用热轧带肋钢筋”产品的“全国工业产品生产许可证”证书。
我公司下设三个生产分厂(炼钢分厂、轧钢分厂、制氧分厂)和六个职能部门(公司办、销售部、供应部、财务部、设备技术部、质量监督部),拥有职工近400人,其中高级工程师、工程师、助理工程师、审计师、会计师、经济师、高级技师、技师等各类人才近80余人,且各工种均有较强的技术骨干。
贵州西电龙腾铁合金有限公司成立于20##年4月,工商注册号:520181000120314,组织机构代码:78547892-7税务登记证号:黔国税字520181785478927号,主要从事铁合金系列产品,硅锰,锰铁的生产与销售业务。位于清镇市站街镇,占地面积230余亩,距离贵阳市50公里,距离清镇市23公里,现有职工260人,拥有铁合金生产电炉四台,年产铁合金10.5万吨,产值约为8亿人民币。20##-2012受市场影响 实际生产1台炉,占总量的25%,20##年总产值为2亿元。
公司奉行“诚信立业,守法经营,精细管理,和谐共赢”的经营理念,曾先后获得清镇市“十佳企业”,“纳税贡献20强企业”等称号,为当地经济与富余劳动力的就业作出较大的贡献
在环保方面,原公司建设时投入了600万元对四台电炉配套了除尘设备,20##年在主管部门的指导下,公司又投入了将近150万元对除尘设备不足部分进行改进,该工程正在实施中。
公司生产用水全部通过循环水池回收利用,不外排。
冶炼过程中的烟气通过除尘风机经烟道引致布袋除尘器中,通过对烟尘过滤将粉尘回收回炉在利用【过滤率达到99%】。烟气中主要含有二氧化硫,氮氧化合物。
固体废物主要为冶炼渣,(俗称水渣)和除尘灰,冶炼渣全部作为水泥生产的原材料销售至水泥厂;除尘灰将作为生产原材料回炉在利用.
3.3氧化铝生产工艺
3.3.1拜耳法生产氧化铝的基本原理
(1)用NaOH溶液溶出铝土矿,所得到的铝酸钠溶液在添加晶种、不断拌的条件下,溶液中的氧化铝呈氢氧化铝析出,即种分过程。
(2)分解得到的母液,经蒸发浓缩后在高温下可用来溶出新的铝土矿,即溶出过程。
交替使用这两个过程,就能够每处理一批矿石便得到一批氢氧化铝,构成所谓的拜耳法循环。
用反应方程式表示如下:
Al2O3·(1或3)H2O+2NaOH+aq =2NaAl(OH)4+aq
3.3.2原矿浆制备
原矿浆制备的主要设备包括:带式输送机、矿浆磨、螺旋分级机。
矿浆磨的构造 矿浆磨全称圆筒湿式溢流球磨机,它主要由中间筒体、两头端盖及空心轴和空心排料器组成。筒壁镶有锰钢棒式衬板和三角衬板,装有不同直径的金属球,物料从两端空心轴进出,并配一套减速传动装置。
从矿山开采的矿石一般呈不规则形状。根据目前破碎设备的生产性能,一次破碎成符合磨矿粒度要求的细颗粒很困难。所以,破碎一般采用分段破碎,将破碎分成粗碎、中碎、细碎过程进行。
由直径1500~500mm的矿石破碎成400~125mm,叫粗碎;由400~125mm破碎成100~25mm叫中碎;由100~25mm破碎成25~5mm叫细碎。
影响矿石破碎的因素很多,主要与矿石的结构、硬度、形状大小以及均匀性等物理性质有关。
铝土矿破碎主要有以下几种方法:压碎、壁碎、折断、磨剥、击碎。
压碎:利用两破碎工作面逼近时加压,使物料破碎。此法的特点是作用力逐步加大,作用力的范围较大,适用于破碎较硬的矿石。
壁碎:破碎工作是由尖齿楔入物料的壁面而完成的。其特点是作用力的范围较为集中而发生局部破裂。此法适用干脆性矿石的破碎。
折断:物料在破碎工作面间如同承受集中负荷的支点梁,除在外力作用点处受壁力之外,矿石本身发生折屈而破碎。
磨剥:破碎工作面在物料上相对移动,对物料施加剪压力,这种力是作用在物料的表面上。此法适用于细粒物料的磨矿。
击碎:利用击碎力的瞬间作用于物料上使物料破裂,是动力破碎。
目的:增加矿石的接触面积,有利于物料的化学反应。
技术经济指标:破矿粒度≤20mm。
在磨矿中,球磨机的下料量要求稳定。因此,原矿浆液固比的调节是调节循环母液的加入量来实现的。在拜耳法磨矿中,循环母液由三个点加入,而磨机内和分级机溢流的液固比在磨矿的操作中要求稳定。因此,调节原矿浆的液固比,实际上是靠增减加入混合槽的循环母液量来实现。
稳定循环母液的浓度和严格铝土矿的配矿制度,是确保拜耳法正确配碱的有效措施。同时应尽量减少非生产用水进入流程及提高石灰质量等,也是拜耳法正确配料,达到良好溶出指标的重要保证。
单位矿石所需要的循环母液量叫配碱量。生产中,要求溶出液具有一定分子比。此指标是工厂根据具体生产条件而确定。
配碱量主要考虑以下三方面的用碱量:
(1)铝酸钠结合碱。例如当规定的MR=1.45时,即是溶出一个分子的氧化铝,在溶液中就要保留有1.45个分子的氧化钠;
(2)与氧化硅反应生成钠硅渣所需碱。矿石中有1kg的氧化硅就要配入M(kg)的苛性钠;
(3)在溶出过程中由于反苛化反应和机械损失的苛性碱。
为了减轻拜耳法过程中硅渣在溶出时析出,影响溶出效果。在原矿浆进入溶出之前进行预脱硅,是减轻结疤的有效途径。预脱硅就是在高压溶出之前,将原矿浆在90℃以上搅拌6~10h,添加钠硅渣晶种,使硅矿物尽可能转变为硅渣,该过程称为预脱硅。预脱硅过程并不是所有的硅矿物都能参加反应,只有高岭石和多水高岭石这些活性的硅矿物才能反应生成钠硅渣,保持较长时间,可以使生成钠硅渣的反应进行得更充分。
3.3.3铝土矿中氧化铝的溶出
高压溶出的目的就是用苛性碱溶液将铝土矿中的氧化铝溶出,生成铝酸钠溶液,有效地提取铝土矿中的氧化铝。使溶液充分脱硅,避免过量的SiO2影响,把苛性碱的消耗降到最低。工业生产中一般采用循环母液来溶出铝土矿。为了加快氧化铝水合物(特别是一水硬铝石)的溶出速度,有时需添加石灰,并且把铝土矿、石灰、循环母液磨制成矿浆后在溶出设备中完成溶出过程。
铝土矿的拜耳法溶出属于多相反应,反应过程发生于两相(矿物和碱液)界面上。两相界面上的OH-不断反应而逐渐消耗,靠近表面溶液的OH-浓度显著降低;同时这一层中反应产物AlO(OH) -的浓度接近于饱和,形成扩散层。因而新的OH-必须不断地通过扩散层的固相表面移动,与氧化铝水合物反应;而反应产物AlO(OH) -则不断的通过扩散层向外移动,使反应继续进行下去。
因此,铝土矿的溶出过程可分为下列几个步骤:
①循环母液润湿矿粒表面;
②氧化铝水合物与OH-相互作用生成铝酸钠;
③形成[Al(OH)4]-的扩散层;
④[Al(OH)4]-从扩散层扩散出来。而OH-则从溶液中扩散到固相接触面上,使反应继续下去。
对于铝土矿来说第二个步骤(化学反应)和第四个步骤(扩散)在一定条件下起主导作用,在高压和高温的条件下扩散过程决定着溶出反应速度。
高压溶出过程添加石灰的主要作用:
(1)消除含钛矿物的有害作用,显著提高Al2O3的溶出速度和溶出率;
(2)促进针铁矿转变为赤铁矿,使其中的氧化铝充分溶出,并使赤泥的沉降性能得到改善;
(3)活化一水硬铝石的溶出反应;
(4)生成水化石榴石,减少氧化钠损失,降低碱耗;
溶出过程的主要技术条件和经济指标有:溶出温度、溶出时间、氧化铝溶出率、碱耗、热耗等。
铝土矿溶出过程中,由于整个过程是复杂的多相反应,所以影响溶出过程的因素比较多,这些影响因素可大致分为铝土矿本身的溶出性能和溶出过程作业条件两个方面。
温度是溶出过程中最主要的影响因素,论反应过程是由化学反应控制或是由扩散控制,温度都是影响反应过程的一个重要因素。一般情况下,升高温度,化学反应速率常数和扩散速率常数都会增大,这从动力学方面说明了提高温度对于增加溶出速率有利。
温度在溶出天然的一水硬铝石型铝土矿时所起的作用比溶出一水软铝石矿物时更加显著,因为在溶出铝土矿时会有钛酸盐和铝硅酸盐保护膜的生成,提高温度使这些保护膜因再结晶而破裂,甚至不加石灰也有良好的溶出效果。
但是提高温度会使溶液的饱和蒸汽压急剧增大,溶出设备和操作方面的困难也随之增加,这就使提高溶出温度受到限制。
当其他条件相同时,母液碱浓度越高,Al2O3的未饱和度越大,铝土矿中Al2O3的溶出速度越快,而且能得到分子比低的溶出液。高浓度溶液的饱和蒸汽压低,设备所承受的压力也要低些。但是从整个流程来看,种分后的铝酸钠溶液,即蒸发原液的Na2O浓度不宜超过240g/L,如果要求母液的碱浓度过高,蒸发过程的负担和苦难必然增大,所以从整个流程来权衡,母液的碱浓度只宜保持为适当的数值。
对某一种矿石,当其粒度越细小时,其比表面积就越大。这样矿石与溶液检出面积就越大,即反应的面积增加了,在其他溶出条件相同时,溶出速率就会增加。另外矿石的磨细加工会使原来被杂质包裹看氧化铝水合物暴露出来,增加了氧化铝的溶出率。溶出三水铝石型铝土矿时,一般不要求磨得很细,有时破碎到16mm既可以进行渗滤溶出。致密难溶的一水硬铝石型矿石则要求细磨。然而过分的细磨使生产费用增加,又无助于进一步提高溶出速率,而且还可能使溶出赤泥变细,造成赤泥分离洗涤的困难。
铝土矿溶出过程中,只要Al2O3的溶出率没有达到最大值,那么增加溶出时间Al2O3的溶出率就会增加。例如,韦伯铝土矿的成分是三水铝石和一水软铝矿,在溶出条件下5min就可达到最大溶出率,所以增加溶出时间对其溶出率不产生影响;也门的内格罗铝土矿的成分是一水软铝石和一水硬铝石,它的溶出速率较慢,所以增加溶出时间能使Al2O3的溶出率增加。
3.3.4溶出矿浆的稀释及赤泥的分离洗涤
溶出后的矿浆在赤泥分离之前用一次赤泥洗液稀释,其作用有四个方面:
①有利于赤泥的分离
溶出后的矿浆浓度高、粘度大,直接分离非常困难,工业生产实际上不能分离。铝酸钠溶液粘度与浓度关系很大。溶出后矿浆浓度Al2O3一般都在280g/L以上,固含110g/L左右,这种赤泥浆液粘度较大。稀释的结果,使溶液浓度降到中等浓度,而且固含也降低到60g/L左右,比重下降,且赤泥溶剂化程度降低,促进了粒子的聚结。因而赤泥沉降速度增加,分离洗涤效率提高。
②降低溶液稳定性,便于晶种分解
溶出后的铝酸钠溶液中Al2O3浓度都在280g/L以上,这样的溶液很稳定,不能直接分解,必须稀释。另一方面,赤泥洗液必须回收。但赤泥洗液中Al2O3浓度一般在30~60g/L,不能单独分解,必须加入高压溶出浆液中。
③使铝酸钠溶液进一步脱硅
在溶出前和溶出过程中虽然进行了脱硅反应,但由于溶液浓度高,铝酸钠中SiO2的溶解度大,溶出液的硅量指数一般在160左右,而晶种分解要求精液的硅量指数在200以上。稀释可以使溶液进一步脱硅。随着溶液浓度降低,SiO2平衡浓度也相应大大地降低,又因浆液中含有大量铝硅酸钠的赤泥作晶种,浆液温度又高(105℃),有利于脱硅反应的进行,因此溶液硅量指数上升。
④有利于稳定沉降槽的操作
生产中高压溶出浆液成分有所波动,它进入稀释槽混合后,可以使稀释浆液成分的波动幅度减小,这有利于沉降槽作业的稳定。稀释浓度的高低很重要,直接影响到拜尔法的生产。浓度过高,将影响赤泥分离洗涤及叶滤机过料,还会降低种分速度,浓度过低,拜尔法物料流量成比例增加,各项消耗(如蒸发汽耗和电能消耗等)会增加。
赤泥分离的目的是将稀释矿浆中的铝酸钠溶液和赤泥分离开来,以获得工业生产上认为的纯净的铝酸钠溶液。
赤泥洗涤的目的是为了回收赤泥中带有的氧化钠和氧化铝,以减少损失。
粗液精制的目的是精华粗液中浮游物,使净化后的铝酸钠溶液含浮游物小于0.02g/L,满足产品质量要求。
拜耳法赤泥分离洗涤的步骤主要包括:
(1)浆液的稀释高压溶出后的压煮矿浆,用一次和二次赤泥洗液稀释,以便于赤泥沉降分离,并且可满足种分对溶液浓度和纯度的要求。
(2)赤泥的沉降分离稀释后的浆液送入沉降槽进行沉降分离赤泥。沉降槽溢流(粗液)中的浮游物含量应小于0.2g/L,以减轻下一步叶滤机的负担。
(3)赤泥反向(逆流)洗涤分离底流即含有一定附液(铝酸钠溶液)的赤泥再经过4~6个沉降槽进行4~6次反向洗涤,回收附液中的A12O3和Na2O。
(4)赤泥的浓缩过滤洗涤沉降槽的末次底流赤泥送过滤机进行浓缩分离,进一步回收赤泥中附液的A12O3和Na2O。
3.3.5铝酸钠溶液晶种分解
控制过滤后的纯净铝酸钠溶液送去进行晶种分解,即在降低溶液温度并加入晶种的条件下使饱和铝酸钠溶液分解而析出氢氧化铝,同时得到分子比较高的种分母液,作为溶出铝土矿的循环母液。晶种分解是拜耳法生产氧化铝的主要工序之一,它对产品质量、产量及全厂的技术经济指标有着重大影响。
衡量种分作业效果的主要指标是氢氧化铝的质量、分解率和分解槽单位产能。这三项指标是互相联系而又互相制约的。
铝酸钠溶液的分解析出Al(OH)3结晶包括两个过程,即铝酸离子分解过程和氢氧化铝结晶形成过程。
其中铝酸离子分解的机理为铝酸根离子通过聚合形成与三水铝石层状结晶结构近似的聚合离子群,即四面体Al(OH)4-相互碰撞形成聚合离子群Aln(OH)4nn-,为八面体结构。再由六个八面体闭合组成环,组成为Al6(OH)246-,进而转变为三水铝石固体Al(OH)3。
氢氧化铝结晶形成的机理主要分为四步:
(1)晶核形成
晶核形成与温度、过饱和度和晶种等因素有关。当分解温度低,晶种表面积小,分解精液的过饱和度高时,生成晶核表面粗糙,长成向外突出细小的晶体,在颗粒相互碰撞或流体的剪切力作用下,这些细小晶体便脱离母晶而进入溶液中,成为新的晶核。新晶核形成的过程称为二次成核。
(2)Al(OH)3晶粒的破裂与磨蚀
破裂是颗粒之间的碰撞以及颗粒与糟壁、搅拌器之间的碰撞结果,使结晶体破裂,氢氧代铝结晶粒度变细。
(3)Al(OH)3晶体的长大
种分过程存在着晶体直接长大的过程,即在晶种表面结晶并沿平面展开,使晶粒直径长大。该过程一般在温度高,溶液过饱和度大,种子比大的条件下发生。但晶体长大的速度与晶种粒度大小无关。
(4)附聚
附聚是指一些细小的晶粒相互依附并粘结成为一个较大晶体的过程。氢氧化铝颗粒附聚分为两部分:
①细颗粒晶体相互碰撞,其中一些结合成松散的絮团,其机械强度小,容易重新分裂;
②絮团在未分裂时,由于溶液分解出来的Al(OH)3起到了一种“粘结剂”的作用,将絮团中的各个晶粒胶结在一起,形成了坚实的附聚物。
溶液过饱和度大,温度高有利于附聚
铝酸钠溶液中的杂质对分解过程有一定影响。溶液中含少量有机物无碍于分解,但如果积累到一定程度,可使分解速度降低,并使分解产物粒度变细,因有机物会增加溶液黏度,且能吸附于晶体表面,阻碍晶体长大。
铝酸钠溶液中的硫主要以硫酸钠的形态存在。硫酸钠和硫酸钾使分解速度降低,但含量低时不甚明显。用明矾石为原料时,种分原液中往往含有大量硫酸盐,当达到SO330~40g/L以上时,分解速度开始显著降低。
铝土矿中含有少量锌,一部分在溶出时进入铝酸钠溶液,种分时全部以氢氧化锌形态析出于氢氧化铝中,从而降低氧化铝产品质量。溶液中存在锌有助于获得粒度较粗的氢氧化铝。
晶种数量习惯用种子比表示。种子比是指添加晶种中Al2O3含量与溶液中Al2O3含量的比值。一般为1.0~3.0。一般说来,在种子粒度组成相同时,增加种子比可以增加种子的表面积,从而提高溶液的分解率。种子比大,可缩短诱导期。对长大过程而言,增加种子比还可促进晶体生长,有助于获得粒度粗、强度好的产品氢氧化铝。晶种的质量是指它活性的大小,它取决于晶种的制备方法和条件、保存时间以及结构和粒度(比表面积)等到因素。
3.3.6氢氧化铝的分离与洗涤
氢氧化铝的分离与洗涤的主要设备为转鼓式真空过滤机。
经种子分解或碳酸化分解得到的氢氧化铝浆液,用过滤设备将氢氧化铝和母液分离,分离得到的氢氧化铝一部分直接返回生产流程,作种子分解的晶种,其余经进一步洗涤生产氢氧化铝成品。
为了达到氢氧化铝与母液分离的目的,可采用不同的方法,如沉降或过滤等。料浆液固比大的可用沉降法,液固比小的可用过滤法。由于料浆液固比影响过滤速率,因此,在一般情况下,都先将氢氧化铝料浆进行浓缩,然后再进行过滤分离。
氢氧化铝浆液经分离所得的氢氧化铝滤饼仍含有一定量的分解母液,必须加以洗涤,以回收Na2O,并保证氢氧化铝产品中Na2O含量符合质量标准要求。
主要技术经济指标有:氢氧化铝洗水量、料浆液固比、成品氢氧化铝含水量、过滤机产能等。
3.3.7氢氧化铝的焙烧
氢氧化铝焙烧的目的为在一定温度下把氢氧化铝的附着水和结合水脱除,并发生分解反应,形成氧化铝,再进行晶型转变,得到具有一定物理和化学性能的氧化铝产品。
工业生产出的氢氧化铝含有10%~15%的附着水,其分子组成为Al(OH)3(Al2O3·3H2O),焙烧是在900~ 1250℃下进行的,氢氧化铝在焙烧过程中发生一系列变化。
当温度达到100~120℃时,附着水随即被完全蒸发掉。继续提高温度则发生结晶水的脱除,以及无水氧化铝的晶形转变。
焙烧反应方程式如下:
100~120℃:2Al(OH)3+附水→Al2O3·3H2O+H2O↑
200~250℃:失去两个结晶水转变为一水软铝石;
Al2O3·3H2O→Al2O3·H2O+2 H2O↑
500℃左右,一水软铝石转变为无水γ-A12O3;
Al2O3·H2O→γ-Al2O3+ H2O↑
900℃以上转变为a-Al2O3;
γ-Al2O3→a-Al2O3
经预热和部分脱水的氢氧化铝在流化床焙烧炉中进行最终焙烧。焙烧过程的主要设备和步骤如下:
1 焙烧炉能源供应
焙烧所需热量是由燃油(重油)在流化床焙烧炉直接燃烧所产生的;供燃烧用的燃油,通过插入流化床焙烧炉下部的四支油枪喷入流化床,用蒸汽将燃油雾化;焙烧炉温度可以通过温度控制器保持稳定。
燃油燃烧所需要的空气,分为一次风和二次风。一次风燃烧用风通过流化床冷却器内间接加热盘管,经管道导入流化床焙烧炉中。二次风作为补充燃烧所需空气不足部分,通过上方炉壁进入流化床焙烧炉中。
2 焙烧炉再循环系统(CFB)
由于焙烧炉中强烈的混合和热交换,焙烧温度是燃烧温度和物料温度之间的混合温度。
在炉子下半区,存在一个固体物料浓度较高的流化床,这有利于燃油的燃烧和增加物料在炉内平均停留时间。在焙烧炉上半区,二次风进口上方,随着固体物料扩散到焙烧炉的顶部,固体物料浓度随之降低。
热气流进入再循环旋风收尘器,固体物料在那里得到分离,分离出的热氧化铝,经密封槽重新进入流化床焙烧炉。在整个焙烧阶段中,固体物料的再循环导致了产品和气流温度几乎一致。
氧化铝的冷却从焙烧系统排出的氧化铝,经二次风旋风收尘器和流化床冷却器被冷却到约80~100℃。经铝氧皮带送入铝氧储存大仓。
为了降低焙烧工艺单位热耗,从焙烧炉排出的氧化铝中所含热量,在流化床冷却器内得到回收,用热氧化铝与燃烧空气直接和间接热交换的方法,来加热燃烧空气,达到可能的最高温度。氧化铝所含不能用于空气预热的部分热量,被冷却水带走。
从冷却器排出的已冷却的氧化铝,经卸料密封槽和卸料空气斜槽,进入氧化铝输送系统。卸料密封槽和卸料空气斜槽的流化风由风机提供。
从卸料空气斜槽卸下的氧化铝,经铝氧皮带和空气斜槽送入铝氧储存大仓。
氢氧化铝焙烧的主要影响因素有:
1)温度;
2)氢氧化铝粒度和强度;
3)矿化剂;
4)燃料及燃烧。
3.3.8分解母液的蒸发与苛化
拜耳法的种分母液和烧结法的碳分母液通常需要进行蒸发,其主要目的:
(1)排除流程中多余的水分,保持循环系统中液量的平衡;
(2)将分解母液蒸浓到符合铝土矿溶出或配制生料浆的浓度要求;
(3)降低母液中杂质的含量:碳酸钠、硫酸钠、氧化硅等。
在氧化铝生产过程中进入流程中的水分主要有:
(1)赤泥洗水,约3~8米3/吨干赤泥;
(2)氢氧化铝洗水,约0.5~1.5米3/吨Al(OH)3;
(3)蒸汽直接加热的冷凝水;
(4)原料带入的附着水和结晶水;
(5)非生产用水,包括用水管冲洗车间地面的水、泵密封用水以及进入的雨水。
蒸发后母液的去向:烧结法大部分碳分母液经蒸发后去配生料浆,少部分不经蒸发去溶出铝土矿;种分母液蒸发后加入脱硅工序,提高溶液的稳定性。拜尔法种分母液蒸发后去溶出下一批铝土矿。
蒸发过程实质上是一种热能传递过程,可以用传热方程式来表示。
q=KFΔt
式中: q— 单位时间的传热量,KJ/h
K— 传热系数。KJ/m2·h·℃
F— 传热面积。m2
Δt— 有效温差。℃
影响分解母液蒸发与苛化的因素有很多,其中主要是有效温差的影响和传热面积的影响。
1)有效温差的影响
有效温差越大,热传递越好,蒸发器的产能越高。
提高有效温差的方法如下:
(1)提高加热蒸汽的使用压力。
(2)提高蒸发器组系统的真空度。
(3)减少温度损失可采用:
①减少蒸汽管路的温度损失;
②减少由液柱静压导致的温度损失。
2)传热面积的影响
防止结垢的生成及及时地清理。
对于易溶解性的碳酸钠和硫酸钠的结垢,可采用:
(1)原液煮罐法。即倒流程,如原作业流程为3-1-2,经过生产一段时间后倒为2-3-1流程,每隔一定时间倒一次,但清除结垢不彻底。
(2)水煮罐法。即在生产一定时间后结垢严重时,用水煮罐一次,可彻底消除结垢,但降低了设备运转率,热损失较大。
(3)通死眼。即对结垢严重,有的加热管被大量的结晶或其它固体物质堵塞成为死眼时,先将蒸发器进行水煮,然后将水放掉,用具有一定温度的高压水冲击和溶化加热管内的结垢,但劳动强度较大,工作条件较差。
对于难溶性的铝硅酸钠的结垢的清除,目前普遍采用:
(1)化学除垢
分为酸法和碱法。
(2)机械除垢
近年来,国外采用高压水射流装置消除结垢,已取得良好效果。如当采用压力为300~500公斤/厘米2的高压水,清理一根(Ф36毫米和长7米)加热管的结垢(硅渣和碳酸钠),只需要5—7分钟。
目前氧化铝生产中的蒸汽消耗,蒸发工序约占总汽耗的30~50%,因此,如何降低蒸发汽耗,对氧化铝生产的节约能耗有很大的实际意义。
降低蒸发能耗的途径,一是降低蒸发每吨水的汽耗,二是减少每吨产品Al2O3的蒸发水量。
降低蒸发每吨水的汽耗措施是:选择高效的蒸发设备与合理的蒸发流程、减少温度损失、防止或减轻加热表面上的结垢生成及合理地利用二次蒸汽等。
减少每吨产品氧化铝的蒸发水量,关键在于减少每吨产品氧化铝所需要的循环碱液量及循环碱液与种分原液中的Na2O浓度差。
减少单位氧化铝蒸发水量的途径有:
(1)减少循碱液量;
(2)降低循环碱液的浓度;
(3)提高种分原液的浓度;
(4)减少进入流程的非生产用水量。
3.4 钢铁生产工艺流程
3.4.1炼铁
炼铁 铁矿石的品种分为磁铁矿Fe3O4、赤铁矿Fe2O3、褐铁矿2Fe2O3.3H2O、菱铁矿FeCO3。铁矿石中除铁的化合物外,还含有硅、锰、磷、硫等的化合物(统称为脉石)。铁矿石刚开采出来时无法直接用于冶炼,必须经过粉碎、选矿、洗矿等工序处理,变成铁精矿、粉矿,才能作为冶炼生铁的主要原料。 将铁精矿、粉矿,配加焦炭、熔剂,烧结后,放在100米高的高炉中,吹入1200摄氏度的热风。焦炭燃烧释放热量,6个小时后温度达到1500度,将铁矿融化成铁水,不完全燃烧产生的CO将氧从铁水(氧化铁)中分离出来,换句话说CO作为还原剂将铁从铁水(氧化铁)中还原出来。熔剂,包括石灰石CaCO3、荧石CaF2,其作用是与铁矿石中的脉石结合形成低熔点、密度小、流动性好的熔渣,使之与铁液分离,以便获得较纯净的铁水。铁水即生铁液,然后被送往炼钢厂作为炼钢的原料。 宝钢炼铁车间由两座4063立米大型高炉组成,预留有第三座高炉的建设场地。 全车间年产生铁600万吨(最终产量可达650万吨)。向炼钢车间热送576.6万吨铁水,钢锭模铸造车间热送6.78万吨,其余16.62万吨铁水送铸铁机铸块。 全车间分两期建设,1号高炉计划1982年4季度投产,2号高炉计划1984年投产。 全车间约占地572,000平米,采用半岛式布置,1、2高炉中心距370米,原料、燃料均用胶带运输机分别由原料场,烧结车间,炼焦车间送入矿槽、焦槽。筛下粉矿、碎焦亦由胶带运输机运出,转送烧结车间。铁水输送采用320吨鱼雷式混铁车。 高炉煤气灰、垃圾、废铁的…
3.4.2炼钢
炼钢就是把原料(铁水)里过多的碳及硫、磷等杂质去掉并加入适量的合金成分。炼钢系统的主要工艺流程为:转炉兑铁——冶炼——出钢——钢包吹氩——LF精炼炉——方坯连铸工艺。
最早的炼钢方法出现在1740 年,将生铁装入坩锅中,用火焰加热溶化炉料,之后将溶化的炉料浇铸成钢锭。1856 年,英国人亨利-贝塞麦发明了酸性空气底吹转炉炼钢法,第一次解决了铁水直接冶炼钢水的难题,从而使钢的质量得到提高,但此法不能脱硫,目前己被淘汰
1880 年,出现了第一座碱性平炉,由于其成本低,炉容大,钢水质量优于转炉,一时成为世界上主要的炼钢法。1878 年,英国人托马斯发明了碱性炉的底吹转炉法,该方法是在吹炼过程中加石灰造碱性渣,从而解决了高磷铁水的脱磷问题。但此法的缺点是炉子寿命短,钢水中氮含量低。1899 年,出现了依靠废钢为原料的电弧炉炼钢法,解决了利用废钢炼钢问题。1940 年代大型空气分离机的出现,使氧气制造成本大大降低,氧气顶吹转炉得到广泛运用。 由于生铁冶炼过程中要使用大量的碳来还原出金属铁,生铁中碳含量较高。钢与生铁化学成分上的主要区别在于含碳量,含碳量超过2.11%的就是生铁,而常用钢的含碳量一般在1%以下。炼钢就是将生铁在高温中进行熔化、净化(或称精炼)和合金化的一个过程。精炼过程主要包括用燃烧的方法去除掉生铁中过量的碳和硅以及锰和磷等杂质。这些杂质要么变成气体冒出去,要么变成残渣被清除掉。精炼时还可以根据需要加入某些其他元素。 炼钢炉有三种:转炉、平炉和电弧炉。转炉和平炉用来炼从高炉出来的铁水加废钢,电弧炉用来将废钢熔化再炼。平炉由于能耗高、生产周期长,己经遭淘汰。 转炉炼钢:转炉的炉体可以转动,用钢板做外壳,里面用耐火材料做内衬。转炉炼钢时不需要再额外加热,因为铁水本来就是高温的,它内部还在继续着发热的氧化反应(来自铁水中硅、碳及吹入氧气)。因为不需要再用燃料加热,故而降低了能源消耗。吹入炉内的氧气与铁水中的碳发生反应后,铁水中的碳含量就会减少而变成钢了。这种反应本身就会发出热量来,因而铁水不但会继续保持着熔化状态,而且可能会越来越热。因此,为调整铁水的适合温度,人们还会再加入一些废钢及少量的冷生铁块和矿石等。同时也要加入一些石灰、石英、萤石等,这些物质可以与铁水在变成钢水时产生的废物形成渣子。因此,它们被称为造渣料。 电炉炼钢:电弧炉炼钢的热源是电能。电弧炉内有石墨做成的电极,电极的端头与炉料之间可以发出强烈的电弧,具有极高的热能。在炼钢时主要是对铁水中的碳进行氧化以减少碳的含量,但有些钢的品种中需要含有一些容易氧化的其他元素时,如果吹入过多的氧,就会把那些元素也一起氧化了。在这时,用电弧炉炼钢就显得优越多啦。因此,电弧炉往往用来冶炼合金钢和碳素钢。电弧炉主要以废钢材为原料。装好炉料后,炉盖会盖上,随后电极就下降接近炉料表面。这时接通电源,电极就会发出电弧将电极附近的炉料熔化。然后加大电压,加快熔化速度。随着炉料的熔化程度,炉料(钢水)的位置会有变化,这时电极也会自动调整高度而不会淹没在钢水中。在炉料将全部熔化时,钢水表面会漂浮着一层炉渣,这时工人们会取出一些钢水和炉渣来分析它们的成分,看看这炉钢炼得怎么样。如果里面有对钢质量有害的元素,还要继续精炼加以除掉。 目前,氧气顶吹转炉炼钢是冶炼普通钢的主要手段,世界钢产量的70%以上是通过这种方法生产的。电弧炉炼钢发展很快,主要用于冶炼高质量合金钢种,已超过了世界钢产量的20%。 宝钢炼钢车间系由三座300吨纯氧顶吹转炉、一套大型双室真空循环脱气装置(RH)、四跨八线钢锭纵向车铸系统及铁水预脱硫设施等辅助装备组成的现代化大型转炉车间。并和拥有二台RIO.5一2500大型板坯连铸机的连铸车间配套,组成一个完整的炼钢生产系统
? 铁水供应 转炉炼钢所需铁水用钢包或鱼雷罐由炼铁厂运往炼钢厂。高炉运来的铁水除一部分兑入混铁炉贮存外,其余铁水经倒包调整和称量作业,保证入炉铁水控制在所需的范围。需要进行脱硫处理的铁水,由天车运往脱硫站进行脱硫处理,不需处理的铁水,直接兑入转炉。铁水是转炉炼钢最主要的金属料,一般占转炉金属料70%以上。铁水的成分、温度是否适当和稳定,对简化、稳定转炉操作,保证冶炼顺行以及获得良好的技术经济指标都十分重要。
? 废钢供应 在炼钢厂设有废钢库,外来的废钢由汽车运到废钢库存放。废钢铁通过磁盘吊车按不同配比和装料顺序装入废钢料槽,由天车加入转炉。转炉炼钢时,由于热量富裕,可以加入多达30%的废钢,作为调整吹炼温度的冷却剂。采用废钢冷却,可以降低铁水量、造渣材料和氧气的消耗,而且比用铁矿石冷却的效果稳定,喷溅少
? 散状原料供应(石灰、铁皮球、镁球等)
1、100吨转炉炼钢散状原料上料系统选用皮带上料工艺。散状原料通过汽车运到地下受料仓,由垂直皮带运送到42m平台,再由水平皮带运输机和布料小车装入相应的料仓。2、加料系统布置在转炉的上方,每座转炉有一套炉顶料仓,每套有10个炉顶料仓,分别为调渣剂、脱硫剂、石灰、铁皮球、镁球、萤石、包渣料仓等。料仓中的散状料分别通过振动给料器→称量斗→汇总斗→下料溜管,加入转炉。
? 铁合金供应 100吨转炉设有一组铁合金料仓,由10个铁合金料仓组成.,为3座转炉供应合金料。 铁合金是脱氧及合金化材料。用于钢液脱氧的铁合金叫做脱氧剂;用于调整钢液成分的铁合金叫做合金剂。 炼钢常用的铁合金有:硅铁、锰铁、钒铁、钼铁、硅钙合金等。
? 转炉冶炼 炼钢是通过氧化反应脱碳、升温、合金化的过程。它的主要任务脱硫、脱磷、脱碳、脱氧,去除有害气体和非金属夹杂物,提高温度和调整成分。[P]对大多数钢来说是有害元素,它在钢中的含量高会引起:“冷脆”,从高温降到0摄氏度以下,钢的塑性和冲击韧性降低,并使钢的焊接性和冷弯性能变差。[S]对大多数钢来说是有害元素,它在钢中的含量高会引起:“热脆”会使钢的热加工性能变坏,引起高温龟裂,并在金属焊缝中产生气孔和疏松,从而降低焊接强度。[O]在吹炼过程中,由于吹入了大量的氧气,当吹炼结束,钢水中有大量氧,在钢的凝固过程中,氧以氧化物形式存在,会降低钢的韧性、塑性等加工性能。[C] 炼钢的主要任务之一就是把溶池里的「C]氧化脱除到所炼钢种的要求。去夹杂物,非金属夹杂物对钢的性能会产生严重影响,应该最大限度驱除。
? 出钢 转炉出钢时,将钢包内村预热到1100~1200℃的钢包运至转炉下方,等待出钢,当钢包车到达预定位置后,转炉开始出钢作业,并由布置在炉后的铁合金旋转溜槽将铁合金加入钢包内。 转炉出完钢,经钢包吹氩喂丝处理后,钢水包由天车至连铸机大包回转台进行浇注。需精炼处理的钢水包,由天车吊往LF精炼炉进行处理,然后再送往连铸机进行浇注。
? 汽化冷却 汽化冷却系统通过循环水给转炉炉体、活动烟罩、烟道等都设备进行降温、冷却,保护设备不被烧漏。
? 转炉一次除尘 烟道降温转炉烟气经汽化冷却冷却后,温度由1450℃~1600℃降到900℃左右,通过高温非金属膨胀节进入高效喷雾蒸发冷却塔,经洗涤降温后,烟气变为饱和烟气,温度降至70℃左右,并得到粗除尘。降温后的饱和一次烟气进入环缝文氏管。通过环缝文氏管精除尘后的烟气温度降至65℃左右。净化后的饱和烟气通过90度弯管进入旋流脱水器精脱水,经管道进入风机。 通过风机的转炉烟气被压送至三通切换阀。放散时,由三通阀切换至放散烟囱放散;回收时,由三通阀切换至煤气回收系统。转炉烟气净化回收系统的运行、放散和回收操作由电脑自动控制。
3.5铁合金生产工艺
铁合金是指一种或一种以上的金属或非金属元素与铁组成的合金,它主要用作炼钢的脱氧剂和合金元素的添加剂。例如锰铁是锰与铁的合金,硅铁是硅与铁的合金,硅钙合金是硅与钙组成的合金。钢铁工业中习惯上把炼钢用的中间合金(不论含铁与否),都叫做铁合金。由于铁合金的生产工艺比纯金属的制取过程简单,而且又具有比纯金属熔点低、体密大(指体密小的金属如钛、硼等)的优点,有利于炼钢过程中脱氧和合金化的进行。因此,炼钢脱氧和添加合金元素多以铁合金形式加入。
3.5.1铁合金的用途
(1)用作脱氧剂。炼钢是用氧化方法去除铁液中的碳、磷等杂质。在完成这些氧化的任务后,同时钢液中也吸收了氧,如果这些氧存在在钢中就会大大地降低钢的性能。因此需要添加一些与氧结合力比较强,且其脱氧产物又能顺利从钢液中排除,从而使钢液中的氧含量降低的元素。这个过程叫做钢的脱氧。用于脱氧的元素或合金叫做脱氧剂。常用的脱氧剂有锰、硅、铝等。这些元素多以铁合金Fe-Mn、Fe-Si和Al等形式加入钢液中。元素与氧的结合能力越强,在钢中含氧量愈高,其脱氧效果也就越好。 (2)用作合金剂。合金元素不但能降低钢中杂质的含量.而且还能调整钢的化学成分。用于调整钢的化学成分使钢合金化的元素或合金叫做合金剂,常用的合金元素有硅、锰、铬、钼、钒、钛、钨、钴、硼、铌等。不同的合金元素和不同的合金元素含量的钢钟具有不同的特性和用途。 铁合金的产量、品种和质量,直接影响着钢铁工业的发展,其用量一般占钢产量的2%~3%左右。 (3)用于铸造工业,改善铸造工艺和铸件性能。改变铸铁和铸钢性能的措施之一是改变铸件的凝固条件,在浇铸前加入某些铁合金作为晶核孕育剂,形成晶粒中心,使形成的石墨变得细小分散,晶粒细化,从而提高铸件的性能。 (4)用作还原剂。硅铁可作为生产钼铁、钒铁等其他铁合金的还原剂;硅铬合金、锰硅合金可分别作为生产中低碳铬铁、中低碳锰铁的还原剂。 (5)用于其他工业。在有色金属和化学工业中,铁合金的使用越来越广泛,如作为有色金属的添加剂;中低碳锰铁用于电焊条的生产;铬铁用于生产铬化物和镀铬阳极材料等。
3.5.2铁合金的分类
随着现代科学技术的发展,铁合金的品种在不断扩大。铁合金的品种繁多,分类方法也多,一般按下列方法分类: (1)单一铁合金。只含一种合金元素的合金叫做单一铁合金。其主要品种有硅铁、锰铁、铬铁、钼铁、钛铁、钨铁、工业硅、硼铁、钒铁、金属锰等。 (2)复合铁合金。含有两种或两种以上合金元素的多元铁合金,主要品种有硅钙合金、锰硅合金、硅铬合金、硅钙铝合金、锰硅铝合金、硅钙钡合金、硅铝钡合金等。 (3)按铁合金中含碳量分类。有高碳、中碳、低碳、微碳、超微碳等品种。 (4)按生产方法分类。有高炉铁合金、电炉铁合金、炉外法(金属热法)铁合金、真空固态还原法铁合金、转炉铁合金、电解法铁合金等。 (5)氮化制品。用锰铁或铬铁粉末,在高温条件下经渗氮等方法生产的氮化产品。其主要品种有氮化锰铁、氮化铬铁等。 (6)氧化物团块。易被铁还原的氧化物团块也可以作为合金剂直接加入钢液中。例如氧化钼团块等。
3.5.3铁合金的生产方法
铁合金的生产方法很多,主要有以下几种。
1 按热量来源分类
根据热量来源不同分为碳热法、电热法、电硅热法和金属热法。 (1)碳热法。碳热法其冶炼过程的热量来源主要是焦炭的燃烧热,用焦炭作还原剂还原矿石中的氧化物,生产在高炉中进行。 (2)电热法。电热法其冶炼过程的热量来源主要是电能,使用碳质还原剂还原矿石中的氧化物,采用连续式的操作工艺,在还原电炉中进行。 (3)电硅热法。电硅热法其冶炼过程的热量来源主要是电能,其余为硅氧化放出的热量,使用硅(如硅铁或中间产品硅锰合金、硅铬合金)作还原剂还原矿石中的氧化物,生产时在精炼电炉中进行间歇式作业。 (4)金属热法。金属热法其热量来源主要是由硅、铝等金属还原剂还原精矿中氧化物时放出的热量,生产采用间歇式,在筒式熔炼炉中进行
2 按操作方法和工艺分类
根据生产工艺特点不同分为熔剂法和无熔剂法、连续式和间歇式、无渣法和有渣法等冶炼方法。 (1)熔剂法。熔剂法生产铁合金是采用碳质材料、硅或其他金属作还原剂,生产时加造渣材料调节炉渣成分和性质(炉渣的酸、碱性)。 (2)无熔剂法。无熔剂法生产铁合金一般多用碳质材料作还原剂,生产时不加造渣材料调节炉渣成分和性质。 (3)连续式冶炼法。连续式冶炼法一方面根据炉口料面下降情况,不断地向炉内加料,另一方面将炉内熔池积聚的合金和炉渣定期排除。采用埋弧还原冶炼,操作功率几乎是均衡稳定的。 (4)间歇式冶炼法。间歇式冶炼法是将炉料集中或分批加入炉内,冶炼过程一般分为熔化和精炼两个时期,熔化期电极埋在炉料中,精炼完毕,排除合金和炉渣,再装入新料,进行下一炉冶炼。由于冶炼各个时期的工艺特点不同,操作功率也不同。 (5)无渣法。无渣法冶炼铁合金采用碳质还原剂、硅石或再制合金为原料,在还原电炉中连续冶炼。 (6)有渣法。有渣法冶炼铁合金是在还原电炉或精炼电炉中,选用合理的造渣制度生产铁合金,其渣铁比受冶炼品种和采用的原料条件等因素影响。
3.5.4铁合金冶炼的本质
铁合金冶炼,尽管品种多样,设备各异,方法繁多,但从其根本上来说就是利用适当的还原剂,从含有氧化物的矿石中还原出所需元素的氧化还原过程。 对一些元素形成的多种氧化物,其还原也同样遵循逐级转化规律,即由高价氧化物向低价氧化物逐级还原,低价氧化物最稳定、最难还原。所以这些元素还原时,应以其低价氧化物的稳定性来考虑。铁合金中常见的氧化物的稳定性由强到弱的顺序是:CaO、MgO、A12O3、TiO2、SiO2、V2O5、MnO、Cr2O3、FeO、P2O5。 矿石中除了有益氧化物外,还有许多杂质,如锰矿中除含氧化锰外,还有P2O5、FeO、SiO2、A12O3等。P2O5、FeO为易还原氧化物,在生产过程中几乎全部被还原;而MnO比FeO稳定故部分被还原;SiO2更稳定只有少部分被还原;而Al2O3、MgO、CaO很稳定,几乎不被还原。因此,生产中应通过控制温度、炉渣成分和选用合适的还原剂等,来促进所需要的有益元素充分还原,而尽量抑制其他杂质元素的还原,以达到选择性还原的目的。 例如冶炼硅铁﹑中低碳锰和金属铬时,其基本反应式是有其共同点的。如以下3个反应式: SiO2+2C=Si+2CO (7-1) 2MnO+Si=2Mn+SiO2 (7-2) Cr2O3+2Al=2Cr+Al2O3 (7-3) 反应式中C、Si、Al,作为不同的还原剂,分别夺取了氧化物SiO2、MnO、Cr2O3中的氧,元素Si、Mn、Cr从各自的氧化物中被还原出来,组成适当成分的合金。但生产这三种产品的炉子、冶炼方法和原料大不相同。生产硅铁用碳质还原剂,在矿热炉中冶炼,采用电热法; 生产中碳锰铁用硅质还原剂,在精炼电炉中冶炼,采用金属热法;生产金属铬用铝质还原剂,在筒式炉中冶炼。 以上3种合金,虽然生产方法不同,选用的还原剂性质不同,但其冶炼实质相同,可用一通式表达: MeO+M=Me+MO (7-4) 即所需元素氧化物+还原剂=所需元素+还原剂中主元素的氧化物 由于各种元素在矿石中富集程度不一样,存在的状态不一样,冶炼过程就产生了区别,导致了铁合金生产的复杂性。如硅、锰、铬矿中的有用元素的含量较高、杂质含量少时则可不进行元素的富集工艺,而将矿石直接入炉冶炼;如果所用金属氧化物矿较贫,且杂质多,则需富集冶炼;如锰铁比低而磷含量高的贫锰矿,必须先在高炉或电炉中冶炼,将矿石中的磷、铁还原生成高磷生铁,将锰在炉渣中富集后,用其生成的富锰渣代替部分或全部锰矿来进行锰合金的冶炼。还有一些矿石,其中有用的元素含量很低,如钼矿中w(Mo)<0.1%,则必须先经过选矿,富集成含Mo元素较高的钼精矿,才能用来进行钼铁生产;稀有元素在矿石中存在较分散,并且常与其它元素组成化合物,则必须采用化学方法将元素富集后,才能用来进行合金的生产。冶炼钒铁时就是将含钒的矿石,经过多次火法、水法处理富集之后才能进行钒铁的生产。其主要工艺流程是: 高炉冶炼 雾化提钒 含钒铁矿w(V)≈0.1% 含钒生产铁w(V)=0.1%~1% 溶解、浸出、熔烧 电炉冶炼 含钒炉渣w(V2O5)=7%~18%) w(V2O5)=90% 钒铁w[V]≥35% 化学处理 由于钒铁原料的富集处理流程很长,使得铁合金的生产工艺,尤如制取化工产品一样,但其冶炼的本质仍然是: 2/5V2O5+Si=4/5V+SiO2 ` (7-6) 或 1/5V2O5+2/3Al=2/5V+1/3Al2O3 (7-7) 在电炉铁合金的生产中,由于矿石带入杂质,大多数品种的冶炼需要采用有渣法进行,并在炉料中配入适量的溶剂,使矿石中带入的杂质在合金的冶炼过程中生成熔点、碱度适宜,且流动性能良好的炉渣,出炉后便于进行炉渣与合金的分离操作。对于这种需要采用有渣法进行生产的铁合金,冶炼者的主要任务是掌握好炉渣成分、熔点和流动性等,通过对炉渣的控制来控制好合金的成分及质量,但其冶炼本质仍然是氧化物矿石被还原的过程。
3.5.5还原剂的选择
1 金属还原剂
关系曲线中可知,曲线位置低的元素与氧的亲和力大,可用它来还原曲线位置高的氧化物。两曲线在图上的位置相距愈远,表明二者与氧的亲和力相差愈大;还原反应就进行得愈彻底。反之,曲线位置相距愈近,表明二者与氧的亲和力相差不大,还原反应就不可能进行得很彻底。如1800K时,用硅还原FeO的反应就比硅还原MnO的反应进行得更彻底。 可作还原剂的金属很多,但从资源条件、经济性、可行性等综合考虑,大多采用Si、A1作还原剂。如果氧化物比较容易还原如MnO、FeO、Cr2O3等,一般选择Si作还原剂;若氧化物比较难还原,则需选择与氧亲和力更强的元素如A1、Mg来作还原剂,如TiO2用A1还原;BO和ZrO用Al或Mg-A1合金还原。 用金属作还原剂时,有如下特点: (1)还原过程为放热反应,故又称为金属热法。如放出的热量足够使全部金属和炉渣熔化,并加热到必要的高温时,则冶炼过程可在无外加热源的炉子中进行,如用Al作还原剂时可产生足够的热量,无需从外面补充热量,因此,这种冶炼方法又称为铝热法或金属热法。若反应放出的热量较少,尚需从外面补加较多的热量,如用Si作还原剂时,则需在电炉中进行冶炼,用电能来补充热量,故又称为电硅热法。 (2)炼得的合金含碳很低,但可能含有一定数量的还原剂金属。 (3)用金属热法时,冶炼反应迅速,设备简单。
2 碳还原剂
由于CO的稳定性与其他氧化物的不同,随温度的升高其稳定性增加,故CO的Po2线与其他氧化物的Po2线有一交点,高于此点所对应的温度,CO比该氧化物稳定,碳可还原该氧化物;低于该点所对应的温度,则该氧化物比CO稳定,碳不能还原该氧化物。故交点所对应的温度是7 铁合金生产 - 5 - 碳还原该氧化物的最低温度,氧化物越稳定则最低还原温度越高。只要温度足够高,CO的曲线几乎与每种氧化物的Po2线都有交点,所以,原则上讲碳可作为各种金属氧化物的还原剂。在实际生产中,要得到预定的产品,所采用的反应温度只有比最低还原温度高得多,才能保证反应顺利进行。 易还原的氧化物如FeO、MnO,其还原温度较低,一般可在高炉内将其还原成金属;而对于难还原的氧化物如Cr2O3、SiO2等,还原温度高,只有在电炉中才能达到所需要的温度将其还原,故又称其为碳热法。 用碳作还原剂有如下特点: (1)用碳还原氧化物的反应是吸热反应,温度愈高碳的还原能力愈强,只有在一定高温厂,碳才能开始进行还原反应。 (2)用碳作还原剂时,生成碳化物比生成金属的还原反应容易进行。所以,如果生成的金属碳化物溶于合金中,则只能得到碳素合金。例如,用碳还原生产锰铁、铬铁时,得到的是碳素锰铁和碳素铬铁;如果生成的碳化物不溶于合金(如SiC),则得到的合金含碳很低,如硅质合金。如果是生成碳化物能力很强的元素(如Ti、Zr等),则用碳还原其氧化物时(如TiO2、ZrO),得到的产品全是碳化物——碳化钛、碳化锆。 (3)金属的硅化物往往比金属的碳化物稳定,为了降低合金中的C量,可采用增加含Si量的方法来生产一些含Si的铁合金,如硅锰合金、硅铬合金。 (4)还原出来的元素与铁或其他元素互溶或生成合金,将降低还原反应温度使反应易于 进行,减少反应吸收的热量。如生产含w[Si]=45%的硅铁比含w[Si]=75%的硅铁电耗低。 (5)用C作还原剂时,反应产物除所需要的有益元素外,就是CO气体。由于CO气体易 从反应区排除,故反应进行得比较彻底。当原料纯净时,可不用熔剂造渣。如炼制硅铁时,硅石中含w(SiO2)一般大于97%,故冶炼过程可不造渣。 碳质还原剂来源广泛,价格便宜,故广泛用于铁合金生产中。常用的有冶金焦、木炭、石油焦、煤等。
第四章 实习总结
通过这次实习,让我们深刻体会到工作实践与学习有极大地不同。通过对这次实习的认识,我要更加严格要求自己,认真学习,把专业课知识学扎实,打实基础,为以后的工作夯实基础。为以后可以更好地将专业知识运用到工作中做好准备。实习生活结束了,而实习的每一天却仍历历在目,让我难以忘怀。对于我们这些出世未深的学生来说意义重大,而我们也深感责任的艰巨。同样,这次实习,让我们真正体验了生活,理解了生活,我们也感触颇多。实习生活,实际上就是学习的另一种方式,这也是我们在课本上学不到的。然而,正是这次实习,让我们在脑海里对冶金有了一个新的认识,有了一个新的框架,让我们能论与实践相结合,将所学的知识应用到实践中。并且,充分将理论知识与实践经验互相补充,互相融合。在实习的过程中,一点一滴的积累经验,一点一滴的去摸索思考。我想,这正是我们实习的意义所在,实习的目的所在吧。
在这次实习中,我的确学到了许多以前不懂的知识。这无疑对今后的工作有了一个认识,也对今后的测量实践打下了一定的基础,更重要的是为以后的工作积累了宝贵的经验。这次实习生活虽然结束了,但却是我人生当中很有意义的一次经历。
感谢中国贵州铝业分公司让我们有了实践的机会,我们定会在大学期间努力学习,提高自己的专业技能,为将来的工作打下一个坚实的基础。为明天努力奋斗!
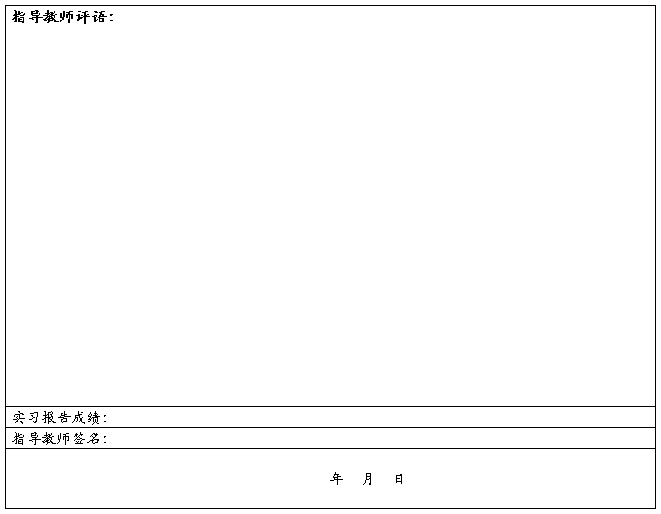