圆垫片冲裁模设计
指导老师:周亚军
姓名:张林琳
班级:10材料
学号:100118023
日期:2013.10.5
目录
摘要.............................................1
一、工艺性分析...................................2
二、工艺方案的确定...............................2
三、冲裁模间隙值确定.............................3
四、凸、凹模刃口尺寸的确定.......................3
五、条料的宽度和导料板间距计算......................4
六、冲裁工艺力和压力中心的计算......................6
七、主要零部件设计..................................8
八、模具总体结构设计................................9
九、压力机的选择.................................11
十、模具总装图......................................11
十一、设计总结......................................12
参考文献............................................12
【摘要】冲压是在室温下,利用安装在压力机上的模具对材料施加压力,使其产生分离或塑性变形,从而获得所需零件的一种压力加工方法。冲压模具在冷冲压加工中,将材料(金属或非金属)加工成零件(或半成品)的一种特殊工艺装备,称为冷冲压模具(俗称冷冲模)。冲压模具是冲压生产必不可少的工艺装备,是技术密集型产品。冲压件的质量、生产效率以及生产成本等,与模具设计和制造有直接关系。模具设计与制造技术水平的高低,是衡量一个国家产品制造水平高低的重要标志之一,在很大程度上决定着产品的质量、效益和新产品的开发能力。
【关键词】圆垫片冲裁模设计、工艺分析、工艺方案、冲裁间隙、凸模与凹模刃口尺寸、条料宽度、导料板间距、冲裁工艺力、压力中心
本设计选取第4组数据:
尺寸a=φ35mm;尺寸b=φ17mm;厚度=1.0mm;精度为IT14;大批量生产;材料为45#钢
一、零件的工艺性分析
该零件是普通圆垫片,材料为45#钢,要对零件进行大批量的生产。该件属于隐蔽件,被完全遮蔽,外观上要求不高,只需平整,中心圆孔是该零件需要保证的重点。
二、确定工艺方案
首先根据零件的形状确定冲压工序类型和选择工序顺序。冲压该零件需要的基本工序有落料和冲孔。
方案一:先落料,再冲孔,采用单工序模生产。
方案二:落料和冲孔复合冲压,采用复合模生产。
方案三:冲孔落料连续冲压,采用级进模生产。
方案一单工序模具结构简单,但需要两道工序、两套模具才能完成零件的加工,生产效率较低,难以满足零件大批量生产的需求。由于零件结构简单,为提高生产效率,主要应采用复合冲裁或级进冲裁方式。
方案二复合模能在压力机一次行程内,完成落料、冲孔等多道工序,所冲压的工件精度较高,不受送料误差影响,内外形相对位置重复性好,由于压料冲裁的同时得到了校平,冲件平直且有较好的剪切断面。
方案三级进模可以加工形状复杂、宽度很小的异形冲裁件,且可冲裁比较厚的零件,但级进模冲裁受压力机工作台面尺寸与工序数的限制,冲裁件尺寸不宜太大。另外级进模冲裁中、小型零件时零件平面度不高,高质量工件需校平。
根据冲压模工艺原理,结合产品(垫圈)结构的特点,通过对比以上三种方案,采用复合模结构简单实用,冲压工艺过程稳定可靠,
比较适合该零件了生产制造。另外为了便于排泄废料,故采用倒装复合模冲裁生产,避免了废料要人工来清除,节省了时间,同时也节省大量劳动力,提高了生产率。所以采用倒装复合模具。
三、冲裁模间隙
凸凹模间隙对冲裁件质量、冲裁力、模具寿命都有很大影响。间隙值有理论确定、经验确定、图表确定三种方法。根据近年来的研究与实际生产经验,在确定间隙值时要按要求分类确定。
本设计中选用图表确定法。根据圆垫片材料为45#钢,厚度为1.0mm,由课本P34 “冲裁模初始间隙值” 表3-4查得Zmin=0.10,Zmax=0.14
考虑到模具在使用过程中的磨损使间隙增大,故选取Z=0.10
四、凸模与凹模刃口尺寸的计算
由p18公差表查得φ17 IT14级为φ170+0.43,由课本P37表3-5“磨损系数”取X=0.5;
由p18公差表查得φ35 IT14级为φ35-0.620,由课本P37表3-5“磨损系数”取X=0.5;
由“冲裁件精度与模具制造精度的关系”确定凸凹模的分别按IT8和IT9级加工制造。
则,冲孔:
dp=(dmin+x△)-δp0=(17+0.5×0.43)-0.0270=17.215-0.0270 mm
dd=(dp+Zmin)0+δd=(17.215+0.10)0+0.043=17.3150+0.043 mm
校核 |δp|+|δd|≤Zmax-Zmin
0.027+0.043≥0.14-0.10
0.07≥0.04 (不满足间隙公差条件),则由δp≤0.4(Zmax-Zmin),δd≤0.6(Zmax-Zmin),则dp=17.2150-0.016mm,dd=17.3150+0.024mmch简单实用,冲压工艺过程稳定可靠。该零件需要的基本工序有落料、
落料:
Dp=(Dmax-x△)0+δp=(35-0.5×0.62)0+0.062=34.690+0.062mm
Dd=(Dp-Zmin)-δp0=(34.69-0.10)-0.0390=34.59-0.0390 mm
校核 |δp|+|δd|≤Zmax-Zmin
0.062+0.039≥0.04
0.101≥0.04 (不满足间隙公差条件),则由δp≤0.4(Zmax-Zmin),δd≤0.6(Zmax-Zmin),则Dp=34.690+0.024mm,Dd=34.590-0.016mmch简单实用,冲压工艺过程稳定可靠。该零件需要的基本工序有落料、
五、条料的宽度和导料板间距计算
1.条料宽度的计算
由课本P46表3-7“最小搭边值”可知,工件间a1=0.8,侧面a=1.0
本设计采用无测压装置冲裁,故
由课本P48公式(3-16)得:
条料宽度 B-△0=(Dmax+2a+Z)-△0
=(35+2×1.0+0.5)-△0
=37.5-0.200
上式中,Z值由课本P50表3-9“导料板与条料之间的最小间隙”知Z=0.5;△值由课本P51表3-11“条料宽度偏差”知△=0.20
2.导料板件距离的计算
由课本P48公式(3-17)得:
导料板间距离B0=B+C=Dmax+2a+2c
=35+2×1.0+2×0.5
=38
确定条料宽度之后,选择1000×500的板料规格,采用横向剪裁。绘制排样图如下:
3.材料利用率
一个步距内的材料利用率
η =A/(B*S) ×100%
=3.14×(35 ²-17 ²)/(37.5×35.8×4)×100%
=2939.04/5370.0×100%
=54.7%
式中,A-一个步距内工件的实际面积;
S-送料步距;
B-条料宽度;
六、冲裁工艺力和压力中心的计算
1.计算工艺力
由课本P52公式(3-21)普通平刃口模具冲裁力 F=KLtτb
一般材料的σb=1.3τb,又K一般为1.3,所以F=Ltσb,式中σb-材料抗拉强度(Mpa)。
查得,45#钢的σb可取得为780 Mpa。
落料力F=Ltσb=35π×1.0×780
=85722N
=85.722KN
冲孔力F=Ltσb=17π×1.0×780
=41636.4N
=41.6364KN
由课本P56表3-15“卸料力、推件力、顶件力系数”查得
KX=0.065-0.075; KT=0.1;
卸料力FX=KXF=85.722×(0.065-0.075)=5.572-6.429KN;
取FX=6KN;
推件力FT=n KTF
上式中工件数n=h/t,h凹模孔口直壁的高度,t为材料厚度;
查得h=4-10,则n=8/1=8;
FT=8×0.1×85.722=685.776KN
冲压工艺力总和FZ=F+FX+FT
=85.722+6.000+685.776
=777.498 KN
2.确定压力中心
因为零件为圆环形垫片,故其压力中心即为其几何中心,在垫片的圆心上。
七、主要零部件设计:
(1)工作零件的结构设计
1、冲孔凸模
结合工件外形并考虑加工,将落料凸模设计成直通式,采用线切割机床加工,台肩固定在凸模固定板上,与凸模固定板的配合按H6/m5。其总长L可按公式计算:凸模L=h1+h2+t+h=h1+l自=(0.6+0.8)*1*+5=28mm
凸模强度的校核由表3-16知,合格。
2、落料凹模
凹模采用整体凹模,各冲裁的凹模孔均采用线切割机床加工,安排凹模在模架上的位置时,要依据计算压力中心的数据,将压力中心与模柄中心重合。其轮廓尺寸可按公式计算:
凹模厚度 H=kb=0.15×34.69mm=5.2mm(查表得k=0.15)
凹模壁厚 c=(1.5~2)H=7.8mm~10.4mm
取凹模厚度H=5mm,凹模壁厚c=10mm,
凹模宽度B=b+2c=(34.69+2×10)mm=55mm
凹模长度L和B相同为55 mm(送料方向)
凹模轮廓尺寸为55mm×55mm×10mm
3、凸凹模
凸凹模长度,Hta=H0-F0+Hx-2-10=80-6.05+10-2-10=72mm
八、模具总体结构设计
冲孔废料由冲孔凸模冲入凹模洞口中,积累到一定数量,由下模漏料孔排出,不必清除废料,操作方便,应用很广,但工件表面平直度较差,凸凹模承受的张力较大,因此凸凹模的壁厚应严格控制,以免强度不足。
经分析,此工件有孔,若采用正装式复合模,操作很不方便;另外,此工件无较高的平直度要求,工件精度要求也较低,所以从操作方便、模具制造简单等方面考虑,决定采用倒装式复合模。
1送料定位机构设计
采用伸缩式挡料销纵向定位,安装在橡胶垫和活动卸料板之间。工作时可随凹模下行而压入孔内,工作很方便.
2卸料机构设计
2.1条料的卸除
采用弹性卸料板。因为是倒装式复合模,所以卸料板安装在下模。
2.2 工件的卸除
采用打料装置将工件从落料凹模中推下,罗在模具工作表面上。
2.3 冲孔废料的卸除
下模座上采用漏料孔排出。冲孔废料在下模的凸凹模内积聚到一定数量,便从下模座的漏料孔中排出。
3 出件机构设计
因为是复合模结构,所以采用上出件机构
4 其他零件尺寸的确定
4.1橡胶垫
为保证橡胶垫不过早失去弹性而破坏,其允许的最大压缩两不得超过摘要高度的45%,一般取自由高度的35%~45%。橡胶垫的预压缩量一般取自由高度的10%~15%。
4.2 凸凹模固定板
凸凹模固定板形状与凹模板一致,厚度为24mm。
4.3凸模固定板
凸模固定板将凸模固定在模座上,其平面轮廓尺寸与凹模板外形尺寸相同,但还应考虑紧固螺钉及销钉的位置。固定板的凸模安装孔与凸模采用过渡配合H7/m6、H7/n6,压装后将凸模端面与固定板一起磨平。凸模固定板为圆形,厚度一般取凹模厚度的0.6~0.8倍,材料为Q235
14mm
4.4垫板
冲裁时,如果凸模的端部对模座的压应力超过模座材料的许用压应力,这时需要在凸模端部与模座之间加上一块强度较高的垫板。由于本套模具选用压入式模柄,在上模座与凸模固定板之间也必须安装垫板,厚度取为8mm。
4.5 卸料板
卸料板同样为圆形板,直径和凹模板一致,厚度为10mm。卸料板材料选A3或(45)钢,不用热处理淬硬。
取卸料板与凸凹模的双面间隙为0.1~0.3mm.
卸料板上设置4个卸料螺钉,公称直径为10mm,螺纹部分为M10×10mm。卸料钉尾部应留有足够的行程空间。卸料螺钉拧紧后,应使卸料板超出凸模端面lmm,有误差时通过在螺钉与卸料板之间安装垫片来调整。
4.6模座
根据凹模板的尺寸,模座采用标准的中间导柱圆形模座,材料采用HT200。
九、压力机的选择
因为该垫片需要大批量生产,故采用高速压力机,采用机器的型号可以为JC23-35
模具的闭合高度为H+H上模+L+H+H下模-h2 =(5+8+28+5+8-2)mm=52mm 式中 L——凸模长度,L=28mm; H——凹模厚度,H=5mm;
h2——凸模冲裁后进入凹模的深度,h2=2mm。
选择压力机JC23-35
公称压力350KN
最大闭合高度280mm
最小闭合高度220mm
所以
压力机工作台尺寸,压力机合格,可用。
十、模具总装图:
通过以上设计,可得到如下图所示的模具总装图。模具上模部分主要由上模板、垫板、凸模、凸模固定板等组成,下模部分由下模座、凹模板、导板、导料板等组成。冲孔废料和成品件均由漏料孔漏出。
条料送进时首先采用始用挡料销作为粗定距,在落料凸模上安装一个导正销,以此作为条料送进的精确定距。操作时完成第二步冲压后,把条料向前移动,用落料孔套在挡料销上,并向前推紧,冲压时凸模上的导正销再作精确定距。活动挡料销位置的设定比理想的几何位置向前偏移0.2mm,冲压过程中粗定位完成以后,当用导正销作精确定位时,由导正销上圆锥形斜面再将条料向后拉回约0.2mm而完成精确定距。用这种方法定距,精度可达0.02mm。具体图解,见装配图。
十一、设计总结
通过对垫片连续模具的设计,我对常用冲压件在冲压过程中对模具的工艺要求有了更深一层的理解,掌握了冲压成型模具的结构特点及设计计算方法,对独立设计模具具有了一次新的锻炼。
根据模具制造的加工工艺,来编写加工工艺卡片。
在设计过程充分利用了各种可以利用的方式,同时在反复的思考中不断深化对各种理论知识的理解,在设计的后一阶段充分利用CAD软件就是一例,新的工具的利用,大在提高了工作效率。
以计算机为手段,专用模具分析设计软件为工具设计模具。软件可直接调用数据库中模架尺寸,金属材料数据库及加工参数,通过几何造型及图形变换可得到模板及凸凹模与型芯形状尺寸迅速完成模具设计。
模具CAD技术是模具传统设计方式的革命,大大提高了设计效率,尤其是系列化或类似冲压模具设计效率更为提高。
【参考文献】
1.《模具设计指导》.史铁梁主编 .机械工业出版社。
2.《冲压模具设计结构图册》.薜啟翔主编 .化学工业出版社。
3.《冲模设计手册》编写组 .机械工业出版社。
4. 《互换性与技术测量》. 魏斯亮主编. 北京理工大学出版社。
5.《模具制造技术》. 成宏主编. 机械工业出版社。
6. 《冲压工艺与模具设计》.魏春雷主编,北京理工大学出版社。
第二篇:垫圈冲压模具设计
兰州交通大学
课程设计说明书
论文题目: 垫圈冲压模具设计
指导教师: 韩兴瑞
学 院: 机电工程学院
专业班级: 材料成型机控制工程092
姓 名:
学 号:
日 期: 20##年12月
垫圈冲压模具设计
摘要:本设计题目为垫圈冲压成形工艺与模具设计,体现了板类冲压零件的设计要求、内容及方向,有一定的设计意义。通过对该零件模具的设计,进一步加强了设计者冲压模具设计的基础知识,为设计更复杂的冲压模具做好了铺垫并吸取了更深刻的经验。
本设计运用冲压成型工艺及模具设计的基础知识,首先分析了工件的成形工艺及模具成形结构对制件质量的影响。介绍了垫板冲压模具设计时要注意的要点,通过对制件进行工艺分析,可确定制件的成形加工用一套复合模即可。从控制制件尺寸精度出发,对垫板冲压模具的各主要尺寸进行了理论计算,以确定各工作零件的尺寸,从模具设计到零部件的加工工艺以及装配工艺等进行详细的阐述,并应用CAD进行各重要零件的设计。
关键词:复合模;工艺分析;模具零部件加工工艺。
目 录
第1章 绪论........................................................... 1
1.1 模具行业的发展现状及市场前景................................... 1
1.2 冲压工艺介绍................................................... 1
1.3 冲压工艺的种类................................................. 2
第2章 冲裁件的工艺分析............................................... 3
2.1冲裁工艺........................................................ 3
2.1.1冲裁工艺概念.............................................. 3
2.1.2冲裁工序分类.............................................. 3
2.2冲裁件的工艺性.................................................. 3
2.2.1冲裁件的结构工艺性........................................ 4
2.2.2冲裁件的尺寸精度和表面粗糙度.............................. 4
2. 3裁工艺方案的确定............................................... 5
第3章 模具的方案设计................................................. 6
3.1模具结构形式的确定.............................................. 6
3.2模具类型的选择.................................................. 6
3.3操作方式........................................................ 6
3.4 卸料、出件方式................................................. 6
3.4.1 卸料方式.................................................. 6
3.4.2出件方式.................................................. 7
3.5确定送料方式.................................................... 7
3.6确定导向方式.................................................... 7
第四章:模具设计计算................................................... 8
4.1 排样方案的确定................................................. 8
4.2搭边的选取...................................................... 8
4.3送料进距、条料宽度计算.......................................... 9
4.3.1送料进距计算.............................................. 9
4.3.2条料宽度计算.............................................. 9
4.4排样图......................................................... 10
4.5计算材料利用率................................................. 10
4.6 冲压力的计算.................................................. 11
4.7压力中心的计算................................................. 13
4.7.1冲模刃口尺寸............................................. 13
4.7.2落料刃口尺寸............................................. 14
4.7.3冲孔刃口尺寸............................................. 14
第5章:主要零部件设计................................................ 15
5.1凹凸模的结构设计............................................... 15
5.1.1凹凸模的刃口形式......................................... 15
5.1.2凹模的外形尺寸计算....................................... 15
5.2 模具的其它零件................................................ 16
5.2.1 模架.................................................... 16
5.2.2模柄..................................................... 16
5.2.3弹压卸料板............................................... 16
5.2.4弹顶和推出装置........................................... 17
5.2.5导向装置(导柱 导套)................................... 18
5.2.6固定零件(固定板、垫板)................................. 18
5.2.7连接零件................................................. 19
第6章 校核模具闭合高度及冲压设备的选择 20
6.1 校核模具闭合高度.............................................. 20
6.2 冲压设备的选定................................................ 20
第7章 绘制模具三维总装图............................................ 21
第8章 模具的安装调试................................................ 22
8.1确定装配方法和装配顺序......................................... 22
8.2装配要点....................................................... 22
设计总结.............................................................. 23
致 谢................................................................................................................................... 24
第1章 绪论
1.1模具行业市场发展状况解读
模具被认为是“工业生产的基础工艺装备”,模具工业是无以伦比的“效益放大器”.用模具加工产品大大提高了生产效率,而且还具有节约原材料,降低能耗和成本,保持产品高一致性等特点。因此模具被称为"效益放大器",在国外,模具被称为“金钥匙”,进入富裕社会的原动力"等等。从另一个角度上看,模具是人性化,时代化,个性化,创造性的产品。更重要的是模具发展了,使用模具的产业其产品的国际竞争力也提高了。据国际模具及塑胶五金产业供应商协会负责人罗百辉介绍,模具可带动其相关产业的比例大约是1:100,即模具发展1亿元,可带动相关产业100亿元,因此,模具产业做为朝阳产业,前景向好。
1.2 冲压工艺介绍
冲压加工是借助于常规或专用冲压设备的动力,使板料在模具里直接受到变形力并进行变形,从而获得一定形状,尺寸和性能的产品零件的生产技术。板料,模具和设备是冲压加工的三要素。冲压加工是一种金属冷变形加工方法。所以,被称之为冷冲压或板料冲压,简称冲压。它是金属塑性加工(或压力加工)的主要方法之一,也隶属于材料成型工程技术。
1.3 冲压工艺的种类
冲压主要是按工艺分类,可分为分离工序和成形工序两大类。分离工序也称冲裁,其目的是使冲压件沿一定轮廓线从板料上分离,同时保证分离断面的质量要求。成形工序的目的是使板料在不破坯的条件下发生塑性变形,制成所需形状和尺寸的工件。在实际生产中,常常是多种工序综合应用于一个工件。冲裁、弯曲、剪切、拉深、胀形、旋压、矫正是几种主要的冲压工艺。
冲压用板料的表面和内在性能对冲压成品的质量影响很大,要求冲压材料厚度精确、均匀;表面光洁,无斑、无疤、无擦伤、无表面裂纹等;屈服强度均匀,无明显方向性;均匀延伸率高;屈强比低;加工硬化性低。
在实际生产中,常用与冲压过程近似的工艺性试验,如拉深性能试验、胀形性能试验等检验材料的冲压性能,以保证成品质量和高的合格率。
模具的精度和结构直接影响冲压件的成形和精度。模具制造成本和寿命则是影响冲压件成本和质量的重要因素。模具设计和制造需要较多的时间,这就延长了新冲压件的生产准备时间。
模座、模架、导向件的标准化和发展简易模具(供小批量生产)、复合模、多工位级进模(供大量生产),以及研制快速换模装置,可减少冲压生产准备工作量和缩短准备时间,能使适用于减少冲压生产准备工作量和缩短准备时间,能使适用于大批量生产的先进冲压技术合理地应用于小批量多品种生产。
冲压设备除了厚板用水压机成形外,一般都采用机械压力机。以现代高速多工位机械压力机为中心,配置开卷、矫平、成品收集、输送等机械以及模具库和快速换模装置,并利用计算机程序控制,可组成高生产率的自动冲压生产线。
在每分钟生产数十、数百件冲压件的情况下,在短暂时间内完成送料、冲压、出件、排废料等工序,常常发生人身、设备和质量事故。因此,冲压中的安全生产是个非常重要的问题。
第2章 冲裁件的工艺分析
2.1冲裁工艺
2.1.1冲裁工艺概念
冲裁是指利用装在压力机上的模具使板料沿着一定的轮廓形状产生分离的一种冲压工艺。
2.1.2冲裁模分类
按工序性质分类:
落料模具:沿封闭轮廓将冲件与板料分离,冲下来的是零件。
冲孔模具:沿封闭轮廓将废料与板料分离,冲下来的是废料。
图2-1垫圈冲裁成型件
2.2冲裁件的工艺性
本次设计的冲压工件零件名称:垫圈,如图2-3生产批量:大批量;材料:20钢;厚度t=2mm;图中未标注公差可按IT12确定工件尺寸公差;冲压件为两个同心圆,无需圆角。查标准公差数值表,各尺寸公差为:φ60 0.3mm; φ28 0.21mm。设计该工件冲裁模工艺方案并绘制模具结构图。
图2-2 冲裁零件图
由图2-2分析知:此工件材料采用20钢,生产批量为大批量,需要用模具进行生产。综合性能较好,强度、塑性等性能较好,有利于成型,总的来说,该零件冲压工艺性较好。
2.2.1冲裁件的结构工艺性
1、冲裁件的形状应符合材料合理的排样,减少废料。
2、冲裁件各直线或曲线的连接处,应有适当的圆角,如表2-1.如果冲裁件有尖角,不仅给冲裁模的制造带来困难,而且模具也容易损坏,只有在采用少废料、无废料排样或镶拼模具结构时不要圆角料。
表2-1 冲裁件的最小过渡圆角半径
2.2.2冲裁件的尺寸精度和表面粗糙度
冲压件尺寸精度的等级要求和表面粗糙度的等级要求是国家推荐标准中的概念,关键就是推荐这两字,实际的冲压生产过程中一般是不采用的,没有什么实际的意义,一般企业生产会根据自己生产的产品要求和实际需要编制未注公差标准和要求,或者采用国家标准公差数值断面表面粗糙度。
冲裁件的断面粗糙度一般为,最高为,见表2-2。
表2-2一般冲裁件断面的表面粗糙度
2. 3工艺方案的确定
该零件包括落料、冲孔两个基本工序。可初选以下几种方案:
方案一:先落料,后冲孔,采用单工序摸生产。模具结构简单、但需要两道工序两副模具,生产效率低。
方案二:落料-冲孔复合冲压,采用复合摸生产。一副模具,形位精度和尺寸精度容易保证,生产率高。
方案三:冲孔-落料连续冲压,采用级进摸生产。一副模具,生产率高,冲压精度稍差,但经济性好。
综上分析,由于冲裁件尺寸精度要求高,形状较小,大批量生产,且板料厚度为。为了保证空位精度和生产效率,分析比较几种冲裁方案后,采用复合模生产。
第3章 模具的方案设计
3.1模具结构形式的确定
复合模是指冲床在一次行程中,完成落料、冲孔等多个工序的一种模具结构。
零件大批量生产,安排生产可采用手工送料方式能够达到批量生产,且能降低模具成本,因此采用手工送料方式。保证孔的精度及较好的定位,宜采用导料板导向,为了提高材料利用率采用始用挡料销和固定挡料销。挡料销控制条料送进距离(步距),送进的距离即等于步距。
3.2模具类型的选择
由冲压工艺分析可知,采用复合模方式冲压,所以模具类型为复合模。
3.3操作方式
零件的生产批量为大批量,但合理安排生产可用手动送料方式,既能满足生产要求,又可以降低生产成本,提高经济效益。
3.4 卸料、出件方式
3.4.1 卸料方式
刚性卸料是采用固定卸料板结构。常用于较硬、较厚且精度要求不高的工件冲裁后卸料。当卸料板只起卸料作用时与凸模的间隙随材料厚度的增加而增大,单边间隙取(0.2~0.5)t。当固定卸料板还要起到对凸模的导向作用时卸料板与 凸模的配合间隙应该小于冲裁间隙。此时要求凸模卸料时不能完全脱离卸料板。主要用于卸料力较大、材料厚度大于2mm且模具结构为倒装的场合。
弹压卸料板具有卸料和压料的双重作用,主要用于料厚小于或等于2mm的板料由于有压料作用,冲件比较平整。卸料板与凸模之间的单边间隙选择(0.1~0.2)t,若弹压卸料板还要起对凸模导向作用时,二者的配合间隙应小于冲裁间隙。常用作落料模、冲孔模、正装复合模的卸料装置。
工件平直度较高,料厚为2mm相对较薄,卸料力较小,弹压卸料模具比刚性卸料模具方便,操作者可以看见条料在模具中的送进动态,且弹性卸料板对工件施加的是柔性力,不会损伤工件表面,所以采用弹性卸料。
3.4.2出件方式
因采用连续模生产,故采用向下落料出件。
3.5确定送料方式
因选用的冲压设备为开式压力机且垂直于送料方向的凹模宽度B小于送料方向的凹模长度L故采用横向送料方式,即由右向左(或由左向右)送料。
3.6确定导向方式
方案一:采用对角导柱模架。由于导柱安装在模具压力中心对称的对角线上,所以上模座在导柱上滑动平稳。常用于横向送料级进模或纵向送料的落料模、复合模。
方案二:采用后侧导柱模架。由于前面和左、右不受限制,送料和操作比较方便。因为导柱安装在后侧,工作时,偏心距会造成导套导柱单边磨损,严重影响模具使用寿命,且不能使用浮动模柄。
方案三:四导柱模架。具有导向平稳、导向准确可靠、刚性好等优点。常用于冲压件尺寸较大或精度要求较高的冲压零件,以及大量生产用的自动冲压模架。
方案四:中间导柱模架。导柱安装在模具的对称线上,导向平稳、准确。但只能一个方向送料。
根据以上方案比较并结合模具结构形式和送料方式,为提高模具寿命和工件质量,该级复合模采用对角侧导柱模架的导向方式,即方案一最佳。
第4章 模具设计计算
4.1 排样方案的确定
排样是指冲裁零件在条料、带料或板料上布置的方法。合理有效的排样有利于保证在最低的材料消耗和高生产率的条件下,得到符合设计技术要求的工件。在冲压生产过程中,保证很低的废料百分率是现代冲压生产重要的技术指标之一。合理利用材料是降低成本的有效措施,尤其在大批量生产中,冲压件的年产量达数十万件,甚至数百万件,材料合理利用的经济效益更为突出。
保证在最低的材料消耗和最高的劳动生产率的条件下得到符合技术要求的零件,同时要考虑方便生产操作、冲模结构简单、寿命长以及车间生产条件和原材料供应等情况,以选择较为合理的排样方案。
根据材料的合理利用情况,条料排样方法可以分为以下三种:
1、有废料排样:冲件与冲件之间、冲件与条料之间都存在搭边废料,冲件尺寸完全由冲模来保证,因此精度高,模具寿命也高,但材料利用率低。
2、少废料排样:只在冲件与冲件之间或冲件与条料之间留有搭边值,因受剪裁条料质量和定位误差的影响,其冲件质量稍差,同时边缘毛刺被凹模带入间隙也影响模具寿命,但材料利用率高,冲模结构简单。
3、无废料排样:冲件与冲件之间或冲件与条料之间均无搭边,沿直线或曲线切断条料而获得冲件。冲件的质量较差,模具寿命较短,但材料利用率高。
采用少、无废料的排样可以简化冲裁模结构,减小冲裁力,提高材料利用率。但是,因条料本身的公差以及条料导向与定位所产生的误差影响,冲裁件公差等级低。同时,由于模具单边受力,不但会加剧模具磨损,降低模具寿命,而且也直接影响冲裁件的断面质量。
综上分析,并考虑冲裁零件的形状、尺寸、材料,选取有废料排样。
4.2搭边的选取
排样时,工件及工件与条料侧边之间的余料叫搭边,搭边的作用是补偿定位误差和保持条料有一定的刚度,以保证冲压件质量和送料方便。搭边太宽,浪费材料;搭边太窄会引起搭边断裂或翘曲,可能“啃刃”现象或冲裁时会被拉断,有时还会拉入模具间隙中、损坏模具刃口,从而影响模具寿命。
搭边值的大小与下列因素有关:
1、材料的力学性能。硬材料可小些,软材料的搭边可要大些。
2、工件的形状与尺寸。尺寸大或有尖突的复杂的形状时,搭边要取得大值。
3、材料厚度。薄材料的搭边值应取的大一些。
4、送料方式及挡料方式。用手工送料、有侧压板导向的搭边值可以取小些。
根据零件形状和尺寸查教材P43页表2.8,可以确定工件的侧搭边值a1=1.6mm,搭边值a=1.3mm。
4.3送料进距、条料宽度计算
4.3.1送料进距计算
模具每次冲裁一次,条料在模具上前进的距离称为送料进距。当单个进距内只冲裁一个零件时,送料进距为:62mm。
4.3.2条料宽度计算
B=60+1.6+1.6+0.8=64mm
根据计算结果,最终确定工件的侧搭边值a1=2mm,搭边值为a=2 mm。
4.4排样图
图4-1
4.5计算材料利用率
冲裁件的实际面积与所用板料面积的百分比叫材料的利用率,它是衡量合理利用材料的重要指标。
一个步距内的材料利用率
K=F/Bh×100%
由此可之,K值越大,材料的利用率就越高,废料越少。废料分为工艺废料和结构废料,结构废料是由本身形状决定的,一般是固定不变的,工艺废料的多少决定于搭边和余量的大小,也决定于排样的形式和冲压方式。因此,要提高材料利用率,就要合理排样,减少工艺废料。
通过选用合适的排样方式提高材料利用率。在保证冲裁件质量的前提下,采用少废料排样或无废料排样。
排样合理与否不但影响材料的经济和利用,还影响到制件的质量、模具的的结构和寿命、制件的生产率和模具的成本等指标。因此,排样时应考虑如下原则:
1、提高材料利用率(不影响制件使用性能的前提下,还可以适当改变制件的形状)。
2、排样方法使应操作方便,劳动强度小且安全。
3、 模具结构简单、寿命高。
4、保证制件质量和制件对板料纤维方向的要求。
所以一个步距内的材料利用率
K=(2826-615)/3968=55.7%
根据计算结果知道选用直排材料利用率可达55.7%,满足要求。
4.6 冲压力的计算
在冲裁过程中,冲裁力是随凸模进入凹模材料的深度而变化的。通常说的冲裁力是指冲裁力的最大值,它是选用压力机和设计模具重要依据之一。
用平刃冲裁时,其冲裁力F一般按下式计算:
P≈Ltσb
式中 F — 冲裁力;
L — 冲裁周边长度;
T — 材料厚度;
σb— 材料抗拉强度(410MPa);
K — 系数;(一般取K=1.3)
卸料力:
Px=KxP
推件力 :
Pt=nKtP
顶件力:
Pd=KdP
式中卸料力、推件力、顶件力系数,如表4-4所示
n-----同时卡在凹模内的工件数量
表4-1 卸料力、推件力及顶件力系数
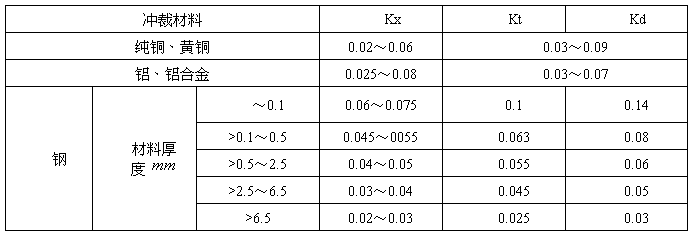
因采用弹性卸料装置和顶件漏料方式,因此需要计算冲裁力和推进力。冲裁力包括冲裁内孔和圆形落料的冲孔力。
冲裁圆形落料力:
P=60π×2×410=154488 N
计算内孔冲孔力:
P=28π×2×410=72094 N
推件力包括冲孔和落料两个工序,取n=3,查表5,取Kt=0.055
落料Pt=3×0.055×154488=25490 N
冲孔Pt=3×0.055×72094=11896 N
卸料力包括冲孔和落料两个工序,查表,取Kx=0.05
落料Px=0.05×154488=7725 N
冲孔Px=0.05×72094=3606 N
冲裁工序力 冲裁工序力是各种冲压工艺的总和,根据不同的模具结构计算,由于本模具采用弹性卸料装置和上出料方式的冲裁模。
=154488+72094+25490+11896+7725+3606
=275.3KN
4.7压力中心的计算
模具的压力中心就是冲压力合力的作用点,为了保证压力机和模具的正常工作,应使模具的压力中心与压力机滑块的中心线相重合。对于级进模以及轮廓形状复杂或多凸模的冲裁模,必须求出冲压力合力的作用点即压力中心。模具的压力中心应与模柄的轴线重合,否则会影响模具及压力机的精度和寿命。
确定压力中心如图4-2所示因为工件为圆形
则冲模的压力中心即工件的几何中心,为圆心。
设计模具时,为选择(0,0)为模具中心。
4.7.1冲模刃口尺寸
因冲模加工方法不同,刃口尺寸的计算方法也不同,基本上可分为两类:
1、按凸模与凹模图样分别加工法:它主要用于圆形或简单规则形状的工作,因冲裁此类工件的凸、凹模制造相对简单,精度容易保证,所以采用分别加工。
2、按凸模与凹模配作法加工:常用于冲制复杂形状的冲模。这种加工方法的特点是模具的间隙有配置保证,工艺比较简单,不必校核的条件,并且还可以放大基准件的制造公差,使制造容易。
查表,确定冲裁间隙为zmin=0.120mm,△z=+0.050mm。
表4-2规则形状凸、凹模的制造偏差
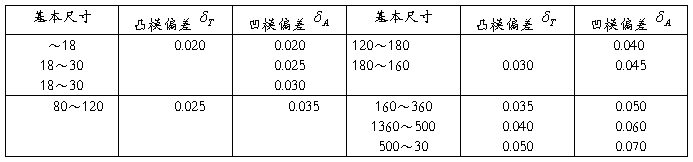
由表4-2确定、
的值
4.7.2落料刃口尺寸
采用配置加工,刃口尺寸以凹模为基准,凸模按相应的凹模实际尺寸进行配制保证双面的间隙为zmin=0.120mm,△z=+0.050mm。
确定所有尺寸的磨损系数均为0.5。
得
Dp=(Dd-zmin)=(D-0.75△-zmin)-δp0
Dd=(D-0.75△)0+δd
4.7.3冲孔刃口尺寸
采用配制加工,刃口尺寸以凸模为基准,凹模尺寸按相应的凸模实际尺寸进行配制,保证双面间隙为zmin=0.120mm,△z=+0.050mm。
确定所有尺寸的磨损系数均为0.5。
dp=(d+x△)-δp0
dd=(d+x△+zmin) 0+δd
第5章:主要零部件设计
5.1凹凸模的设计
5.1.1凹凸模的刃口尺寸设计
1)确定冲裁间隙为,
2)计算落料刃口尺寸,采用互换性加工,刃口尺寸以凸模为基准,凹模尺寸按相应的凸摸实际尺寸进行互换。
零件为IT12级,取.
凸凹模按IT9加工制造,则落料模尺寸:
凸模:Dp =(60-0.75×0.3-2×0.120)0-0.074=59.5350-0.074
凹模:Dd =(60-0.75×0.3)+0.0740=59.775+0.0740
校核:=0.03满足间隙公差条件。
冲孔模尺寸:
凹模:dp =(28+0.75×0.21)0-0.052=28.15750-0.052
凸模:dd =(28+0.75×0.21+0.12)+0.0520=28.2775+0.0520
5.1.2凹模的外形尺寸计算
凹模的外形一般有矩形与圆形两种。凹模的外形尺寸应保证凹模有足够的强度,刚度和修磨量,凹模的外形尺寸一般是根据被冲材料的厚度和冲裁件的最大外形尺寸来确定,凹模的厚度h
查 冲模设计手册图14-15得h= 24mm (5-1)
查资料圆整取标准值h=25mm
凹模壁厚:
查表 取壁厚b=35mm (5-2)
查资料圆整取标准值b=40mm.
式中,Ha—凹模厚度,mm;
F—冲裁力,N;
c—凹模壁厚(指最小壁厚),mm。
(5-3)
凹模的直径:
d= 60+2×25=110mm (5-4)
根据GB/T8057-1995,确定凹模的外形尺寸为
d×h=110×40mm
5.2 模具的其它零件
5.2.1模架
模具除简单冲模外,一般冲模多利用模架的结构。模架的和种类很多,要根据模具的精度要求,模具的类别,模具的大小选择合适的模架.
模架的选择可从《实用模具技术手册》P192页选择标准架。根据查阅的内容及分析,此复合模可选用对角导柱模架、导柱安装在后侧,有偏心裁荷时容易歪斜,滑动不够平稳,可从左右前三个方向关料操作比较方便。所选模架的结构如图5-1所示:
图5-1模架的结构
5.2.2 模柄
模柄的作用是把上模部分与压力机的滑块相连接,并将作用力由压力机传到模具。根据所选用的压力机,选择凸缘模柄。
5.2.3弹压卸料板
卸料板的主要作用是将冲压的料从凸模或凸、凹模上推下来,此外在进模比较复杂的模具中,卸料板还具有保护小凸模作用,常用的卸料板结构形式及适用范围见表11-24和第八章级进模表8-10《实用模具技术手册》卸料板的尺寸可根据《实用模具技术手册》表11-25查得,本模具选用刚性卸料板。
5.2.4弹顶和推出装置
弹顶装置由橡胶元件组成装于模具的下面通过顶杆起到推料的作用,弹顶装置通常在压力机的工作台孔中,弹顶装置结构形式见《冲压模具标准件选用与设计指南》,具体结构及尺寸见装配图及零件图所示。设计过程如下:
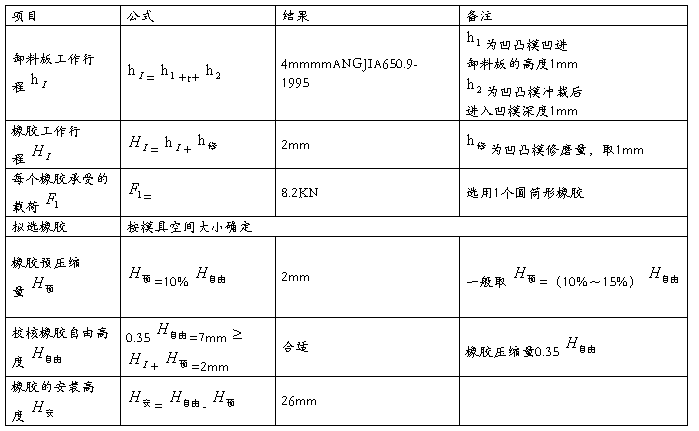
5.2.5导向装置(导柱 导套)
导向装置指得是模架上的导柱、导套。模具在开模,闭模过程中,导柱和导套起导向的作用,使得凸凹模正确的闭合,故此,导柱、导套需要有严格的配合精度及尺寸要求,导柱、导套的选择可以《冲压手册》中选取,(取H7/h6配合)
5.2.6固定零件(固定板、垫板)
1)垫板 垫板的作用是承受凸模和凹模的压力,防止过大的冲压,在上下模座上压出凹坑,影响模具的正常工作,垫板厚度根据压力机的大小选择,一般取5-12mm,外形与固定板相同,材料45钢,热处理后硬度为45-48HRC。
2)固定板 固定板的作用起固定凸、凹模,防止其在冲压过程中松动,造成模具的损坏,固定板的形状要根据凸、凹模而定,而外形尺寸与垫板相似。固定板结构和尺寸关系见装配图及零件图。
5.2.7连接零件
此类零件包括螺钉、销钉等,主要作用是联接其它零部件,使之共同完成工件的组装,螺钉和销钉可由《冲压手册》第十章、第七、八章查选,
第6章 校核模具闭合高度及压力机有关参数
6.1 校核模具闭合高度
模具闭合高度H应该满足
(Hmax-5)≥H≥(Hmin+10)
式中 Hma—压力机最大闭合高度;
Hmin—压力机最小闭合高度;
H —冲模的闭合高度。
根据拟选压力机J23—40A,
经计算该模具闭合高度
H=196mm
因为:180+10mm<196mm<220-5mm
所以:符合要求。
6.2 冲压设备的选定
按上述要求可选用开式可倾压力机,需要在工作台面上加设垫板。型号为JB23-40A,
主要技术参数为:
公称压力:400kN; 滑块行程:120mm;
行程次数:55次/min; 最大封闭高度:220mm;
连杆调节长度:70mm; 工作台板厚度:70mm;
工作台尺寸:480710mm; 电动机功率:4KW;
模柄孔尺寸:φ50×70mm
第7章 绘制模具三维总装图
按已确定的模具形式及参数,从冷冲模标准中选取标准件。绘制模具三维装配图。
图7-1 模具总装配图
工作原理:工作时,板料以挡料销定位,上模下压,凸凹模外形与推荐块配合,在凹模腔内落料,同时冲孔凸模与凹模内控进行冲孔,冲孔废料直接落下;然后上模上行,当滑块碰到上死点时,推杆开始工作,将工件从凹模内推出落下。
第8章 模具的安装调试
8.1确定装配方法和装配顺序
采用直接装配法。先分组装配后总装配。分组装配的有凸模和模柄装配。选择凹模为基准件,先装配下模、再装配上模,最后装配卸料板等辅助零件。
8.2装配要点
1、按装配图标题栏准备模具零部件。
2、装配模柄,将模柄压入到上模座的型孔中,然后用止转销钉用来定位,使其止转。
3、装配凸模,凸模固定板组件
(1)、将冲孔凸模安装在凸模固定板相应孔内,并打上防转销
(2)、将落料凸模安装在凸模固定板相应孔内,并铆接
(3)、端面磨平
4、按装配、调整要领,将导料板,卸料板在凹模上安装合适后,固紧螺钉、钻、铰销孔,装入定位圆销。
5、将凹模组件与下模座安装合适后,固紧螺钉、钻、铰销孔,装入定位圆销。
6、将上模座与凸模固定板,垫块安装合适后,固紧螺钉、钻、铰销孔,装入定位圆销
7、装配后的冲裁凸模、凹模的工件端面应磨平,保证粗糙度Ra0.8。
8、试切
9、装配其他零件(导柱,导套)及标准件。
10、试冲
将装配好的模具安装在指定的压力机上,试冲合格后交付生产使用。
试冲时重点检查各型孔与凸模的间隙合理和均匀、条料送料准确、可靠、无阻滞和落料件、冲孔废料下落顺畅。
设计总结
本学期冲压模具课程设计以老师命题为主,为期一个半月,内容包括数据计算,课程设计说明书制作,图纸绘制以及课程设计小结。以小组为单位进行。
我们认为,在这学期的实验中,在收获知识的同时,还收获了阅历,收获了成熟,在此过程中,我们通过查找大量资料,请教老师,以及不懈的努力,不仅培养了独立思考、动手操作的能力,在各种其它能力上也都有了提高。更重要的是,在实验课上,我们学会了很多学习的方法。而这是日后最实用的,真的是受益匪浅。要面对社会的挑战,只有不断的学习、实践,再学习、再实践。
而且,这对于我们的将来也有很大的帮助。以后,不管有多苦,我想我们都能变苦为乐,找寻有趣的事情,发现其中珍贵的事情。就像中国提倡的艰苦奋斗一样,我们都可以在实验结束之后变的更加成熟,会面对需要面对的事情。
总的来说课程设计锻炼了我们的动手能力与总体规划能力,也让我们对冲压模具有了更深刻的认识,让我们在模具方面有了更大的成长,也学会了合作,学会了彼此迁就与忍让,学会了倾听,学会了正确的表达自我。记住每一次有意义的经历,我们都能成长。
致 谢
在大学三年的努力和学习,在韩兴瑞老师的指导下,我们完成了大学期间很重要的一次作业。以前,我们在校车间进行了实训和在校外的企业进行实习,为现在的模具设计打下了坚实的基础。尽管如此,我们在设计的过程中仍然遇到了一系列问题例如模具材料的选择、定位距离,孔距等等的问题。幸好在老师的指导和帮助下,才能把上述的问题都基本解决,顺利完成了模具设计。通过这次设计,它让我们知道了一种做事的章程,知道了一项计划实现的规划与过程。更重要的是它让我们学会了如何查阅资料,如何将理论实际相结合,学到更多的专业知识。
在这里,我感谢所有教过我们、帮助过我们的老师和同学!在课程设计的这些时间里,我们得到了一种做事的风格,得到了学习的方法,得到了你们传授的知识。
再次感韩兴瑞老师对我们的无私指导!