五金检验与试验作业指导书
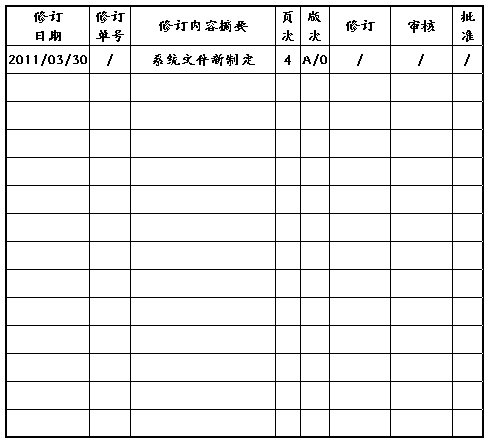

五金检验与试验作业指导书
1、 目的:规范、掌握五金的检验标准和检验方法
2、 适用范围:所使用的五金材质的检验
3、 检验仪器:菲林尺、游标卡尺、塞规、色卡、3M胶纸、酒精(97度)、1KG砝码。
4.0 基本定义
4.1 A 面:指组装成整机后的正前面、上表面及丝印面(在使用过程能直接看到及吸引视觉的表面);
4.2 B 面:指组装成整机后的侧面(需将视线偏转45°~ 90°才能看到的四周边);
4.3 C 面:指组装成整机后的背面及底面(正常使用时看不到的背面及底面)。
4.4 ΔE (Delta-E):在均匀颜色感觉空间中,人眼感觉色差的测试单位。当 ΔE 为1.0时,人眼就可以感觉到色彩的变化了。这种测试方法用于当用户指定或接受某种颜色时,产商用以保证色彩一致性的量度。
5.0 不良缺陷定义
5.1、不良缺陷
5.1.1 毛边:由于机械冲压或切割后未处理好,导致加工件边缘或分型面处所产生的金属毛刺。
5.1.2 划伤:由于在加工或包装、运输过程中防护不当导致产品表面出现的划痕、削伤。
5.1.3 裁切不齐:由于产品在加工过程中定位或设备固定不当,导致产品边缘切割不齐。
5.1.4 变形:因加工设备调校不当或材料因內应力而造成的产品平面形变。
5.1.5 氧化生锈:因产品加工后未进行相应防锈处理或处理措施不当,而导致产品表面出现锈斑。
5.1.6 尺寸偏差:因加工设备的精度不够,导致产品尺寸偏差超过设计允许水平。
5.1.7“R 角”过大/小:产品因折弯或冲压设备精度不够,导致折弯处弧度过大/小。
5.1.8 表面凹痕:由于材料热处理不好或材料生锈,其内部杂质导致金属表面形成的凹痕。
5.1.9 倒圆角不够:产品裁切边缘因切割或冲压原因产生的锐边未处理成圆弧状,易导致割手。
5.1.10 异色点:在产品表面出現颜色异于周围颜色的点。
5.1.11 破裂:因机加工损伤而造成产品的裂纹或细小开裂。
5.1.12 麻点:喷涂件表面上有附著的细小颗粒。
5.1.13 堆漆:喷涂件表面出现局部的油漆堆积现象。
5.1.14 阴影:喷涂件表面出现的颜色比周围暗的区域。
5.1.15 露底:喷涂件出现局部的油漆过薄而露出底材颜色的现象。
5.1.16 鱼眼:由于溶剂挥发速度不对而在喷涂件表面出现凹痕或小坑。
5.1.17 飞油:超出了规定的喷涂区域。
5.1.18 剥落:产品表面出现涂层脱落的现象。
5.1.19 色差:产品表面顏色与标准样品颜色有差异。
5.1.20 手印:产品表面出现的手指印。
5.1.21 硬划痕:由于硬物磨擦而造成产品表面有明显深度的划痕(用指甲刮有明显感觉)。
5.1.22 软划伤:沒有明显深度的划痕(无手感,但肉眼能明显看出)。
5.1.23 毛丝:产品表面出现细小的尘丝。
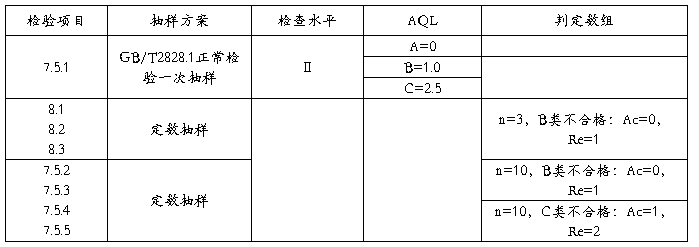
6、抽样方案:
7、检验项目,技术要求及判定标准
7.1 外观检验条件
7.1.1 光源:物件距光源0.65~1.0m 的40W日光灯下。
7.1.2 目视距离:30-40cm。
7.1.3 目视角度:检测面与人眼方向成45°~ 90°。
7.1.4 目视时间:5 ~10S。
7.2 检验常用单位代码对照表

7.3 检验标准说明
7.3.1 当非异色的缺陷的直径D<0.20mm 且不连续时,可以不作为缺陷。
7.3.2 以下所提到的不良缺陷的数目均指单面上的不良缺陷数目。
7.3.3 以下所提到的不良缺陷的数目中A 面缺点总数不大于2,B 面缺点总数不大于3,C面缺点总数不大于5。
7.3.4 各材料如有本标准未规定之要求或不同于本标准要求,则应按相应工程资料及《来料检验与试验控制程序》的不合格定义执行。
7.4 外观检验允收标准
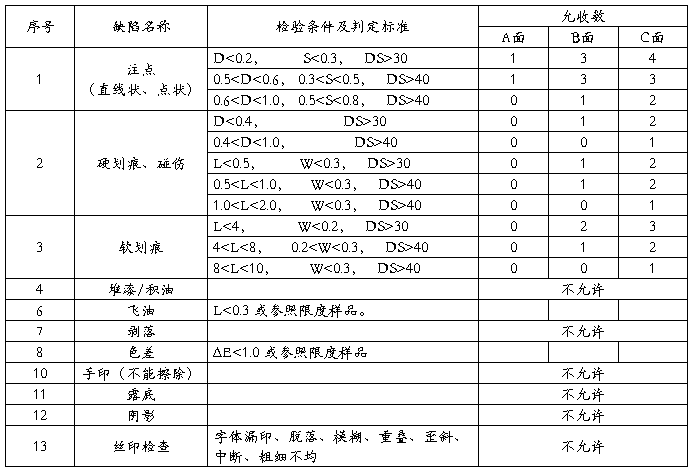
注:1、注点状缺陷包括颗粒、尘点、毛丝、鱼眼等呈现点状的缺陷。(异色点不允许)。
7.5检验项目:缺陷分类、缺陷判定、检验方法
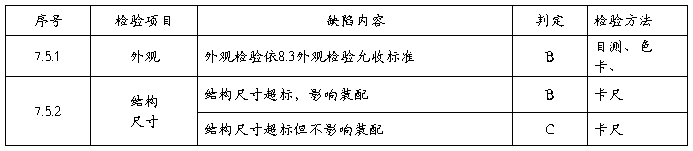
8、试验项目,技术要求及判定标准
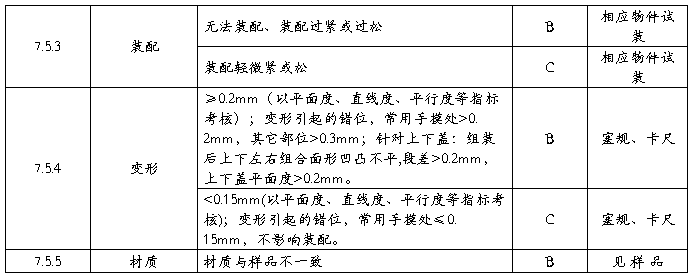
8.1 附着力测试:
8.1.1 测试规范及要求:用3M 胶纸(型号:600#)贴于样品丝印表面并按紧,使胶带均匀粘附于样品表面,提起胶带一边沿45°角迅速拉起,拉起胶带后丝印无脱落现象,每单位测试样品以五次试验后结果为准。
8.1.2 附着力判定标准:

8.2百格试验
8.2.1 测试规范及要求:用刀片在被测样品表面割划1*1mm2的方格(伤至本体上),用3M 胶纸(型号600#)
贴于其表面并按紧,使胶带均匀粘附于样品表面,然后提起胶带一边沿45°角迅速拉起,拉起胶带后方格內涂装无脱落现象,每单位测试样品以两次试验后结果为准。
8.2.2判定标准:

8.3、防腐测试
8.3.1 测试规范及要求:用浓度为95-98%的酒精湿润棉布,以1kg 的力,每秒一次循环的频率來回擦于被测品喷油或丝印表面,擦拭长度大于5cm,擦拭20次后丝印字体不可有变形与脱落现象,50 次后喷油不可露底。
8.3.2 判定标准:

9、相关记录:
9.1《IQC检验日报表》
9.2《IQC检验检验不合格报告》
第二篇:五金件检验标准
五金冲压件检验标准
文件编号:PZBJB2005002 版本/修订号:A/1
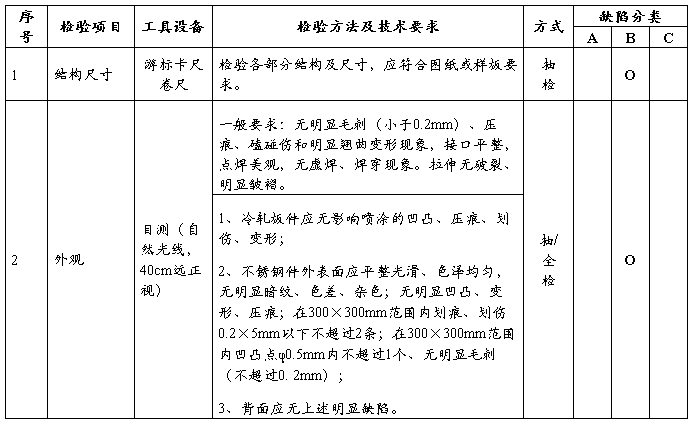
注:1、彩图板件与不锈钢件(除配件外)生产时需全检第2项。
2、抽样检验按GB2828正常检查一次抽样方案 IL=Ⅱ AQL:A类=2.5 B类=4.0 C类=6.5
制定:王记召 2/12/05 审批:
不锈钢彩板检验标准
文件编号:PZBJB2005001 版本/修订号:A/1
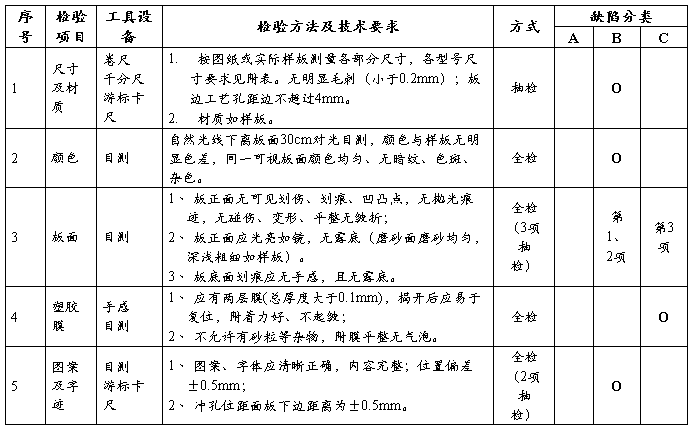
注: 1、抽样检验:按GB2828正常检查一次抽样方案 IL=I AQL:A类=2.5 B类=4.0 C类=6.5;
2、抽检合格后全检。
附表: 各型号灶具(嵌入式)面板规格一览表
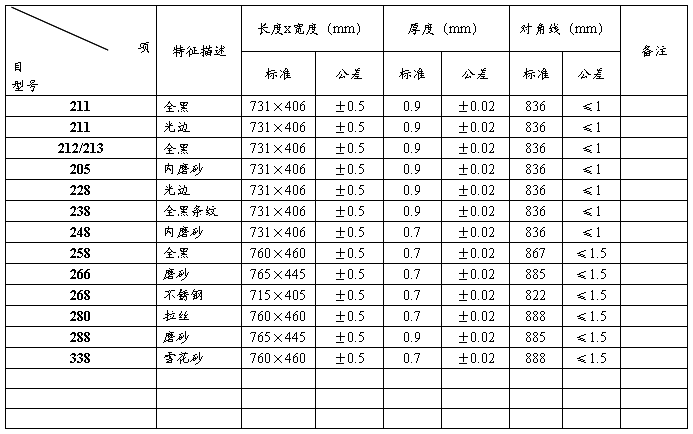
制定: 王记召20##-10-12 审批:
冲压板材检验标准
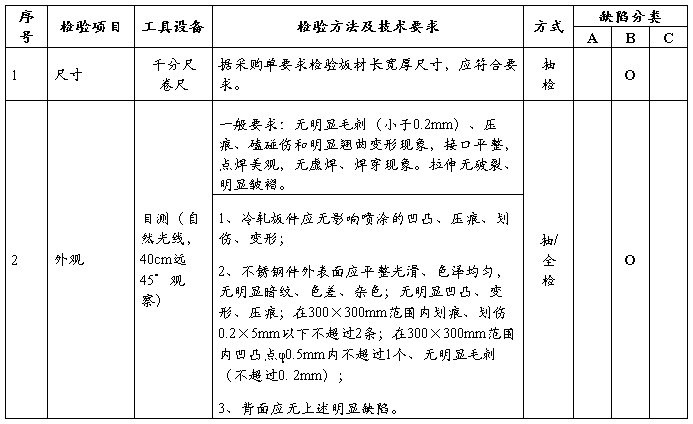
注:1、彩图板件与不锈钢件(除配件外)生产时需全检第2项。
2、抽样检验按GB2828正常检查一次抽样方案 IL=Ⅱ AQL:A类=2.5 B类=4.0 C类=6.5
制定:王记召 2/12/05 审批:
不锈钢面板、彩图板检验标准
文件编号:PZBJB2006001 版本/修订号:A/2
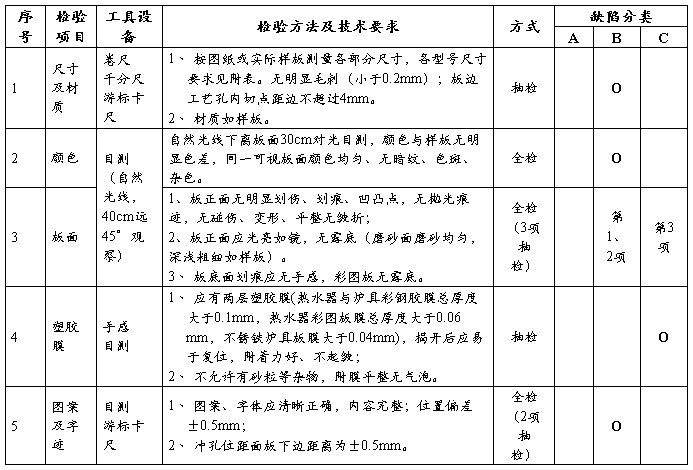
注: 1、抽样检验:按GB2828正常检查一次抽样方案 IL=I AQL:A类=2.5 B类=4.0 C类=6.5;
2、抽检合格后全检,全检项目按以上检验方式。
制定: 郑双明20##-1-12 审批:
附表: 各型号板材规格一览表
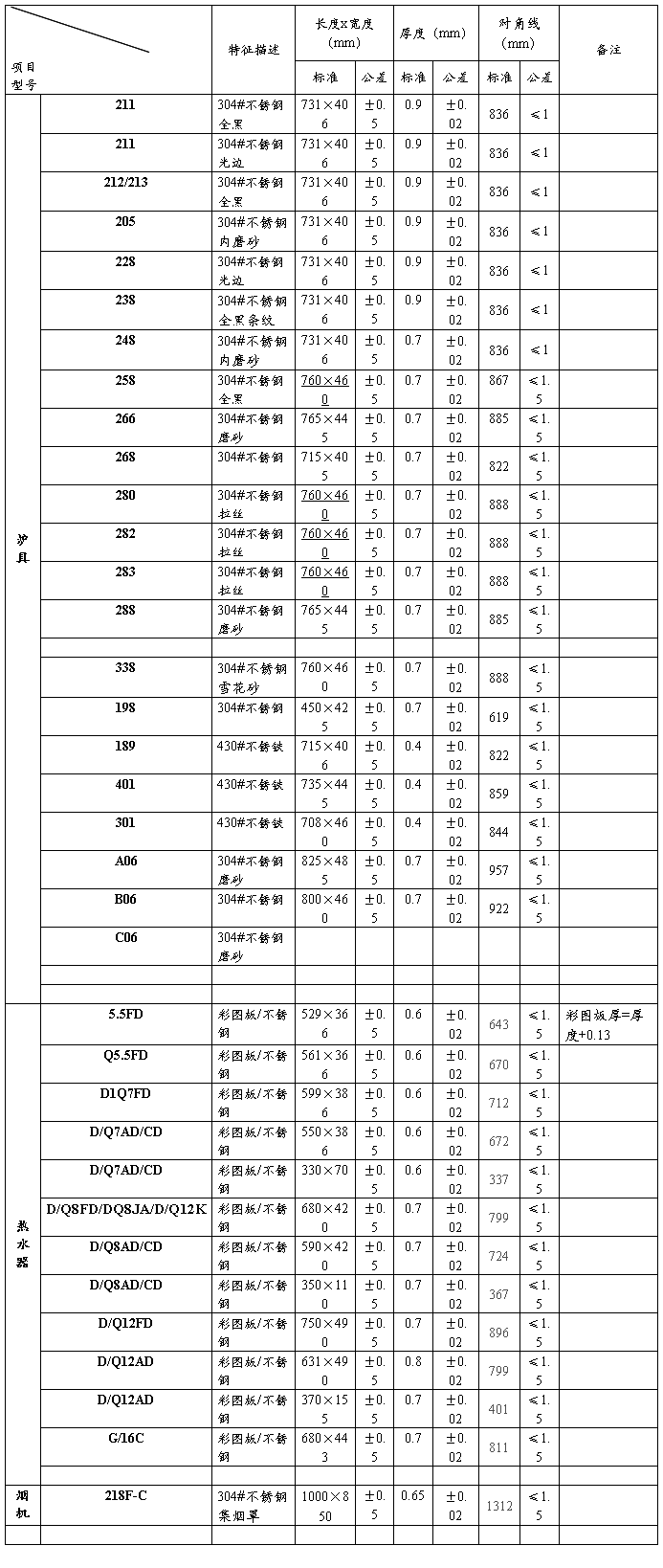