攀枝花学院
学生课程设计(论文)
题 目: 组合机床动力滑台液压系统的设计
学生姓名: 学 号:
所在院(系): 机械工程学院
专 业: 机械设计制造及其自动化
班 级:
指 导 教 师: 职称:
20##年6月13日
攀枝花学院教务处制
攀枝花学院本科学生课程设计任务书
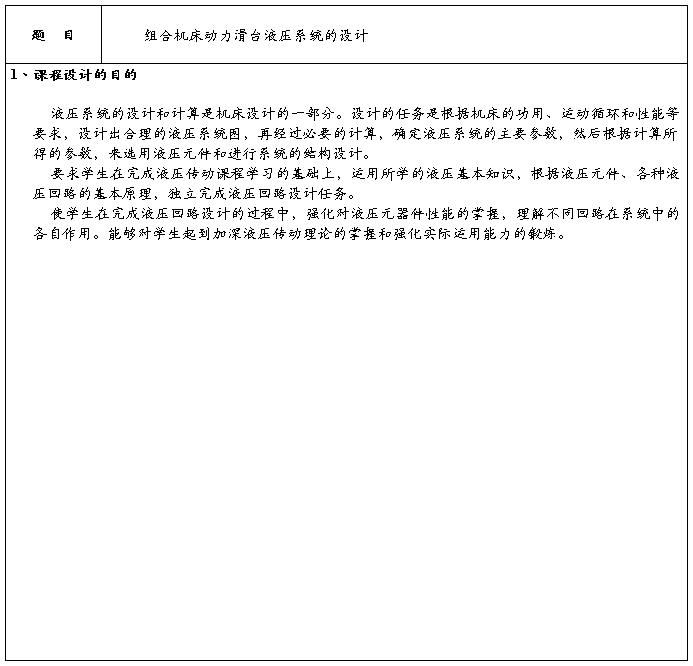
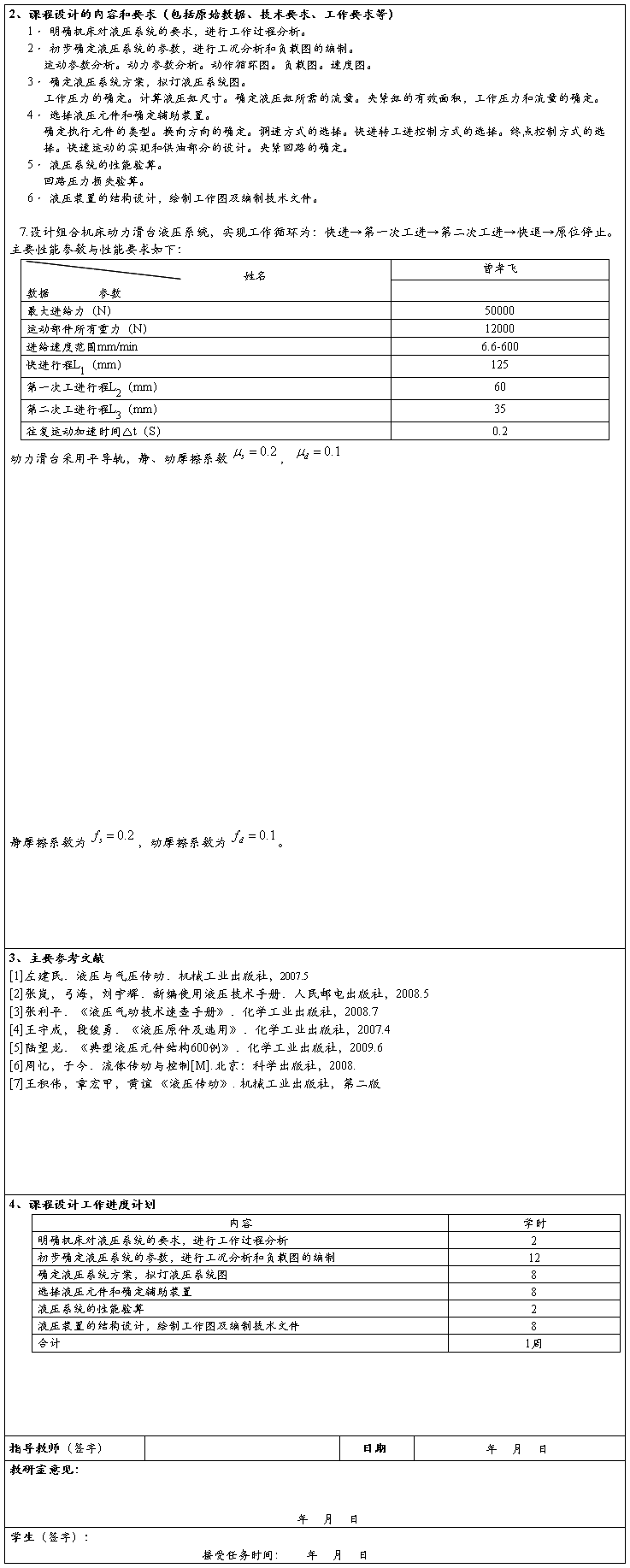
注:任务书由指导教师填写。
课程设计(论文)指导教师成绩评定表
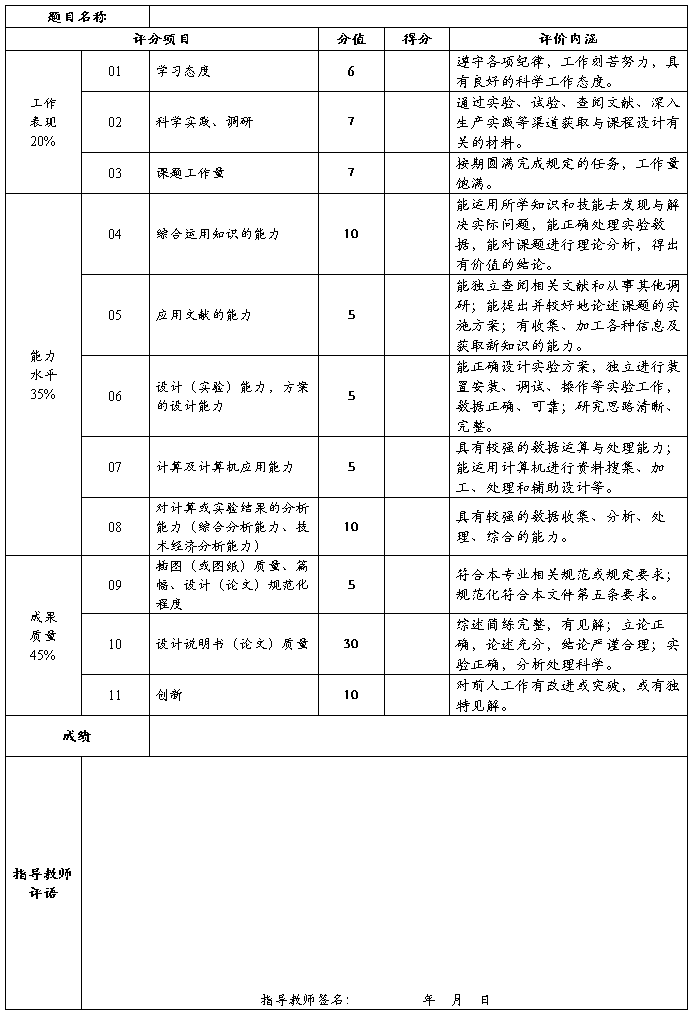
摘要
本说明书主要用于说明根据工作进程和一些工作要求设计出的组合机床动力滑台液压系统,能实现的工作循环是:快进→ 第一次工进→ 第二次工进→快退 →原位停止。液压技术是机械设备中发展速度最快的技术之一。特别是近年可与微电子、计算机技术相结合、使液压技术进入了一个新的发展阶段。目前,已广泛应用在工业各领域。由于近年来微电子、计算机技术的发展,液压元器件制造技术的进一步提高,使液压技术不仅在作为一种基本的传统形式上占有重要地位而且以优良的静态、动态性能成为一种重要的控制手段。
面对我国经济近年来的快速发展,机械制造工业的壮大,在国民经济中占重要地位的制造业领域得以健康快速的发展。制造装备的改进,使得作为制造工业重要设备的各类机加工艺装备也有了许多新的变化。
本液压系统的设计,除了满足主机在动作和性能方面规定的要求外,还必须符合体积小、重量轻、成本低、效率高、结构简单、工作可靠、使用和维修方便等一些公认的普遍设计原则。液压系统的设计主要是根据已知的条件,来确定液压工作方案、液压流量、压力和液压泵及其它元件的设计。
综上所述,完成整个设计过程需要进行一系列艰巨的工作。设计者首先应树立正确的设计思想,努力掌握先进的科学技术知识和科学的辩证的思想方法。同时,还要坚持理论联系实际,并在实践中不断总结和积累设计经验,向有关领域的科技工作者和从事生产实践的工作者学习,不断发展和创新,才能较好地完成机械设计任务。
关键词: 组合机床 液压系统 液压缸
目录
摘要............................................................................................................................ I
1 设计要求.................................................................................................................... 1
1.1前言(设计任务书)............................................................................................ 1
1.2液压传动的发展概况和应用................................................................................. 2
1.2.1 液压传动的发展概况..................................................................................... 2
1.2.2 液压传动在机械行业中的应用....................................................................... 2
1.2.3 静液压传动装置的应用................................................................................. 3
1.3液压传动的工作原理和组成................................................................................. 4
1.3.1工作原理....................................................................................................... 4
1.3.2液压系统的基本组成...................................................................................... 4
1.4液压传动的优缺点............................................................................................... 5
1.4.1液压传动的优点............................................................................................. 5
1.4.2 液压传动的缺点............................................................................................ 5
2 负载分析.................................................................................................................... 7
2.1题目分析与假设................................................................................................... 7
2.2负载分析............................................................................................................. 7
2.3液压缸各阶段的负载............................................................................................ 8
2.4负载图和速度图的绘制........................................................................................ 9
3 液压缸参数的确定..................................................................................................... 11
3.1初选液压缸的工作压力....................................................................................... 11
3.2.液压缸尺寸........................................................................................................ 11
3.3液压缸的最大流量.............................................................................................. 12
3.4各工作段液压缸压力.......................................................................................... 12
3.5各工作段功率..................................................................................................... 12
3.6绘制工况图........................................................................................................ 12
3.7液压缸其余参数................................................................................................. 13
4 液压系统图的拟定..................................................................................................... 16
4.1供油方式的选择................................................................................................. 16
4.2速度控制回路..................................................................................................... 16
4.3液压系统原理..................................................................................................... 20
5 液压元件的选择........................................................................................................ 22
5.1确定液压泵的型号和电动机的功率..................................................................... 22
5.2选择阀类元件及辅助元件................................................................................... 22
6 液压系统的验算........................................................................................................ 24
参考文献........................................................................................................................ 25
1 设计要求
1.1前言(设计任务书)
1.1.1课程设计的目的
液压传动与控制课程设计是机械电子工程专业学生在学完《流体传动与控制》以及其他有关课程,并经过生产实习后进行的一个重要的实践性教学环节。学生通过本课程设计能够进一步熟悉并掌握液压传动与控制的基本概念、熟悉液压元件结构原理、熟悉液压基本回路、掌握液压系统图的阅读方法及基本技能、能够综合运用本课程及工程力学、机械设计等有关课程的知识设计一般工程设备液压系统。
同时,学生通过本课程设计可在以下几方面得到训练:
1正确进行工程运算和使用技术文件、技术资料的能力;
2掌握系统方案设计的一般方法;
3正确表达设计思想的方法和能力;
4综合利用所学知识解决工程实际问题的能力。
1.1.2 课程设计题目
设计组合机床动力滑台液压系统,实现工作循环为:快进→第一次工进→第二次工进→快退→原位停止。主要性能参数与性能要求如下:
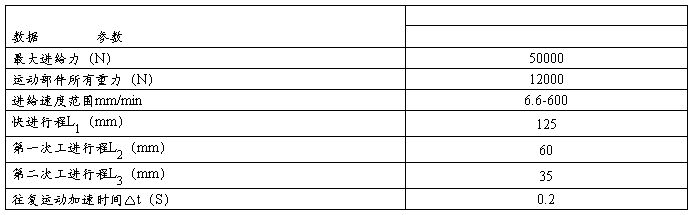
动力滑台采用平导轨,静、动摩擦系数,
1.1.3课程设计主要内容
1)查阅文献,了解并熟悉设计工况;
2)确定液压系统及主油缸的主要参数;
3)绘制系统原理图;
4)计算选择各液压元件;
5)验算系统性能;
6)绘制主液压缸装配图;
7)编制技术文件,撰写课程设计说明书;
1.2液压传动的发展概况和应用
1.2.1 液压传动的发展概况
液压传动和气压传动称为流体传动,是根据17世纪帕斯卡提出的液体静压力传动原理而发展起来的一门新兴技术,是工农业生产中广为应用的一门技术。如今,流体传动技术水平的高低已成为一个国家工业发展水平的重要标志。
第一个使用液压原理的是1795年英国约瑟夫·布拉曼(Joseph Braman,1749-1814),在伦敦用水作为工作介质,以水压机的形式将其应用于工业上,诞生了世界上第一台水压机。1905年他又将工作介质水改为油,进一步得到改善。
第一次世界大战(1914-1918)后液压传动广泛应用,特别是1920年以后,发展更为迅速。液压元件大约在 19 世纪末 20 世纪初的20年间,才开始进入正规的工业生产阶段。1925 年维克斯(F.Vikers)发明了压力平衡式叶片泵,为近代液压元件工业或液压传动 的逐步建立奠定了基础。20 世纪初康斯坦丁·尼斯克(G·Constantimsco)对能量波动传递所进行的理论及实际研究;1910年对液力传动(液力联轴节、液力变矩器等)方面的贡献,使这两方面领域得到了发展。
我国的液压工业开始于20世纪50年代,液压元件最初应用于机床和锻压设备。60年代获得较大发展,已渗透到各个工业部门,在机床、工程机械、冶金、农业机械、汽车、船舶、航空、石油以及军工等工业中都得到了普遍的应用。当前液压技术正向高压、高速、大功率、高效率、低噪声、低能耗、长寿命、高度集成化等方向发展。同时,新元件的应用、系统计算机辅助设计、计算机仿真和优化、微机控制等工作,也取得了显著成果。
目前,我国的液压件已从低压到高压形成系列,并生产出许多新型元件,如插装式锥阀、电液比例阀、电液伺服阀、电业数字控制阀等。我国机械工业在认真消化、推广国外引进的先进液压技术的同时,大力研制、开发国产液压件新产品,加强产品质量可靠性和新技术应用的研究,积极采用国际标准,合理调整产品结构,对一些性能差而且不符合国家标准的液压件产品,采用逐步淘汰的措施。由此可见,随着科学技术的迅速发展,液压技术将获得进一步发展,在各种机械设备上的应用将更加广泛。
1.2.2 液压传动在机械行业中的应用
机床工业——磨床、铣床、刨床、拉床、压力机、自动机床、组合机床、数控机床、加工中心等
工程机械——挖掘机、装载机、推土机等
汽车工业——自卸式汽车、平板车、高空作业车等
农业机械——联合收割机的控制系统、拖拉机的悬挂装置等
轻工机械——打包机、注塑机、校直机、橡胶硫化机、造纸机等
冶金机械——电炉控制系统、轧钢机控制系统等
起重运输机械——起重机、叉车、装卸机械、液压千斤顶等
矿山机械——开采机、提升机、液压支架等
建筑机械——打桩机、平地机等
船舶港口机械——起货机、锚机、舵机等
铸造机械——砂型压实机、加料机、压铸机等
1.2.3 静液压传动装置的应用
静液压传动由于具有无级变速,调速范围宽,可以实现恒扭或恒功率调速,容易实现电控等优点,在工程机械中具有良好的应用前景。但是在铲土运输机械和起重机械中作为主要传动就用却很少,其主要问题是在于国内液压元件质量差,而国外的液压元件价格又太高,会造成主同成本过高。90年代以来,国内已引进了德国林德公司静液压叉车,以及利勃海尔公司静液压推土机的装载机,但在国内市场所占份额很小。从国内工程机械市场的实际出发,本文对静液压传动在国内的推广应用提出探讨性的意见如下:
(1)静液压传动叉车在发达国家已经被广泛采用,由于国内部分仓库、码头和工厂等使用部门对叉车的机动性能(尤其是低速性能)、噪声已经有较高的要求,因此这些部门正在成为国内静液压叉车用户。国内叉车和液压元件生产企业应该看到静液压叉车的良好前景,联合研究开发适合我国国情的叉车静液压系统,提供能先进,工作可靠,价格适中的产品。也可以采用与国际静液压元件制造公司联合开发的方式,加快开发的速度。
(2)中小型多功能工程机械由于具有挖掘,装载,叉车和起重等多功能,在发达国家已经得到了广泛的应用。随着我国经济建设尤其是城市建设的发展,中小型多功能工程机械也将在我国推广应用,而它们无疑将首先采用静液压传动作为其主要传动装置。国内工程机械企业应该看到中小型多功能工程机械的发前景,联合国内外静液压元件生产企业共同开展对它们的研究开发,以促进中小型多功能工程机械在我国的发展。
(3)在国内大型铲土运输和起重机械中,由于配套的静液压与电子控制元件的技术难度大,价格太高,在国内用户中难以接受。因此,在我国暂时不宜将静液压传动研究开发的重点放在与大型铲土运输和起重机械配套上,而应将重点放在上述两类工程机械上。
1.3液压传动的工作原理和组成
液压传动是用液体作为工作介质来传递能量和进行控制的传动方式。液压系统利用液压泵将原动机的机械能转换为液体的压力能,通过液体压力能的变化来传递能量,经过各种控制阀和管路的传递,借助于液压执行元件(缸或马达)把液体压力能转换为机械能,从而驱动工作机构,实现直线往复运动和回转运动。 驱动机床工作台的液压系统是由油箱、过滤器、液压泵、溢流阀、开停阀、节流阀、换向阀、液压缸以及连接这些元件的油管、接头等组成。
1.3.1工作原理
1)电动机驱动液压泵经滤油器从油箱中吸油,油液被加压后,从泵的输出口输入管路。油液经开停阀、节流阀、换向阀进入液压缸,推动活塞而使工作台左右移动。液压缸里的油液经换向阀和回油管排回油箱。
2)工作台的移动速度是通过节流阀来调节的。当节流阀开大时,进入液压缸的油量增多,工作台的移动速度增大;当节流阀关小时,进入液压缸的油量减少,工作台的移动速度减少。由此可见,速度是由油量决定的。
1.3.2液压系统的基本组成
1)能源装置——液压泵。它将动力部分(电动机或其它远动机)所输出的机械能转换成液压能,给系统提供压力油液。
2)执行装置——液压机(液压缸、液压马达)。通过它将液压能转换成机械能,推动负载做功。
3)控制装置——液压阀。通过它们的控制和调节,使液流的压力、流速和方向得以改变,从而改变执行元件的力(或力矩)、速度和方向,根据控制功能的不同,液压阀可分为村力控制阀、流量控制阀和方向控制阀。压力控制阀又分为益流阀(安全阀)、减压阀、顺序阀、压力继电器等;流量控制阀包括节流阀、调整阀、分流集流阀等;方向控制阀包括单向阀、液控单向阀、梭阀、换向阀等。根据控制方式不同,液压阀可分为开关式控制阀、定值控制阀和比例控制阀。
4)辅助装置——油箱、管路、蓄能器、滤油器、管接头、压力表开关等.通过这些元件把系统联接起来,以实现各种工作循环。
5)工作介质——液压油。绝大多数液压油采用矿物油,系统用它来传递能量或信息。
1.4液压传动的优缺点
1.4.1液压传动的优点
1)在相同的体积下,液压执行装置能比电气装置产生出更大的动力。在同等功率的情况下,液压执行装置的体积小、重量轻、结构紧凑。液压马达的体积重量只有同等功率电动机的12%左右。
2)液压执行装置的工作比较平稳。由于液压执行装置重量轻、惯性小、反应快,所以易于实现快速起动、制动和频繁地换向。液压装置的换向频率,在实现往复回转运动时可达到每分钟500次,实现往复直线运动时可达每分钟1000次。
3)液压传动可在大范围内实现无级调速(调速比可达1:2000),并可在液压装置运行的过程中进行调速。
4)液压传动容易实现自动化,因为它是对液体的压力、流量和流动方向进行控制或调节,操纵很方便。当液压控制和电气控制或气动控制结合使用时,能实现较复杂的顺序动作和远程控制。
5)液压装置易于实现过载保护且液压件能自行润滑,因此使用寿命长。
6)由于液压元件已实现了标准化、系列化和通用化,所以液压系统的设计、制造和使用都比较方便。
1.4.2 液压传动的缺点
1)液压传动是以液体为工作介质,在相对运动表面间不可避免地要有泄漏,同时,液体又不是绝对不可压缩的,因此不宜在传动比要求严格的场合采用,例如螺纹和齿轮加工机床的内传动链系统。
2)液压传动在工作过程中有较多的能量损失,如摩擦损失、泄漏损失等,故不宜于远距离传动。
3)液压传动对油温的变化比较敏感,油温变化会影响运动的稳定性。因此,在低温和高温条件下,采用液压传动有一定的困难。
4)为了减少泄露,液压元件的制造精度要求高,因此,液压元件的制造成本高,而且对油液的污染比较敏感。
5)液压系统故障的诊断比较困难,因此对维修人员提出了更高的要求,既要系统地掌握液压传动的理论知识,又要有一定的实践经验。
6)随着高压、高速、高效率和大流量化,液压元件和系统的噪声日益增大,这也是要解决的问题。
总而言之,液压传动的优点是突出的,随着科学技术的进步,液压传动的缺点将得到克服,液压传动将日益完善,液压技术与电子技术及其它传动方式的结合更是前途无量。
2 负载分析
2.1题目分析与假设
由于题目中只给了进给速度的范围,所以根据题意作如下假设,
设:快进速度为0.1m?s-1 ,
第一次工进速度0.001 m?s-1 ,
第二次工进速度0.0005 m?s-1,
快退速度0.1m?s-1
第一次工进切削负载
第二次工进切削负载
则动力滑台运动参数和动力参数如下:
表2.1 动力滑台运动参数和动力参数
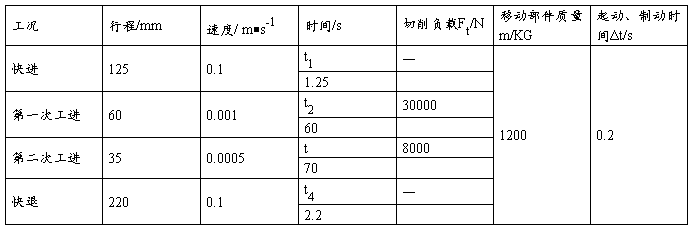
2.2负载分析
1)工作负载
第一次工进:
第二次工进:
2)摩擦负载
静摩擦力:
动摩擦力:
3)惯性负载
加速(启动—快进):
N
减速(快进—工进1):
N
减速 (工进1—工进2):
制动(工进2—停留):
N
反向加速(停留—快退):
N
反向制动(快退—停止):
N
2.3液压缸各阶段的负载
液压缸各阶段负载如下表所示
表2.3 液压缸各阶段负载
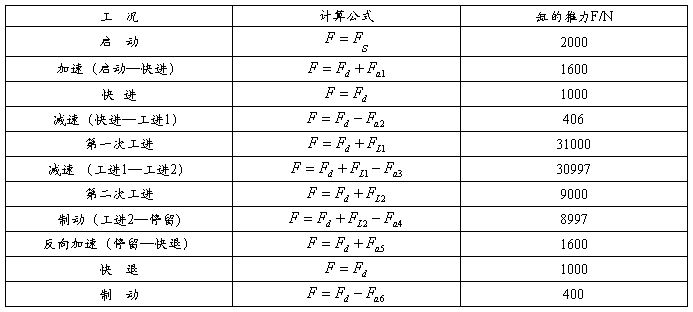
2.4负载图和速度图的绘制
按照前面的负载分析结果及已知的速度、行程等,绘制负载图及速度图如下:
图2.4 负载图和速度图
3 液压缸参数的确定
3.1初选液压缸的工作压力
此设备属机床类且所加工的孔的粗糙度及尺寸精度要求较高,且最大负载为 42000N,查表3-6,初选液压缸的工作压力为5.0MPa。
3.2.液压缸尺寸
图3.2 液压缸
A=F/P=
查GB/T2348—1993,按标准取缸筒内径D=100mm。
由题意可知
,所以
,则活塞杆的直
查GB/T2348—1993,按标准取d=70mm。
则液压缸的有效作用面积为:
无杆腔面积
有杆腔面积
由于缸体总行程为220mm,而活塞杆直径d=70mm,<10,故不需进行稳定性校核。
3.3液压缸的最大流量
3.4各工作段液压缸压力
3.5各工作段功率
3.6绘制工况图
归纳工作循环中各个工作阶段的液压缸压力、流量和功率如下表:
表3.6 各工作阶段液压缸压力、流量、功率
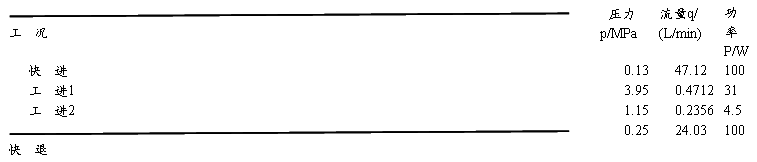
由上表可绘出液压缸的工况图,如下:
图3.6 液压缸工况图
3.7液压缸其余参数
3.7.1液压缸的壁厚
液压缸的壁厚由液压缸的强度条件来计算。
液压缸的壁厚一般是指缸筒结构中最薄处的厚度,从材料力学可知,承受内压力的圆筒,其内应力分布规律因壁厚的不同而各异,一般计算时可分为薄壁圆筒,起重运输机械和工程机械的液压缸一般用无缝钢管材料,大多属于薄壁圆筒结构,其壁厚按薄壁圆筒公式计算
σ≥PyD/2[δ]式中
——液压缸壁厚(m);
D——液压缸内径(m);
——试验压力,一般取最大工作压力的(1.25-1.5)倍 ;
——缸筒材料的许用应力。
无缝钢管:
=3.95
1.25=4.94MPa
σ≥4.94×250/(2×110)=5.61mm
故取σ=6mm
3.7.2液压缸的缸体外径
液压缸壁厚算出后,即可求出缸体的外径D1为D1≥D+2δ=100+2×6=112mm
液压缸工作行程长度,根据执行机构实际工作的最大行程为200mm,取标准值,液压缸工作行程选l=250mm。
3.7.3缸盖厚度的确定
一般液压缸多为平底缸盖,其有效厚度t按强度要求可用下面两式进行近似计算。
无孔时
有孔时
式中 t——缸盖有效厚度(m);
——缸盖止口内径(m);
——缸盖孔的直径(m)。
无孔时,取
有孔时,取
3.7.4最小导向长度
对一般的液压缸,最小导向长度H应满足以下要求:
设 计 计 算 过 程
式中 L——液压缸的最大行程;
D——液压缸的内径。
H≥L/20+D/2=220/20+100/2=61mm,取H=80mm
3.7.5.导向滑动面长度
根据液压缸内径D而定
当D<80mm时,取A=(0.6-1.0)D
当D>80mm时,取A=(0.6-1.0)d
A=(0.6~1.0)×70=(42-70)mm,取A=60mm
3.7.6活塞宽度
活塞的宽度B一般取B=(0.6-10)D
B=(0.6~1.0)D=(0.6~1.0)×100=(60-100)mm,取B=80mm。
3.7.7隔套的长度
为保证最小导向长度H,若过分增大A和B都是不适宜的,必要时可在缸盖与活塞之间增加一隔套K来增加H的值。隔套的长度C由需要的最小导向长度H决定,即 C=H-(A+B)/2=80-(60+80)/2=10mm。
3.7.8.缸体内部长度
液压缸缸体内部长度应等于活塞的行程与活塞的宽度之和。缸体外形长度还要考虑到两端端盖的厚度。一般液压缸缸体长度不应大于内径的20-30倍。
缸体内部长度:L=B+l=80+220=300mm。
4 液压系统图的拟定
4.1供油方式的选择
由工况图可知,系统工作压力为低压状态(<25MPa),且在快进和快退时所需流量较大而工进时流量较小,工进时低速运行,进给速度要求平稳,综合考虑宜选用单作用叶片泵作为油源。
4.2速度控制回路
4.2.1增速回路
采用差动连接增速回路,实现快进和快退,回路结构如下:
图4.1 差动连接回路
4.2.2两个调速阀的速度换接回路
该回路主要实现第一次工进→第二次工进的慢速→慢速的换接,回路结构如下:
图4.2 调速阀连接回路
4.2.3行程阀的速度换接回路
该回路主要实现快进→第一次工进和第二次工进→快退的快速——慢速之间的换接,回路结构如下:
图4.3行程阀速度换接回路
4.2.4限压式变量泵和调速阀的容积节流调速回路
该回路主要是保证进入液压缸的流量稳定,使泵的供油流量自动的和液压缸所需的流量相适应,以满足快退/进运动与工进运动时的流量差距调节。
图4.4 容积节流调速回路
本液压系统的换向阀采用三位五通M型中位机能的液控换向阀和三位四通Y型中位机能电磁换向阀,根据上面列出的四种回路,可拟定系统原理图。
图4.5 液压系统动作循环图
表4.2.4 电磁铁和行程阀动作顺序表
注:“+”表示电磁铁得电和行程阀压下,“—”表示电磁铁失电和行程阀原位。
4.3液压系统原理
图4.6 液压系统原理图
动力滑台是组合机床用来实现进给运动的通用部件,根据加工工艺的需要,可在滑台台面上装置动力箱、多轴箱及各种专用切削头等动力部件,以完成钻、扩、铰、镗、铣、刮端面、倒角和攻丝等加工工序以及完成多种复杂进给工作循环。
液压动力滑台的机械结构简单,配上电器后能很容易地实现进给运动的自动循环,同时工进速度也可方便地进行调节,应用比较广泛。
该系统由限压式变量叶片泵、单杆活塞式液压缸及液压元件等组成,在机、电、液的联合控制下能实现工作循环,即:快进→第一次工作进给→第二次工作进给→死挡铁停留→快退→原位停止。
1.快进
进油路:过滤器→泵1→单向阀2→换向阀6左位→行程阀11下位→液压缸左腔。
回油路:液压缸右腔→换向阀6左位→单向阀5→行程阀11下位→液压缸左腔。
2.第一次工作进给
进油路:过滤器→泵1→单向阀2→换向阀6左位→调速阀7→电磁换向阀12右位→液压缸左腔。
回油路:液压缸右腔→换向阀6左位→液控顺序阀4→背压阀3→油箱。
3.第二次工作进给
进油路:过滤器→泵1→单向阀2→换向阀6左位→调速阀7、8→液压缸左腔。
回油路:液压缸右腔→换向阀6左位→液控顺序阀4→背压阀3→油箱。
4.死挡铁停留
当滑台完成第二次工作进给后,碰上死挡铁而停止运动,停留时间由时间继电器来调定。
5.快退
进油路:过滤器→泵1→单向阀2→换向阀6右位→液压缸右腔。
回油路:液压缸左腔→单向阀10→换向阀6右位→油箱。
5 液压元件的选择
5.1确定液压泵的型号和电动机的功率
液压缸在整个工作循环中最大工作压力为3.95MPa,由于该系统有调速阀和管路较复杂,取其压力损失为,所以液压泵的工作压力为
液压泵向系统供油时,若回路中的泄露按10%计算,则泵的总流量应为。
根据以上压力和流量的数值查产品目录,选用V4-1-20S/Y-jL型的限压实式变量叶片泵,其额定压力为6.3MPa;容积效率为总效率为
,所以驱动该泵的电动机的功率由泵的工作压力(6.07MPa)和输出流量(当电动机转速为910r/min)
求出
查电机产品目录,拟选用电机的型号为Y90S-6,功率为750W,额定转速为910r/min。
5.2选择阀类元件及辅助元件
图5.2 液压系统图
1—液压泵 2、5、10—单向阀 3—背压阀 4—顺序阀 6、12—换向阀
7、8—调速阀 9—继电器 11—行程阀 13—滤油器 14—液压缸
现选用规格为800的带支撑脚的矩形油箱油箱,容量为450 L。
油管出油口内径
,取整为8mm
式中 q—流经油管的流量 —油管内的允许流速
6 液压系统的验算
现取进、回油管长l=2m.选用L-HL32液压油,考虑油的最低温度为15℃,查得15℃时该液压油的运动粘度v=150cst=1.5/s,油的密度ρ=920kg/
。
在整个工作循环中,高压下行阶段所占的时间最长,为了简化计算,主要考虑工进时的发热量。一般情况下,高压下行速度大时发热量较大,计算如下: v=1cm/min:
流量q=v(πd2/4)= π×0.072×0.1/4=0.92(L/min)
此时泵的效率为0.1,泵的出口压力为o,92Mpa,则有:
P(输入) = 0.92×0.92/(60×0.1) = 0.15(kW)
P(输出)= Fv = 25980×10/60×10-2×10-3 = 0.0517(kW)
此时的压力损失为:
ΔP = P(输入) - P(输出) = 0.0983(kW)
假定系统的散热状况一般,取K=10×10-3 =kW/(cm2℃),油箱的散热面积A为1.92cm2,则系统的温升为:
ΔT =ΔP/KA = 0.205/(10×10-3 ×1.92) = 20.1(℃)
验算表明系统的温升在许可范围内。
参考文献
[1]左建民.液压与气压传动.机械工业出版社,2007.5
[2]张岚,弓海,刘宇辉.新编使用液压技术手册.人民邮电出版社,2008.5
[3]张利平.《液压气动技术速查手册》.化学工业出版社,2008.7
[4]王守成,段俊勇.《液压原件及选用》.化学工业出版社,2007.4
[5]陆望龙.《典型液压元件结构600例》.化学工业出版社,2009.6
[6]周忆,于今.流体传动与控制[M].北京:科学出版社,2008.
[7]王积伟,章宏甲,黄谊 《液压传动》. 机械工业出版社,第二版