前处理实习报告
一、简介
1、材料:优质碳素结构钢、合金结构钢、轴承钢、代号钢
2、工艺:
处理工序流程:1、热处理 2抛丸 3磷皂化
3、前处理主要设备
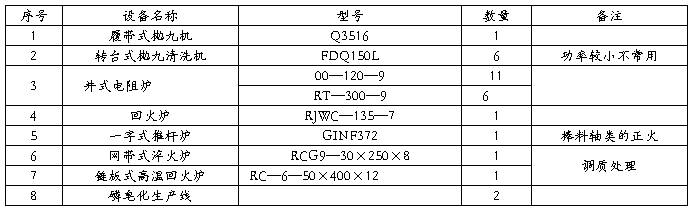
二、主要工艺及其原理
钢的热处理: 是将固态钢材采用适当的方式进行加热、保温和冷却以获得所需组织结构与性能的工艺 。热处理不仅可用于强化钢材,提高机械零件的使用性能,而且还可以用于改善钢材的工艺性能。其共同点是:只改变内部组织结构,不改变表面形状与尺寸。
其目的是改变钢的内部组织结构,以改善钢的性能,通过适当的热处理可以显著提高钢的机械性能,延长机器零件的使用寿命。热处理工艺不但可以强化金属材料、充分挖掘材料性能潜力、降低结构重量、节省和能源,而且能够提高机械产品质量、大幅度延长机器零件的使用寿命。
热处理工艺分类:(根据热处理的目的、要求和工艺方法的不同分类如下)
1、 整体热处理:包括退火、正火、淬火、回火和调质;
2、 表面热处理:包括表面淬火、物理气相沉积(PVD)和化学气相沉积(CVD)等;
3、 化学热处理:渗碳、渗氮、碳氮共渗等。
目前本公司采用的是整体热处理:包括不完全退火、求化退火、去应力退火、正火、回火
调质处理、淬火。
热处理的三阶段:加热、保温、冷却
一、 钢在加热时的转变
加热的目的:使钢奥氏体化
(一)奥氏体(A)的形成
奥氏体晶核的形成以共析钢为例A1点则Wc =0.0218%(体心立方晶格F)Wc =6.69%(复杂斜方渗碳体)当T上升到A c1 后Wc =0.77%(面心立方的A)由此可见转变过程中必须经过C和Fe原子的扩散,必须进行铁原子的晶格改组,即发生相变,A在铁素体和渗碳体的相界面上形成。有两个有利条件① 此相界面上成分介于铁素体和渗碳体之间②原子排列不规则,空位和位错密度高。
珠光体向奥氏体转变过程:a) 形核 b) 长大 c) 剩余渗碳体溶解 d) 奥氏体均匀化
(二)奥氏体晶粒的长大
奥氏体大小用奥氏体晶粒度来表示。分为 00,0,1,2…10等十二个等级,其中常用的1~10级,4级以下为粗晶粒,5-8级为细晶粒,8级以上为超细晶粒。
影响A晶粒粗大因素
1、加热温度越高,保温时间愈长,奥氏体晶粒越粗大。因此,合理选择加热和保温时间。以保证获得细小均匀的奥氏体组织。(930~950℃以下加热,晶粒长大的倾向小,便于热处理)
2、A中C含量上升则晶粒长大的倾向大。
二、钢在冷却时的转变
生产中采用的冷却方式有:等温冷却和连续冷却
(一) 过冷奥氏体的等温转变
A在相变点A1以上是稳定相,冷却至A1 以下就成了不稳定相。
1、 共析碳钢奥氏体等温转变产物的组织和性能
1) 高温珠光体型转变: A1~550℃
(1)珠光体(P)A1~650℃粗层状约0.3μm<25HRC
(2)索氏体(S)650~600℃ 细层状 0.1~0.3μm ,25~35HRC
(3)屈氏体(T)600~550℃ 极细层状约0.1 μm,35~40HRC
2) 中温贝氏体型转变:550℃~Ms
(1)上贝氏体(B上) 550~350 ℃ 羽毛状 40~45HRC脆性大,无使用价值
(2)下贝氏体(B下) 350~Ms黑色针状 45~55HRC韧性好,综合力学性能好
(3)低温马氏体型转变:Ms~M f 当A被迅速过冷至M s以下时,则发生马氏体(M)转变,主要形态是板条状和片状。(当 Wc<0.2%时,呈板条状,当 Wc>1.0%呈针片状,当 Wc =0.2%~1.0%时,呈针片状和板条状的混合物)
钢的退火
1、概念:将钢件加热到适当温度 (AC1以上或以下),保持一定时间,然后缓慢冷却以获得近于平衡状态组织的热处理工艺称为退火。
2、目的:
(1)降低硬度,提高塑性,
(2)细化晶粒,消除组织缺陷
(3)消除内应力
(4)为淬火作好组织准备
3、类型:根据加热温度可分为在临界温度(Ac1或Ac3)以上或以下的退火,前者又称相变重结晶退火,包括完全退火、扩散退火、均匀化退火、不完全退火、球化退火;后者包括再结晶退火及去应力退火。
(1)不完全退火:
1) 概念:将钢件加热到AC1+和AC3(或ACm)之间,经保并缓冷(随炉、埋入砂、石灰中),以获得接近平衡状态的组织的热处理工艺称为不完全退火。
2) 目的:细化晶粒、均匀组织、消除内应力、降低硬度、改善切削加工性能。
3) 工艺:由于不完全退火所采取的温度较完全退火要低,过程时间也较短,因而是比较便宜的一种工艺,如果不必通过完全重结晶去改变铁素体与珠光体的分布及晶粒度(如出现魏氏组织),则总是采用不完全退火来代替完全退火
4) 适用范围:亚共析钢和过共析钢的铸、焊、锻、轧制件等。
(2)球化退火
1) 概念:使钢中碳化物球状化而进行的退火工艺称为球化退火。
2) 工艺:一般球化退火工艺Ac1+(10~20)℃随炉冷至500~600℃空冷。
3) 目的:降低硬度、改善组织、提高塑性和切削加工性能。
4) 适用范围:主要用于共析钢、过共析钢的刃具、量具、模具等。
(3)去应力退火
1) 概念:为去除由于塑性变形加工、焊接等而造成的应力以及铸件内存在的残余应力而进行的退火称为去应力退火。
2) 工艺:将工件缓慢加热到 Ac1以下100~200℃(500~600℃)保温一定时间(1~3h)后随炉缓冷至200℃,再出炉冷却。
钢的一般在 500~600℃;铸铁一般在 500~550℃超过550℃容易造成珠光体的石墨化; 焊接件一般为 500~600℃。
3)适用范围:消除铸、锻、焊件,冷冲压件以及机加工工件中的残余应力,以稳定钢件的尺寸,减少变形,防止开裂。
井式电阻炉的操作步骤为:1、装料2、装炉3、抽真空4、充氮气5、打开冷却水6、开炉及设定工艺7、巡查8、出炉(详见工艺卡片)
120kw和300kw两种型号的井式电阻炉都可用作整体热处理, 120kw井式电阻炉最高加热温度为900℃,300kw的井式电阻炉最高加热温度为950℃。
各个炉子的炉况不一样:如1#与6#炉常出现温度偏高,如进行球化退火,往往会出现球化率较低使组织异常,
另外UF3700星形套由于锻造后变形量较大,不完全退火过程中,虽然温度并不太高,但形变提供了驱动力使边缘组织异常粗大,工艺可能需要调整。
钢的正火
1、概念:将钢件加热到Ac3(或ACcm)以上30~50℃,保温适当时间后;在静止空气中冷却的热处理工艺称为正火。
2、目的:细化晶粒,均匀组织,调整硬度等。
3、组织:共析钢P、亚共析钢F+P、过共析钢Fe3CⅡ+P
4、工艺:正火保温时间和完全退火相同,应以工件透烧,即心部达到要求的加热温度为准,还应考虑钢材、原始组织、装炉量和加热设备等因素。正火冷却方式最常用的是将钢件从加热炉中取出在空气中自然冷却。对于大件也可采用吹风、喷雾和调节钢件堆放距离等方法控制钢件的冷却速度,达到要求的组织和性能。
5、应用范围:
1)改善钢的切削加工性能。碳的含量低于0.25%的碳素钢和低合金钢,退火后硬度较低,切削加工时易于“粘刀”,通过正火处理,可以减少自由铁素体,获得细片状P,使硬度提高,改善钢的切削加工性,提高刀具的寿命和工件的表面光洁程度。
2)消除热加工缺陷。中碳结构钢铸、锻、轧件以及焊接件在加热加工后易出现粗大晶粒等过热缺陷和带状组织。通过正火处理可以消除这些缺陷组织,达到细化晶粒、均匀组织、消除内应力的目的。
3)消除过共析钢的网状碳化物,便于球化退火。过共析钢在淬火之前要进行球化退火,以便于机械加工并为淬火作好组织准备。但当过共析钢中存在严重网状碳化物时,将达不到良好的球化效果。通过正火处理可以消除网状碳化物。
4)提高普通结构零件的机械性能。一些受力不大、性能要求不高的碳钢和合金钢零件采用正火处理,达到一定的综合力学性能,可以代替调质处理,作为零件的最终热处理。
设备参数:等温正火的周期时间为26min±2min,强冷时间为6min,强冷速度为50Hz,缓冷速度为30HZ,缓冷时间为1.5min,每只料框装48-50件,氮气流量:加热室5-6立方米/小时,等温室1-2立方米/小时,甲醇及液化气气阀均不容许打开,速冷室和缓冷室的氮气流量为18-22立方米/小时。
甲醇的作用是燃烧以消耗氧气,防止工件脱碳,液化气的作用是为了使甲醇充分燃烧。
棒料正火后往往出现脱碳层过深,原因:1、原材料出厂时本身脱碳层就较深2、可能是正火炉本身问题。
钢的淬火
1、定义:将钢件加热到 Ac3 或Ac1以上某一温度,保持一定时间。然后以适当速度冷却获得 M或B组织的热处理工艺。
2、 目的:显著提高钢的强度和硬度。
3、淬火温度的选择
1)碳钢的淬火加热温度由Fe-Fe3C相图来确定,其目的是为了 ①淬火后得到全部细小的M;②淬火后希望硬度高。
① 亚共析钢Ac3 +(30~50)℃,可获得细小的均匀的M,如温度过高则有晶粒粗化现象,淬火后获得粗大的M,使钢的脆性增大;如温度过低则淬火后M+F,有铁素体出现,淬火硬度不足。
② 共析钢与过共析钢Ac1 +(30~50)℃,由于有高硬度的渗碳体和M存在,能保证得到高的硬度和耐磨性。如果加热温度超过ACcm 将会使碳化物全部溶入A中,使A中的含碳量增加,淬火后残余奥氏体量增多,降低钢的硬度和耐磨性;淬火温度过高,奥氏体晶粒粗化、含碳量又高,淬火后易得到含有显微裂纹的粗片状马氏体,使钢的脆性增大。
2)合金钢
①对含有阻碍奥氏体晶粒长大的强碳化物形成元素(如Ti、Nb等),淬火温度可以高一些,以加速其碳化物的溶解,获得较好的淬火效果
②对含有促进奥氏体晶粒长大的元素(如Mn等),淬火加热温度应低一些,以防止晶粒粗大。
理想冷却速度: 650℃以上应当慢冷,以尽量降低淬火热应力。650~400℃之间应当快速冷却,以通过过冷奥氏体最不稳定的区域,避免发生珠光体或贝氏体转变。 400以下至Ms点附近应当缓以尽量减小马氏体转变时产生的组织应力。具有这种冷却特性的冷却介质可以保证在获得M组织条件下减少淬火应力、避免工件产生变形或开裂。
4、淬火介质
淬火介质:钢从奥氏体状态冷至 Ms点以下所用的冷却介质。常用的有三种:水、油、有机水溶液
水:650~400℃范围内冷却速度较小,不超过200℃/s ,但在需要慢冷的马氏体转变温度区,其冷却速度又太大,在340℃最大冷却速度高达775℃/s ,很容易引起工件变形和开裂。此外,水温对水的冷却特性影响很大,水温升高,高温区的冷却速度显著下降,而低温区的冷却速度仍然很高。因此淬火时水温不应超过 30℃,加强水循环和工件的搅动可以加速工件在高温区的冷却速度。 水虽不是理想淬火介质,但却适用于尺寸不大、形状简单的碳钢工件淬火。
油:在650~550℃内冷却较慢,不适用于碳钢,300~200℃范围内冷很慢,有利于淬火工件的组织应力,减少工件变形和开裂倾向。与水相反,提高油温可以降低粘度,增加流动性,故可以提高高温区的冷却能力。但是油温过高易着火,一般应控制在60~80℃。适用于对过冷奥氏体比较稳定的合金钢。
水与油作为淬火介质各有优缺点,但均不是属于理想的冷却介质。水的冷却能力很大,但冷却特性不好;油冷却特性较好,但其冷却能力又低。由于水是价廉、容易获得、性能稳定的淬火介质,因此目前世界各国都在发展有机水溶液作为淬火介质。美国应用浓度为 15%聚乙烯醇、0.4%抗粘附剂、0.1%防泡剂的淬火介质,以及国内使用比较广泛的新型淬火介质有过饱和硝盐水溶液等。它们的共同特点是冷却能力介于水、油之间,接近于理想淬火介质。主要用于贝氏体等温淬火,马氏体分级淬火,常用于处理形状复杂、尺寸较小和变形要求严格的工件。
5、淬火方法(常用的淬火方法:单介质淬火、双 介质淬火、马氏体分级淬火、贝氏体等温淬火)
1、单介质淬火
优点:操作简单、易实现机械化、应用广泛。 缺点:水中淬火变形与开裂倾向大;油中淬火冷却速度小,淬透直径小,大件无法淬透。
2、 双介质淬火
优点:减少热应力与相变应力,从而减少变形、防止开裂。 缺点:工艺不易掌握,要求操作熟练。 适用于中等形状复杂的高碳钢和尺寸较大的合金钢工件。
3、局部淬火
为了避免工件其它部分产生变形或开裂,即可用局部淬火 。
4、马氏体分级淬火
优点:使过冷奥氏体在缓冷条件下转变成马氏体,从而减少变形。
缺点:只适用于尺寸较小的零件,否则淬火介质冷却能力不足,温度也难于控制。
5、马氏体等温度淬火优点:下贝氏体的硬度略低于马氏体,但综合力学性能较好,应用广泛。
6、钢的淬透性与淬硬性
(一)淬透性:决定钢材淬硬深度和硬度分布的特性,即应该是全淬成马氏体的深度。
1. 影响淬透性因素
(1) 钢的化学成分。除Co以外的合金元素溶于奥氏体后,均能增加过冷奥氏体稳定性,降低马氏体临界冷却速度,从而提高钢的淬透性。
(2) 奥氏体化条件。提高奥氏体的温度,延长保温时间,使奥氏体晶粒粗大,成分均匀,残余渗碳体和碳化物的溶解彻底,使过冷奥氏体起稳定,使 C曲线越向右移,马氏体临界冷却速度就越小,则钢的淬透性越好。
2. 淬透性表示方法。常用临界直径大小来定理的比较不同钢种的淬透性大小。临界直径是指钢材在某种介质中淬冷后,心部得到全部马氏体(或 50%马氏体)组织的最大直径。用Dc表示。在同一冷却介质中,钢的临界直径越大,其淬透性越好;但同一钢种在冷却能力大的介质中,比冷却能力小的介质中所得的临界直径要大些。
3. 淬透性的实用意义:
1)淬 透——性能均匀一致
2)未淬透——韧性降低
(二)钢的淬硬性:钢在理想条件下进行淬火硬化所能达到的最高硬度的能力。值得注意的:钢的淬透性与淬硬性是两个不同的概念。淬透性好的钢其淬硬性不一定高,而淬火后硬度低的钢也可能是具有高的淬透性。
7、钢的淬火缺陷及其防止措施
1. 淬火工件的过热和过烧
过热:工件在淬火加热时,由于温度过高或时间过长造成奥氏体晶粒粗大的缺陷。
由于过热不仅在淬火后得到粗大马氏体组织,而且易于引起淬火裂纹,因此,淬火过热的工件强度和韧性降低,易于产生脆性断裂。轻微的过热可用延长回火时间补救。严重的过热则需进行一次细化晶粒退火,然后再重新淬火。
过烧:淬火加热温度太高,使奥氏体晶界局部熔化或者发生氧化的现象。
过烧是严重的加热缺陷,工件一旦过烧无法补救,只能报废。过烧的原因主要是设备失灵或操作不当造成的。高速钢淬火温度高容易过烧,火焰炉加热局部温度过高也容易造成过烧。
2. 淬火加热时的氧化和脱碳
淬火加热时,钢件与周围加热介质相互作用往往会产生氧化和脱碳等缺陷。氧化使工件尺寸减小,表面光洁度降低,并严重影响淬火冷却速度,进而使淬火工件出现软点或硬度不足等新的缺陷。工件表面脱碳会降低淬火后钢的表面硬度、耐磨性,并显著降低其疲劳强度。因此,淬火加热时,在获得均匀化奥氏体时,必须注意防止氧化和脱碳现象。 在空气介质炉中加热时,防止氧化和脱碳最简单的方法是在炉子升温加热时向炉内加入无水分的木炭,以改变炉内气氛,减少氧化和脱碳。此外,采用盐炉加热、用铸铁屑覆盖工件表面,或是在工件表面热涂硼酸等方法都可有效地防止或减少工件的氧化和脱碳。
3. 淬火时形成的内应力
有两种情况:①工作在加热或冷却时,引起的热应力。②由于热处理过程中各部位冷速的差异引起的相变应力。当两力相复合超过钢的屈服强度时,工件就变形;当复合力超过钢的抗拉强度时,工件就开裂。
解决办法:①工件在加热炉中安放时,要尽量保证受热均匀,防止加热时变形;
②对形状复杂或导热性差的高合金钢,应缓慢加热或多次预热,以减少加热中产生的热应力;
③选择合适的淬火冷却介质和淬火方法,以减少冷却中热应力和相变应力。但淬火不是最终热处理,为了消除淬火钢的残余内应力,得到不同强度、硬度和韧性配合的性能,需要配以不同温度的回火。钢淬火后再经回火,是为了使工件获得良好的使用性能,以充发挥材料的潜力。所以淬火和回火是不可分割的、紧密衔接在一起的两种热处理工艺。
钢的回火
1、定义:钢件淬火后,再加热到A1以下某一温度,保持一定时间,然后冷却到室温的热处理工艺称为回火。
2、目的: 1) 稳定组织,消除淬火应力 2) 调整硬度、强度、塑性、韧性
3、 淬火钢在回火时组织的转变 1)马氏体的分解(> 100℃) 2)残余奥氏体的转变(200~300℃) 3)碳化物的转变(250~450℃) 4)渗碳体的聚集长大和铁素体再结晶(> 450℃)
4、钢在回火时性能变化
1)回火方法:
(1)低温回火(150~250℃),组织是回火马氏体,和淬火马氏体相比,回火马氏体既保持了钢的高硬度、高强度和良好耐磨性,又适当提高了韧性。硬度为58~64HRC,主要用于高碳钢,合金工具钢制造的刃具、量具、模具及滚动轴承,渗碳、碳氮共渗和表面淬火件等。
(2)中温回火(350~500℃),组织为回火屈氏体,对于一般碳钢和低合金钢,中温回火相当于回火的第三阶段,此时碳化物开始聚集,基体开始回复,淬火应力基本消除。硬度为 35~50HRC,具有高的弹性极限,有良好的塑性和韧性,主用于弹性件及模具处理。
(3)高温回火(500~650℃),组织为回火索氏体,硬度为220~330HBS。
淬火和随后的高温回火称为调质处理,经调质处理后,钢具有优良的综合机械性能。因此,高温回火主要适用于中碳结构钢或低合金结构钢,用来制作汽车、拖拉机、机床等承受较大载荷的结构零件,如曲轴、连杆、螺栓、机床主轴及齿 轮等重要的机器零件。钢经正火后和调质后的硬度很相近,但重要的结构件一般都要进行调质而不采用正火。在抗拉强度大致相同情况下,经调质后的屈服点、塑性和韧性指标均显著超过正火,尤其塑性和韧性更为突出。
2)回火时间:一般为1~3h
3)回火冷却:一般空冷。一些重要的机器和工模具,为了防止重新产生内
应力和变形、开裂,通常都采用缓慢的冷却方式。对于有高温回火脆性的钢件,回火后应进行油冷或水冷,以抑制回火脆性。
调质后工件的组织应为为回火索氏体,甲醇的作用是是燃烧以消耗氧气,防止工件脱碳,由于采用油淬,所以工件不会出现变形超差。
技术数据:淬火炉最高加热温度950℃,产量100Kg/小时,淬火介质的浓度控制在0.03-0.05之间,最短加热时间为22min,最长加热时间为90min。
抛丸
1、 定义:以压缩空气作为动力,将丸砂或钢丸喷射到工件表面,是工件表面的氧化皮或污物脱落下来,这种清除氧化物或污物的方法称为喷丸处理。
2、 目的:清除氧化物或污物以使工件表面光洁发亮,同时能使工件表面产生残留压应力,提高工件的疲劳强度。
3、 适用范围:硬度在40HRC以下的工件不能进行喷丸。硬度在40—55HRC之间的工件,喷丸不能太久。另外,工具及形状复杂的工件也不易进行喷丸。
4、 丸砂的选用:对于棒料,应选用钢丝切刃φ0.8—1.0进行粗抛,粗抛还可选用70%的尖角砂(QG,H,L,P—4)+30%的钢丸(QB—10~12)。对于形状较复杂的工件应选用70%的尖角砂(QG,H,L,P—4)+30%的钢丸(QB—6)。
5、 产品检验:无锈迹、氧化皮。
磷皂化
1、目的:为了降低坯料与模具之间的摩擦,减少模具磨损,延长模具使用寿命,改善和提高挤压零件的表面质量,是坯料表面润滑而用磷皂化处理方法。
2、磷皂化的工艺流程:1、脱脂2、水洗3、酸洗4、水洗5、磷化6、烫洗7、皂化8、烫洗
3、产品检验:
磷化膜外观检测:表面是否为浅灰色或银灰色,结晶是否均匀,致密,牢固,完整,是否有沉淀物附于表面和未磷化的空白区。
皂化膜外观检测:用手指甲扣挖后有粉状剔层,摸上去光滑,表面无金属光泽(拐角处除外)。