机械制造工艺学与机床夹具设计
题目:设计扁叉零件机械加工工艺规程及某一工序的夹具
专业班级:08机制(2)班
姓 名:俞烽炜
学 号:08530058
指导教师:尹成龙、杨义
时 间:11.21-12.04
引言
《机械制造工艺学与机床夹具设计》课程是机械类专业的一门主要专业课。它授予学生制订经济合理、切实可行的机械加工和装配工艺,确定各工序的工装与设备等方面的综合知识,以及基本的工艺理论和国内外先进的新工艺、新技术方面的知识;培养学生分析生产实际加工过程中产生误差的原因和存在的具体工艺问题,并能初步提出改进产品质量、提高生产率与降低成本的工艺途径和方法的能力。为提高学生解决实际问题的能力,本课程学完后,特安排此课程设计。
本课程设计是在学完了机械制造工艺学及夹具设计之后进行的下一个教学环节。它一方面要求学生在设计中能初步学会综合应用过去所学的全部课程,另外也为搞好毕业设计做一次综合训练。学生应当通过机械制造工艺学及夹具设计课程设计在下述各方面得到锻炼:
能熟练运用机械制造工艺学及夹具设计课程设计中的基本理论,正确地解决一个零件在加工中的定位,夹紧以及工艺路线合理安排等问题,保证零件的加工质量。
提高结构设计能力。学生通过设计夹具的训练,应当掌握如何根据被加工零件的加工要求,设计出高效、省力、既经济合理,又能保证加工质量的夹具来。
学会使用手册及图表资料。掌握与本设计有关的各种资料的名称出处,能够做到熟练应用。
目录
引言…………………………………………………………………………………2
零件图的分析………………………………………………………………………4
1.1零件的结构要求
1.2零件的工艺分析
零件的毛坯设计……………………………………………………………………4
2.1确定毛坯的制造形式
2.2确定毛坯的机械加工余量和公差
2.3毛坯图
工艺规程设计………………………………………………………………………5
3.1基面的选择
3.2制订加工工艺路线
工序设计……………………………………………………………………………6
4.1机械加工余量、工序尺寸及毛坯尺寸的确定
4.2确定切削用量和基本工时
4.3扁叉零件图
夹具设计……………………………………………………………………………8
5.1问题的提出
5.2夹具设计
5.3定位误差分析
5.4夹具设计及操作的简要说明
总结…………………………………………………………………………………9
参考文献……………………………………………………………………………10
零件图的分析
1.1零件的结构要求
扁叉结构要合理,要求扁叉结构不但要应该达到设计要求,而且要有好的机械加工工艺性,也就是要有加工的可能性,要便于加工,要能够保证加工质量,同时使劳动量最小。而设计和工艺是密切相关的又是相辅相成的。设计者要考虑加工工艺的问题。
扁叉是一个很重要的零件,因为其零件尺寸比较小,结构形状复杂程度一般,但其加工两同轴内孔的精度要求较高,此外还有上端面以及凸块两侧台阶面要求加工精度很高,对圆柱的四个端面也有一定的精度要求。
该零件的两小孔有同轴度要求,且凸块两侧面相对孔轴线有对称度要求,凸块两侧台阶面对两孔轴线也各自有平行度要求。
因此,该零件的尺寸精度、几何形状精度和相互位置精度,以及各表面的表面质量均影响机器或部件的装配质量,进而影响其性能与工作寿命,因此对他们的加工是非常关键的。
1.2零件的工艺分析
⑴以φ10H7为轴心线为基准,两圆柱同轴度有较高的要求。
⑵以两孔轴线为基准,要求凸块两侧台阶面有较高的对称度和平行度。
⑶凸块两侧台阶面要求粗糙度为3.2,上端面粗糙度为6.3。
⑷短圆柱的四个端面:.有一定的位置要求和粗糙度要求。
⑸两孔的粗糙度有很高的要求。
由上面分析可知,加工时应先加工一组表面(铣削上端面和两侧台阶面),再以这组加工后表面为基准加工另外两组(分别是铣圆柱端面和钻铰两同轴小孔)。
零件的毛坯设计
2.1确定毛坯的制造形式
零件材料为HT35-32零件在机床运行过程中所受冲击不大,零件结构又比较简单,故选择金属型浇注铸件毛坯。
2.2确定毛坯的机械加工余量和公差
参考《机械制造技术基础课程设计》(以下称指导书)查表2-11,《公差与机械加工余量》(GB/T6414-1999),查表2-11,轮廓尺寸尺寸不超过160mm,得加工余量5-7mm,故取6mm。
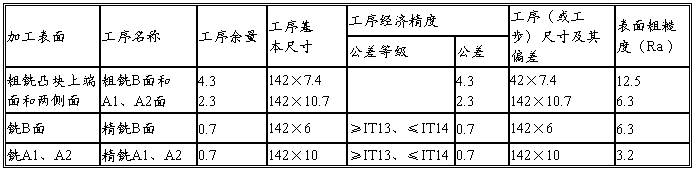
2.3设计及绘制毛坯图
工艺规程设计
3.1基面的选择
本零件是有精度较高要求的孔的叉架零件,平面和孔是设计的基准,也是装配和测量的基准,在加工时,应尽量以平面为基准。
先以圆柱面为粗基准,铣出上端面和凸块侧面及其两有平行度要求的平面,再以加工的平面为精基准,加工出两短圆柱的四个端面,同样,也是以该已加工表面为基准钻出两同轴的Φ10H7孔;加工前后四个圆柱端面时,先以凸块表面为基准,在铣床上利用组合铣刀一次性铣出端面。
3.2制订加工工艺路线。
工艺路线方案:
I. 粗铣凸块两侧台阶面A1、A2和凸块上端面B面
II. 粗铣C圆柱两端面C1、C2
III. 粗铣D圆柱两端面D1、D2
IV. 钻孔φ10
V. 精铣C圆柱两端面C1、C2
VI. 精铣D圆柱两端面D1、D2
VII.精铣B面
VIII. 精铣A1、A2面
IX. 粗铰φ10,铰孔精度为0.07mm
X. 精铰φ10,铰孔精度为0.07mm
XI. 检查入库
工序设计
4.1机械加工余量、工序尺寸及毛坯尺寸的确定。
“扁叉”材料为HT15-32,生产类型中批量,金属型铸造毛坯。
据以上原始资料及加工路线,确定工序一中粗铣圆柱C 的C1、C2两个端面d的机械加工余量、工序尺寸及毛坯尺寸如下:
查《机械制造基础课程设计》表2-11,工序尺寸加工余量为5-7mm,故取6mm。
查《工艺手册》表2.2~2.5,工序尺寸加工余量
铣C1、C2台阶面
φ200mm的高速钢镶齿套式面铣刀
粗铣 2.3mm
精铣 0.7mm
4.2确定切削用量和基本工时。
工序Ⅷ:粗铣圆柱C 的C1、C2两个端面
本工序是精铣侧凸台面,已知加工材料为HT15-32,σb=195Mpa,铸件无外皮,机床为X6142型卧式铣床,所选刀具为高速钢镶齿套式面铣刀,其参数:直径d=200mm,齿数Z=20。粗铣时,为了提高切削效率,一般选择铣削背吃刀量等于加工余量,一个工作行程铣完。
(1)确定每齿进给量。根据《机械制造基础课程设计》表5-4知X6142型卧式铣床的主电动机功率为14.175KW。查5-27知工艺系统刚性中等、镶齿端铣刀加工铸铁时,每齿进给量
=0.3—0.5mm/z。由于本工序背吃刀量
=0—1mm和切削宽度
=7.4mm,故选择每齿进给量
=0.3mm/z。
(2)选择铣刀磨钝标准和耐用度。跟据《机械制造工艺学课程设计指导书》,查表5-28,用高速钢镶齿铣刀粗加工铸铁时,选择铣刀后刀面磨损极限值为2mm,查《机械制造基础课程设计》表5-72续知,铣刀合理耐用度时间T=240min。
(3)确定切削速度和工作台每分钟进给量
。由《机械制造基础课程设计》表5-72续查得,高速钢切削铸铁的切削速度为V=20m/min,则所需铣床主轴转速范围是:n=1000V/∏d=31.85r/min。
选取n=35r/min,则实际铣削速度为=∏dn/1000=21.98m/min
铣刀每转工作台移动速度,即每转进给量 f=z=0.3×20=6mm
工作台每分钟进给量为 =
z n=0.3×20×35=210mm/min
根据表5-13中工作台标准纵向进给量,选取f=150mm/min,则实际每齿进给量为 =f/zn=150/(20×35)=0.214mm/z
(4)校验机床功率。由《机械制造工艺学课程设计指导书》查表5-31和5-32知,由铣削力Fz和铣削功率Pm得,故选X6142合适。最后确定的切削用量为:=0.7mm
==6mm
=0.214mm/z
=150m/min
=22m/min
上述中:—铣削速度(m/min)
、
—铣刀直径(mm)
—铣刀转速(r/min)
—铣刀每分钟工作台移动速度,即每转进给量(mm/r)
—铣刀每齿工作台移动速度,即每齿进给量(mm/z)
—进给速度,即工作台每分钟移动速度(mm/min)
—铣刀齿数
—铣削宽度
—铣削背吃刀量
2.基本时间tm
tm=(Lw+L1+L2)/
LW ——工件铣削部分长度
L1——切入行程长度 当主偏角为90时,L1=0.5( d—)+(1—3)
L2——切出行程长度 L2=3—5mm
已知n=35r/min,Lw=142mm。计算得L1+L2=8mm。所以,基本时间为: tm=(142+8)/150=1mim
故,A1,A2两面的基本时间为:t=2×tm=2min
4.3扁叉零件图如下:
夹具设计
设计的是第八道工序——精铣A1、A2面的铣床夹具。本夹具将用于x6142卧式铣床,道具为直径d=200mm的高速钢镶齿套式面铣刀。
5.2夹具设计
1. 第八道工序的定位基准的选择
由零件图可知,台阶面A1、A2对φ10H7的平行度和对称度,其设计基准为零件上表面,定位时零件上表面定位。
2. 切削力及夹紧力的计算
,
,
,
,
,
,
,
当铣削时,
在计算切削力时,必须把安全系数考虑在内。安全系数。
其中:为基本安全系数1.5;
为加工性质系数1.1;
为刀具钝化系数1.1;
为断续切削系数1.1。
选用M8mm。当螺纹直径为8mm,手柄长度为140mm,作用力为70N时,其夹紧力为。此时
已大于所需的3085N的夹紧力,故本夹具可安全工作。
5.3定位误差分析
本工序采用上表面为基准定位,使加工基准和设计基准统一,能很好的保证定位的精度。
5.4夹具设计及操作的简要说明
夹具的夹紧力不大,故使用手动夹紧。为了提高生产力,可使用有快换垫圈。
总结
通过为期两个星期的课程设计使我加深了对机械制造工艺学这一门课程实用性的理解,同时也使我回顾了我以往所学的知识。因为这次课程设计是我们在毕业设计前一次重要的实践设计,涉及到的知识综合性很强,这就要求我们对所学的基础课、技术基础课和专业课有较熟练的掌握。我们在做课程设计时,需要学会将书本上的理论知识和实践相结合,但这对我们来说有不少困难,因为我们根本没有什么实际经验。所以这次课程设计我们主要通过反复的查阅资,、反复的思考,和设计同一种零件的同学相互间反复讨论来完成的。经过繁忙困难的过程后,我们对知识的印象更加深刻了。此外,整个过程中同学互帮互助,我们在快乐中共同学习,学习中共同进步, 同学之间的关系也更加密切了。
在此次收获课程设计成功经验的同时,再次感谢尹老师、杨老师的辛勤指导,以及同学们的帮助。
参考文献
[1] 郭艳玲.机械制造工艺学.北京:北京大学出版社,2008.01
[2] 尹成龙.机械制造工艺学与机床夹具设计.安徽:安徽农业大学工学院,2009.10.
[3]机床夹具设计手册.上海:上海科学技术出版社,1991.12.
[4] 徐圣群.简明机械加工工艺手册.上海:上海科学技术出版社,1994.7
[5]李益明.机械制造工艺设计简明手册.机械工业出版社, 1994.7
[6] 卢秉恒.机械制造技术基础.北京:机械工业出版社,2007.12.
[7] 孟少农.机械加工工艺手册[M].北京:机械工业出版社,1991.
[8] 柯建宏,宾鸿赞.机械制造技术基础课程设计.华中科技大学出版社,2006.
[9]郑修本.机械制造工艺学[M].北京:机械工业出版社,1999.
第二篇:变速器换挡叉加工工艺及夹具设计课程设计说明书
机械制造技术
课程设计说明书
课程名称: 机械制造技术
题目名称: 变速器换挡叉加工工艺及夹具设计
班 级:
姓 名:
学 号:
指导教师:
评定成绩:
指导老师签名:
20##年12月10日
目录
第一章:零件分析—————————————————————1
1.1、零件的作用———————————————————1
1.2.零件的工艺分析——————————————————1
1.3、尺寸和粗糙度的要求————————————————2
1.4、位置公差要求——————————————————
第二章:毛坯的设计——————————————————
2.1选择毛坯—————————————————————
2.2确定机加工余量、毛坯尺寸和公差——————————
2.3 确定机械加工加工余量———————————————
2.4 确定毛坯————————————————————
2.5 确定毛坯尺寸公差————————————————
2.6设计毛坯图————————————————————
第三章:选择加工方法,拟定工艺路线———————————
3.1、基面的选择————————————————————
3.2、粗基准的选择———————————————————
3.3、精基准的选择———————————————————
3.4、制定机械加工工艺路线———————————————
第四章:加工设备及道具、夹具、量具的选择———————
第五章:确定切削用量—————————————————
第六章:基本时间的确定————————————————
第七章:夹具设计———————————————————
第八章:总结—————————————————————
第一章:零件分析
1.1、零件的作用
题目所给定的零件是变速器换档叉,如下图所示。它位于传动轴的端部,主要作用是换挡。使变速器获得换档的动力。
1.2.零件的工艺分析
由零件图可知,该零件的材料为35#钢,锻造成型,由零件的尺寸公差选择模锻加工成型,保证不加工表面达到要求的尺寸公差。
该零件需要加工的表面可大致分为以下四类:
(1)Φ15.81的孔。
(2)以Φ15.81孔的轴心线为基准的两平面。
(3)以15mm槽为基准的两插口端面。
(4)以Φ15.81孔的轴心线为基准的两叉口侧面。
(5)15mm槽中心的两个侧面及槽外的两端面。
(6)拨槽的最前端面
(7)以15mm槽为基准的M10*1-7H的螺纹孔。
其中Φ15.81的孔和15mm的槽以及叉口的上下端面和叉口的中间两侧面为主要的配合面,加工的精度及粗糙度的要求较高,应作为加工的重点
1.3,尺寸和粗糙度的要求
Φ15.81的孔的上偏差为+0.043,下偏差为+0.016,配合公差为F8,属于间隙配合,孔的内表面的粗糙度为3.2,要求较高,鉴于孔径为15.81,可先采用Φ14的麻花钻钻孔,在用Φ10的立铣刀进行扩孔,最后用无心砂轮进行精加工。
Φ15.81的孔的上下两平面距离孔中心线的尺寸分别为11mm和12.7mm,上表面的粗糙度为6.3,下表面的粗糙度为12.5,直接采用立铣刀铣削加工即可达到要求。
以Φ15.81的孔的轴心线为基准的尺寸为9.65mm的两侧面的表面粗糙度为6.3,可直接用端面立铣刀进行加工保证尺寸要求。
以15mm拨槽为基准的叉口的上下端面的尺寸分别为33.5mm和39.4mm其表面粗糙度为6.3,可直接用端面立铣刀进行加工保证尺寸要求。
以Φ15.81的孔的轴心线为基准的叉口两侧面尺寸为53mm,表面粗糙度为6.3,可直接用端面立铣刀进行加工保证尺寸要求。
拨槽的最前端面,以Φ15.81孔的下端面为基准,其尺寸为56,其表面粗糙度为12.5
以15mm拨槽为基准的M10*1-7H的螺纹孔,先采用Φ8.5的麻花钻钻孔,再采用Φ10的丝锥攻丝完成。
1.4、位置公差要求
由零件图可知,该零件主要要求保证Φ15.81的孔和叉口的上下端面之间的垂直度要求,以Φ15.81的孔作为加工叉口上下端面的定位基准便可以保证其垂直度的要求。
第二章:毛坯的设计
2.1选择毛坯
该零件的材料为35#钢,考虑到零件在工作时要求有较高的强度和抗扭性,非加工面的尺寸精度要求较高,以及批量为大批量生产,所以采用模锻毛坯成型。
2.2确定机加工余量、毛坯尺寸和公差
(1)确定最大轮廓尺寸
根据零件图计算零件的最大轮廓尺寸为:长147.4mm,宽76mm,高56mm
(2)选择锻件公差等级
查手册模锻成型,零件材料按中碳钢,得锻件公差等级为8~12级取为10级。
(3)求铸件尺寸公差
公差带相对于基本尺寸对称分布。
(4)求机械加工余量等级
查手册得按模锻成型的方法,锻件材料为35#钢的机械加工余量等级E-G级选择F级。
2.3 确定机械加工加工余量
根据锻件质量、零件表面粗糙度、形状复杂程度,取铸件加工表面的单边余量为4㎜,孔的加工余量按相关表查找选取。
2.4 确定毛坯
上面查得的加工余量适用于机械加工表面粗糙度Ra≧1.6@.Ra<1.6@的表面,余量要适当加大。
分析本零件,加工表面Ra≧1.6@,因此这些表面的毛坯尺寸只需将零件的尺寸加上所查的余量即可。(由于有的表面只需粗加工,这时可取所查数据的小值)
生产类型为大批量生产,可采用模锻毛坯。
2.5 确定毛坯尺寸公差
毛坯尺寸公差根据锻件质量、材质系数、形状复杂系数查手册得,本零件毛坯尺寸允许偏差为0.1-0.2mm,表面粗糙度 为Ra12.5-25
2.6设计毛坯图
用查表法确定锻件各表面的加工总余量:
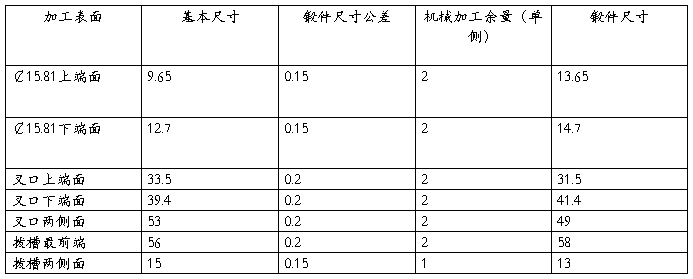
下图为零件毛坯图:
第三章 选择加工方法,拟定工艺路线
3.1、基面的选择
基面选择是工艺规程设计中的重要设计之一,基面的选择正确与合理,可以使加工质量得到保证,生产率得到提高。否则,加工工艺过程会问题百出,更有甚者,还会造成零件大批报废,使生产无法进行。
3.2、粗基准的选择
粗基准的选择影响影响各加工面的余量分配及不需加工表面与加工表面之间的位置精度。为了保证叉口上下平面与Φ15.81孔的垂直度要求以及叉口上下面的加工余量分配均匀,所以选择叉口的上端面作为第一道工序的定位基准。
3.3、精基准的选择
以第一道工序中的已加工面作为下到工序的定位平面,以Φ15.81孔的中心轴线为定位基准,确保设计基准与工艺基准的重合,以减少加工误差。
3.4、制定机械加工工艺路线
工艺路线一:
工序一:
(1)粗铣叉口下端面加工经济精度IT12,粗糙度12.5(组合夹具)
(2)精铣叉口下端面,加工经济精度IT10,粗糙度6.3
工序二:
(1)用Φ14的麻花钻加工孔,加工经济精度IT13,粗糙度12.5(专用夹具)
(2)用Φ10的立铣刀扩孔到直径为15.5mm,加工精度为IT10,粗糙度为6.3
工序三:
(1)粗铣叉口上端面,加工经济精度IT12,粗糙度12.5(组合夹具)
(2)粗铣叉口中间的两侧面,加工经济精度IT12,粗糙度12.5
(3) 粗铣拨槽下端面,加工经济精度IT12,粗糙度12.5
(4)精铣叉口上端面,加工经济精度IT10,粗糙度6.3
(5)精铣叉口中间的两侧面,加工经济精度IT10,粗糙度6.3
工序四:
(1)粗铣拨槽的一个侧面,加工经济精度IT12,粗糙度12.5(专用夹具)
(2)精铣拨槽侧面,加工精度IT10,粗糙度6.3
工序五:
(1)粗铣拨槽的另一个侧面,加工经济精度IT12,粗糙度12.5(专用夹具)
(2)粗铣拨槽的中间两个小侧面,加工经济精度IT12,粗糙度12.5
(3)粗铣拨槽的最前端面,加工经济精度IT12,粗糙度12.5
(4)精铣拨槽侧面,加工精度IT10,粗糙度6.3
(5)精铣拨槽的中间的两个小侧面,加工精度IT10,粗糙度6.3
(6)加工0.8*45°的倒角
工序六:
(1),用Φ8.5的麻花钻钻孔
(2),用Φ10的丝锥攻丝,加工M10的螺纹孔。
工序七:
(1),用无心磨床精加工Φ15.81的孔,粗糙度3.2
(2),加工0.4*45°的倒角
工序八:
(1),钳工,去毛刺
工序九:
(1),检验
工艺路线二:
工序一:
(1)用Φ14的麻花钻加工孔,加工经济精度IT13,粗糙度12.5(专用夹具)
(2)用Φ10的立铣刀扩孔到直径为15.5mm,加工精度为IT10,粗糙度为6.3
工序二:
(1)粗铣叉口下端面加工经济精度IT12,粗糙度12.5(组合夹具)
(2)精铣叉口下端面,加工经济精度IT10,粗糙度6.3
工序三:
(1)粗铣叉口上端面,加工经济精度IT12,粗糙度12.5(组合夹具)
(2)粗铣叉口中间的两侧面,加工经济精度IT12,粗糙度12.5
(3) 粗铣拨槽下端面,加工经济精度IT12,粗糙度12.5
(4)精铣叉口上端面,加工经济精度IT10,粗糙度6.3
(5)精铣叉口中间的两侧面,加工经济精度IT10,粗糙度6.3
(6)加工0.8*45°的倒角
工序四:
(1)粗铣拨槽的一个侧面,加工经济精度IT12,粗糙度12.5(专用夹具)
(2)精铣拨槽侧面,加工精度IT10,粗糙度6.3
工序五:
(1)粗铣拨槽的另一个侧面,加工经济精度IT12,粗糙度12.5(专用夹具)
(2)粗铣拨槽的中间两个小侧面,加工经济精度IT12,粗糙度12.5
(3)粗铣拨槽的最前端面,加工经济精度IT12,粗糙度12.5
(4)精铣拨槽侧面,加工精度IT10,粗糙度6.3
(5)精铣拨槽的中间的两个小侧面,加工精度IT10,粗糙度6.3
(6)加工0.8*45°的倒角
工序六:
(1),用Φ8.5的麻花钻钻孔
(2),用Φ10的丝锥攻丝,加工M10的螺纹孔。
工序七:
(1),用无心磨床精加工Φ15.81的孔,粗糙度3.2
(2),加工0.4*45°的倒角
工序八:
(1),钳工,去毛刺
工序九:
(1),检验
工艺路线三:
工序一:
(1)粗铣叉口下端面加工经济精度IT12,粗糙度12.5(组合夹具)
(2)精铣叉口下端面,加工经济精度IT10,粗糙度6.3
工序二:
(1)用Φ14的麻花钻加工孔,加工经济精度IT13,粗糙度12.5(专用夹具)
(2)用Φ10的立铣刀扩孔到直径为15.5mm,加工精度为IT10,粗糙度为6.3
工序三:
(1)粗铣叉口上端面,加工经济精度IT12,粗糙度12.5(组合夹具)
(2)粗铣叉口中间的两侧面,加工经济精度IT12,粗糙度12.5
(3)粗铣拨槽的最前端面,加工经济精度IT12,粗糙度12.5
(4)精铣叉口上端面,加工经济精度IT10,粗糙度6.3
(5)精铣叉口中间的两侧面,加工经济精度IT10,粗糙度6.3
(6)加工0.8*45°的倒角
工序四:
(1) 粗铣拨槽下端面,加工经济精度IT12,粗糙度12.5
工序五:
(1)粗铣拨槽的一个侧面,加工经济精度IT12,粗糙度12.5(专用夹具)
(2)粗铣叉口中间的两侧面,加工经济精度IT12,粗糙度12.5
(3)精铣拨槽侧面,加工精度IT10,粗糙度6.3
(4)粗铣拨槽的另一个侧面,加工经济精度IT12,粗糙度12.5(专用夹具)
(5)精铣拨槽侧面,加工精度IT10,粗糙度6.3
(6)加工0.8*45°的倒角
工序六:
(1),用Φ8.5的麻花钻钻孔
(2),用Φ10的丝锥攻丝,加工M10的螺纹孔。
工序七:
(1),用无心磨床精加工Φ15.81的孔,粗糙度3.2
(2),加工0.4*45°的倒角
工序八:
(1),钳工,去毛刺
工序九:
(1),检验
工艺路线四:
工序一:
(1)用Φ14的麻花钻加工孔,加工经济精度IT13,粗糙度12.5(专用夹具)
(2)用Φ10的立铣刀扩孔到直径为15.5mm,加工精度为IT10,粗糙度为6.3
工序二:
(1) 粗铣叉口上端面加工经济精度IT12,粗糙度12.5(组合夹具)
(2) 粗铣叉口最上端面加工经济精度IT12,粗糙度12.5
工序三:
(1)粗铣叉口下端面加工经济精度IT12,粗糙度12.5(组合夹具)
(2)粗铣叉口中间的两侧面,加工经济精度IT12,粗糙度12.5
工序四:
(1)下叉口淬火处理,硬度要求为45HRC。
工序五:
(1)精铣叉口上端面,加工经济精度IT10,粗糙度6.3
工序六:
(1) 精铣叉口的下端面,加工经济精度IT10,粗糙度6.3
(2) 精铣叉口中间的两侧面,加工经济精度IT10,粗糙度6.3
(3) 加工0.8*45°的倒角。
工序七:
(1)粗铣拨槽的一个侧面,加工经济精度IT12,粗糙度12.5
(2)粗铣拨槽的中间两侧面,加工经济精度IT12,粗糙度12.5
(3)精铣拨槽的一个侧面,加工经济精度IT10,粗糙度6.3
(4)精铣拨槽的中间两侧面,加工经济精度IT10,粗糙度6.3
(5)加工0.8*45°的倒角
工序八:
(1)粗铣拨槽的另一个侧面,加工经济精度IT12,粗糙度12.5(专用夹具)
(2)精铣拨槽侧面,加工精度IT10,粗糙度6.3
(3)加工0.8*45°的倒角
工序九:
(1) 粗铣拨槽下端面,加工经济精度IT12,粗糙度12.5
(2),用Φ8.5的麻花钻钻孔
(3),用Φ10的丝锥攻丝,加工M10的螺纹孔。
工序十:
(1),用无心磨床精加工Φ15.81的孔,粗糙度3.2
(2),加工0.4*45°的倒角
工序十一:
(1),钳工,去毛刺
工序十二:
(1),检验
3.5工艺路线比较
上述四个工艺路线,路线一和路线三先加工拨叉的底平面,后加工孔,遵循先面后孔的原则,路线二和路线四是鉴于孔的加工要求较高,与底面的垂直度要求也较高,并且是很多尺寸的设计基准,为遵循基准统一的原则,同时也更能保证叉口上下两平面与孔的垂直度要求,所以路线二和路线四要优于路线一和路线三。而由于叉口的下端面是一上端面为基准的,为遵循互为基准的原则,保证底面的加工尺寸精度,应先加工上叉口,后加工下叉口,所以路线四优于路线二,固选择路线四为最终的工艺路线。
拟定工艺过程
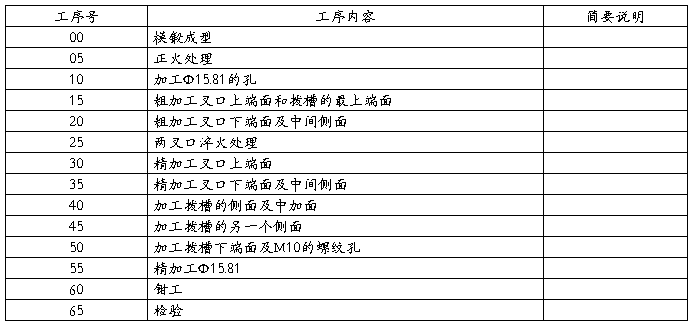
第四章 加工设备及道具、夹具、量具的选择
由于生产类型为大批量,故加工设备以通用机床为主,辅以少量专用机床,其生产方式以通用机床专用夹具为主,辅以少量专用机床的流水生产线,工件在各机上的装卸及各机床间的传送均由人工完成。
4.1根据不同的工序选择不同的机床
10工序是加工Φ15.81的孔,先用Φ14的麻花钻钻孔,再用选用Φ15的扩孔钻扩孔,可选用立式摇臂钻床完成。
15工序是粗铣叉口上端面,可选用立式铣床完成。
20工序是粗铣叉口下端面及中间两侧面,可以选用立式铣床完成。
30工序是精加工叉口上端面,选用立式铣床完成。
35工序是粗铣叉口上端面及中间两侧面,可以选用立式铣床完成。
40 工序是铣削加工拨槽的侧面以及拨槽的中间两个小侧面,可选用卧式铣床来完成。
45工序是加工拨槽的另一个侧面,在上道工序的基础将夹具旋转180°,同样的采用卧式铣床。
50 工序是铣削拨槽的下端面和钻孔加工M10*1的螺纹孔,可以选用卧式铣床完成
55 为精加工Φ15.81的孔,采用万能无心磨床来保证精度。
4.2 刀具选择
选用硬质合金铣刀,硬质合金钻头,硬质合金扩孔钻、加工中碳钢零件采用YG硬质合金,粗加工用YG8,半精加工为YG6
各工序所需刀具如下表:
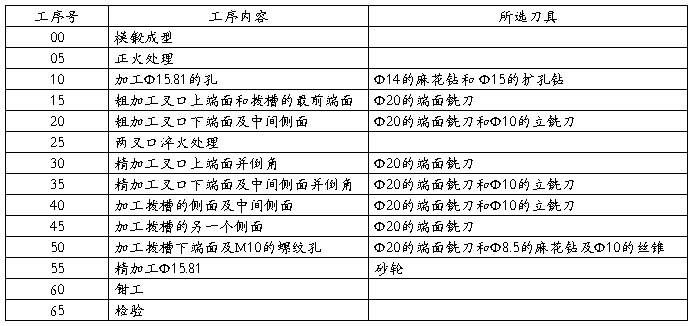
4.3,选择量具
本零件属于成批生产,一般情况下尽量采用通用夹具。根据零件的表面的精度要求,尺寸和形状特点,参考相关资料,选择如下:
10工序采用游标卡尺和塞规。
15、20、30、35、40、45工序采用游标卡尺和标准粗糙度块。
倒0.8*450角度,采用万能角度卡尺。
50工序采用塞规检验。
第五章 确定切削用量
工序一:
工步一:用Φ14的麻花钻钻孔
a p=5.5mm, Vc=50-70m/min,取Vc=50m/min
n=(1000×50)/(3.14×14)=1137.4r/min
主轴最大转速1400 r/min ,所以取n=1135r/min, Vc=(1135×3.14×14)/1000=49.89m/min
工步二:用Φ15的扩孔钻扩孔
a p=5.5mm, Vc=50-70m/min,取Vc=50m/min
n=(1000×50)/(3.14×15)=1061.6r/min
主轴最大转速1400 r/min ,所以取n=1060r/min, Vc=(1060×3.14×15)/1000=49.92m/min
工序二:
工步一:粗铣叉口上端面
已知工件材料为35#钢,选择镶齿套式面铣刀,齿数z=10,材料YG8, fz=0.2~0.29/齿。
确定每齿进给量和背吃刀量。
查表取每齿进给量,查表取af=1.2mm/z
背吃刀量取4mm
查表得:
V=64m/min Pm=1.33kw
计算实际主轴转速
主轴转速n=1000×64/(3.14×20)=1019.1 r/min ,查表得n=1000 r/min ,
计算Vc=1000×3.14×20/1000=62.8 m/min
功率校核PM=1.33 kw<P
经检查所有要求符合要求
工步二:精铣叉口上端面
选择镶齿套式面铣刀,齿数z=10,材料YG6,fz=0.1mm/齿V=124m/min。
计算实际主轴转速
主轴转速n=1000×124/(3.14×20)=493.6 r/min
计算Vc=600×3.14×80/1000=150.7 m/min
计算得n=494 r/min,实际转速V=150 m/min ,
经检查所有参数符合要求。
工步三:粗铣叉口中间的侧面
选择普通的Φ10立铣刀,齿数为Z=2,材料YG6,fz=0.1mm/齿V=20m/min。
计算实际主轴转速
主轴转速n=1000×20/(3.14×10)=636.9 r/min
取n=630 r/min
计算Vc=630×3.14×10/1000=19.7m/min
计算得n=630 r/min,实际转速V=19.7m/min ,
经检查所有参数符合要求。
工步四:精铣叉口中间的侧面
转速及切削速度同上。
工序三:
工步一:粗铣下端面,刀具、转速及切削用量同上表面的加工。
工步二:精铣下端面同上
工序四、五:刀具、转速及切削用量同工序一
工序六:
工步一:粗铣拨槽的下面,刀具、转速及切削用量同上表面的加工
工步二:用Φ8.5的麻花钻钻孔
用Z535卧式钻床加工
切削用量f
刀具采用莫式锥柄麻花钻钻头,直径d=8.5mm,使用切削液。
1. 确定进给量f
由于孔径和深度均很小,宜采用手动进给
2. 选用钻头磨钝标准和耐用度
根据表5-130,钻头后刀面最大磨损量为0.6mm耐用度为60min
3. 确定切削速度v
由表5-132, σb=670上的35#刚的加工性为5类,根据表5-127,暂定进给量=0.16mm/r由表5-131,可查v=16m/min.根据Z535卧式钻床说明书选择主轴实际转速=1400r/min.
工步三:用Φ10的丝锥攻丝
螺纹的螺距为P=1mm,牙深=0.6495P=0.6495mm
取S=200r/min,F=S*P=200mm\min
第六章 基本时间的确定
6.1工时定额的计算
工时定额是指完成零件加工的就一个工序的时间定额
Td=Tj+Tf+Tb+Tx+Tz/N
其中:Td是指单件时间定额
Tj是指基本时间(机动时间),通过计算求得
Tf是指辅助时间,一般取(15-20)%Tj;Tj与Tf和称为作业时间
Tb是指布置工作时间,一般按作业时间的(2-7)%估算
Tx是指休息及生理需要时间,一般按作业时间的(2-4)%估算
Tz是指准备与终结时间,大量生产时,准备与终结时间忽略不计
N是指一批零件的个数
下表是各个工步基本时间的计算公式及其结果
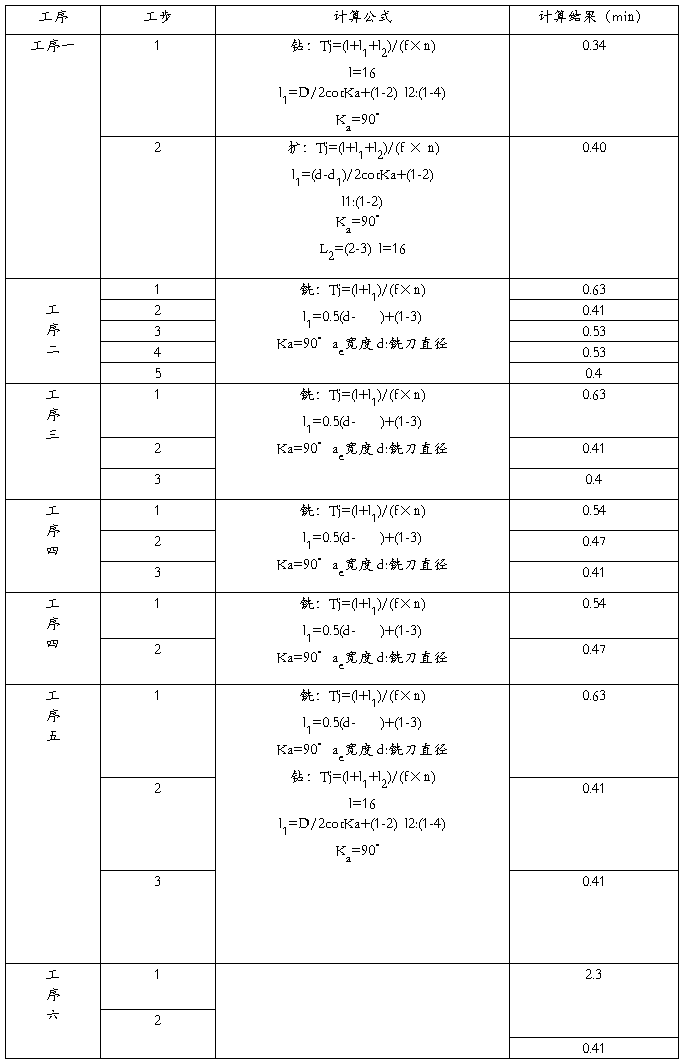
6.2 工序额的确定
(1)Td=Tj+Tf+Tb+Tx+Tz/N
= Tj1~19+ Tf+Tb+Tx
= (Tj1-Tj19)+18% (Tj1-Tj19)+5%( Tj+Tf)+3% ( Tj+Tf)
= (Tj1-Tj19)+18% (Tj1-Tj19)+5%((Tj1-Tj19)+18% (Tj1-Tj19))+3% ((Tj1-Tj19)+18% (Tj1-Tj19))
Tj=0.24+……+0.049=2.48
Td=2.48+18%×2.48+5%(2.48+18%×2.48)+3%(2.48+18%×2.48)
=3.2min
=192s
(2)工序二的时间定额:
Td=Tj+Tf+Tb+Tx+Tz/N
=Tj1+Tj2+Tj3+Tf+Tb+Tx
=(Tj1+……+Tj5)+ 18% (Tj1+……Tj5)+ 5%(Tj+Tf)+ 3% (Tj+Tf)
=(Tj1+……+Tj5) + 18% (Tj1+……Tj5)+ 5%((Tj1+……+Tj5)+ 18% (Tj1+……Tj5))+3%((Tj1+……+Tj5)+ 18% (Tj1+……Tj5))
Tj=0.063+0.18+0.09+0.06+0.14=0.533min
Td=0.533+18%×0.533+5%(0.533+18%×0.533)+3%(0.533+18%×0.533)
=0.68min
=40.7s
(3)工序三的时间定额:
Td=Tj+Tf+Tb+Tx+Tz/N
=Tj1+Tj2+Tj3+Tf+Tb+Tx
=Tj1+18% Tj1+5%(Tj+Tf) + 3% (Tj+Tf)
= Tj1+18% Tj1+5%( Tj1+18% Tj1)+ 3%( Tj1+18% Tj1)
=0.049+18%×0.049+5%(0.049+18%×0.049)+3%(0.049+18%×0.049)
=0.063min
=3.75s
(4)工序四的时间定额:
Td=Tj+Tf+Tb+Tx+Tz/N
=Tj1+Tj2+Tj3+Tf+Tb+Tx
=Tj1+18% Tj1+5%(Tj+Tf) + 3% (Tj+Tf)
= Tj1+18% Tj1+5%( Tj1+18% Tj1)+ 3%( Tj1+18% Tj1)
=0.63+18%×0.63+5%(0.63+18%×0.63)+3%(0.049+18%×0.049)
=2.86min
(5)工序五德时间定额:
Td=Tj+Tf+Tb+Tx+Tz/N
=Tj1+Tj2+Tj3+Tf+Tb+Tx
=Tj1+18% Tj1+5%(Tj+Tf) + 3% (Tj+Tf)
= Tj1+18% Tj1+5%( Tj1+18% Tj1)+ 3%( Tj1+18% Tj1)
=0.63+18%×0.63+5%(0.63+18%×0.63)+3%(0.049+18%×0.049)
=2.86min
(6)工序六的时间定额:
Td=Tj+Tf+Tb+Tx+Tz/N
=Tj1+Tj2+Tj3+Tf+Tb+Tx
=Tj1+18% Tj1+5%(Tj+Tf) + 3% (Tj+Tf)
= Tj1+18% Tj1+5%( Tj1+18% Tj1)+ 3%( Tj1+18% Tj1)
=0.63+18%×0.63+5%(0.63+18%×0.63)+3%(0.049+18%×0.049)
=2.62min
第七章:夹具的设计
本夹具是用立式铣床加工换挡叉的叉口下表面专用夹具。
7.1.工件的加工工艺和定位分析
叉下表面的粗糙度为3.6,相对左端槽的中心线误差为±0.15,叉口上下表面以Φ15.81的孔为定位基准,垂直度误差为0.15,倒角为0.8。
7.2.夹具设计方案
1、定位方案。工件以已加工的叉口上表面和右边的圆柱为定位基准来保证加工要求。为防止换挡叉转动,在叉口内侧加一定位螺栓,让换挡叉内侧和螺栓的两侧面可靠接触。这样就实现了6点定位限制6个自由度。
2、夹紧机构。为保证叉口上表面和表面可靠接触,在叉口的右上面用压板将其夹紧。
3、夹具的结构设计详见装配图。
总结
此次课程设计确定了换挡叉从锻件毛坯到成品在大量成批生产时的工艺过程,同时也设计了其中一道面铣工序的夹具。
作为本学期的一次课程设计,需要我们综合前阶段所学习的机械制图、金属工艺学、金属材料、机械设计基础、互换性与测量技术、机械制造工艺学等多门课程的知识,同时还要运用数学、力学等基础学科知识以及设计手册上的标准。所以此次课程设计是我们本科阶段学习的知识的巩固,也是一个总结。
参考文献
致 谢
机械制造工艺学课程设计是学完了机械制造工艺学基础和大部分专业课,并进行了生产实习的基础上进行的又一个实践性教学环节。这次课程设计过程中遇到了不少困难,在老师和同学的帮助下和在图书馆查阅资料,最终解决了困难。而且,这次设计使我们能综合运用机械制造技术基础中的基本理论,并结合生产实习中学到的实践知识,独立地分析和解决了零件机械制造工艺问题,设计了机床专用夹具这一典型的工艺装备,提高了结构设计能力 ,为今后的毕业设计及未来从事的工作打下了良好的基础。
附录
附录1:零件图
附录2:工艺卡
附录3:夹具装配图
由www.clcw114.com www.gz-rcw.com www.boyhao.com 整理