砂型铸造
钢、铁和大多数有色合金铸件都可用砂型铸造方法获得。由于砂型铸造所用的造型材料价廉易得,铸型制造简便,对铸件的单件生产、成批生产和大量生产均能适应,长期以来,一直是铸造生产中的基本工艺。砂型铸造所用铸型一般由外砂型和型芯组合而成。为了提高铸件的表面质量,常在砂型和型芯表面刷一层涂料。涂料的主要成分是耐火度高、高温化学稳定性好的粉状材料和粘结剂,另外还加有便于施涂的载体(水或其他溶剂)和各种附加物。
铸造分类铸造分类主要有砂型铸造和特种铸造两大类。
1 普通砂型铸造,利用砂作为铸模材料,又称砂铸,翻砂,包括湿砂型、干砂型和化学硬化砂型3类,但并非所有砂均可用以铸造。好处是成本较低,因为铸模所使用的沙可重复使用;缺点是铸模制作耗时,铸模本身不能被重复使用,须破坏后才能取得成品。
2特种铸造,按造型材料又可分为以天然矿产砂石为主要造型材料的特种铸造(如熔模铸造、泥型铸造、壳型铸造、负压铸造、实型铸造、陶瓷型铸造,消失模铸造等)和以金属为主要铸型材料的特种铸造(如金属型铸造、压力铸造、连续铸造、低压铸造、离心铸造等)两类。
砂型材料
制造砂型的基本原材料是铸造砂和型砂粘结剂。最常用的铸造砂是硅质砂。硅砂 的高温性能不能满足使用要求时则使用锆英砂、铬铁矿砂、刚玉砂等特种砂。为使制成的砂型和型芯具有一定的强度,在搬运、合型及浇注液态金属时不致变形或损坏,一般要在铸造中加入型砂粘结剂,将松散的砂粒粘结起来成为型砂。应用最广的型砂粘结剂是粘土,也可采用各种干性油或半干性油、水溶性硅酸盐或磷酸盐和各种合成树脂作型砂粘结剂。砂型铸造中所用的外砂型按型砂所用的粘结剂及其建立强度的方式不同分为粘土湿砂型、粘土干砂型和化学硬化砂型3种。
1.粘土湿砂型
以粘土和适量的水为型砂的主要粘结剂,制成砂型后直接在湿态下合型和浇注。湿型铸造历史悠久,应用较广。湿型砂的强度取决于粘土和水按一定比例混合而成的粘土浆。型砂一经混好即具有一定的强度,经舂实制成砂型后,即可满足合型和浇注的要求。因此型砂中的粘土量和水分是十分重要的工艺因素。
优点:①粘土的资源丰富、价格便宜。②使用过的粘土湿砂经适当的砂处理后,绝大部分均可回收再用。③制造铸型的周期短、工效高。④混好的型砂可使用的时间长。⑤砂型舂实以后仍可容受少量变形而不致破坏,对拔模和下芯都非常有利。
缺点:①混砂时要将粘稠的粘土浆涂布在砂粒表面上,需要使用有搓揉作用的高功率混砂设备,否则不可能得到质量良好的型砂。②由于型砂混好后即具有相当高的强度,造型时型砂不易流动,难以舂实,手工造型时既费力又需一定的技巧,用机器造型时则设备复杂而庞大。③铸型的刚度不高,铸件的尺寸精度较差。④铸件易于产生冲砂、夹砂、气孔等缺陷。 2.粘土干砂型
制造这种砂型用的型砂湿态水分略高于湿型用的型砂。砂型制好以后,型腔表面要涂以耐火涂料,再置于烘炉中烘干,待其冷却后即可合型和浇注。烘干粘土砂型需很长时间,要耗用大量燃料,而且砂型在烘干过程中易产生变形,使铸件精度受到影响。粘土干砂型一般用于制造铸钢件和较大的铸铁件。自化学硬化砂得到广泛采用后,干砂型已趋于淘汰。
3.化学硬化砂型
这种砂型所用的型砂称为化学硬化砂。其粘结剂一般都是在硬化剂作用下能发生分子聚合进而成为立体结构的物质,常用的有各种合成树脂和水玻璃。
化学硬化基本上有3种方式。① 自硬:粘结剂和硬化剂都在混砂时加入。制成砂型或型芯后,粘结剂在硬化剂的作用下发生反应而导致砂型或型芯自行硬化。自硬法主要用于造型,但也用于制造较大的型芯或生产批量不大的型芯。② 气雾硬化:混砂时加入粘结剂和其他辅加物,先不加硬化剂。造型或制芯后,吹入气态硬化剂或吹入在气态载体中雾化了的液态硬化剂,使其弥散于砂型或型芯中,导致砂型硬化。气雾硬化法主要用于制芯,有时也用于制造小型砂型。③ 加热硬化:混砂时加入粘结剂和常温下不起作用的潜硬化剂。制成砂型或型芯后,将其加热,这时潜硬化剂和粘结剂中的某些成分发生反应,生成能使粘结剂硬化的有效硬化剂,从而使砂型或型芯硬化。加热硬化法除用于制造小型薄壳砂型外,主要用于制芯。
化学硬化砂型铸造工艺的特点是:①化学硬化砂型的强度比粘土砂型高得多,而且制成砂型后在硬化到具有相当高的强度后脱膜,不需要修型。因而,铸型能较准确地反映模样的尺寸和轮廓形状,在以后的工艺过程中也不易变形。制得的铸件尺寸精度较高。②由于所用粘结剂和硬化剂的粘度都不高,很易与砂粒混匀,混砂设备结构轻巧、功率小而生产率高,砂处理工作部分可简化。③混好的型砂在硬化之前有很好的流动性,造型时型砂很易舂实,因而不需要庞大而复杂的造型机。④用化学硬化砂造型时,可根据生产要求选用模样材料,如木、塑料和金属。⑤化学硬化砂中粘结剂的含量比粘土砂低得多,其中又不存在粉末状辅料,如采用粒度相同的原砂,砂粒之间的间隙要比粘土砂大得多。为避免铸造时金属渗入砂粒之间,砂型或型芯表面应涂以质量优良的涂料。⑥用水玻璃作粘结剂的化学硬化砂成本低、使用中工作环境无气味。但这种铸型浇注金属以后型砂不易溃散;用过的旧砂不能直接回收使用,须经再生处理,而水玻璃砂的再生又比较困难。⑦用树脂作粘结剂的化学硬化砂成本较高,但浇注以后铸件易于和型砂分离,铸件清理的工作量减少,而且用过的大部分砂子可再生回收使用。
砂芯类型
型芯 为了保证铸件的质量,砂型铸造中所用的型芯一般为干态型芯。根据型芯所用的粘结剂不同,型芯分为粘土砂芯、油砂芯和树脂砂芯几种。
1.粘土砂芯 用粘土砂制造的简单的型芯。
2..油砂芯 用干性油或半干性油作粘结剂的芯砂所制作的型芯,应用较广。油类的粘度低,混好的芯砂流动性好,制芯时很易紧实。但刚制成的型芯强度很低,一般都要用仿形的托芯板承接,然后在200~300℃的烘炉内烘数小时,借空气将油氧化而使其硬化。这种造芯方法的缺点是:型芯在脱模、搬运及烘烤过程中容易变形,导致铸件尺寸精度降低;烘烤时间长,耗能多。
3.树脂砂芯 用树脂砂制造的各种型芯。型芯在芯盒内硬化后再将其取出,能保证型芯的形状和尺寸的正确。根据硬化方法不同,树脂砂芯的制造一般分为热芯盒制芯和冷芯盒制芯两种方法。①热芯盒法制芯:50年代末期出现。通常以呋喃树脂为芯砂粘结剂,其中还加入潜硬化剂(如氯化铵)。制芯时,使芯盒保持在200~300℃,芯砂射入芯盒中后,氯化铵在较高的温度下与树脂中的游离甲醛反应生成酸,从而使型芯很快硬化。建立脱模强度约需10~100秒钟。用热芯盒法制芯,型芯的尺寸精度比较高,但工艺装置复杂而昂贵,能耗多,排出有刺激性的气体,工人的劳动条件也很差。②冷芯盒法制芯:60年代末出现。用尿烷树脂作为芯砂粘结剂。用此法制芯时,芯盒不加热,向其中吹入胺蒸汽几秒钟就可使型芯硬化。这种方法在能源、环境、生产效率等方面均优于热芯盒法。70年代中期又出现吹二氧化硫硬化的呋喃树脂冷芯盒法。其硬化机理完全不同于尿烷冷芯盒法,但工艺方面的特点,如硬化快、型芯强度高等,则与尿烷冷芯盒法大致相同.
砂型铸造生产常规工艺流程
铸造工艺设计的内容和一般程序
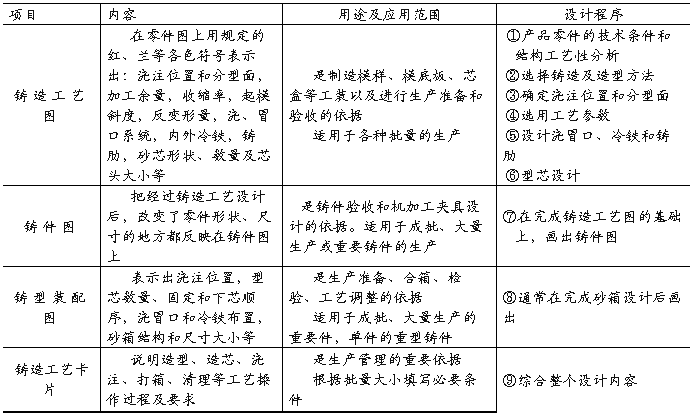
造型的基本操作
造型方法很多,但每种造型方法大都包括舂砂、起模、修型、合箱工序。
1. 造型模样
用木材、金属或其它材料制成的铸件原形统称为模样,它是用来形成铸型的型腔。用木材制作的模样称为木模,用金属或塑料制成的模样称为金属模或塑料模。目前大多数工厂使用的是木模。模样的外形与铸件的外形相似,不同的是铸件上如有孔穴,在模样上不仅实心无孔,而且要在相应位置制作出芯头。
2. 造型前的准备工作
① 准备造型工具,选择平整的底板和大小适应的砂箱。砂箱选择过大,不仅消耗过多的型砂,而且浪费舂砂工时。砂箱选择过小,则木模周围的型砂舂不紧,在浇注的时候金属液容易从分型面即交界面间流出。通常,木模与砂箱内壁及顶部之间须留有30~100mm的距离,此距离称为吃砂量。吃砂量的具体数值视木模大小而定。② 擦净木模,以免造型时型砂粘在木模上,造成起模时损坏型腔。③ 安放木模时,应注意木模上的斜度方向,不要把它放错。
3. 舂砂
① 舂砂时必须分次加入型砂。对小砂箱每次加砂厚约50~70mm。加砂过多舂不紧,而加砂过少又费用工时。第一次加砂时须用手将木模周围的型砂按紧,以免木模在砂箱内的位置移动。然后用舂砂锤的尖头分次舂紧,最后改用舂砂锤的平头舂紧型砂的最上层。
② 舂砂应按一定的路线进行。切不可东一下、西一下乱舂,以免各部分松紧不一。
③ 舂砂用力大小应该适当。用力过大,砂型太紧,浇注时型腔内的气体跑不出来。用力过小,砂型太松易塌箱。同一砂型各部分的松紧是不同的,靠近砂箱内壁应舂紧,以免塌箱。靠近型腔部分,砂型应稍紧些,以承受液体金属的压力。远离型腔的砂层应适当松些,以利透气。
④ 舂砂时应避免舂砂锤撞击木模。一般舂砂锤与木模相距20~40mm,否则易损坏木模
4. 撒分型砂
在造上砂型之前,应在分型面上撒一层细粒无粘土的干砂(即分型砂),以防止上、下砂箱粘在一起开不了箱。撒分型砂时,手应距砂箱稍高,一边转圈、一边摆动,使分型砂经指缝缓慢而均匀散落下来,薄薄地复盖在分型面上。最后应将木模上的分型砂吹掉,以免在造上砂型使,分型砂粘到上砂型表面,而在浇注时被液体金属冲下来落入铸件中,使其产生缺陷。
5. 扎通气孔
除了保证型砂有良好的透气性外,还要在已舂紧和刮平的型砂上,用通气针扎出通气孔,以便浇注时气体易于逸出。通气孔要垂直而且均匀分布。
6. 开外浇口
外浇口应挖成60°的锥形,大端直径约60~80mm。浇口面应修光,与直浇道连接处应修成圆弧过渡,以引导液体金属平稳流入砂型。若外浇口挖得太浅而成碟形,则浇注液体金属时会四处飞溅伤人。
7. 做合箱线
若上、下砂箱没有定位销,则应在上、下砂型打开之前,在砂箱壁上作出合箱线。最简单的方法是在箱壁上涂上粉笔灰,然后用划针画出细线。需进炉烘烤的砂箱,则用砂泥粘敷在砂箱壁上,用墁刀袜平后,再刻出线条,称为打泥号。合箱线应位于砂箱壁上两直角边最远处,以保证x和y方向均能定位,并可限制砂型转动。两处合箱线的线数应不相等,以免合箱时弄错。做线完毕,即可开箱
起模。
8. 起模
① 起模前要用水笔沾些水,刷在木模周围的型砂上,以防止起模时损坏砂型型腔。刷水时应一刷而过,不要使水笔停留在某一处,以免局部水分过多而在浇注时产生大量水蒸汽,使铸件产生气孔缺陷。
② 起模针位置要尽量与木模的重心铅锤线重合。起模前,要用小锤轻轻敲打起模针的下部,使木模松动,便于起模。
③ 起模时,慢慢将木模垂直提起,待木模即将全部起出时,然后快速取出。起模时注意不要偏斜和摆动。
9. 修型
起模后,型腔如有损坏,应根据型腔形状和损坏程度,正确使用各种修型工具进行修补。如果型腔损坏较大,可将木模重新放入型腔进行修补,然后再起出。
10. 合箱
合箱是造型的最后一道工序,它对砂型的质量起着重要的作用。合箱前,应仔细检查砂型有无损坏和散砂,浇口是否修光等。如果要下型芯,应先检查型芯是否烘干,有无破损及通气孔是否堵塞等。型芯在砂型中的位置应该准确稳固,以免影响铸件准确度,并避免浇注时被液体金属冲偏。合箱时应注意使上砂箱保持水平下降,并应对准合箱线,防止错箱。合箱后最好用纸或木片盖住浇口,以免砂子或杂物落入浇口中。
心得
通过学习砂型铸造我认识到了知识实践的重要性,我们不能只学习书本知识,我们更应该把知识应用到实践中去,砂型铸造只是一个我们机械学习中很基础的一小部分,我们要好好的学习以后的东西,为我们的未来也为我们机械的发展。
第二篇:铸钢实习报告
中煤张家口煤矿机械有限责任公司铸钢车间实习报告
实习地点:中煤张家口煤矿机械有限责任公司铸钢车间
实习时间:20##年3~8月
实习目的:
通过实习,将课堂上所学的有关理论知识与生产实际紧密结合,做到理论联系实际,加深自己对铸钢车间特别是对冶炼过程的感性认识,增强自己的实践经历和知识;通过实习使自己加深对专业领域的认识,以便能更好的掌握冶炼有关的生产工艺、生产设备以及铸件质量、性能等因素,力图达到能对生产中的各项经济指标进行分析与计算,从而改进生产工艺或者生产的组织与管理,提高效益,降低能耗;同时通过车间的生产实习,全面了解车间的现状、产品以及生产状况,加强自己对车间的存在感、归属感。
五个月的生产实习,加强了自己从事专业技术工作及管理工作所必须的各种基本技能和实践动手能力。了解了本行业业务范围内的现代工业生产组织形式、管理方式、工艺过程及工艺技术方法。培养自己理论联系实际、从实际出发分析问题、研究问题和解决问题的能力,并将所学知识系统化,实践化。培养自己热爱劳动、不怕苦、不怕累的工作作风。
实习内容:
一、中煤张家口煤炭中煤张家口煤矿机械有限责任公司铸钢车间简介
中煤张家口煤炭中煤张家口煤矿机械有限责任公司隶属于中煤集团下的中煤装备公司,是专业生产煤矿用输送设备的公司,公司主要产品有刮板输送机、转载机、破碎机、刨煤机。铸钢车间主要负责刮板输送机主要部件中部槽槽帮、破碎机锤体、刨煤机的一些部件的铸造成型、表面喷丸,以及刮板、销轨等的喷丸处理。
铸钢车间是一个非常具有锐意与创新的车间。在一个年设计制造能力只有4000吨的车间,它完成了公司规定的10800吨的生产任务,这不得不说是个奇迹。
整个铸钢车间由三个工段组成,分别为造型、冶炼、清铲。造型主要负责砂型箱体的制作,分为造型组和刻芯组。本工段采用水玻璃生产工艺,拥有从日本引进的真空VRH造型生产线。冶炼工段负责铸件的冶炼以及浇铸成型,拥有两个三吨碱性电弧炉,以废钢为原料,采用氧化法炼钢生产各类铸件。清铲主要负责铸件的砂子清理以及浇冒口的切割,以及铸件的表面喷丸工作。
二、铸钢车间生产工艺流程简介
在生产实习中,我了解到铸钢车间采用水玻璃生产工艺制造各类铸件,先在造型工段制作砂型箱体,经冶炼工段浇铸成型,然后至清铲工段清理、切割、修补、喷丸得到最终产品。
造型工段分为刻芯和造型组。造型线主要制作中部槽槽帮箱体,刻芯主要制作箱体内所需要的砂型部件。中部槽槽帮为车间的主要产品,需求量大,拥有专门的真空VRH造型线,进行规模化生产,生产效率高。相对而言需求量小很多的破碎机锤体以及一些小件砂型箱的制作全由人工制作成型,效率慢很多,劳动量也比较大。
冶炼工段主要由钢炉和浇铸两部分组成。是车间技术含量比较高的工段。钢炉组拥有两个3吨碱性电弧炉,承担车间各类铸件的冶炼工作。钢炉组主要炼制30MnSi和30MnSiMo(6BM)两个钢种。它以废钢为主要原料,利用氧化法的炼钢工艺进行炼制。钢炉组克服很多苦难,锐意进取,在保证质量的同时,开创了3吨炉炼5~6吨钢水的伟大壮举,极大的提高了生产效益。而且在设备老化严重,故障多的情况下顺利完成了公司的给类生产任务,而且获得了公司质量先进班组的称号。
浇铸组主要负责烘焙盛钢桶以及浇铸工作。负责把镇静好的钢液浇铸入倒扣好的砂型箱中。
清铲工段是可以说是全公司环境最恶劣的工段,主要负责铸件的清理以及切割工作。这是车间产品的最后一个工段,车间产品质量的好坏很大一部分都在清铲工段,特别是切割工序。切割工序使用氧炔枪对铸件的浇冒口进行切割,关系到产品的尺寸和形貌,工艺要求严格,质量控制也比较严格。
清铲工段还得对铸件的表面进行喷丸处理,拥有四台喷丸机,可以对槽帮、销轨、刮板进行喷丸处理。清铲工段还有一个主要工作是对有缺陷的铸件进行修补,主要手段是堆焊修补。
三、实习情况简介
在本次实习中,我主要以学习观察为主,先在造型和清铲两个工段实习三个星期,以了解车间的大体情况、生产流程以及主要产品。然后再到冶炼区钢炉组实习四个月,主要了解碱性电弧炉生产过程中的工艺路线,操作方法。
在钢炉组的实习,是本次实习的核心和重中之重,本次实习的主要目的旨在通过在钢炉的实习,了解氧化法炼钢的工艺流程和实际操作,并通过与自身的理论知识相结合,来提高自己的综合能力与素质,为车间服务。
车间使用的是炉盖旋开,顶部装料的钢炉,炉体出钢槽出钢,炉门的开关使用压缩空气,为3吨碱性电弧炉。为了完成公司给车间下达的每月成品900吨的冶炼任务,现在基本上每炉装料达到6~7吨,出钢5~6吨,每晚每炉必须冶炼4炉。钢炉组是车间生产的一大亮点,也是车间技术革新,技术改善的重点对象。
电弧炉炼钢有许多因素要考虑,尤其车间所使用的电弧炉,基本上所有操作都由手工完成,加料,喷氧,取样,扒渣,测温都由人工动手完成,劳动强度大,劳动环境恶劣,操作过程难以精准控制,比较容易出现小的差错,会导致所炼钢水成分、温度不准,除气不净等缺陷。而且在节能减排的今天,降低能耗也是我们必须考虑的一个大问题。
在钢炉的实习过程中,我对碱性电弧炉氧化法炼钢的六个个过程:补炉、配料装料、熔化期、氧化期、还原期、出钢均做了详细了解,并对一些环节进行了实践操作。下面是我对车间钢炉组冶炼过程工作的的归纳总结:
1.补炉
每炼完一炉钢后,在装料前必须要进行补炉,其目的是修补被侵蚀的渣线和炉底以及其他被破坏的部位,以维持正常的炉体形状,从而保证冶炼的正常进行和安全生产。补炉的原则是高温、快补、薄补,维护炉膛原状。车间采用湿补,在出钢后带炉体恢复正常扒除炉门上残余渣后,立即用镁砂修补渣线和炉壁薄弱处,然后休整炉门。补炉必须达到高温、快补、薄补,利用炉膛余热使镁砂烧结在炉壁上。
2.配料装料
主要原料为废钢,利用焦炭配。废钢先用电子秤称质量,确定炉料量,然后计算确定所用焦炭量。配炭要充分考虑客观因素,如果炉料氧化皮比较多、潮湿,配炭得稍多点,不然会造成后期除气不尽。我在实习期间,发现了不少由于配炭不准,造成除气不净,返炉重炼的现象。还有炭不能配得太高,这样会造成氧化期实践延长,提高能耗。
装料前,先向炉底铺上一层石灰以及部分萤石,这有利于早期去磷,减少钢液吸气以及去除部分非金属夹杂。装料时,直接使用天车吊着料斗把料倒进炉内。有时进行二次加料,二次加料要快,先把料准备好后,再旋开炉盖加料。 如果炉底造渣材料不足,也可在二次加料时加入部分石灰和萤石,减轻后期劳动强度。这样亦可以更好的捕捉脱磷时机。
如果冶炼6BM,由于钼铁熔点高,不易挥发和氧化,我们一般先在前期加料时一并加入炉内,以便在以后的过程中充分扩散,使成分均匀。
3.熔化期
熔化期是主要耗电时期,分为启弧、穿井、电极上升、低温区炉料熔化四个阶段。熔化期的任务是将固体炉料迅速熔化成钢液,并进行脱磷,减少钢液吸气和以及防止金属挥发。
为了加速熔化,预前脱磷,在炉料熔化到2/3时,进行吹氧助熔。吹氧助熔有利于加速大料以及炉内部分低温区域炉料的熔化,有效的降低能耗,节省成本。吹氧时,吹氧压力大概为0.5~0.6Mpa,吹氧管折成20到30度角,插入深度10~20cm。吹大料使,为了防止塌料,造成钢液翻溅,失炭严重,吹氧位置和角度的选择至关重要。
熔化期熔化渣的好坏直接影响的脱磷的成败以及电能的利用率。所以在吹氧的同时,必须时刻关注渣面,适时调渣,最好形成泡沫渣。熔化期快结束时,应采取流渣操作,重造新渣,这样既有利于后期进一步脱磷也可以节省造渣材料,并可以减小钢液的后期回磷量。
熔化期快结束时,取样分析化学成分,确定炭、硫、磷含量作为后阶段氧化还原反应控制成分的依据。
4.氧化期
个人认为氧化期是这个冶炼过程中最复杂也是最重要,最难控制的过程。氧化期的主要任务是脱炭、脱磷,以及去除气体和夹杂物,并提高钢液温度。氧化前期主要目的是造渣脱磷,这时温度得偏低,炉渣要有强氧化性和强碱性,并且流动性要好,氧化后期是脱炭除气去杂质,采用吹氧(主要)和加矿石结合的方法脱炭。氧化后期渣的流动性好,渣要薄,可以做到炉渣自动流出或者进行流渣操作。氧化期结束后要进行扒渣操作。在整个氧化期采用磨炭花的方法确定炭含量来保证石灰的加入量和流渣操作。车间正常的氧化期时间为20~30分钟。
氧化期操作:1)渣况良好方可分批加矿石,每批加矿石量不得太多。2)调整渣况。当氧化沸腾开始,采用流渣,要求炉渣碱度2~3,炉内渣量控制在3%~4%。氧化期后阶段,应使炉渣流动性好,渣层要薄,渣量控制在2%~3%。3)温度控制。氧化期总的来讲是一个升温阶段,升温速度的快慢根据钢液中磷的情况而定。氧化末期必须使钢液温度升高到大于该钢种出钢温度的10~20℃。4)净沸腾。当温度、化学成分合适,就停止加矿石,调整好炉渣,并加入少许锰铁进行预脱氧,让熔池进入自然沸腾(5~10min),使钢液中的残余含氧量降低,并使气体及夹杂物充分上浮,以利于还原期的顺利进行。5)扒渣。氧化期炉渣中FeO含量很高,又含有P2O5,为了还原期脱氧及防止回磷必须扒渣,扒渣的条件是扒渣温度高于出钢温度10~2O℃;扒渣前炭、磷及其他限制性成分应符合要求。
5.还原期
还原期主要任务是造好还原渣对钢液进行脱氧、脱硫,并调整化学成分,控制好出钢温度。
扒渣结束后,立即加入锰铁、硅铁预脱氧,然后迅速加入石灰、萤石造渣。待渣面形成后加入还原剂炭化硅粉,立即关闭炉门,进行还原反应进行脱氧。而且每隔5到8分钟分批加入造渣材料、还原剂确保反应的持续进行。在第二次造渣以及添加还原剂前搅拌熔池,使各种合金料充分溶解,扩散,达到去除非金属夹杂,均匀成分的目的。然后取样分析成分,确定C、Mn、Si、S、P含量,以确定是否需要增炭(用生铁),加硅铁,锰铁量,并去硫以达到合格的化学成分。车间还原期时间一般为30~40分钟。
出岗前分析渣中氧化铁含量,确定是否脱氧良好,确保成分合格,非金属夹杂少,并测温确定出钢温度。
6.出钢
出钢桶先经过烘烤,成暗红色。出岗前先在出钢桶内加入铝线,以最终脱氧。出钢时保持钢液流出顺畅,钢渣混出。
出钢后取样分析化学成分,并加入钢包覆盖剂,喂硅钙线,测温决定镇静时间,然后浇铸。
以上是我对整个冶炼过程的了解,其中有的环节经过自己亲手操作,在操作过程中发现并不是如书上写的那么简单。实际操作过程中有很多技巧,有很多方法值得我去学习和借鉴,譬如吹氧,就得考虑氧气气压,吹氧角度,吹氧位置以及人站立的位置,稍有不慎很有可能造成大塌料,造成后期炭量低,必须增炭去气,致使后期磷含量增高,降低钢水品质。而且塌料是造成钢液飞溅,存在比较大的安全隐患。尤其现在处于夏季,温度高,在钢炉前吹氧,也是对身体的一种考验。
问题与发现:
1. 去磷时机的把握。
去磷时间就短短几分钟,稍有不慎,就会造成去磷时机的丧失,去磷效果不明显。所以抓住去磷时机在炼钢过程中很重要。车间炼钢时,去磷效果不是很理想,最大的问题就是把握不住去磷时机。去磷的关键是低温,高碱,强氧。所以在熔化期的去磷操作至关重要,一般可以去除50~70%的磷。归结到操作的话,就是提前造渣,把握好吹氧时间。但是由于条件以及习惯限制,车间吹氧时间全部由工人自己估计,所以造成吹氧时间的不一致,所以去磷效果参差不齐。查阅有关资料,我觉得有种方法可行,就是在装料时,可在炉底装入少量的矿石,以加强渣液的氧化性。待渣熔化时,就可在钢液上面形成强氧化性渣,提高去磷效果。
2. 氧化期炭含量判断。
氧化期含炭量的判断贯穿整个氧化期。含炭量的高低是判断是否净沸腾,是否扒渣的重要标准,一旦判断失误,就会造成整炉炭含量不准,增加还原期的难度或者返炉重练。在车间氧化期含炭量的判断主要是通过砂轮磨样品,通过火花的特征来判断。该法偏差比较大,其原因是火花的形成与砂轮机的转数及砂轮的砂粒粗细等有关,而且如果含有其他成分,也会使火花的特征改变。所以为了更加精确的判断含炭量,我觉得可以采取磨火花与其他手段相结合的方法来实现。通过查阅资料我找到了另外一种炭含量的判断方法——碳花观察法。该法简单、迅速、准确,获得普遍的应用,其介绍如下:
未经脱氧的钢液在样勺内冷却时,能够继续进行碳氧反应,当气泡逸出时,表面附有一薄层钢液的液衣,宛如空心钢珠,这就是火星。又因为气泡是连续逸出的,所以迸发出来的火星往往形成火线。如果钢中的游离碳较多,有时在火星的表面上还附有碳粒。当气泡的压力较大而珠壁的强度不足时,迸发出来的火星破裂,进而形成所谓的碳花。然而,CO 气泡压力随钢液碳含量的降低而降低,碳花的数目和大小也依次递减,火星的迸发力量也是由强到弱。有经验的炼钢工可根据火星(碳花)的数量、大小与破裂情况及迸发力量的强弱、火线的断续情况或发出的声音等进行判断,碳含量越低判断得越准确,误差常常只有±0.01%~0.02%,而碳含量越高,碳花越大,分叉越多,跳跃越猛烈,也越缺乏规律性,因此碳含量很高时难以准确的判断。当碳含量超过0.80%以上时,碳花在跳跃破裂过程中还发出吱吱的响声。碳花的具体观察方法有两种:一种是直接观察从勺内迸发出来的火星(碳花)情况;另一种是观察火星(碳花)落地后的破裂情况。一般碳钢的碳含量与碳花特征的关系见表1。
表1 碳钢的碳含量与碳花特征的关系
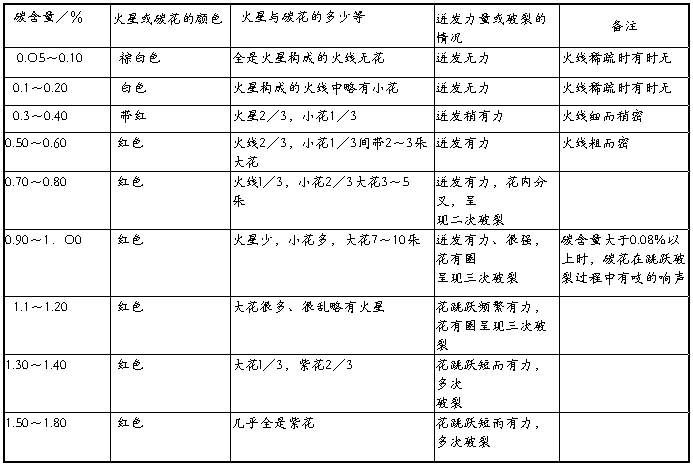
3.熔化期非金属夹杂的去除。
非金属夹杂物对钢的力学性能影响很大。钢中非金属夹杂物主要为脱氧产物和二次氧化产物。钢液脱氧越好,脱氧产物越容易上浮,夹杂物也就越少。二次氧化时形成的夹杂颗粒大,而且由于钢液凝固难于上浮,大部分残留在钢中形成夹杂物。二次氧化产物与钢液中氧的含量,温度高低以及钢液与大气的接触面积大小,时间有关。
要减少夹杂物,其主要手段就是控制好脱氧。车间主要采用的是沉淀脱氧与扩散脱氧相结合的方法来脱氧。沉淀脱氧的原料是硅铁和锰铁,所以最好在预脱氧时强调两者的加入比例(Mn/Si=4.5),加入量,以及加入的先后顺序,力争硅锰同加,其次先锰后硅,杜绝先硅后锰,以达到减少SiO2以及FeO的形成,形成以MnO.SiO2为主的熔点低易凝聚,易上浮的氧化产物。。而且有条件的话,可以适当插铝,加强脱氧效果。
车间还原期白渣中FeO含量对夹杂物的影响很大,FeO含量大,说明钢水中含氧量高,越容易形成基本不能去除的二次氧化产物,所以在操作中,应当尽量减少其含量,最好控制在0.5%以下。终脱氧产物也应当尽量控制好,最好使铝含量为0.002~0.003%,这样既可以良好脱氧,又可以细化晶粒,提高钢的力学性能。
实习总结:
在这五个月的参观、学习和操作的生产实习期间,我参观了整个生产车间,并对工艺流程有了大概的了解,初步认识了本企业特别是本车间的基本情况和它的发展历程,并且对其生产流程有了一些大致的了解。觉得生产实际中的炼钢的过程与在学校所作的实验过程有着巨大的差别,在其过程中需要考虑的问题和因素也增加了很多,而不能一味的追求高性能。在实习中,我明白了生产注重的是效益,是质量与成本的有机结合。在生产中,尤其在冶炼过程中我们需要考虑的不仅仅是把铸件做出来,而是需要综合考虑原料成本,能耗等诸多因素,以图设计最佳的工艺路线,工作方法以及最优生产组织与管理,降低成本,加强质量,提高效益。
在钢炉的实习过程中,师傅给了我无微不至的关怀和细心的指导。他丰富的实践经验令人折服,一丝不苟的工作态度令人钦佩。从他身上,我看到了我们企业,我们车间师傅的工作态度和敬业精神,使我明白只有热爱本职工作,才能全身心的投入工作中,服务企业,提高自己。工作的目的,不能只是物质利益地获取,而是要学会享受工作,快乐工作。
我知道要想真正了解一个企业的内涵与文化,短短的五个月是不够的,这需要长期的深入到企业当中,深入到车间之中,为企业作出自己贡献才能更细致、更具体地了解它,解读它。
实习体会:
通过本次生产实习,使我明白了理论联系实践的重要性,使我明白了冶炼过程在生产领域的具体应用。我明白了只有把课堂所学基础理论、专业知识和基本技能合理结合,以及掌握有关技术规范、工艺流程以及工作技能,才能锻炼了我分析、解决有关冶炼实际问题的能力,从而提高我的专业综合素质,培养自己的创新精神与创造能力,为将来从事研究冶炼成型打下良好的应用基础,并且在这个基础上把所学的理论知识与实践紧密结合起来,培养实际工作能力与分析能力,以达到学以致用的目的。同时也为以后的工作打下了一定的基础,让自己更好、更快的投入工作中。
实习生:
20##-8-20