型砂实验报告单
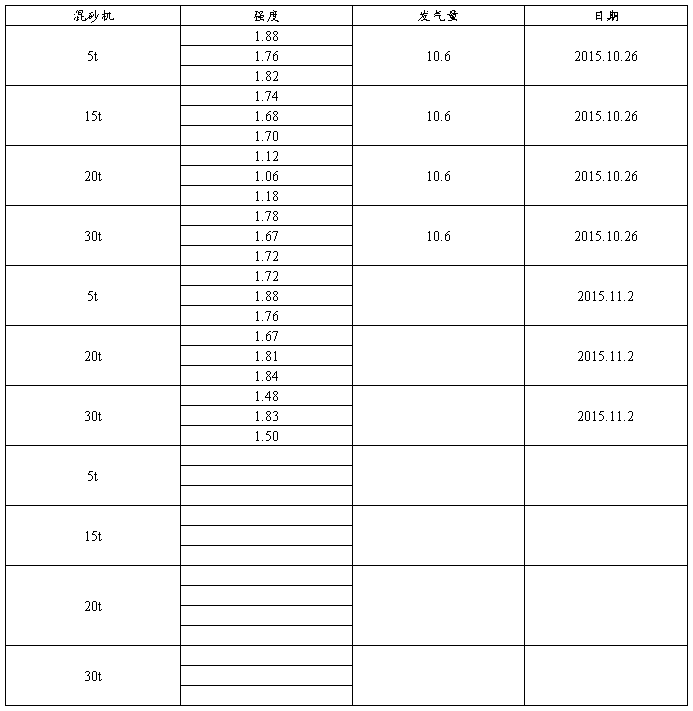
第二篇:湿型砂
半型砂箱
基本简介
高密度造型方法(或称高紧实度造型,包括多触头高压、气冲、挤压、射压、静压、真空吸压等造型方法)的生产效率高、铸件品质较好,因而国内应用日益普遍。高密度造型对型砂品质的要求比较严格。本文用表格仅列举出作者搜集的一些比较典型的国内外铸造工厂实际应用的和部分设备公司推荐的高密度砂型的型砂性能,并在以下段落中加以评论。受纸张宽度限制,只在表格中列出几种主要的和经常测定的性能。数据搜集来源一部分为近年来中外公开发行刊物,在表格最右侧注明刊物名称和出版年月或期号。另一部分是由各公司或工厂的工程师最近提供的。在表中只标明数据获得日期而不具体注明工厂名称。所列举数据只是当时情况,并不代表目前的实际状况。表中工厂编号A、B、C分别代表国外工厂(或外资厂)、合资厂、本国厂。符号中“○”—造型机处取样;“●”—混砂机处取样;“□”—型砂含泥量;“*”—旧砂含泥量。
1、紧实率和含水量
湿型砂不可太干,否则膨润土未被充分润湿,起模困难,砂型易碎,表面的耐磨强度低,铸件容易生成砂孔和冲蚀缺陷。型砂也不可太湿,过湿型砂易使铸件产生针孔、气孔、呛火、水爆炸、夹砂、粘砂等缺陷,而且型砂太粘、型砂在砂斗中搭桥、造型流动性降低,砂型的型腔表面松紧不均,还可能导致造型紧实距离过大和压头陷入砂箱边缘以内而损伤模具和砂型吃砂量过小。表明型砂干湿状态的参数有两种:紧实率和含水量。附表中国内各厂的紧实率和含水量除特别注明外,取样地点可能都在混砂机处。但是型砂紧实率和含水量的控制应以造型处取样测定为准。从混砂机运送到造型机时紧实率和含水量下降幅度因气候温度和湿度状况、运输距离、型砂温度等因素而异。如果只根据混砂机处取样检测结果控制型砂的湿度,就要增多少许以补偿紧实率和水分的损失。
多年前的观点认为手工造型和震压式机器造型造型机处最适宜干湿状态的紧实率约在45~50%;高压造型和气冲造型为40~45%;挤压造型要求流动性好,紧实率为35~40%。由表中可以看出铸件品质较好的工厂的高密度造型的型砂紧实率通常在25~45%范围内,比起当年有明显降低。这是由于高密度造型设备的起模精度提高,而且砂型各部位硬度均匀分布的要求使型砂的流动性成为重要因素。工厂的控制原则大多是只要能够保证起模,就尽量降低紧实率。比较理想的造型机处型砂紧实率集中于34~38%之间,不可高于40%,也避免低于32%。
从减少铸件气孔缺陷的角度出发,要求最适宜干湿状态下型砂的含水量尽可能低。高强度型砂的膨润土加入量多,型砂中含有多量灰分,所购入煤粉和膨润土的品质低劣而需要增大加入量,混砂机的加料顺序不良、揉捻作用不强、刮砂板磨损、混砂时间太短,以致型砂中存在多量不起粘结作用的小粘土团块,都会提高型砂的含水量。根据资料,世界各国高密度造型工厂造型机处的型砂含水量基本上都是分布在2.5~4.2%之间,比较集中于2.8~3.5%。如果生产的铸件具有大量树脂砂芯(如发动机铸件),型砂含水量大多偏于下限,这是由于大量树脂砂芯溃散后混入型砂使含泥量下降和型砂吸水量降低。
我国有些铸造工厂的型砂含水量很高:如表中C-8厂实测高达5.0%,可能与旧砂含泥量高达16.7~18.0%有关。
型砂的(紧实率)/(含水量)比值可表示每1%型砂含水量能够形成多少紧实率,最好在10~12。由几家外商独资或合资企业的检验结果计算比值大多在10~12.7范围内。曾测定三家乡镇铸造厂的比值只有5.0~8.5之间,说明型砂中吸水物质过多。
2、透气率
砂型的透气率不可过低以免浇注过程中发生呛火和铸件产生气孔缺陷。但是绝对不可理解为型砂的透气性能“越高越好”。因为透气率过高表明砂粒间孔隙较大,金属液易于渗入而造成铸件表面粗糙,还可能产生机械粘砂。所以湿型用面砂和单一砂的透气性能应控制在一个适当的范围内。对湿型砂透气率的要求需根据浇注金属的种类和温度、铸件的大小和厚薄、造型方法、是否分面砂与背砂、型砂的发气量大小、有无排气孔和排气冒口、是否上涂料和是否表面烘干等等各种因素而异。用单一砂生产中小铸件时,型砂透气性能的选择必须兼顾防止气孔与防止表面粗糙或机械粘砂两个方面。高密度造型的砂型排气较为困难,要求型砂的透气率通常稍高些。
从附表可以看出较为适当的高密度造型型砂透气率大多在100~140之间。如果型砂透气率在160以上或更高,除非在砂型表面喷涂料,否则铸件表面会出现粗糙甚至有局部机械粘砂。附表中A-2的透气率实测结果竟达250,上、下型都需喷醇基涂料。另一外资工厂的透气率不作为控制项目,偶尔测得透气率大约为200~280。观察其铸件表面相当粗糙,原因是型砂中混入大量20/40目粗粒溃碎砂芯。实际上,有很多生产发动机的铸造厂都遇到溃碎砂芯混入旧砂而使型砂透气率偏高的问题。C-13的铸件表面并不粗糙,而测得的透气率高达230~240,是仪器的通气塞孔洞尺寸过大所致。
3、湿态强度
如果型砂湿态强度不足,在起模、搬运砂型、下芯、合型等过程中,砂型有可能破损和塌落;浇注时砂型可能承受不住金属液的冲刷和冲击,而造成砂孔缺陷甚至跑火(漏铁水);浇注铁水后石墨析出会造成型壁移动而导致铸件出现疏松和胀砂缺陷。生产较大铸件的高密度砂型所用砂箱没有箱带,高强度型砂可以避免塌箱、胀箱和漏箱。无箱造型的砂型在造型后缺少砂箱支撑也需要具有一定的强度。挤压造型时顶出的砂型要推动其它造好砂型向前移动,更对型砂的强度提出了较高要求。但是,强度也不宜过高。因为高强度的型砂需要加入更多的膨润土,不但影响型砂的水分和透气性能,还会使铸件生产成本增加,而且给混砂、紧实和落砂等工序带来困难。以下文章中各种型砂强度的单位均为kPa,不再逐个标明。
3.1湿压强度
一般而言,欧洲铸造行业对铸铁用高密度造型型砂的的湿压强度值要求较高。欧洲造型机供应商推荐的湿压强度值范围在130~250之间,集中于180~220。有些日本铸造工厂对型砂湿压强度的要求偏低。除表上所列的丰田上乡和三菱川崎强度较高以外,很多工厂只有80~180。北美铸造行业的型砂强度似乎介于欧洲于日本之间。例如福特汽车厂Cleveland铸造厂排气管高压造型型砂为172,万国收割机公司Loisville铸造厂生产拖拉机缸体高压型砂为134~156。有人认为欧洲铸造工厂的型砂湿压强度比美、日两国工厂高的原因之一是由于欧洲铸铁用原砂含SiO2较高,型砂中必须加入大量膨润土才能避免铸件产生夹砂结疤缺陷。我国工厂高密度造型的型砂湿压强度比较接近美洲和日本工厂,对于铸铁件而言,除个别铸造厂以外,高密度造型的湿压强度大多在120~200范围内,比较集中在140~180。湿压强度控制值较低的优点之一是即使所使用的振动落砂机破碎效果不好,也不致有大砂块随铸件跑掉。而且很多铸造工厂所选用膨润土的品质较差,宁愿型砂的湿压强度稍低些,就无需加入大量膨润土,型砂含水量也可低些。高密度湿型铸钢需要防止铸件生成热裂缺陷,因而所用型砂的湿压强度大多在70~130之间,以降低对铸件收缩阻力。
3.2湿拉强度和湿劈强度
从材料力学角度来看,抗压强度除代表型砂粘结强度以外,也还受砂粒之间摩擦阻力的影响,而抗拉强度无此缺点。通常要求湿拉强度>20kPa。但是测定型砂的湿态抗拉强度必须使用特制的试样筒和试验机,所以很多中小铸造工厂不测定型砂的抗拉强度。有人按照混凝土试验中曾使用过的办法将圆柱形标准试样横放,使它在直径方向受压应力,就可以得出近似抗拉强度的湿态劈裂强度值。我国几家工厂的要求在30~50范围内。DISA公司推荐的湿劈强度是30~34,还给出了用劈裂强度估算抗拉强度的近似公式:湿拉强度=湿劈强度×0.65。
3.3湿剪强度
湿剪强度比湿压强度较能表明型砂的粘结力而且容易测定。国外设备公司建议的高密度造型线型砂的湿剪强度值为30~50(剪切力作用在标准试样的两端平面上)。A-5实测为52,B-1实测为38~55。另一种较新的测试方法,剪切力作用在试样圆周面上。这种仪器可以同时测出抗剪强度和剪切断裂时的变形量。两种湿剪强度数值是一致的。通常生产用型砂的变形量多在0.40~0.70mm范围内。例如A-6测得挤压造型型砂的剪切强度约为60kPa,变形量约在0.50mm。
3.4表面强度(表面耐磨性)
湿砂型应当具有足够高的表面强度,能够经受起模、清吹、下芯、浇注金属液等过程的擦磨作用。否则型腔表面砂粒受外力作用下容易脱落,可能造成铸件的表面粗糙、砂孔、粘砂等缺陷。在有些铸造工厂中,从起模到合箱之间砂型敞开放置较长时间,以致铸型表面水分不断蒸发,即“风干现象”,可能会导致表面耐磨性急剧下降。间隔时间长,天气干燥,型砂温度较高时,风干现象尤其严重。美国Dietert公司推荐利用测定造型性的圆筒筛,将两只圆柱标准试样并列放置其中,转动1min后称量掉落的砂量,用来代表型砂表面耐磨性。日本较多使用的方法是将标准试样放置在6目筛上,在震摆式筛砂机上震动60s,以震摆前、后试样重量的比率称为“表面安定度(SSI)”。例如东久公司推荐水平分型无箱射压线的型砂试样湿态即时表面安定度为>88%。该公司调查6家铸造厂的表面安定度都在88.9~91.0%范围内。土芳公司调查8家静压和气冲线在77.6~86.6%范围内,平均82.5%。我国A-1实测结果在70~89范围内;A-4实测结果是89.9~90.6%。在湿砂型喷涂表面稳定剂或涂料和在型砂中加入淀粉材料都能提高表面耐磨性。为了避免表面安定度试验的试样在筛上出现不规则的颠簸翻滚,而使掉落砂量波动。清华大学研制出的耐磨性测定装置使用钢丝针布对试样施加100g正压力刷磨表面,称量1min的磨下量即可代表湿型砂试样的表面耐磨性。用内蒙精选砂100%,天然钠基膨润土或钙基膨润土8%,α淀粉量0~1%配制型砂,紧实率按45%控制。不加α淀粉的钠基膨润土空白试样,即时磨损量约为8g,风干2h后磨损量即已增加到40g以上。加入α淀粉1%的钠基膨润土试样即时磨损量降为0.37g,风干2h后磨损量仅约为2g左右。钙基膨润土试样即时磨损量高达16g,加入α淀粉后即时磨损量降为1.8g。
4、型砂含泥量
型砂和旧砂的泥分是由有效的膨润土、煤粉以及无效的灰分组成的。一般型砂比旧砂的泥分含量多出0.5~3.0%。型砂的含泥量直接地影响型砂的各种性能的因素,旧砂的含泥量只是供参考之用。所以应当以型砂含泥量的检测和控制为主。附表中含泥量除专门注明外大概都是指旧砂而言。
大多数铸造厂的型砂和旧砂含泥量过高的原因可能是所使用的原砂、膨润土和煤粉品质不良,旧砂缺乏有效地除尘处理造成的。还有些发动机铸造工厂的型砂出现含泥量过低的现象,是旧砂中混入大量溃碎树脂砂芯造成的,以致型砂适宜含水量太低,透气率太高,性能难以控制。一些国外生产铸铁件工厂型砂含泥量的情况举例如下:美国的汽车制造厂型砂含泥量大多较低,例如InternationalHarvester生产拖拉机缸体的型砂含泥量为9~10%;GMC生产雪佛兰缸体型砂为9~11%。德国Meinheim的JohnDeere工厂的三种型砂含泥量的控制指标分别为10.0~12.5%、11.0~13.0%和11.0~13.5%;Luitpold铸造厂生产大众汽缸体用型砂为12~13.5%。日本三菱自动车川崎工厂的SPO线型砂管理标准规定含泥量为12~14%,五十铃汽车厂型砂含泥量为9.6%。几家国外铸造设备公司推荐型砂含泥量在10~13.5%范围内。我国几家外资和合资工厂的含泥量(估计均为旧砂)在9.5~13%。但有些本国工厂的旧砂含泥量偏高。例如C-8的B&P线––16.7%;北京和山东两乡镇企业的气冲线和挤压线分别为25.8%和28%。山西某纺织机厂Hunter线达16~19%。
归纳以上的数据可以得出:高密度造型最理想的铸铁用型砂(含煤粉)含泥量为10~13%,不应≥14%和≤9%;理想的旧砂含泥量为8~11%,不应≥12%和≤7%。关于型砂泥分中无效的灰分含量,德国Mettman铸造厂要求灰分不超过3.0%,国外也有人主张应当不超过3.5~5.0%。如果含泥量过高,应当加强各种原材料的选用和检验,改善旧砂除尘装置的工作效果。如果含泥量过低,就应该将除尘系统的排出物部分地返回旧砂系统中。
5、型砂粒度
型砂粒度直接影响透气性和铸件表面粗糙程度。原砂的粒度并不能代表型砂粒度,因为在铸造过程中部分砂粒可能破碎成细粉,另一部分可能烧结成粗粒。粒度较粗的砂芯溃碎后也会混入旧砂。经过多次铸造过程的积累就使型砂的粗细逐渐改变。因此很多工厂将测定过含泥量的型砂用筛分法测定粒度。国外一般认为型砂的粒度分布不可过分集中,最好是4筛分布(停留量超过10%即可算为一筛)。Buhr调查加拿大铸造厂铸件品质较好的型砂AFS细度为50~65(大致相当于50/140或140/50目),四筛分布。日本新东公司要求射压型砂粒度目标值为50~60(相当于50/100~100/50目);川崎三菱自动车作业标准58±2(大致相当于100/50目)。几家国内外资和合资工厂如A-1工厂洗后粒度48.5~51;A-4实测型砂去泥后粒度65.2;B-1实测52~54。经验表明发动机铸造工厂型砂粒度接近50/100左右的原因是有大量溃散砂芯混入。造成后果是型砂透气性可能高达180以上,砂型表面不喷涂料就会导致铸件表面粗糙,甚至出现粘砂。如果粒度过粗,最好加入特定粒度(例如100和140目两筛砂)的细粒原砂、或旋流除尘器的砂粒来调整。还有人提出停留在200目、270目和底盘的微粒含量应当为3~5%,以便降低型砂对水分的敏感性。
6、有效膨润土量
一般湿型铸造生产中,都是根据型砂实测的湿态抗压强度高低补加膨润土。如果型砂中灰分含量多而含有效膨润土量不足,也仍会显得湿压强度较高。这种型砂的性能变脆,起模性变坏,透气性下降,同样紧实率下的含水量提高。铸件容易产生夹砂、冲砂、砂孔、气孔等缺陷。自五十年代末期起美国有些人陆续通过大量有关型砂的湿压强度、含水量、紧实率和膨润土加入量关系绘制成直线和折线形成的网格图。后来又将“膨润土”改称为较为笼统的“粘结剂”。从网格图可得出总的粘结剂含量称为可用粘结剂量(AB);还又得出型砂中真正起着粘结砂粒作用的粘结剂量称为工作粘结剂量(WB)。又从网格图推导出AB和WB的两个计算式。我国有个别外资铸造工厂也引用这些计算式,例如A-2高压造型用型砂计算得出:AB=8.1~8.3%,WB=4.3~4.7%。到80年代末期起,美国有人考虑到湿型砂中大多数含有煤粉,膨润土含量已超过绘图时的5~7%,而且钠基膨润土和钙基膨润土是按不同比例掺合使用,混碾效率有所提高,所绘制出的网格图是由极为复杂的曲线形成的,已不能用简单的数学式计算出AB和WB。此外,各国的膨润土和原砂资源各异,更难于简单地利用前述的网格图和计算公式。从上世纪六、七十年代起,国内外大多数工厂已开始改用亚甲基蓝吸附量检验型砂的有效膨润土含量。
型砂中最适宜的有效膨润土含量不仅取决于对型砂湿态强度的要求如何,所用膨润土的品质如何,也还受型砂中的膨润土是否混合均匀的影响。因此各厂型砂的有效膨润土含量都有相当大的差异。例如国外造型机设备公司要求高密度造型的型砂有效膨润土含量6~9%。我国使用一般品质膨润土的本国工厂大多为8~11%,而使用优质膨润土的型砂有效膨润土量可以降低到6~7%。我国膨润土的品质相差悬殊,测得有效膨润土量(%)并不能直接说明型砂的粘结强度,不如用吸蓝量表示。例如有的工厂要求高密度型砂的吸蓝量为55~65mL。
当年作者将亚甲基蓝溶液浓度定为0.2%时,通常的型砂吸蓝量都不超过40mL。如今高密度造型型砂的亚甲基蓝溶液的滴定量都超过了50mL滴定管的容积。因此,建议可将型砂试料量缩减成2.50g,将测得滴定量乘以2即可得出试料量5.00g时的滴定量。我国有些外资企业采用美国AFS标准的亚甲基蓝溶液浓度0.374%,例如A-1静压型砂要求吸蓝量为30±1mL,如亚甲基蓝浓度按0.20%计算,测定出的吸蓝量乘以0.374/0.200,即乘以1.87。要求应为54.4~58.1mL。A-7工厂实测的高压型砂滴定量为31~33.5mL,如亚甲基蓝溶液浓度按照0.20%计算应为58.1~62.8mL。
型砂的有效膨润土是指全部仍然具有粘结能力的膨润土而言。生产用型砂中有一部分膨润土自己积聚成粘土团或砂豆,成为对型砂不起粘结作用的“潜在膨润土”。主要形成原因是型砂制备时混合不均匀。美国有人将前面所述的工作粘土量(WB)除以可利用粘土量(AB)做为混砂机效率,也用来说明型砂的膨润土利用率,即起粘结作用的膨润土占膨润土总量的比率有多少,认为通常在55~65%。A-2计算得出的混砂机效率为52.6~56.6%。作者推荐的方法是取铸造工厂现用的型砂,在实验室小混砂机中先将紧实率调整成45±2%,测定其湿态强度。然后每次继续混碾1min,同时补充加水少许以保持型砂紧实率稳定不变,直到湿态强度不再升高为止,即达到“峰值强度”为止。混砂机的混砂效率可以按下式计算:混砂机的混砂效率(%)=实际混砂强度/型砂峰值强度×100。
7、型砂的有效煤粉量和灼减量
生产铸铁件的湿型砂大多加入煤粉,但是每次混砂时煤粉的补加量需要靠型砂和旧砂的有效煤粉量差值来确定。因此必须采取既方便、又准确的检测方法测定出型砂有效煤粉量。国外靠测定型砂或旧砂的的灼减量(通常简写为LOI,美国又称为可燃物总量)、挥发分、含碳量,固定碳量等参数推测有效煤粉量。我国几家外资和合资企业的型砂灼减量如下:B-1高压造型要求4.0~5.5%;A-3的FBM造型用型砂目标值为2.5~4.5%;A-7挤压型砂实测为4.4~4.6%。A-5的FBM造型和A-4挤压造型的灼减量分别为3.7%和2.0~2.2%,挥发分为3.06%和1.4%。A-1规定面砂和背砂的灼减量分别为4.10±0.30%和3.80±0.30%,总碳量分别为3.00±0.50%和2.80±0.50%。但是各国规定的灼减量和挥发分测试规范有很大差别,而且都不能明确说明型砂中有效煤粉到底有多少百分数。当年作者认为煤粉起抗粘砂作用主要靠挥发分而不是固定碳或灼减量。因而采用反映型砂中挥发分的发气量来测定有效煤粉量。目前有的国內工厂没有发气量测定仪器,也使用灼减量估计型砂中煤粉量。
铸铁件型砂中应有的有效煤粉量因铸件大小和厚薄、浇注温度、面砂或单一砂等因素而异。更重要的是因煤粉品质不同而异。例如,应用普通煤粉的高密度造型的型砂中有效煤粉量多为5~7%,应用较高品质煤粉的有效煤粉量可降低到4~5%。如果使用高效煤粉只要3~4%即可。目前我国各地销售供应的煤粉品质差异较大,有的煤粉中杂质甚多,发气量较低。高密度造型用型砂发气量大体应在14~24mL。例如天津某合资厂静压线型砂实测为16mL。有些型砂中还含有淀粉类材料或混有溃散芯砂,也都起抗粘砂作用和发生气体,可以和煤粉一并考虑。还应注意个别煤粉是用挥发分相当高的气煤或长焰煤制成的。配制出型砂的发气量虽高但其抗粘砂能力较差,而且铸件易出气孔缺陷。因此,用发气量控制型砂和旧砂中有效煤粉量的方法适合用于挥发分28~37%和灰分≤10%范围内的煤粉。
国外靠测定型砂或旧砂的的灼减量(简写为LOI,美国又称为可燃物总量)、挥发分、含碳量,固定碳量等参数做为推测有效煤粉量的参考。美国铸造学会编著的“型砂试验手册”书中规定将烘干的型砂10g盛入试料瓷皿中,放入马福炉逐渐升温至1800F(982℃)保持2h后,称量并计算出烧掉或挥发掉材料占原重量的百分比即为灼减量。挥发分的测定方法为将50g干燥型砂盛入坩埚中,加盖后置入温度已达900F(482℃)或1200F(649℃)炉中加热1h后,称量并计算出挥发分的百分比。通常认为铸铁件湿型砂在649℃时的挥发分为1.5~2.5%,982℃灼减量为3.0~4.5%,其有效煤粉量就是在适宜范围内。德国铸造学会规定的灼减量测定方法是称取预先在105℃烘干的试料约5g(精度0.01g),放入经过焙烧和称重的瓷坩锅中,在850℃的氧化气氛中灼烧至恒重(至少需3h)。冷却后称量和计算出试料重量减少量占原来重量的百分率。DISA公司推荐型砂的灼减量为3.5~7.5%,挥发分为1.5~3.0%。GF公司建议生产后桥球铁件灼减量为4.7%。Levelink认为通常型砂的灼减量为4~6%。Fahn调查欧洲一百余铸铁工厂的灼减量在1.6~11.6%范围内,平均值为5.3%。Buhr调查了加拿大76家铸造工厂,其中铸件品质较好的灼减量在2~5%之间。Berndt记述四铸造厂的灼减量在3.3~4.47%范围内。日本土芳公司调查8家静压和气冲造型的灼减量在1.98~4.46%范围内,平均3.29%,三菱自动车为5.0±0.5%。德国Luitpold生产大众汽车汽缸体型砂为3.6~4.0%;美国JohnDeere生产缸体和缸头高压造型为3.8~4.5%,泵阀用砂为3.0~3.5%;通用汽车公司Pontiac厂型砂则为4.0~4.5%。我国几家三资企业的型砂灼减量如下:烟台大宇动力冲击造型要求3~5%;山西国际高压造型要求4.0~5.5%;昆山富士和FBM造型用型砂目标值为2.5~4.5%;常州小松常林挤压型砂实测为4.4~4.6%。天津新伟祥FBM造型和勤美达挤压造型的实测灼减量分别为3.7%和2.0~2.2%,挥发分为3.06%和0.8%。日本丰田汽车厂要求测定型砂灼减量(1000℃空气中燃烧1h的减少重量)和固定碳量(灼减量减去1000℃密闭容器加热3min测得的挥发分量)。江苏某日资汽车件铸造厂规定面砂和背砂的灼减量分别为4.10±0.30%和3.80±0.30%,总碳量分别为3.00±0.50%和2.80±0.50%。虽然测得结果很难与有效煤粉含量建立明确关系,而且测定需时较长,大约需3h左右,但所需仪器和工具在化学分析室中都有,仍不失为有效控制方法。
8、热湿拉强度
国内外很多铸造工厂都用热湿拉强度来检验型砂的抗夹砂性能。影响型砂热湿拉强度的最主要因素是膨润土所吸附阳离子的种类,其次是膨润土纯度和型砂中有效膨润土含量。天然钠土和活化土的热湿拉强度比钙基膨润土高几倍。然而用碳酸钠活化钙土超过极限活化量后热湿拉强度反而下降,而且还可能会形成热粘砂。我国常用钙土的极限活化量是碳酸钠加入量4~5%。对型砂热湿拉强度值的要求需根据生产条件而定。美国汽车铸铁件工厂考虑到混砂、造型和落砂的需要将怀俄明天然钠土和美国南部钙土比例按2:1掺合应用;生产小铸铁件所用膨润土按1:1比例掺和。相当于在我国将钙土的碳酸钠加入量分别为极限活化量的67%和50%左右。在欧洲,普通铸铁件高密度造型用型砂的热湿拉强度大约为1.5~2.5kPa,对于较敏感的铸件可能要求>2.5kPa。例如,德国Luitpold铸造厂生产大众汽缸体型砂的热湿拉强度为2.7~3.0kPa;Benz公司的Esslingen铸造厂用BMD无箱射压造型机生产制动鼓的型砂热湿拉强度为2.8kPa。Hofmann实测五家使用气冲造型机铸造厂的型砂为1.35~3.7kPa。DISA公司推荐挤压造型用型砂的热湿拉强度应>2.0kPa。我国铸铁生产所用原砂的SiO2不高,型砂中还加入了煤粉,生成的热压应力较低,可放宽对热湿拉强度的要求。几家生产汽车和柴油机发动机铸造工厂的型砂热湿拉强度大多在1.6~3.0kPa之间。也有些生产形状简单小件、薄壁件的工厂只从是否生成夹砂缺陷考虑,型砂热湿拉强度极低,例如山西某纺织机械厂的Hunter造型机用型砂的热湿拉强度只要求>0.9kPa,仅只使用钙土似乎已然足够。但是高密度造型还考虑到钠土和活化土的热稳定性高和不易烧损,应当使用适当活化的膨润土。
9、型砂韧性和起模性
9.1型砂韧性
型砂应当具有一定的韧性。否则在起模、下芯、合型和运搬时砂型的棱角和吊砂受到冲击和震动容易碰碎或掉落。但型砂韧性也不应太高,以免其流动性下降而影响砂型的紧实均匀程度。强度代表将物体破坏所需施加的力大小如何;而韧性代表的是将物体破坏所需做的功大小如何,它包含了强度和变形量两种参数。早年美国有人曾用下列公式似地计算使试样破碎所做的功来表示韧性:型砂韧性=湿压强度×变形量×1000,式中的湿压强度单位为磅/平方英寸,变形量单位为英寸。但靠眼睛观看试验机上附带千分表是不可能准确读出达到强度最大值时的变形量。60年代末期美国Dietert等人研制出落球式破碎指数测定仪,用来检测型砂韧性。我国仿制的仪器存在网孔宽度稍窄和钢球滚落筛网上等问题。仪器工厂为防止钢球滚落而震碎砂块,将具有三根直立细钢丝的钢环套在铁砧上来防止落下的钢球滚动。虽然尚无有关标准,但不失为良好的解决方案。清华大学的研究表明,将网孔中心尺寸由10mm增大到12.7~14mm,则可使常用型砂破碎指数的变化范围扩大一倍以上。将砧座厚度减薄到不超过3mm,注意调整测定仪的垂直度,不加钢丝也可以防止钢球滚落到筛网上。几家国内铸造厂高密度造型的型砂破碎指数大多集中在75~85%范围内。
9.2起模性
型砂的起模性指的是起模时砂型的棱角、边缘和砂台不破碎的性能。当型砂的膨润土量、紧实率、糊精加入量等有利于起模的参数提高时,试样的破碎指数也随之提高。但是砂型的紧实程度越高就越难起模,而型砂的破碎指数仍随紧实程度提高。因此破碎指数不能完全代表砂型的起模性。型砂的起模性是一个综合复杂的特性,假定模样的材质、起模斜度、表面粗糙度、清洁度、与型砂的温度差异、脱模剂有无和种类、是否形成真空等因素都不变,则砂型的起模难易除了取决于型砂抗拉、抗剪强度和韧性以外,也还取决于型砂的变形量和砂型与模样间的摩擦阻力和粘附力。
9.2.1变形量
手工造型起模前在围绕模样的砂型棱角上刷水,虽然使局部的砂型各种强度剧烈下降,但能够大大改善起模性能。刷水的作用主要是提高了砂型棱角和吊砂型砂的变形能力,起模时受模样水平方向振击和碰撞能够退让变形,就能避免砂型棱角破损。因而型砂破碎前的变形量也是表达型砂起模性能的重要参数。清华大学新研制的剪切强度与变形测定仪和气动湿压强度仪是由压力传感器、位移传感器、微型计算机和打印机组成的。不仅能够用液晶显示试样的强度,而且能够精确记录下型砂试样破坏时的变形量。也还可以推算出型砂的韧性。
9.2.2试样顶出阻力
在液压式强度试验机上安装一个附加装置,测定使型砂试样在试样筒中受顶推作用而开始移动的力称为顶出阻力,它是起模时砂型与模样之间的摩擦阻力和粘附力的综合表现。试验结果表明,型砂的湿压强度越高,顶出阻力也高。型砂中加有煤粉、淀粉,试样筒表面涂有硅油,都能降低顶出阻力。清华大学研究表明型砂的膨润土含量对试样顶出阻力仅有不大的影响。而提高紧实率和减少试样冲击次数都能降低试样的顶出阻力。研究结果还表明,型砂中加入糊精或α-淀粉可使型砂对模样的摩擦阻力极为减小到原来的1/3~1/2,对起模尤其有利。
10、型砂流动性和可紧实性
型砂的颗粒在外力作用下可以紧密靠近的性能称为可紧实性。型砂在外力作用下质点可以自由地越过模样的边角,通过狭窄缝隙和孔洞的性能称为流动性。具有良好可紧实性和流动性的型砂能保证高密度砂型的硬度分布均匀,棱角、凸台清晰无疏松,铸件表面光洁和无局部机械粘砂。然而各种不同紧实方法所要求的可紧实性和流动性都有不同,至今没有标准测试方法。本文仅介绍几种使用稍多的试验方法如下:
10.1试样硬度差法
Kyle提出将型砂过筛使它均匀分散,称取170g置入圆柱形标准试样筒中。用锤击式制样机冲击一次后,顶出试样,用湿型硬度计测量试样两端的硬度。硬度差别越小,说明其可紧实性越好。
10.2试样冲击阻力法
将冲击Φ50×50mm标准试样所需型砂量置入试样筒中,放到制样机下用重锤冲击。第三次冲击前后的试样高度差(mm)越小,表示冲击阻力低。这就是日资铸造工厂所测定的型砂“抗缩值”。A-1要求面砂抗缩值为1.30±0.15mm;A-3实测为1.1~1.2mm。
10.3阶梯试样硬度差法
在圆柱形标准试样筒中放置高度为25mm的半圆形金属块。将110~120g型砂放入试样筒中,用制样机冲击三次。测定试样筒底盖端面和金属块端面的试样硬度。二者的硬度值差别越小,说明型砂向空隙中移动的流动性越好。
10.4环形空腔法
为GF公司型砂仪器中一种测定型砂流动性的附件。先将型砂冲制成圆柱形标准试样,并称量其重量。再按此重量称取型砂,置入专门的环形空腔试样筒中,在制样机上冲击3次。测量试样的高度,高度越小,表示型砂向侧面空腔的流动性越好
10.5试样重量法
①称量测定型砂紧实率后的试样重量,可反映不同型砂在松散状态下流动的性能,可称为松散流动性。将紧实率试样重除以试样筒容积235.62cm3可得型砂的堆密度,德国Rexroth要求堆密度为0.86~0.94g/cm3。②称量Φ50×50mm标准圆柱试样的重量,可反映不同型砂在紧实过程中的可紧实性。德国Rexroth公司规定为148~150g。我国A-5规定为145~155g;A-7实测为144~145g;B-1实测147~148g。如果标准试样重量较低(例如C-8只有135g),估计其原因是型砂中灰分过多。
湿型砂的流动性和可紧实性除了受紧实率影响外,原砂的颗粒形状对型砂也有明显影响。如果湿型砂的膨润土含量和紧实率不变,用椭圆形内蒙砂混制型砂的标准试样重量比用方角形新会砂大约重10g左右。A-3用内蒙砂替代福建砂后发现不但型砂流动性提高,而且含水量也有下降。型砂经过松砂处理可以减少团块和提高可紧实性。提高型砂的膨润土量或加入糊精能够提高型砂韧性,但都会使流动性和可紧实性下降。
结束语
以上各段所述的高密度砂型的型砂性能是生产高品质铸件需要控制的项目。具体的检测技术可按照专门的标准、手册等资料。
为了准确反映型砂的真实性能和及时得到控制,铸造工厂的型砂实验员应当亲自按规定频率取样,然后进行检验,随时记录测定结果。用图表绘制出每日各种性能的变化趋势图。如有特殊情况就可立即采取相应措施。高密度砂型的型砂检测频率可以分为以下三类:
①随时性检验:为一日之内多次检验的项目,包括紧实率、含水量、透气性、湿压强度、标准试样重量。一个具有良好旧砂冷却和混砂湿度自动控制设备的工厂,铸件厚薄和砂芯数量相近或者能够合理搭配的条件下,型砂随时性检测频率每班两次可能已够。否则可能需要每班检测4次以上。
②逐日性检验:为一天或两三天检验一次的项目,包括有效膨润土量、有效煤粉量、热湿拉强度、韧性。
③周期性检验:为一两周检验一次的项目,包括含泥量、型砂粒度、团块量。