实践报告
常减压、催化、焦化相关知识
专业: 检测技术及应用 班级:检测0931
姓名: 日期:20##年6月
前言
很有幸能在20##年的八月份成为宝来北方沥青的一名成员。在这里的十个月的时间里。我学到了很多在学校没有学习到的知识。体会到了自己身上的不足,随着时代的日益进步对我们新一代毕业生也将是一个严峻的考验,没有全面的知识很难再自己的岗位上发挥自己的力量。已经走出校园的我们只能在工作中慢慢的学习让自己尽快的成长起来,毕业前夕的实习就成为非常重要阶段,认识到自己的不足,弥补自己的不足,进一步的玩的完善自己,理论结合实际把自己打造成全能行的人才,去适应整个社会的发展,为自己的将来打下坚实的基础。接下来我把其中一部分整理成了这篇报告和大家一起分享。
实习单位:
盘锦北方沥青燃料有限公司坐落在盘锦市大洼县辽滨开发区工业园内,交通便利,是辽宁省第二大公路交通枢纽,与沈大、京沈、盘海等多条高速公路相连;沟海铁路、京沈高速铁路从盘锦经过。距大连港、营口鲅鱼圈港、锦州港、盘锦港等港口距离很近,其中距盘锦港仅五公里,海上运输十分方便。距沈阳桃仙国际机场、大连机场仅两小时路程。
公司成立于20##年,是由辽宁宝来投资有限公司与盘锦北方沥青股份有限公司合资组建的股份制企业。现辽滨开发区项目占地面积约1700亩,可用规划预留地3000亩,于20##年二月开始建设, 20##年八月份实现一期全部装置一次投料试车成功至今,正在运行的一期装置有一套150万吨/年重交道路沥青装置、一套150万吨/年延迟焦化装置、一套100万吨/年加氢精致装置、一套50万吨/年加氢裂化装置、一套20000Nm/h干气制氢装置、一套3万吨/年硫磺回收装置及配套公用工程和30万吨原料、成品罐区;
二期工程装置现已经进入工艺配管阶段,计划在今年八月份投料试车,包括两套150万吨/年重交道路沥青装置、一套60万吨/年FDFCC重油催化裂化装置、一套60万吨/年加氢裂化装置、一套10万吨/年芳构化,一套20000Nm/h干气制氢装置及新增40万吨罐区,装置达产后一、二期装置能力如下附表。
三期工程为一套30万吨/年食品级润滑油加氢装置,主要目的是将生产沥青装置副产的减线蜡油经过高压加氢处理,将其转化为食品级润滑油及SPS级光亮油,该装置由大连化工设计院设计,北京石油科学研究院出工程设计工艺包。现在长周期设备订货已经结束,计划20##年八月份投料试车。
综上所述,到今年八月份,我公司原油总加工能力到达450万吨/年,主导产品为重交道路沥青、丙烯、车用液化气、化工轻油、变压器油、石油焦、石油针状焦、各类芳烃及硫磺等。实现年销售收入400亿元人民币。
实习目的:
熟练掌握各项石化工人的专业技能及相关知识,能良好的操作各项设备,以及各项安全知识。了解整个厂区装置的流程,熟记各项生产工艺和生产流程,牢记流程图。掌握调度员的工作性质,要求与责任:
1.认真做好生产调度会记录,落实并督办调度会提出的问题,详细做好督办记录,准确无误传达各项生产指令并做好记录。
2.了解公司的生产经营动态,及时向上级主管领导汇报,并做好跟踪记录。
3.协调并处理好生产中出现的问题,做好水,电,汽的平衡调度工作。
4.了解掌握各生产车间的生产情况,工艺指标情况及各车间生产进度和生产安排,发现问题及时向主管领导汇报。
5.负责每日统计原料加工量,各成品质量,收率及销售量并做好数据统计与记录。
6.协调好生产车间及外界有关部门的工作关系。
7.及时完成调度室主任及主管领导交办的其他工作。
第一章 常减压、催化装置
1.1常减压蒸馏装置
常减压蒸馏的原理是精馏,即在常压和减压的条件下,根据各组分相对挥发度的不同,在塔盘上汽液两相进行逆向接触、传质传热,经过多次汽化和多次冷凝,将原油中的汽、煤、柴馏分切割出来,生产合格的汽油、煤油、柴油及蜡油及渣油等。它的装置是以“三塔两炉”为核心的。三塔指初馏塔、常压塔、减压塔;两炉则是常压炉和减压炉。常减压蒸馏被认为是石油加工的“龙头装置”,之所以如此重要,原因是后续二次加工装置的原料和产品都是由常减压蒸馏装置提供,可以说如果常减压装置停工,那么整个化工厂也只得停止生产。石油蒸馏与连续精馏相比具有显著特点。一是石油的蒸馏并不需要分离出纯组分,而是收集一定沸点的混合流出物;二是石油蒸馏过程中出料油品的分离需要通过汽提塔来实现。我们从师傅介绍中知道了宝来公司的三套常减压蒸馏装置能力为850万吨/年,每年可向社会提供汽油、柴油、煤油、润滑油、石蜡等33个品种75个牌号的石油化工产品;其中全精炼石蜡、60号食品蜡、石油甲苯、导热油等产品获得国家金奖或银奖;有27种产品曾获国家、部、市级优质产品称号,他们的产品畅销全国各地,享有很高的声誉。
1.2催化裂化装置
催化裂化是实现二次加工的重要方法之一。它的原理较为复杂,其中5种最为常见,分别是断裂反应、异构化反应、芳烃化反应、氢转移反应和叠合缩合反应。总反应呈吸热趋势。催化的过程可分为反应、分馏、稳定。反应过程需要两个部件来完成,即反应器和再生器。反应器的作用是进行裂化并使裂化后产品与催化剂分离。新鲜原料(减压馏分油)经过一系列换热后与回炼油混合,进入加热炉预热到370℃左右,由原料油喷嘴以雾化状态喷入提升管反应器下部,油浆不经加热直接进入提升管,与来自再生器的高温(约650℃~700℃)催化剂接触并立即汽化,油气与雾化蒸汽及预提升蒸汽一起携带着催化剂以7米/秒~8米/秒的高线速通过提升管,经快速分离器分离后,大部分催化剂被分出落入沉降器下部,油气携带少量催化剂经两级旋风分离器分出夹带的催化剂后进入分馏系统。由于催化剂表面的焦质燃烧,使得催化剂失活,为了使催化剂活化就需要再生器发挥作用。积有焦炭的催化剂由沉降器进入其下面的汽提段,用过热蒸汽进行汽提以脱除吸附在催化剂表面上的少量油气。再生后的催化剂经过淹流管、再生斜管及再生单动滑阀返回提升管反应器循环使用。分馏系统的作用是将反应过程的产物进行分离,得到部分产品和半成品的步骤。由反应过程来的高温油气进入催化分馏塔下部,经脱过热段后进入分馏段,经分馏后得到富气、粗汽油、轻柴油、重柴油、回炼油和油浆。富气和粗汽油稍后进入吸收系统;轻、重柴油为成品油,回炼油返回反应––再生系统进行回炼。油浆的一部分送回反应系统回炼,另一部分经换热后循环回到分馏塔。从分馏塔顶油气分离器出来的富气中带有汽油组分,而粗汽油中则溶解有C3、C4甚至C2组分。吸收系统的作用就是利用吸收和精馏的方法将富气和粗汽油分离成干气(≤C2)、液化气(C3、C4)和蒸汽压合格的稳定汽油。
1.3裂解
裂解的关键装置是裂解炉。轻柴油、石脑油、加氢尾油和循环乙烷经预热后,在裂解炉内裂解,原料在进炉前加入稀释蒸汽,自裂解炉出来的裂解气在相应的废热锅炉中被冷却至400~550℃,并同时产生压力约为12.0MPa的超高压蒸汽。从废热锅炉出来的混合裂解气用循环急冷油冷却后进入汽油分离塔,在塔中将进料分离为塔底的循环和一个侧线馏分。急冷的关键装置是急冷水塔。自汽油分馏塔出来的气体入急冷水塔,用水急冷至40℃后去裂解气压缩机,急冷塔底液体经沉降分为急冷水和碳氢化合物两相液层,急冷水经热量回收后循环使用,分出的冷凝轻质碳氢化合物,一部分作汽油分馏塔回流,另一部分进入汽油汽提塔,汽提出轻组分后,由塔底得到裂解汽油,送出与脱丁烷塔的釜液混和经冷却后作为裂解汽油产品送出。压缩的关键装置是压缩机。急冷塔顶出来的裂解气入蒸汽透平驱动的五段离心式压缩机压缩至3.658MPa,在第三段和第四段间气体经过一个碱洗水塔,以除去裂解气中的H2S、CO2等酸性气体。脱甲烷、脱乙烷和乙烯精制、脱丙烷和脱丁烷及丙烯精馏的过程均为裂解分离过程这套装置具有七个明显的特点:一、工艺流程总体格局呈“两头一尾”;二、工艺技术路线采用管式炉蒸汽裂解、顺序分离流程;三、装置全部采用DCS控制,压缩机采用电子调速器控制;四、改造的裂解炉采用KTI 6万吨/年的GK-V型裂解炉,新建裂解炉为中石化和LUMMUS合作开发的10万吨裂解炉(SL-I型);五、在世界乙烯工业中首次采用了二元制冷技术和催化精馏技术;六、在裂解气压缩机上采用了注水工艺,在制冷压缩机上采用了干气密封技术;七、在塔器上采用多种高效填料,提高了塔的生产能力和分离效率。
第二章 常减压蒸馏装置的减压拔出
现状和改进措施
2.1现状
常压系统的拔出率对减压深拔的影响很大,应根据加工原油性质的变化尽可能地提高常压塔的拔出率,降低常压渣油中350oC含量到4%以下。主要措施有控制合理的过汽化率,提高常压炉出口温度、降低常压塔顶压力、调整常压塔底吹汽量和侧线汽提蒸汽量、提高常压侧线的拔出量(尤其是常压最下侧线)。在拥有相关工具软件的情况下,应根据加热炉的设计参数和进料性质进行模拟计算,绘制加热炉的结焦曲线,以模拟结果为指导逐步提高炉温;即使没有炉管结焦曲线的模拟软件,也可小幅提高炉温并增大炉管注汽,观察减压塔操作工况确定合适的炉温并维持操作,首先要达到设计温度,在此基础上再增加炉管注汽,继续提温优化减压塔顶抽空器和抽空冷却器的运行,减少抽空系统泄露,保证塔顶真空度。要确保洗涤段底部填料保持润湿,即合理的喷淋密度能够保证总拔出率和减压馏分油的质量,洗涤段操作效果好,可以降低过汽化率,在同样的烃分压和蜡油质量的前提条件下可以提高拔出率。为提高装置总拔出率,减压塔的取热可作适当调整,降低减压塔下部中段回流取热量,以增加减压塔上部气相负荷。投用减压塔底急冷油流程,控制塔底温度不超过370oC即可,过多的急冷油量会影响塔底的换热效率。
2.2提高减压系统拔出率应注意的事项
应根据减压渣油的加工流向确定是否适合深拔操作,减压渣油作延迟焦化原料和减压渣油虽作催化裂化原料,但由于催化消化不完还有减压渣油作燃料油或外售的蒸馏装置。
原油实沸点切割达到565oC时,减压塔最下侧线的干点必然在580oC以上,若有携带现象还将导致蜡油中的沥青质和重金属含量上升,可能会给加氢裂化装置带来操作问题,建议实施深拔后重新考虑重蜡油的流程走向,由现在的进加氢裂化改进蜡油加氢处理或催化裂化装置等。
减压拔出深度的提高需要高的炉出口温度、高的进料段真空度,还需要增加注汽量和增设急冷油流程等,蒸馏装置的能耗相应会有所上升,但从全炼厂角度,减压深拔操作能实现节能和增效的双重收益。
第三章 常减压装置的介绍及安全操作
3.1安全操作
常减压装置是将原油经初馏塔、常压塔和减压塔进行常、减压蒸馏,生产石脑油、轻柴油、柴油、馏分油、渣油等油品的炼油装置。常减压装置主要包括原油电脱盐、常减压工序等部分。全过程的易燃、易爆、易中毒和加热炉易结焦等是装置操作的主要安全要点。
3.1.1认真巡回检查,及时发现和消除炉、塔、贮槽等设备管线的跑、冒、滴、漏。禁止乱排乱放各种油品和可燃气体,防止火灾发生。
常减压蒸馏过程中许多高温油品一旦泄漏,遇空气会立即自燃着火,火灾危险很大。造成热油跑料着火的原因主要有:
法兰垫刺开跑料;
年久腐蚀漏油;
液面计、热电偶套管等漏油着火;
原油含水多,塔内压力过高,安全阀起跳喷油着火;
减压操作不当,空气进入减压塔内引起火灾爆炸;
压力过大,造成爆炸着火;(风险管理世界网-安全员之家)
压力和真空度剧烈变化引起漏油等。
3.1.2火灾现场处理方法:
初期火灾可用蒸汽或石棉布扑盖火源,或用干粉灭火器灭火;
减压塔火灾要向塔内吹人蒸汽,恢复常压。不允许在负压系统管线上动火堵漏;
火势大时要立即通知消防队灭火。并紧急停车,将塔内油抽空。
3.1.3加热炉结焦处理
加热炉内油品温度高、油晶轻、组分复杂。如果加热炉进料量和炉温度控制不当,或仪表温度测量指示、仪表流量控制指示不准,都会导致炉管结焦。炉管结焦不仅影响传热,严重时还会堵塞以致烧毁炉管,爆炸着火。尤其是常压炉分四路进料,加热后又合为一路去常压塔;减压炉分两路进料,加热后也合为一路去减压塔。如果各支路的进料量不平衡,易局部超温而加快炉管结焦。针对加热炉的这些特点,操作中应特别注意以下问题:
加热炉各支路进料量均衡,严防偏烧。如各支路间进料量不平衡,有的支路就会因进料量少,减缓或停止管内油品流动,使炉管局部超温结焦,烧坏炉管。
平衡好各塔底液面,稳定加热炉的进料流量。
不论是正常停车,还是异常情况下的紧急停车,加热炉进料降量时要维护局部循环,必须保证炉管内的油品流动,以防炉管结焦烧坏。
正常停炉要严格按规定程序进行,同时应特别注意控制加热炉的原油降量速度和降温速度;加热炉停止进油之后仍要改为热循环,并注意维持三塔液面平衡;常压炉降温至250℃,减压炉降温至230℃时,炉子全部熄火。炉膛温度降到200℃时,自然通风降温;加热炉熄火后继续冷循环降温到90℃时开始退油。
加热炉紧急停车时也应该注意:熄火后要向炉膛吹入适当蒸汽,尽量保证炉膛温度不要下降太快;减压塔恢复常压时,末级抽真空器放空阀要关闭,严防空气倒入减压塔;尽快退走设备内存油,但要尽量维护局部循环,防止超温超压。
3.1.4加热炉回火
炉子回火是发生操作事故的主要原因之一。加热炉回火原因主要有如下几个方面:
燃料油大量喷入炉内或瓦斯带油。
烟道气挡板开度过小,降低了炉子抽力,烟气排不出去。
炉子超负荷运行,烟气来不及排放。
升温点火时瓦斯阀门不严,瓦斯窜入炉内,造成炉膛爆炸着火。
加热炉回火时首先要及时打开炉子垂直挡板,然后熄火,待查明回火原因,处理后重新点火。
3.2装置简介
常减压装置是常压蒸馏和减压蒸馏两个装置的总称,因为两个装置通常在一起,故称为常减压装置。主要包括三个工序:原油的脱盐、脱水;常压蒸馏;减压蒸馏。从油田送往炼油厂的原油往往含盐(主要是氧化物)带水(溶于油或呈乳化状态),可导致设备的腐蚀,在设备内壁结垢和影响成品油的组成,需在加工前脱除。
编辑本段基本原理
电脱盐基本原理:为了脱掉原油中的盐份,要注入一定数量的新鲜水,使原油中的盐充分溶解于水中,形成石油与水的乳化液。 在强弱电场与破乳剂的作用下,破坏了乳化液的保护膜,使水滴由小变大,不断聚合形成较大的水滴,借助于重力与电场的作用沉降下来与油分离,因为盐溶于水,所以脱水的过程也就是脱盐的过程。 常压蒸馏和减压蒸馏都属物理过程,经脱盐、脱水的混合原料油加热后在蒸馏塔里,根据其沸点的不同,从塔顶到塔底分成沸点不同的油品,即为馏分,这些馏分油有的经调和、加添加剂后以产品形式出厂,绝大多是作为二次加工装置的原料,因此,常减压蒸馏又称为原油的一次加工。
3.3编辑本段主要设备
电脱盐罐 其主要部件为原油分配器与电级板。
原油分配器的作用是使从底部进入的原油通过分配器后能够均匀地垂直向上流动,目的一般采用低速槽型分配器。电极板一般有水平和垂直两种形式。交流电脱盐罐常采用水平电极板,交直流脱盐罐则采用垂直电极板。水平电极板往往为两至三层。
防爆高阻抗变压器 变压器是电脱盐设备的关键设备。
混合设施。
油、水、破乳剂进脱盐罐前应充分混合,使水和破乳剂在原油中尽量分散到合适的浓度。一般来说,分散细,脱盐率高;但分散过细时可形成稳定乳化液反而使脱盐率下降。脱盐设备多用静态混合器与可调差压的混合阀串联来达到上述目的。
3.4常压减压蒸馏原理
常压蒸馏原理:
精馏又称分馏,它是在精馏塔内同时进行的液体多次部分汽化和汽体多次部分冷凝的过程。
原油之所以能够利用分馏的方法进行分离,其根本原因在于原油内部的各组分的沸点不同。在原油加工过程中,把原油加热到360~370℃左右进入常压分馏塔,在汽化段进行部分汽化,其中汽油、煤油、轻柴油、重柴油这些较低沸点的馏分优先汽化成为气体,而蜡油、渣油仍为液体。
减压蒸馏原理:
液体沸腾必要条件是蒸汽压必须等于外界压力。降低外界压力就相当于降低液体的沸点。压力愈小,沸点降的愈低。如果蒸馏过程的压力低于大气压以下进行,这种过程称为减压蒸馏。常减压装置的主要设备为:塔和炉。塔是整个装置的工艺过程的核心,原油在分馏塔中通过传质传热实现分馏作用,最终将原油分离成不同组分的产品。最常见的常减压装置流程为三段气化流程或称为“两炉三塔流程”,常减压中的塔包括:初馏塔或闪蒸塔、常压塔、减压塔。
3.5蒸馏塔结构
蒸馏塔的结构:
塔体:塔体是由直圆柱型桶体,高度在35~40米左右,材质一般为A3R或16MnR,对于处理高含硫原油的装置,塔内壁还有不锈钢衬里。
塔体封头:一般为椭圆形或半圆形。
塔底支座:塔底支座要求有一定高度,以保证塔底泵有足够的灌注压头。
塔板或填料:是塔内介质接触的载体,传质过程的三大要素之一。开口及管嘴:是将塔体和其它部件连接起来的部件,一般由不同口径的无缝钢管加上法兰和塔体焊接而成。人孔:是进入塔内安装检修和检查塔内设备状况之用,一般为直径450~500的圆型或椭圆型孔。进料口:由于进料气速高,流体的冲刷很大,为减小塔体内所受损伤。同时为使气、液分布和缓冲的作用。进料处一般有较大的空间,以利于气液充分分离。液体分布器:使回流液体在填料上方均匀分布,常减压装置应用较多的是管孔式液体分布器和喷淋型液体分布器。气体分布器:气体分布器一般应用在汽提蒸汽入塔处,目的是使蒸汽均匀分布。破沫网:在减压塔进料上方,一般都装有破沫网,破沫网由丝网或其它材料组成,当带液滴的气体经过破沫网时,液滴与破沫网相撞,附着在破沫网上的液滴不断积聚,达到一定体积时下落集油箱:主要作用是收集液体供抽出或再分配。集油箱将填料分成若干个气相连续液相分开的简单塔,它靠外部打入液体建立塔的回流。塔底防漏器:为防止塔底液体流出时,产生旋涡将油气卷入,使泵抽空。塔底装有防漏器。它还可以阻挡塔内杂质,防止其阻塞管线和进入泵体内。外部保温层:一般用集温温砖砌成,并用螺丝固定,外包薄铁皮或铝皮,保温层起隔热和保温作用。b、加热炉:一般为管式加热炉,其作用为:是利用燃料在炉膛内燃烧时产生的高温火焰与烟气作为热源,加热炉中高速流动的物料,使其达到后续工艺过程所要求的温度。管式加热炉一般由辐射室、对流室、余热回收系统、燃烧及通风系统五部分组成。 通常包括钢结构、炉管、炉墙、燃烧器、孔类配件等。
辐射室:辐射室是加热炉进行热交换的主要场所,其热负荷占全炉的70~80%。
辐射室内的炉管,通过火焰或高温烟气进行传热,以辐射为主,故又称辐射管。它直接受火焰辐射冲刷,温度高,所以其材料要具有足够的高温强度和高温化学稳定性。
对流室:对流室是辐射室排出的高温烟气进行对流传热来加热物料。烟气以较高的速度冲刷炉管管壁,进行有效的对流传热其热负荷占全炉的20~30%。对流室一般布置在辐射室之上,有的单独放在地面。为了提高传热效果,多采用钉头管和翅片管。
余热回收系统:余热回收系统用以回收加热炉的排烟余热。 以靠预热燃烧空气来回收,使回收的热量再次返回到炉中是采用另外的系统回收热量。前者称为空气预热方式,后者通用水回收称为废热锅炉方式。
燃烧及通风系统:通风系统的作用是把燃烧用空气导入燃烧器,将废烟气引出炉子。它分为自然通风和强制通风两种方式。前者依靠烟囱本身的抽力,后者使用风机。过去,绝大多数炉子都采用自然通风方式,烟囱安装在炉顶。近年来,随着炉子的结构复杂化,炉内烟气侧阻力增大,加之提高加热炉的热效率的需要,采用强制通风方式日趋普。
第四章 中控常减压蒸馏装置自动化解决方案
4.1装置自动化
中控在石化行业有着完善的装置解决方案,丰富的工程实施经验。目前WebField系列控制系统已在诸如常减压蒸馏、催化裂化、加氢精制、延迟焦化、溶剂脱沥青、气体分离、各类制氢、硫磺回收、PVC、苯酐、苯胺、环己酮等炼油及石化行业的各个主流装置得到广泛应用,在国内炼油和石化行业市场占有率一直居于领先地位,是国内唯一的与中石化建立了MES建设战略合作伙伴关系的DCS厂家,包括中石化、中石油所属的镇海炼化、扬子石化、茂名石化、齐鲁石化、大庆石化等大中型石化企业中均已采用中控提供的控制系统和解决方案实现了对炼油及石化生产过程的控制。
常减压装置是炼油企业的基本装置,是原油加工的第一道工序,在炼油中起着非常重要的作用。它的工艺过程是采用加热和蒸馏的方法反复地通过冷凝与汽化将原油分割成不同沸点范围的油品或半成品,将原油分离的过程。主要分离产物有:重整原料、汽油组分、航空煤油、柴油、二次加工的原料(润滑油、催化裂化原料等)及渣油(重整及焦化、沥青原料)。
4.2常压部分
在常压塔中,对原油进行精馏,使气液两相充分实现热交换和质量交换。在提供塔顶回流和塔底吹气的条件下,从塔顶分馏出沸点较低的产品汽油,从塔底分馏出沸点较高的重油,塔中间抽出得到侧线产品,即煤油、柴油、重柴、蜡油等。常压蒸馏后剩下的重油组分分子量较大,在高温下易分解。为了将常压重油重的各种高沸点的润滑油组分分离出来,采用减压塔减压蒸馏。使加热后的常压重油在负压条件下进行分馏,从而使高沸点的组分在相应的温度下依次馏出,作为润滑油料。常减压装置的减压蒸馏常采用粗转油线、大塔径、高效规整填料(GEMPAK)等多种技术措施。实现减压操作低炉温、高真空、窄馏分、浅颜色,提高润滑油料的品质。
常减压装置通常以常规单回路控制为主,辅以串级、均匀和切换等少量复杂控制。
脱盐罐差压调节、注水流量定值控制和排水流量定值控制。
塔顶温度控制:通过调节塔顶回流油量来实现对塔顶温度的控制,并自动记录回流流量,以便观察回流变化情况。
塔底液位控制:在初馏塔底采用差压式液面计,同时在室内指示和声光报警,以防止冲塔或塔底泵抽空。
塔顶压力控制:为了保证分馏塔的分馏效果,一般在塔顶装有压力变送器,并在室内进行监视、记录。
回流罐液位和界位控制:在回流罐上装有液面自动调节器来控制蒸顶油出装置流量以保证足够的回流量;同时通过界面调节器,以保持油水界面一定(调节阀安装在放水管上)。
蒸侧塔控制:为了减轻常压炉的负荷,提高处理量,在初馏塔旁增设了蒸侧塔。蒸侧塔液面需 自动控制(调节阀安装在初馏塔馏出口上),并设有流量调节器控制进入常压塔的流量。
炉的四个分支进料线上,各装有流量调节器,来调节加热炉的流量。
加热炉出口温度控制:通过调节燃料油和燃料气的量来保持常压加热炉出口温度的恒定(燃料气可在低压瓦斯燃料气、自产瓦斯燃料气、高压瓦斯燃料气之间切换使用)。
常压塔顶出口温度控制:通过调节入塔回流量来保持常压塔顶出口处温度的恒定;如果常一线是生产航空煤油方案时,可以用常一线温度来控制入塔回流量,并对回流流量进行记录。
回流罐液位和界位控制:为了保证常压塔顶回流油量,在回流罐上部装有液位调节器,调节常压塔顶汽油的出装置量。在其下面装有界面调节器,以保持一定的油水界面(调节阀安在放水管线上)。
常压塔压力调节:一般装有压力变送器,并在室内记录,以供控制产品质量进行参考;也可以在回流罐中安装压力调节器,调节放出的气体量。
常压塔底液位调节:为了保证常压塔底液位平稳而不造成冲塔、减压加热炉进料泵不抽空,故在塔底装有差压式液位变送器,并有液位记录和声光报警,便于分析事故。为了节约能源,有些装置塔底设置有变频器,通过调节阀和变频器的切换来控制塔底液位。
汽提塔液位和流量调节:为了控制侧线的产品质量,在常压塔各侧线汽提塔中装有液位自动调节器,以调节常压塔馏出口至侧线汽提塔的油量。各侧线成品出装置时有流量调节器,调节阀装在各馏分抽出泵的出口管线上。
4.3减压部分
关键控制:
减压塔顶温度调节:为了保证减压塔顶温度一定,避免油气损失,在塔顶出管线上装有温度调节器,以调节塔顶回流油量。
塔顶产品流量调节:为了提高轻油收率,塔顶轻质油出装置管线装有流量调节器。减一线也设有温度调节器,以控制回流油量。减一线出装置管线上,也装有流量调节器。
侧线回流流量调节:为了取走减压塔的热量,并保证侧线产品质量,设有减二、三线回流。同时为了保证回流一定,在入塔后回流油管线上,装有流量调节器。
减压塔底液位调节:为了保证塔底液位稳定,设有塔底液位调节器,以调节减压塔底渣油出装置的油量。为了节约能源,有些装置塔底设置有变频器,通过调节阀和变频器的切换来控制塔液 设有真空压力发讯器,记录减压塔的真空度。
中控是国内能提供和实施石化生产装置先进及优化控制为数不多并且领先的厂家之一,在常减压蒸馏先进控制有常压优化压优化、减压炉支路平衡控制等控制策略。
主要目标是在操作的约束范围内稳定操作,在满足各产品指标的前提下,使产品
原理是通过改变加热炉进料量在分支之间的分配,达到使分支温度出口相近的目的;实际上是牺牲流量上的分配均匀,来实现温度的均匀。优化控制的目标是兼顾流量与温度的均匀性。
中控在常减压蒸馏、催化裂化、PTA、加氢精制等主流装置上的优化控制策略,接近或达到国外先进水平,已具备与国外先进公司同台竞争的实力,目前已有数十套成功应用的业绩和经验。随着石化企业对先进控制需求的日益增长,必将体现出越来越强的竞争优势。
第五章 催化裂化工艺简介
催化裂化是原油二次加工中最重要的加工过程,是液化石油气、汽油、煤油和柴油的主要生产手段,在炼油厂中占有举足轻重的地位。
催化裂化一般以减压馏分油和焦化蜡油为原料,但是随着原油的日趋变重的增长趋势和市场对轻质油品的大量需求,部分炼厂开始掺炼减压渣油,甚至直接以常压渣油作为裂化原料。下面将从七个方面对催化裂化展开介绍。
5.1催化裂化的一般特点
轻质油(包括汽油、煤油和柴油)收率高,可达70~80wt%,而原油初馏的轻质油收率仅为10~40wt%。
催化裂化汽油的辛烷值较高,研究法辛烷值可达85以上,汽油的安定性也较好。
催化裂化柴油的十六烷值低,常与直馏柴油调合使用,或者加氢精制提高十六烷值。
催化裂化气体产品约占10~20wt%,其中90%是液化石油气,并且含有大量的C3、C4烯烃,是优良的石油化工和生产高辛烷值汽油组分的原料。
5.1.1重油催化裂化的特点
焦炭产率高。重油催化裂化的焦炭产率高达8~12wt%,而馏分油催化裂化的焦炭产率通常为5~6wt%。
重金属污染催化剂。与馏分油相比,重油含有较多的重金属,在催化裂化过程中这些重金属会沉积在催化剂表面,导致催化剂受污染或中毒。
硫、氮杂质的影响。重油中的硫、氮等杂原子的含量相对较高,导致裂化后的轻质油品中的硫、氮含量较高,影响产品的质量;另一方面,也会导致焦炭中的硫、氮含量较高,在催化剂烧焦过程中会产生较多的硫、氮氧化物,腐蚀设备,污染环境。
催化裂化条件下,重油不能完全气化。重油在催化裂化条件下只能部分气化,未气化的小液滴会附着在催化剂表面上,此时的传质阻力不能忽略,反应过程是一个复杂的气-液-固三相催化反应过程。
5.1.2 单体烃的催化裂化反应
烷烃主要发生分解反应,生成较小分子的烷烃和烯烃。
烯烃除发生分解反应外,还发生异构化、氢转移和芳构化等反应。
环烷烃可以发生开环反应生成链状烯烃,也可以发生氢转移反应生成芳香烃。
芳香烃不发生开环反应,只发生断侧链反应,且断裂的位置主要发生在侧链同芳香环连接的键上。
烃类催化裂化反应机理和产物分布规律
绝大多数学者认为烃类的催化裂化反应遵循碳正离子反应机理。按照碳正离子反应机理,烃类催化裂化的反应性能和产物分布规律如下:
裂化原料中,烯烃裂化的速度和芳香烃断侧链的速度都很快,而环烷烃和异构烷烃的反应速度较慢,正构烷烃的分解速度最慢。
汽油中的烯烃含量很高,芳香烃含量也比较高,汽油的辛烷值较高。
柴油中烷烃含量较低,十六烷值较低。
裂化气体中C3和C4产物的含量很高,并且主要是丙烯和丁烯,在C4产物中,异构烃类的含量较高。
5.1.3催化裂化的影响因素
催化裂化的影响因素主要包括原料油的性质、催化剂性质、操作条件以及反应装置。
裂化原料油性质的影响。一般来说,原料油的H/C比越大,饱和分含量越高,则裂化得到的汽油和轻质油收率越高。原料的残炭值越大,硫、氮以及重金属含量越高,则汽油和轻质油收率越低,且产品质量越差。
催化剂的性质。催化裂化催化剂分为硅酸铝催化剂和分子筛催化剂两种,催化剂的活性、选择性、稳定性、抗重金属污染性能、流化性能和抗磨损性能都对催化裂化有着不同程度的影响。一般来说,催化剂的活性越高,原料的转化率也越大;而催化剂的选择性越高,则轻质油品的收率也越高。分子筛催化剂的活性和选择性一般都优于硅酸铝催化剂,可提高汽油产率15~20%。
操作条件的影响。操作条件包括原料的雾化效果和气化效果、反应温度、反应压力、反应时间、剂油比、水蒸汽量和催化剂的停留时间等。原料的雾化效果和气化效果越好,原料油的转化率越高,轻质油品的收率也越高;反应温度越高,剂油比越大,则原料油转化率和汽油产率越高,但是焦炭的产率也变大;油气停留时间不能太短,也不宜过长,一般在2~4秒;催化剂停留时间越长,则意味着单位催化剂上发生的反应数越多,催化剂的平均活性下降,会导致原料油的转化率下降;而反应压力的影响相对较小。
目前炼油厂催化裂化装置普遍采用提升管作为反应装置,提升管的长短对裂化有一定的影响,提升管越长,则二次反应加剧,气体和焦炭产率较高。另外原料油雾化喷嘴和旋风分离器的性能也对裂化产品分布有着一定的影响。
5.2催化裂化的工艺流程
催化裂化装置一般由三部分组成:反应-再生系统、分馏系统和吸收-稳定系统。其中,反应-再生系统是催化裂化装置的核心部分,其装置类型主要有床层反应式、提升管式,提升管式又分为高低并列式和同轴式两种。尽管不同装置类型的反应-再生系统会略微有所差异,但是其原理都是相同的,下面就以高低并列式提升管催化裂化为例进行简单介绍,其反应-再生系统的工艺流程如下图所示。
反应-再生系统工艺流程示意图
① 反应-再生系统
新鲜原料油经过换热后与回炼油混合,经加热炉加热至300~400℃后进入提升管反应器下部的喷嘴,用蒸汽雾化后进入提升管下部,与来自再生器的高温催化剂(600~750℃)接触,随即气化并进行反应。油气在提升管内的停留时间很短,一般2~4秒。反应后的油气经过旋风分离器后进入集气室,通过沉降器顶部出口进入分馏系统。
积有焦炭的再生催化剂(待生催化剂)由沉降器进入下面的汽提段,用过热水蒸汽进行汽提,以脱除吸附在待生催化剂表面的少量油气,然后经过待生斜管、待生单动滑阀进入再生器,与来自再生器底部的空气接触反应,恢复催化剂的活性,同时放出大量的热量。
分馏系统
分馏系统的作用是将反再系统的产物进行分离,得到部分产品和半成品。由反再系统来的高温油气进入催化分馏塔下部,经装有人字挡板的脱过热段脱热后进入分馏段,经分馏后得到富气、粗汽油、轻柴油、回炼油和油浆。富气和粗汽油去吸收稳定系统;轻柴油经汽提、换 热、冷却后碱洗出装置,回炼油返回反应––再生系统进行回炼。油浆的一部分送反应再生系统回炼,另一部分经换热后循环回分馏塔。为了取走分馏塔的过剩热量以使塔内气、液相负荷分布均匀,在塔的不同位置分别设有4 个循环回流:顶循环回流,一中段回流、二中段回流和油浆循环回流。
催化裂化分馏塔底部的脱过热段装有约十块人字形挡板。由于进料是460℃以上的带有催化剂粉末的过热油气,因此必须先把油气冷却到饱和状态并洗下夹带的粉尘以便进行分馏和避免堵塞塔盘。因此由塔底抽出的油浆经冷换热后分上返塔和下返塔两路返回分馏塔与由塔底上来的油气逆流接触,一方面使油气冷却至饱和状态,另一方面也洗下油气夹带的粉尘,另一路控制塔底温度。`
吸收-稳定系统
从分馏塔顶油气分离器出来的富气中带有汽油组分,而粗汽油中则溶解有c3、c4甚至c2组分。吸收––稳
定系统的作用就是利用吸收和精馏的方法将富气和粗汽油分离成干气(≤c2)、液化气(c3、c4)和蒸汽压合格的
稳定汽油。该部分包括吸收塔、解吸塔、再吸收塔、稳定塔和相应的冷却换热设备,目的是将来自分馏部分的富气中C2以下组分与C3以上组分分离以便分别利用,同时将混入汽油中的少量气体烃分出,以降低汽油的蒸气压。
5.3催化裂化工艺技术研究进展
随着人们对催化裂化认识的逐步加深和相关研究的不断进展,开发出了多种催化裂化技术和工艺。如预提升技术、新型喷嘴进料技术、混合温度控制技术、提升管急冷油技术、反应终止剂技术、提升管分路进料技术、急冷技术、油剂快速分离技术、毫秒催化裂化技术、高温短时间接触催化裂化技术。
另外,也出现一些新型的催化裂化工艺(催化裂化家族工艺),如两段提升管催化裂化工艺、多产气体烯烃和优质汽油的MGG工艺、多产异丁烯和异戊烯的MIO工艺、以常压渣油为原料多产液化气和汽油的ARGG工艺等。
重质油国家重点实验室的张建芳教授、山红红教授等人开发了两段提升管催化裂化工艺。该工艺可以实现催化剂接力、分段反应、短反应时间和大剂油比,可有效强化希望的催化反应,抑制不利的二次反应和热裂化反应。这里,催化剂接力是指当裂化原料经过一段适宜的反应时间、催化剂活性由于积炭而下降到一定程度时,失活催化剂及时与油气分开,并返回再生器再生,油气在第二段提升管与再生后的另一批催化剂接触,继续反应。就整个反应过程而言,催化剂的平均活性和选择性均高于普通的催化裂化过程,催化反应所占比例增大,有利于提高柴油产率和十六烷值,并降低干气和焦炭产率。
重质油国家重点实验室的高金森教授等人开发了辅助提升管反应降烯烃技术。该技术依托常规重油催化裂化装置,装置改动小,投资低,易于实现;不用对改质汽油进行额外分离,操作稳定,易于控制;将改质油气与主提升管油气混合后进入主分馏塔分离,辅助提升管反应器采用单独的沉降器。该工艺在华北石化公司100万吨/年重油催化裂化装置和滨州石化公司20万吨/年重油催化裂化装置上成功应用,催化汽油烯烃含量从45v%至55v%降到35v%以下,且辛烷值保持不变。适当调节改质反应条件,可以将汽油的烯烃含量降低到18v%以下,能够满足欧Ⅲ汽油的烯烃含量要求。利用该技术可直接生产出合格的高品质汽油,实现了汽油产品的升级换代,满足当前汽油新标准,经济和社会效益显著。
第六章 延迟焦化装置
6.1概况
焦化是深度热裂化过程,也是处理渣油的手段之一。它又是唯一能生产石油焦的工艺过程,是任何其他过程所无法代替的。是某些行业对优质石油焦的特殊需求,致使化过程在炼油工业中一直占据着重要地位
延迟焦化是一种石油二次加工技术,是以贫氢的重质油(如减压渣油、裂化渣油以及沥青等)为原料,在高温(400~500℃)进行深度的热裂化反应。通过裂解反应,使渣油的一部分转化为气体烃和轻质油品;由于缩合反应,使渣油的另一部分转化为焦炭。
延迟焦化是一个成熟的减压渣油加工工艺,多年来一直作为一种重油深加工手段。近年来随着原油性质变差(指含流量增加)、重质燃料油消费的减少和轻质油品需求的增加,焦化能力增加的趋势很快。
延迟焦化装置的作用:将重质油馏分经裂解、聚合,生成油气、轻质油、中间馏分和焦炭。
6.2工艺原理
焦化是在高温条件下,热破坏加工重油(减压渣油)的一种方法,其目的是得到汽油、柴油、焦炭、裂化馏分油(焦化蜡油)和气体。焦化过程是一种热分解和缩合的综合过程。也是一种渣油轻质化的过程。原料油一般加热到420℃开始热解,于500℃下进行深度热裂化反应。延迟焦化是将原料油通过加热炉加热时,采用高的油流速(入口混相流速3.54m/s)和高的加热强度(35kw/m2),使油品在短时间内达到焦化反应所需的温度同,并且迅速离开加热炉进入焦炭塔,从而使生焦反应不在加热炉中进行,而延迟到焦炭塔中进行的一种热加工过程。焦化反应的机理较为复杂,一般简单表示为:
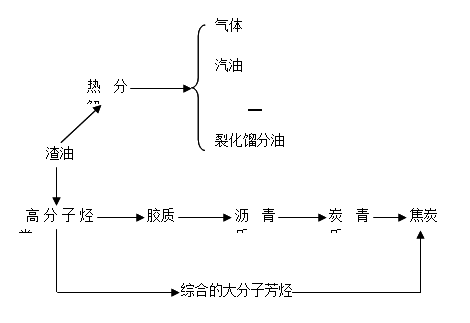
6.3主要工艺流程
减压渣油从1#常减压装置来,温度为200℃以上,冷渣油从罐区来,温度为70~80℃。从1#常减压来的热渣油进入原料油缓冲罐V-101,经原料油泵P-101(102)抽出与循环油混合后先后与中段回流(E-110)和轻蜡油换热(E-107)(若冷热混炼,则冷渣油在换-110前与热渣油汇合),然后分两路,分别与循环油及回流(E-111/1~4)、重蜡油及回流(E-112/1~4)、循环油及回流(E-113/1~4)换热到约330℃进入加热炉进料缓冲罐V-104。V-104罐底油经加热炉进料泵P-409(410)分别送到加热炉F-303、F-301加热到495~505℃,经四通阀进入焦碳塔T-201(202)。炉-303进料分为四路,每路设二点注水,一点注汽。在焦碳塔内进行裂解和缩合反应,反应产物除焦炭聚集在塔内,其它产品均呈气相从焦碳塔顶进入分馏塔T-101。油气进分馏塔,轻组分上升,重组分落入塔底,上升到精馏段的油气通过塔盘进行传质传热,在不同的部位分离出富气、汽油、柴油、轻蜡油、重蜡油和循环油,炉子注水随气体一起从T101顶逸出。焦炭塔内的焦炭聚集到一定的高度,停止进料,切换到另一个已预热好的焦炭塔内继续生产。停止后的塔通过大量吹汽和给水冷焦,将焦炭温度冷却到80℃以下,焦炭经水力除焦进入焦池,用吊车抓斗装车出厂或用履带送动力厂CFB锅炉出燃料。
分馏塔T-101底循环油自塔底经过滤器后由循环油泵P-121、P122抽出,与加热炉进料换热器E-113/1~4、E-111/1~4换热到280℃~310℃分为五路,一路作为回流控制分馏塔蒸发段温度,二路作为回流控制分馏塔底温度,三路作为循环油,用于调节装置循环比,四路作为热蜡油出装置,五路经冷却器L-105冷却至80℃~100℃出装置。
重蜡油从蜡油箱由泵P-124、P-108抽出,一路作为内回流返塔,另一路经与加热炉进料换热器E-112/1~4换热至295℃左右分为三路,一路返分馏塔六层塔盘,二路作为热蜡油出装置,三路经低温水换热器E114冷却出装置。
轻蜡油自分馏塔11层塔盘由泵P-123、P-107抽出,经与加热炉进料换热器E-107、轻蜡油蒸汽发生器E-101换热后,一路作为热蜡油出装置,另一路经低温水换热器E-108冷却后去1#催化或加氢制氢装置进行改质。
中段回流自分馏塔19层塔盘由中段回流泵P-106、P1O9抽出,经稳定塔底重沸器E708、加热炉进料换热器E-110、中段回流蒸汽发生器E-102换热到190℃~215℃返回分馏塔的23层,控制柴油质量。
塔顶循环回流自汽油箱用顶回流泵P-103、P-104抽出,经低温水换热器E-106换热后返回塔顶,控制顶部负荷和汽油干点。
柴油自柴油箱由泵P-120、P105抽出分为两路,一路作为内回流返塔,另一路经柴油蒸汽发生器E103、除氧水换热器E-104、气分塔底重沸器、富柴换热器E-105/1换热到150℃,再分两路,一路作为回流返塔,另一路继续经低温水换热器E-105/2~5、柴油冷却器L-104冷却送柴油加氢装置改质。从E105出来柴油可作机泵端面密封冲洗油,也可经仪表冲洗油泵P113、P114升压后用作仪表冲洗油。从L104出来的柴油可作机泵端面密封冲洗油,也可经仪表冲洗油泵P113、P114升压后和作仪表冲洗油。从L104抽出,经P701、P702加压E704冷却后进贫气再生塔T701,从T701底出来的富柴油与柴油换热器E105/1换热后和25层回流一起返回分馏塔。
水蒸汽、汽油、气体从T-101顶部逸出,经塔顶空冷器L101、后冷器L-102冷凝至40℃进入油、水、气分离罐V-102分离,水从V-102底部经污水泵P-116、P-117抽出经污水过滤器V107后送入污水脱硫装置。汽油用汽油泵P-111、P-112抽出部分可作为T-101顶冷回流,部分作为吸收剂送至吸收塔T702。
焦化富气自V102来,进压缩机入口缓冲罐V704,底部凝缩油由凝缩油泵P705、P706返回V102。富气进入压缩机C701,经一段压缩,温度达到123℃,压力为0.35MPa,经一段中间冷却器L702冷却至40℃,再进入中间分离器V703,由V703出来的富气进C701二段入口,经二段压缩后温度达139℃,压力为1.1Mpa,再与解吸气、吸收塔底油混合后进入冷却器L701冷却到40℃,进气液水分离罐V702分离,含硫污水自压出装置,气相进汽油吸收塔;凝缩油经泵P702抽出分两路:一路去解吸塔T703顶,另一路与稳定汽油换热器E710加热后去解吸塔第9层。经解吸出轻组分后的塔底油由解吸塔底泵P713抽出与稳定汽油换热器E709加热后进稳定塔T704。解吸塔底重沸器E707热源为焦化分馏塔柴油。
解吸油经稳定塔分离出液态烃后,稳定汽油自塔底采出,经E709、E710、E711冷却后分两路:一路出装置去加氢;另一路经吸收油泵P712送至吸收塔顶作吸收油。T704塔顶出来的气态烃经E706冷却后去稳定塔顶回流罐V711。液态烃泵P714抽出的液态烃分两路:一路送出装置去脱硫;另一路回流去稳定塔顶。稳定塔底重沸器E708的热源为焦化分馏塔中段回流油。
自分液罐V702来的富气经吸收塔T702被焦化粗汽油及稳定汽油吸收重组分后的气体去柴油再吸收塔T701。为了提高吸收效果,吸收塔设有一个中段回流,取走多余的热量。从T701顶部出来的焦化干气经V705后送往加氢装置。
液氨由系统管网来,与系统来的低温软化水(与机泵端面软化水相同)按比例进入氨水配制罐V706,并按焦化富气中硫含量的高低控制氨浓度,一般情况下氨浓度控制在1%-4%,配好的氨水由V706底抽出,经注氨泵P703、P704可注入静态混合器M701前,使富气氨洗脱硫,也可注入分馏塔与油气混合脱除富气中的硫,富气和含氨污水进入V102分离,含氨污水送往脱硫装置。
3.5MPa蒸汽自动力管网来,驱动汽轮机做功后,背压汽排入1.0MPa蒸汽管网,为保证汽轮机背压不超高,在背压汽管道上还设置了安全阀。
氮气从系统管网来,有高压N2和N2低压,高压N2经过两级减压,作为气压机密封用氮气,注入气压机密封腔。
焦碳塔大量吹汽和给水冷焦产生的高温蒸汽及少量油气进入放空塔T205,塔底油用污油泵P211抽出,一部分进分馏塔二层回炼,另一部分经污油换热器E201(或水箱冷却器L202/56)后作塔顶回流,控制T205顶部温度在104℃左右,也可甩至污油罐V205、V206或五垅灌区。T205顶油气直接进入放空塔顶空冷器L303、循环水冷却器L301、L302后,进入放空分液罐V204分离,V204污油用泵甩至沉降罐V205,污水压至冷焦水罐V211,分液罐顶部的不凝气排入火炬系统。
从焦碳塔T201/T202自流下来的冷焦水和从冷焦水泵P204来的冷焦水经混合器混合后,先进入冷焦水缓冲罐V208,然后由冷焦水泵P208送入热水罐V211,热水由热水泵P214抽出经焦粉过滤器V210/AB过滤后进入除油器V209/AB除油后分两路:水经空冷L203冷却后进冷水罐V212;油水进入V211或小油池,小油池的污油经P215/AB送至V205。
焦碳塔切焦用的高压水,由高压水泵P503、P501送出,经三位控制阀送到水力切焦器切焦。焦碳塔出来的切焦水经过储焦池、一沉淀池、二沉淀池,用切焦水提升泵P1402送至山上水池循环使用。
6.4主要工艺设备
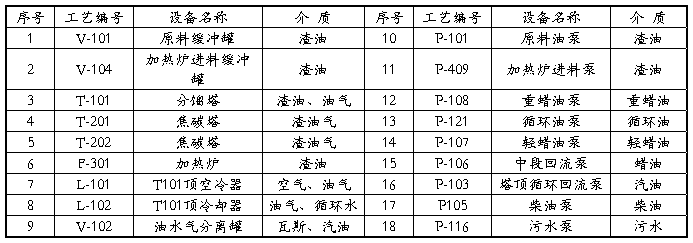
6.5主要工艺操作指标
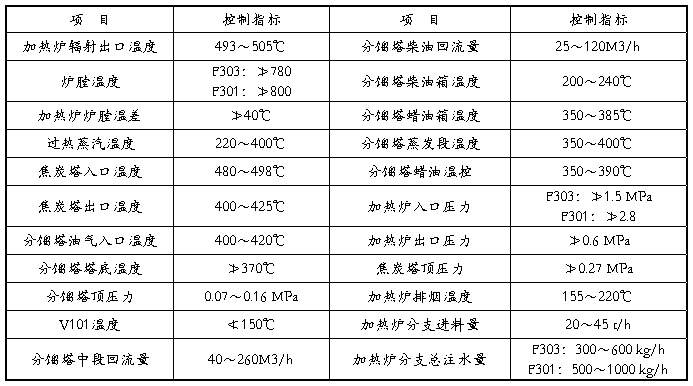
第七章 实践总结
虽然只有短短十个月的时间,却感触颇深。实习过程中,我采用了勤看、勤问、勤学、的方式,对宝来日常生产工作的开展有了比较全面而深入的了解。在系统分析了公司生产的特点、方式和运做规律后,对吉化有机合成厂生产流程、工艺设备、监察方式及企业精神有了深刻的认识。
有如下几个特点:一、注重安全生产,在稳定中求发展。吉林石化公司有机合成厂坚持以抓实受控管理为主线,狠抓装置安全平稳生产,实现了在安全生产中增幅产量。开展了“百日安全无事故”等一系列的活动,积极落实“四有工作法”,对所有装置工艺规程和岗位操作法进行了重新修订;全面实行了四级生产操作变动监控管理规定,加强对员工巡检和使用电子巡检仪的技能培训。二、启动企业联盟战略,有效利用品牌优势。宝来北方沥青,大力实施装置长期稳定创效的明星产品战略,20##年一季度,生产丁苯橡胶产品41213.9吨,超额完成生产计划804吨,产量在中国石油合成橡胶行业勇夺第一。此举标志着吉林石化在做大做强我国合成橡胶生产基地方面,又迈出坚实一步。三、在实现产量稳定的基础上,节俭开支,节约能源。吉林石化有机合成厂从今年1月份开始,把开展“勤俭节约、挖潜增效”主题实践活动作为应对经济危机的有效措施。为了节约用电,他们把周分析、月分析、季分析中需要加热的项目归类,统一进行加热,每年可节约用电XX多度。在实习的时候我们注意到,所有厂区的电器类再没人使用时都保持关闭。
第八章 未来展望
由于刚刚来到这里没有多久对于未来的展望也只能暂时放在自身的发展之上。毕竟水平一般能力有限。对于未来我的期望是在短时间内能够尽快的掌握了解宝来北方沥青艺流程以及所作工作,注意把书本上学到的相关理论知识与生产相结合,深入理解。用理论加深对实践的感性认识,用实践来验证理论知识的准确性,积极探求化工工艺的本质与规律。光阴似箭,三年的大学生活就要结束了,三年里有太多的辛酸苦辣,有太多的留恋往返。按照中国最传统的教育晋升步伐,我来到了现在的学校。进入大学前我可以说是无知的,今天的我也不能说是什么都懂,但略带点知识内涵的我即将踏出这个学校的大门,成为社会中的真正一份子。三年的大学生活让我体会到了什么是独立自主,什么是为自己负责,什么是勇于挑战,什么是完善自我。虽说,在这三年里自己还有许多不足的,但让我初步知道了大学生活是什么样的。令我感到自豪的是,这三年的时间没有白白的浪费掉,学到了自己应该掌握的知识,结识了许多朋友。
使自己真正的成长起来去适应这个在不断发展的社会,想让自己不被淘汰就要去跟上进步的脚步。实习生活,满含着紧张和新奇,更从中收获了丰硕的成果。再多的辛酸与辛苦都在见证着我们的进步和成长,在这不断成长中我们的未来将不再迷茫,面对未来的挑战酱油更大的信心去接受。机会是留给有准备的人,当我们准备好了,离成功只有一步之遥。