毕业设计(论文)学生开题报告
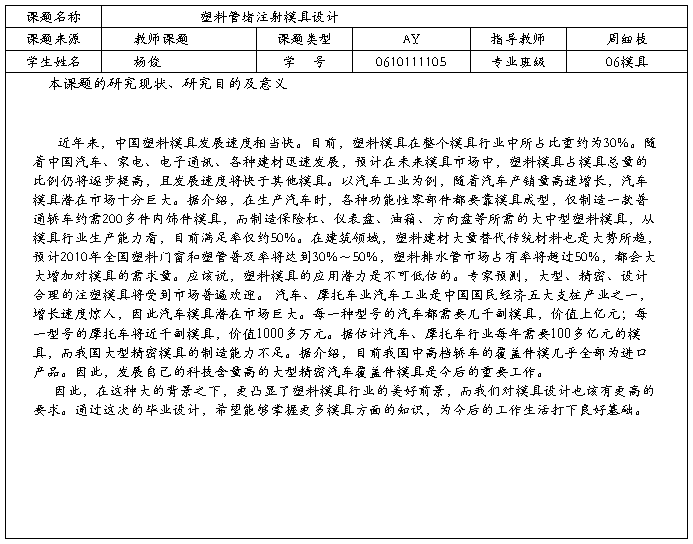
课题类型:
(1)A—工程实践型;B—理论研究型;C—科研装置研制型;D—计算机软件型;
E—综合应用型
(2)X—真实课题;Y—模拟课题;
(1)、(2)均要填,如AY、BX等。
2
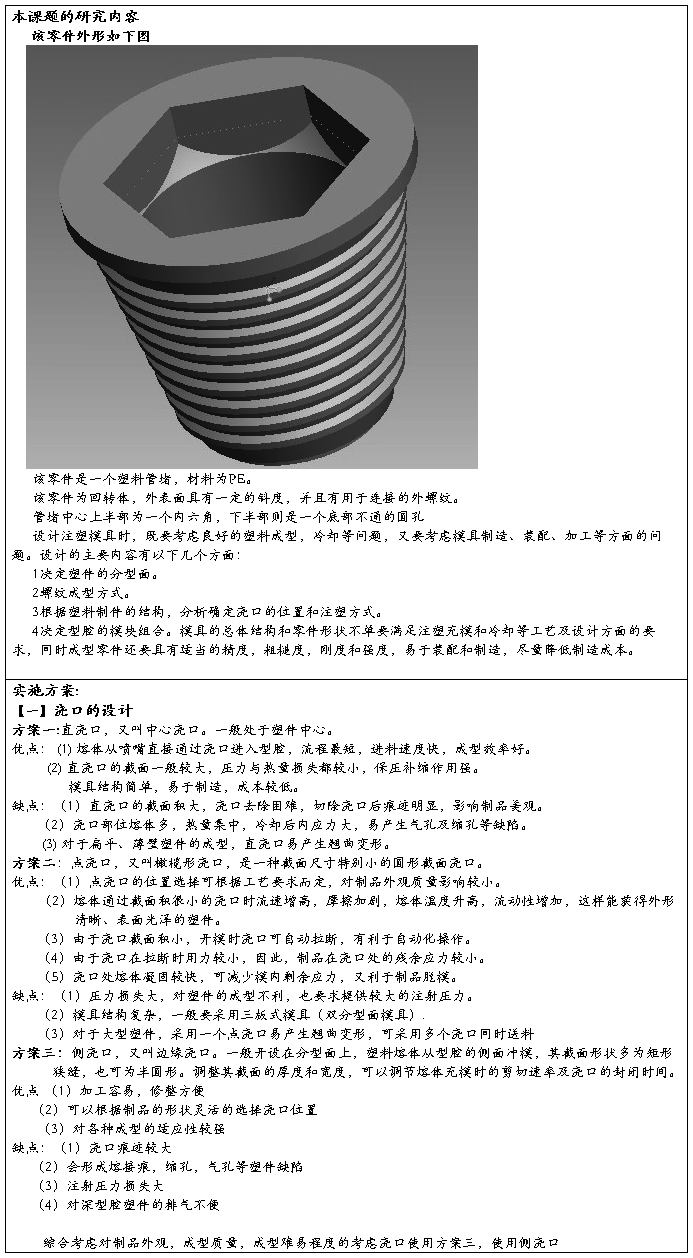
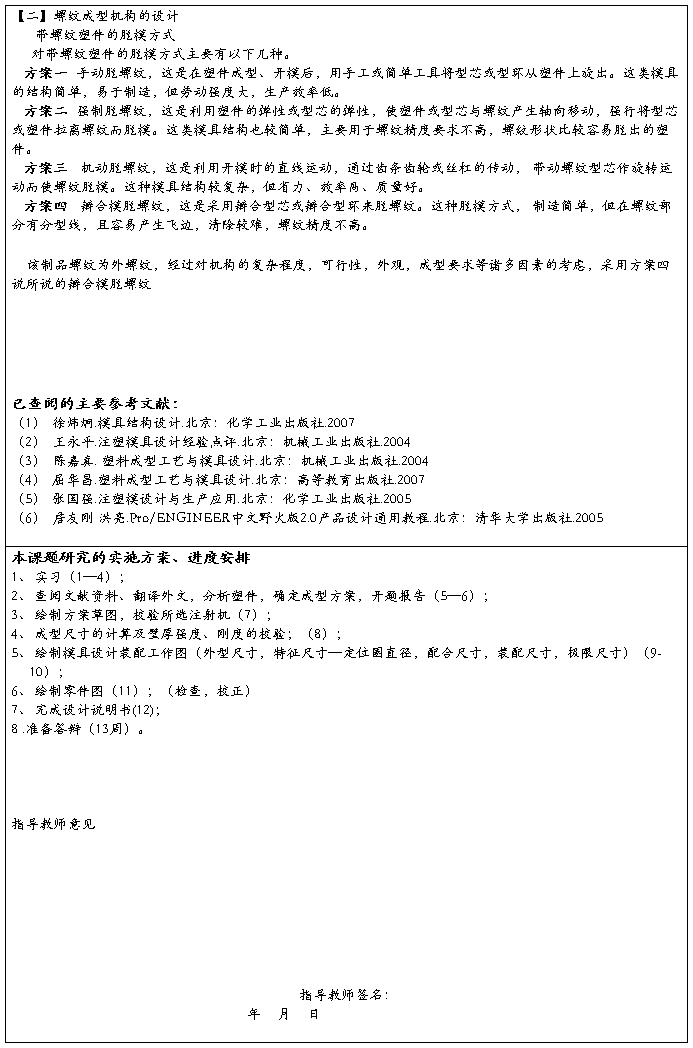
第二篇:塑料模具设计的意义
【摘要】塑料工业是当今世界上增长最快的工业门类之一,而注塑模具是其中发展较快的种类。因此,研究注塑模具对了解塑料产品的生产过程和提高产品质量有很大意义。
本设计介绍了注射成型的基本原理,特别是单分型面注射模具的结构与工作原理,对注塑产品提出了基本的设计原则。通过本设计,可以对注塑模具有一个初步的认识,注意到设计中的某些细节问题,了解模具结构及工作原理.
绪论
一、模具工业在国民经济中的地位
模具是制造业的一种基本工艺装备,它的作用是控制和限制材料(固态或液态)的流动,使之形成所需要的形体。用模具制造零件以其效率高,产品质量好,材料消耗低,生产成本低而广泛应用于制造业中。
模具工业是国民经济的基础工业,是国际上公认的关键工业。模具生产技术水平的高低是衡量一个国家产品制造水平高低的重要标志,它在很大程度上决定着产品的质量,效益和新产品的开发能力。振兴和发展我国的模具工业,正日益受到人们的关注。、
模具工业既是高新技术产业的一个组成部分,又是高新技术产业化的重要领域。模具在机械,电子,轻工,汽车,纺织,航空,航天等工业领域里,日益成为使用最广泛的主要工艺装备,它承担了这些工业领域中60%~90%的产品的零件,组件和部件的生产加工。
目前世界模具市场供不应求,模具的主要出口国是美国,日本,
法国,瑞士等国家。中国模具出口数量极少,但中国模具钳工技术水平高,劳动成本低,只要配备一些先进的数控制模设备,提高模具加工质量,缩短生产周期,沟通外贸渠道,模具出口将会有很大发展。研究和发展模具技术,提高模具技术水平,对于促进国民经济的发展有着特别重要的意义。
二、各种模具的分类和占有量
模具主要类型有:冲模,锻摸,塑料模,压铸模,粉末冶金模,玻璃模,橡胶模,陶瓷模等。除部分冲模以外的的上述各种模具都属于腔型模,因为他们一般都是依靠三维的模具形腔使材料成型。
(1) 冲模:冲模是对金属板材进行冲压加工获得合格产品的工具。冲模占模具总数的50%以上。按工艺性质的不同,冲模可分为落料模,冲孔模,切口模,切边模,弯曲模,卷边模,拉深模,校平模,翻孔模,翻边模,缩口模,压印模,胀形模。按组合工序不同,冲模分为单工序模,复合模,连续模。
(2) 锻模:锻模是金属在热态或冷态下进行体积成型时所用模具的总称。按锻压设备不同,锻模分为锤用锻模,螺旋压力机锻模,热模锻压力锻模,平锻机用锻模,水压机用锻模,高速锤用锻模,摆动碾压机用锻模,辊锻机用锻模,楔横轧机用锻模等。按工艺用途不同,锻模可分为预锻模具,挤压模具,精锻模具,等温模具,超塑性模具等。
(3) 塑料模:塑料模是塑料成型的工艺装备。塑料模约占模具总数的35%,而且有继续上升的趋势。塑料模主要包括压塑模,挤塑模,注射模,此外还有挤出成型模,泡沫塑料的发泡成型模,低发泡注射成
型模,吹塑模等。
(4) 压铸模:压铸模是压力铸造工艺装备,压力铸造是使液态金属在高温和高速下充填铸型,在高压下成型和结晶的一种特殊制造方法。压铸模约占模具总数的6%。
(5) 粉末冶金模:粉末冶金模用于粉末成型,按成型工艺分类粉末冶金模有:压模,精整模,复压模,热压模,粉浆浇注模,松装烧结模等。
模具所涉及的工艺繁多,包括机械设计制造,塑料,橡胶加工,金属材料,铸造(凝固理论),塑性加工,玻璃等诸多学科和行业,是一个多学科的综合,其复杂程度显而易见。
三、我国模具技术的现状及发展趋势
20世纪80年代开始,发达工业国家的模具工业已从机床工业中分离出来,并发展成为独立的工业部门,其产值已超过机床工业的产值。改革开放以来,我国的模具工业发展也十分迅速。近年来,每年都以15%的增长速度快速发展。许多模具企业十分重视技术发展。加大了用于技术进步的投入力度,将技术进步作为企业发展的重要动力。此外,许多科研机构和大专院校也开展了模具技术的研究与开发。模具行业的快速发展是使我国成为世界超级制造大国的重要原因。今后,我国要发展成为世界制造强国,仍将依赖于模具工业的快速发展,成为模具制造强国。
尽管我国模具工业有了长足的进步,部分模具已达到国际先进水平,但无论是数量还是质量仍满足不了国内市场的需要,每年仍需进
口10多亿美元的各类大型,精密,复杂模具。与发达国家的模具工业相比,在模具技术上仍有不小的差距。今后,我国模具行业应在以下几方面进行不断的技术创新,以缩小与国际先进水平的距离。
(1) 注重开发大型,精密,复杂模具;随着我国轿车,家电等工业的快速发展,成型零件的大型化和精密化要求越来越高,模具也将日趋大型化和精密化。
(2) 加强模具标准件的应用;使用模具标准件不但能缩短模具制造周期,降低模具制造成本而且能提高模具的制造质量。因此,模具标准件的应用必将日渐广泛。
(3) 推广CAD/CAM/CAE技术;模具CAD/CAM/CAE技术是模具技术发展的一个重要里程碑。实践证明,模具CAD/CAM/CAE技术是模具设计制造的发展方向,可显著地提高模具设计制造水平。
(4) 重视快速模具制造技术,缩短模具制造周期;随着先进制造技术的不断出现,模具的制造水平也在不断地提高,基于快速成形的快速制模技术,高速铣削加工技术,以及自动研磨抛光技术将在模具制造中获得更为广泛的应用。
塑件工艺性分析
零件名称:塑料仪表盖(如图)
生产批量:大批量
材料:聚甲醛(POM)
平面图 立体图
一、塑件原材料分析
1、聚甲醛的工艺特性
干燥处理:如果材料储存在干燥环境中,通常不需要干燥处理
熔化温度:均聚物材料为190~230℃,共聚物材料为190~210℃ 模具温度:80~105℃,为了减小成型后收缩率可选用高一些的模具温度
注射压力:80~130MPa
注射速度:中等或偏高的注射速度
注射成型机类型:螺杆式
流道和浇口:可以使用任何类型的浇口,如果使用隧道形浇口,则最好使用较短的类型。对于均聚物材料,建议使用热注嘴流道,对于共聚物材料既可使用内部的热流道也可使用外部热流道。
化学和物理特性: POM是一种坚韧有弹性的材料,即使在低温下仍有很好的抗蠕变特性、几何稳定性和抗冲击特性。POM既有均聚物材料也有共聚物材料。均聚物材料具有很好的延展强度、抗疲劳强度,但不易于加工。共聚物材料有很好的热稳定性、
化学稳定性并且易于加
工。无论均聚物材料还是共聚物材料,都是结晶性材料并且不易吸收水分。
收缩率:POM的高结晶程度导致它有相当高的收缩率,可高达到
1.2%~3.0%。对于各种不同的增强型材料有不同的收缩率。
2、塑件的尺寸
塑件尺寸的大小受制于以下因素:
a)取决于用户的使用要求
b)受制于塑件的流动性
c)受制于塑料熔体在流动充填过程中所受到的结构阻力
3、塑件尺寸公差标准
影响塑件尺寸精度的因素主要有:
a)塑料材料的收缩率及其波动
b)塑件结构的复杂程度
c)模具因素(含模具制造、模具磨损及寿命、模具的装配、模具的合模及模具设计的不合理所可能带来的形位误差等)
d)成型工艺因素(模塑成型的温度T、压力p、时间t及取向、结晶、成型后处理等)
e)成型设备的控制精度等
其中,塑件尺寸精度主要取决于塑料收缩率的波动及模具制造误差,题中没有公差值,则我们按未注公差的尺寸许偏差计算,查表取MT5。
4、塑件的表面质量
塑件的表面质量包括塑件缺陷、表面光泽性与表面粗糙度,其与模塑成型工艺、塑料的品种、模具成型零件的表面粗糙度、模具的磨损程度等相关。
模具型腔的表面粗糙度通常应比塑件对应部位的表面粗糙度在数值上要低1~2级。
二、注塑成型的准备
1、注塑成型工艺条件
(1)温度;注塑成型过程中需要控制的温度有料筒温度,喷嘴温度和模具温度等。喷嘴温度通常略微低于料筒的最高温度,以防止熔料在直通式喷嘴口发生“流涎现象”;模具温度一般通过冷却系统来控制;为了保证制件有较高的形状和尺寸精度,应避免制件脱模后发生较大的翘曲变形,模具温度必须低于塑料的热变形温度。PS料与温度的经验数据如下表所示:
(2)压力;注射成型过程中的压力包括注射压力,保压力和背压力。注射压力用以克服熔体从料筒向型腔流动的阻力,提供充模速度及对熔料进行压实等。保压力的大小取决于模具对熔体的静水压力,与制件的形状,壁厚及材料有关。
(3)时间;完成一次注塑成型过程所需要的时间称为成型周期。包括
注射时间,保压时间,冷却时间,其他时间(开模,脱模,涂脱磨剂,安放嵌件和闭模等),在保证塑件质量的前提下尽量减小成型周期的各段时间,以提高生产率,其中,最重要的是注射时间和冷却时间,在实际生产中注射时间一般为3~5秒,保压时间一般为20~120秒,冷却时间一般为30~120秒(这三个时间都是根据塑件的质量来决定的,质量越大则相应的时间越长)。确定成型周期的经验数值如下表所示:
经过上面的经验数据和推荐值,可以初步确定成型工艺参数,因为各个推荐值有差别,而且有的与实际注塑成型时的参数设置也不一致,结合两者的合理因素,初定制品成型工艺参数如下表所示:
2、注塑机的选择 ① 塑件的投影面积计算 A=3.14×(1102-4×102-132)=11.53cm2 ② 型腔的压力计算P腔=2/3×P=86.7Mpa
③ 锁模力的计算F=AP腔 =11.53×86.7=999.7N
根据计算,查表选螺杆式注射机 :XS-ZY-250
注塑机的有关参数
3、注塑机的参数校核 根据以上计算,浇注系统的体积为V型 =23.7cm3
(1)最大注射量的校核计算
校核式:(0.8-0.85)V公≥V型
其中:V型 =23.7 cm3
(0.8-0.85) V公=0.8×250=200 cm3
可见满足校核式,即所设计模具注射量满足XS-ZY-250 最大注射量要求。
(2)注射机压力的校核
P机≥P塑
P机——注射机的最大注射压力,Mpa或N/cm3
P塑——成型塑件所需的注射压力,Mpa或N/cm3
一般PS取 100~140Mpa, XS-ZY-250注射机的最大注射压力P机=130Mpa,可见XS-ZY-250注射机满足PS注射压力的要求。
综合验证,XS-ZY-250型注射机完全能满足此模具的注射要求。
4、模具开模行程校核
模具开模行程应满足:Sm<SZ
其中:Sz为最大开模行程,查注射机
XS-ZY-250型Sz=500mm,
Sm为模具的开模行程;
Sm=塑件的高度+浇注系统的高度+顶件的顶出高度+(5-10)mm =75+98+65=238mm
可见Sm<SZ
模具设计
一、分型面的确定
根据分型面的选择原则:
(1)便于塑件脱模;
(2)在开模时尽量使塑件留在动模;
(3)外观不遭到损坏;
(4)有利于排气和模具的加工方便。
结合该产品的结构,分型面确定在塑件的最大投影面积上。如图:
二、型腔数目的确定
注塑模的型腔数目,可以是一模一腔,也可以是一模多腔,在型腔
数目的确定时主要考虑以下几个有关因素:
(1)塑件的尺寸精度;
(2)模具制造成本;
(3)注塑成型的生产效益;
(4)模具制造难度。
根据大批量生产要求,本模具采用一模两腔,塑件型腔位置对称分布。
三、浇口确定
根据塑件外形特征,确定使用侧浇口。
四、浇注系统设计
注塑模的浇注系统是指模具中从注塑机喷嘴开始到型腔入口为止的塑料熔体的流动通道,它由主流道,分流道,冷料穴和浇口组成。它向型腔中的传质,传热,传压情况决定着塑件的内在和外表质量,它的布置和安排影响着成型的难易程度和模具设计及加工的复杂程度,所以浇注系统是模具设计中的主要内容之一。
浇注系统结构如下图:
五、主流道
主流道是连接注塑机的喷嘴与分流道的一段通道,通常和注塑机的喷嘴在同一轴线上,断面为圆形,有一定的锥度,目的是便于冷料的脱模,同时也改善料流的速度,因为要和注塑机相配,所以其尺寸与注塑机有关。查表得知XS-ZY-250型注射机的喷嘴孔直径d0=Φ9mm、喷嘴球半径R0=18mm,
故取模具浇口套主流道小端直径为:
d=d0+1=9+1=10mm
模具浇口套主流道球面半径为:
R=R0+(1~2)=18+2=20mm
将主流道设计成圆锥形,锥度取4°
由于主流道要与高温的塑料熔体和喷嘴反复接触和碰撞,所以主流道部分常设计成可拆卸的主流道浇口套,以便选用优质的钢材单独加工和热处理。
六、分流道
分流道是主流道与浇口之间的通道,一般开设在分型面上,起分流和转向作用,分流道的长度取决于模具型腔的总体布置和浇口位置,分流道的设计应尽可能短,以减少压力损失,热量损失和流道凝料。查表可知,聚甲醛分流道断面尺寸3.5~10mm.
七、冷料穴
冷料穴设置在主流道的末端,采用倒锥形的拉料穴拉料
八、浇口
浇口是连接分流道与型腔的一段细短的通道,它是浇注系统的关键部分,浇口的形状,数量,尺寸和位置对塑件的质量影响很大,浇口的主要作用有两个,一是塑料熔体流经的通道,二是浇口的适时凝固可控制保压时间。浇口的类型有很多,有点浇口,侧浇口,直接浇口,潜伏式浇口等,各浇口的应用和尺寸按塑件的形状和尺寸而定。该模具采用侧浇口,其尺寸如下:
t=kδ=0.7×2.5=1.55
侧浇口深度尺寸a的确定
a=1/3~2/3t=1.55×2/3 = 1mm
侧浇口宽度尺寸l的确定
l=0.7~2,取l=2
(k塑料系数POM取0.7;δ塑件在浇口位置处的壁厚,该设计取壁厚δ=2.5mm)
九、标准模架的选择
1、通过相关计算可知:
① 采用推杆推出制件
② 定模座板厚32mm,支承板厚50mm,垫块厚125mm,动模板厚100mm
2、模具高度尺寸的确定
安装模具的高度应满足: Hmin<H<Hmax
设计模具高度为H总=389mm
XS-ZY-250型注射机所允许模具的最小厚度为Hmin=200mm,最大厚度为Hmax=400mm,H总=389mm介于二者之间,模具闭合高度满足安装
要求。
十、导向与定位机构
注射模的导向机构主要有导柱导向和锥面定位两种类型。导柱导向机构用于动、定模之间的开合模导向和脱模机构的运动导向。锥面定位机构用于动、定模之间的精密对中定位。
导柱:国家标准规定了两种结构形式,分为带头导柱和有肩导柱,大型而长的导柱应开设油槽,内存润滑剂,以减小导柱导向的摩擦。若导柱需要支撑模板的重量,特别对于大型、精密的模具,导柱的直径需要进行强度校核。
导套:导套分为直导套和带头导套,直导套装入模板后,应有防
止被拔出的结构,带头导柱轴向固定容易。
设计导柱和导套需要注意的事项有:
(1) 合理布置导柱的位置,导柱中心至模具外缘至少应有一个导柱直径的厚度;导柱不应设在矩形模具四角的危险断面上。通常设在长边离中心线的1/3处最为安全。导柱布置方式常采用等径不对称布置,或不等直径对称布置。
(2) 导柱工作部分长度应比型芯端面高出6~8 mm,以确保其导向与引导作用。
(3) 导柱工作部分的配合精度采用H7/f7,低精度时可采取更低的配合要求;导柱固定部分配合精度采用H7/k6;导套外径的配合精度采取H7/k6。配合长度通常取配合直径的1.5~2倍,其余部分可以扩孔,以减小摩擦,降低加工难度。
(4) 导柱可以设置在动模或定模,设在动模一边可以保护型芯不受损坏,设在定模一边有利于塑件脱模。
十一、顶出系统设计
注射成型每一循环中,塑件必须准确无误地从模具的凹模或型芯上脱出,完成脱出塑件的装置称为脱模机构,也称顶出机构。 脱模机构的设计一般遵循以下原则:
(1) 塑件滞留于动模边,以便借助于开模力驱动脱模装置,完成脱模动作。
(2) 由于塑件收缩时包紧型芯,因此推出力作用点尽量靠近型芯,同时推出力应施于塑件刚性和强度最大的部位。
(3) 结构合理可靠,便于制造和维护。
本设计使用简单的推杆脱模机构,因为该塑件的分型面简单,结构也不复杂,采用推简单的脱模机构可以简化模具结构,给制造和维护带来方便。在对脱模机构做说明之前,需要对脱模力做个简单的计算。
推杆脱模机构是最简单、最常用的一种形式,具有制造简单、更换方便、推出效果好等特点。推杆直接与塑件接触,开模后将塑件推出。
推杆的截面形状;可分为圆形,方形或椭圆形等其它形状,根据塑件的推出部位而定,最常用的截面形状为圆形;推杆又分为普通推杆和成型推杆两种,前者只是起到将塑件推出的作用,后者不仅如此还能参与局部成型,所以,推杆的使用是非常灵活的。
1、脱模力的计算
由于Qe=Qc+Qb,式中:
Qc—制品对型芯包紧的脱模阻力(N),
Qb—使封闭壳体脱模需克服的真空吸力(N),
Qb=0.1Ab,0.1的单位为Mpa,Ab为型芯的横截面面积mm2, Ab=38.59×115.28=4448.66mm2,Qb=0.1×4448.66=444.9N, 对于制品dk=(l+b)/2=(54+21)/2=37.5,
dk/t=37.5/2=18.75<20属于薄壁制品。
Qc=[2(l+b)EεhKf]/(1+u+Kλ)cosβ,式中:
E—塑料的拉伸弹性模量(Mpa),查表取1.95×103,
ε—塑料的平均成形收缩率,查表取0.5%,
u—塑料的泊松比,查表取0.3,
b—矩形型芯断面的两边长度(mm),
β—型芯的脱模斜度,
h—脱模方向高度(mm),
Kf—脱模斜度修正系数,计算式为:
Kf=(f cosβ-sinβ)/(1+ f cosβsinβ)
=(0.45 cos6- sin6)/(1+0.45 cos6 sin6)=0.3
f—制品与钢材表面之间的静摩檫系数,查表取0.45,
Kλ—薄壁制品的计算系数,
Kλ= 2λ2/(cosβ+2λcosβ),式中:
λ—比例系数,λ=rcp/t,
β—塑件脱模斜度,
rcp—型芯的平均半径(mm),(对于型芯,rcp=(l+b)/∏=(54+21)/ π=23.8 mm),
Kλ=2×(23.8/2)2/[cos6+2×(23.8/2)×cos6]=12.6
Qc=[2(l+b)EεhKf]/(1+u+Kλ)cosβ
Qc=[2(54+21)×1.95×103×0.5%×15×0.3]/[(1+0.3+12.6)×cos6]=4782N
则 Qe=444.9+4782=5226.9N
2、推杆尺寸计算:本设计采用的是推杆推出,在求出脱模力的前提下可以对推杆做出初步的直径预算并进行强度校核。本设计采用的是圆形推杆,圆形推杆的直径由欧拉公式简化为:
d=k(LQe/nE)1/4 =1.5×(257×5226.9/4×2.0×105)1/4=7.4mm d—推杆直径;
n—推杆的数量,n取4;
L—推杆长度(参考模架尺寸,估取L=257mm);
E—推杆材料的弹性模量,取E=2.1×105 MPa
k—安全系数,取k=1.5;
Qe—总的脱模力,Qe=5226.9(N);
实际推杆尺寸直径为8 mm。但为了安全起见,再对其进行强度校核,强度校核公式为:
d≥(4Qe/nπζ压)1/2= (4×5226.9/4×3.14×150)1/2=7.1mm (4-8)
满足强度要求。
ζ压—推杆材料的许用压应力, ζ压=150Mpa。
3、推杆的固定形式:推杆的固定形式有多种,但最常用的是推杆在固定板中的形式,此外还有螺钉紧固等形式。
4、推出机构的导向:当推杆较细或推杆数量较多时,为了防止因塑
件反阻力不均匀而导致推杆固定板扭曲或倾斜折断推杆或发生运动卡滞现象,需要在推出机构中设置导向零件,一般称为推板导柱。
5、推出机构的复位:脱模机构完成塑件的顶出后,为进行下一个循环必须回复到初始位置,目前常用的复位形式主要有复位杆复位和弹簧复位。本设计采用弹簧复位机构,弹簧复位机构是一种最简单的复位方式。推出时弹簧被压缩,而合模时弹簧的回力就将推出机构复位。
6、推杆与模体的配合:推杆和模体的配合性质一般为H8/f7或H7/f7,配合间隙值以熔料不溢料为标准。
十二、成型零件工作尺寸的计算
成型零件的工作尺寸是指凹模和凸模直接构成塑件的尺寸。凹、凸模工作尺寸的精度直接影响塑件的精度。
成型零件工作尺寸计算方法一般有两种:一种是平均值法,即按平均收缩率、平均制造公差和平均磨损量进行计算;另一种是按极限收缩率、极限制造公差和磨损量进行计算;前一种方法简便,但不适合精密塑件的模具设计,后一种复杂,但能较好的保证尺寸精度。本设计采用平均值法。
成型零件的尺寸计算如下表:
十三、排气设计 在塑料熔体填充注射模腔过程中,模腔内除了原有的空气外,还有塑料含有的水分在注射温度下蒸发而形成的水蒸汽,塑料局部分解产生的低分子挥发气体,塑料助剂挥发(或化学反应)所产生的气体以及热固性塑料交联硬化释放的气体等;这些气体如果不能被熔融塑料顺利地排出模腔,将在制件上形成气孔,接缝,表面轮廓不清,不能完全充满型腔,同时,还会因为气体被压缩而产生的高温灼伤制件,使之产生焦痕,色泽不佳等缺陷。
模具的排气可以利用排气槽排气,分型面排气,利用型芯,推杆,镶件等的间隙排气,POM推荐的排气槽深度为0.04。
1、 排气设计原则:
通常,选择排气槽的开设位置时,应遵循以下原则:
① 排气口不能正对操作者,以防熔料喷出而发生工伤事故; ② 最好开设在分型面上,如果产生飞边易随塑件脱出;
③ 最好设在凹模上,以便于模具加工和清模方便;
④ 开设在塑料熔体最后才能填充的模腔部位,如流道或冷料穴的终端;
⑤ 开设在靠近嵌件和制件壁最薄处,因为这样的部位最容易形成熔接痕;
⑥ 若型腔最后充满部位不在分型面上,其附近又无可供排气的推杆或活动的型心时, 可在型腔相应部位镶嵌烧结的多孔金属块,以供
排气;
⑦ 高速注射薄壁型制件时,排气槽设在浇口附近,可使气体连续排出;
若制件具有高深的型腔,那么在脱模时需要对模具设置引气系统,那是因为制件表面与型心表面之间在脱模过程中形成真空,难于脱模,制件容易变形或损坏。热固性塑料制件在型腔内的收缩小,特别是不采用镶拼结构的深型腔,在开模时空气无法进入型腔与制件之间,使制件附粘在型腔的情况比热塑性制件更甚,因此,必须引入引气系统。
2、推杆、镶件排气功能的证明
由上面我们知道,推杆和型芯的公差配合取H8/f7,属于间隙配合,现在计算这个配合的极限间隙。推杆外径为4mm,所以计算Φ4 H8/f7。 解:Φ4 H8/f7的极限偏差
查表求得基本尺寸Φ4的标准公差IT8=18μm,IT7=12μm。 孔、轴的上、下偏差为:
基准孔H8 EI=0; ES=EI+IT8=0+18=18μm
基准轴f7 es=-10;
ei=es-IT7=-10-12=-22μm
孔、轴的极限偏差分别为:Φ4H8 0+18Φ4f7-10-22
Φ4 H8/f7的极限间隙为:
Xmax=ES-ei=18-(-22)=40μm
Xmin=EI-es=0-(-10)=10μm
从计算结果看,间隙在0.01~0.04 mm之间,公差带图如图4-5所示。相比排气槽的深度0.02,似乎推杆能更好的排气,这也说明了,增加推杆和镶件等可以有利于型腔的排气
十四、温度调节系统设计
在注塑成型过程中,模具的温度直接影响到塑件成型的质量和生产效率。由于各种塑料的性能和成型工艺要求不同,模具的温度要求也不同。流动性差的塑料如PC,POM等,要求模具温度高,温度过低会影响塑料的流动,增大流动剪切力,使塑件内应力增大,出现冷流痕,银丝,注不满等缺陷。普通的模具通入常温的水进行冷却,通过调节水的流量就可以调节模具的温度,为了缩短成型周期,还可以把常温的水降低温度后再通入模内,可以提高成型效率。对于高熔点,流动性差的塑料,流动距离长的制件,为了防止填充不足,有时也在水管中通入温水把模具加热。POM推荐的成型温度为170~280℃,模具温度为20~70℃ 。
1、温度调节对塑件质量的影响
1)采用较低的模温可以减小塑料制件的成型收缩率;
2)模温均匀,冷却时间短,注射速度快可以减少塑件的变形
3)对塑件表面粗糙度影响最大的除型腔表面加工质量外就是模具温度,提高模温能大大改善塑件的表面状态;
温度对塑件质量的影响有相互矛盾的地方,设计时要根据材料特性和使用要求偏重于主要要求。
2、对温度调节系统的要求
1)根据塑料的品种确定是对模具采用加热方式还是冷却方式;
2)希望模温均一,塑件各部同时冷却,以提高生产率和提高塑件质量;
3)采用低的模温,快速,大流量通水冷却效果一般比较好;
4)温度调节系统应尽可能做到结构简单,加工容易,成本低廉; 从成型温度和使用要求看,需要对该模具进行冷却,以提高生产率。
3、冷却系统设计:
设计原则:
1)尽量保证塑件收缩均匀,维持模具的热平衡;
2)冷却水孔的数量越多,孔径越大,则对塑件的冷却效果越好;
3)尽可能使冷却水孔至型腔表面的距离相等,与制件的壁厚距离相等,经验表明,冷却水管中心距B大约为2.5~3.5D,冷却水管壁距模具边界和制件壁的距离为0.8~1.5B。最小不要小于10。
4)浇口处加强冷却,冷却水从浇口处进入最佳;
5)应降低进水和出水的温差,进出水温差一般不超过5℃
6)冷却水的开设方向以不影响操作为好,对于矩形模具,通常沿宽度方向开设水孔。
7)合理确定冷却水道的形式,确定冷却水管接头位置,避免与模具的其他机构发生干涉。