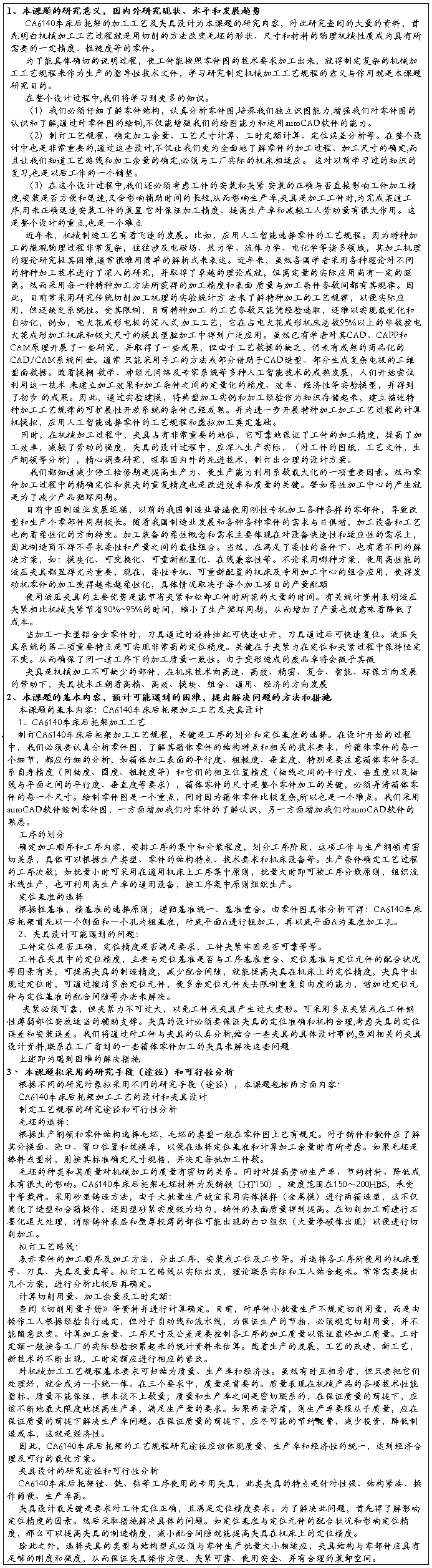
第二篇:CA6140机床后托架加工工艺及夹具设计11
山西农业大学课程设计(论文)
CA6140车床后托架
加工工艺及夹具设计
学生姓名: 蒙建国
学生学号:2006151111
院 (系): 工学院
专业:机械设计制造及自动化
指导教师: 张秀全
二〇一零年四月
摘 要
在生产过程中,使生产对象(原材料,毛坯,零件或总成等)的质和量的状态发生直接变化的过程叫工艺过程,如毛坯制造,机械加工,热处理,装配等都称之为工艺过程。在制定工艺过程中,要确定各工序的安装工位和该工序需要的工步,加工该工序的机车及机床的进给量,切削深度,主轴转速和切削速度,该工序的夹具,刀具及量具,还有走刀次数和走刀长度,最后计算该工序的基本时间,辅助时间和工作地服务时间。
关键词 工序,工艺,工步,加工余量,定位方案,夹紧力
ABSTRACT
Enable producing the target in process of production (raw materials, the blank , state of quality and quantity on part become always ) take place direct course of change ask craft course, if the blank is made, machining, heat treatment , assemble etc. and call it the craft course. In the course of making the craft , is it confirm every erector location and worker step that process need this of process to want, the locomotive of processing , this process , and the entering the giving amount of the lathe, cut depth , the rotational speed of the main shaft and speed of cutting, the jig of this process, the cutter and measuring tool, a one hundred sheets of number of times still leaves and a one hundred sheets of length leaves, calculate basic time of this process , auxiliary time and service time of place of working finally.
Keywords: The process, worker one, worker's step , the surplus of processing, orient the scheme , clamp strength
目 录
摘 要......................................................................................................................... I
ABSTRACT................................................................................................................ II
1 CA6140机床后托架加工工艺............................................................................ 3
1.1 CA6140机床后托架的工艺分析.......................................................................... 3
1.2 CA6140机床后托架的工艺要求及工艺分析....................................................... 3
1.2.1 CA6140机床`后托架的技术要求...................................................................... 4
1.3 加工工艺过程...................................................................................................... 4
1.4 确定各表面加工方案........................................................................................... 4
1.4.1 在选择各表面及孔的加工方法时,要综合考虑以下因素.................................. 5
1.4.2 平面的加工.................................................................................................... 5
1.4.3孔的加工方案.................................................................................................. 5
1.5 确定定位基准...................................................................................................... 6
1.5.1 粗基准的选择................................................................................................. 6
1.5.2 精基准选择的原则.......................................................................................... 7
1.6 工艺路线的拟订.................................................................................................. 7
1.6.1工序的合理组合.............................................................................................. 7
1.6.2 工序的集中与分散.......................................................................................... 8
1.6.3 加工阶段的划分............................................................................................. 9
1.6.4 加工工艺路线方案的比较............................................................................. 10
1.7 CA6140机床后托架的偏差,加工余量,工序尺寸及毛坯尺寸的确定............ 13
1.7.1 毛坯的结构工艺要求.................................................................................... 13
1.7.2 CA6140机床后托架的偏差计算...................................................................... 13
1.8 确定切削用量及基本工时(机动时间)........................................................... 17
1.8.1 工序1:粗、精铣底面.................................................................................. 17
1.8.2 工序2 粗、半精、精镗CA6140侧面三杠孔................................................. 18
1.8.3 工序3:钻顶面四孔..................................................................................... 25
1.8.4 工序4:钻侧面两孔..................................................................................... 29
1.9 时间定额计算及生产安排................................................................................. 31
1.9.1 粗、精铣底面............................................................................................... 31
1.9.2 镗侧面三杠孔............................................................................................... 32
1.9.3 钻顶面四孔.................................................................................................. 33
2 专用夹具设计...................................................................................................... 35
2.1 铣平面夹具设计................................................................................................ 35
2.1.1 研究原始质料............................................................................................... 35
2.1.2 定位基准的选择........................................................................................... 35
2.1.3 切削力及夹紧分析计算................................................................................. 35
2.1.4 误差分析与计算........................................................................................... 36
2.1.5 夹具设计及操作的简要说明.......................................................................... 37
2.2 镗孔夹具设计.................................................................................................... 37
2.2.1 研究原始质料............................................................................................... 37
2.2.2 定位基准的选择........................................................................................... 37
2.2.3 切削力及夹紧力的计算................................................................................. 38
2.2.4 误差分析与计算........................................................................................... 40
2.3钻顶面四孔夹具设计......................................................................................... 40
2.3.1 研究原始质料............................................................................................... 40
2.3.2 定位基准的选择........................................................................................... 41
2.3.3 切削力及夹紧力的计算................................................................................. 41
2.3.4 误差分析与计算........................................................................................... 42
2.3.5 夹具设计及操作的简要说明.......................................................................... 42
结 论......................................................................................................................... 43
参考文献.................................................................................................................... 44
致 谢......................................................................................................................... 45
1 CA6140机床后托架加工工艺
1.1 CA6140机床后托架的工艺分析
CA6140机床后托架的是CA6140机床的一个重要零件,因为其零件尺寸较小,结构形状也不是很复杂,但侧面三杠孔和底面的精度要求较高,此外还有顶面的四孔要求加工,但是对精度要求不是很高。后托架上的底面和侧面三杠孔的粗糙度要求都是,所以都要求精加工。其三杠孔的中心线和底平面有平面度的公差要求等。因为其尺寸精度、几何形状精度和相互位置精度,以及各表面的表面质量均影响机器或部件的装配质量,进而影响其性能与工作寿命,因此它的加工是非常关键和重要的。
1.2 CA6140机床后托架的工艺要求及工艺分析
图1.1 CA6140机床后托架零件图
一个好的结构不但要应该达到设计要求,而且要有好的机械加工工艺性,也就是要有加工的可能性,要便于加工,要能够保证加工质量,同时使加工的劳动量最小。而设计和工艺是密切相关的,又是相辅相成的。设计者要考虑加工工艺问题。工艺师要考虑如何从工艺上保证设计的要求。
1.2.1 CA6140机床后托架的技术要求
其加工有三组加工。底面、侧面三孔、顶面的四个孔、以及左视图上的两个孔。
⑴.以底面为主要加工的表面,有底面的铣加工,其底面的粗糙度要求是,平面度公差要求是0.03。
⑵.另一组加工是侧面的三孔,分别为,
,
,其表面粗糙度要求
要求的精度等级分别是
,
,
。
⑶.以顶面为住加工面的四个孔,分别是以和
为一组的阶梯空,这组孔的表面粗糙度要求是
,
,以及以
和
的阶梯孔,其中
是装配铰孔,其中
孔的表面粗糙度要求是
,
,
是装配铰孔的表面粗糙度的要求是
。
⑷.CA6140机床后托架毛坯的选择金属行浇铸,因为生产率很高,所以可以免去每次造型。
单边余量一般在,结构细密,能承受较大的压力,占用生产的面积较小。因为CA6140机床后托架的重量只有3.05kg,而年产量是5000件,由[7]《机械加工工艺手册》表2.1-3可知是中批量生产。
1.3 加工工艺过程
由以上分析可知。该箱体零件的主要加工表面是平面及孔系。一般来说,保证平面的加工精度要比保证孔系的加工精度容易。因此,对于CA6140机床后托架来说,加工过程中的主要问题是保证孔的尺寸精度及位置精度,处理好孔和平面之间的相互关系。
由上面的一些技术条件分析得知:CA6140后托架的尺寸精度,形状机关度以及位置机精度要求都很高,就给加工带来了困难,必须重视。
1.4 确定各表面加工方案
一个好的结构不但应该达到设计要求,而且要有好的机械加工工艺性,也就是要有加工的可能性,要便于加工,要能保证加工的质量,同时是加工的劳动量最小。设计和工艺是密切相关的,又是相辅相成的。对于我们设计CA6140机床后托架的加工工艺来说,应选择能够满足孔系加工精度要求的加工方法及设备。除了从加工精度和加工效率两方面考虑以外,也要适当考虑经济因素。在满足精度要求及生产率的条件下,应选择价格较底的机床。
1.4.1 在选择各表面及孔的加工方法时,要综合考虑以下因素
⑴.要考虑加工表面的精度和表面质量要求,根据各加工表面的技术要求,选择加工方法及分几次加工。
⑵.根据生产类型选择,在大批量生产中可专用的高效率的设备。在单件小批量生产中则常用通用设备和一般的加工方法。如、柴油机连杆小头孔的加工,在 小批量生产时,采用钻、扩、铰加工方法;而在大批量生产时采用拉削加工。
⑶.要考虑被加工材料的性质,例如,淬火钢必须采用磨削或电加工;而有色金属由于磨削时容易堵塞砂轮,一般都采用精细车削,高速精铣等。
⑷.要考虑工厂或车间的实际情况,同时也应考虑不断改进现有加工方法和设备,推广新技术,提高工艺水平。
⑸.此外,还要考虑一些其它因素,如加工表面物理机械性能的特殊要求,工件形状和重量等。
选择加工方法一般先按这个零件主要表面的技术要求选定最终加工方法。再选择前面各工序的加工方法,如加工某一轴的主要外圆面,要求公差为IT6,表面粗糙度为Ra0.63μm,并要求淬硬时,其最终工序选用精度,前面准备工序可为粗车——半精车——淬火——粗磨。
1.4.2 平面的加工
由参考文献[7]《机械加工工艺手册》表2.1-12可以确定,底面的加工方案为底平面:粗铣——精铣(),粗糙度为
6.3~0.8,一般不淬硬的平面,精铣的粗糙度可以较小。
1.4.3孔的加工方案
⑴.由参考文献[7]《机械加工工艺手册》表2.1-11确定,以为孔的表面粗糙度为1.6,则选侧孔(,
,
)的加工顺序为:粗镗——精镗。
⑵.而顶面的四个孔采取的加工方法分别是:
因为孔的表面粗糙度的要求都不高,是,所以我们采用一次钻孔的加工方法,
的孔选择的加工方法是钻,因为
的孔和
是一组阶梯孔,所以可以在已经钻了
的孔基础上再锪孔钻锪到
,而另一组
和
也是一组阶梯的孔,不同的是
的孔是锥孔,起表面粗糙度的要求是
,所以全加工的方法是钻——扩——铰。
1.5 确定定位基准
1.5.1 粗基准的选择
选择粗基准时,考虑的重点是如何保证各加工表面有足够的余量,使不加工表面与加工表面间的尺寸、位子符合图纸要求。
粗基准选择应当满足以下要求:
⑴.粗基准的选择应以加工表面为粗基准。目的是为了保证加工面与不加工面的相互位置关系精度。如果工件上表面上有好几个不需加工的表面,则应选择其中与加工表面的相互位置精度要求较高的表面作为粗基准。以求壁厚均匀、外形对称、少装夹等。
⑵.选择加工余量要求均匀的重要表面作为粗基准。例如:机床床身导轨面是其余量要求均匀的重要表面。因而在加工时选择导轨面作为粗基准,加工床身的底面,再以底面作为精基准加工导轨面。这样就能保证均匀地去掉较少的余量,使表层保留而细致的组织,以增加耐磨性。
⑶.应选择加工余量最小的表面作为粗基准。这样可以保证该面有足够的加工余量。
⑷.应尽可能选择平整、光洁、面积足够大的表面作为粗基准,以保证定位准确夹紧可靠。有浇口、冒口、飞边、毛刺的表面不宜选作粗基准,必要时需经初加工。
⑸.粗基准应避免重复使用,因为粗基准的表面大多数是粗糙不规则的。多次使用难以保证表面间的位置精度。
要从保证孔与孔、孔与平面、平面与平面之间的位置,能保证CA6140机床后托架在整个加工过程中基本上都能用统一的基准定位。从CA6140机床后托架零件图分析可知,选择侧面三孔作为CA6140机床后托架加工粗基准。
1.5.2 精基准选择的原则
⑴.基准重合原则。即尽可能选择设计基准作为定位基准。这样可以避免定位基准与设计基准不重合而引起的基准不重合误差。
⑵.基准统一原则,应尽可能选用统一的定位基准。基准的统一有利于保证各表面间的位置精度,避免基准转换所带来的误差,并且各工序所采用的夹具比较统一,从而可减少夹具设计和制造工作。例如:轴类零件常用顶针孔作为定位基准。车削、磨削都以顶针孔定位,这样不但在一次装夹中能加工大多书表面,而且保证了各外圆表面的同轴度及端面与轴心线的垂直度。
⑶.互为基准的原则。选择精基准时,有时两个被加工面,可以互为基准反复加工。例如:对淬火后的齿轮磨齿,是以齿面为基准磨内孔,再以孔为基准磨齿面,这样能保证齿面余量均匀。
自为基准原则。有些精加工或光整加工工序要求余量小而均匀,可以选择加工表面本身为基准。例如:磨削机床导轨面时,是以导轨面找正定位的。此外,像拉孔在无心磨床上磨外圆等,都是自为基准的例子。
此外,还应选择工件上精度高。尺寸较大的表面为精基准,以保证定位稳固可靠。并考虑工件装夹和加工方便、夹具设计简单等。
要从保证孔与孔、孔与平面、平面与平面之间的位置,能保证CA6140机床后托架在整个加工过程中基本上都能用统一的基准定位。从CA6140机床后托架零件图分析可知,它的底平面与侧面三孔平行而且占有的面积较大,适于作精基准使用。但用一个平面定位仅仅能限制工件的三个自由度,如果使用典型的一面两孔定位方法,则可以满足整个加工过程中基本上都采用统一的基准定位的要求。至于两侧面,因为是非加工表面,所以也可以用与顶平面的四孔的加工基准。
选择精基准的原则时,考虑的重点是有利于保证工件的加工精度并使装夹准。
1.6 工艺路线的拟订
对于大批量生产的零件,一般总是首先加工出统一的基准。CA6140机床后托架的加工的第一个工序也就是加工统一的基准。具体安排是先以孔定位粗、精加工顶平面。
后续工序安排应当遵循粗精分开和先面后孔的原则。
1.6.1工序的合理组合
确定加工方法以后,就按生产类型、零件的结构特点、技术要求和机床设备等具体生产条件确定工艺过程的工序数。确定工序数的基本原则:
⑴.工序分散原则
工序内容简单,有利选择最合理的切削用量。便于采用通用设备。简单的机床工艺装备。生产准备工作量少,产品更换容易。对工人的技术要求水平不高。但需要设备和工人数量多,生产面积大,工艺路线长,生产管理复杂。
⑵.工序集中原则
工序数目少,工件装,夹次数少,缩短了工艺路线,相应减少了操作工人数和生产面积,也简化了生产管理,在一次装夹中同时加工数个表面易于保证这些表面间的相互位置精度。使用设备少,大量生产可采用高效率的专用机床,以提高生产率。但采用复杂的专用设备和工艺装备,使成本增高,调整维修费事,生产准备工作量大。
一般情况下,单件小批生产中,为简化生产管理,多将工序适当集中。但由于不采用专用设备,工序集中程序受到限制。结构简单的专用机床和工夹具组织流水线生产。
加工工序完成以后,将工件清洗干净。清洗是在的含0.4%—1.1%苏打及0.25%—0.5%亚硝酸钠溶液中进行的。清洗后用压缩空气吹干净。保证零件内部杂质、铁屑、毛刺、砂粒等的残留量不大于
。
1.6.2 工序的集中与分散
制订工艺路线时,应考虑工序的数目,采用工序集中或工序分散是其两个不同的原则。所谓工序集中,就是以较少的工序完成零件的加工,反之为工序分散。
⑴.工序集中的特点
工序数目少,工件装,夹次数少,缩短了工艺路线,相应减少了操作工人数和生产面积,也简化了生产管理,在一次装夹中同时加工数个表面易于保证这些表面间的相互位置精度。使用设备少,大量生产可采用高效率的专用机床,以提高生产率。但采用复杂的专用设备和工艺装备,使成本增高,调整维修费事,生产准备工作量大。
⑵.工序分散的特点
工序内容简单,有利选择最合理的切削用量。便于采用通用设备。简单的机床工艺装备。生产准备工作量少,产品更换容易。对工人的技术要求水平不高。但需要设备和工人数量多,生产面积大,工艺路线长,生产管理复杂。
工序集中与工序分散各有特点,必须根据生产类型。加工要求和工厂的具体情况进行综合分析决定采用那一种原则。
一般情况下,单件小批生产中,为简化生产管理,多将工序适当集中。但由于不采用专用设备,工序集中程序受到限制。结构简单的专用机床和工夹具组织流水线生产。
由于近代计算机控制机床及加工中心的出现,使得工序集中的优点更为突出,即使在单件小批生产中仍可将工序集中而不致花费过多的生产准备工作量,从而可取的良好的经济效果。
1.6.3 加工阶段的划分
零件的加工质量要求较高时,常把整个加工过程划分为几个阶段:
⑴.粗加工阶段
粗加工的目的是切去绝大部分多雨的金属,为以后的精加工创造较好的条件,并为半精加工,精加工提供定位基准,粗加工时能及早发现毛坯的缺陷,予以报废或修补,以免浪费工时。
粗加工可采用功率大,刚性好,精度低的机床,选用大的切前用量,以提高生产率、粗加工时,切削力大,切削热量多,所需夹紧力大,使得工件产生的内应力和变形大,所以加工精度低,粗糙度值大。一般粗加工的公差等级为IT11~IT12。粗糙度为Ra80~100μm。
⑵.半精加工阶段
半精加工阶段是完成一些次要面的加工并为主要表面的精加工做好准备,保证合适的加工余量。半精加工的公差等级为IT9~IT10。表面粗糙度为Ra10~1.25μm。
⑶.精加工阶段
精加工阶段切除剩余的少量加工余量,主要目的是保证零件的形状位置几精度,尺寸精度及表面粗糙度,使各主要表面达到图纸要求.另外精加工工序安排在最后,可防止或减少工件精加工表面损伤。
精加工应采用高精度的机床小的切前用量,工序变形小,有利于提高加工精度.精加工的加工精度一般为IT6~IT7,表面粗糙度为 Ra10~1.25μm。
⑷.光整加工阶段
对某些要求特别高的需进行光整加工,主要用于改善表面质量,对尺度精度改善很少。一般不能纠正各表面相互位置误差,其精度等级一般为IT5~IT6,表面粗糙度为Ra1.25~0.32μm。
此外,加工阶段划分后,还便于合理的安排热处理工序。由于热处理性质的不同,有的需安排于粗加工之前,有的需插入粗精加工之间。
但须指出加工阶段的划分并不是绝对的。在实际生活中,对于刚性好,精度要求不高或批量小的工件,以及运输装夹费事的重型零件往往不严格划分阶段,在满足加工质量要求的前提下,通常只分为粗、精加工两个阶段,甚至不把粗精加工分开。必须明确划分阶段是指整个加工过程而言的,不能以某一表面的加工或某一工序的性质区分。例如工序的定位精基准面,在粗加工阶段就要加工的很准确,而在精加工阶段可以安排钻小空之类的粗加工。
1.6.4 加工工艺路线方案的比较
在保证零件尺寸公差、形位公差及表面粗糙度等技术条件下,成批量生产可以考虑采用专用机床,以便提高生产率。但同时考虑到经济效果,降低生产成本,拟订两个加工工艺路线方案。见下表:
表1.1加工工艺路线方案比较表
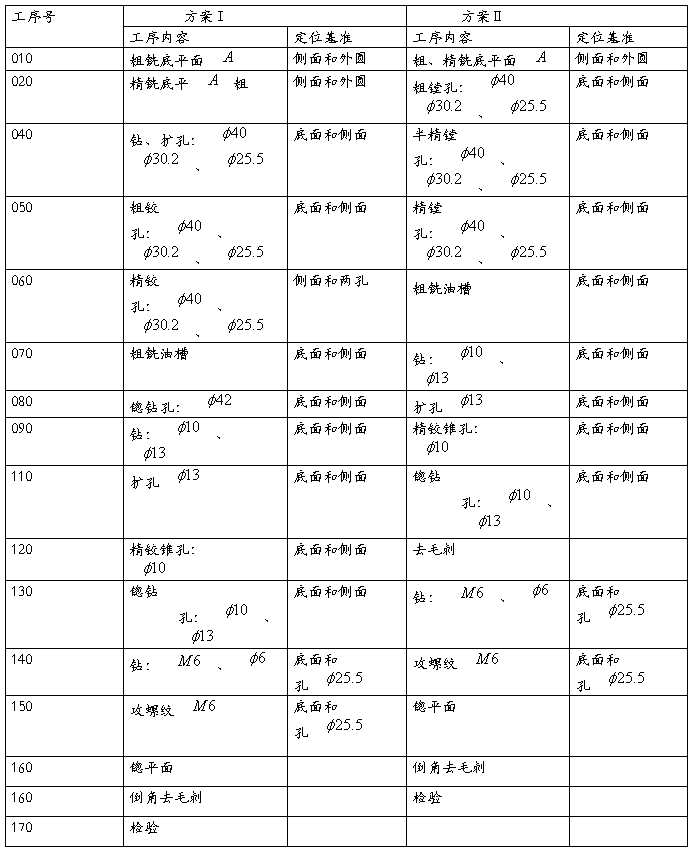
加工工艺路线方案的论证:
⑴.方案Ⅱ在120工序中按排倒角去毛刺,这不仅避免划伤工人的手,而且给以后的定位及装配得到可靠的保证。
⑵.方案Ⅱ在010工序中先安排铣底平面,主要是因为底平面是以后工序的主要定位面之一,为提高定位精度。
⑶.方案Ⅱ符合粗精加工分开原则。
由以上分析:方案Ⅱ为合理、经济的加工工艺路线方案。具体的工艺过程如下表:
表1.2加工工艺过程表
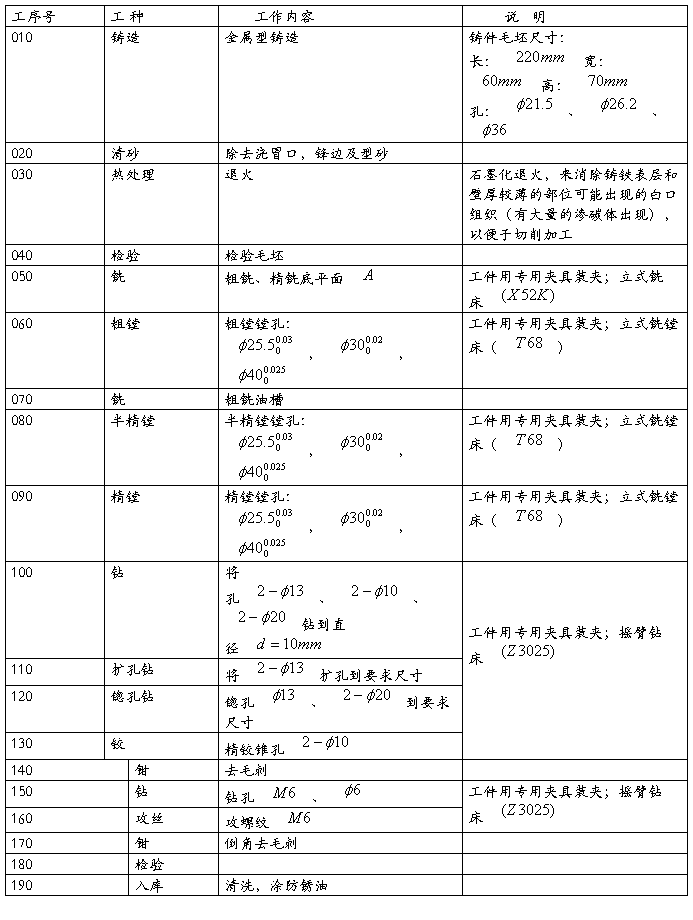
1.7 CA6140机床后托架的偏差,加工余量,工序尺寸及毛坯尺寸的确定
CA6140机床后托架的铸造采用的是铸铁制造,其材料是HT150,硬度HB为150-200,生产类型为中批量生产,采用铸造毛坯。
1.7.1 毛坯的结构工艺要求
⑴.CA6140车床后托架为铸造件,对毛坯的结构工艺有一定要求:
①、铸件的壁厚应和合适,均匀,不得有突然变化。
②、铸造圆角要适当,不得有尖角。
③、铸件结构要尽量简化,并要有和合理的起模斜度,以减少分型面、芯子、并便于起模。
④、加强肋的厚度和分布要合理,以免冷却时铸件变形或产生裂纹。
⑤、铸件的选材要合理,应有较好的可铸性。
毛坯形状、尺寸确定的要求
⑵.设计毛坯形状、尺寸还应考虑到:
①、各加工面的几何形状应尽量简单。
②、工艺基准以设计基准相一致。
③、便于装夹、加工和检查。
④、结构要素统一,尽量使用普通设备和标准刀具进行加工。
在确定毛坯时,要考虑经济性。虽然毛坯的形状尺寸与零件接近,可以减少加工余量,提高材料的利用率,降低加工成本,但这样可能导致毛坯制造困难,需要采用昂贵的毛坯制造设备,增加毛坯的制造成本。因此,毛坯的种类形状及尺寸的确定一定要考虑零件成本的问题但要保证零件的使用性能。在毛坯的种类
形状及尺寸确定后,必要时可据此绘出毛坯图。
1.7.2 CA6140机床后托架的偏差计算
⑴.底平面的偏差及加工余量计算
底平面加工余粮的计算,计算底平面与孔(,
,
)的中心线的尺寸为
。根据工序要求,顶面加工分粗、精铣加工。各工步余量如下:
粗铣:由参考文献[5]《机械加工工艺手册第1卷》表3.2-23。其余量值规定为,现取
。表3.2-27粗铣平面时厚度偏差取
。
精铣:由参考文献[7]《机械加工工艺手册》表2.3-59,其余量值规定为。
铸造毛坯的基本尺寸为,又根据参考文献[7]《机械加工工艺手册》表2.3-11,铸件尺寸公差等级选用CT7,再查表2.3-9可得铸件尺寸公差为
毛坯的名义尺寸为:
毛坯最小尺寸为:
毛坯最大尺寸为:
粗铣后最大尺寸为:
粗铣后最小尺寸为:
精铣后尺寸与零件图尺寸相同,即与侧面三孔(,
,
)的中心线的尺寸为
。
⑵.正视图上的三孔的偏差及加工余量计算
参照参考文献[7]《机械加工工艺手册》表2.3-59和参考文献[15]《互换性与技术测量》表1-8,可以查得:
孔:
粗镗的精度等级:,表面粗糙度
,尺寸偏差是
半精镗的精度等级:,表面粗糙度
,尺寸偏差是
精镗的精度等级:,表面粗糙度
,尺寸偏差是
孔
粗镗的精度等级:,表面粗糙度
,尺寸偏差是
半精镗的精度等级:,表面粗糙度
,尺寸偏差是
精镗的精度等级:,表面粗糙度
,尺寸偏差是
孔
粗镗的精度等级:,表面粗糙度
,尺寸偏差是
半精镗的精度等级:,表面粗糙度
,尺寸偏差是
精镗的精度等级:,表面粗糙度
,尺寸偏差是
根据工序要求,侧面三孔的加工分为粗镗、半精镗、精镗三个工序完成,各工序余量如下:
粗镗: 孔,参照[7]《机械加工工艺手册》表2.3-48,其余量值为
;
孔,参照[7]《机械加工工艺手册》表2.3-48,其余量值为
;
孔,参照[7]《机械加工工艺手册》表2.3-48,其余量值为
。
半精镗: 孔,参照[7]《机械加工工艺手册》表2.3-48,其余量值为
;
孔,参照[7]《机械加工工艺手册》表2.3-48,其余量值为
;
孔,参照[7]《机械加工工艺手册》表2.3-48,其余量值为
。
精镗: 孔,参照[7]《机械加工工艺手册》表2.3-48,其余量值为
;
孔,参照[7]《机械加工工艺手册》表2.3-48,其余量值为
;
孔,参照[7]《机械加工工艺手册》表2.3-48,其余量值为
。
铸件毛坯的基本尺寸分别为:
孔毛坯基本尺寸为
:
;
孔毛坯基本尺寸为
:
;
孔毛坯基本尺寸为
:
。
根据参考文献[7]《机械加工工艺手册》表2.3-11,铸件尺寸公差等级选用CT7,再查表2.3-9可得铸件尺寸公差分别为:
孔毛坯名义尺寸为
:
;
毛坯最大尺寸为:
;
毛坯最小尺寸为:
;
粗镗工序尺寸为:
半精镗工序尺寸为:
精镗后尺寸是,已达到零件图尺寸要求
孔毛坯名义尺寸为
:
;
毛坯最大尺寸为:
;
毛坯最小尺寸为:
;
粗镗工序尺寸为:
;
半精镗工序尺寸为:
精镗后尺寸与零件图尺寸相同,即:
孔毛坯名义尺寸为
:
;
毛坯最大尺寸为:
;
毛坯最小尺寸为:
;
粗镗工序尺寸为:
半精镗工序尺寸为:
精镗后尺寸与零件图尺寸相同,即
⑶.顶面两组孔和
,以及另外一组
的锥孔和
毛坯为实心,不冲孔。两孔精度要求为,表面粗糙度要求为
。参照参考文献[7]《机械加工工艺手册》表2.3-47,表2.3-48。确定工序尺寸及加工余量为:
第一组:和
加工该组孔的工艺是:钻——扩——锪
钻孔:
扩孔:
(Z为单边余量)
锪孔:
(Z为单边余量)
第二组:的锥孔和
加工该组孔的工艺是:钻——锪——铰
钻孔:
锪孔:
(Z为单边余量)
铰孔:
1.8 确定切削用量及基本工时(机动时间)
1.8.1 工序1:粗、精铣底面
机床:双立轴圆工作台铣床
刀具:硬质合金端铣刀(面铣刀)材料:
齿数
⑴.粗铣
铣削深度:
每齿进给量:根据参考文献[7]《机械加工工艺手册》表2.4-73,取
铣削速度
:参照参考文献[7]《机械加工工艺手册》表2.4-81,取
机床主轴转速:
,
式(1.1)
实际铣削速度:
式(1.2)
进给量:
式(1.3)
工作台每分进给量:
:根据参考文献[7]《机械加工工艺手册》表2.4-81,
被切削层长度:由毛坯尺寸可知
刀具切入长度:
式(1.4)
取
刀具切出长度:取
走刀次数为1
机动时间:
式(1.5)
⑵.精铣:
铣削深度:
每齿进给量:根据参考文献[7]《机械加工工艺手册》表2.4-73,取
铣削速度
:参照参考文献[7]《机械加工工艺手册》表2.4-81,取
机床主轴转速,由式(1.1)有:
,
实际铣削速度,由式(1.2)有:
进给量,由式(1.3)有:
工作台每分进给量:
被切削层长度:由毛坯尺寸可知
刀具切入长度:精铣时
刀具切出长度:取
走刀次数为1。
机动时间,由式(1.5)有:
本工序机动时间
1.8.2 工序2 粗、半精、精镗CA6140侧面三杠孔
机床:卧式镗床
刀具:硬质合金镗刀,镗刀材料:
⑴.粗镗孔
切削深度:
,毛坯孔径
。
进给量:根据参考文献[7]《机械加工工艺手册》表2.4-66,刀杆伸出长度取
,切削深度为
。因此确定进给量
。
切削速度:参照参考文献[7]《机械加工工艺手册》表2.4-66取
机床主轴转速,由式(1.1)有:
,取
实际切削速度,由式(1.2)有:
工作台每分钟进给量:
式(1.7)
被切削层长度:
刀具切入长度:
式(1.6)
刀具切出长度:
取
行程次数:
机动时间,由式(1.5)有:
⑵.粗镗孔
切削深度:
,毛坯孔径
进给量:根据参考文献[7]《机械加工工艺手册》表2.4-66,刀杆伸出长度取
,切削深度为
。因此确定进给量
。
切削速度:参照参考文献[7]《机械加工工艺手册》表2.4-66,取
机床主轴转速,由式(1.1)有:
取
实际切削速度,由式(1.2)有:
工作台每分钟进给量,由式(1.7)有:
被切削层长度:
刀具切入长度,由式(1.6)有:
刀具切出长度:
取
行程次数:
机动时间,由式(1.5)有:
⑶.粗镗孔
切削深度:
,毛坯孔径
。
进给量:根据参考文献[7]《机械加工工艺手册》表2.4-66,刀杆伸出长度取
,切削深度为
。因此确定进给量
切削速度:参照参考文献[7]《机械加工工艺手册》表2.4-66,取
机床主轴转速,由式(1.1)有:
,取
实际切削速度,由式(1.2)有:
工作台每分钟进给量,由式(1.7)有:
被切削层长度:
刀具切入长度,由式(1.6)有:
刀具切出长度:
取
行程次数:
机动时间,由式(1.5)有:
⑷.半精镗孔
切削深度:
,粗镗后孔径
进给量:根据参考文献[7]《机械加工工艺手册》表2.4-66,刀杆伸出长度取
,切削深度为
。因此确定进给量
切削速度:参照参考文献[7]《机械加工工艺手册》表2.4-66,取:
机床主轴转速,由式(1.1)有
,取
实际切削速度,由式(1.2)有:
工作台每分钟进给量,由式(1.7)有:
被切削层长度:
刀具切入长度,由式(1.6)有:
刀具切出长度:
取
行程次数:
机动时间,由式(1.5)有:
⑸.半精镗孔
切削深度:,粗镗后孔径
进给量:根据参考文献[7]《机械加工工艺手册》表2.4-66,刀杆伸出长度取
,切削深度为
。因此确定进给量
切削速度:参照参考文献[7]《机械加工工艺手册》表2.4-66,取:
机床主轴转速,由式(1.1)有:
,取
实际切削速度,由式(1.2)有:
工作台每分钟进给量,由式(1.7)有:
被切削层长度:
刀具切入长度,由式(1.6)有:
刀具切出长度:
取
行程次数:
机动时间,由式(1.5)有:
⑹.半精镗孔
切削深度:
,粗镗后孔径
进给量:根据参考文献[7]《机械加工工艺手册》表2.4-66,刀杆伸出长度取
,切削深度为
。因此确定进给量
切削速度:参照参考文献[7]《机械加工工艺手册》表2.4-66,取
机床主轴转速,由式(1.1)有:
,取
实际切削速度,由式(1.2)有:
工作台每分钟进给量,由式(1.7)有:
被切削层长度:
刀具切入长度,由式(1.6)有:
刀具切出长度:
取
行程次数:
机动时间,由式(1.5)有:
⑺.精镗孔
切削深度:
,半精镗后孔径
进给量:根据参考文献[7]《机械加工工艺手册》表2.4-66,刀杆伸出长度取
,切削深度为
。因此确定进给量
切削速度:参照参考文献[7]《机械加工工艺手册》表2.4-66,取
机床主轴转速,由式(1.2)有:
,取
实际切削速度,由式(1.2)有:
工作台每分钟进给量,由式(1.7)有:
被切削层长度:
刀具切入长度,由式(1.6)有:
刀具切出长度:
取
行程次数:
机动时间,由式(1.5)有:
⑻.精镗孔
切削深度:
,半精镗后孔径
进给量:根据参考文献[7]《机械加工工艺手册》表2.4-66,刀杆伸出长度取
,切削深度为
。因此确定进给量
切削速度:参照参考文献[7]《机械加工工艺手册》表2.4-66,取
机床主轴转速,由式(1.1)有:
,取
实际切削速度,由式(1.2)有:
工作台每分钟进给量,由式(1.7)有:
被切削层长度:
刀具切入长度,由式(1.6)有:
刀具切出长度:
取
行程次数:
机动时间,由式(1.5)有:
⑼.精镗孔
切削深度:
,半精镗后孔径
进给量:根据参考文献[7]《机械加工工艺手册》表2.4-66,刀杆伸出长度取
,切削深度为
。因此确定进给量
切削速度:参照参考文献[7]《机械加工工艺手册》表2.4-66,取
机床主轴转速,由式(1.2)有:
,取
实际切削速度,由式(1.2)有:
工作台每分钟进给量,由式(1.7)有:
被切削层长度:
刀具切入长度,由式(1.6)有:
刀具切出长度:
取
行程次数:
机动时间,由式(1.7)有:
本工序所用的机动时间:
1.8.3 工序3:钻顶面四孔
钻顶面四孔(其中包括钻孔,
和扩孔
,铰孔
,以及锪孔
,
)
机床:
刀具:硬质合金锥柄麻花钻头。型号:E211和E101
带导柱直柄平底锪钻(GB4260-84)
公制/莫式4号锥直柄铰刀 刀具材料:
⑴.钻孔,以及
的锥孔
钻孔时先采取的是钻到
在扩到
,所以
,另外的两个
锥孔也先钻到
。
切削深度:
进给量:根据参考文献[7]《机械加工工艺手册》表2.4-52,取
切削速度:参照参考文献[7]《机械加工工艺手册》表2.4-53,取
机床主轴转速,由式(1.1)有:
,取
实际切削速度,由式(1.2)有:
被切削层长度:
刀具切入长度:
式(1.8)
刀具切出长度:
取
走刀次数为1
机动时间:
式(1.9)
⑵.扩孔
钻孔时先采取的是钻到
再扩到
,所以
,
切削深度:
进给量:根据参考文献[7]《机械加工工艺手册》表2.4-52,取
切削速度:参照参考文献[7]《机械加工工艺手册》表2.4-53,取
机床主轴转速,由式(1.1)有:
,取
实际切削速度,由式(1.2)有:
被切削层长度:
刀具切入长度,由式(1.8)有:
刀具切出长度:
取
走刀次数为1
机动时间,由式(1.9)有:
⑶.锪孔
切削深度:
,
根据参考文献[7]《机械加工工艺手册》表查得:进给量
,切削速度
;取
机床主轴转速,由式(1.1)有:
,取
实际切削速度,由式(1.2)有:
被切削层长度:
刀具切入长度,由式(1.8)有:
刀具切出长度:
取
走刀次数为2
机动时间,由式(1.5)有:
⑷.锪孔
切削深度:
,
根据参考文献[7]《机械加工工艺手册》表查得:进给量
,切削速度
;取
机床主轴转速,由式(1.1)有:
,取
实际切削速度,由式(1.2)有:
被切削层长度:
刀具切入长度,由式(1.8)有:
刀具切出长度:
取
走刀次数为1
机动时间,由式(1.5)有:
⑸.铰孔
切削深度:
,
进给量:根据参考文献[7]《机械加工工艺手册》表2.4-58,
取
切削速度:参照参考文献[7]《机械加工工艺手册》表2.4-60,取
机床主轴转速,由式(1.1)有:
,取
实际切削速度,由式(1.2)有:
被切削层长度:
刀具切入长度,由式(1.8)有:
刀具切出长度:
取
走刀次数为1
机动时间,由式(1.9)有:
1.8.4 工序4:钻侧面两孔
钻侧面两孔(其中包括钻的孔和
的螺纹孔)
机床:
⑴.钻
切削深度:
根据参考文献[7]《机械加工工艺手册》表查得:进给量
,切削速度
,
机床主轴转速,由式(1.1)有:
,取
实际切削速度,由式(1.2)有:
被切削层长度:
刀具切入长度,由式(1.8)有:
刀具切出长度:
取
加工基本时间,由式(1.5)有:
⑵.钻螺孔
切削深度:
进给量:根据参考文献[7]《机械加工工艺手册》表2.4-39,
,取
切削速度:参照参考文献[7]《机械加工工艺手册》表2.4-41,取
机床主轴转速,由式(1.1)有:
,取
实际切削速度,由式(1.2)有:
被切削层长度:
刀具切入长度,由式(1.8)有:
刀具切出长度:
走刀次数为1
机动时间,由式(1.5)有:
③、攻螺纹孔
机床:组合攻丝机
刀具:高速钢机动丝锥
进给量:由于其螺距
,因此进给量
切削速度:参照参考文献[7]《机械加工工艺手册》表2.4-105,取
机床主轴转速,由式(1.1)有:
,取
丝锥回转转速:取
实际切削速度,由式(1.2)有:
被切削层长度:
刀具切入长度:
刀具切出长度:
走刀次数为1
机动时间,由式(1.5)有:
钻顶面四孔的机动时间:
这些工序的加工机动时间的总和是:
1.9 时间定额计算及生产安排
根据设计任务要求,该CA6140机床后托架的年产量为5000件。一年以240个工作日计算,每天的产量应不低于21件。设每天的产量为21件。再以每天8小时工作时间计算,则每个工件的生产时间应不大于22.8min。
参照参考文献[7]《机械加工工艺手册》表2.5-2,机械加工单件(生产类型:中批以上)时间定额的计算公式为:
(大量生产时
) 式(1.10)
因此在大批量生产时单件时间定额计算公式为:
式(1.11)
其中: —单件时间定额
—基本时间(机动时间)
—辅助时间。用于某工序加工每个工件时都要进行的各种辅助动作所消耗的时间,包括装卸工件时间和有关工步辅助时间
—布置工作地、休息和生理需要时间占操作时间的百分比值
1.9.1 粗、精铣底面
机动时间:
辅助时间:参照参考文献[7]《机械加工工艺手册》表2.5-45,取工步辅助时间为
。由于在生产线上装卸工件时间很短,所以取装卸工件时间为
。则
:根据参考文献[7]《机械加工工艺手册》表2.5-48,
单间时间定额,由式(1.11)有:
因此应布置一台机床即可以完成本工序的加工,达到生产要求。
1.9.2 镗侧面三杠孔
⑴、粗镗侧面的三孔(,
,
)
机动时间:
辅助时间:参照参考文献[7]《机械加工工艺手册》表2.5-37,取工步辅助时间为
。由于在生产线上装卸工件时间很短,所以取装卸工件时间为
。则
:根据参考文献[7]《机械加工工艺手册》表2.5-39,
单间时间定额,由式(1.11)有:
因此应布置一台机床即可以完成本工序的加工,达到生产要求。
⑵、半精镗侧面的三孔(,
,
)
机动时间:
辅助时间:参照参考文献[7]《机械加工工艺手册》表2.5-37,取工步辅助时间为
。由于在生产线上装卸工件时间很短,所以取装卸工件时间为
。则
:根据参考文献[7]《机械加工工艺手册》表2.5-39,
单间时间定额,由式(1.11)有:
因此应布置一台机床即可以完成本工序的加工,达到生产要求。
⑶、精镗侧面的三孔(,
,
)
机动时间:
辅助时间:参照参考文献[7]《机械加工工艺手册》表2.5-37,取工步辅助时间为
。由于在生产线上装卸工件时间很短,所以取装卸工件时间为
。则
:根据参考文献[7]《机械加工工艺手册》表2.5-39,
单间时间定额,由式(1.11)有:
因此应布置一台机床即可以完成本工序的加工,达到生产要求。
1.9.3 钻顶面四孔
钻顶面四孔(其中包括钻和
、扩钻
,铰孔
以及锪孔
和
)
机动时间:
辅助时间:参照参考文献[7]《机械加工工艺手册》表2.5-41,取工步辅助时间为
。由于在生产线上装卸工件时间很短,所以取装卸工件时间为
。则
:根据参考文献[7]《机械加工工艺手册》表2.5-43,
单间时间定额,由式(1.11)有:
因此应布置一台机床即可完成本工序的加工,达到生产要求
钻左侧面两孔(其中包括钻的孔和
的螺孔)
机动时间:
辅助时间:参照参考文献[7]《机械加工工艺手册》表2.5-41,取工步辅助时间为
。由于在生产线上装卸工件时间很短,所以取装卸工件时间为
。则
:根据参考文献[7]《机械加工工艺手册》表2.5-43,
单间时间定额,由式(1.11)有:
因此应布置一台机床即可完成本工序的加工,达到生产要求
的螺纹孔攻丝
机动时间:
辅助时间:参照钻孔辅助时间,取装卸工件辅助时间为
,工步辅助时间为
。则
:参照钻孔
值,取
单间时间定额,由式(1.11)有:
因此布置一台机床即可完成本工序的加工,达到生产要求。
2 专用夹具设计
为了提高劳动生产率,保证加工质量,降低劳动强度。在加工CA6140机床后托架零件时,需要设计专用夹具。
根据任务要求中的设计内容,需要设计加工工艺孔夹具及铣底面夹具一套。其中加工侧面的三孔的夹具将用于卧式镗床,而顶面的四孔用到的刀具分别为两把麻花钻、扩孔钻、铰刀以及锪钻进行加工,侧面两个孔将用两把麻花钻对起进行加工。
2.1 铣平面夹具设计
2.1.1 研究原始质料
利用本夹具主要用来粗铣底平面,该底平面对孔、
、
的中心线要满足尺寸要求以及平行度要求。在粗铣此底平面时,其他都是未加工表面。为了保证技术要求,最关键是找到定位基准。同时,应考虑如何提高劳动生产率和降低劳动强度。
2.1.2 定位基准的选择
由零件图可知:粗铣平面对孔、
、
的中心线和轴线有尺寸要求及平行度要求,其设计基准为孔的中心线。为了使定位误差达到要求的范围之内,在此选用V形块定心自动找到中心线,这种定位在结构上简单易操作。
采用V形块定心平面定位的方式,保证平面加工的技术要求。同时,应加一侧面定位支承来限制一个沿轴移动的自由度。
2.1.3 切削力及夹紧分析计算
刀具材料:(高速钢端面铣刀)
刀具有关几何参数:
由参考文献[16]《机床夹具设计手册》表1-2-9 可得铣削切削力的计算公式:
式(2.1)
查参考文献[16]《机床夹具设计手册》表得:
对于灰铸铁: 式(2.2)
取 , 即
所以
由参考文献[17]《金属切削刀具》表1-2可得:
垂直切削力 :(对称铣削) 式(2.3)
背向力:
根据工件受力切削力、夹紧力的作用情况,找出在加工过程中对夹紧最不利的瞬间状态,按静力平衡原理计算出理论夹紧力。最后为保证夹紧可靠,再乘以安全系数作为实际所需夹紧力的数值。即:
式(2.4)
安全系数K可按下式计算:
式(2.5)
式中:为各种因素的安全系数,见《机床夹具设计手册》表
可得:
所以 式(2.6)
式(2.7)
式(2.8)
由计算可知所需实际夹紧力不是很大,为了使其夹具结构简单、操作方便,决定选用手动螺旋夹紧机构。
单个螺旋夹紧时产生的夹紧力按以下公式计算:
式(2.9)
式中参数由参考文献[16]《机床夹具设计手册》可查得:
其中:
螺旋夹紧力:
易得:
经过比较实际夹紧力远远大于要求的夹紧力,因此采用该夹紧机构工作是可靠的。
2.1.4 误差分析与计算
该夹具以平面定位V形块定心,V形块定心元件中心线与平面规定的尺寸公差为。为了满足工序的加工要求,必须使工序中误差总和等于或小于该工序所规定的工序公差。
与机床夹具有关的加工误差,一般可用下式表示:
式(2.10)
由参考文献[16]《机床夹具设计手册》可得:
⑴、平面定位V形块定心的定位误差 :
⑵、夹紧误差 : 式(2.11)
其中接触变形位移值:
式(2.12)
⑶、磨损造成的加工误差:通常不超过
⑷、夹具相对刀具位置误差:取
误差总和:
从以上的分析可见,所设计的夹具能满足零件的加工精度要求。
2.1.5 夹具设计及操作的简要说明
如前所述,应该注意提高生产率,但该夹具设计采用了手动夹紧方式,在夹紧和松开工件时比较费时费力。由于该工件体积小,工件材料易切削,切削力不大等特点。经过方案的认真分析和比较,选用了手动夹紧方式(螺旋夹紧机构)。这类夹紧机构结构简单、夹紧可靠、通用性大,在机床夹具中很广泛的应用。
此外,当夹具有制造误差,工作过程出现磨损,以及零件尺寸变化时,影响定位、夹紧的可靠。为防止此现象,支承钉和V形块采用可调节环节。以便随时根据情况进行调整。
2.2 镗孔夹具设计
2.2.1 研究原始质料
利用本夹具主要用来镗加工孔、
、
。加工时除了要满足粗糙度要求外,还应满足孔轴线对底平面的平行度公差要求。为了保证技术要求,最关键是找到定位基准。同时,应考虑如何提高劳动生产率和降低劳动强度。
2.2.2 定位基准的选择
由零件图可知:孔、
、
的轴线与底平面有平行度公差要求,在对孔进行加工前,底平面进行了粗铣加工。因此,选底平面为定位精基准(设计基准)来满足平行度公差要求。
孔、
、
的轴线间有位置公差,选择左侧面为定位基准来设计镗模,从而满足孔轴线间的位置公差要求。工件定位用底平面和两个侧面来限制六个自由度。
2.2.3 切削力及夹紧力的计算
镗刀材料:(硬质合金镗刀)
刀具的几何参数:
由参考文献[16]《机床夹具设计手册》查表可得:
圆周切削分力公式: 式(2.13)
式中
式(2.14)
查表得:
取
由表可得参数:
即:
同理:径向切削分力公式 : 式(2.15)
式中参数:
即:
轴向切削分力公式 : 式(2.16)
式中参数:
即:
根据工件受力切削力、夹紧力的作用情况,找出在加工过程中对夹紧最不利的瞬间状态,按静力平衡原理计算出理论夹紧力。最后为保证夹紧可靠,再乘以安全系数作为实际所需夹紧力的数值。即:
安全系数K可按下式计算,由式(2.5)有::
式中:为各种因素的安全系数,见《机床夹具设计手册》表
可得:
所以,由式(2.6)有:
由式(2.7)有:
由式(2.8)有:
螺旋夹紧时产生的夹紧力按以下公式计算,由式(2.9)有:
式中参数由参考文献[16]《机床夹具设计手册》可查得:
其中:
螺旋夹紧力:
该夹具采用螺旋夹紧机构,用螺栓通过弧形压块压紧工件。受力简图如下:
图2.1 弧形压块受力简图
由表得:原动力计算公式
即: 式(2.15)
由上述计算易得:
由计算可知所需实际夹紧力不是很大,为了使其夹具结构简单、操作方便,决定选用手动螺旋夹紧机构。
2.2.4 误差分析与计算
该夹具以两个平面定位,要求保证孔轴线与左侧面间的尺寸公差以及孔轴线与底平面的平行度公差。为了满足工序的加工要求,必须使工序中误差总和等于或小于该工序所规定的工序公差。
孔轴线与左侧面为线性尺寸一般公差。根据国家标准的规定,由参考文献[15]《互换性与技术测量》表
可知:
取(中等级)即 :尺寸偏差为
由[16]《机床夹具设计手册》可得:
⑴ 、定位误差(两个垂直平面定位):当时;侧面定位支承钉离底平面距离为
,侧面高度为
;且满足
;则:
⑵ 、夹紧误差 ,由式(2.11)有::
其中接触变形位移值:
式(2.16)
⑶、磨损造成的加工误差:通常不超过
⑷、夹具相对刀具位置误差:取
误差总和:
从以上的分析可见,所设计的夹具能满足零件的加工精度要求。
2.3钻顶面四孔夹具设计
2.3.1 研究原始质料
利用本夹具主要用来钻、铰加工顶面的四孔,其中包括钻顶面四孔(其中包括钻孔和扩孔
,铰孔
,以及锪孔
,
)。加工时除了要满足粗糙度要求外,还应满足孔轴线对底平面的平行度公差要求。为了保证技术要求,最关键是找到定位基准。同时,应考虑如何提高劳动生产率和降低劳动强度。
2.3.2 定位基准的选择
由零件图可知:顶面四孔的轴线与左侧面和后侧面的尺寸要求要求,在对孔进行加工前,底平面进行了铣加工,后侧面也是一直都不加工的侧面,因此,选后侧面和做侧面面为定位精基准(设计基准)来满足CA6140机床后托架顶面四孔加工的尺寸要求。
由零件图可以知道,图中对孔的的加工没有位置公差要求,所以我们选择左侧面和后侧面为定位基准来设计钻模,从而满足孔轴线和两个侧面的尺寸要求。工件定位用底面和两个侧面来限制5个自由度。
2.3.3 切削力及夹紧力的计算
由资料《机床夹具设计手册》查表可得:
切削力公式: 式(2.17)
式中
查表得:
即:
实际所需夹紧力:由参考文献[16]《机床夹具设计手册》表得:
安全系数K可按下式计算,由式(2.5)有::
式中:为各种因素的安全系数,见参考文献[16]《机床夹具设计手册》表
可得:
所以
由计算可知所需实际夹紧力不是很大,为了使其夹具结构简单、操作方便,决定选用手动螺旋夹紧机构。
取,
,
螺旋夹紧时产生的夹紧力,由式(2.9)有::
式中参数由[16]《机床夹具设计手册》可查得:
其中:
由[16]《机床夹具设计手册》表得:原动力计算公式:
由上述计算易得:
因此采用该夹紧机构工作是可靠的。
2.3.4 误差分析与计算
该夹具以底面、侧面和顶面为定位基准,要求保证孔轴线与左侧面间的尺寸公差。为了满足工序的加工要求,必须使工序中误差总和等于或小于该工序所规定的工序公差。
孔与左侧面为线性尺寸一般公差。根据国家标准的规定,由参考文献[15]《互换性与技术测量》表可知:
取(中等级)即 :尺寸偏差为
、
由[16]《机床夹具设计手册》可得:
⑴、定位误差:定位尺寸公差,在加工尺寸方向上的投影,这里的方向与加工方向一致。即:故
⑵、夹紧安装误差,对工序尺寸的影响均小。即:
⑶、磨损造成的加工误差:通常不超过
⑷、夹具相对刀具位置误差:钻套孔之间的距离公差,按工件相应尺寸公差的五分之一取。即
误差总和:
从以上的分析可见,所设计的夹具能满足零件的加工精度要求。
2.3.5 夹具设计及操作的简要说明
本夹具用于在钻床上加工后托架的底孔、锥孔。工件以底平面、侧面和顶端为定位基准,在支承钉和支承板上实现完全定位。采用手动螺旋压板机构夹紧工件。该夹紧机构操作简单、夹紧可靠。
结 论
通过本次的毕业设计,使我能够对书本的知识做进一步的了解与学习,对资料的查询与合理的应用做了更深入的了解,本次进行工件的工艺路线分析、工艺卡的制定、工艺过程的分析、铣镗钻夹具的设计与分析,对我们在大学期间所学的课程进行了实际的应用与综合的学习。
参考文献
[1] 许晓旸,专用机床设备设计[M],重庆:重庆大学出版社,2003。
[2] 孙已德,机床夹具图册[M],北京:机械工业出版社,1984:20-23。
[3] 贵州工学院机械制造工艺教研室,机床夹具结构图册[M],贵阳:贵州任命出版社,1983:42-50。
[4] 东北重型机械学院等,机床夹具设计手册[M],上海:上海科学技术出版社,1979。
[5] 孟少龙,机械加工工艺手册第1卷[M],北京:机械工业出版社,1991。
[6] 《金属机械加工工艺人员手册》修订组,金属机械加工工艺人员手册[M],上海:上海科学技术出版社,1979。
[7] 李洪,机械加工工艺手册[M],北京:机械工业出版社,1990。
[8] 马贤智,机械加工余量与公差手册[M],北京:中国标准出版社,1994。
[9] 上海金属切削技术协会,金属切削手册[M],上海:上海科学技术出版社,1984。
[10] 周永强,高等学校毕业设计指导[M],北京:中国建材工业出版社,2002。
[11] 刘文剑,曹天河,赵维,夹具工程师手册[M],哈尔滨:黑龙江科学技术出版社,1987。
[12] 余光国,马俊,张兴发,机床夹具设计[M],重庆:重庆大学出版社,1995。
[13] 东北重型机械学院,洛阳农业机械学院,长春汽车厂工人大学,机床夹具设计手册[M],上海:上海科学技术出版社,1980。
[14] 李庆寿,机械制造工艺装备设计适用手册[M],银州:宁夏人民出版社,1991。
[15] 廖念钊,莫雨松,李硕根,互换性与技术测量[M],中国计量出版社,2000:9-19。
[16] 王光斗,王春福,机床夹具设计手册[M],上海科学技术出版社,2000。
[17] 乐兑谦,金属切削刀具,机械工业出版社,2005:4-17。
[18] Machine Tools N.chernor 1984.
[19] Machine Tool Metalworking John L.Feirer 1973.
[20] Handbook of Machine Tools Manfred weck 1984 .
致 谢
首先,我要感谢我的毕业设计指导老师卢宗彪老师。在毕业设计中,他给予了我学术和指导性的意见。我万分的感谢他给我的宝贵的指导意见和鼓励。
同时,我深深感谢姚必强老师、谢永春老师、李泽容老师、文广老师、周汝忠老师、党玉春老师、乔水明老师、卢宗彪老师、张勇老师、唐锐老师、翟秀云老师、周丹老师、莫文辉老师等。在他们的课堂上,我受益匪浅,得到了不少对我论文有帮助的知识和想法。
我也非常感谢我的父母。在学习和生活上,他们一直都很支持我,使我能全身心地投入到学习中。
最后,很感谢阅读这篇毕业设计(论文)的人们。感谢您们抽出宝贵的时间来阅读这篇毕业设计(论文)。