供应商评价和再评价制度
第一章 总则
第一条 目的
为规范原料供应商的管理,保证原料供应商的合法性和挑选合格供应商提供依据,确保原料供应商的质量和数量,对供应商进行阶段性的评估与考核,从而有效保证质量的稳定性,保证本公司使用的原料安全、质优和追溯性。
第二条 适用范围
本制度规定的供应商泛指一切可以向公司提供饲料原料、单一饲料、饲料添加剂、药物饲料添加剂、添加剂预混合饲料、浓缩饲料的原料、包装耗材的生产企业和经销商,适用于本公司生产管理部门使用。
第三条 管理职责
1、生产管理部负责组织对供应商进行选择、评价与再评价,并对供应商的供货情况进行评价与再评价;
2、制造部部长负责对合格供应商进行最后审批。
第二章 供应商评价与再评价
第一条 供应商评价原则
本着公平、公正、公开的原则,以信誉可靠、产品合法、质优价廉为评审依据,选择合格的原料供应商。
第二条 供应商选择、评价及再评价流程
1、生产管理部按公司质量管理和产品质量控制的要求,根据关键原料的一致性、符合性和有效性原则,收集符合供货条件的供应商信息、资质等资料,并对所收集的供应商信息、资料进行初步筛选。
2、生产管理部在品管部的配合下对经过初步筛选的供应商的资质、产品质量、保障能力及诚信度等进行全面的分析、考核、评估后确定符合条件的供应商,并填写《供方评价表》。
3、将经过筛选的合格供应上报制造部部长审核,将通过制造部部长审批的合格供应商录入公司的《合格供方名单》之中,归入档案,妥善保存。
4、采购担当负责对合格供应商进行供货质量、到货及时性随时记录,并填写《合格供方供货明细》。以便对供应商随时评价、每年再评价。
第三条 评价内容
评价供应商主要针对其资质、诚信、产品质量、供货保障能力等,对影响程度不同的采购产品可采用不同的评价准则。公司在评价供应商时应全面考虑以下因素:
1、供应商的产品质量、价格、后续服务、历史业绩等;
2、供应商的诚信度、保障能力;
3、来自外部方面的信息(如同行的评价、主管部门的推荐、第三方认证等);
4、若涉及采购产品中有强制性认证的,还应有认证的证书和质量证明等。
第四条 评价与再评价频率
1、随时评价:对新入选供应商或已经入选但供应的原料质量不够稳定,或信誉、能力一般的供应商应该随时进行评价。
2、年度再评价:公司每年年底对合格供应商进行一次再评价,对供应能力、质量信誉较差、到货及时性较差的供应商坚决剔除。
第五条 评价与再评价标准
1、对第一次供应原辅材料的供应商,除提供充分的书面证明材料外,还需经样品测试,测试合格才能供货:
(1)新供应商根据相关要求提供少批量原料;
(2)交品管部实验,实验结果反馈给生产管理部门;
(3)实验结果不合格则取消其供货资格。实验结果合格的,必要时再经试用,均合格的,经制造部长批准后,可列入《合格供方名单》,并且进行随时评价。
2、随时评价标准:
采购担当负责对合格供应商进行供货质量,到货及时性随时记录,如有质量或者到货及时性发现一次问题,坚决剔除该供货商。
3、再评价标准:
公司每年年底对合格供应商进行一次再评价,采购担当根据一年的《合格供方供货明细》,如有质量或者到货及时性发现问题多于三次的确定不合格,剔除该供货商。三次以下(含三次)的确定合格,上报制造部部长审核签字,继续录入公司的《合格供方名单》之中。
4、供应商的日常管理
生产管理部应时常与供应商进行沟通,并对供应商的供货业绩进行跟踪,及时与品管部进行沟通。供应商产品如出现严重质量问题,生产管理部应及时要求供应商限期整改,但质量仍没有明显改进的,应取消其供货资格。
第二篇:供应商质量评价制度
供应商质量评价手册
(版本:A)
编制:
审核:
批准:
发布日期:20##-9-15 实施日期:20##-9-30
供应商质量评价标准(试行)
1 目的:对供应商进行定期的质量评价,确定供应商质量等级,根据考评结果确定相应的管理和辅导对策,促进供应商品质改善,能够长期、稳定地供应公司要求的合格物料、适应公司的长期发展需要。
2 范围:适合于主要原料供应商的质量评价过程。
3 职责:
3.1品质部进货检验负责供应商的质量评价管理;
3.2品质部过程检验和生产各车间负责原材料使用情况的收集和反馈。
4 工作程序:
4.1总则:
品质部对以下几个方面综合评价:进货品质、使用品质、品质改善、配合度;
评价频次:按月度进行评价,季度/半年/年度按照月度平均进行评价。
评价对象:自动焊丝管、丝母、下排气帽、法兰盘、端盖(可根据情况适当调整)
4.2月度评价标准:
4.2.1进货品质(60分)
4.2.1.1批退率(进货不合格批次/总进货批次*100%)(40分)
A.当月质量得分=(1-批退率)*30分
B.近期质量得分=(1-累计3月批退率)*10分
4.2.1.2不良率(抽检不良数/抽检总数*100%)(10分)
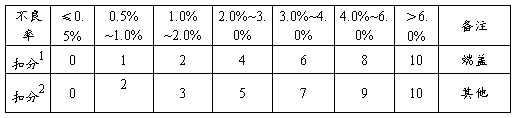
4.2.1.3出货检验报告(5分)
要求供应商随货提交出货检验报告,每缺少1个批次扣2分,出货检验报告不符合要求每次扣2分,扣完为止。
4.2.1.4来料包装质量(5分)

4.2.2使用品质(20分)
4.2.2.1过程批不良(10分)
在生产使用中,因原材料问题导致批量不良(一般外观缺陷>5%;严重外观缺陷、尺寸不良>3%;功能方面>2%),每出现一次过程投诉经确认批退的分别扣2、3、5分,扣完为止。
4.2.2.1月使用个例不良(10分)
根据生产过程中出现的不良情况,对同类供应商进行排名,按照9,7,5,3,1计算得分。
4.2.3品质改善效果(10分)
对反馈品质问题的改善情况跟踪验证,根据问题出现的频次和改善效果,给出评分。
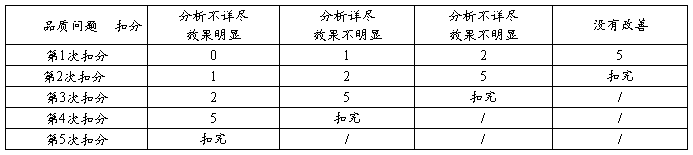
4.2.4配合度(10分)
4.2.4.1投诉处理配合度(7分)

注:收到投诉报告或电话投诉1天内,及时向投诉人沟通并经其同意延时回复的不纳入评分范围。
4.2.4.2服务配合度(3分)
对品质要求提供的其他资料(如材质报告等)或服务要求,不能如期提供的,每次扣1分,未提供的扣3分。
4.3质量评价等级
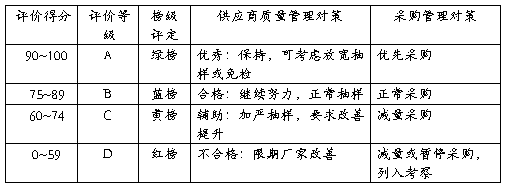
注:1)评为B级以下的,需进行品质改善提升,由品质部发出《供应商品质改善通知单》,供应商按要求提供改善措施并由品质在后续供货中监督。
2)D级发生一次时,一个月必须改善不良点;D级发生两次时,限期整改,予以警告;若连续三个月被评为D级,则取消该供应商资格。
4.3季度/半年/年度评价:
取供应商月度平均值作为该供应商季度/半年/年度评分,评分=累计总得分/月数。
4.4来料质量异常及过程异常的反馈处理
4.4.1 SCAR报告《Supplier Corrective Action Request Report》
4.4.1.1发放条件:
a) 来料抽检时,功能不良超出AQL;
b) 来料抽检时,尺寸不良影响装配,并且不良率超过3%;
c) 来料抽检时,外观缺陷的不良率大于5%;
d) 生产线投诉时,与a)、b)、c)相同;
e) 客户投诉并要求书面回复时。
4.4.1.2 结案条件:
a) 来料连续3批无类似缺陷;
b) 一个月内只有一批来料,且该批来料无类似缺陷或不良率有明显降低;
c) 一个半月内无上货,其他同类产品无类似缺陷或不良率有明显降低;
4.4.2 除4.4.1.1项之外发现的来料不良,可以通过电话或其它形式反馈给供应商改善、处理;
4.5附表
附表一《供应商品质改善通知单》
附表二《来料不良改善通知单》
附表三《供应商月度质量评价表》
附表一
供应商品质改善通知单
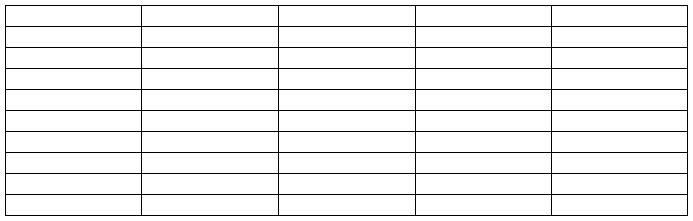
附表二
来料不良改善通知单
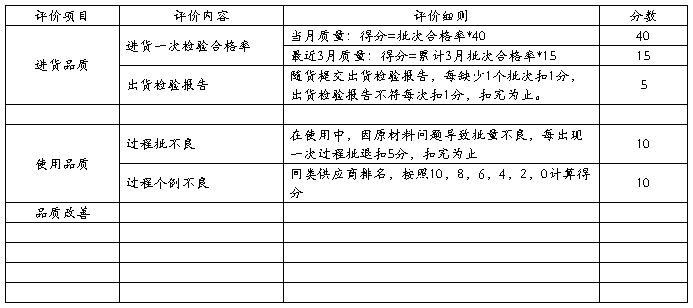
3.6 来料质量异常的反馈及处理
3.6.1 SCAR报告《Supplier Corrective Action Request Report》
3.6.1.1发放条件:
f) 来料抽检时,功能不良超出AQL;
g) 来料抽检时,尺寸不良影响装配,并且不良率超过3%;
h) 来料抽检时,外观缺陷的不良率大于5%;
i) 生产线投诉时,与a)、b)、c)相同;
j) 客户投诉并要求书面回复时;
3.6.1.2 结案条件:
d) 来料连续3批无类似缺陷;
e) 一个月内只有一批来料,且该批来料无类似缺陷或不良率有明显降低;
f) 一个半月内无上货,其他同类产品无类似缺陷或不良率有明显降低;
3.6.2 除3.5.1.1项之外发现的来料不良,SQE都必须以电话或其它形式反馈给供应商改善、处理;
? 5.1.3 考评标准
? 5.1.3.1 现场质保体系等级考评
本公司通过对供方现场审核,根据供方质保体系实际满足要求的程度,对附表1“供方评定评分表”中的项目,按标准逐项进行打分,并以得分高低按以下标准确定供方质保体系考评结论及等级:
A级(合格):得分为90-100。
B级(合格):得分为80-89。
C级(合格需改进):得分为70-79。
D级(不合格):得分为70以下。
? 5.1.3.2 实物质量等级考评
? A级(合格):经在本公司及供方现场实物质量抽查均无缺陷,且供方所供产品一次入库批次合格率为100%。
? B级(合格):经在本公司及供方现场实物质量抽查无缺陷,且供方所供产品一次入库批次合格率为98%以上。
? C级(合格需改进):经在本公司及供方现场实物质量抽查一般项存在缺陷且总项数小于2项(含),同时供方所供产品一次入库批次合格率为96%以上(含)。
? D级(不合格):经在本公司及供方现场实物质量抽查一般项存在缺陷且总项数大于2项,且供方所供产品一次入库批次合格率为96%以下。
? 5.1.3.3 供货业绩考评
a. 供方交付产品的合格率(以本公司质量部的质量统计报表为准)在98%以上为合格,否则为不合格。
b. 供方产品交付及时率(以本公司采购部的供方供货业绩记录表为准)为100%者合格,否则不合格。
c. 供方服务到位率(以本公司发出的“质量问题信息反馈单”和要求供方前来处理质量问题或有关事宜的实现程度来评价)不低于95%者为合格,否则不合格。
? 5.1.3.4 综合考评
为了更真实、客观、全面地反映供方的总体状况,分别从供方的质量保证能力、生产/交付能力、服务能力以及提供产品的价格水平等方面建立相应的供方综合评价指标,并根据各供方的实际供货情况,逐一予以评价打分,最后结合各指标重要度权数,得出其综合考评得分。供方的综合考评得分由本公司采购部按季、按年予以统计,并及时向各供方通报。其各评价指标的评价打分标准如下:
A. 质量保证能力(得分范围为0-100分;权数为0.35)
a) 供方所供产品一次入库批次合格率×100作为得分基数。
b) 本公司生产过程中发现不合格,每次扣1分。
c) 供方事故(供方在交付产品时因延迟交付或交付后因质量问题造成本公司停产的)每发生一次扣5分。
d) 重复发生同类不合格问题的,每次扣2分。
B. 生产/交付能力(得分范围为0-100分;权数为0.3)
a) 供方产品交付及时率(以本公司采购部的供方供货业绩记录表为准)×100作为得分基数。
b) 供方事故(供方在交付产品时因延迟交付或交付后因质量问题造成本公司停产的)每发生一次扣5分。
c) 提供产品未按包装规范包装的,每次扣3分。
C. 服务能力(得分范围为0-100分;权数为0.15)
a) 评价得分基数为100分。
b) 供方对本公司发出的“质量问题信息反馈单”,不能在规定的时间内给予答复的,每次扣5分。
c) 因供方问题,未能及时到现场进行服务的或服务不解决问题的,每次扣5分。
D. 产品价格水平(得分范围为80-100分;权数为0.2)
a) 评价得分基数为100分。
b) 高于同行业同类产品市场平均价的为“偏高”,扣20分;
c) 接近同行业同类产品市场平均价的为“平价”,扣10分;
d) 低于同行业同类产品市场平均价的为“偏低”,不扣分。
E. 综合考评得分
综合考评得分=质量保证能力评价得分×0.35+生产/交付能力评价得分×0.35+服务能力评价得分×0.15+产品价格水平评价得分×0.2
? 5.2 供方年度奖惩
? 5.2.1 奖惩原则
? 5.2.1.1 为了更好地奖励先进、鞭策落后,自20##年开始,各供方需在本公司设立一定数额(按各供方年供货额大小和年度综合考评得分高低而定)的综合质量保证金。
? 5.2.1.2 供方在本公司设立的综合质量保证金,由本公司统一使用,并定期向各供方通报使用情况。
? 5.2.1.3 经各供方确认的各类质量损失赔偿款及本公司技术、质量和其他专业人员亲临供方现场的技术咨询、指导费,均在供方的综合质量保证金中列支,若综合质量保证金不足,则在本公司应付供方的货款中扣除。
? 5.2.1.4 经综合考评,被评为年度优秀供方的,本公司将给予一定的奖励,并在综合质量保证金中列支。
? 5.2.1.5 经综合考评,最终定为不合格的供方,本公司将没收该供方当年度的综合质量保证金。若其质量赔偿额超过当年度综合质量保证金的,则在本公司应付该供方的货款中扣除。
? 5.2.2 奖惩标准
? 5.2.2.1 经综合考评,评审合格的供方,将列入本公司合格分承包方名册。
? 5.2.2.2 经综合考评,评审不合格的供方,本公司给予拆点黄牌警告,且供方必须制定整改措施,并按本公司要求限期进行整改,整改措施需报本公司。整改期间本公司暂停供方的供货。限期整改仍不合格的,本公司有权中止与供方的供货关系。
? 5.2.2.3 经综合考评,供方质保体系考评等级和实物质量考评等级均为A级的供方,优先推荐为本公司当年度的优秀供方。
? 5.2.2.4 对过程控制好、产品质量稳定、服务到位、价格适宜、供货及时且质保体系考评等级和实物质量考评等级均为A级的供方,可评选为“优秀供方”,发给“优秀供方证书”,并在下年度给予以下奖励:
a. 凡属两家配套的产品,优秀分供方所供产品份额可提升到60-80%。
b. 本公司应付该供方的货款可以根据规定的压款期减少一个月。
c. 本公司新产品开发时,该供方可享有优先研制和接受订单的待遇。
5.2.2.5 对于经综合考评,评审不合格且经限期整改后仍不合格的供方,本公司除没收其综合质量保证金外,将逐步予以淘汰,并重新选点。